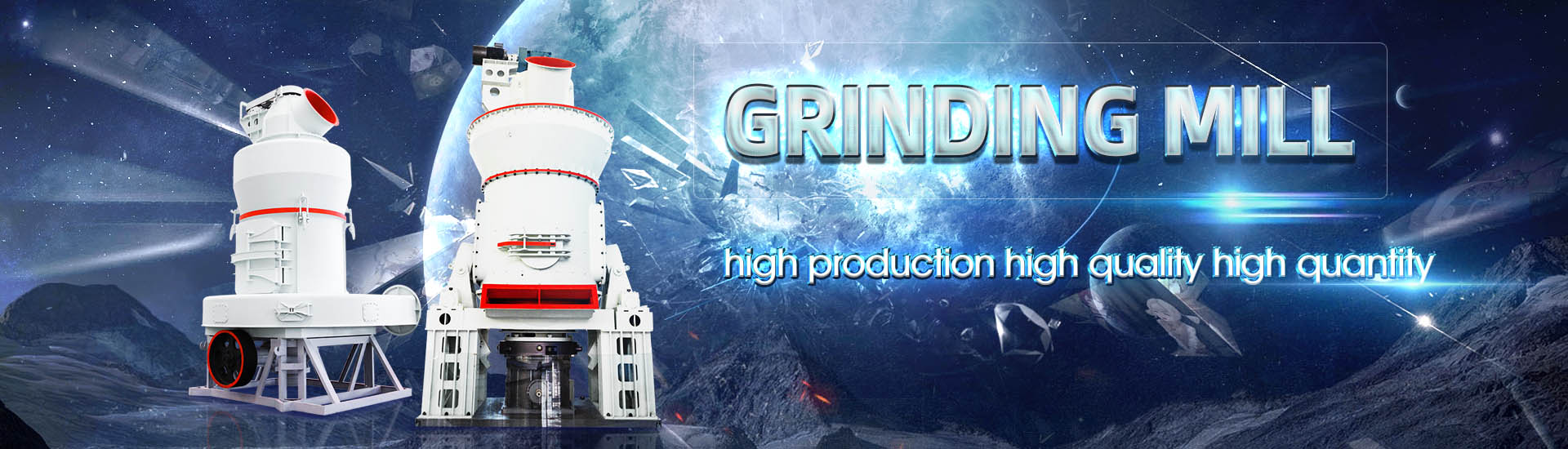
Refractory material crushing process
.jpg)
Design, Manufacturing and Properties of Refractory Materials
2024年4月5日 Refractory materials are both economically and socially strategic materials as they enable the production of other crucial products, including steel, nonferrous metals, 2020年5月21日 The liquid phase formation above 1200 °C limits the ferrochrome slag use for refractory applications Results suggest ferrochrome slag’s feasibility as an aggregate raw Ferrochrome Slag Feasibility as a Raw Material in Refractories refractory raw materials themselves have the function of binder, such as bonding clay The role of additives is to improve the production or construction process of refractory materials or to Refractories, Properties and Application of2023年1月20日 Refractory materials are strategic materials taking into account the fact that they enable the production of strategic building materials, such as steel, cement, or glass Additionally, they ensure safe human work and eco Design, Manufacturing and Properties of Refractory
.jpg)
Refractory Bricks
Raw materials are processed by drying, crushing, screening and milling to produce a wide range of size fractions from millimetre to micron sizes Air swept ball mills produce the very fine flour 2002年5月10日 Any aggregate can potentially be used in the formulation of a monolithic refractory They are chosen based on their stability at the temperature of application, mechanical strength, and corrosion resistance As a guide, An Introduction to Refractory Aggregates AZoM2024年4月5日 With pleasure, we present this Special Issue of Materials, titled “Design, Manufacturing and Properties of Refractory Materials”Refractory materials are both economically and socially strategic materials as they enable the production of other crucial products, including steel, nonferrous metals, cement clinker, lime, glass and many othersDesign, Manufacturing and Properties of Refractory MaterialsREFRACON REFRACTORY IS ONE OF THE TOP MANUFACTURER OF REFRACTORY CASTABLE WITH UNMATCHED QUALITY Refractory Castables, is a kind of granular and powdery material made form refractory Production RRMSB REFRACTORY CASTABLE
.jpg)
Refractory: Characterization SpringerLink
2020年11月29日 This chapter discussed the purpose of use of refractories and gives a general introduction to available refractory materials, which include Through thorough study and longtime experience, the engineers have standardized the refractory practices for different process industries 11251 Cold Crushing Strength While the insitu formed Al 4 C 3 is highly refractory, at ambient temperatures it hydrates to form Al(OH) 3 (leading to an approximately 110% volume increase) and methane (equation 2) Therefore, the Al 4 C 3 in reclaimed material must be stabilised before being recycled in refractories or it will promote cracks and result in scrap production Al 4 C 3 + 12H 2 O → Technical Challenges for Refractory Recycling and Innovative service conditions, where the refractory used is heating from all sides such as checkers, partition walls, etc the RUL test data is quite significant 8) Creep at high temperature: Creep is a time dependent property which determines the deformation in a given time and at a given temperature by a material under stress Refractory materials mustOverview of Refractory Materials PDHonline2021年10月14日 Mixing: The process of homogenizing the composition and particle size of two or more nonuniform materials and promoting particle contact and plasticization is called mixing Refractory mixing is a method of mixing, accompanied by a certain degree of extrusion, kneading, and venting The mixing process is to make the components in the mud reach a uniform The production process of refractory materials
.jpg)
Properties of Castable Refractories Becht
2023年6月12日 Cold crushing strength is a measure of the refractory’s strength and durability As refractory falls within the domain of ceramic materials, it tends to fail in brittle fracture In addition, castable materials naturally contain a large population of 2023年5月15日 In order to obtain highquality products, a new homogenized material calcined process is proposed : Raw materials enter the factory→storage→crushing→grinding→desiliconization→wet homogenization→press filtration→sliming→extrusion molding→drying→calcination→crushing→finished products Bauxite Rotary Kiln Calcination Process and Refractory Manufacturing Process The manufacturing of refractory bricks involves several stages It begins with the selection and preparation of raw materials This typically involves crushing, grinding, and blending of the various components to achieve the desired mixtureRefractory Brick Formula, Properties Application2021年9月3日 Abstract: This paper reviews the raw materials, additives, general properties, oxidation and corrosion of MgOC refractories, which are irreplaceable in the steelmaking process Because it is a composite refractory, it benefits from the combined properties of magnesia and carbon Highpurity magnesia aggregates (fused as well as sintered), graphite MgOC Refractories: A Detailed Review of These Irreplaceable
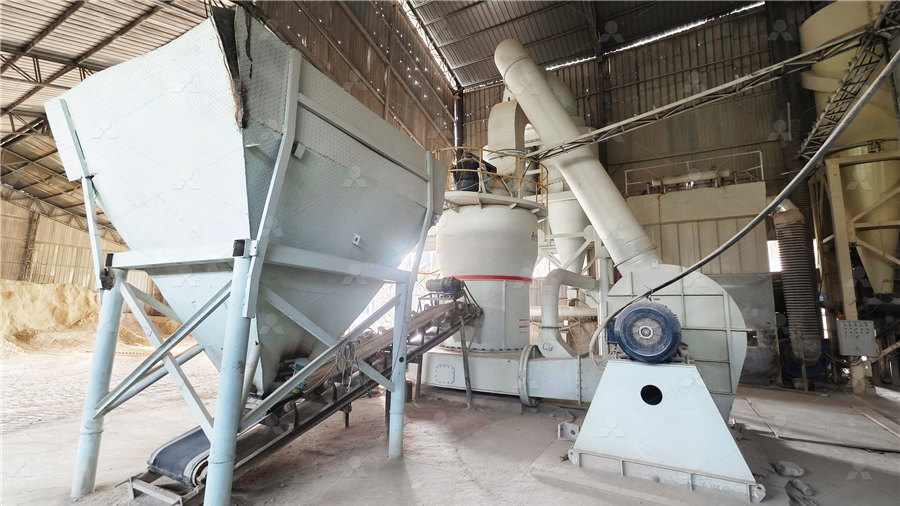
Refractory Raw Materials
that the starting material is furnace grade alumina produced by the Bayer Process (see section on Calcined alumina) • Both materials are highly refractory, having melting points of just under 2000oC, and bulk densities of x 3900kg/m3 (brown) and 3500/3700kg/m3 (white)2021年9月29日 The mechanical properties of refractory materials refer to the strength of the material at different temperatures, elastic and plastic properties This type 86Mechanical properties of Refractory MaterialsBauxite crushing classification machine, process flow July11,2020 Bauxite is widely used in the aluminum smelting industry usually The most commonly used raw ore for smelting aluminum and producing refractory materials The Bauxite crushing classification machine, process IntroductionThermally stable mineral aggregates, a binder phase, and additives make up refractories, which are inorganic, nonmetallic, porous, and heterogeneous materials The main raw materials used in the manufacture of refractories are silicon, aluminum, magnesium, calcium, and zirconium oxides Carbides, nitrides, borides, silicates, and graphite are examples of non Standards and Testing for Refractory Materials
.jpg)
Introduction to Refractories IspatGuru
2013年9月28日 Fireclay refractory bricks are manufactured from unfired refractory bond clay and fireclays (chamotte), fired refractory clay, or similar grog materials Fireclay refractory bricks have two main components namely 18 % to 44 % of alumina (Al2O3) and 50 % to 80 % of silica (SiO2) Fireclay refractories are least costly and are used extensively2015年2月3日 Fig 1 Typical flow in the production process for refractories Shapeless refractories are normally dispatched from the refractory manufacturing plant not as a refractory but as refractory materials which become refractory only after it undergoes mixing, forming, aging, drying, and preheating etc at the site of useProduction Process for Shaped Refractories – IspatGuruProduction Process Itis divided intothe production processof shaped refractory products and of monolithic refractory materials The production process is shown in Fig 1 The production process of shaped refractory products mainly includes (1) calcination of raw materials Most natural refractory raw materials need calcination to obtain Refractories, Properties and Application ofZhongwei Metallurgical Material Co, LtdFocus on high temperature refractory materials roll crushing mill, cone crusher, large ramon mill, On the one hand, between refractory brick materials and quality In the process of production, Zhongwei Metallurgical Material Co, LtdrefractoryChamotte
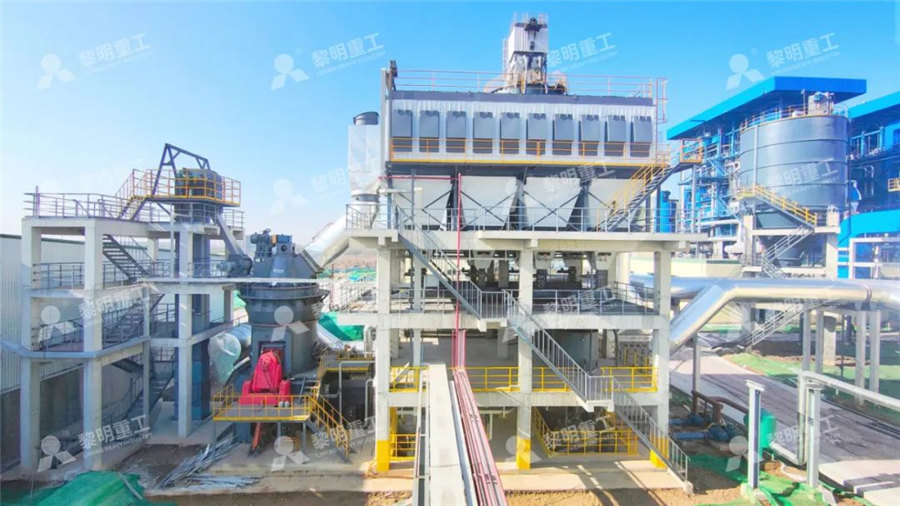
Cold Crushing Strength (CCS) of Refractory Bricks and Castables
2009年11月3日 The concept of testing CCS of a refractory material has perhaps, come from metallurgy This is because for any refractory brick it is rather; rare that it would fail simply due to load on it in cold condition and therefore, the determination of cold crushing strength does not appear to be important from that point of vieware lined with refractory materials such as magnesia, which has a melting point of 5070 degrees Requirements of Right Refractory The general requirements of a refractory material can be summed up as: 1) Its ability to withstand high temperatures and Overview of Refractories CED Engineering2020年6月10日 Selection of Refractory Materials [6, 25] Ceramic cup material made of oxide refractory has bulk density of 28–32 gm/cc, which is much lower that the density of hot metal, 69–70 gm/cc, so the refractory oxide layer may be dislodge and float by the upward thrust of hot metal during its turbulent flowBlast Furnace Refractory SpringerLink2022年4月19日 Discover how LMM advanced Refractory Bricks Manufacturing Process can significantly enhance your industrial performance By integrating stateoftheart technology and precision engineering, LMM ensure each brick Advanced Refractory Bricks Manufacturing Process
.jpg)
Limestone crushing, sand making and grinding process
2022年7月20日 Application analysis of limestone crushing, sand making and grinding After testing by several cases and relevant departments, as long as the process of limestone processing sand and gravel materials is reasonable, the 2016年2月24日 Testing of the durability of refractory materials in a specific chemical environment can be done at laboratory scale This makes it possible to follow the meltrefractory reactions in small volume instead of at full scale With wellchosen, valid refractory grades longer campaigns can be expected in operationRefractory Lining Materials Testing Metso2023年10月9日 It is important to note that refractory materials may have different CCS values depending on their composition, manufacturing process, and intended application High CCS values are desirable for applications where the bricks will be subjected to high mechanical stresses, such as in the linings of industrial furnaces and kilnsWhat is Cold Crushing Strength – CCS of Refractory BricksBasis their chemical composition, refractory materials expand when they are exposed to heat Magnesium oxide is by far the most commonly used material and it has a high coefficient of expansion A typical manufacturing process for refractory materials involves steps like crushing and grinding, followed by forming, firing, and final processing Silica Fume in Refractory Materials Henan Superior Abrasives
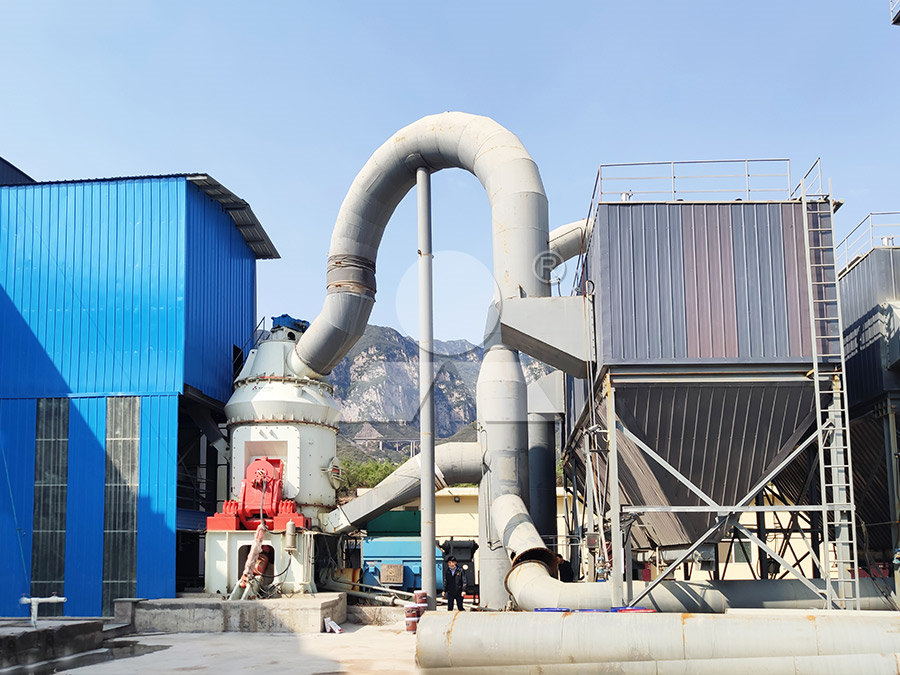
Refractory Material an overview ScienceDirect Topics
Resource Recovery and Recycling from Metallurgical Wastes S Ramachandra Rao, in Waste Management Series, 2006 626 Refractories Refractory materials are used to line smelting furnaces The most usual lining configuration in North America is one that consists of a thin layer of insulation castable protected from the liquid metal by a monolithic material with nonwetting The waste material is classified as hazardous waste due to its chromium content In this study, arc furnace technology was used for thermal treatment of the waste materials to enable recycling of refractory materials (Received January 21, 2003; Accepted March 10, 2003) Keywords: refractories, thermochemical treatment, chromium oxide, eco Refractory Materials from Waste JSTAGE2016年10月28日 This includes the fundamentals of refractory technology supported by phase diagrams as well as detailing the prominent applications of these essential industrial materialsRefractory Technology: Fundamentals and ApplicationsRefractory manufacturing involves four processes: raw material processing, forming, firing, and final processing Figure 1151 illustrates the refractory manufacturing process Raw material processing consists of crushing and grinding raw materials, followed if necessary by size classification and raw materials calcining and drying115 Refractory Manufacturing US EPA
.jpg)
IS 15287 (2010): METHODS OF SAMPLING AND PHYSICAL TESTS FOR REFRACTORY
high silica refractory materials (first revision) 1528 Methods of sampling and physical tests for refractory materials: (Part 1) : 2010 Determination of pyrometric cone equivalent (PCE) or softening point (third revision) (Part 10) : 1974 Determination of size of refractory bricks (first revision) (Part 14) : 1974 Determination of sieve analysisASTM's refractory standards are instrumental in specifying, testing, and evaluating the chemical, physical, and mechanical properties of various materials and products made of refractory These materials, which are commonly made from the oxides of aluminum (alumina), silicon (silica), magnesium (magnesia), and calcium (lime), have the distinct Refractory Standards Standards Products Standards2021年7月29日 The refractory bricks production process from material ,mixing, pressing ,drying, burning ,cooling and packing and shipment Skip to content LMM GROUP The production procedureof a refractory brick is divided into Refractory Brick Production ProcessPhysical and Mechanical Properties of High Alumina Refractory Materials for shielding Applications of Steam Reformer (PLC), the cold crushing strength Key Words: Primary and secondary Reformer, alumina base refractory materials, ASTM C134,C133, C856, Ammonia production process DOI: 107176/CMR/11705 Publication date:September Physical and Mechanical Properties of High Alumina Refractory Materials
.jpg)
Review of Refractory Materials for Innovative Investigation and
2018年3月27日 This paper is a review of thermal analysis and testing of different refractory materialsRefractories are ceramic based materials that can withstand unusually high heat as well as abrasion and the Following Part 1 of this publication series which dealt with the procedure and the determination of precision of Cold Crushing Strength (CCS) data on several refractory brick grades, part 2 deals with the comparison of ISO 100591/EN 9935 and ASTM C133 This includes the influence of specimen shape (50 mm cylinders and 50 mm cubes) Weiterlesen Evaluation of Test Methods for Refractory Bricks: A Comparison The most common way to manufacture Portland cement is through a dry process The first step is to quarry the principal raw materials, mainly limestone, clay, and other materials After quarrying, the rock is crushed This involves several stages First, crushing reduces the rocks to a maximum size of about 6 inches The rocksChapter 4 Cement Manufacturing and Process ControlCrushing and pulverizing components designed to reduce the particle size of hard materials will gradually succumb to wear, requiring regular maintenance to ensure optimal performance Yet most grinding, crushing, and pulverizing components will need replacing due to irreversible wearCrushing Pulverizing Grinding Wear Resistant Technologies

Drying behavior of dense refractory ceramic castables Part 1
2021年8月15日 Usually, adding water to refractory products is required due to two main aspects: (i) to induce a more efficient mixture and homogenization of the raw materials, making it easier to convey the fresh castable and shape it, and (ii) to favor the development of chemical reactions and further precipitation of hydrated phases due to the interaction of the liquid with hydraulic ciated with high volume expansion which completely destroys the Refractory [1–4] Chamoˆe Crushing ScreeningB atch Weighing Mixing Binder Plasc fireclay Ball Milling Pressing Drying PRODUCT Firing at 11001400 °C Fig 31 Flowsheet of the process of manufacturing of fireclayshaped RefractoryChapter 3 Manufacturing and Properties of Refractories