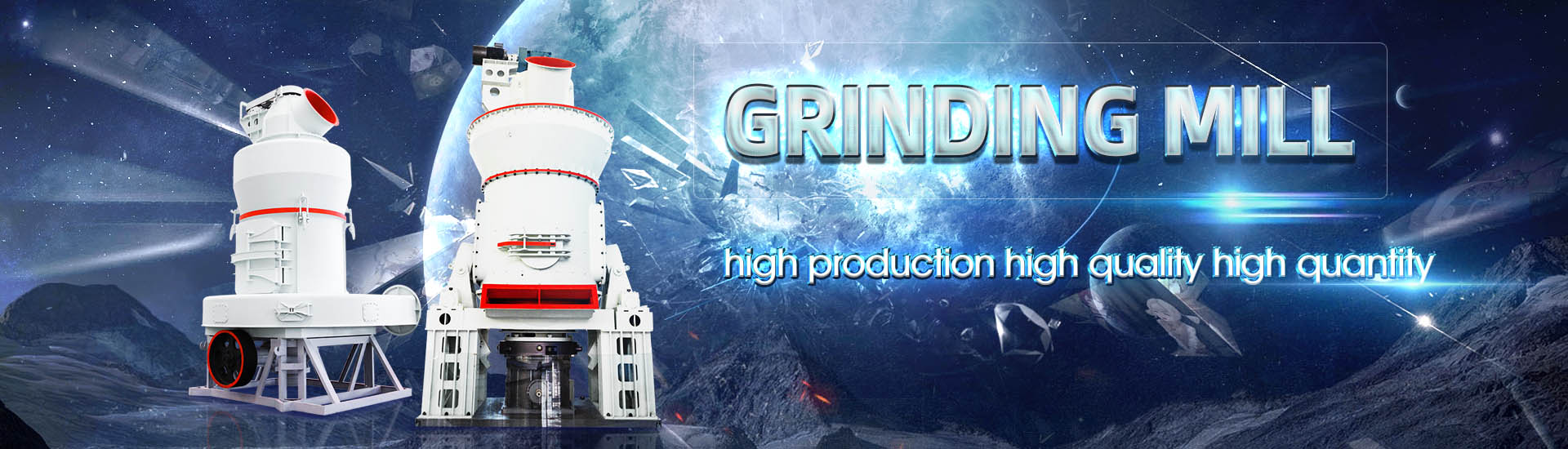
13 Ore grinding mill design book
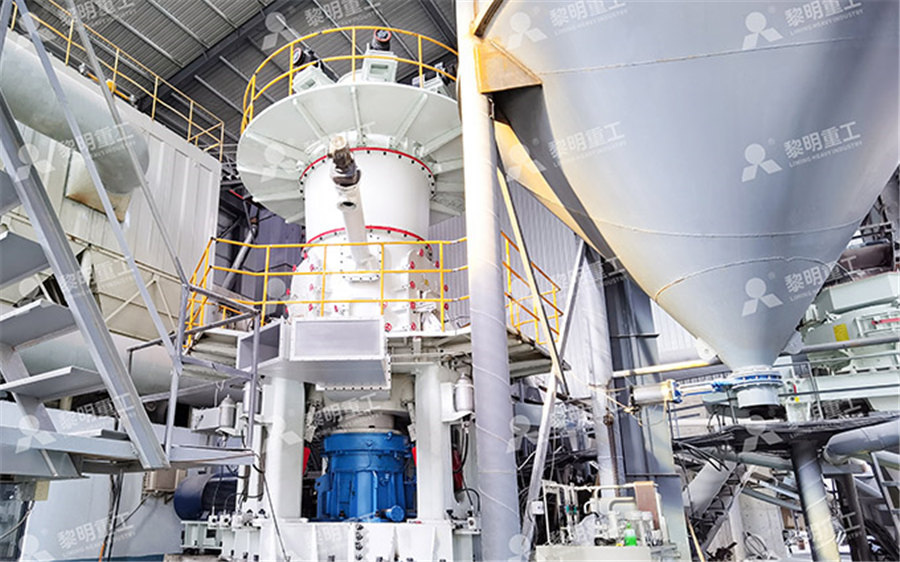
Mineral Processing Design and Operations ScienceDirect
The designs of tubular mills loaded with steel rods along its length as the grinding medium are described in this chapter Details of operation and computations of mill capacities and the This document provides guidance on ball mill grinding processes It covers topics such as ball mill design including length to diameter ratios, percent loading, critical speed, and internals evaluation Methods for assessing ball charge, Ball Mill Grinding Process HandbookThis second edition describes theories and practices of design and operation of apparatus and equipment, including an additional chapter on magnetic, electrostatic, and conductivity modes of mineral separationMineral Processing Design and Operations 2nd Advances in automated mineralogy and analysis and highpressure grinding rolls are given dedicated coverage The new edition also contains more detailed discussions of comminution efficiency, classification, modeling, flocculation, Wills' Mineral Processing Technology 8th Edition
CFB石灰石脱硫剂制备64.jpg)
Mineral Processing Design and Operations: An ResearchGate
2016年5月17日 The process of grinding in a tumbling mill is carried out by combining three mechanisms of interaction of grinding bodies with particles of the processed material impact This chapter reviews the role of grinding in manufacture including its origins, the nature of the process and the strategic importance of grinding in modern manufacture Key issues are Principles of Modern Grinding Technology ScienceDirectGrinding is the last stage in the comminution process where particles are reduced in size by a combination of impact and abrasion, either dry, or more commonly, in suspension in water It Chapter 7 Grinding Mills Wills' Mineral Processing Technology, This document provides information about grinding mills, including standard sizes and dimensions of mills, descriptions of mill types and components, and methods for estimating mill power requirementsBall Mill Design Power PDF Mill (Grinding) Iron
.jpg)
How grinding mill design changed over the last 30 years
2020年6月3日 The design of such grinding mills is extremely critical, requiring sophisticated software tools, proprietary calculation worksheets, and experienced technical engineers and drafters This blog will review how the mill design 2020年10月1日 These include mill power draft calculations, shell lifter design, lifter wear prediction, pulp lifter simulation and ore particle breakage in grinding mills The status of advancement in each of A Review on Current Mill Liner Design and 2007年8月1日 SAG mill liner development draws primarily on practical experience from SAG milling operations supported by computerbased modeling of charge motion in SAG mills and on established good design practice Liner design needs to respond to the process aspects of mill liner action that are critical to good SAG mill performance, ie, the impact of shell liners on the Semiautogenous grinding (SAG) mill liner design and developmentThis document discusses SAG mill grinding circuit design Some key points: 1) Adding pebble crushing is common to reduce buildup of critical sized particles in SAG mills and improve efficiency 2) Important aspects of pebble crusher SAG Mill Grinding Circuit Design
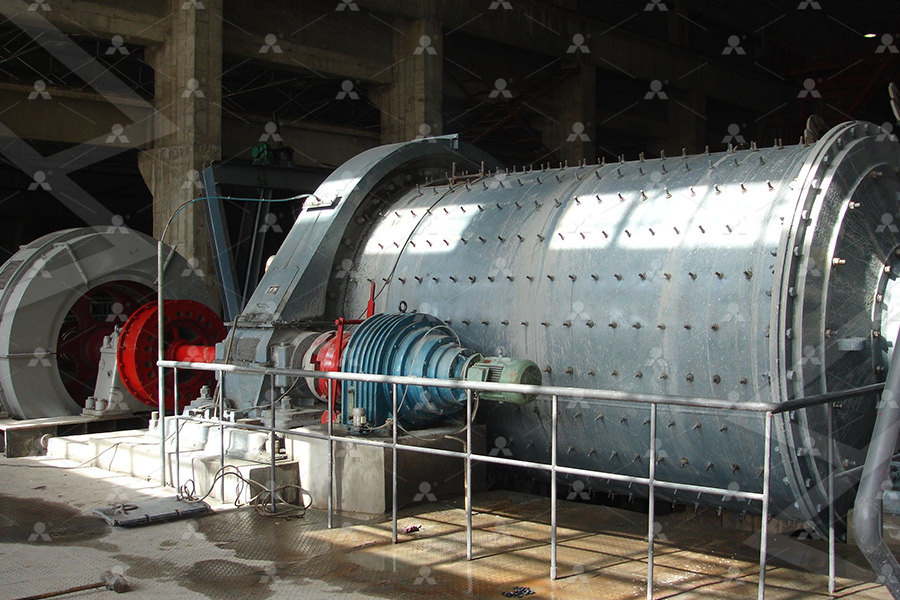
Grinding Mill an overview ScienceDirect Topics
In the mill, the mixture of medium, ore, and water, known as the mill charge, is intimately mixed, the medium comminuting the particles by any of the above methods Apart from laboratory testing, grinding in mineral processing is a continuous process, material being fed at a controlled rate into one end of the mill and discharging at the other end after a suitable dwell (residence) timeThis document provides an overview of the design of a ball mill used to grind copper ore Key details include: The mill has a diameter of 7300mm, length of 11,000mm, and processes 1211 tonnes of ore per hour It uses a combination of crushing and abrasion to grind the ore, aided by balls lifting and dropping in the mill The overview describes the main components of the mill A Ball Mill DesignOverview 1 PDF Mill (Grinding) Tools2021年1月19日 Key Words: Comminution Tests, Bond Work Indices, Grinding Mill Design, Database, Ore Hardness Measurements, SAGDesign Test, JK Dropweight Test, MacPherson Test the Bond Ball Mill Wi was 13 kWh/t for this ore The Bond Rod Mill Wi was 20 kWh/t, whereas the SAG pinion energy to grind the ore to T80 17 mm was 30 kWh/tSuccessful Design of the NICO Grinding Circuit for Unusually Hard OreSelection and Design of Mill Liners ISBN13: 9780873352468, Society for Mining, metallurgy, and exploration, Inc, Colorado, USA pp 331376 The Selection and Design of Mill Liners used to strike the best economic balance between liner life and mill grinding performance, thusThe Selection and Design of Mill Liners 911 Metallurgist
.jpg)
DYNAMIC DESIGN FOR GRINDING MILL FOUNDATIONS
herein The diameter of mill is 80 m with length of 131 m, operating at 12 rpm The height of mill shaft is 181 m above ground The weight of mill and charge (ore and grinding media) is 3,452 tons2016年6月6日 Because SAG mills rely both on the ore itself as grinding media with a size range of 13—75 mm Criticalsized particles can result from a simple failure of a mill’s breakage rates to exceed the breakage rate of incoming particles, SAG Mill Design and Specification SAG Mill Grinding Circuit Design 911Metallurgist2024年1月1日 The vertical stirred mill is vertically installed, and gravity works in the grinding process With the advantages of high grinding efficiency and less area occupation, it is widely used in the regrinding, fine grinding, and ultrafine grinding process of such metal mines as iron ore, copper ore, leadzinc, and such nonmetallic mineral industries as calcium carbonate, Stirred Mill SpringerLink2015年6月19日 The basic parameters used in ball mill design (power calculations), rod mill or any tumbling mill sizing are; material to be ground, characteristics, Bond Work Index, bulk density, specific density, desired mill Ball Mill Design/Power Calculation 911Metallurgist
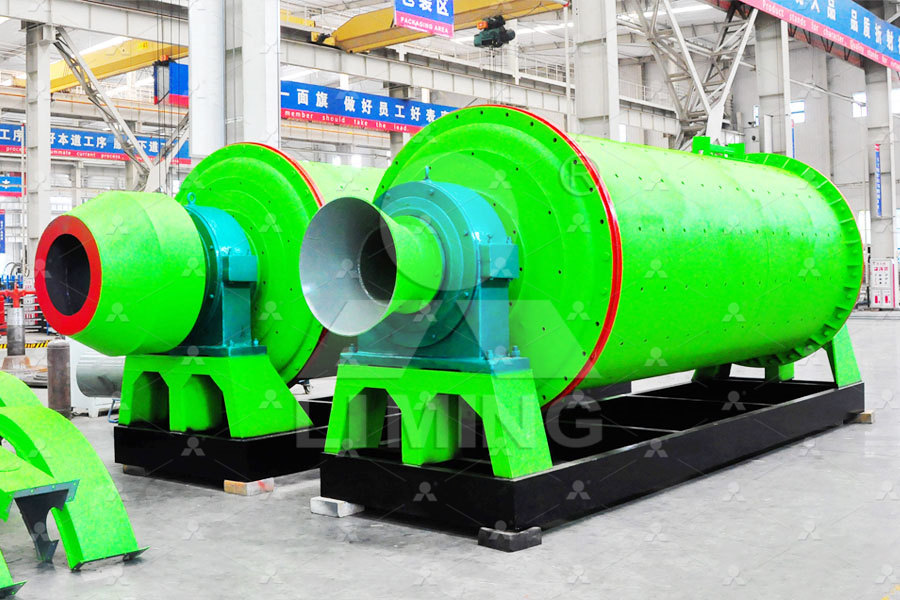
Grinding Operations Design Overview PDF Mill
Grinding Operations Design Overview Free download as PDF File (pdf), Text File (txt) or read online for free on empirical data and do not explain the This document provides an overview of grinding concepts and mill operation and 2016年4月22日 In all ore dressing and milling processes, including flotation, cyanidation, gravity concentration, and amalgamation, it is necessary to crush and grind, often with rob mill ball mills, the ore in order to liberate the Ball Mill Rod Mill Design 911MetallurgistLargediameter autogenous and semiautogenous grinding mills represent the primary thrust of the expanding grinding technology In spite of initial difficulties, large autogenous and semiautogenous mills have reached an acceptable level of technology that provides the mineral engineer with a reliable, low cost means of ore comminutionA successful milling installation Semiautogenous mill liners: Designs, alloys, and maintenance procedures 2021年1月7日 John Starkey, President, Starkey Associates Grinding Design and Process Engineering, and Graham Holmes, mill, by continuously feeding ore that has been crushed to 100 % passing 125 inches The design goal was achieved by selecting the gross specific energy value of 138 kWh/t for the Kubaka SAG mill 5DESIGN OF THE KUBAKA GRINDING CIRCUIT USING SPI AND BOND
.jpg)
Optimum Design of Hammer Mill for Grinding Leonardite
2023年1月16日 The objective of this research is to design and construct a hammer mill for grinding leonardite charcoal (Lignite, class J) The conditions for the design and construction of the grinder are However, other factors such as mill design and the type of ore being processed also play a role in how well the ball milling process works Effect of media type on ore grinding performance There are many factors that will affect the ore grinding performance in ball millsFactors affecting ores grinding performance in ball mills2023年4月23日 ciency include mill design, liner design, mill speed, charge ratio, and grinding media properties The authors also indi cated that circuit efficiency is determined by how well the power applied (PDF) Grinding Media in Ball MillsA Review ResearchGate2006年1月1日 The stanex diaphragm between the grinding compartments effectively screens the material passing from the in numerous industrial applications; coarse ore is ground in mills before being mixed [2 (PDF) Selection and design of mill liners ResearchGate

Grinding Media in Ball Mills for Mineral Processing
2023年11月24日 Therefore, the grinding action is achieved by attrition, abrasion, and impact between the ore itself and between the ore particles and grinding media Factors that influence the grinding efficiency include mill design, liner design, mill speed, mineralogical composition of the ore, charge ratio, and grinding media properties SAG mill liner design and configuration can significantly impact mill performance Key considerations for liner design include lifter spacing and angle, grate open area and aperture size, and pulp lifter design and capacity As mills increase SAG Mill Liner Design PDF Mill (Grinding) Steel2012年6月1日 As the cylinder starts to rotate, the grinding balls inside the cylinder crush and grind the feed material, generating mechanical energy that aids in breaking bonds, activating the catalyst, and Grinding in Ball Mills: Modeling and Process Control2015年4月9日 Grinding Mills and Their Types satyendra; April 9, 2015; 12 Comments ; autogenous grinding, ball mill, grinding mills, hammer mill, rod mill, roller mill, SAG,; Grinding Mills and Their Types In various fields of the Grinding Mills and Their Types – IspatGuru
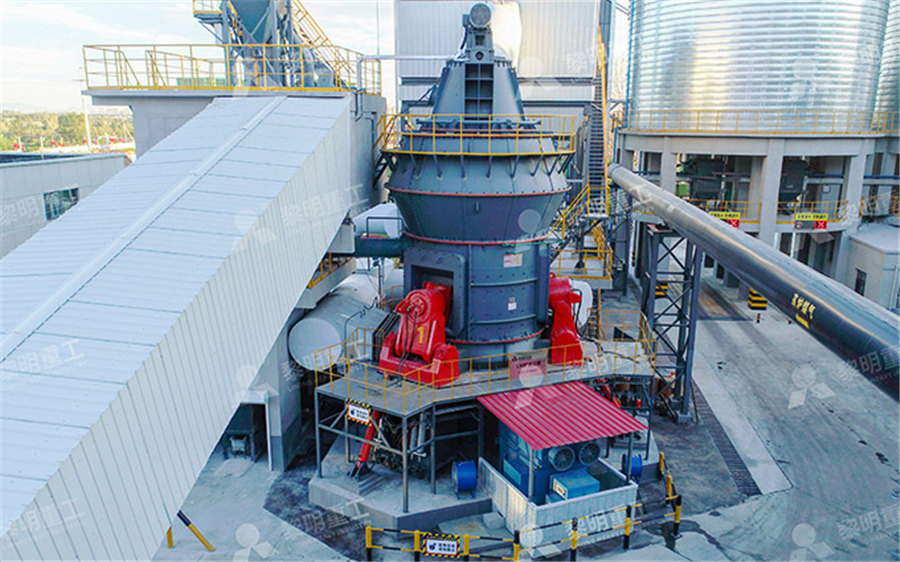
Optimizing Grinding and Regrinding Capacity in Mill Design
2019年4月25日 Much work has been devoted to the technical aspects of grinding, the “how” of grinding But, in the writers’ opinion, the economically important subject of optimizing grinding capacity in mill design has not received the attention it deserves, at least not in published literature Optimizing Primary Grinding CapacitySAG MILL TESTING AN OVERVIEW OF THE TEST PROCEDURES AVAILABLE TO CHARACTERIZE ORE GRINDABILITY AUTHOR: FO VERRET, G CHIASSON AND A MCKEN SGS KEYWORDS Comminution, grindability, grinding, SAG mill, AG mill, milling, HPGR, work index, pilot plant INTRODUCTION The resistance of ore samples to breakage (or hardness) is SAG Mill Testing Test Procedures to Characterize Ore Grindability2018年8月8日 One of the most effective methods of grinding Portland cement is the use of an electromagnetic mill, which has proven its advantage in creating clinkerless binders [2], regulating the kinetics of (PDF) Grinding Kinetics Adjustment of Copper Ore Grinding in 2018年4月8日 Referring to Table VII a 305 meter (10 foot) by 305 meter (10 foot) overflow ball mill with a 40 percent by mill volume ball charge, new liners and 50 mm (2″) balls draws 491 HP Using equation 5 there will be a loss of 055 Kw (074 Hp) per metric tonnes of ballsHow to Size Design a Regrind Ball Mill 911Metallurgist
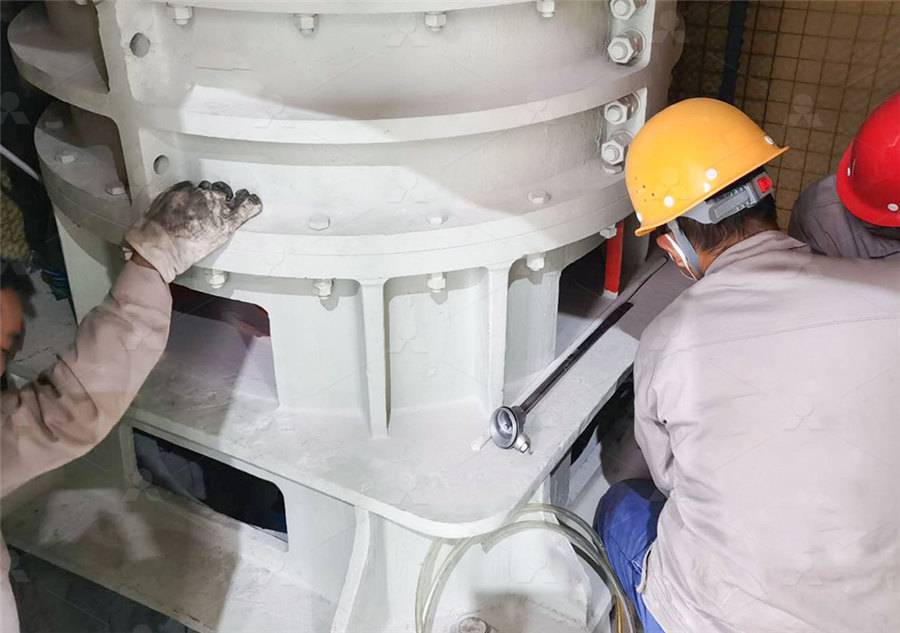
Grinding Ball Design 911Metallurgist
2017年11月6日 Grinding balls are essential mechanical components in ball and semiautogenous (SAG) mills Their function is crushing and grinding ore rocks weighing up to 45 kg (100 lb) preparatory to recovery of valuable minerals, from lead through rare earth elements, which are essential to the approaching 21st century technological societyReducing Grinding Energy and Cost Magnetite Iron Ore Design Case The performance of grinding mills depends on many operating factors among which are the time of grinding, mill speed, grinding media–toore of 3045 per cent was suggested to be possible (Valery and Jankovic, 2002), although significantly lover reductions, 913 per (PDF) Reducing Grinding Energy and Cost Magnetite Iron Ore Design 2020年7月23日 Optimization of stirred mill parameters for fine grinding of PGE bearing chromite ore, Particulate Science and Technology, DOI: 101080/2020 To link to this article: https://doi Optimization of stirred mill parameters for fine grinding of PGE 2014年8月20日 The dynamic analysis of grinding mill foundation is a typical problem of soilstructure interaction The substructure method is used to carry out the dynamic analysis and design in practiceDYNAMIC DESIGN FOR GRINDING MILL FOUNDATIONS
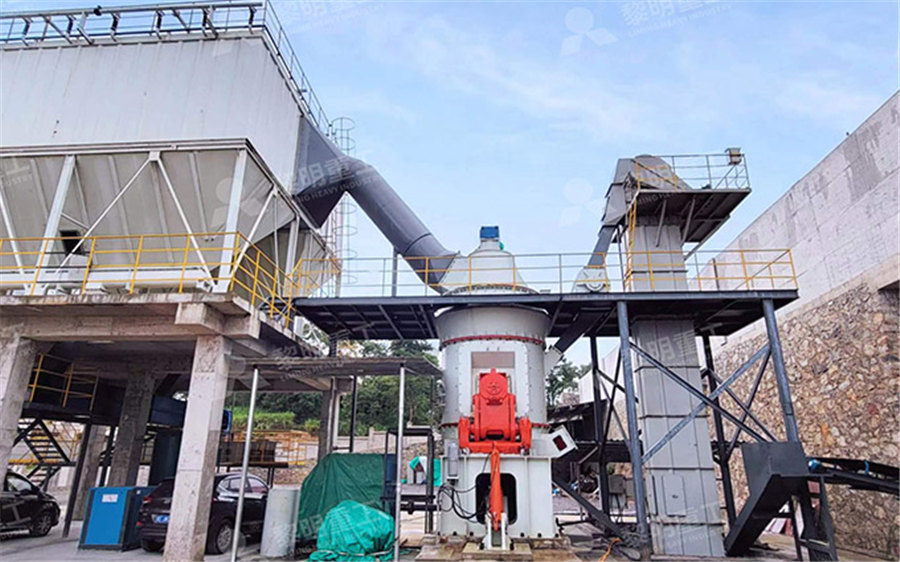
Semiautogenous grinding (SAG) mill liner design and development
grinding balls of up to 150 mm (6 in) in diameter These actions apply crushing, attrition and abrasion comminution processes to reduce primarycrushed ores down to ballmill sized feed Feed ore with a top size of up to 200 mm (8 in) and water enter the feed end of a SAG mill through a feed chute; the ore is milled in the shell and2021年1月12日 W Total = WSAG + W Ball Mill (2) Where W is the grinding mill work input in kWh/t For the above reason, the Starkey SAG mill was built in 1991 to measure the energy required to grind ore to a size of 80% passing 10mesh or 017 mm (T80) by grinding small drill core samples to precisely that sizeDESIGN OF THE KUBAKA GRINDNG CIRCUIT USING SPI AND BONDRequest PDF On Mar 15, 2015, Mathis Reichert and others published Research of iron ore grinding in a verticalrollermill Find, read and cite all the research you need on ResearchGateResearch of iron ore grinding in a verticalrollermill2016年6月6日 Grinding Mill Shell Design Because of the nature of the grinding media (large ore pieces) and lack of steel ball media, various white irons are used because of their high abrasion resistance and, if properly alloyed, 13 8 Kgm (1,0 00 ftlb) for irons SAG Mill Liner Design 911Metallurgist
.jpg)
Mineral Processing Design and Operations ScienceDirect
Mineral Processing Design and Operations An Introduction Book • Second Edition • 2016 Download all chapters About the book To liberate minerals from sparsely distributed and depleting the ore bodies finer grinding than generally obtained by the conventional Rod Mill –Ball Mill grinding circuits is neededThe Autogenous Mill, also known as AG Mill, is a type of grinding mill used in the mining industry This machine uses ore and rock itself as grinding media to perform its job Unlike other types of mills that use steel balls or rods for grinding materials, the Autogenous Mill relies on the material being ground to break itself into smaller piecesUnderstanding the SAG Mill in Copper Ore Mining Process2021年1月14日 Grinding Mill Design for the Tenke Project John Starkey1, Principal Consulting Engineer Comminution Tests, Bond Work Indices, JKTech, Grinding Mill Design, Database, Ore Hardness Measurements, JK Drop Weight Test, SAGDesign Test Bond Rod Mill Wi, kWh/t Hazen 127 135 70 101 119 125 113 Bond Ball Mill Wi, kWh/t Comparison of Ore Hardness Measurements for Grinding Mill Design 2023年7月20日 Therefore, the rod mill is mostly used for coarse grinding of the previous period of ball mill, or grinding of brittle materials and materials against overcrushing, such as tungsten and tin ore before gravity separation; and (3) autogenous mill – it refers to the materials which themselves are collided and ground mutually to be crushed when the grinding mill rotates, and Ore Grinding SpringerLink
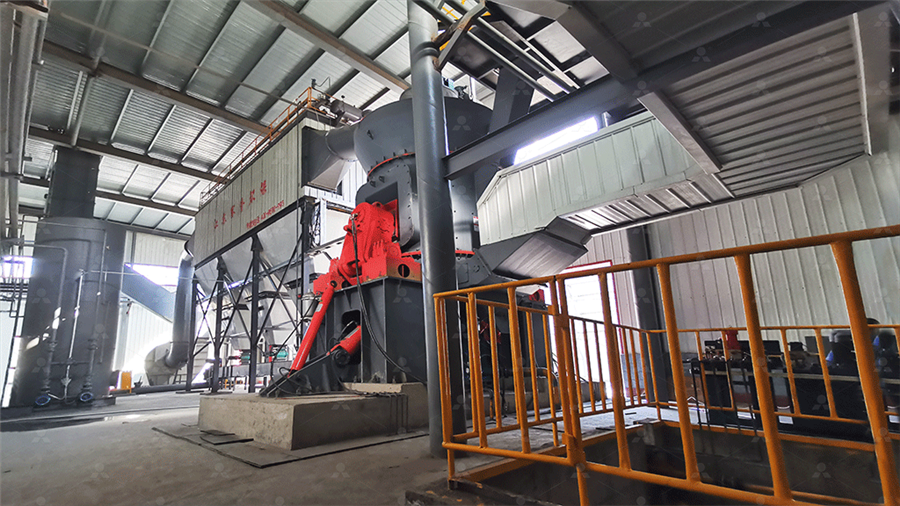
Ore Grinding Mill
Rod Mill The rod mill is loaded with steel bars as grinding media and comprises five parts: cylinder shell, feeding system, discharge system, main bearing, and transmission system It is suitable for both dry and wet grinding to meet customer needs Materials with a Moh's Hardness of 5512 can all be handled by our mill