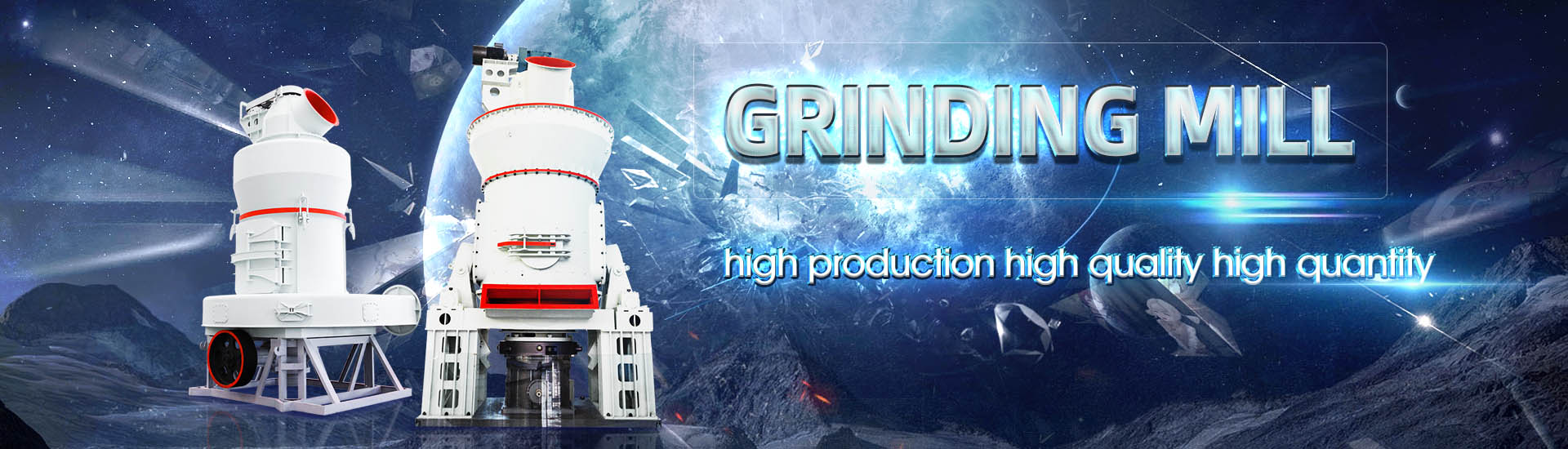
General operating procedures requirements for industrial roller mills
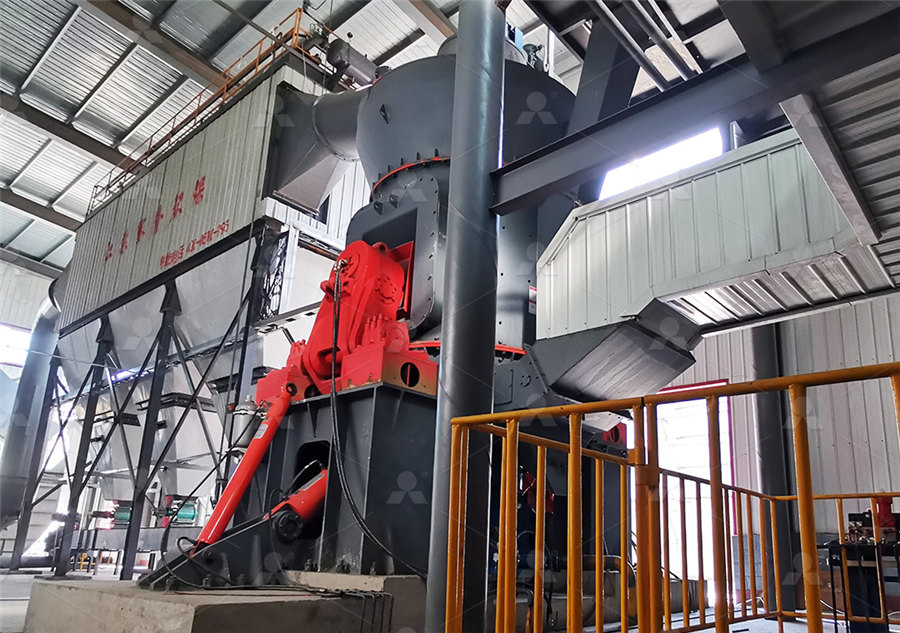
Rolling Mill Safety: Essential Guidelines for a Secure
2023年7月7日 This article presents comprehensive and practical general safety norms for rolling mills, providing valuable insights for businesses of all sizes By adhering to these safety guidelines, companies can safeguard their workforce Prior to commencing operation of the milling plant operators must familiarize themselves with all aspects of the mill and auger system to the operating instruction contained in the mill manual Safe Operating Procedures SOP 20 Feed Mill / Roller Mill Scope 11 Objective This standard operating procedure is intended to provide operating instructions and safety information for the Department of Mechanical Engineering’s rolling STANDARD OPERATING PROCEDURE AND SAFETY GUIDE FOR rolling operation III Rolling mill: To roll the hot crude steel products into desired shape by passing and squeezing it between set of revolving rolls The rolls may be plain or grooved rolls SAFETY GUIDELINES FOR IRON STEEL SECTOR MINISTRY OF
.jpg)
Roll Drive Design Considerations for Steel Mill Rolling Operations
Preventative maintenance procedures, spare parts procurement, system monitoring and rapid change out procedures are some design considerations for components critical to production III Rolling mill: To roll the hot crude steel products into desired shape by passing and squeezing it between set of revolving rolls The rolls may be plain or grooved rolls depending on product SAFETY GUIDELINES FOR IRON STEEL SECTOR Ministry of SteelIt begins with comprehensive coverage of rolling processes and the mechanics of rolling, which is the theoretical content of the subject This is followed by a chapter on ‘rolling practices’ that Principles and Applications of Metal RollingThe major contents of the handbook are fusion welding processes, grinding and abrasive processes, width change by rolling and pressing, metallurgical defects in cast slabs and hot Steel Rolling Technology Handbook (2nd Revised Edition)
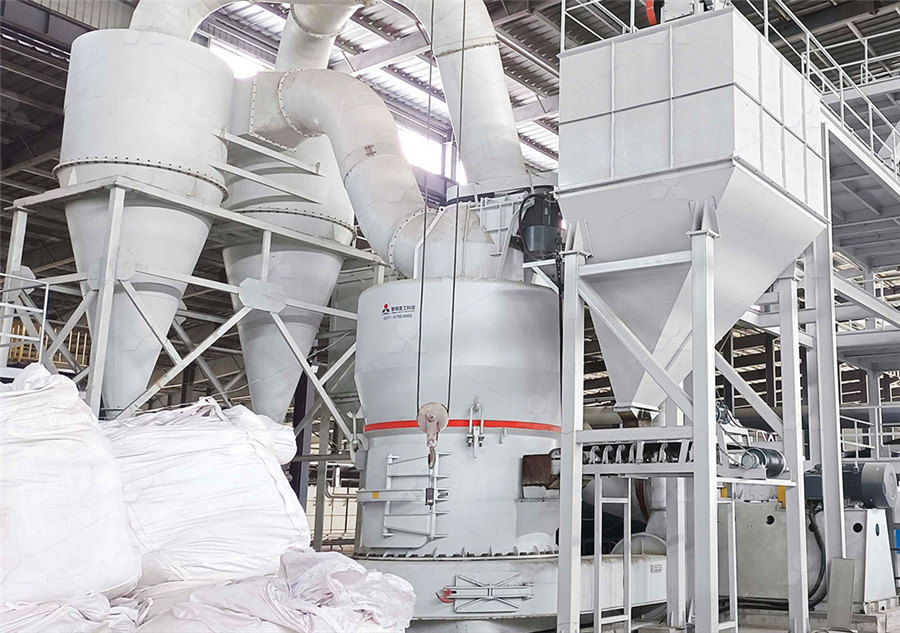
RISK ASSESSMENT AND SAFE ACCESS MANAGEMENT IN LONG
Description of the solution for safe access to bars production rolling mill line The safe access in various areas could be achieved in several Operating Modes of the production line locally, 2011年3月13日 The general level of operating noises can be around 8490dBA, and peaks up to 115 dBA or more are not unusual See the article “Iron and steel making” for information on Rolling Mills ILO Encyclopaedia of Occupational Health and SafetyPDF On Jan 1, 2017, J Harder published Drives for large vertical roller mills Find, read and cite all the research you need on ResearchGate(PDF) Drives for large vertical roller mills ResearchGateAn SOP (Standard Operating Procedure) Manual for Iron and Steel Mills and Ferroalloy Manufacturing is notably noteworthy within the heavy industry and metallurgical sector for several significant reasons: Safety: This manual SOP Manual for Iron and Steel Mills and Ferroalloy
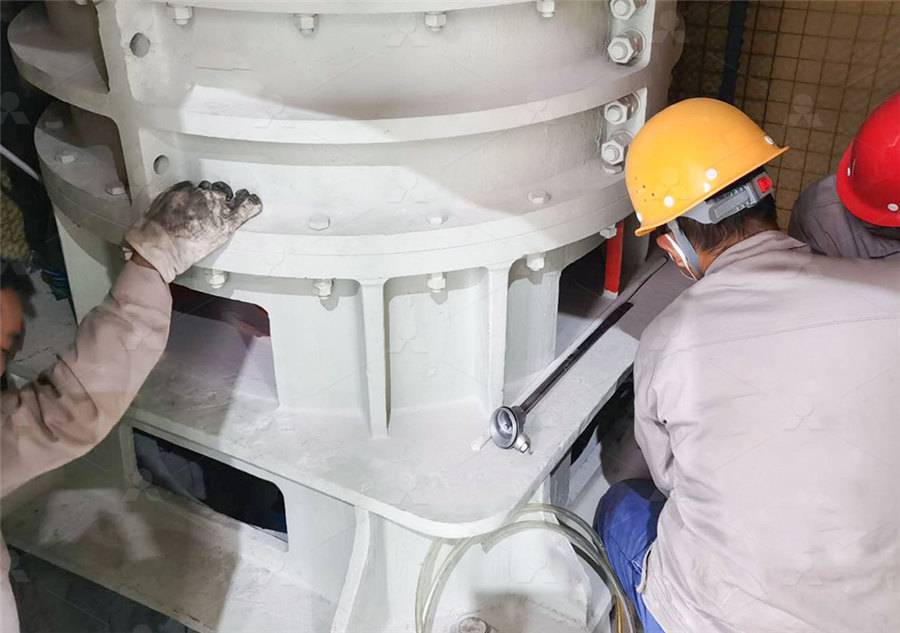
BALL MILLS Ball mill optimisation Holzinger Consulting
and cement Roller presses are used mainly in combination with a ball mill for cement grinding applications and as finished product grinding units, as well as raw ingredient grinding equipment in mineral applications This paper will focus on the ball mill grinding process, its tools and optimisation possibilities (see Figure 1) The ball mill2020年7月10日 What’s a Standard Operating Procedure (SOP)? A standard operating procedure, or SOP, is a set of detailed stepbystep instructions that describe how to carry out any given process Most companies that are serious about process management use SOPs to manage their daytoday activities Why? Well, Standard Operating Procedures allow you to:Standard Operating Procedure (SOP) Guide ExamplesProper ventilation system is not a requirement for the operation of rolling machine 33 Kinetic, Thermal and Acoustic The moving parts of the rolling machine consist of plain and threaded roller pairs and an output shaft Do not wear loose clothing and be certain to tie back long hair when operating the rolling machineSTANDARD OPERATING PROCEDURE AND SAFETY GUIDE FOR High Shock Load Capabilities: It is no surprise that this is a critical design element for a reducer operating in a steel mill Nonuniform and heavy shock loads are considered normal operating conditions Many design engineers handle this requirement by increasing the service factor of the gearbox According to the AmericanRoll Drive Design Considerations for Steel Mill Rolling Operations
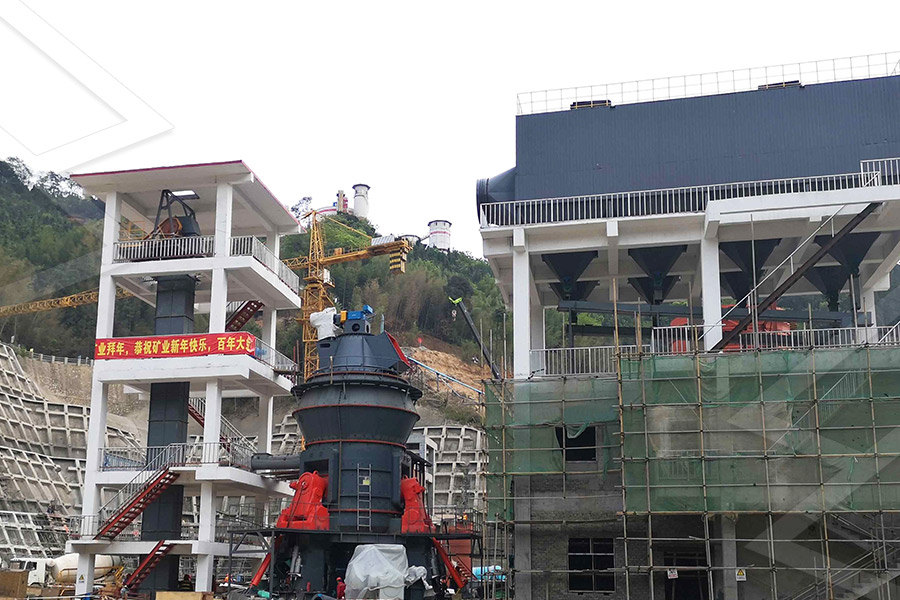
RAYMOND® ROLLER MILLS Thomasnet
Raymond Roller Mills: More than 2,000 roller mills have been supplied since the first mills were designed in the late 1800’s These early machines were the forerunner of the heavyduty, rugged ringroll mill manufactured today The roller mill provides the needed flexibility to economically and efficiently process a wide variety of materialsFig 2 Modular Vertical Roller Mill 5000 R4 Installed in Canada Fig 3 Modular Vertical Roller Mill 5000 R4 Installed in Canada V Operational Experience with Modular Vertical Roller MillsGrinding Process Optimization Featuring Case Studies and Operating requirement of the tests generally increases with top size, with the media competency (150mm rocks) being at the top of the requirement scale The work index series (ball mill, rod mill, and MacPherson autogenous) and pilot plant tests require relatively more weight (for a given top size) because they are run until a steadystate is achieved, whichSAG Mill Testing Test Procedures to Characterize Ore GrindabilityGeneral requirements for all machines GPO Source: eCFR 1910212(a) Machine guarding 1910212(a)(1) so designed and constructed as to prevent the operator from having any part of his body in the danger zone during the operating cycle 1910212(a)(3)(iii)1910212 General requirements for all machines
.jpg)
Grain Roller Mills Automatic Equipment
Automatic's industrial grain roller mills produce precise particle size every time, even when it comes to high volume grain processing – as much as 15,000 bushels an hour for our hardestworking, highcapacity models4 SikaGrind® FOR VERTICAL ROLLER MILLS Pilot Mill (Picture: Loesche GmbH, Germany) The production of Portland Cement (OPC, CEM I) with Vertical Roller Mills can demand the following benefits from a Grinding Aid: ́ Increased production rate, energy saving ́ Higher fineness, faster strength development ́ Reduced vibration, less wearSikaGrind® for vertical roller millsroller mill tests of your material in the manufacturer’s test facility with various roll corrugation styles and under conditions that duplicate your operating environment Figure 1 Particle size distributions: Roller mill versus other grinding methods Other grinding methods Roller mill Overs Target particle size Fines Figure 2Roller mills: Precisely reducing particle size with greater efficiency"Bridgeport" style mills, these versatile mills are capable of performing many operations, including some that are similar to those performed on the drill press like drilling, reaming, countersinking, and counter boring Other operations performed on the mill include but are not limited to side and face milling, fly cutting, and precision boringMILLING MACHINE TRAIN THE TRAINER (SAFETY, PARTS
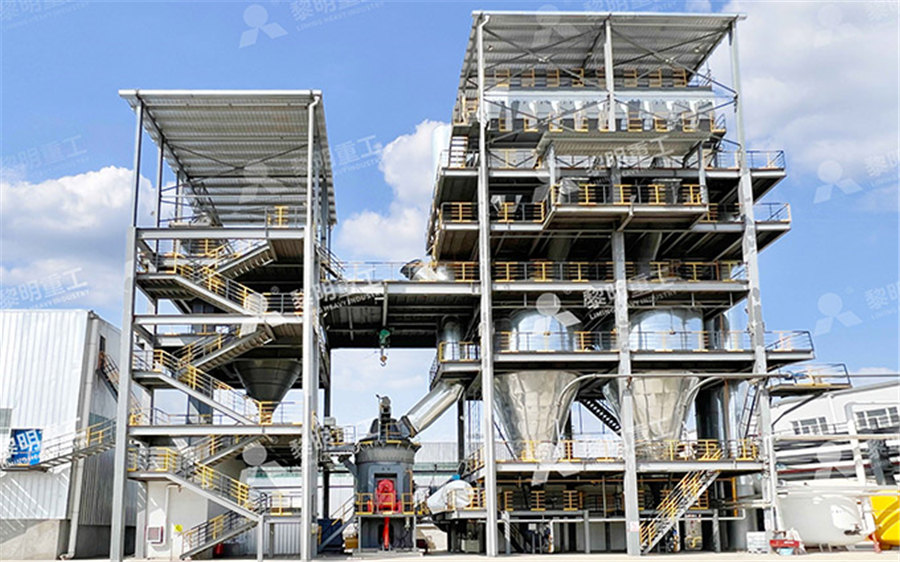
Standard Operating Procedure (SOP) Examples SafetyCulture
2024年7月31日 Standard Operating Procedures (SOPs) are essential documents that outline the steps necessary to perform specific tasks consistently within an organization They serve as a guideline for employees, making sure that processes are executed properly across various functions, which is important for meeting quality standards and ensuring compliance with themMore highquality output with optimized solutions for hot rolling mills Despite the everyday challenges of heat, lots of cooling water and highimpact forces, hot rolling mills are expected to continuously increase output while maintaining and improving the quality of the finished productHot rolling mill SKF2012年3月1日 Vertical roller mills are the mills traditionally used for processing granulated blastfurnace slag and for grinding composite cements From the energy aspect they are superior to grinding plant Operating experience with a vertical roller mill for grinding doors Requirements'), – EN 12445 ('Industrial, commercial and garage doors and gates Safety in use of power operated doors Test methods'), Requirements for the owner of the door system: – Familiarity with and safekeeping of the operating manual – Knowledge of the general safety and accident prevention regulationsInstallation, Operating and Maintenance Instructions for Industrial
.jpg)
VERTICAL ROLLER MILLS A holistic VRM approach
n by M Hastrich and P Guerrero Palma, thyssenkrupp Industrial Solutions, Germany VERTICAL ROLLER MILLS 1 SEPTEMBER 2021 INTERNATIONAL CEMENT REVIEW P ut simply and briefly, thyssenkrupp’s quadropol® vertical roller mill (VRM) remains one of the leading VRMs in the market in terms of its simple and compatible design structure RequirementsThis standard operating procedure describes using a ball mill and sieve columns to separate an ore sample by size First, a sieve column is used to separate different sizes of untreated ore Then a ball mill is used to grind down a portion of the ore sample The sieve column is used again to separate the ball milled sample by size Results are recorded in a table and graph showing the Standard Operating Procedure For Ball Mills and Sieve Columns2 Rolling Mills Revamp: Roll Upgrades for Extreme Loads Introduction Market Overview Today’s rolling mill market environment can be characterized by low investment in new equipment and higher requirements for output The mills are getting older, but to increase productivity, their operational loads are becoming much heavierTechnical Article Rolling Mills Revamp Timken Company2020年8月12日 This study shows the performance of a currently running vertical roller coal mill (VRM) in an existing coalfired power plant In a power plant, the coal mill is the critical equipment, whose An investigation of performance characteristics and
.jpg)
General Safety Norms for Rolling Mills Steefo
Rolling mills play a crucial role in the steel industry, enabling the shaping and processing of metal materials As businesses consider investing in rolling mill machinery or upgrading their existing infrastructure, it is imperative to prioritize SOP471038: Standard Operating Procedure for Industrial Hygiene Monitoring SOP471039: Standard Operating Procedure for Bloodborne Pathogens SOP471040: Standard Operating Procedure for Welding and Cutting Safety SOP471041: Standard Operating Procedure for Crane and Hoist SafetyStandard Operating Procedures (SOP) Manual for SafetyHSS rolls, often installed in the earlier stands of hot strip mills, provide improved wear resistance along with a better surface roughing resistance However, HSS are rolls more sensitive during operation and require a higher grade of attention with regard to roll cooling than HighCr rolls HSS rolls need an adequate mill operating environmentGENERAL ASPECTS OF ROLL COOLING FOR HOT COLD ROLLING MILLS the foundation of the mill goes directly through the gearbox, which must be taken into account while designing the gearbox Fig 2: General setup of gearbox for vertical mill 12 Requirements on the gearboxes The main gearbox is an integral part of the complete mill equipment, and the requirements of the millA New Gearbox Generation for Vertical Roller Mills Artec Machine
.jpg)
Grain Roller Mills RMS RollerGrinder
Farmers who grow soy, oats, wheat, barley, and corn (the country’s primary feed grain) rely heavily on a feed roller mill for processing their grainA roller mill’s capacity to grind large volumes of various materials makes it ideal for producing highquality feed for staples of the American diet—beef, poultry, and porkAdditionally, flours produced by a roller mill are essential for Singleroller mill With the singleroller mills, brittle, soft to mediumhard materials can be reduced in size with a reduction ratio of approx 1:5 to 1:5 The stepped arrangement of the crushing jaws on the crushing wall enables any material rolling off being minimised, so that, compared to the doubleroller mill, coarser material can be Roller Mills SIEBTECHNIK TEMA2024年8月6日 While the process of developing roller milling came into existence in the 19th century, it took an industrial revolution to make roller flour mills the most common flour mills today The arrival of automatic machinery, forced by steam and like electricity, put the wheel of grain processing on the move, achieving higher yields and cleaner flour qualityRevolutionizing Flour Production: The Development and thyssenkrupp is one of the few fullrange suppliers for the cement industry – from individual machines, all the way up to complete cement plants, and this since decades The market requirement is easy to define Present kiln lines have capacities of up to 10,000 tons per day Kiln lines of 12,000 tons per day were already built by polysius ® technologyquadropol® thyssenkrupp Polysius Grinding Technologies
.jpg)
Machine Safety, Chapter 296806, WAC Labor Industries
Other General Workplace Safety Health Rules WAC 29680620008 Make sure operating controls meet these requirements 14 WAC 29680620010 Protect employees from unintentional machine operation WAC 29680642069 Slat and rollerslat conveyors FeedSafe® accredited feed mills will have procedures in place for managing and minimising food safety risks (eg Salmonella) within the stock feed being produced These procedures are also considered good practice for feed mill biosecurity during the manufacturing process Purpose of NATIONAL BIOSECURITY MANUAL FOR FEED MILLSThe vertical roller mill (VRM) is a type of grinding machine for raw material processing and cement grinding in the cement manufacturing processIn recent years, the VRM cement mill has been equipped in more and more cement Vertical Roller Mill Operation in Cement PlantTitle General Security Procedure for Manufacturing Area Prepared by: Date: Supersedes: Checked by: Date: Date Issued: Approved by: Date: Review Date: 10 AFFECTED PARTIES All Environment, Health and Safety personnel 20 PURPOSE To detail the General Security Requirements and Procedures for persons entering the site to access the BuildingsGeneral Security Procedure for Manufacturing Area
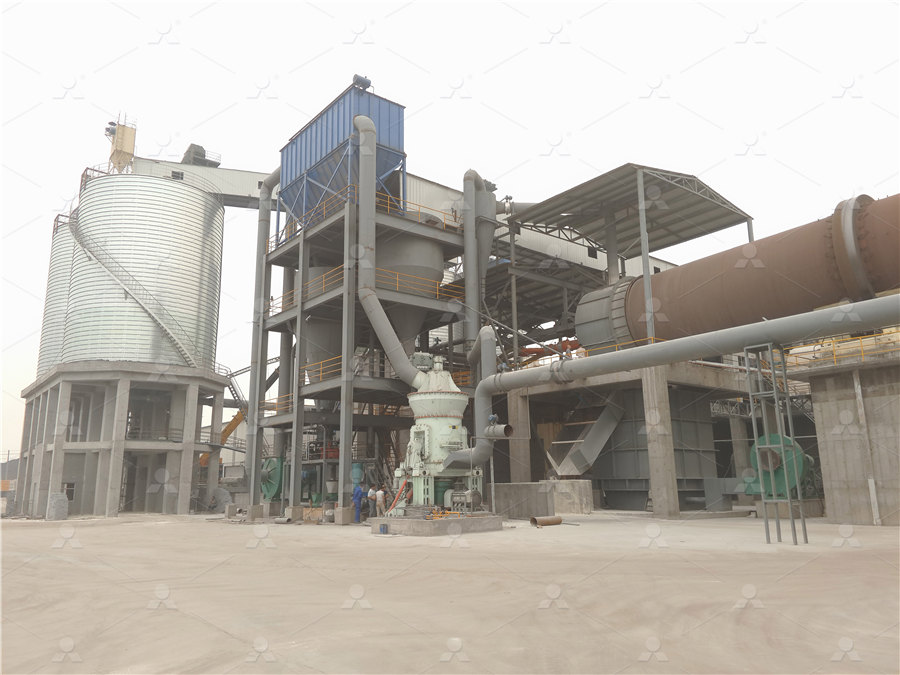
RENN Roller Mills High Performance Grain Processing Grain
RENN is the leader in roller mills, grain processing, hammer mills, Elevator Discharge, Crimper Mill, Blower Discharge Mill power, and discharge options PTO models have a minimum power requirement of 15 to 120 horsepower, while Electric Stationary units operate with a minimum power requirement of 5 to 50 horsepower Discharge Systems 2017年1月17日 AgnicoEagle Goldex Division, Mine Canadian Malartic, and New Gold New Afton Mine participated in the study by providing operating data for 3 semiautogenous grinding (SAG) mills and 4 ball millsBreaking down energy consumption in industrial grinding millsenergy practitioners for incorporating energy efficient options in their regular operating procedures The total energy consumption of Indonesia in the year 2012 was about 162 million tonnes of oil equivalent Industrial sector contributes to the final energy consumption of 299%, closely followed by households (285%) and transportation (268%)Energy Efficient Technologies and Best Practices in Steel Rolling 2024年9月23日 For bearings operating under normal conditions, a general guideline is to relubricate every 3 to 6 months However, this interval may need to be adjusted based on specific application requirements Bearings operating in harsh environments, high temperatures, or under heavy loads may require more frequent lubrication, possibly as often as every 1 to 3 monthsWhat are the Maintenance Procedures for RB Cross Roller Bearings?
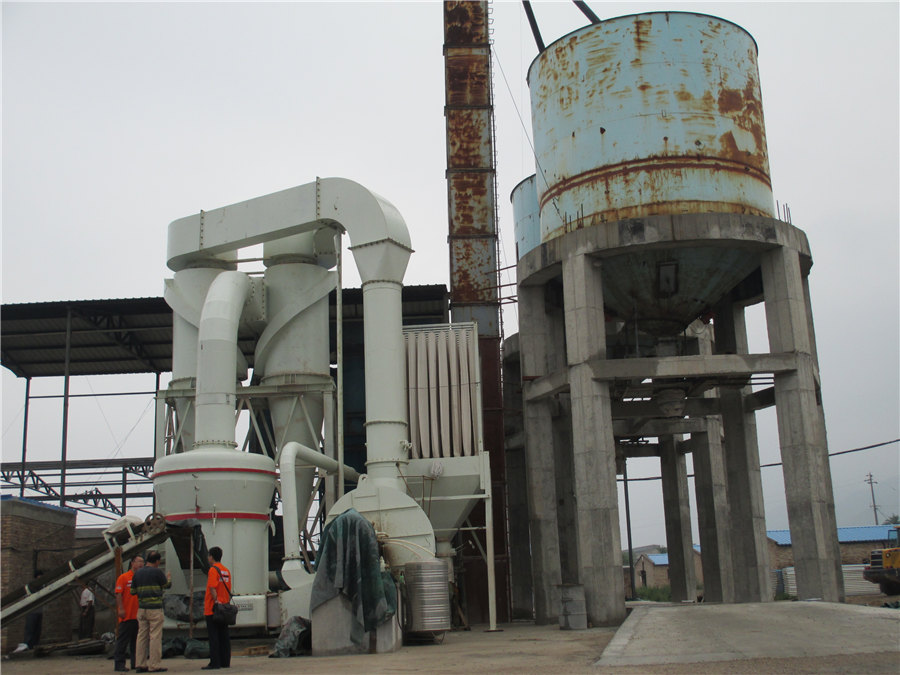
Principles and Applications of Metal Rolling
42 Mill Drive 229 421 Mill couplings 229 422 Gear box and pinion stand 232 423 Spindles 237 424 Rolling mill electrics 241 43 Auxiliary Equipment and Systems 252 431 Shears and saws 252 432 Straightening and leveling machines 259 433 Coilers and decoilers 263 434 Roller table 271 435 Miscellaneous equipment 276PARAMETERS ON VERTICAL ROLLER MILLS’ as a Partial Fulfilment to the Requirements for the Award of the Degree of Master of Science in Mining Engineering works were performed to investigate the influences of the design and operating parameters on vertical roller mill grinding performance In this context, systematicINVESTIGATION OF EFFECT OF OPERATIONAL PARAMETERS ON VERTICAL ROLLER