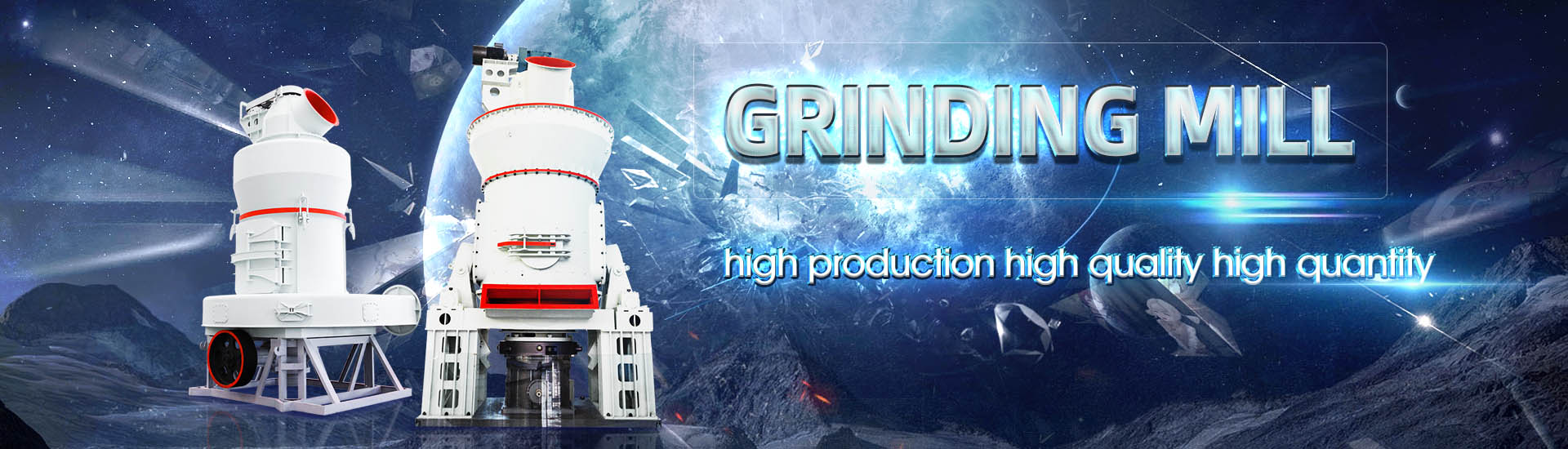
HOME→Cement production crushing and grinding process technology and equipment Cement production crushing and grinding process technology and equipment Cement production crushing and grinding process technology and equipment
Cement production crushing and grinding process technology and equipment Cement production crushing and grinding process technology and equipment Cement production crushing and grinding process technology and equipment
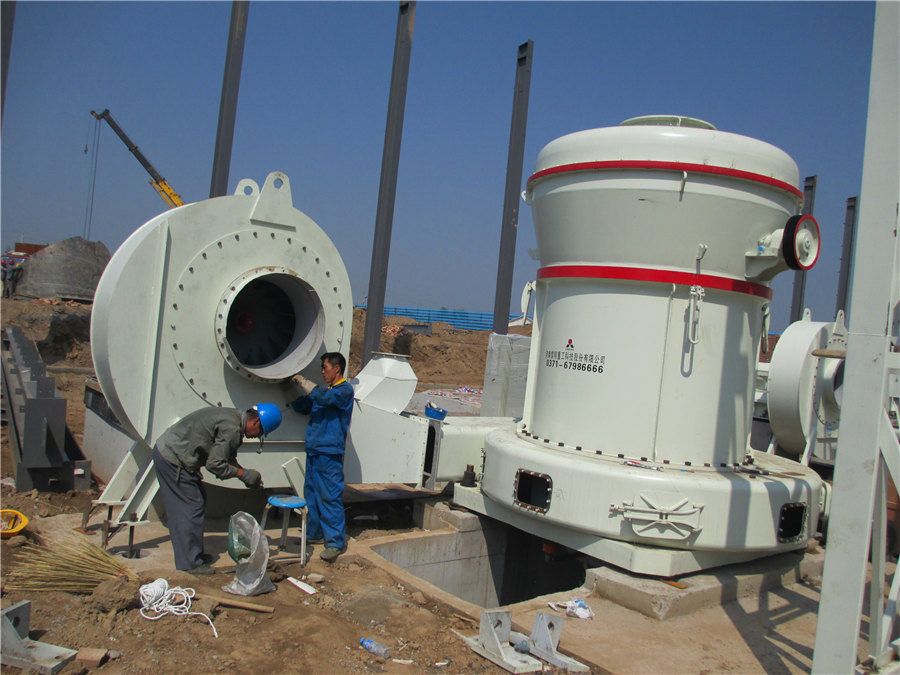
Cement grinding optimisation ScienceDirect
2004年11月1日 Precrushing of cement clinker using a Barmac crusher offers realistic benefits to a cement plant in terms of process efficiency The introduction of the Barmac crusher can 2006年11月1日 Several technologies and measures exist that can reduce the energy consumption of the various process stages of cement production including raw and finish (PDF) Pregrinding technology ResearchGateThe three broad processes of cement manufacturing are: Raw milling — the preparation of the kiln feed Calcining and burning or clinkering — the conversion process that takes place within The Cement Production ProcessThe cement production process 1 The Quarry: The cement production process begins with the extraction of limestone and clay from the quarry 2 Crusher and PreBlending: The material is A practical guide to improving cement manufacturing processes
.jpg)
Energy and cement quality optimization of a cement grinding circuit
2018年7月1日 Within the study, it was aimed to optimize both the energy utilization and the product quality of a conventional cement grinding circuit during CEM I 425R cement 2017年5月19日 PDF Grinding is an essential operation in cement production given that it permits to obtain fine powder which reacts quickly with water, sets in few Find, read and cite all the researchOverview of cement grinding: fundamentals, additives, 2016年10月5日 In this chapter an introduction of widely applied energyefficient grinding technologies in cement grinding and description of the operating principles of the related equip‐ ments and comparisons over each other in EnergyEfficient Technologies in Cement Grinding2023年8月21日 The grinding process is a critical stage in cement production and plays a significant role in the organisation’s operations and productivity Here’s how the grinding process fits into the cement production cycle and its Grinding process is a critical stage in cement production
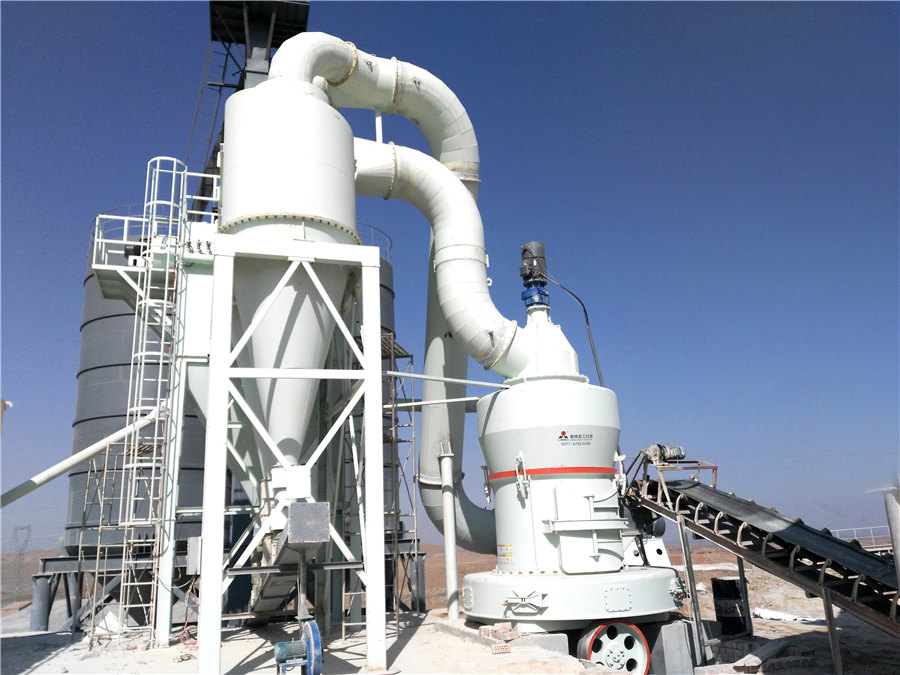
Cement Euipment Overview Cement Making
2019年9月27日 Cement equipment refers to the cement making machines that are applied to the cement manufacturing plant Before learning the cement equipment, we learn the process of cement manufacturing process first 2022年7月4日 responsible for cement production while the rest are subordinates The report focuses on three departments which are; Mining department, Production (Processing) department and QualityMining Activities, Cement Production Process and 2019年1月3日 Clinker grinding technology is the most energyintensive process in cement manufacturing Traditionally, it was treated as "low on technology" and "high on energy" as grinding circuits use more than 60 per cent of total energy Clinker grinding technology in cement manufacturing4 天之前 The manufacture of Portland cement is a complex process and done in the following steps: grinding the raw materials, mixing them in certain proportions depending upon their purity and composition, and burning them to sintering in a kiln at a temperature of about 1350 to 1500 ⁰C During this process, these materials partially fuse to form nodular shaped clinker by Manufacturing of Portland Cement – Process and Materials
.jpg)
Grinding in Ball Mills: Modeling and Process Control
2012年6月1日 Basic kinetic and energy models of the grinding process are described and the most commonly used control strategies are analyzed and discussed +1 Figures uploaded by Vladimir Monov2024年11月4日 A 6week modular course is designed to give the course attendee a solid understanding of the grinding system and its auxiliary equipment The purpose of the training is to Identify and understands necessary known and unknown information towards the completed cycle of the grinding system, whether it is a ball mill, vertical mill, or crushing processGRINDING TECHNOLOGY COURSE The Cement Institute76 4 Cement Manufacturing—Technology, Practice, and Development Fig 42 Modern dry process cement production process 424 Manufacturing of Cement Clinker The prepared raw material is called the “kiln feed” and is fed to the kiln In the kiln, this kiln feed is subjected to a thermal treatment process which consists ofCement Manufacturing—Technology, Practice, and DevelopmentCement Manufacturing Process by TIZITA MOGES , SELAMU ABULE DEREJE ENDALAMAW IF YOU NEED THIS GUIDE AND ALL OTHER USEFUL EXCEL SHEETS WHICH WILL MAKE YOU MASTER THE PRODUCTION , PROCESS , MAINTENANCE ACTIVITY IN YOUR CEMENT PLANT KINDLY CLICK HERE Raw Material Preparation and Cement Manufacturing Process INFINITY FOR CEMENT EQUIPMENT

Crushing and Grinding Process JXSC Machine
2019年10月8日 The crushing and grinding operations are an important part of the processing of mineral resources, and it is also operation with high investment and high energy consumption In the case of metal mines, equipment investment in crushing operations accounts for 65% to 70% of the total plant value, power consumption is about 50% to 65%, and steel consumption is as June 2022; ARCHIVE Proceedings of the Institution of Mechanical Engineers Part C Journal of Mechanical Engineering Science 19891996 (vols 203210) 236(2):1107(PDF) A comprehensive review on the grinding process: 2015年8月1日 The results show that approximately 248t, 469t, and 341t of materials are required to produce a ton of the product in raw material preparation, clinker production, and cement grinding stages Analysis of material flow and consumption in Description The cement grinding station with an annual output of 1 million tons adopts the technology of separately grinding clinker and slag, among which the clinker grinding adopts the combined grinding process composed of two Φ Cement Production Line,Cement Machine,Rotary
.jpg)
(PDF) CEMENT PRODUCTION PROCESS REPORT A
PDF On Apr 7, 2022, Alick Sinoya published CEMENT PRODUCTION PROCESS REPORT A SINOYA 1 Find, read and cite all the research you need on ResearchGateCement production is a complex process A batch of highquality cement needs many kinds of raw materials to be mixed together and then formed through layers of working procedures Problems occurred in any stage will affect the quality of the final products Clinker calcination is the core part of the cement manufacturing, in which raw materials Cement Clinker Calcination in Cement Production Process AGICO Cement After crushing, the crushed limestone is piled longitudinally by an equipment called stacker / reclaimer The stacker deposits limestone longitudinally in the form of a pile The pile is normally 250 to 300 m long and 810 m heightKnow all about cement manufacturing process in india mycem cement343 Cement production Cement production is one of the largest CO 2emitting industries globally, with the US contributing 643 MMT of CO 2 in 2014 [38] In 2014, the US produced 826 MMT of cement while the world produced a total of 4180 MMT China accounts for the majority of production, claiming 596% of global cement productionCement Production an overview ScienceDirect Topics
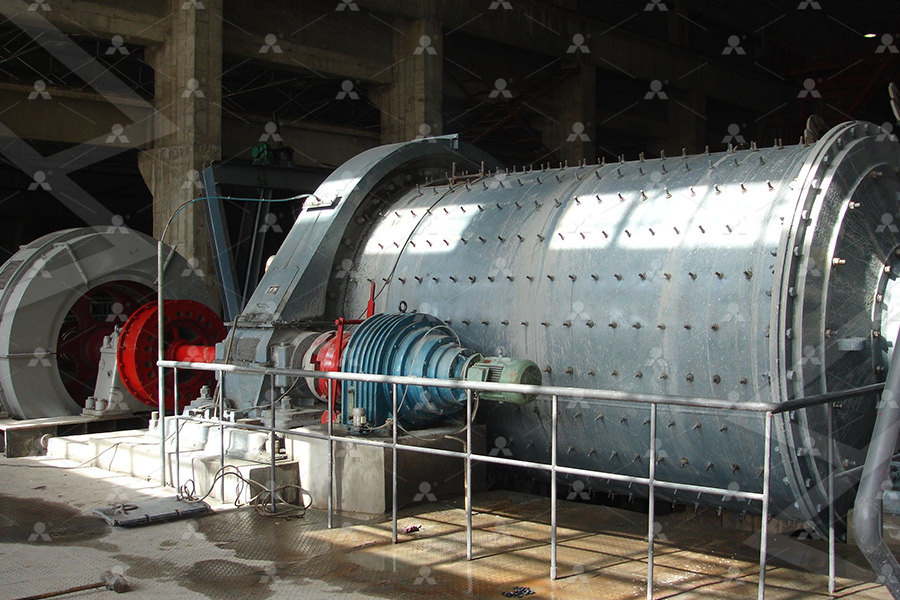
Cement Production Demystified: StepbyStep Process and
The use of fossil fuels such as coal, natural gas, and oil is common in cement production, both as a fuel for the kiln and as a source of heat for other parts of the process which leads to CO2 emitted by combustionHowever chemical reactions happening in the kiln (calcination) are also responsible for up to 60% of the total of emissions of the cement production process [PCA]2023年7月10日 Cement manufacturing is a significant industrial activity that plays a vital role in the construction sector However, the process of cement production is associated with various environmental Cement Manufacturing Process and Its Environmental Impact2016年10月5日 In this chapter an introduction of widely applied energyefficient grinding technologies in cement grinding and description of the operating principles of the related equip‐ ments and comparisons over each other in terms of grinding efficiency, specific energy consumption, production capacity and cement quality are given A case study per‐ formed on a EnergyEfficient Technologies in Cement Grinding2017年5月19日 Grinding is an essential operation in cement production given that it permits to obtain fine powder which reacts quickly with water, sets in few hours and hardens over a period of weeks i Overview of cement grinding: fundamentals, additives, technologies
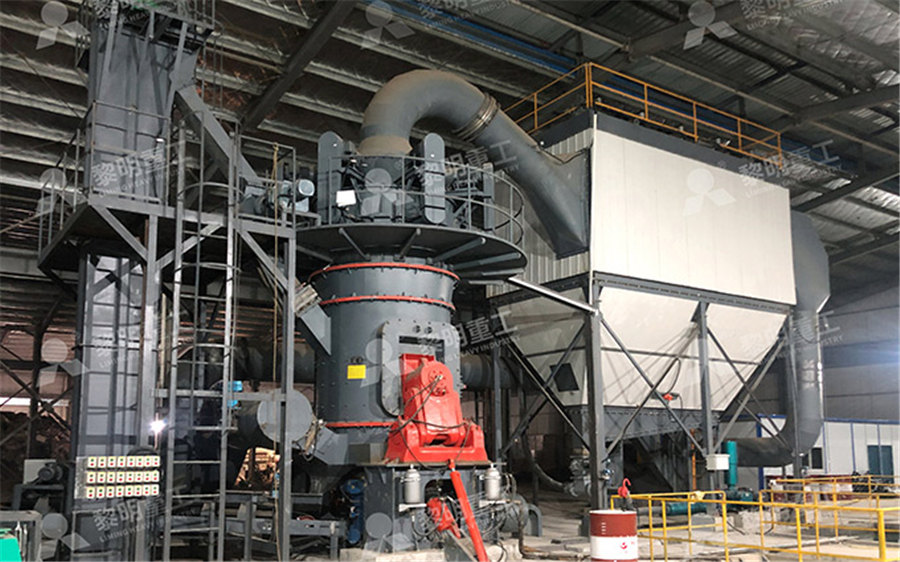
Cement manufacturing process PPT Free Download
2014年6月10日 Evolution of the cement Process • Wet process easiest to control chemistry better for moist raw materials • Wet process high fuel requirements fuel needed to evaporate 30+% slurry water • Dry process Each step of the cement production process is carefully monitored to ensure efficiency and quality Grinding, Mixing, and Blending The rock fragments are finely ground and combined with other ingredients including clay, chalk, marl, How Cement is Made Portland Cement Association2023年12月20日 Accurate cement production also depends on belt scale systems to monitor output and inventory or regulate product loadout, as well as tramp metal detectors to protect equipment and keep the operation running The Cement Manufacturing Process Thermo Fisher Stage 2: Grinding, Proportioning, and Blending The crushed raw ingredients are made ready for the cementmaking process in the kiln by combining them with additives and grinding them to ensure a fine homogenous mixture The composition of cement is proportioned here depending on the desired properties of the cement Generally, limestone is 80%, and the remaining 20% How Cement is Made Cement Manufacturing Process
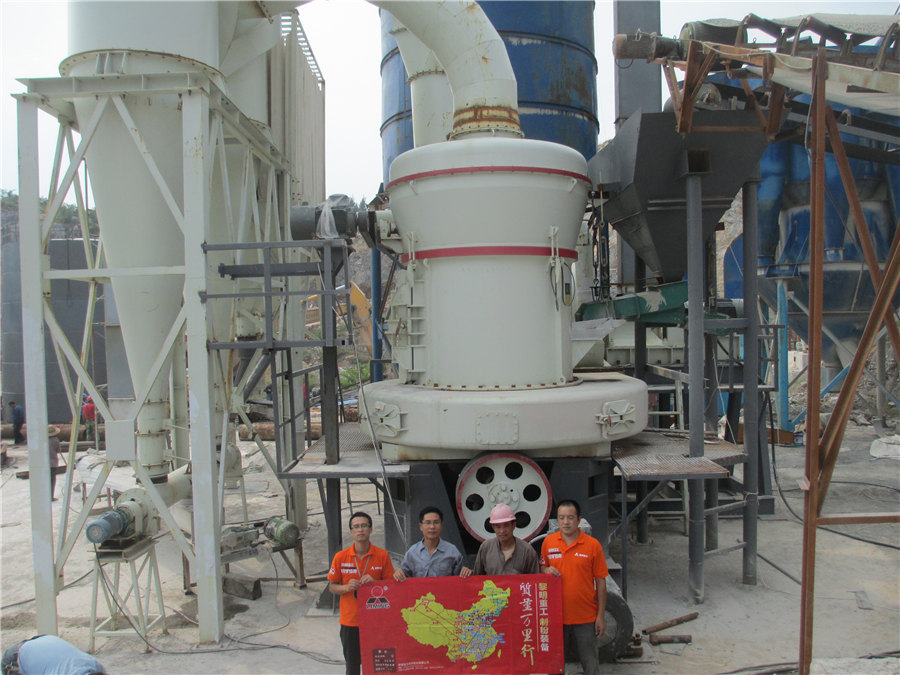
Cement Production Seminar: Grinding
Cement Production Seminar: Grinding Understand the fundamentals and gain insights on how to improve the performance and productivity, efficiency, and product quality of your grinding systems This 3day seminar covers ball and vertical mills with a focus oncomminution theory, design basis, operational principles, control and regulation, process troubleshooting, 2021年5月3日 In the paper, the energy potential of different fossil fuels is analyzed and the environmental aspect from pairing fossil fuels with refusederived fuel (RDF) in the cement production processEnergy and Economic Comparison of Different Fuels in Cement ProductionAGICO CEMENT is a cement plant manufacturer supplies cement equipment with high quality and competitive lime production, crushing plant and etc Cement grinding plants Cement manufacturing plants Mini Cement the material availability, the required output capacity, the process technology, your budgetary and financing status, the Cement Equipment, Cement Plant Equipment Cement Plant 2023年8月15日 Cement plays a pivotal role in the development and maintenance of urban infrastructure The substance in question finds application in the production of concrete and mortar, serving the purpose of fortifying the structural integrity of infrastructure through the process of binding individual building components togetherCement: History, Types, Manufacturing Process Science Info
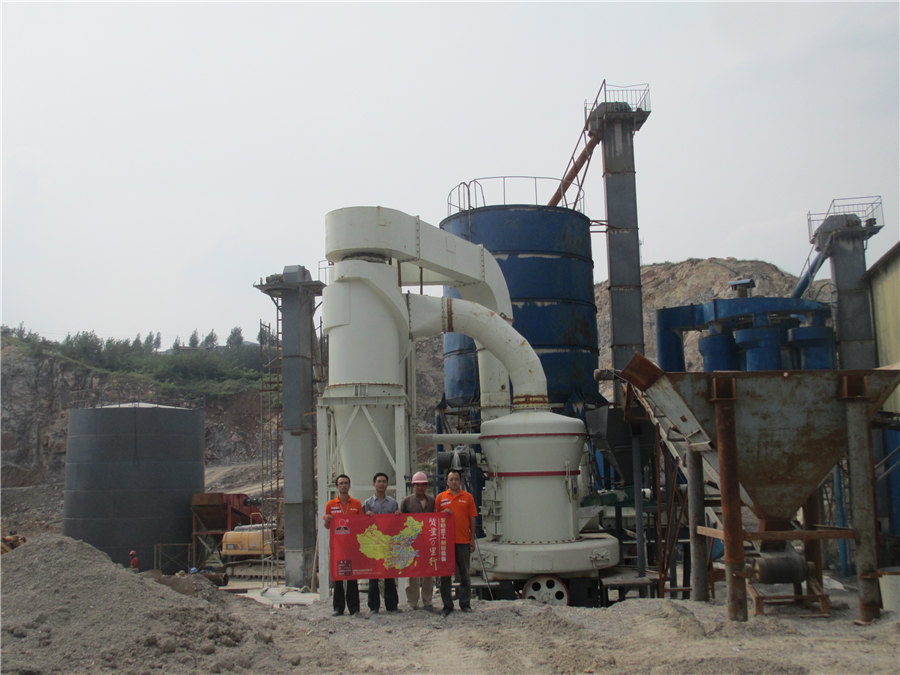
Cement Grinding Technology In Cement Production Process
2022年8月15日 Cement Grinding Technology in Cement Production Process English VersionIn this session I will explain about Cement Grinding Technology for cement productioA cement mill is just a general term for clinker grinding mill It is a kind of grinding equipment that used to grind the calcined cement clinker then make them reach the particle fineness requirement of the finished cement product It is the core equipment of the last step in the cement production process The cement mill we usually used in Cement Manufacturing Machine Cement Making Machine Cement Cement Production, Hard Crushing and Classifying Bearings for Rough Conditions Machines used in the production of cement aggregates operate in extremely harsh conditions that can result in costly downtime and reduced Cement Production, Hard Crushing and ClassifyingTechniques for proportioning and grinding raw materials Equipment used in this stage Word count: 1000; Section 2: Types of Cement Kilns Role in cement production Efficiency benefits Word count: 1000; Cooler Final thoughts on Comprehensive Guide to Cement Kilns: Processes,
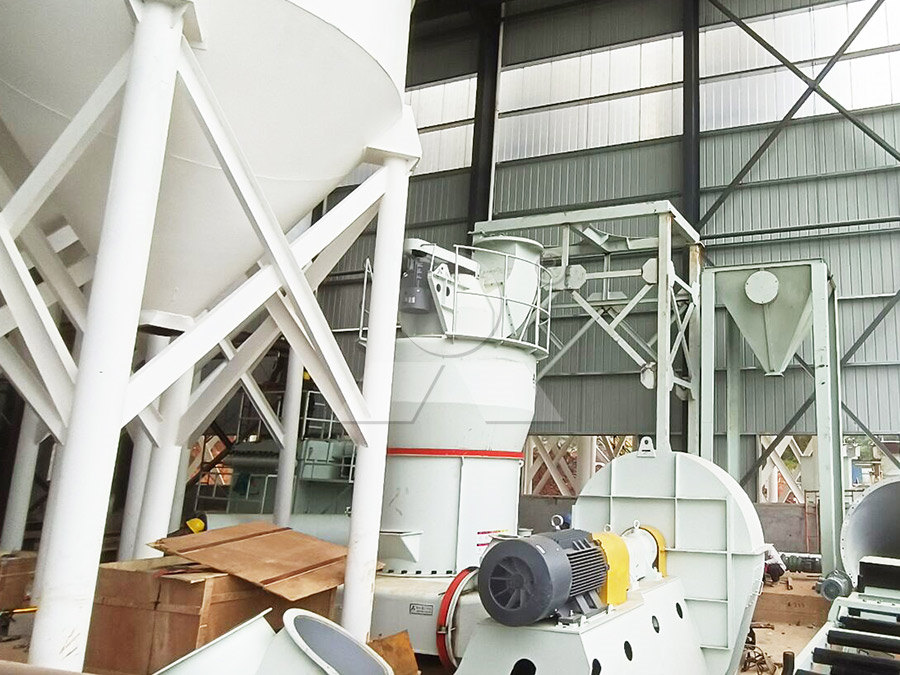
Manufacture of Cement Materials and Manufacturing
The grinding process can be done in ball or tube mill or even both Then the slurry is led into collecting basin where composition can be adjusted The slurry contains around 3840% water that is stored in storage tanks and kept ready Everything you need to know about clinker/cement Grinding if You read and understand this article , you will be ready to be a cement grinding area manager FEED AND FEED SYSTEM Feed Temperature Plants with satellite coolers have high clinker temperatures: eg Cumarebo, Oujda Exit satellite cooler 200250°C Exit grate cooler 100150°CEverything you need to know about clinker/cement GrindingDuring the Pyroprocess Operations and Maintenance training, participants will acquire the necessary knowledge, understanding, and jobrelated skills to handle and comprehend the technology and equipment delivered The process of technology transfer will be completed in a way that directly relates to the operation and maintenance of the equipmentCRUSHING AND GRINDING SEMINAR The Cement InstituteL G Austin, “A Review Introduction to the Description of Grinding as a Rate Process,” Powder Technol 5:1–17 (1971/72) Article Google Scholar L G Austin, R R Klimpel, and P T Luckie, The Process Engineering of Size Reduction: Ball Milling, AIME, New Size Reduction of Solids Crushing and Grinding Equipment
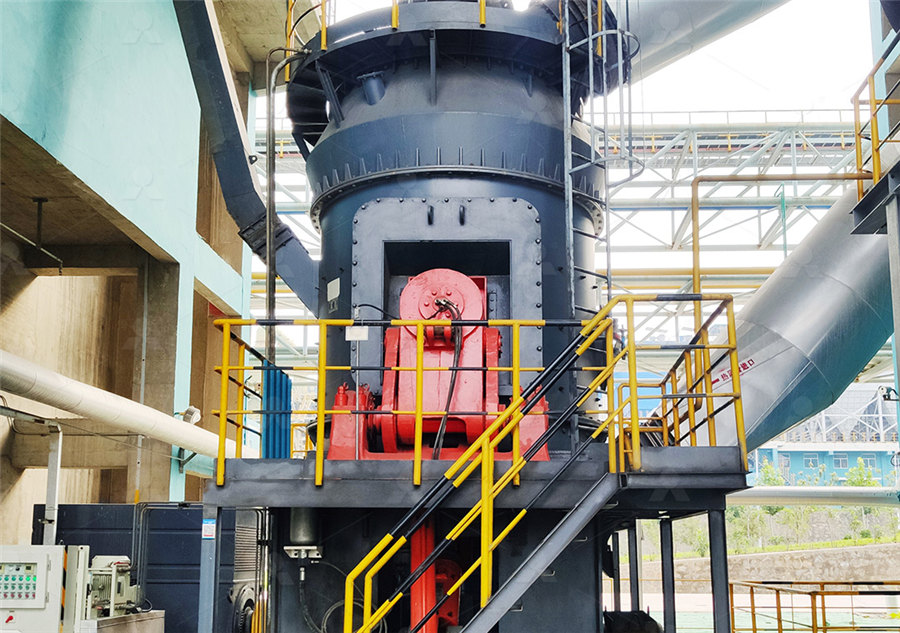
Cement Manufacturing—Technology, Practice, and Development
2021年11月17日 During the twentieth century, cement manufacture spread worldwide By 2019, India and China have become the world leaders in cement production, followed by Vietnam, the United States, and Egypt The primary cement manufacturing process involves the mining of raw materials, mainly limestone and clay, which are used in cement manufacturing2004年11月1日 The current world consumption of cement is about 15 billion tonnes per annum and it is increasing at about 1% per annum The electrical energy consumed in cement production is approximately (PDF) Cement grinding optimisation ResearchGate2016年1月20日 In the surveyed cement plant, three balances are established between input and output material in the raw mill, clinker production, and cement grinding system 248 t, 469 t, and 341 t of materials are required to produce a ton of the product in raw material preparation, clinker production, and cement grinding stages; waste gases account for the largest proportion of the Analysis of material flow and consumption in cement production process From the limestone quarry to the delivery of the end product, follow every step in the cement manufacturing process Step 1: Mining The cement Skip to main content Crushing, stacking, and The clinker is taken from the clinker storage to Manufacturing process Lafarge