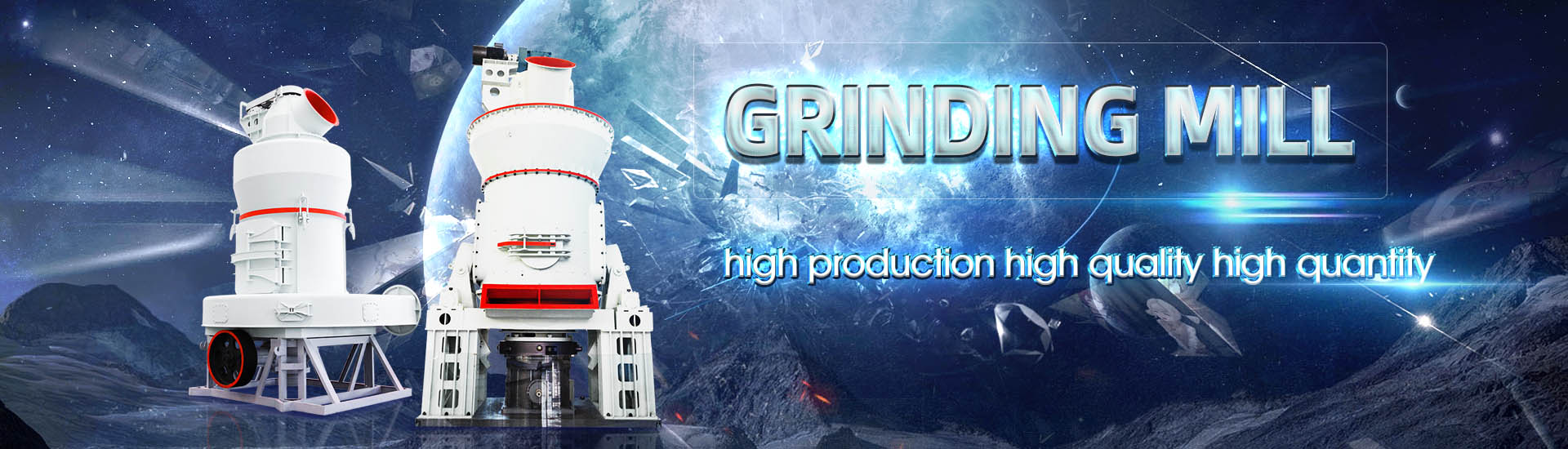
Matching ratio of cement ball mill
.jpg)
BALL MILLS Ball mill optimisation Holzinger Consulting
Ball mills and grinding tools Cement ball mills are typically twochamber mills (Figure 2), where the first chamber has larger media with lifting liners installed, providing the coarse grinding stage, whereas, in the second chamber, medium and fine grinding is carried out with smaller media Clinker, Gypsum and other desired additives are fed to the ball mill in specific proportions based on the quality requirement Feed material is ground in the ball mill, discharged and fed to a OPTIMIZATION OF CEMENT GRINDING OPERATION IN BALL MILLSconsumption for a typical 3500 Blaine ordinary portland cement (OPC) Roller press finish‐grinding systems, due to lower fan power ement compared to VRM or ball mill, no Thomas Holzinger, Holzinger Consulting, grinding system Optimization of a ball charge for cement and raw mills with objective of optimizing the grinding efficiency The ball charge in first and particularly in the second compartment, will be adapted Ball charge optimization INFINITY FOR CEMENT EQUIPMENT

PROCESS DIAGNOSTIC STUDIES FOR CEMENT MILL
HOLTEC has undertaken Performance Optimisation of the cement grinding circuits by doing process diagnostic studies in many cement plants The paper describes the approach for the 2022年11月1日 In numerous cement ball mill operations (Genc, 2008, Tsakalakis and Stamboltzis, 2008, Altun, 2018, Ghalandari and Iranmanesh, 2020), the ratio of maximum ball Impact of ball size distribution, compartment configuration, and 2004年12月10日 The L/D ratio of the ball mill was varied in four steps of 175, 21, 279 and 349, and the ball charge filling ratio was varied in three steps of 15%, 20% and 25% The Optimization of continuous ball mills used for finishgrinding of 2012年6月1日 PDF The paper presents an overview of the current methodology and practice in modeling and control of the grinding process in industrial ball mills Find, read and cite all the research you Grinding in Ball Mills: Modeling and Process Control
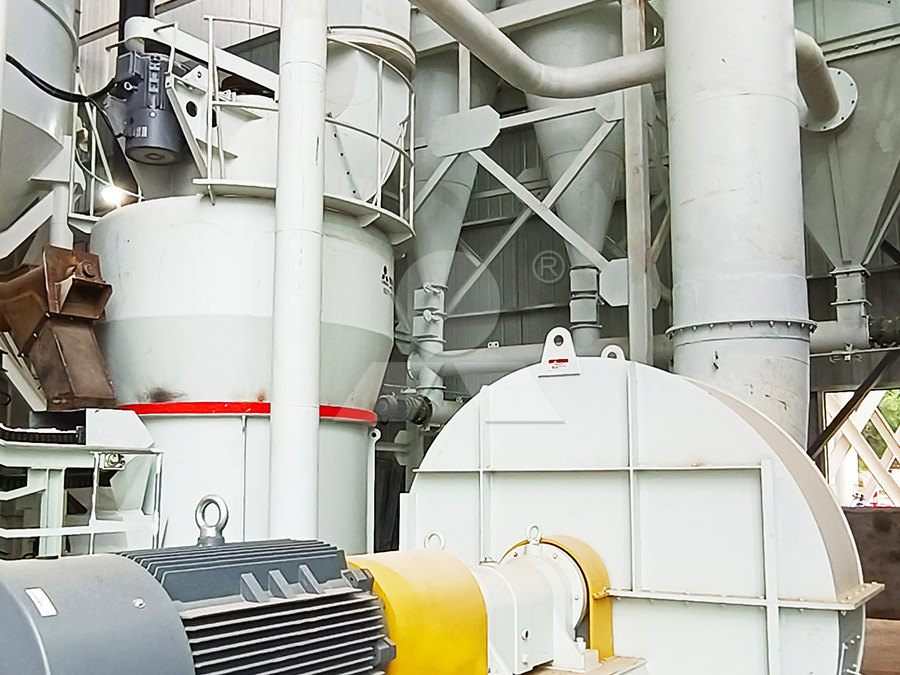
A comparison of wear rates of ball mill grinding
2016年1月1日 The wear of balls used during a grinding process is considered one of the losses that cause an increase in the operating cost allocated to the ball mill [21]BALL MILL OPERATION Ball mills for finish grinding cement usually consist of two compartments An intermediate diaphragm separates both compartments from each other The 1 compartment is filled with coarser balls and lifting Process Training Ball Mill INFINITY FOR CEMENT 2020年7月2日 A comprehensive investigation was conducted to delineate the effect of ball size distribution, mill speed, and their interactions on power draw, charge motion, and balls segregation in a (PDF) Effects of Ball Size Distribution and Mill Speed and Their 2021年6月29日 The research focuses on the mill speed as well as air classifier speed effect on the two compartment Cement ball mill Φ40 mm 1538%; filling ratio of 32%; material ball ratio of 10 Effects of Mill Speed and Air Classifier Speed on Performance of
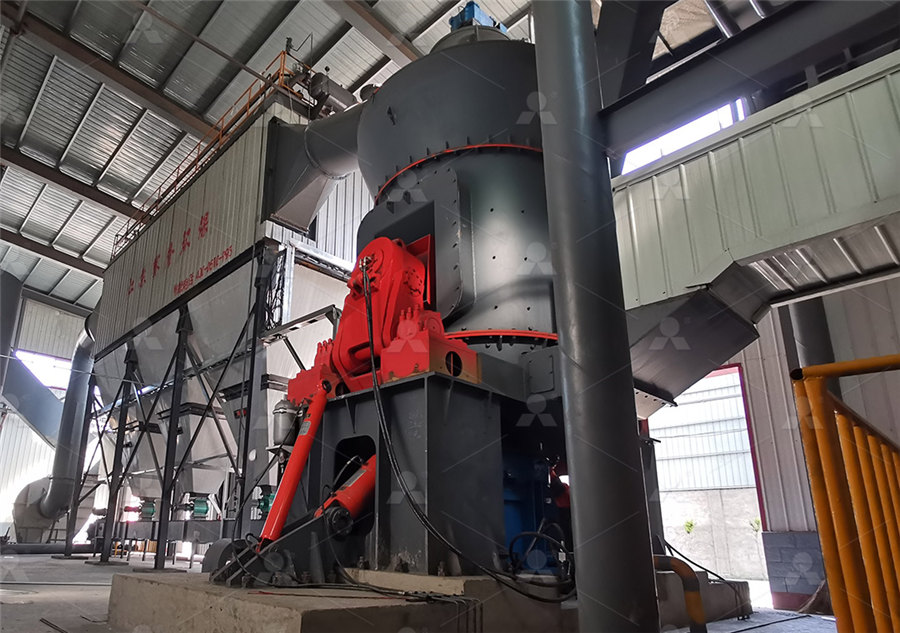
17 Signs of Problems with Ball Mills: Quickly Remove Hidden Troubles
2023年2月15日 High temperature of the ball mill will affact the efficiency 3 For every 1% increase in moisture, the output of the ball mill will be reduced by 8% 10% 4 when the moisture is greater than 5%, the ball mill will be unable to perform the grinding operation 5 The bearing of the ball mill is overheated and the motor is overloaded Reasons2015年6月19日 Now we much select a Ball Mill that will draw this power The ball mill motor power requirement calculated above as 1400 HP is the power that must be applied at the mill drive in order to grind the tonnage of feed from one size distribution The following shows how the size or select the matching mill required to draw this power is calculated Ball Mill Design/Power Calculation 911MetallurgistTypes of cement mills There are basically 4 types of cement mills in use today: Ball Mill (BM) Ball Mill (BM): predominant despite higher energy consumption partly because of historical reason but partly also because it still offers considerable advantages over other mills, often operate with roller press for pregrinding or in combined grinding;Improvements in New Existing Cement Grinding Mills by Tim 2023年8月23日 The production process of a cement ball mill involves raw material preparation, grinding, linearization, clinker grinding, and the eventual storage and distribution of the finished cement product This process is integral to the production of cement, a vital building material that plays a central role in construction and infrastructure development around the worldWhat Are the Parts of a Cement Mills? Cement Ball Mill
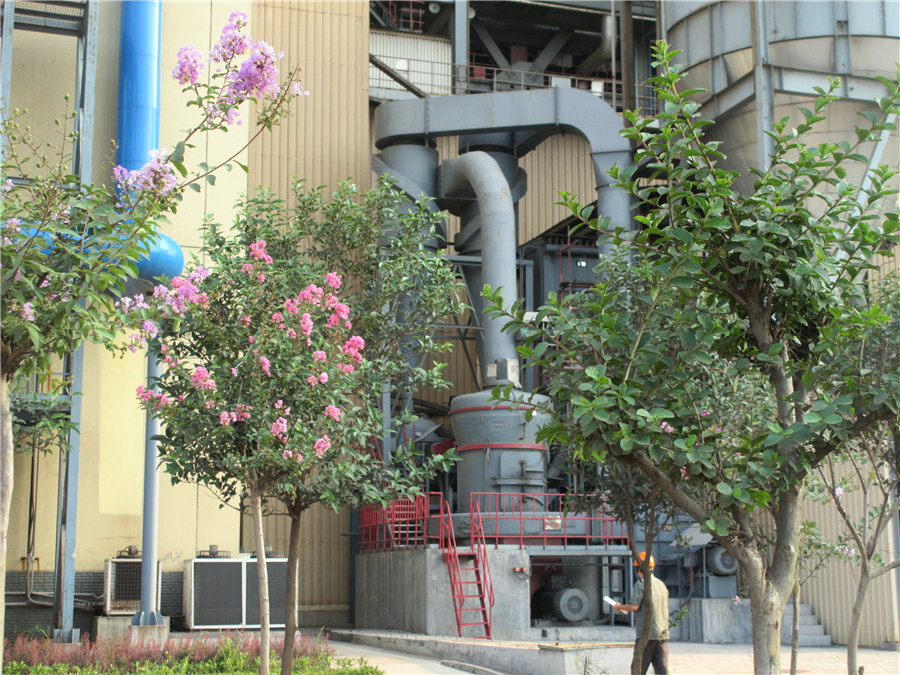
3 Necessary Cement Milling Comparison Ball Mill, Vertical Roller Mill
2020年11月5日 We compare 3 cement milling and cement mill processes, including cement ball mill, vertical roller mill, and rod mill Find your answer here! Skip to content +86 s about blog contact EN ES Menu Menu The term ball mill is restricted to those having a length to diameter ratio of 2 to 1 and less Ball mills in which the length to diameter ratio is between 3 and 5 are designated tube mills Usually, for large scale operations, as in the case of rawmeal grinding mills or cement mills, only continuous mills are usedBall Mill an overview ScienceDirect Topics2004年12月10日 Optimization of continuous ball mills used for finishgrinding of cement by varying the L/D ratio, ball charge filling ratio, ball size and residence time Author links open overlay panel R Schnatz The L/D ratio of the ball mill was varied in four steps of 175, 21, 279 and 349, Optimization of continuous ball mills used for finishgrinding of 2017年10月26日 The following are factors that have been investigated and applied in conventional ball milling in order to maximize grinding efficiency: a) Mill Geometry and Speed – Bond (1954) observed grinding efficiency to be a Factors Affecting Ball Mill Grinding Efficiency
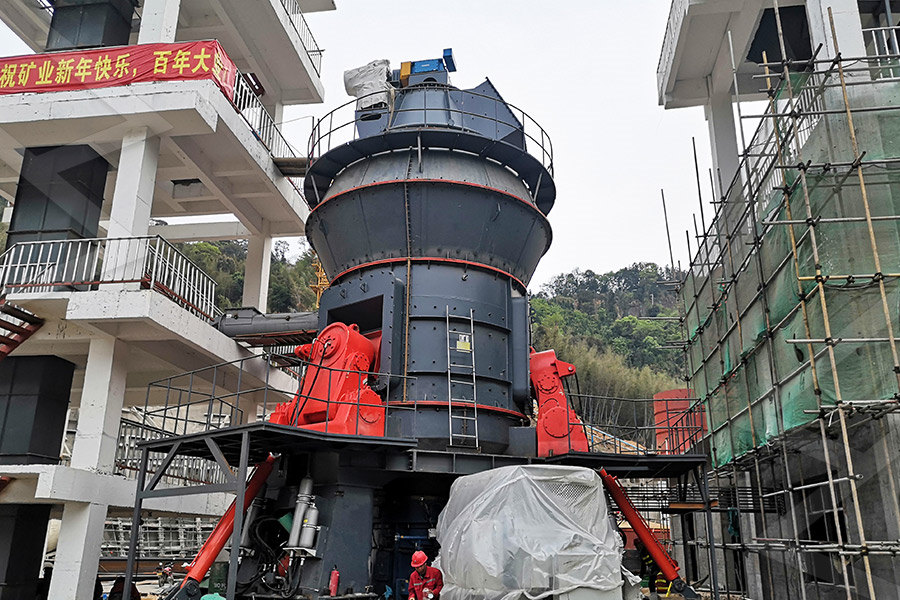
(PDF) Analysis of ball mill grinding operation using mill power
2014年3月1日 The object of the study reported here is the grinding process in a tumbling mill where the mechanism of destruction by crushing is implemented, which is caused by the mechanism of compression loading2024年1月5日 3 Ball mill for dry grinding (eg cement) Coarse grinding chamber 33 % of total grinding path length Lifter plate lining 100 mm – 60 mm balls Fine grinding chamber 67 % of total grinding path length Classifying plate lining 50 mm 15 mm balls Intermediate diaphragm Discharge diaphragmCement ball mill process calculation pdf PPT SlideShareOf course, even if we set a more appropriate cement fineness, it is difficult to change the current situation that the flow velocity in the opencircuit ball mill is only 1/21/3 of that in the closedcircuit ball mill with the same specification, which will lead to poor comprehensive performance of finished cement, low system output and unsatisfactory enterprise benefitsBall Mill In Cement Plant Cement Ball Mill AGICO CementClinker, Gypsum and other desired additives are fed to the ball mill in specific proportions based on the quality requirement Feed material is ground in the ball mill, discharged and fed to a classifier with the help of a bucket elevator for classification of the ground cement into two streams – coarse and finesOptimization of Cement Grinding Operation in Ball Mills PEC
.jpg)
Optimization of A Fully AirSwept Dry Grinding Cement Raw Meal Ball
This document discusses optimizing the production capacity of a fully airswept industrial scale twocompartment cement ball mill through simulation The mill has two compartments, with the first used for predrying and the second for grinding The study models the mill as a single compartment using the perfect mixing ball mill modeling approach Static separators are A cement ball mill has the capacity typically ranging from 10 to 300 tons per hour Chromium content exceeds 11%, with a chromiumtocarbon ratio over 45 Rubber Liners: Made with a steel membrane and vulcanized using styrenebutadiene or natural rubber, with an Akron abrasion of 014 cm³/16 kmCement ball mill DARKO2020年1月11日 Compared with other ball mills that used for the same period, his ball mill grinding efficiency is higher by about 25% At present, the capacity of the gold ball mill is 180TPH, the particle size of the feed is controlled at about 20mm, and the output easily reaches 200 mesh Gold ore working site5 Ways to Improve the Ball Mill Efficiency FTMAdjusting mill parameters: Finetuning mill parameters such as mill speed, ball charge, filling ratio, and grinding media size can have a substantial impact on the grinding efficiency of the mill For example, a 10% increase in mill speed can Cement Mill Optimization: Practical Strategies for
.jpg)
Impact of ball size distribution, compartment configuration, and
2022年11月1日 In the context of fullscale continuous cement ball milling, there is no exact rule for ball selection; rather, the cement industry designs the mixture of ball sizes and BSD on the basis of their experience along with recommendations from the mill machine suppliers (eg, FLSmidth, 2012, FLSmidth, 2014) and (empirical) Bond’s approach (Bond, 1958), in which top 2024年1月26日 Cement ball mill is a well known machine to grind raw material (hard clinker) into grey powder: Optimization of continuous ball mills used for finishgrinding of cement by varying the L/D ratio, ball charge filling ratio, ball size and residence time Int J Miner Process, 74 (2004), pp 5563 Google Scholar [9]Computation of charging media for a double compartment cement ball mill 2019年12月10日 The cement ball mill is mainly used for grinding the finished products and raw materials of cement plants, The crushing ratio is large, the feeding size can reach 50 mm, the discharging particle size can be controlled, and the particle quality is good 3Cement Ball Mill JXSC Machine2024年7月31日 The production of cement, an essential material in civil engineering, requires a substantial energy input, with a significant portion of this energy consumed during the grinding stage This study addresses the gap in the literature concerning the collective impact of key parameters, including ball size, feed rate, and mill speed, on grinding efficiency Nine spherical Effect of Grinding Conditions on Clinker Grinding Efficiency: Ball
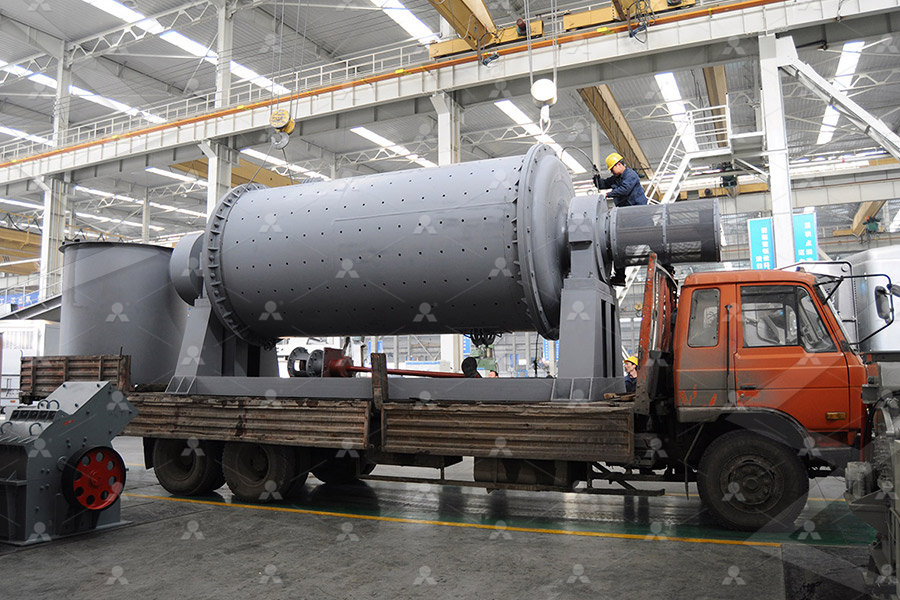
Cement Ball Mill Cement Grinding Machine Cement Mill
What Is A Cement Ball Mill The cement ball mill is a kind of cement grinding millIt is mainly used for grinding the clinker and raw materials of the cement plant, and also for grinding various ores in metallurgical, chemical, and electric power enterprisesIt has the characteristics of strong adaptability to materials, continuous production, a large crushing ratio, and easytoadjust the A 15 mio t/a cement plant is having a closed circuit ball mill for cement grinding: The mill has been operating with satisfactory performance interms of system availability and output, however L/D ratio Mill drive 358 5000 kW Diaphragm Double blind plate Mill speed 152 rpm GM in I PROCESS DIAGNOSTIC STUDIES FOR CEMENT MILL 2017年2月13日 Ball Mills or Rod Mills in a complete range of sizes up to 10′ diameter x 20′ long, They have vast applications within different branches of industry such as for example the ore dressing, cement, Rod mills have usually a length/diameter ratio of at least 14 Tube MillsBall Mills 911Metallurgist2022年2月28日 Additionally, the specific rate of breakage ratios between dry and wet grinding environments ranges from 11 to around 2, Deniz, V: A study on the specific rate of breakage of cement materials in a laboratory ball mill Cem Concr Res 33, 439–445 (2003)Grinding SpringerLink
.jpg)
Cement grinding Vertical roller mills VS ball mills
Vertical roller mills and ball mills represent two clearly distinct technologies However, with proper adjustments to the operational parameters of the vertical roller mill almost identical cement properties can be achieved by the two mills that satisfy the cement user’s demandsNevertheless, the two types of mills have their distinctive merits2015年1月27日 The use of highpressure grinding rolls (HPGR) prior to ball mills has become a common practice in cement clinker grinding due to significant energy savings in comparison to ball milling aloneBallMill Grinding Kinetics of Cement Clinker Comminuted in the Ball top size (bond formula): calculation of the top size grinding media (balls or cylpebs):Modification of the Ball Charge: This calculator analyses the granulometry of the material inside the mill and proposes a modification of the ball charge in order to improve the mill efficiency:Ball charges calculators2019年8月14日 Common Types of Ball mill back to top The common industrial ball mills mainly include cement ball mill, tubular ball mill, ultrafine laminating mill, cone ball mill, ceramic ball mill, intermittent ball mill, overflow ball mill, grid ball mill, wind discharge ball mill, double bin ball mill, energy saving ball mill 1The Ultimate Guide to Ball Mills Miningpedia
.jpg)
Quantitative Morphological Characterization of Cement Particles
Portland Cement, Portland Slag Cement Portland Pozzolana Cement drawn from different milling systems, ie close circuit Ball Mill, Vertical Roller Mill hybrid systems consisting of Roll Press Ball Mill have been analyzed using digitized images, in order to explore the effect of above shape descriptors on cement propertiesModeling And Simulation Of A Closed Loop Ball Mill Grinding Circuit Proceedings of IRF International Conference, Chennai, India, 20th April 2014, ISBN: 978938 10 II DYNAMICS OF THE BALL MILL GRINDING CIRCUIT product Blaine measured in cm²/g and the rejects Fig1 In a continuous ball mill grinding circuit, the ball millMODELING AND SIMULATION OF A CLOSED LOOP BALL MILL 2024年8月8日 This makes them especially suitable for heavyduty milling tasks in mining and cement production, where robust grinding media are required to break down hard materials efficiently Steel balls are valued for their durability and costeffectiveness, offering a balance between upfront costs and operational longevityBall Mill Success: A StepbyStep Guide to Choosing the Right BallFillingDegreeMillCalculation Free download as Excel Spreadsheet (xls), PDF File (pdf), Text File (txt) or read online for free This document contains calculations and specifications for a cement mill, including: Dimensions of the mill such as diameter, length, motor power, compartment lengths, and ratio of length to diameterMill Calculation: Plant: Date: Mill: Visa PDF Electric Power Scribd
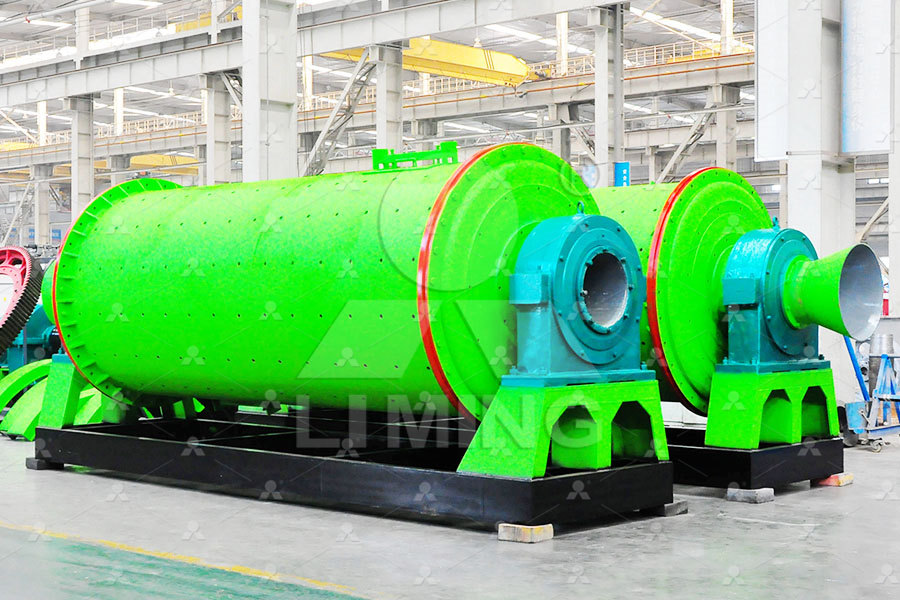
Factors Affect The Output and Quality of Ball Mills And How to
2023年12月28日 The ball mill is widely loved by people in mineral For example, in the cement industry, actual production shows that when the product fineness is 5 to 10%, the output bonding between them improves grinding efficiency and is conducive to energy savings and high productivity of the ball mill 10 Balltomaterial ratio2004年12月10日 The specific power consumption is, as already said, influenced by the L/D ratio and the ball charge filling ratio of a ball mill The investigations known from the literature were carried out with two compartment cement mills in the Optimization of continuous ball mills used for finishgrinding of