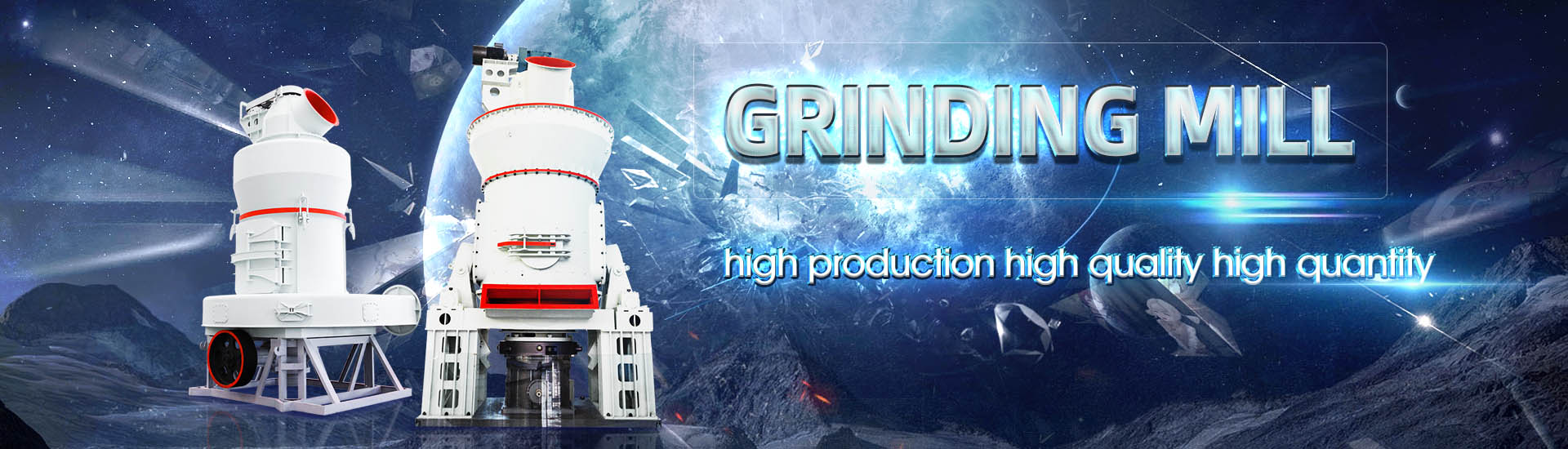
How much slope can the coal mine ring roller mill be used
.jpg)
Technical specifications of vertical roller coal mill
Technical specifications of vertical roller coal mill This study shows the performance of a currently running vertical roller coal mill (VRM) in an existing coalfired power plant2020年8月12日 To understand the performance of a vertical roller coal mill, the real operational tests have been performed considering three different coal sources Obtained results indicate An investigation of performance characteristics and energetic 1999年11月1日 The slopes can be considered as an indication for the grindability The ratio of these slopes to the slope of a standard coal may express how much better or worse the Labscale roller table mill for investigating the grinding behaviour 2009年1月1日 Four grinding circuits are used with different materials: vertical mills (Loesche) for coal and cement feed; vertical roller mills for cement clinkers; and ball mills for cement Grinding process within vertical roller mills: experiment and
.jpg)
Roller Mill Springer
Roller mill is a type of grinding equipment for crushing materials by pressure between two or more rolling surfaces or between rolling grinding bodies (balls, rollers) and a track (plane, ring, and 2017年4月1日 Vertical roller mills (VRM) have found applications mostly in cement grinding operations where they were used in raw meal and finish grinding stages and in power plants Operational parameters affecting the vertical roller mill 2020年8月12日 This study shows the performance of a currently running vertical roller coal mill (VRM) in an existing coalfired power plant In a power plant, the coal mill is the critical An investigation of performance characteristics and energetic Roller mills are mills that use cylindrical rollers, either in opposing pairs or against flat plates, to crush or grind various materials, such as grain, ore, gravel, plastic, and others Roller grain Roller mill Wikipedia
.jpg)
Raymond Roller Mill airswept vertical ringroll
The Raymond Roller Mill is an airswept vertical ringroll mill with an integral classification system that simultaneously dries, pulverizes and classifies a number of different types of products Vertical roller mill is a type of grinder used to grind materials into extremely fine powder for use in mineral dressing processes, paints, pyrotechnics, cements and ceramics It is an energy Vertical roller mill WikipediaVertical Coal Mill (VCM) is equipment for grinding and pulverizing coal into micron size Rotary kilns then use the powders as fuel burners The VCM has a housing section equipped with a lining The layout of the coal mill with a rotary classifier2019年10月5日 In the US, coal mining is a shrinking industry In 1923, there were about 883,000 coal miners; today there are about 53,000; Working in coal mines is dangerous — miners have to deal with toxic What Life Is Like Working in Underground Coal Mines in the US
.jpg)
Review on vertical roller mill in cement industry its
2021年1月1日 Grinding Mill Vertical Roller Mill or Ball Mill: The reclaimed raw mix fed to Raw Mills, for drying and fine grinding of Raw meal for kiln feed: 4: Coal Grinding: Grinding Mill Vertical Roller Mill or Ball Mill: Coal is ground in Coal mill, which is a fuel for use in Kiln firing: 5: Pyro Section, Clikerization: In line calciner six stage 2022年8月31日 Slope failures in surface mines are a severe threat and can result in deaths and significant damage to infrastructure and machinery Though complicated, most of these failures can be predictedSlope Monitoring and Failure Prediction Techniques in Mines: A China Ring Roller Mill wholesale Ring Roller Mill for Mine Stone Grinding US$ 60000 / Piece 1 Piece (MOQ) Hengtu Industry Co, LTD Hengtu Industry Co, LTD Gold Member Audited Supplier Coal Ball Mill Mining Stamp Mill Ring Roller Mill MadeinChina2016年9月1日 Furthermore, VRM separator speed (rpm) is one of the key operational parameters that determines product particle size Increasing the classi er rotor speed from 60 to 80 rpm decreases the particle Operational parameters affecting the vertical roller mill
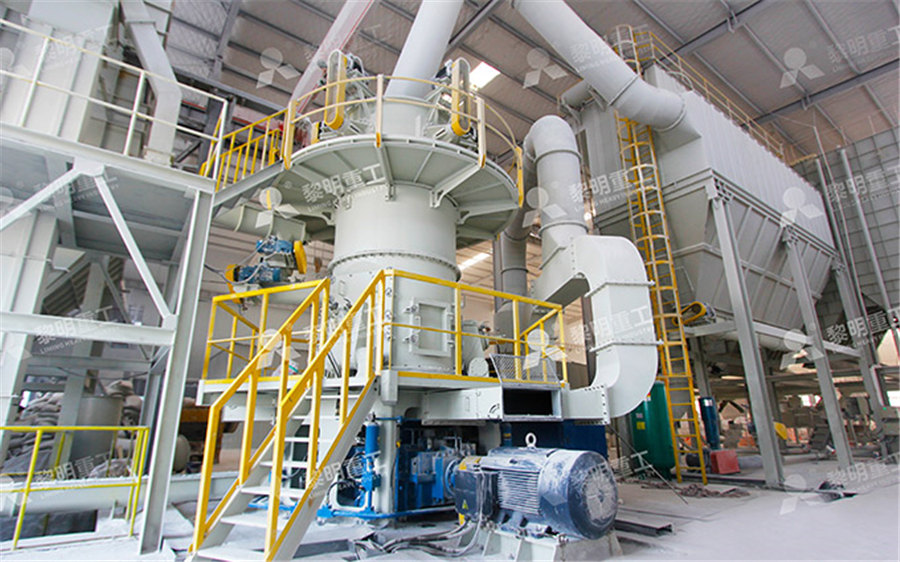
Vertical Mill Calculations PDF Mill (Grinding) Nozzle
There are two main layouts for a vertical roller mill (VRM) system, with product collection in cyclones or a filter The power consumption of a VRM is calculated using factors like the specific grinding pressure, roller dimensions, grinding track speed, and number of rollers The grinding pressure has components from the roller weight and hydraulic system Key internals are the 2016年5月10日 To stabilize the vertical mill grinding table, we must do a good adjustment of dam height , which is the basis of a vertical mill grinding table, the key of vertical mill normal operation Chaeng will introduce you to describe how to establish stable abrasive bed Material thickness can be adjusted to adjust the height of dam, retaining ring material vertical mill is a How to stabilize the vertical roller mill material dam ring?RingRoll (BowlMill) and BallRace Mills comprise most coal pulverizers currently in service at pulverized coal power plants The grinding rolls are stationary in this design, while a worm gear drive rotates the ring (commonly known as the bowl)Coal Pulverizer – Power Plant Pall Corporation2023年7月4日 Roller mill is a type of grinding equipment for crushing materials by pressure between two or more rolling surfaces or between rolling grinding bodies (balls, rollers) and a track (plane, ring, and table) The roller mill with several grinding rollers as working components rolls along the grinding ring or the grinding table to crush the Roller Mill SpringerLink
.jpg)
Cements ground in the vertical roller mill fulfil the
2013年3月1日 This is referred to as the classifier cut size Generally, the plant operator can control the classifier cut size, and thus the comminuted product fineness by adjusting the classifier rotor speed Open pit mining is widely used with metallic ore bodies (aluminum, bauxite, copper, iron), and nearly all nonmetallic (coal, uranium, phosphate, etc) It is a traditional coneshaped excavation (although it can be of any shape, depending on the size and shape of the ore body) that is used when the ore body is typically pipeChapter Open Pit MiningMill Feeders: Feeders for coal mill are generally installed directly under hoppers with rod gate in between The feeders are generally 2 to 3 m long and discharge on to conveyor or feeding chute to mill For coal mill feeding, table feeders, belt feeders, Coal Grinding Cement Plant OptimizationGoogle's service, offered free of charge, instantly translates words, phrases, and web pages between English and over 100 other languagesGoogle Translate
.jpg)
ATOX® Coal Mill FLSmidth Cement
Our ATOX® Coal Mill has large rollers with great grinding capability of virtually all types of raw coal The rollers work harmoniously with a highlyefficient separator and feed sluice to consistently and reliably deliver coal meal to your desired fineness and moisture levelthe conveyor is coal, so some properties of the coal are given in Table 1 Table 1: Pulley Some mechanical properties of coal 2 width Pile mater Density of coal [t/m 3] Maximu m slope Pile angle Static Slope Resistance Coefficient Particle Size a [mm] Coal 0,9 15 40 1,85 80 Transportation capacity of the belt conveyor is 500 tons perCONSTRUCTIVE DESIGN OF A BELT CONVEYOR FOR A COAL MINERoller mills are also more sensitive to instantaneous changes in the feed rate than are other pieces of process equipment Feeding a roller mill directly from a screw conveyor or bucket elevator will cause surges in the feed rate that the roller mill “sees” instantaneously unless some damping system such as a surge hopper is usedCPM Roller Mill MaintenMax hot gas temperature 450°C for roller and 350°C for ball mill trunnion bearing (but note that Réunion is 550°C above trunnion), 250300°C for roller press separator bearing Center Discharge Mill: 1 st compartment hot gases only, max 1015% with kiln air + extra hot airEverything you need to know about clinker/cement Grinding
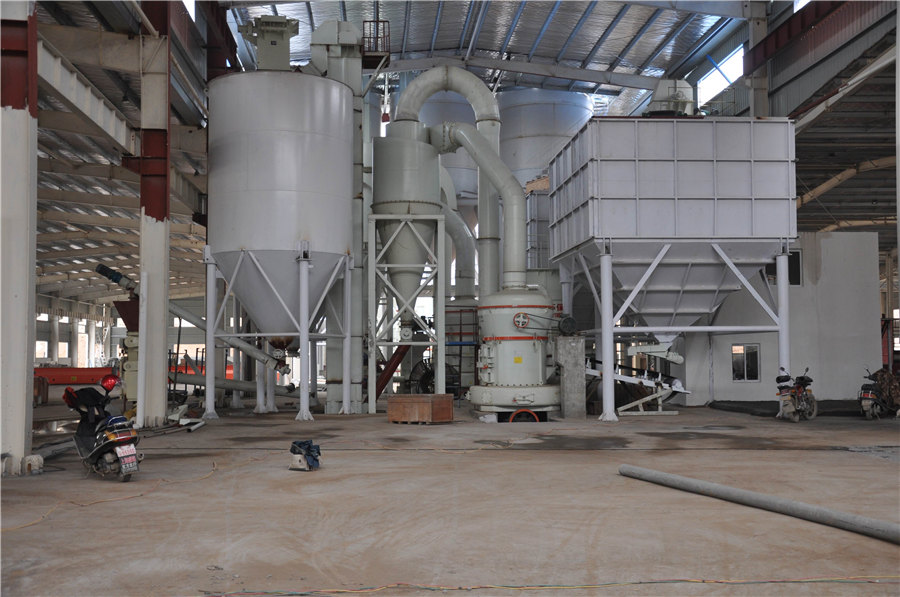
Study of Slope Stability of the Mining Wall in an OpenPit Coal Mine
2024年7月15日 According to this study’s findings, slope stability problems in openpit coal mines can be avoided, and mine wall collapse can be effectively mitigated by the use of cutandbackfill mining Based on the depth of the coal seam and the surrounding terrain, the decision of what type of mine to construct is decided More or less all underground mines are not as much of 1,000 feet deep, but some mines reach depths of about 2,000 feet As a rule, slope mines begin in a valley bottom, and a tunnel slopes down to the coal to be minedSlope Mining, Shaft Mining, Drift Mining, Mining Techniques, Coal 2024年6月10日 The stability of coalmine overburden dumps is a crucial aspect and often requires a slope stabilization method in place to prevent slope failures Mechanical methods like benching, gabion wall construction, geogrid reinforcement, and biological methods like the use of vegetation can suffice the need for slope stabilization In this study, a life cycle assessment of Slope stabilization of coal mine overburden dumps: life cycle 2022年3月30日 Raymond roller mill is used for getting coarse powder It is widely used in grinding calcite, limestone, talc, kaolin and other nonflammable and explosive mHow Does The Raymond Roller Mill Work? YouTube

Technical specifications of vertical roller coal mill
This study shows the performance of a currently running vertical roller coal mill (VRM) in an existing coalfired power plant In a power plant, the coal mill is the critical equipment, whose 2016年10月5日 1 Introduction Cement is an energyintensive industry in which the grinding circuits use more than 60 % of the total electrical energy consumed and account for most of the manufacturing cost []The requirements for the cement industry in the future are to reduce the use of energy in grinding and the emission of CO 2 from the kilns In recent years, the production EnergyEfficient Technologies in Cement Grinding IntechOpen2014年1月2日 For example, the landslide accident at the Shengli East No 2 openpit coal mine directly caused the mine to stop production and, ultimately, the company running the mine became insolvent (Fan et (PDF) Applying real time seismic monitoring technology for slope 2017年11月23日 Ring roller mill has widely application in the field of slag, coal mine, cement, nonmetallic mineral and other industries, Fujian Fengli produced ring roller mill has many advantages andWhat are the advantages and characteristics of ring roller mill?
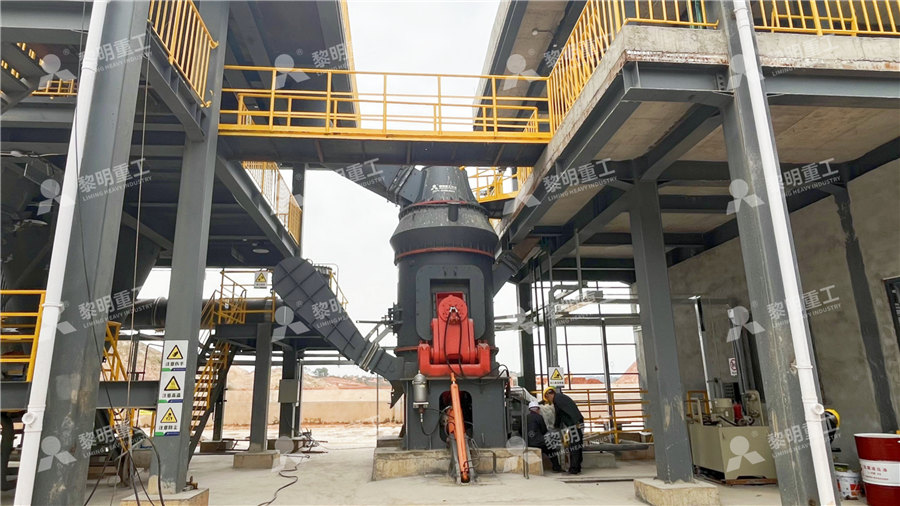
Complete mine shaft equipment from FLS
It stands to reason that the systems used in the mine shaft should also be tailored to those conditions It’s the philosophy behind much of our mine shaft equipment We don’t crowbar in standard solutions; we work with you to design and deliver systems fit for the application, based on more than a century of experience implementing mine shaft systems2020年4月15日 We apply the method to the design of a monitoring system for an Australian coal mine and demonstrate how the approach can facilitate the identification and design of new sensing modalitiesSystems Engineering Approach to Slope Stability Monitoring An early 20thcentury oilseed rollermill from the Olsztyn district, Poland A late 19th century double roller mill displayed at Cook's Mill in Greenville, West Virginia in 2022 Closeup of Barnard's Roller Mill, New Hope Mills Complex, New York Cutaway drawing of a centrifugal roller mill for mining applications, 1913 Roller mills are mills that use cylindrical rollers, either in opposing Roller mill WikipediaKeywords: vertical roller mill, model predictive control, proportional integral and derivative control, artificial neural networks, fuzzy logic 1 INTRODUCTION The VRM is a type of grinding mill integrated with multi functions such as grinding, drying and separation, used for grinding of coal, petroleum coke and mineralsPROCESS CONTROL FOR CEMENT GRINDING IN VERTICAL ROLLER MILL
.jpg)
Optimization and slope stability coal mine with
2020年5月19日 Slope stability and rockfall control are key aspects for the success of an open pit mine operation This study was motivated by a slope failure which occurred at the coal mine in the year 2015 Table 1 lists technical specifications of vertical roller coal mill used in coalfired power plant The combined drying and grinding operation takes place according to the airflow principleAn investigation of performance characteristics and energetic What is a Roller Mill Used For? Roller mills are essential equipment used extensively in the industrial processing sector, particularly for drying, grinding, and classifying a variety of materials Roller mills use the centrifugal force of Industrial Roller Mills Williams Crusher2014年1月1日 Two mill systems are employed for most coal grinding applications in the cement industry These are, on the one hand, vertical roller mills (VRM) that have achieved a share of almost 90% and, on (PDF) MPS mills for coal grinding ResearchGate
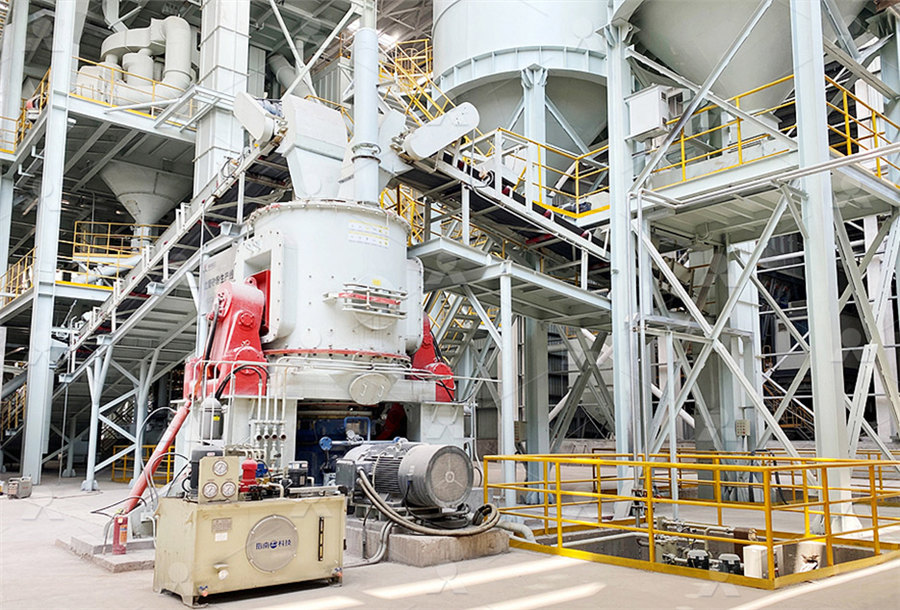
“Unseen by the World:” Johnstown’s 1902 Rolling Mill Mine
2024年5月29日 The Mine and Its Coal Johnstown’s Rolling Mill Mine was already old in 1902 Established in 1856, its operation instantly “raised the number of working miners in the Johnstown area to two hundred,” galvanizing mining in the region (3) For the next fifty years, 2022年11月7日 Slope Stability Numerical Analysis and Landslide Prevention of Coal Mine Waste Dump under the Impact of Rainfall—A Case Study of Janina Mine, Poland November 2022 Energies 15(21):8311Slope Stability Numerical Analysis and Landslide Prevention of Coal 2017年4月1日 Vertical roller mills (VRM) have found applications mostly in cement grinding operations where they were used in raw meal and finish grinding stages and in power plants for coal grinding The mill combines crushing, grinding, classification and if necessary drying operations in one unit and enables to decrease number of equipment in grinding circuitsOperational parameters affecting the vertical roller mill 2011年8月1日 Pulverizers prepare raw fuel by grinding it to a desired fineness and mixing it with the just the right amount of air before sending the mixture to boiler burners for combustion In Part I of Pulverizers 101: Part I POWER Magazine
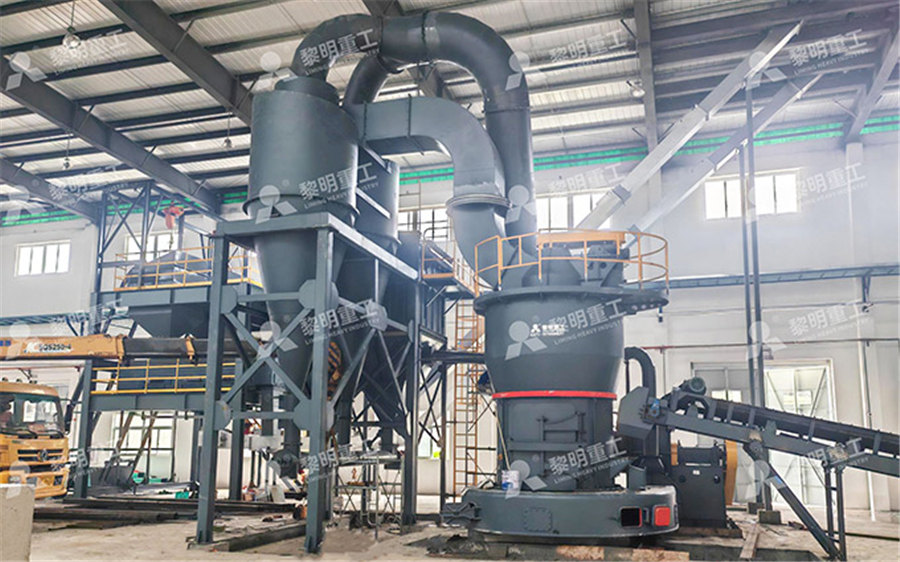
HOW ELECTRICITY IS PRODUCED AT A COALFIRED POWER
Lethabo Power Station burns 50 000 tons of coal every day, enough to fill 1 500 trucks carrying 33 tons each Conveyor systems are used to transport the coal from a nearby mine to a coal stockyard and then to the power station site The purpose of the coal stockyard is 2023年10月12日 The present Indian annual demand of 120 Mt is expected to go up to 310 Mt by the end of this century Although the major share of this is expected to come from opencast mines, underground coal (PDF) INSTALLATION OF HIGH CAPACITY BELT CONVEYOR