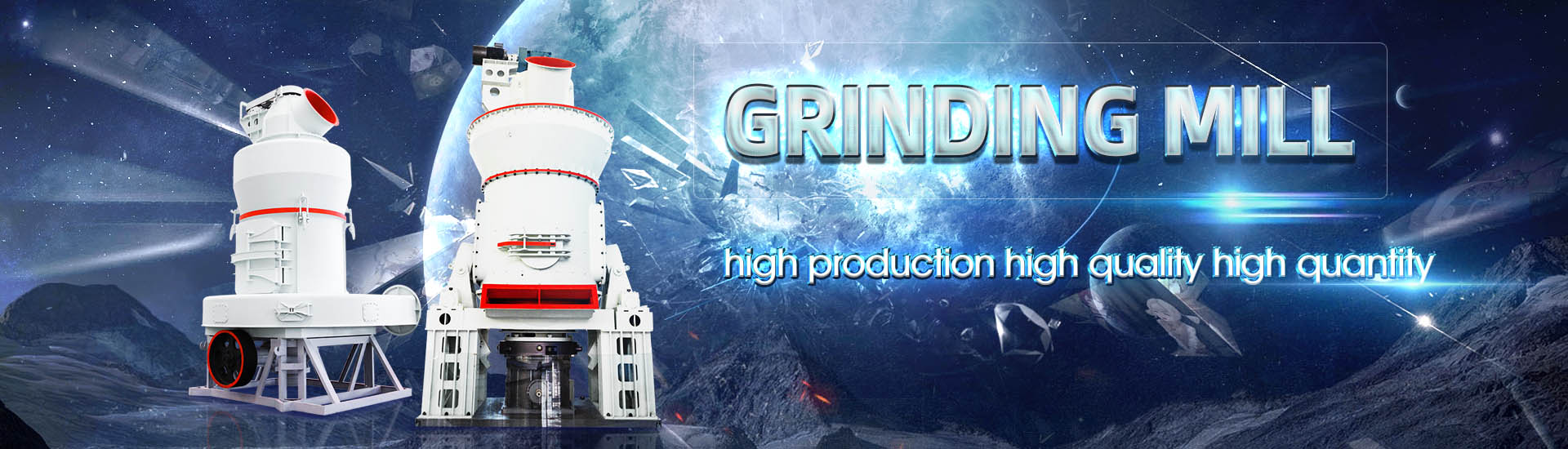
Pulverized coal furnace process flow
.jpg)
Pulverized Coal Boiler an overview ScienceDirect Topics
Steps in the process are (1) mining of the coal from nearsurface or deep mines, (2) transporting crushed coal several centimeters in size to the power station, (3) pulverizing the coal to a powder predominantly less than 100 μ m in size, (4) pneumatically transporting this coal dust with Adjusting the pulverized coal injection angle significantly improves combustion Numerical simulation of the Pulverized coal combustion (PCC) is the most widely used technology for coal power generation In this process, coal is milled, pulverized, and injected in the boiler with air to allow Pulverised Coal Combustion an overview ScienceDirect TopicsIt addresses the processes and their underlying mechanisms involved in pulverised coal combustion namely: drying and heating, devolatilisation, volatile oxidation and char oxidation Fundamentals of pulverised coal combustion ICSC
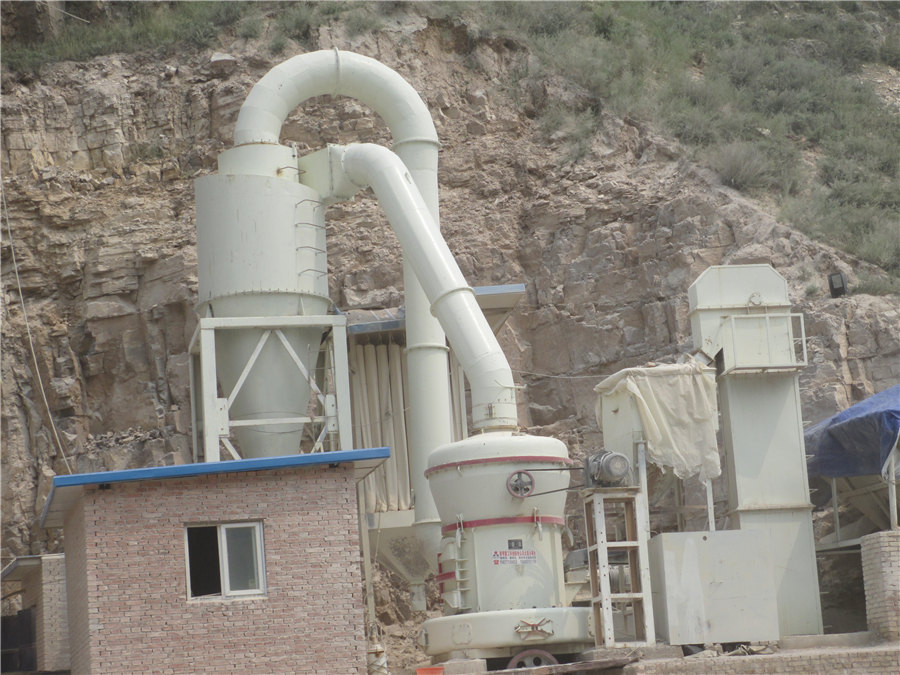
Numerical simulation of the effect of coaxial and crossaxis
2024年10月1日 Adjusting the pulverized coal injection angle significantly improves combustion efficiency Different blowing methods affect temperature distribution and gas flow in the 2023年1月13日 The pulverized coal combustion process in power boilers is still being improved by the preliminary cleaning of coal and the use of various catalytic additives Another area of research that could be valuable is the development Pulverized CoalFired Boilers: Future Directions of 2012年1月1日 In this work, numerical simulation of flow, heat transfer, and combustion process in a 600MW ultra supercritical (USC) pulverized coal boiler under low load is performed using Numerical Study of Furnace Process of a 600 MW Pulverized Coal 2023年3月27日 The influence of TRI with particle flow in opposite pulverized coal boilers on combustion in a furnace was studied in this paper The actual working conditions were simulated in FLUENT and compared with the field Simulation of Pulverized Coal Combustion Process
.jpg)
Combustion and Heat Transfer Characteristics of a 300mw
5 天之前 Abstract Biomass cocombustion is an important measure to reduce the carbon dioxide emissions for pulverized coal boilers In this paper, the heat transfer process of the This part of the book provides recommended values of coefficients and parameters for treating complex reacting flows Parts I and II may well be suitable for use in an advanced course in reacting flows, and have been written partly PulverizedCoal Combustion and Gasification Springer• no pulverized coal buffer volume (Splitter type Distribution Device) Inward Transfer Hot blast backpressure as well as pressure drops in pneumatic conveying lines and flow rate control devices require a pressurizing of pulverized coal from atmosphere pressure level to overpressure level After pressurizing, pulverized coal is transferredPulverized Coal Injection Paul Wurthcoal substance, and only small quantities are held by the associated mineral matter In contrast, inherent moisture depends on its humidity and thermal history, as well as on coal type 22 Process of drying The process of drying includes the evaporation of surface moisture and, subsequently, the loss of inherent moistureFundamentals of pulverised coal combustion ICSC
.jpg)
Twostage gasification process simulation and optimization of
2024年1月2日 Subsequently, it proceeded to Part Ⅱ, where it serves as both the heat source and medium for the rapid pyrolysis of the pulverized coal The simulation process for the rapid pyrolysis of the pulverized coal in Part Ⅱ is analogous to that in Part Ⅰ, with the sole distinction being the conversion coefficient of each component utilized in 2011年2月2日 Pulverized coal (pulverized fuelpf) has been fired in rotary cement kilns (see Kilns) and boiler furnaces (see Boilers)The latter are basically boxes lined with tubes in which water is evaporated and contain a water/steam mixture The coal is pulverized to a fine powder, usually so that 70% is less than about 75 μm in size, before being carried by part of the PULVERIZED COAL FURNACESThe blast furnace process with pulverized coal injection (PCI) rate of up to 250 The oxygen blast furnace process flow chart is shown in Fig 19 (Zhang, HJ et al, 2015) The current problem of oxygen blast furnace is the uneven distribution of recycled gas, which affects the utilization of recycled gasBlast Furnace Process an overview ScienceDirect Topics2011年2月2日 Pulverized coal (pulverized fuelpf) has been fired in rotary cement kilns (see Kilns) and boiler furnaces (see Boilers)The latter are basically boxes lined with tubes in which water is evaporated and contain a water/steam mixture The coal is pulverized to a fine powder, usually so that 70% is less than about 75 μm in size, before being carried by part of the PULVERIZED COAL FURNACES

Multiscale analysis of fine slag from pulverized coal gasification in
2024年2月3日 Fine slag (FS) is an unavoidable byproduct of coal gasification FS, which is a simple heap of solid waste left in the open air, easily causes environmental pollution and has a low resource utilization rate, thereby restricting the development of energysaving coal gasification technologies The multiscale analysis of FS performed in this study indicates typical grain size 2024年10月1日 Notably, the blast furnace process, which consumes large amounts of coke and pulverized coal (PC), is responsible for over 70% of the carbon emissions from steel production (Dutta Sah, 2016) Therefore, optimizing blast furnace operations is imperative, with one key area of research being the improvement of the PC injection process in blast furnaces ( Fig 1 )Numerical simulation of the effect of coaxial and crossaxis Control and Distribution: A reliable pulverized coal flow rate control and an accurate distribution of the global coal flow onto the hot blast tuyeres are key aspects to an efficient replacement of coke in the blast furnace process As such, Paul Wurth has developed a PULVERIZED COAL INJECTION FOR HIGH INJECTION RATES2021年8月18日 Medium oxygenenriched blast furnaces that utilize reducing gas injections are a feasible new ironmaking process that can significantly reduce the coke ratio and carbon dioxide emissions To better inject the reducing gas into the blast furnace, two injection methods were designed in this study, and the effects of the reducing gas on the combustion of pulverized Influence of Reducing Gas Injection Methods on Pulverized Coal
.jpg)
PulverizedCoal Combustion and Gasification: Theory And
A zonal model for radiation heat transfer in coalfired boiler furnaces Whitney Ogalaletseng through which, the entire combustion process for pulverized coal combustion (PCC) can be Numerical simulation investigations into the influence of the mass ratio of pulverizedcoal in fuelrich flow to that in fuellean flow on the 2012年1月1日 Numerical simulation of flow, heat transfer, and combustion process in a 600MW pulverized coal boiler under low load is performed using Computational Fluid Dynamics (CFD) code Fluent The distributions of temperature and species were obtained and their influences onNumerical Study of Furnace Process of a 600 MW Pulverized Coal 2023年1月13日 The paper provides an outlook on future directions of research and the possible applications for pulverized coalfired boilers One potential direction for future research is to focus on the ways (PDF) Pulverized CoalFired Boilers: Future Directions Because pulverized coal firing uses less excess air than stoker firing, and because the rate of coal combustion is governed by particle size, firing pulverized coal in boilers of this vintage elevated combustion temperatures and the process had a high propensity to form slag in Pulverised Coal an overview ScienceDirect Topics
.jpg)
Optimization of pulverized coal injection (PCI) rate in an
2022年5月1日 Comparative study on the combustion performance of coals on a pilotscale test rig simulating blast furnace pulverized coal injection and a labscale droptube furnace Development of Particle Flow Simulator in Charging Process of Blast Furnace by Discrete Element Method Miner Eng, 33 (6) (2012), pp 2733 View in Scopus Google 2023年6月15日 The blast furnace injection process system is mainly composed of raw coal storage and transportation system, dry gas preparation system, pulverized coal preparation system, pulverized coal conveying system, pulverized coal injection system, and gas supply system (Fig 1)There is also a computer control center to control the entire pulverized coal Pulverized Coal Injection of Blast Furnace Ironmaking2024年7月31日 The basic national condition that is dominated by coal will not alter in the foreseeable future Coalfired boiler is the main equipment for coal utilization, and cyclone burner is a practical type of burner There is a cyclone formation, a primary air duct inside the center air duct, and a secondary air duct Introducing a small stream of pulverized coal gas or oil mist Numerical Simulation Study of Combustion under Different Excess 2019年1月1日 For coal and gas dualfired boiler, pulverized coal mass flow and gas volume flow into furnace are important criteria for boiler operation adjustment, and they are important input parameters for Calculation Method of Pulverized Coal Mass Flow Into Coal and
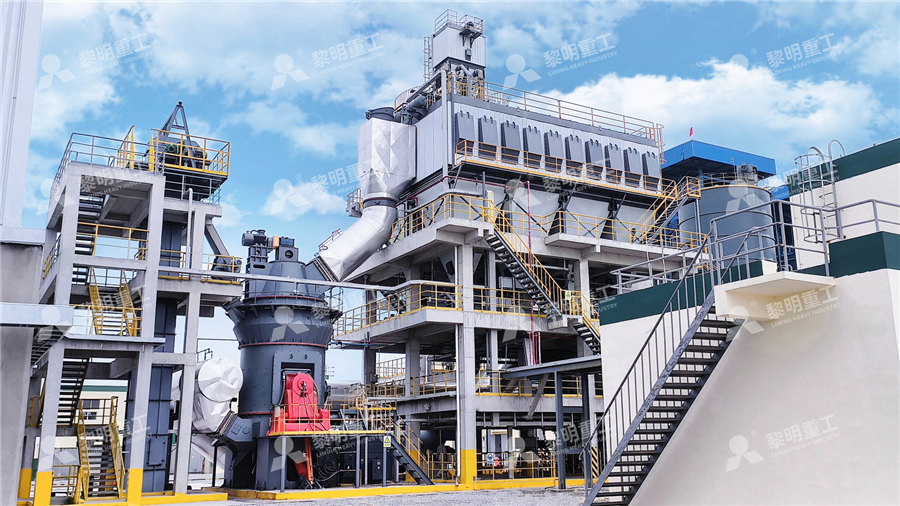
Understanding Blast Furnace Ironmaking with Pulverized Coal
2018年11月4日 Understanding Blast Furnace Ironmaking with Pulverized Coal Injection satyendra; November 4, 2018; which flow up the furnace As coal and coke enter the raceway, they are ignited by the hot air blast and immediately combust as per the following reaction to It can also help remove S released from the coke and coal Process 2024年9月15日 Currently, the steelmaking process uses a pulverized coal injection (PCI) system that serves as the heat source and reductant for ironmaking (blast furnace and FINEX) where system uses expensive highgrade coal and high operating costs Hydrogen steelmaking is currently being developed to achieve carbonfree operation To achieve a softlanding during Combustion visualization analysis of alternative fuels in the 2024年8月15日 Based on a 200 kW downfired onedimensional furnace, the actual peaking process of a power station boiler was simulated to perform a combustion characterization study during the load proposed a new lowload stable combustion method by adjusting the oil secondary air parallel to the fuelrich pulverized coal air flow, Combustion stability and emission characteristics of a pulverized coal Influence of pulverized coal into the blast furnace is an invaluable technology for reducing ironmaking costs In order to increase the rate of pulverized coal injection, it is necessary to investigate the combustion behavior of pulverized coal around the tuyere, and many numerical simulations as well as experimenPrediction of Pulverized Coal Combustion Behavior around
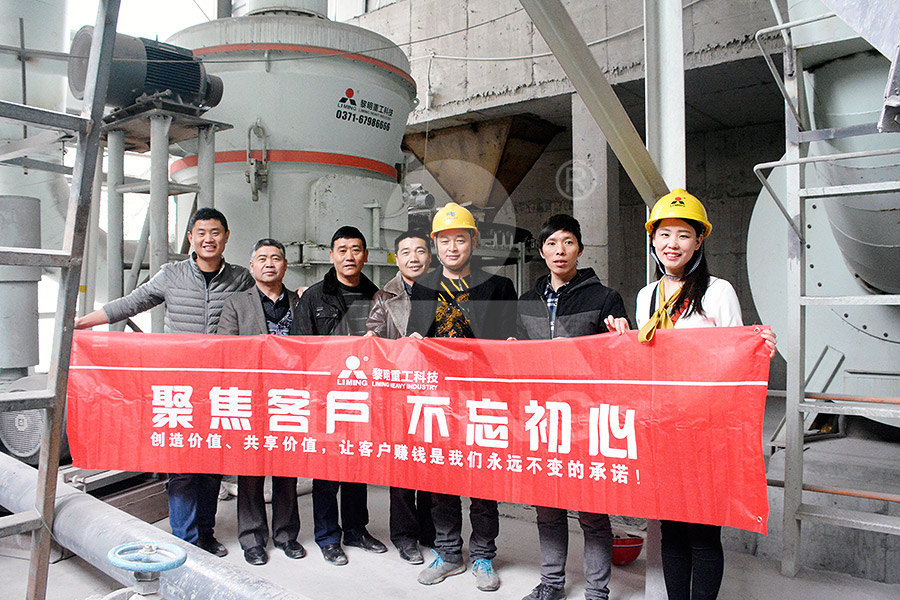
Optimising fuel flow in pulverised coal and biomassfired boilers
41 Commercially available coal flow measurement and control equipment 32 411 GreenBank’s PFMaster 33 412 Mistras Products Systems’ Coal Flow Monitoring Systems (CFM) 33 413 PROMECON’s MECONTROL Coal (in USA licensed to Air Monitor Power as PF FLO III) 34 414 MIC’s Coal Flow Analyser 年4月10日 New pulverized coalfired systems routinelyinstalled today generate power at net thermal cycle efficienciesranging from 34 to 37% (higher heating value) while removingup to 97% of the combined Developments in Pulverized CoalFired Boiler Technology2017年1月1日 A comprehensive mathematical model for prediction of turbulent transport processes and reactions during cocombustion of pulverized fuels in furnace fired by 150 kW swirl stabilizedburner has Development of mathematical model for cofiring pulverized coal 2016年4月8日 Blast furnaces are countercurrent chemical reactors, widely utilized in the ironmaking industry Hot reduction gases injected from lower regions of the furnace ascend, reacting with the descending burden Through this reaction process, iron ore is reduced into liquid iron that is tapped from the furnace hearth Due to the extremely harsh environment inside the Comprehensive Numerical Modeling of the Blast Furnace Ironmaking Process
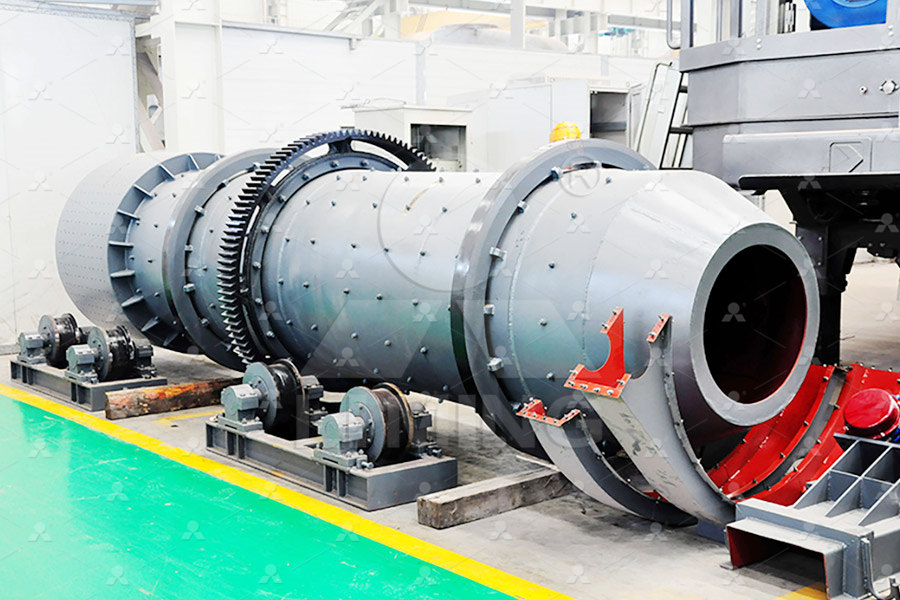
Direct Numerical Simulation of Pulverized Coal Combustion in
2012年9月27日 A compressible direct numerical simulation (DNS) solver for pulverized coal combustion has been developed and used to study a pulverized coal jet flame with a Reynolds number of 28 284 based on the nozzle diameter An eighthorder center differential scheme combined with an explicit tenthorder filter is used for spatial discretization The classical fourth 2020年10月10日 Coalfired industrial boilers should operate across a wide range of loads and with a higher reduction of pollutant emission in China In order to achieve these tasks, a physical model including two swirling burners on the front wall and boiler furnace was established for a 35 t/h pulverized coalfired boiler Based on Computational Fluid Dynamics (CFD) theory and the Numerical Simulation of Combustion in 35 t/h Industrial Pulverized Coal 2024年6月3日 Hydrogen can replace partially pulverized coal in the blast furnace injection as the clean and highcalorific energy, which can reduce energy consumption and carbon emission in molten iron production In this study, a discrete phase model is used to describe the complex flow and thermochemical behavior associated with the coinjection of hydrogen and pulverized coal Numerical Simulation Study of Coinjection of Pulverized Coal 2019年2月14日 The aim of present paper is to review various aspects of pulverized coal combustion such as oxyfuel combustion, cocombustion of coal and biomass, emissions from pulverized coal furnaces, ash formation and deposition, and carbon capture and sequestration (CCS) technologies to outline the progress made in these aspectsA complete review based on various aspects of pulverized coal
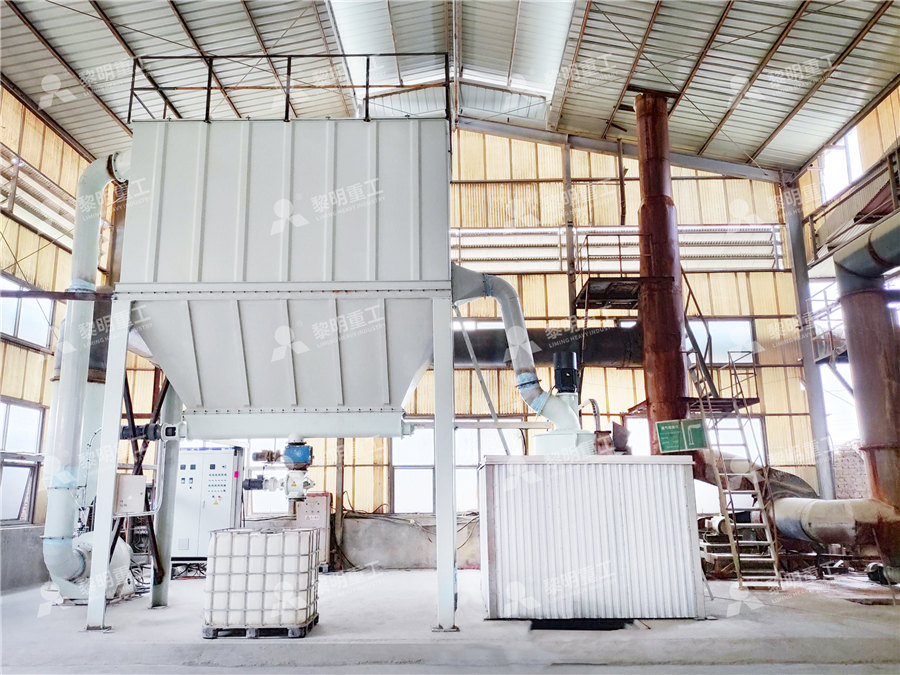
Combustion Enhancement of Pulverized Coal with
2021年2月28日 In this study, a targeted oxygenenrichment technology was proposed to enhance coal combustion in an ironmaking blast furnace The coal flow and combustion characteristics under targeted oxygenenrichment were 2019年7月15日 For the basic (reference) testcase considered in simulations (7 burners turned on, guarantee coal), standard (nominal) operating conditions at full load are defined as follows: total coal feed rate was 4243 t/h and total preheated air flow rate was 1050⋅10 3 Nm 3 /h; aircoal dust mixture temperature was 200 °C and flow rates of pulverized coal and transport fluid of Fullscale CFD investigation of gasparticle flow, interactions and 1996年10月1日 Replacement of metallurgical coke by pulverized coal (PC) injected in blast furnace (BF) tuyeres is a major economical challenge, due to the high price of coke and unfavorable effect of its Increase of Pulverized Coal Use Efficiency in Blast FurnaceAccording to the peak shape of the DTG and DSC curves, the combustion process of pulverized coal can be divided into two stages: (1) The volatile escaping and homogeneous combustion stage (260–410 °C); the organic components in coal undergo a small amount of easytobreak small molecular sidechain pyrolysis at about 320 °C, perform a fast Combustion Characteristics of Coal for Pulverized Coal
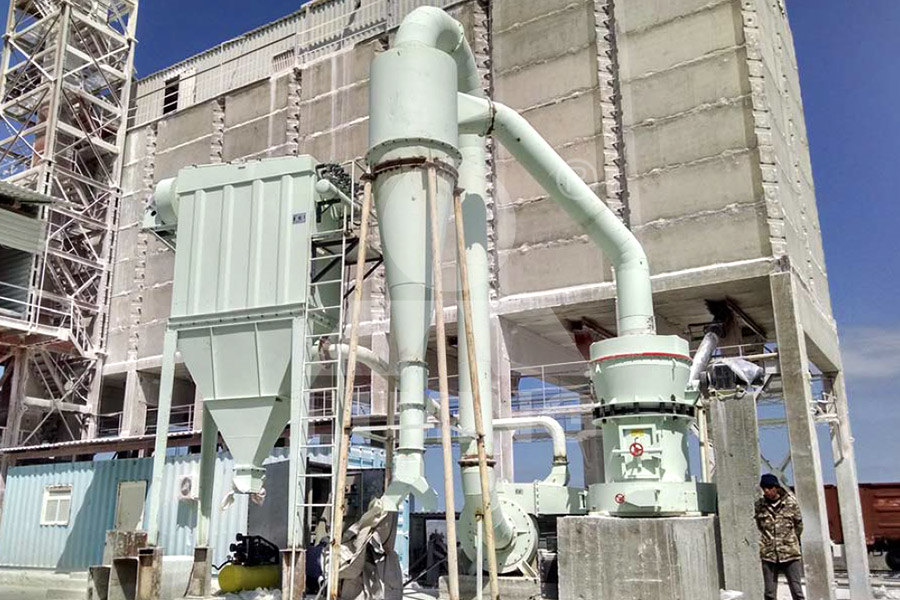
Numerical Simulation of Coal Combustion in a Tangential Pulverized
2021年4月8日 Understanding of the flow field and heat transfer in a boiler is important to meet with the oftenconflicting objectives of efficient steam generation, safe operation and minimization of pollutant emissions Steam generation requires high gas temperatures, which often lead to high NOx emissions High gas temperatures inside the boiler may also lead to slagging and fouling 2010年12月1日 The behavior of the flow of air and pulverized coal through the burners was analyzed, and the threedimensional fluegas flow through the combustion chamber and heat exchangers was reproduced in CFD Analysis of the Pulverized Coal Combustion Processes in a Zhou et al [23, 24] studied the combustion characteristics of pulverized coal by CFD method in a top gas recycling oxygen blast furnace CFD modeling of pulverized coal combustion has proven to be a reliable and efficient method In this study, a threedimensional lance–blowpipe–tuyere–raceway model was developedEffect of the Injection Angle of Reducing Gas on Coal Flow and Index Terms— Blast furnace, coal injection, feedback control, flow estimation, image analysis, soft sensor, video I INTRODUCTION IN THE blast furnace process, coke is usually used as fuel and reduction agent Since coal is 40% cheaper than coke, injecting pulverized coal instead of using coke is economically beneficial According to [1 Video monitoring of pulverized coal injection in the blast furnace
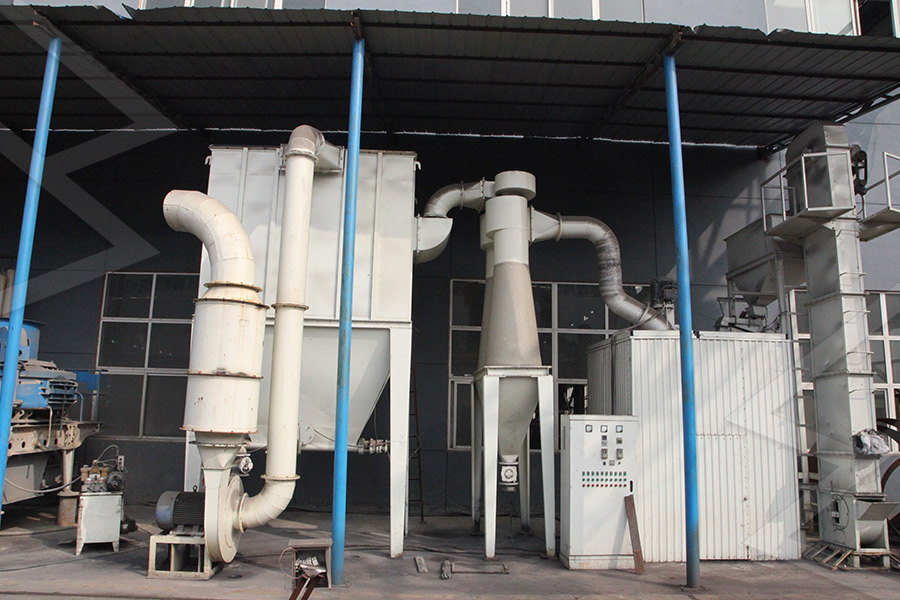
Advanced Dynamic Models for a Pulverized Coal Injection Plant
CMAX Coal injection maximum flow (50 t/h); CMIN Coal injection minimum flow (10 t/h); CREQ Required coal flow injection into blast furnace (t/h) The densities and the temperatures of coal and nitrogen and others important pneumatic conveyor variables and calculated parameters were included in order to obtain new others models2019年1月1日 Review of the investigations of pulverized coal combustion processes in large power plants in laboratory for thermal engineering and energy: Part B January 2019 Thermal Science 23(Suppl 5):16111626(PDF) Review of the investigations of pulverized coal combustion