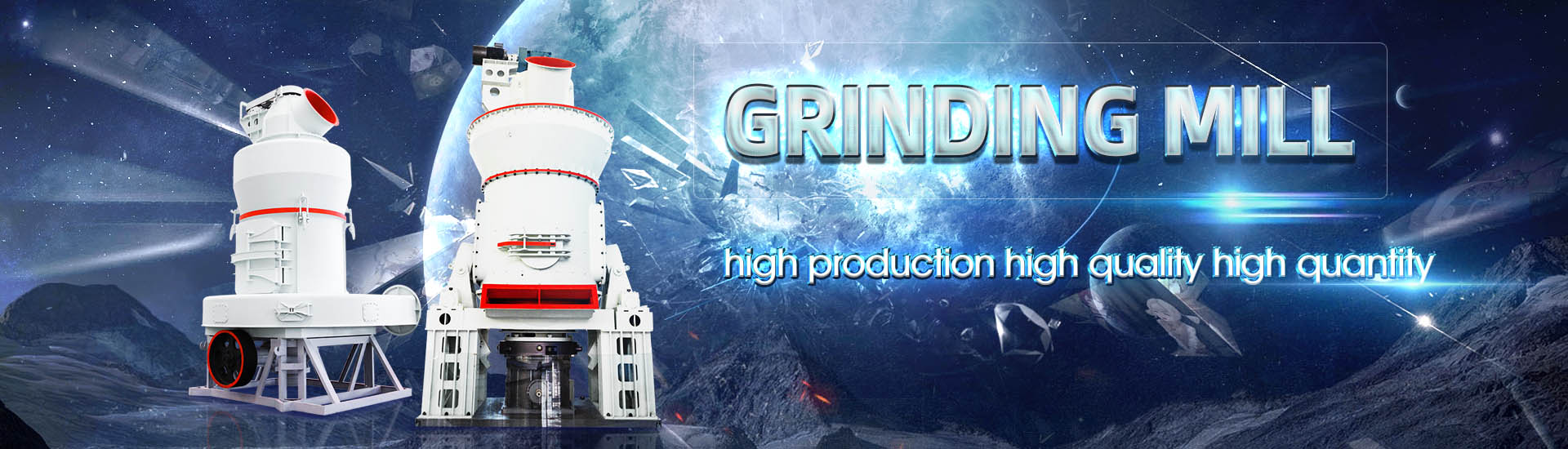
Zinc slag mill
.jpg)
Recovery of Zinc and Iron from Steel Mill Dust—An Overview of
The leaching slag cannot be reused in a steel mill due to its high residual content of zinc The alkali fusion–alkali leaching method can convert ZnFe 2 O 4 into ZnO, Na 2 ZnO 2 and Fe 2 O 2013年9月10日 In the present paper, results of a systematic study on the effect of milling environment (air and CO 2) on the reactivity of milled zinc slag and on properties of Utilization of zinc slag through geopolymerization: Influence of 2020年8月14日 This paper highlights environmentally friendly utilisation of solid wastes like lead–zinc mill tailings and lead–zinc smelter fuming furnace slag (FFS) as paste backfilling for an underground metalliferous mineUtilisation of lead–zinc mill tailings and slag as paste Metallurgical slag and dust (MSD) from lead and zinc smelting, steel dust and galvanized steel scrap are important secondary sources of zinc and other valuable metals This paper describes the production feasibility and rationality Zinc recovery from metallurgical slag and dust by
.jpg)
Recovery of Zinc and Iron from Steel Mill Dust—An
2022年6月10日 The leaching slag cannot be reused in a steel mill due to its high residual content of zinc The alkali fusion–alkali leaching method can convert ZnFe 2 O 4 into ZnO, Na 2 ZnO 2 and Fe 2 O 3 through the alkali fusion 2023年7月3日 Therefore, the formation process, fundamental characteristics, and current extraction process of Zn from zincbearing dust, associated with thermodynamics and kinetics Research status and development of extraction process of zinc 2020年1月25日 Generated by the pyrometallurgical process, zinc smelting slag contains a high content of zinc , lead , and cobalt as secondary resource And zinc leach residue, generated in A Critical Review on Generation, Characteristics, and Utilization of 2021年11月22日 Critical review on utilising mill tailings, fly ash and slag in mine paste backfilling Explains strength prediction using statistical and artificial intelligence techniques Utilization of mill tailings, fly ash and slag as mine paste backfill
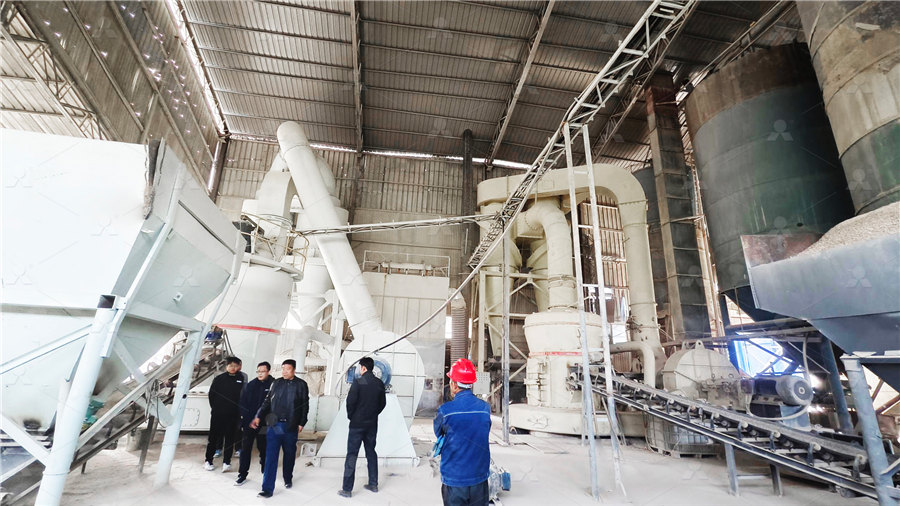
Slag Wikipedia
Slag from steel mills in ferrous smelting is designed to minimize iron loss, which gives out the significant amount of iron, following by oxides of calcium, silicon, magnesium, and aluminium2019年4月5日 In the future, RecoDust in combination with dry slag granulation will become an efficient technique for processing lower zinccontaining materials of a steel mill A challenging area in the field of RecoDust is the RecoDust—An Efficient Way of Processing Steel 2021年11月22日 Leadzinc slag: Glassy state without any visible crystalline phases: Ozturk and Gultekin [112], and reported marginal improvement in strength after replacing OPC by 50% of FA Similarly, He et al [167] used lead–zinc mill tailings for paste backfill and UCS increased by 40% with the replacement of OPC (10 wt% group) by FA (up Utilization of mill tailings, fly ash and slag as mine paste backfill Utilisation of leadzinc mill tailings and slag as paste backfill materialsUtilisation of leadzinc mill tailings and slag as paste backfill
.jpg)
Zinc recovery from metallurgical slag and dust by coordination
1 Introduction Currently, the main source of zinc metal is the traditional zinc resource—zinc sulfide ores However, as the zinc consumption increases and the zinc sulfide ore grades deteriorate, the gap between supply and demand has become a major problem for the zinc industry [1,2]At the same time, large quantities of metallurgical slag and dust (MSD) are zinc contents in the dust but also by too high zinc levels above 30 % for several reasons, such values are welcome for the described concept what is an important advantage Investigations concerning slag optimization In Figures 4 to 6, two developed scenarios for the treatment of steel mill dusts from electric arcRecovery of Zinc and Iron from Steel Mill Dusts by the useRecently, there is an increasing interest in use of zinc slagcontaining materials as partial substitutes for sand in road materials Grinding and magnetic separation of the prepared samples were performed using a laboratory ball mill and a drum magnetic separator designed and assembled by Technical Center of EkoLab (Poland)Selective Recovery of Zinc from Metallurgical Waste Materials Then in 1948, the Smog disaster occurred, marking the beginning of the end of the mill While the Zinc Works created an abundance of prosperity for the town, it would prove to be its Achilles heel Slag is a byproduct of the steel making process and getting rid of it is a constant issueDonora Historical Society and Smog Museum Steel Mill and Zinc
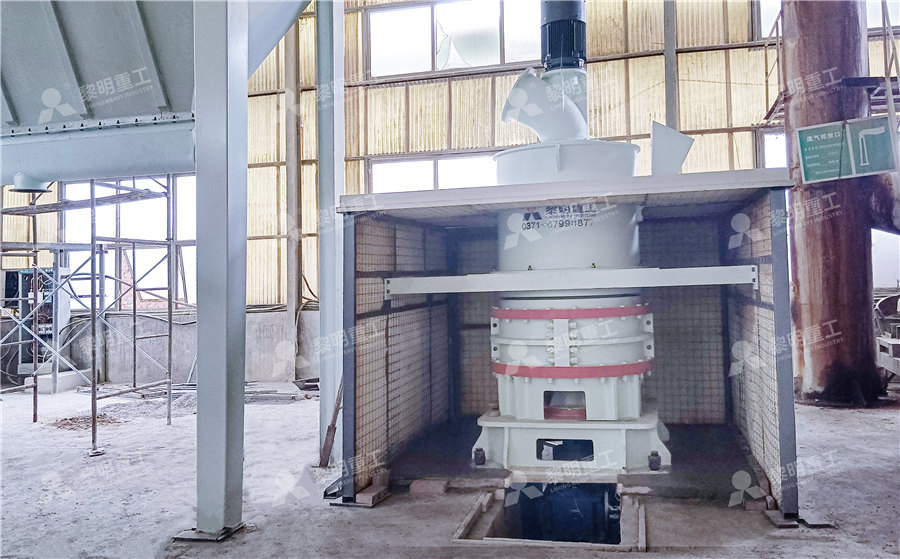
Characterization of lead–zinc mill tailings, fly ash and their
2019年7月10日 Request PDF Characterization of lead–zinc mill tailings, The physicochemical properties of both the lead–zinc mill tailings and fuming furnace slag (FFS) have been examined2021年1月4日 Li and Yao12 found that mechanical activation with a stirring mill can enhance the leaching of indium from zinc slag with hydrochloric acid The atmospheric pressure sulfuric acid leaching of zinc, indium, and germanium from zinc slag, which is a conventional twostage leaching process, involves leaching with a lowconcentration final acid and subsequent Recovery of Indium from Hard Zinc Slag by Pressure Leaching and 2007年3月1日 Integrated steel plants utilize mostly five materials such as raw materials, air, water, fuel and power to produce steel During the production of steel, 2–4 t of wastes are being generated per tonne of steel producedThe various solid wastes in the form of slags and sludges that are emerged from steel plants are blast furnace slag, blast furnace flue dust and sludge, An overview of utilization of slag and sludge from steel industriesExtracting zinc from steel mill dust and finding uses for the resulting slag is only part of the story how Rönnskär contributes to a circular economy The smelter finds uses for a variety of other societal endoflife materials, which also helps Extracting zinc through steel mill dust recycling at
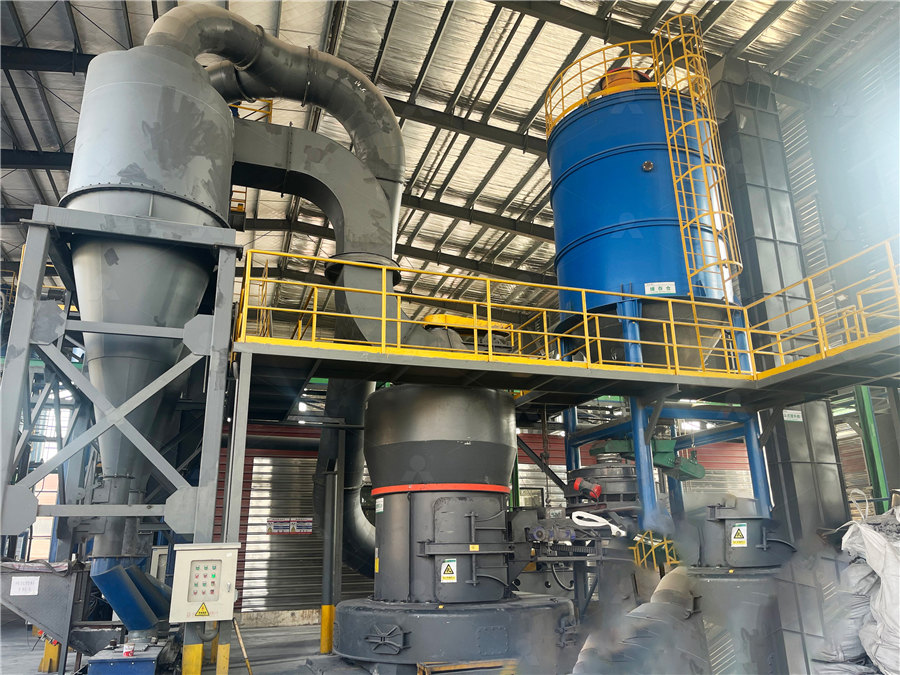
Tensile strength of cemented paste backfill for lead–zinc mill
2023年7月4日 Paste backfill preparation Cylindrical paste backfill samples were prepared in the lab with a targeted 28day UCS of 1100 kPa The ingredients of paste were lead–zinc mill tailings, OPC, fly ash (FA) or lead–zinc smelter fuming furnace slag (FFS), or crushed fuming furnace slag (CFFS) as partial OPC replacementsThe leaching slag cannot be reused in a steel mill due to its high residual content of zinc The alkali fusion–alkali leaching method can convert ZnFe 2 O 4 into ZnO, Na 2 ZnO 2 and Fe 2 O 3 through the alkali fusion process, and then zinc in the ZnO and Na 2 ZnO 2 can be leached out by the alkali leaching method, so as to achieve efficient and selective leaching of zincRecovery of Zinc and Iron from Steel Mill Dust—An Overview of 2020年1月25日 Zinc smelting slag is generated by the zinc pyrometallurgical process In general, total contents of zinc and lead of the zinc smelting slag are about 5–15%, while the contents of rare and noble metals are very low []Therefore, it is not economic for the recovery of valuable metals from the zinc smelting slag by the traditional hydrometallurgical processes A Critical Review on Generation, Characteristics, and Utilization of MSDS: Slag Page 3 of 6 Revised: 03/01/14 Section 4: FIRST AID MEASURES Eye Contact: Rinse eyes thoroughly with water for at least 15 minutes, including under lids, to remove all particles Seek medical attention for abrasions Skin Contact: Wash with cool water and a pH neutral soap or a mild skin detergent Seek medicalMSDS: Slag Material Safety Data Sheet
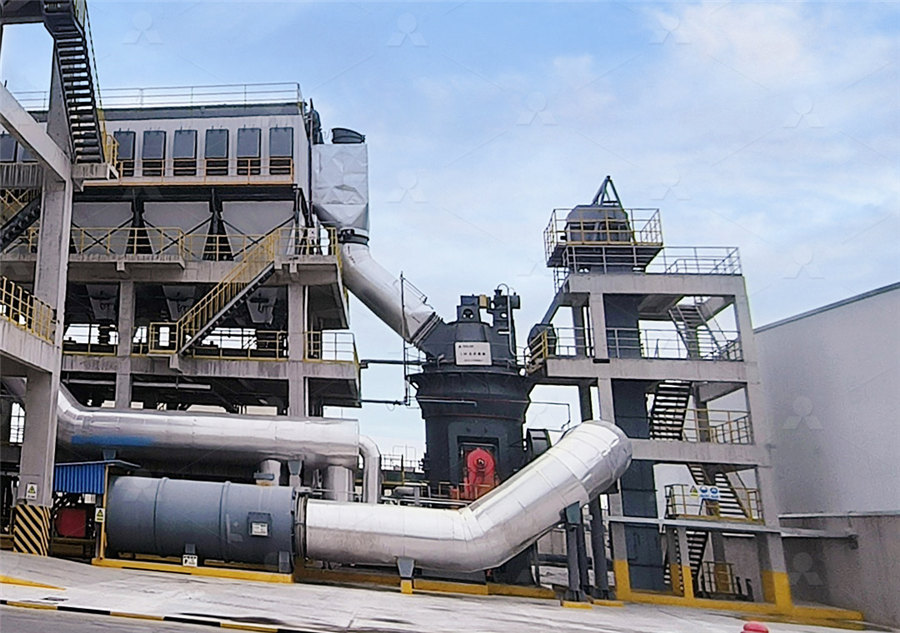
Slag Grinding Plant GGBS Plant Slag Mill, Slag Grinding Mill
The complete set of equipment is mainly composed of jaw crusher, bucket elevator, cement silo, vibrating feeder, slag mill, fan, powder collector, bag filter, etc 1 Crushing equipment 800tpd Zinc Oxide Rotary Kiln Project In Shandong; CONTACT US +86 s USEFUL LINKS About blog2023年7月4日 [Show full abstract] utilisation of solid wastes like lead–zinc mill tailings and lead–zinc smelter fuming furnace slag (FFS) as paste backfilling for an underground metalliferous mineTensile strength of cemented paste backfill for lead–zinc mill 2024年4月1日 No 4 230 Alexander Glinin et al: Outotec ® Ausmelt Technology for Treating Zinc Residues 1 Introduction Zinc production has been steadily increasing by 4 % per annum to 13 million tonnes in Technology Selection for Slag Zinc Fuming Process ResearchGate2020年5月1日 1 Introduction Environment friendly bulk disposal of solid wastes, such as mine overburden, gangue, fly ash (FA), mill tailings (MT), slag, jarosite and red mud generated due to mining and mineral processing, is one of the vital components of waste management [[1], [2], [3], [4]]Utilisation of these wastes as backfilling material in underground mine voids is always Strength development and microstructural investigation of leadzinc
.jpg)
SEM–EDS analysis: a SEM image of lead–zinc mill tailings, and b
Behera et al (2020a) used lead zinc mill tailings and slag as paste backfill materials, using slag as a partial replacement of cementHot dip galvanizing is the process of coating iron or steel with a layer of zinc by immersing the metal in a bath of molten zinc at a temperature of around 450 °C (842 °F) The article is then dipped in hydrochloric acid at ambient temperature to remove rust and mill scale Welding slag, Galvanizing process2013年2月19日 Recovery of Zinc and Iron from Steel Mill Dusts by the Use of a TBRC: A Possible MiniMill Solution? Jürgen Antrekowitsch, Jürgen Antrekowitsch Investigations Concerning Slag Optimization Experimental Setup Results of Investigations Economic Considerations ConclusionRecovery of Zinc and Iron from Steel Mill Dusts by the Use of a Almost 2957–3846 million tons of zincbearing dust were produced in Chinese iron and steel enterprises annually The recovery of Zn and other metals in zincbearing dust from ironmaking and steelmaking could improve economic efficiency However, zincbearing dust was classified as hazardous waste, and the volatile metals (like Zn, Na, Pb, etc) in zincbearing dust limited the Research status and development of extraction process of zinc
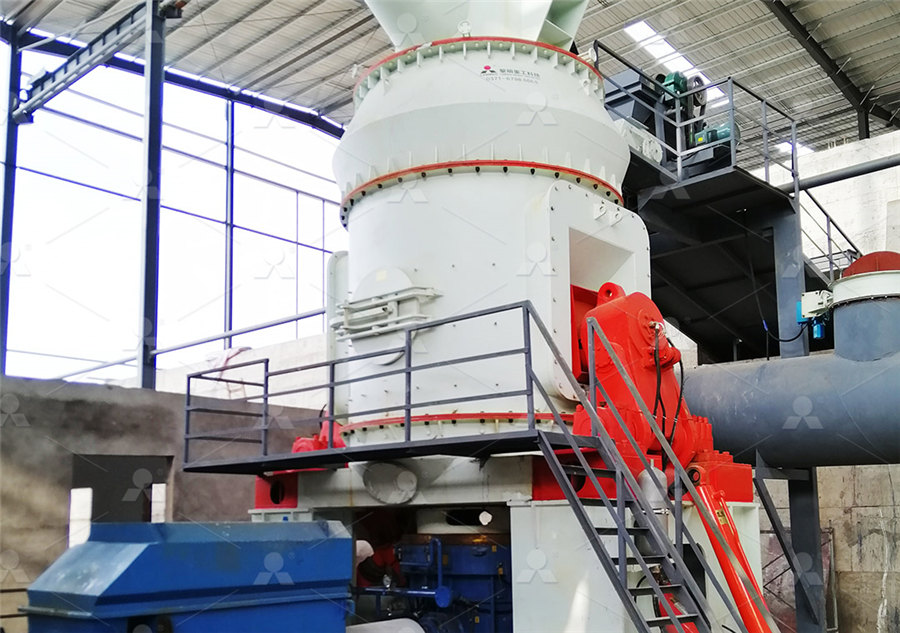
Hydrometallurgical Processes for the Recovery of Metals from
Abstract The state of the art for the recovery of metals from steel industry byproducts using hydrometallurgical processes is reviewed The steel byproducts are different slags, dusts, and sludges from a blast furnace (BF), basic oxygen furnace (BOF), electric arc furnace (EAF), and sinter plant, as well as oily mill scale and pickling sludge The review highlights that dusts and Reduction of liquid slag at 1400–1500 °C for 10–20 h; Drainage of metallic iron and slag at 1450–1550 °C into flat ingot moulds lined with refractory concrete with a zero opening; Zinc vapour combustion and CO afterburning in the furnace gas space, extraction pipeline and afterburning chamber by free atmospheric air intake through slots;HighPerformance Method of Recovery of Metals from EAF Dust 2020年12月4日 Using a softwarebased experiment design, the application of the leaching process for the extraction of manganese from Zinc Plant Slag (ZPS) was investigatedRecovery of Manganese from Zinc Smelter Slag ResearchGate2022年1月11日 Steel mill dusts with high zinc content, occurring during the production of carbon At a residual content of 4% zinc oxide in the slag, the reaction rates of all tests are belowInfluence of Different Carbon Content on Reduction of Zinc Oxide
.jpg)
Thermodynamic Behavior Analysis of FeFeAl2O4 Cermet Prepared by Zinc
2021年2月24日 The use of zinc kiln slag to prepare FeFeAl 2 O 4 cermet can realize the recycling of zinc kiln slag and promote sustainable development The thermodynamic behavior was analyzed by XRD, XRF and using FactSage The results showed that reaction temperature was higher than 710 °C, 7% of C contained in the zinc kiln slag can reduce the iron oxide to Recovery of Indium from Hard Zinc Slag by Pressure Leaching and Solvent Extraction ZHIGAN DENG,1,2 XINGBIN LI,1,3 CHANG WEI,1 GANG FAN,1 stirring mill can enhance the leaching of indium from zinc slag with hydrochloric acid The atmospheric pressure sulfuric acid leaching of Recovery of Indium from Hard Zinc Slag by Pressure Leaching and 2022年2月2日 Steel mill dust recycling contributes essentially to the worldwide zinc production As for every industrial sector, environmental related questions about CO 2footprint, energy consumption, and waste generation are fundamental also for this sectorWhen trying to answer the questions facing the current state of the art, not many satisfying answers can be foundEfficient Steel Mill Dust Recycling—Aiming for Zero WasteMill Diameter Mill Length Installed Power Mill Volume Power Intensity (m) (m) (kW) m3 (kW/m3) Autogenous Mill 10 45 6400 353 18 Ball Mill 5 64 2600 126 21 Regrind Ball Mill 32 48 740 39 19 Tower Mill 25 25 520 12 42 IsaMill 13 3 1120 3 280 3 3) 23/m) Ball Mill Tower Mill IsaMill (m Power Intensity Media Size No Balls / m Surface Area Fine Grinding as Enabling Technology – The IsaMill
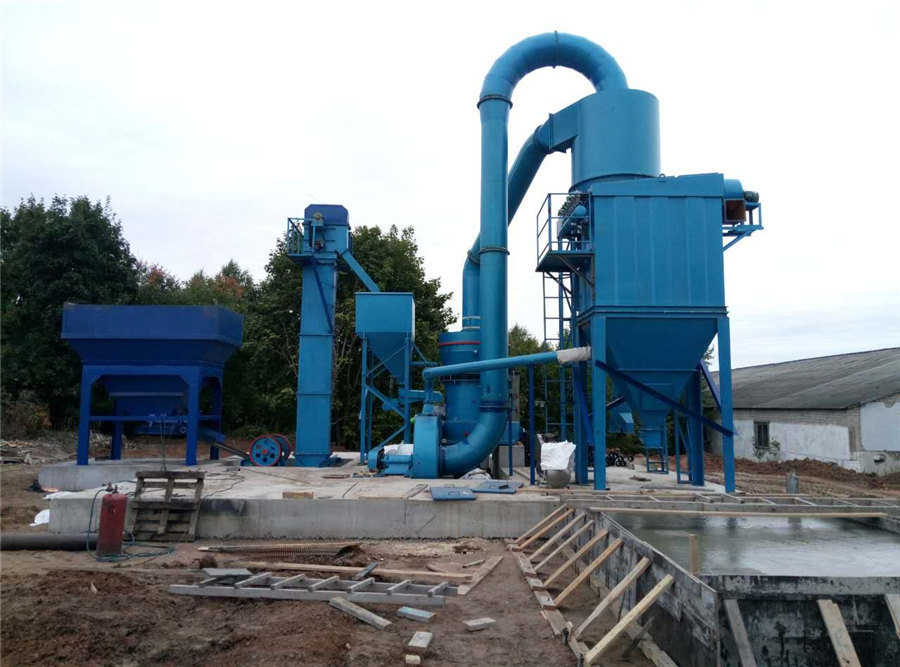
Gold Round Mill/Wet Pan Mill Henan Forui
The wet pan mill is mainly used for the beneficiation of gold, silver, lead, zinc, iron, molybdenum, copper, antimony, and other ore It is also called a gold round mill Because of the small investment, quick results, and high benefits of using DOI: 101016/s10036326(22)660072 Corpus ID: ; Enhanced recovery of zinc and lead by slag composition optimization in rotary kiln @article{Lin2022EnhancedRO, title={Enhanced recovery of zinc and lead by slag composition optimization in rotary kiln}, author={Hongfu Lin and Wei Weng and Shuiping Zhong and Guangzhou Qiu}, Enhanced recovery of zinc and lead by slag Semantic Scholar2013年9月10日 Chemical analysis of the ISF slag is presented in Table 1 It is typical of an ISF slag with about 92% zinc oxide Silica and alumina, which take part in the geopolymerization process, are significantly less than that found in fly ash, which has been used for making geopolymers in many previous studies (Kumar and Kumar, 2011, Kumar et al, 2007, Puertas Utilization of zinc slag through geopolymerization: Influence of 2019年4月5日 In the future, RecoDust in combination with dry slag granulation will become an efficient technique for processing lower zinccontaining materials of a steel millRecoDust—An Efficient Way of Processing Steel Mill Dusts
.jpg)
Particle size distribution curves of mill tailings, FFS and CFFS
The particle size of leadzinc mill tailings, FFS and CFFS varies in the range of 01420, 011200 and 0190 μm, respectively (Table 1) The particle size distribution curve of mill tailings 2001年8月1日 Sulphuric acid has been used for the recovery of zinc from the different wastes/secondaries viz automobile shredded nonferrous fraction (Coyle et al, 1977), slag of zinc cathode melting (Singh and Row, 1981), white dust resulting from the smelting of secondary copper (Southwire Co, United States, 1980), brass mill dust (Kennecott Copper Review of hydrometallurgical recovery of zinc from industrial 2015年10月8日 Pyrometallurgical, largescale lab experiments of a carbonsaturated iron melt as reduction agent for a molten zinc oxide slag were performed to determine reaction constants and accurately State of the Art in Steel Mill Dust Recycling Request PDF2022年4月21日 Electric arc furnace dust (EAFD) is an important secondary resource for the zinc industry The most common process for its recycling is the pyrometallurgical treatment in the Waelz process However, this process focuses on the recycling of the zinc, whereas the recovery of other metals from the EAFD—such as iron and other alloying elements—is neglected An Influence of Different Carbon Content on Reduction of Zinc Oxide
.jpg)
Valorization of lead and zinc slags for the production of
2023年2月1日 The physicochemical properties of both the lead–zinc mill tailings and fuming furnace slag (FFS) have been examined In the first set of experiments, raw slag (FFS)