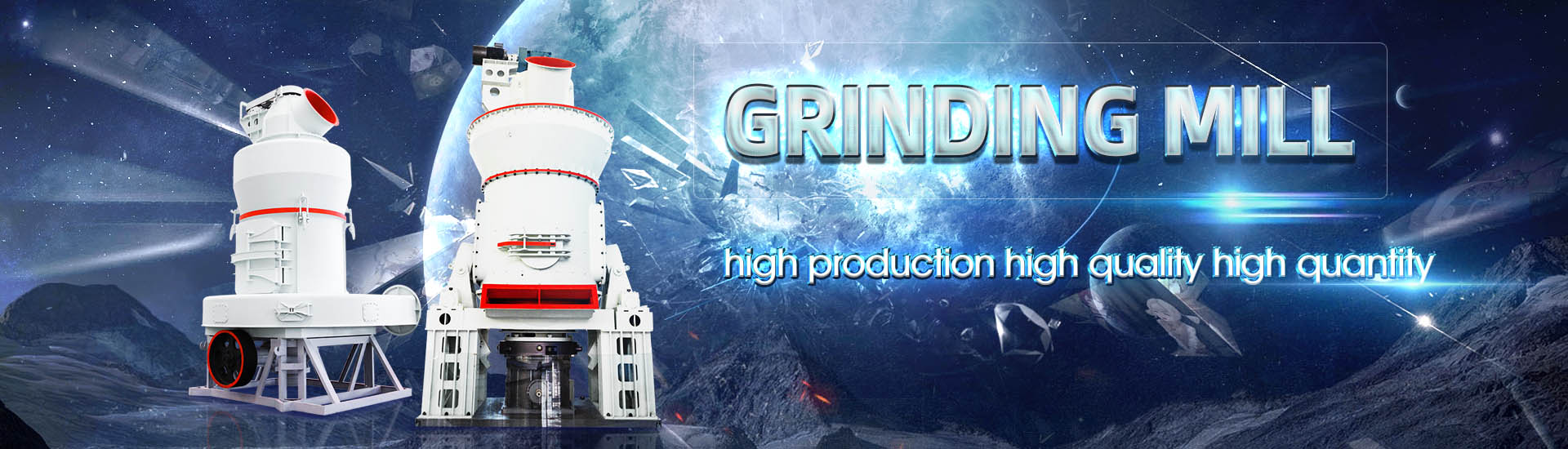
Coal mill roller sleeve Shanxi Power Plant
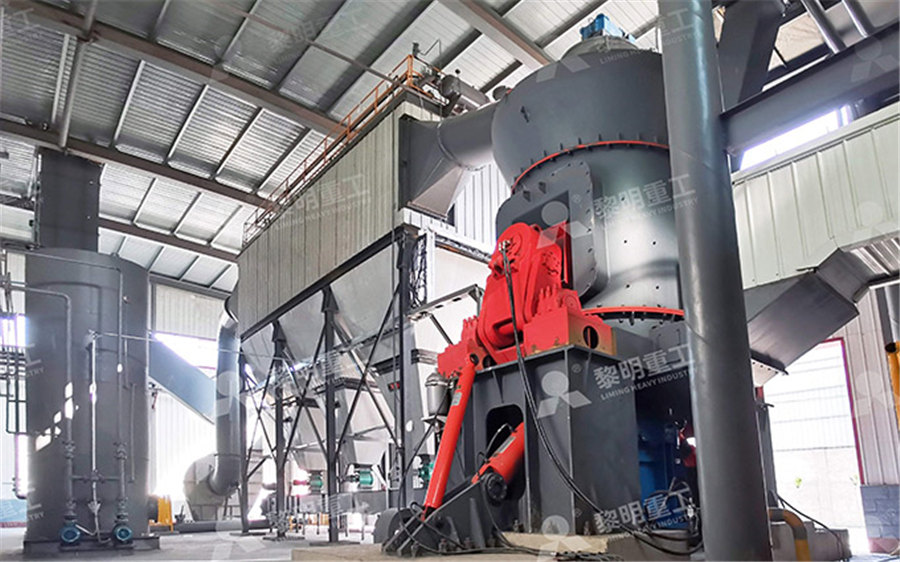
The layout of the coal mill with a rotary classifier
This study shows the performance of a currently running vertical roller coal mill (VRM) in an existing coalfired power plant In a power plant, the coal mill is the criticalIn a coalfired power plant, one of the main equipment is the coal mill, whose efectiveness influences mainly the whole power plant performance (Shah, Vuthaluru, and Vuthaluru 2009)An investigation of performance characteristics and energetic 2020年12月21日 In order to realize the monitoring of grinding roller wear state of coal mill in power plant as well as improve the reliability and safety of equipment, it is essential to build a A Wear Condition Monitoring Model of Coal Mill Grinding Roller 2019年12月12日 SEPHS is able to supply whole series of coal mills with high reliability The MGS double inlet double outlet ball mill is aimed to fit for power plant conditions from the 上海电气上重碾磨特装设备有限公司
.jpg)
Monitoring Model of Coal Mill in Power Plant Based on Big Data
Abstract: In order to monitor the wear condition of grinding roller of coal mill in power plant and improve the reliability of production equipment, it is necessary to establish a state monitoring Three dimensional (3D) computational fluid dynamics modelling was used to investigate the effect of the steepness of the classifier blade angle on the classification efficiency in Coal INVESTIGATION ON CLASSIFICATION EFFICIENCY FOR COAL 2014年3月1日 Comparing to the E ball mill of Tarong power plant in Australia, the mediumspeed mills have several significant advantages, which are widely used recently The purpose Breakage and separation mechanism of ZGM coal mill based on 2023年7月15日 To implement the target of double carbon, the Shanxi power system is changing its energy structure from heavy coal to relatively clean energy The continuous growth of VRE Multipath retrofit planning approach for coalfired power plants in
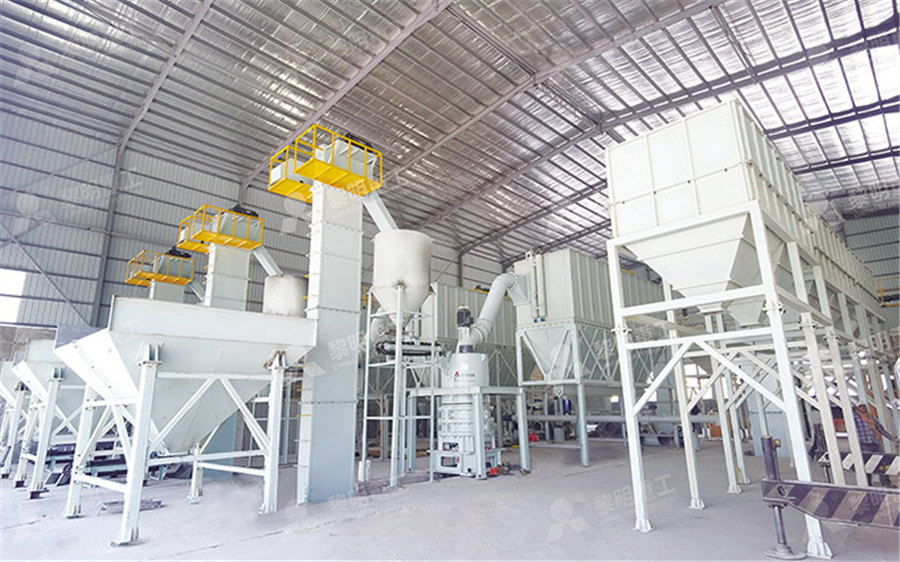
An investigation of performance characteristics and energetic
2020年8月12日 In a power plant, the coal mill is the critical equipment, whose effectiveness impacts the overall power plant efficiency Uniform coal feeding mass flow rate and required Mills are mechanical devices used to break different types of solid materials in small pieces by grinding, crushing or cutting In pulverised coalfired power plants, a pulveriser coal mill grinds Coal Mill an overview ScienceDirect Topics2020年8月12日 In a power plant, the coal mill is the critical equipment, whose effectiveness impacts the overall power plant efficiency Uniform coal feeding mass flow rate and required particle size and temperature at the outlet channel throughout with better classifier performance are crucial indicators that characterize the coal mill performanceAn investigation of performance characteristics and energetic 2020年6月29日 Grinding takes place by Impact and attrition The primary air is divided into two parts: A Bypass Air: Mixes with the raw coal and dries it before it enters the Mill It also carries the Pulverized fuel by maintaining sufficient classifications and working of mills in a power plant
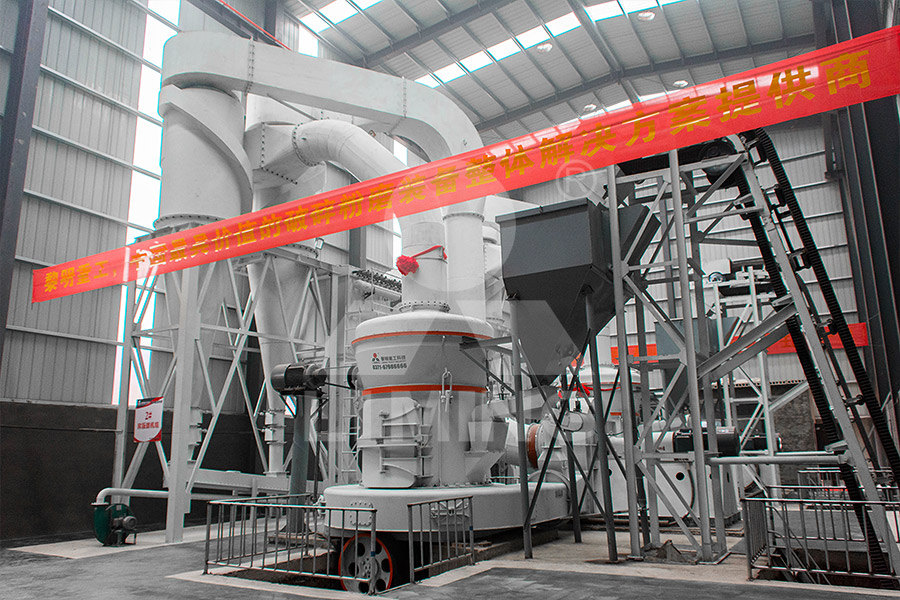
Monitoring Model of Coal Mill in Power Plant Based on Big Data
In order to monitor the wear condition of grinding roller of coal mill in power plant and improve the reliability of production equipment, it is necessary to establish a state monitoring model with high accuracy and good prediction effect It has been shown that the power of coal mill can reflect the wear degree of grinding roller If the voltage and power factor of coal mill are constant Download scientific diagram Sectional view of MBF coal mill from publication: Modeling and Parameter Identification of Coal Mill The coal mill used in the coalfired power plants is modeled Sectional view of MBF coal mill Download Scientific DiagramVertical coal grinding mill integrates crushing, drying, grinding, powder selection and conveying; It has simple system and compact structure Vertical coal mill covers an floor area about 50% of the coal ball mill with the same specification; Coal vertical mills can work in openair environments, greatly reducing the cost of investment The design of the vertical coal mill system is simple Vertical Coal Mill for Coal Grinding in Cement Plant Power PlantHequ Power Plant Coal Mill Differential Pressure Level Meter Xiaodong Gao Shenhua Guoneng Power Hequ Power Generation Co Ltd, Hequ Shanxi Received: Feb 7th, 2017; accepted: Feb 20th, 2017; published: Feb 23rd, 2017 Abstract This paper introduces the working principle of the coal mill differential pressure level DifferenHequ Power Plant Coal Mill Differential Pressure Level Meter
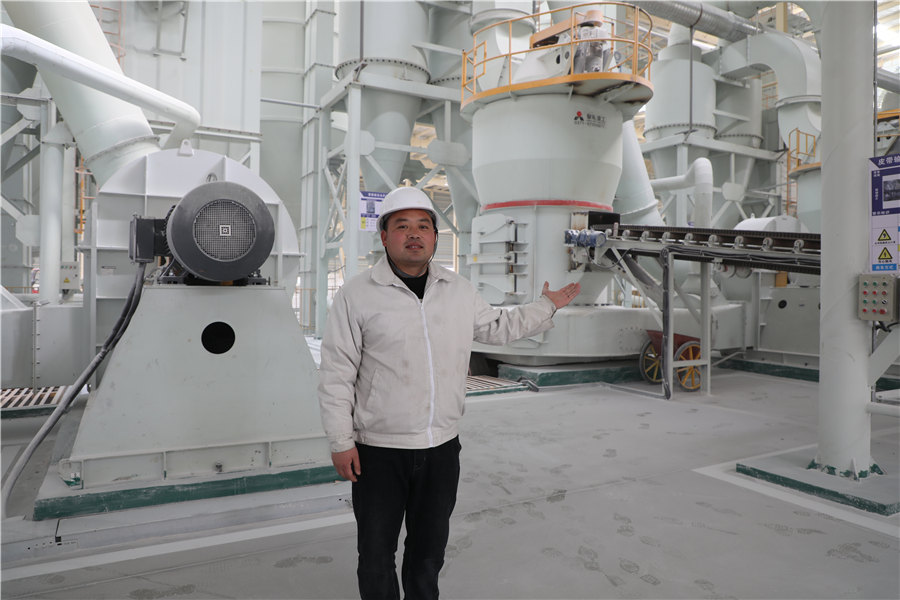
INVESTIGATION ON CLASSIFICATION EFFICIENCY FOR COALFIRED POWER PLANT
angle on the classification efficiency in CoalFired power plants The gas flow inside the coal mill was solved by the realizable k ε turbulence model (RKE) with a detailed 3D classifier geometry meanwhile the discrete phase model was used to solve the coal particles flow The steepest classifier blade angle of 40 o achievedSince the first application using an MPS mill to process pulverized coal in Germany in the mid 1960s, there have been over 2,000 different MPS mill installations operating in coalfired power plants worldwide As one of the most popular coal pulverizers in the utility industry, the MPS mill was first introduced into the US in the early 1970sCoal Pulverizer Design Upgrades to Meet the Demands of Babcock Power1990 Central coal grinding plant (LM 263 D) for gas and steam power station (coal gasification) 1992 Central coal grinding plant (LM 263 D) for the production of lignite (brown) coal dust 2002 Coal grinding plant (LM 232 D) for grinding wood pellets for power stations 2005 First 4roller pressure mill (LM 434 D) becomes available LOESCHEMILLSCoal grinding mills LOESCHE coal grinding mills are distinguished by characteristics that improve efficiency, safety and environmental protection, from the standard version to topoftherange installations Special versions are available with characteristics that meet special safety regulation or output control requirementsCoal Mills for Cement Plants Loesche
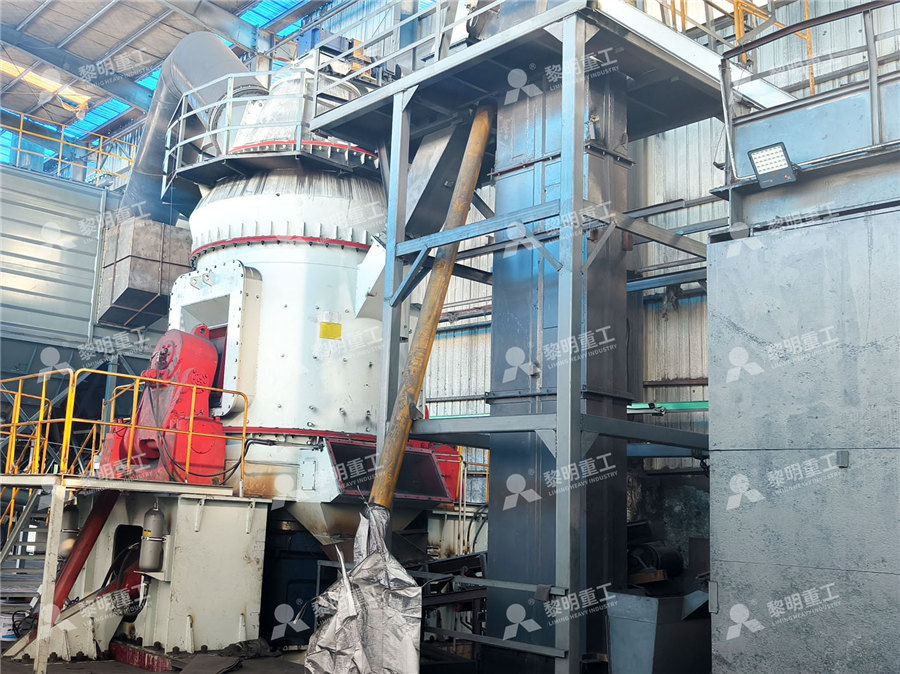
(PDF) Fault analysis and optimization technology of HP
2021年8月1日 A root cause failure analysis of coal mill vertical shaft used in thermal power plant has been carried out The failed parts of the shaft showed the signature of fatigue failuresCoal Mills are used to pulverize and dry to coal before it is blown into the power plant furnace Operation The coal is feed into the coal mill through a central inlet pipe where gravity is used to lead the coal to the bottom of the mill, where the Coal Mills SolidsWikiThe company has set up a 2 x 600 MW thermal power plant at Mutiara in the made in China: DC motor, cooling blower, coal mill spares, DP switches, lube oil filter element for turbinedriven boiler feed water pump, nozzle ring of coal mill, Power Plant Spares Dornier GroupAs the significant ancillary equipment of coalfired power plants, coal mills are the key to ensuring the steady operation of boilers In this study, a fault diagnosis model was proposed on the Technical specifications of vertical roller coal mill
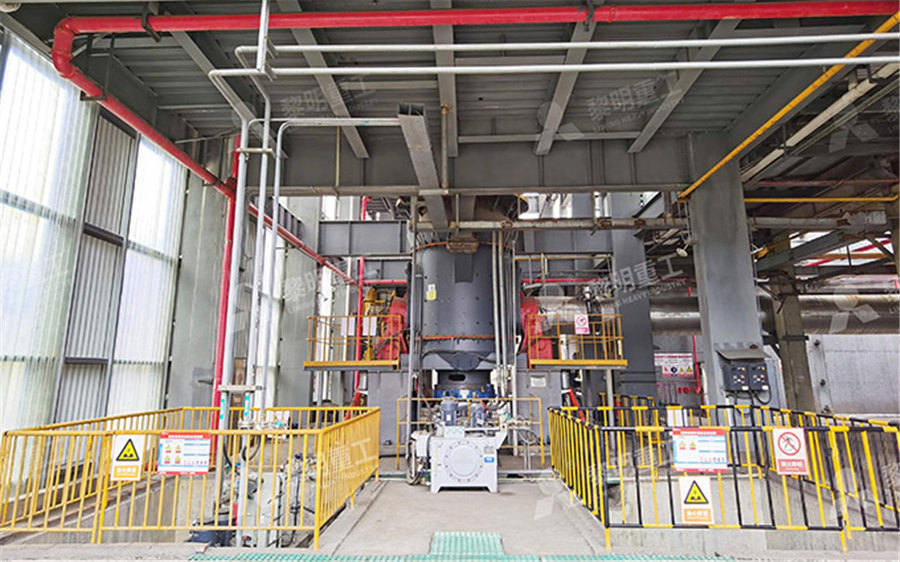
Live Working of Ball and Tube Coal Mill in Thermal Power Plant/ Coal
In this video you will get a live overview of ball and tube type coal mill used in thermal power plantVertical Roller Mill The vertical roller mill (VRM) shown in Figure 4 is an air swept, mediumspeed, vertical pulverizer with integral classifier It pulverizes coal by applying hydraulicallyloaded grinding pressure through three grin ding rollers onto a rotating bed of coal Grinding pressure can be adjusted to account for variations in coalA Comparison of Three Types of Coal Pulverizers Babcock Power2009年9月20日 The coal mill used in the coalfired power plants is modeled in view of the controller design rather than the educational simulator The coal mass flow and the outlet temperature are modeled by Modeling and Parameter Identification of Coal MillAs the significant ancillary equipment of coalfired power plants, coal mills are the key to ensuring the steady operation of boilers In this study, a fault diagnosis model was proposed on the Effect of mill outlet temperature on the coal moisture content
.jpg)
An investigation of performance characteristics and energetic
Table 1 lists technical specifications of vertical roller coal mill used in coalfired power plant The combined drying and grinding operation takes place according to the airflow principleCan GE service my boiler mills? YES Our boiler mills and coal pulverizers span the globe and are built in a variety of sizes and capacitiesWe provide customized maintenance solutions, and offer a full spectrum of highquality solutions for each—in addition to our thousands of standard boiler mill parts and boiler service solutionsThis is the Power of YesBoiler Mill and Coal Pulverizer Performance GE Steam Power2020年4月2日 Milling system in coal power plant purposely to process the raw coal to become as pulverise fuel before enter to the boiler furnace Pulverise fuel enter to the boiler furnace through pulverise Analysis of the Coal Milling Operations to the Boiler 2014年1月1日 Two mill systems are employed for most coal grinding applications in the cement industry These are, on the one hand, vertical roller mills (VRM) that have achieved a share of almost 90% and, on (PDF) MPS mills for coal grinding ResearchGate
.jpg)
Coal Conveyor in Thermal Power Plant Handing Systems
2024年6月6日 What is Coal Conveyor in Thermal Power Plant The coal conveyor in thermal power plant systems is crucial for transporting coal from storage areas to the boilers, ensuring a consistent and reliable fuel The core elements of these plants are the Loesche vertical mills for drygrinding the abovementioned grinding stock Loesche has developed and built the largest and most efficient grinding plants for its customers Loesche plants are specifically planned for the required process steps and equipped with the associated techno logy This technologyPROCESS OPTIMISATION FOR LOESCHE GRINDING PLANTSThe coal mill manufactured by the SINOMALY is made of highstrength alloy, Main Motor Power(KW) Capacity for bituminous coal(t/h) Capacity for anthracite and petrol coke(t/h) LRMC142: 110~132: 8: 55: LRMC162: 160~185: 13: 9: and the roller sleeve can be easily disassembled and removed for convenient overhaul and maintenanceCoal Mill Coal Grinding Mill Producer SINOMALYPower generation industry studies have shown that pulverized coal power plants are an area where improved equipment reliability is essential The Electric Research Institute (EPRI) has determined that 1% of plant availability is lost on average due to pulverizerrelated problemsCoal Pulverizer – Power Plant Pall Corporation
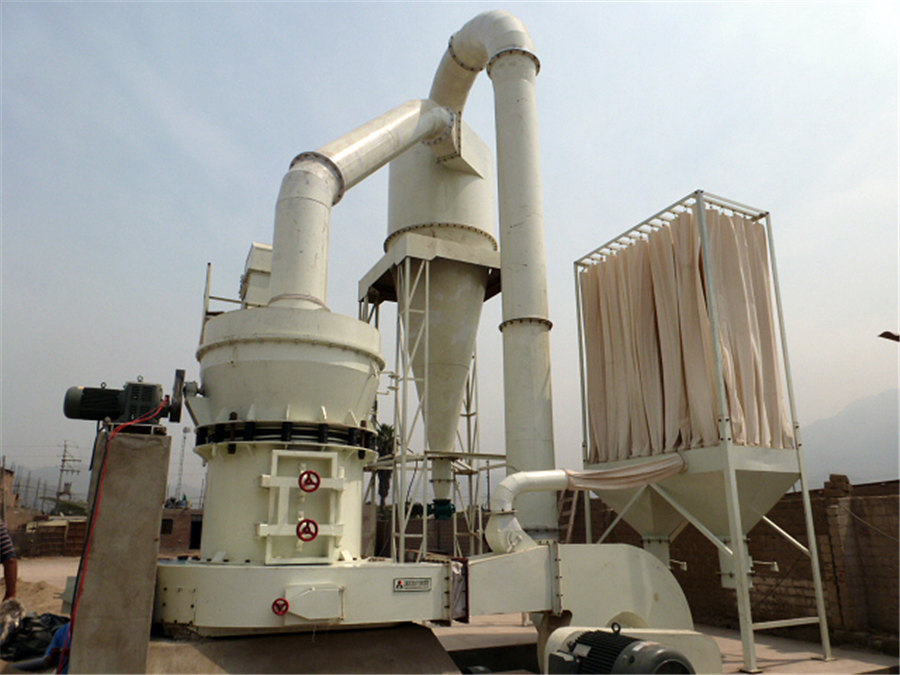
COAL PULVERIZER DESIGN UPGRADES TO MEET THE DEMANDS
Since the first application using an MPS mill to process pulverized coal in Germany in the mid 1960s, there have been over 2,000 different MPS mill installations operating in coalfired power plants worldwide As one of the most popular coal pulverizers in the utility industry, the MPS mill was first introduced into the US in the early 1970sThe coal mill under study is a vertical roller type, such as the one available at the PLTU (coalfired steam power plant) Rembang unit, which has two boilers with a steam generator capacity of 513 t/h The schematic of a coal pulverizer mill is provided in Fig 1 Details of these coal mill parameters are presented in Table 1 Coal mill modelingDecision Support System for Coal Mill Fault Diagnosis in Coal 2024年9月26日 In response, coalfired power plants proactively reduced their output to make room for renewable energy, ensuring safe and stable operation of the power grid throughout the day Shanxi, a major coalproducing province in China, has over 483 billion tons of proven coal reserves, accounting for 233 percent of the national totalCoalrich province Shanxi makes progress in energy revolution2 Steps for using coal powder for boilers 1)Coal powder preparation: Select suitable coal as raw material based on the combustion requirements and coal quality characteristics of the boiler; The raw coal is crushed into small pieces by a crusher and then sent to a coal mill for grinding to prepare coal powder that meets the requirements of boiler combustionGuilin Hongcheng HMM Series Bowl Coal Mill Promoting Efficient,
.jpg)
Multipath retrofit planning approach for coalfired power plants
2023年7月15日 Finally, based on the Shanxi Provincial power system, the roles of flexibility reformation, carbon capture utilization and storage reformation, and Carnot battery reconstruction are analysed, and coalfired power plant retrofit planning suggestions for the Shanxi power system are provided in this study2011年12月31日 Automation technologies can play a vital role in thermal power plants equipment maintenance, where coal bunker liner are critical parts in terms of functioning and safetyOperation and Maintenance of Coal Handling Shanxi Binchang Coal Power Plant is a 400MW coal fired power project It is located in Shanxi, China According to GlobalData, who tracks and profiles over 170,000 power plants worldwide, the project is currently active It has been developed in multiple phases Buy the profile herePower plant profile: Shanxi Binchang Coal Power Plant, Chinachamber Milling system in coal power plant purposely to process the raw coal to become as pulverise fuel before enter to the boiler furnace Pulverise fuel enter to the boiler furnace through pulverise coal pipe (PC) which attached to the boiler The different mill has different PC pipe corners, and withAnalysis of the Coal Milling Operations to the Boiler Parameters
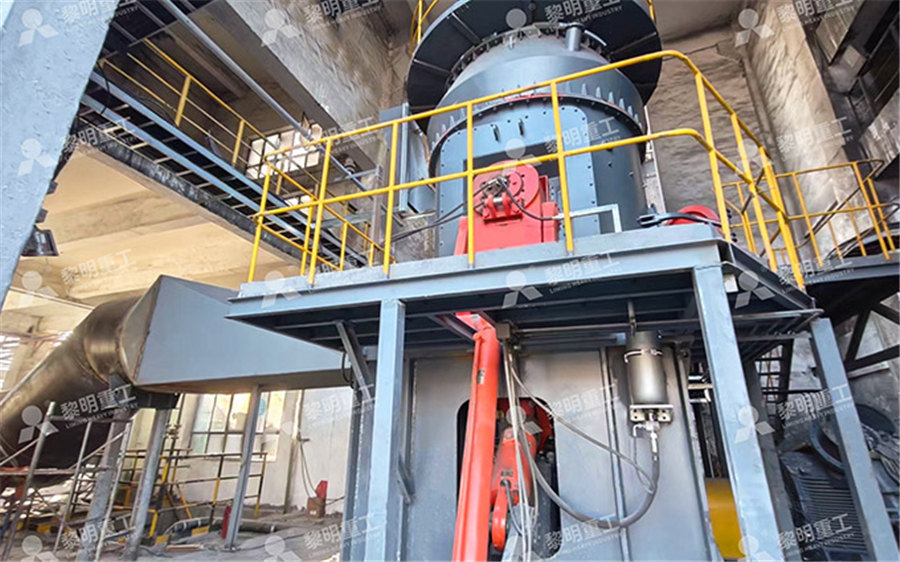
The structure of MPS mediumspeed coal mill system
Monitoring and diagnosis of coal mill systems are critical to the security operation of power plants The traditional datadriven fault diagnosis methods often result in low fault recognition rate Vertical Roller Mill 1 Rotary Lock 2 Separator 3 Chute 4 Roller 5 Swing Lever 6 Table 7 UMseries Coal Mill Models with details of structural dimension, driving power (approx Values) Roller Arrangement A B H Flow Sheet of Coal / Petcoke Grinding AMCL Machinery Limited Corporate Office: 2, Red Cross Place (HNGIL), Kolkata VERTICAL ROLLER MILLS AMCLThe pulverized coal is taken out of the mill by hot air Advantages Compared with the vertical roller mill, the advantages of airswept ball mill are strong adaptability to raw coal quality, simple operation and low investment cost; the disadvantages are high power consumption and high noise Vertical Roller Mill Vertical Roller Coal MillCoal Mill in Cement Plant Vertical Roller Mill AirSwept Ball MillWyoming Hanna Basin coal, Rosebud seam, having a heating value 913% below that of the original coal; analysis is shown in Figure 2 This fuel change did not affect Unit 5's load carrying capability Then during 198384, OPP D began procurement of a significantly lower cost Wyoming Powder River Basin coal for their two coalfired plants This coal,WorldProven Coal Pulverizer Technology Debuts in the US Babcock Power
.jpg)
Coal Mill In Cement Plant
Airswept coal mill is the main equipment of cement plant, also called coal mill in cement plant, used for grinding and drying various hardness of coal, crushing the coal briquette into pulverized coalIt is the important auxiliary equipment of pulverized coal furnace The airswept coal mill runs reliably, can work continuously, also has a large production capacity and less energy of mill systems, since the steam inerting principle is the same and inerting system requirements are similar, regardless of different mill types INTRODUCTION In a coalfired power plant, the coal pulverizer is critical for fuel processing It is important to operate theMill Steam Inerting System Review and Performance Validation