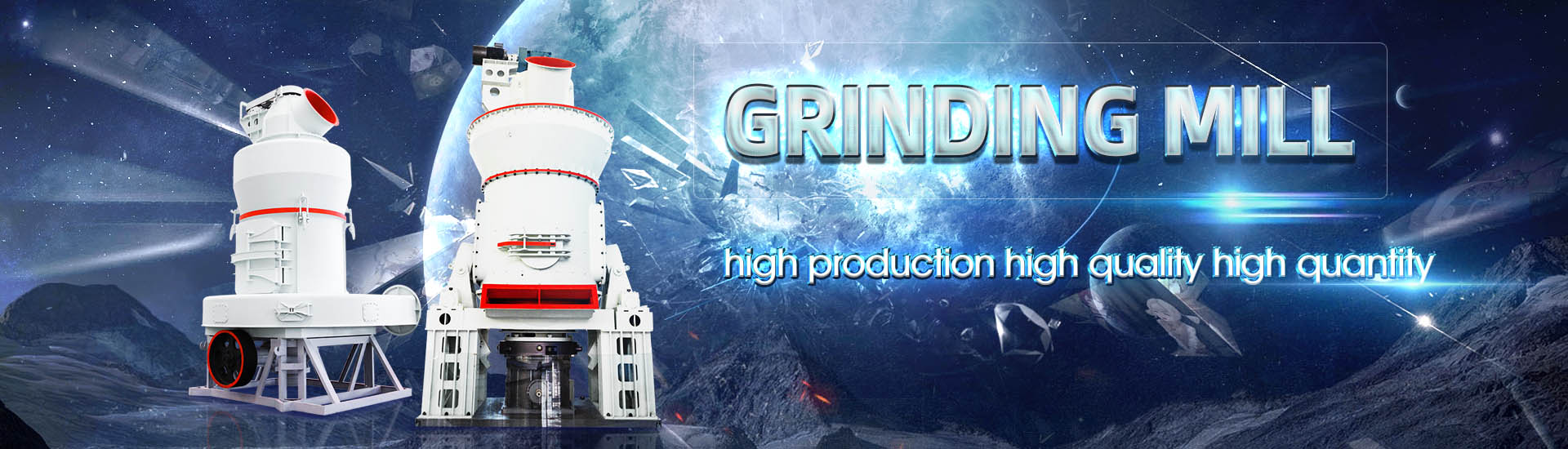
3200t cement grinding mill selection
.jpg)
Thomas Holzinger, Holzinger Consulting, grinding system
Cement grinding In Table 1, three common cement grinding systems are compared on their electrical consumption for a typical 3500 Blaine ordinary portland cement (OPC) Roller press Grinding of cement clinker and granulated blast furnace slag in roller grinding mills (vertical airswept grinding mills) is a technology introduced by Loesche The first use of a Loesche mill, 2 µm 5 µm LoescheVertical Roller Mills (VRM) have a clearly higher energy eficiency than ball mills, even if the ball mill is combined with a roller press This and further arguments led to the increased share of SikaGrind® for vertical roller millscommon solution to grind raw materials and cement Roller presses are used mainly in combination with a ball mill for cement grinding applications and as finished product grinding BALL MILLS Ball mill optimisation Holzinger Consulting
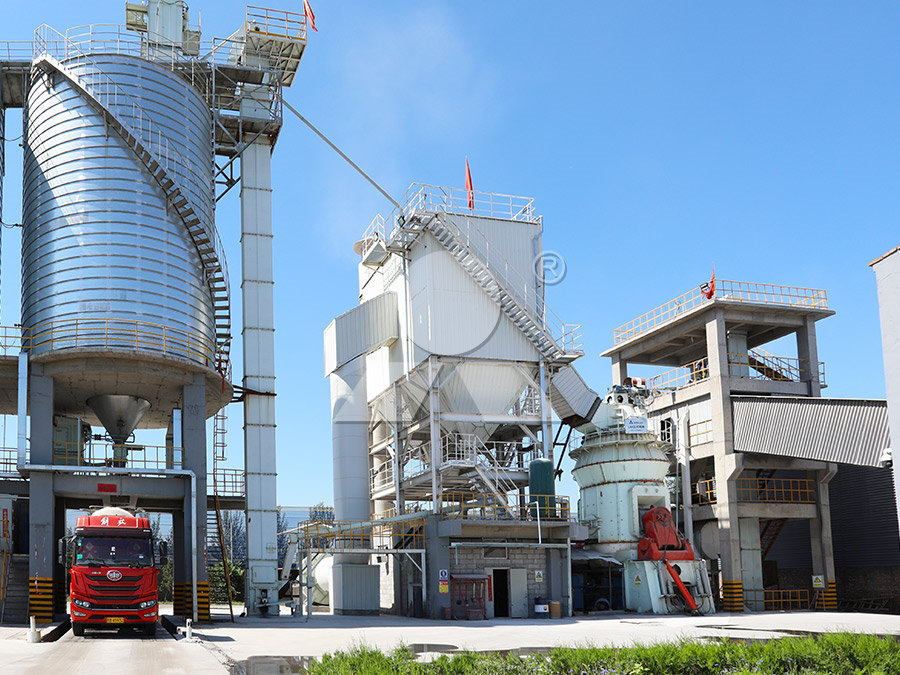
GRINDING OPTIMISATION Adapting to the market
The selection of suitable grinding systems is an important part of ensuring the competitiveness of a cement producer and its ability to rapidly respond to market requirements2021年1月1日 With the grinding capacity of a vertical roller mill and the ability to dry, grind and sort in a single unit, the vertical roller mill offers a definite advantage over the ball mill system Review on vertical roller mill in cement industry its performance Several energy efficient options for cement grinding are available today such as vertical roller mills, roller presses (typically in combination with a ball mill), and clinker pregrinder s with ballOPTIMIZATION OF CEMENT GRINDING OPERATION IN BALL MILLSCompact and easy to install, the FCB Horomill® offers process specificities that are ideal for modern cement plants Thanks to its advanced technology and its use in combination with the Fives Sustainable grinding with FCB Horomill®
.jpg)
Everything you need to know about clinker/cement
For a cement mill: intermediate or outlet diaphragm For the case of; cement mills with a drying chamber see raw mills Mill working conditions: ventilation air speed through the mill Bigger or smaller than 12 [m/s] Material abrasivity The [%] 6 Cement Production Technology –Cement Grinding –Mechanical Design and Function of Separator Separators –General Classification of Separating Principles •according to flow direction relative to particle track •according to kind of separating field separation by gravitational force separation by centrifugal forceCement Grinding myPolysiusService2017年10月26日 The following are factors that have been investigated and applied in conventional ball milling in order to maximize grinding efficiency: a) Mill Geometry and Speed – Bond (1954) observed grinding efficiency to be a Factors Affecting Ball Mill Grinding EfficiencyAGICO Cement Vertical Mill AGICO Cement Ball Mill Cement Vertical Mill Grinding System Cement vertical mill, also called roller mill, is another raw mill commonly used in cement pared with the cement ball mill, it has a great difference in structure, grinding principle, process layout, automatic control, and energy consumption, which play an important role in the Raw Mill – Raw Mill In Cement Plant AGICO Cement Raw Mill
36.jpg)
Cement Grinding Plant Expert Cement Grinding Solutions from
Part of the materials return to the roller press for regrinding, and the qualified materials enter the cement mill for further grinding Therefore, the selection of appropriate grinding systems and grinding equipment is very important to produce high SINOMALY produces cement raw material grinding mills in various specifications These machines are suitable for grinding mill production lines with an output of 2500t/d, 3200t/d, 4000t/d, 5000t/d, 6000t/d and 8000t/d The vertical grinding mill is utilized for the grinding of raw materials, mixed cement, and slag powderSupply Vertical Roller Mill Customized Factory SINOMALY Heavy 2023年4月23日 Proper selection of High mill filling reduces the grinding rate because the collision zone on the energy efficiency of cement finish grinding in a dry batch ball mill(PDF) Grinding Media in Ball MillsA Review ResearchGate2022年8月10日 ICR gets Vimal Jain, Director – Technical, HeidelbergCement India, to share his views about the innovations in technology of the grinding process and grinding aids as well as his understanding on how the entire process can be made more energyefficient and costeffective Explain the grinding process in cement manufacturingThe grinding process is needed to Efficient grinding unit selection impacts profitability Indian Cement
.jpg)
(PDF) Cement grinding optimisation Alex Jankovic
CEMENT GRINDING OPTIMISATION Dr Alex Jankovic, Metso Minerals Process Technology AsiaPacific, Brisbane , Australia email: alexjankovic@metso Dr Walter Valery, Metso Minerals Process Technology AsiaPacific, Brisbane, Australia Eugene Davis, Metso Minerals AsiaPacific, Perth, Australia ABSTRACT The current world consumption of cement is about The cement mill produced by AGICO can be divided into the raw mill, cement grinding mill and coal mill Skip to content Blog Contact About Cases Factory CONTACT US info@cementplantequipment CALL US +86 REQUEST A QUOTE Just ask! Menu Cement Plant Solutions Cement Production Line;Cement Mill Cement Grinding Machine AGICO Cement Grinding Mill1995年10月29日 The tube mill is still the most common machine in the cement industry for grinding clinker Large scale production upgrades of tube mills have been available since 1990, when the roller press has (PDF) Cement mill optimization: Design parameters 2015年1月31日 From hubandspoke model to split grinding; from singlegrinding solution to a combination of system solutions; and from energyintensive traditional ball mill to upgraded versions and use of pregrinders, the cement Grinding Solutions Indian Cement Review
.jpg)
Clinker grinding technology in cement manufacturing
2019年1月3日 Clinker grinding technology is the most energyintensive process in cement manufacturing Traditionally, it was treated as "low on technology" and "high on energy" as grinding circuits use more than 60 per cent of total energy 2021年6月10日 This study investigated a mathematical model for an industrialscale vertical roller mill(VRM) at the Ilam Cement Plant in Iran The model was calibrated using the initial survey's data, and the Ventilation Prediction for an Industrial Cement Raw Ball Mill by The use of advanced grinding media and liners is crucial for achieving highcapacity cement grinding Optimized media selection and wearresistant liners help in: Increasing Grinding reducing variations in mill performance Efficient Conveying Systems: Highspeed conveyors and advanced loaders minimize delays in material transportation HighCapacity Cement Grinding Solutions: Enhancing Efficiency The installation of liners Length Diameter Ratio The lengthdiameter ratio of the cement ball mill is relatively large For mills of opencircuit grinding system, the lengthdiameter ratio is usually between 35 and 6 to ensure that the product fineness is qualified through single grinding; For ball mills in closedcircuit grind system, in order to increase the material flow rate, the length Cement Ball Mill Cost Effective Cement Grinding Mill from AGICO
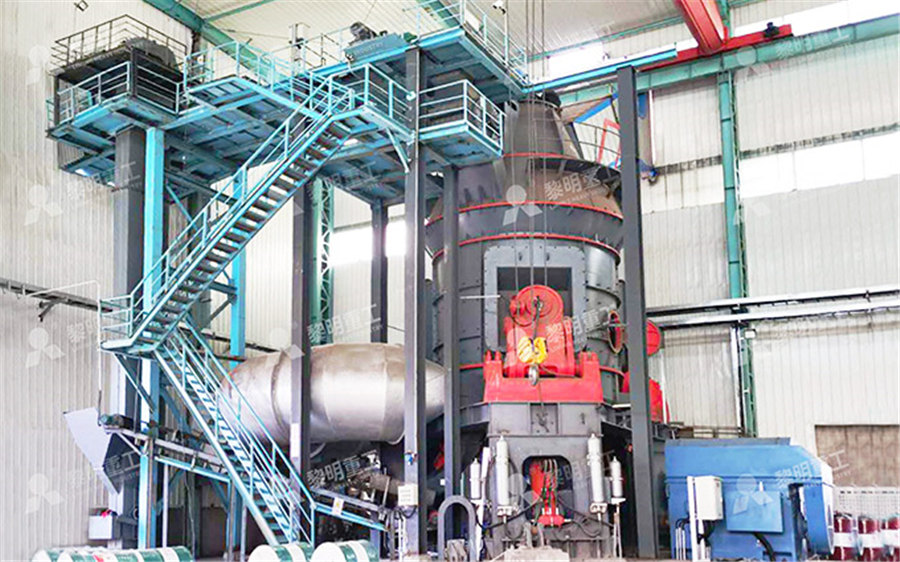
THYSSENKRUPP Optimized Crusher Selection For The Cement
The document discusses selecting the optimal crusher for cement production based on characteristics of raw materials like hardness, abrasiveness, and moisture content It provides an overview of different crusher types (eg hammer, impact, roll) and their specifications regarding crushing ratio, strength of materials they can handle, silica and moisture limits Impact 2021年4月29日 Metso Outotec unveiled horizontal mill product lines that represent the best of both legacy Metso and Outotec companies: Premier and Select “With the introduction of the Premier and Select horizontal grinding mills, Metso Outotec continues its more than 100year legacy in grindingMetso Outotec Launches Two Horizontal Grinding Mill LinesThere is no doubt that cement grinding mill and cement roller press are the core equipment of cement grinding unit Cement grinding machine selection will directly decide the quality and cost of whole cement grinding unknit According to the real cement projects, there are three common solutions for cement grinding plantCement Grinding Plant Overview Cement Grinding Unit AGICO Cement2023年10月23日 In this study we compare the effects of three different grinding aids on clinker grinding using a ball mill A commercial grinding additive, triethanolamine (TEA), and two industrial grinding aids (PDF) A study of different grinding aids for lowenergy cement
制粉项目-2023.11.17.jpg)
(PDF) Intensifying the cement grinding process
2023年7月19日 A A Stronin, Grinding of cement clinker in ball mill using dense ball packing and grinding intensifier, in Proceedings of the Conference "Youth and Scientific and Technological Progress", BSTU o Finished grinding may consume 25 – 50 kWh/t cement, depending on the feed material grindability, additives used, plant design especially the required cement fineness Cement grinding is the single biggest consumer of electricity Improvements in New Existing Cement Grinding power consumption [1, 34, 36] Optimization of cement grinding using standard bond grinding calculations based on population balance models is successfully applied [4, 38] Various grinding laws, energy relationships, control factors and controller design for cement grinding are discussed in [37] Figure1 Vertical roller mill for cement PROCESS CONTROL FOR CEMENT GRINDING IN VERTICAL ROLLER MILL When dry grinding cement raw material, a protective coating of ground material covers the mill liners and grinding balls It is known that cement raw material is much less abrasive than cement clinker The wear of raw mill liners does not present an urgent financial problem, because extension of their lifetime is of insignificant influence on Grinding ball data INFINITY FOR CEMENT EQUIPMENT
.jpg)
Overview of cement grinding: fundamentals, additives, technologies
2017年5月19日 Grinding is an essential operation in cement production given that it permits to obtain fine powder which reacts quickly with water, sets in few hours and hardens over a period of weeks i 2017年10月12日 Some investigations observed that VRM installation in grinding saves 30% of cement mill energy with ease of control and reduces the mill startup/shut down durations [1,2,3,4, 5] Predictive Control of a Closed Grinding Circuit System in Cement Ball mill for cement grinding is a kind of important cement equipment in cement plants The JD series cyclone air separator is a new type of highefficiency cement separator Its powder selection efficiency is more than 80%, with small size, Ball Mill For Cement Grinding – Cement Ball Mill Ball Mill 2023年9月19日 Limestone grinding mill Material: Limestone Finished product particle size: 01730044mm Processing capacity: 8176t/shift Applicable materials: calcium carbonate crushing processing, gypsum powder processing, power plant desulfurization, nonmetallic ore pulverizing, coal powder preparation, etc Main limestone grinding machines Vertical roller Limestone Grinding Mill That You Need To Know Mortar Plant
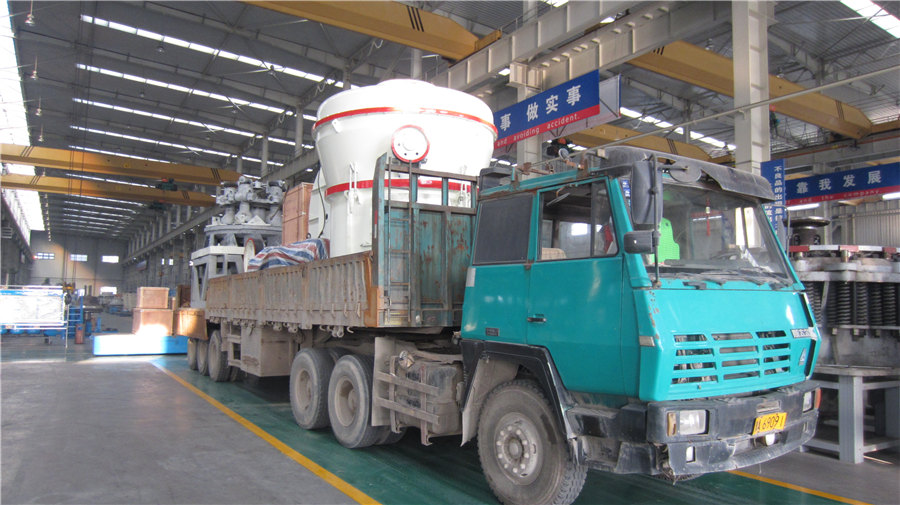
Fosroc Grinding Aids Performance Enhancers: CEMAX Technology
FosrocCemaxBrochure Free download as PDF File (pdf), Text File (txt) or read online for free Fosroc produces grinding aids and performance enhancers under the Cemax brand to improve cement production efficiency and cement quality Cemax products work to reduce agglomeration during cement grinding, increase mill output, and improve cement flowability and strengthChemical process industries are running under severe constraints, and it is essential to maintain the endproduct quality under disturbances Maintaining the product quality in the cement grinding process in the presence of clinker heterogeneity is a challenging task The model predictive controller (MPC) poses a viable solution to handle the variability This paper addresses the Predictive Controller Design for a Cement Ball Mill Grinding Highquality cement vertical roller mill manufacturer Tongli ZJTL series cement vertical mill is a very important link in cement production and is the best choice for raw material grinding and clinker grinding As an iterative product of the ball mill, the vertical mill occupies a small area, which is about 50% less than the ball millCement Vertical Roller Mill CEMENTLCement Grinding Systems Free download as PDF File (pdf), Text File (txt) or read online for free The document discusses different cement grinding systems It describes three main groups: tube mill only systems, tube mill with Cement Grinding Systems PDF Mill (Grinding)
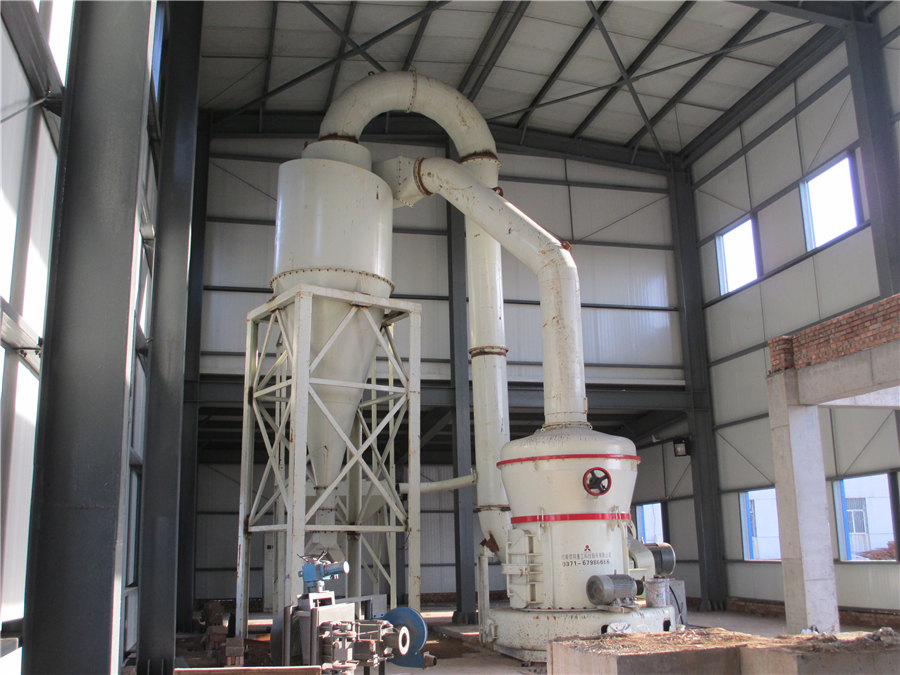
Polysius Roller Mills For grinding
uses the testroller mill Atrol (throughput approx 240 kg/h) for grindability testing and quantitative prediction of wear in industrial mills Roller mill for granulated blast furnace slag grinding in China Roller mill for cement raw material grinding in China Roller mill for cement clinker grinding in Mexico Coal grinding plant in PolandCondition in one of the grinding chambers of the mill Results of Optimization The graphical analysis presented in Figure 2 represents progress of grinding along the length of the mill after optimizing the grinding process rogress of grinding is clearly visible in Desired p the graphs Figure 2: Analysis of longitudinal samplesOPTIMIZATION OF CEMENT GRINDING OPERATION IN BALL MILLS2012年6月1日 ball mill grinding process should normally ta ke into account certain economic value Mill – Cement and Concrete Research, V ol 33, The Selection and Design of Mill Lin ers – In: Grinding in Ball Mills: Modeling and Process ControlComparison of cement grinding systems for ordinary portland cement at 3500 Blaine, 4% limestone Ball mill Combi grinding system Finish grinding Ball mill with cage rotor separator Roller press in semifinish mode and ball mill VRM Roller press Specel Energy consumption mill motors kWh/t 30 25 17 17 % at mill motor (ball mill 100%) % 100 83 57 57Thomas Holzinger, Holzinger Consulting, grinding system

Grinding Mills and Pulverizers Selection Guide: Types, Features
Video credit: shsbjq / CC BYSA 40 Specifications Important specifications when selecting grinding mills and pulverizers include, The size of the mill can range from pilot/lab to production, eg, 35 to 1600 cu ft; Feed size, material, and hardness of feed must be considered; Output size ranges; Mills can handle dry or wet input, or both; Mills operate in batches or continuously2021年6月29日 Nowadays, ball mills are widely used in cement plants to grind clinker and gypsum to produce cement The research focuses on the mill speed as well as air classifier speed effect on the two Effects of Mill Speed and Air Classifier Speed on Performance of Lower cement grinding energ y consumption While many efforts have concerned the kiln and fuels, optimisation of grinding can also play a significant role in cutting CO 2 Energy consumption can be reduced by mill system design and optimisation, selection of cement grade and by improving grindabilityReducing CO2 emissions through cement grinding optimisation2018年7月1日 Among the industries, the nonmetallic industry was reported as the third largest energy user and accounted for about 12% of the global energy use [1]Within this portion, cement industry had the majority of the utilization with 85–12% [1], [2]US Energy Information Administration (EIA) [7] named cement industry as the most energy intensive among the Energy and cement quality optimization of a cement grinding circuit