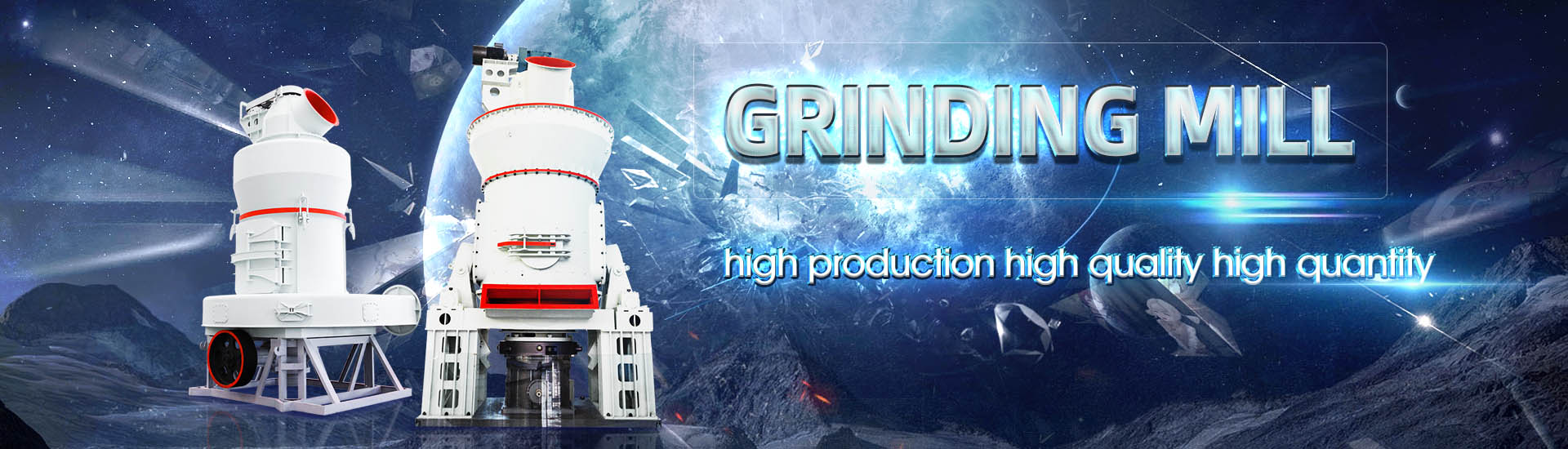
Clean coal powder preparation process
.jpg)
Coal Preparation SpringerLink
Coal produced by mechanized mining operations contains particles as small as fine powder and as large as several hundred millimeters Particles too large to pass into the plant are crushed to an appropriate upper size, or rejected where insufficient recoverable coal is present in the coarse size fractions The crushed 展开Coal preparation, also called washing, cleaning, processing, and beneficiation of coal, is a physical process where coal is upgraded by the reduction of ash, sulfur, and moisture content Coal Preparation an overview ScienceDirect Topicss to metal detectors Removing tramp iron from the coal processing stream reduces damage to an electric plant’s conveyor belts, pulverizers and coal feeders, and allows electric plant op Clean Coal Processing Eriez2021年5月1日 As conventional methods for extracting clean coal from tailings reported poor yields, a twostage process ie wetgrinding followed by densitygradientcentrifugal Sustainability of coal mines: Separation of clean coal from the fine
.jpg)
A review of stateoftheart processing operations in coal
2015年7月1日 This article, which describes the historical influences and stateoftheart design for the various coal preparation unit operations, is organized to distinguish between 2023年7月17日 Binders play a crucial role in the cokeforming process by reducing viscosity, fixing sulfur on raw coal, and optimizing the quality of raw coal This optimization leads to improved parameters such as coal activity, thermal Clean Preparation of Formed Coke from Semicoke by coal cleaning is highly site specific But the general procedure involves size reduction to control top size and to free or unlock occluded mineral matter followed by separation of relatively pure CHAPTER 3 Coal Preparation and CleaningABSTRACT: In order to address the low thermal eficiency of lowrank coal combustion and the accompanying serious environmental issues, formed coke was prepared using a carbonization Clean Preparation of Formed Coke from Semicoke by the
.jpg)
Mineral Beneficiation and Processing of Coal SpringerLink
2021年5月11日 In this chapter, coal preparation techniques employed in the generation of clean coal for various applications are briefly discussed Presentday coal washeries are equipped 2021年7月31日 Chemicophysical method of clean coal separation by hydrothermal extraction followed by density separation results in clean coal at 498% yield with an increase in vitrinite Extraction of clean coal from washery rejects and its effect on 2019年1月15日 Autogenous grinding is the process in which, the ore is grounded itself without any grinding media As the grinding media is harder than the ore, there is always high impact force applied to the ore, which leads to the breakage throughout the materials but not through the interfaces between the materials present in ore [21]For the present study, two different run of Generation of low ash fine clean coal powder by autogenous few studies have been carried out on the preparation of coalganguebased silicon fertilizer using hightemperature activation technology In this study, coal gangue mixed with calcium carbonate and corn stalk powder is used as a raw material to produce ganguebased silicon fertilizer through hightemperature activationSustainable and clean utilization of coal gangue: activation and
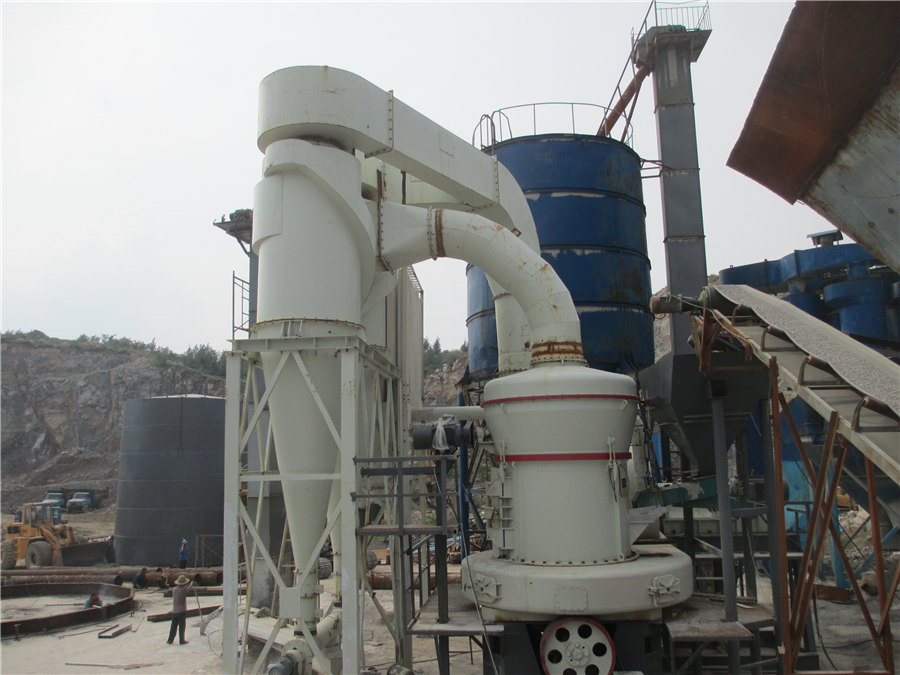
Technology Innovation in the Coal Industry 一般財団法人
Technological Innovation in the Coal Industry 1 Clean Coal Technologies in Japan Preface˜ Part 1 CCT Classifications ˜ (1) CCT Classifications in the Coal Product Cycle (2) Clean Coal Technology Systems (3) CCT in the Marketplace (4) CCT in Japanese Industries (5) Environmental Technologies (6) International Cooperation Part 2 CCT Overview˜2021年5月1日 Typical coal washing plants adopt dense media cyclone for coarse coal (−13 mm + 05 mm size) and froth flotation technique for the fine coal (−05 mm size) [3] However, due to the drift origin of Indian coals, clean coal yield is limited to 35–40%, which makes the process cumbersome and costly [4]Sustainability of coal mines: Separation of clean coal from the fine 2023年9月1日 A clean process for alumina extraction and ferrosilicon alloy preparation from coal fly ash via vacuum thermal reduction J Clean Prod , 240 ( 2019 ) , Article , 101016/jjclepro2019A clean process for preparing ferrosilicon alloy from coal 2014年8月21日 China’s energy supply heavily relies on coal and China’s coal resource and water resource has a reverse distribution The problem of water shortages restricts the applications of wet coal beneficiation technologies in drought regions The present situation highlights the significance and urgency of developing dry beneficiation technologies of coal Progress in developments of dry coal beneficiation
.jpg)
Research on highly efficient quality improvement process and
2023年12月1日 Steam coal is an important coal resource and that is used as a fuel in electric power plants to generate steam for producing electricity, it accounts for large proportion in the coal structure [[1], [2], [3]]Coal preparation is a key link to achieve effective improvement in the quality of steam coal for its clean utilization [[4], [5], [6]]generally be divided into four basic phases: initial preparation, fine coal processing, coarse coal processing, and final preparation A process flow diagram for a typical coal cleaning plant is presented in Figure 11101 In the initial preparation phase of coal cleaning, the raw coal is unloaded, stored, conveyed,1110 Coal Cleaning US EPA2016年12月1日 A large proportion of China’s coal resources has a high sulfur content The coalwashing process produces a large amount of coal gangue that needs to be used CFB combustion technology, with its wide fuel scope, low cost of desulfurization, and low NO x emissions, has the advantage of largely using this kind of fuelClean Coal Technologies in China: Current Status and Future 2021年12月10日 Low ash coal demand has been increased in integrated steel plants, coalfired power plants and, cement industries due to global warming gas emissions cut and increase in productivity (Wang et al, 2019; Sriramoju et al, 1016)Typical Indian coal washeries adopted dense medium cyclone for coarse coal separation and froth flotation technique for fines, which Integrated process for coal chemical demineralization and spent caustic
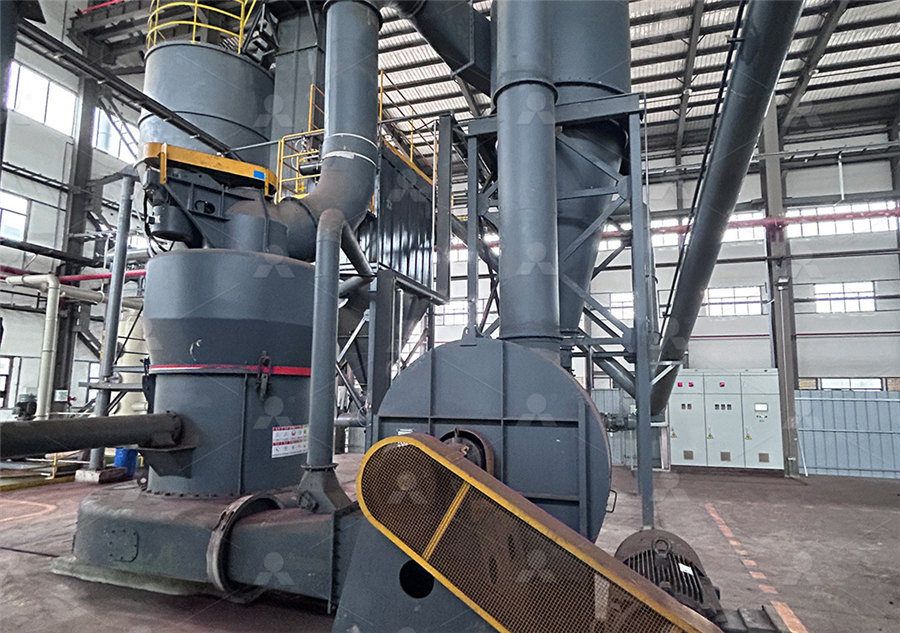
Coal Preparation an overview ScienceDirect Topics
After the raw coals are treated by the separator, vibrating screen, crusher, centrifuge, the particle size decreases from more than 100 mm to the final 2–25 mm, and meanwhile, the ash content decreases from 278% of the raw coal to 81% of the final clean coal During this coal preparation process, the vibrating screens used include a flip Coal preparation—or cleaning—is the removal of mineral matter from asmined coal to produce clean coal, The Initiation of Research in the US Department of Energy's Coal Preparation Process Research Facility Paper presented at the 5 COAL PREPARATION, COALLIQUID MIXTURES, 2020年5月1日 At present, the full grain inclusion process of dynamic coal results in the production of slime as a byproduct during coal preparation The produced coal slime needs to be dehydrated and recycled properly, otherwise it may lower the calorific value of separationcleaned coal compared to that of raw coal [10, 11]Certain types of coal are more prone to producing A novel and low cost coal separation process: Combination of Clean coal is rarely sized, except for some industrial markets Storage and stockpiling Coal is stored in silos or stockpiled before and after cleaning Raw coal is stored between the mine and the preparation plant, and clean coal is stored between the preparation plant and product loadoutCoal Mining and Processing Methods The National Academies
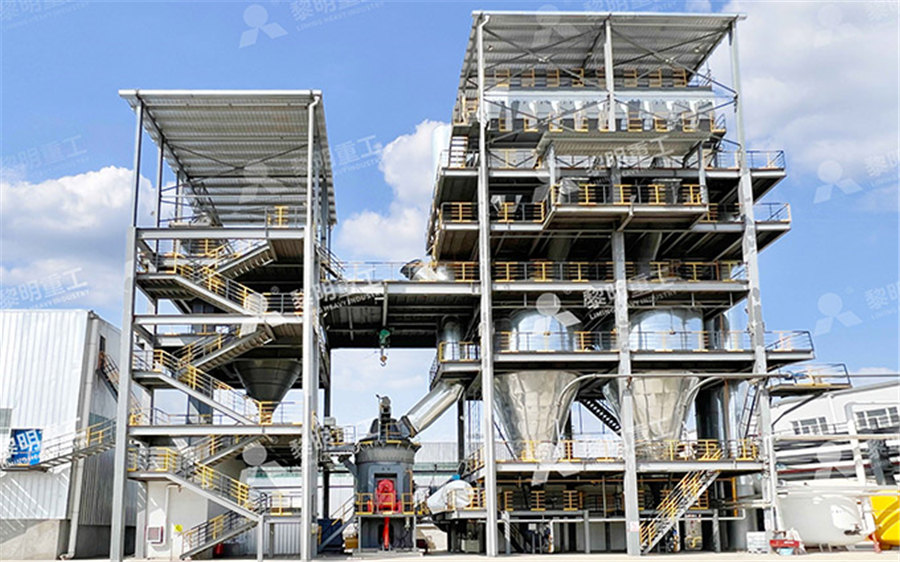
Assessing the feasibility of silicabased media for coal preparation
2016年1月1日 During the silicon smelting process, silica and carbon raw materials are charged into the arc furnace, and the inside temperature is immediately increased to 700–1300 °C by high temperature gases rising in the arc furnaceIn this environment, different chemical reactions can occur based upon the carbon coverage, 1 which result in the production of free molten silicon, 2019年12月10日 A clean process for alumina extraction and ferrosilicon alloy preparation from coal fly ash via vacuum thermal reduction Author links open overlay panel Additionally, a charcoal powder with particle size less than 500 μm was employed as the reducing reagent, and its composition is shown in Table 1 Furthermore, a A clean process for alumina extraction and ferrosilicon alloy water into steam in boilers Coal is pulverized into fine powder, for proper combustion, and then it is fed to boilers for steam generation The steam is then used to drive steam turbines The turbine shaft is coupled to a generator shaft which generates electricity The process of cleaning coal begins at preparation plants and ultimatelyClean Coal Processing Eriez2021年5月11日 The modernday coal processing plants can be categorized into four different circuits, depending upon the size of the coal particles to be treated: (a) coarse coal processing circuit treating particles coarser than 10 mm, (b) small coal circuit for washing particles in the size range of 110 mm, (c) fine coal circuit for cleaning particles in size range of 015–1 mm, and Mineral Beneficiation and Processing of Coal SpringerLink
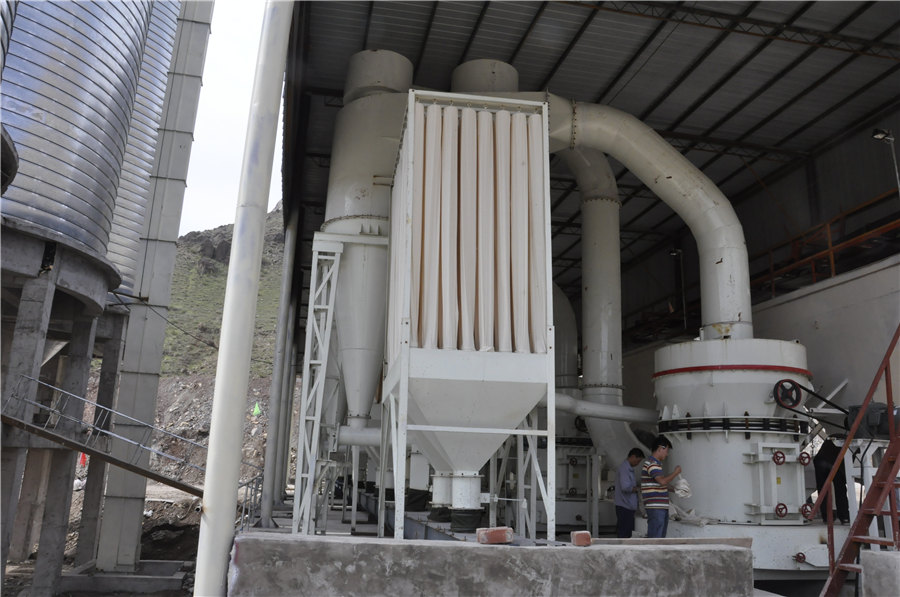
Optimization, simulation, and control of coal preparation plants
2023年1月1日 The flowsheet for a coal preparation plant can typically be represented by a series of sequential unit operations for sizing, cleaning, and dewatering (Fig 181)This sequence of steps is repeated for each size fraction, since the processes used in modern plants have a limited range of applicability in terms of particle size (Osborne, 1988)Coal Gasification: It bypasses the conventional coal burning process altogether by converting coal into a gas With integrated gasification combined cycle (IGCC) systems, steam and hot pressurized air or oxygen combine with coal in a reaction that forces carbon molecules apart The resulting syngas, a mixture of carbon monoxide, hydrogen, CO 2Clean Coal Technologies visionias/2021年12月1日 During the whole process of coal utilization, coal preparation and separation is an initial and crucial stage for hazards emission control Gravity dry separation technologies, as representative sorting methods, have advantages of high separation efficiency, water conservation, low investments, etcRecent progress and potential challenges in coal upgrading via coal units have to be more exible, not only for owing the load demand, but also for faster integration with the grid The general coal red energy conversion process is depicted in Fig 1 below The process starts from coal preparation to be in powder form and mixed with primary air (PA) in order to speedupSpeedingup Startup Process of a Clean Coal Supercritical Power
.jpg)
A novel process for preparation of ultraclean micronized coal
2007年3月1日 HPWJM was used for coal comminution in the novel process, which is the essential difference form the traditional preparation process The present work, which a is part of an ultraclean micronized coal water slurry preparation program in our department, is carried out to demonstrate that the new preparation process has great application potential in the Photo 1 Briquetted UBC Photo 2 Lowrank coal upgrading demonstration plant 1) Toru Sugita et al, UBC (Upgraded Brown Coal) Process Development, Kobe Steel Engineering Reports, 53, 42, 20034D2 Lowrank Coal Upgrading Technology (UBC Process)2020年1月3日 'Coal Preparation' published in 'Fossil Energy' According to the annual census of coal preparation plants conducted by Coal Age [], the USA operates 286 coal preparation plants in 12 statesThis number is relatively small by comparison to the worldwide fleet which is estimated to be 2283 plants []The capacity of the plants can range from less than 200 t/h for Coal Preparation SpringerLinkPreparation of ferrosilicon or SiFeAlCa alloys from CGFS by carbothermal reduction is an efficient method to recycle CGFS (Wang et al, 2023b, Wang et al, 2024b)Siliconcontaining alloys can be used as deoxidizers in steel making (Liu et al, 2022) and alloying agents of iron casting (Skaland, 2003)The carbothermal reduction process takes full advantage of the high An improved process for the preparation of SiFeAlCa alloy from coal
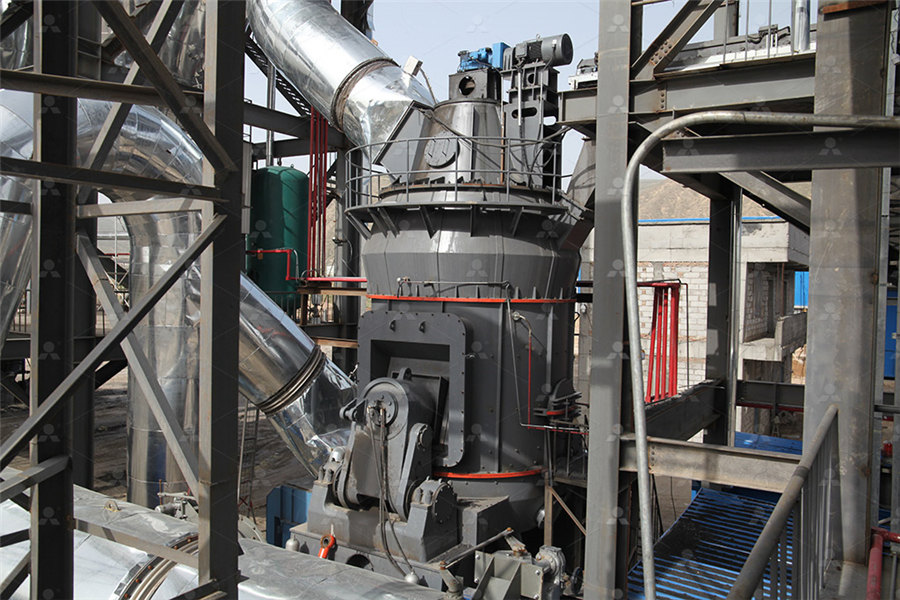
Thermal extraction of coal and derivatives to prepare hotpressed coal
2024年2月1日 Coal is a major source of energy for electricity generation, iron and steel manufacturing, and chemical production, accounting for 272% of global primary energy consumption in 2020 [1], [2], [3]However, its combustion for power generation and industrial heating incurs a large amount of CO 2, SO x, NO x, and other noxious compounds 2023年11月28日 In recent years, the efficient and clean utilization of coal has been widely concerned by scholars at home and abroad Despite the abundance of global coal resources, the deep utilization rate of coal is still insufficient To address this challenge, it has been explored the development and preparation of coalbased high valueadded carbonaceous materials In the Controlled CVD preparation and quality characterization of 2014年1月1日 Deep cleaning of coal by fine grinding leading to liberation of mineral matter prior to combustion is consequently seldom practised as part of the coal preparation process Practically speaking, preparation of ultraclean coal needs to take place as a pretreatment step at the power plant and not during coal preparation at the mining siteCoal Processing and Use for Power Generation ScienceDirect2015年6月1日 Powder Technology Volume 277, June 2015 Due to the fine middling clay had a significant effect on the medium density in the coal preparation process, without using the leaching process, the froth flotation process could only produce a clean coal with 6641% total sulfur, 9771% inorganic sulfur and 7952% ash content Recent advances in beneficiation for low rank coals
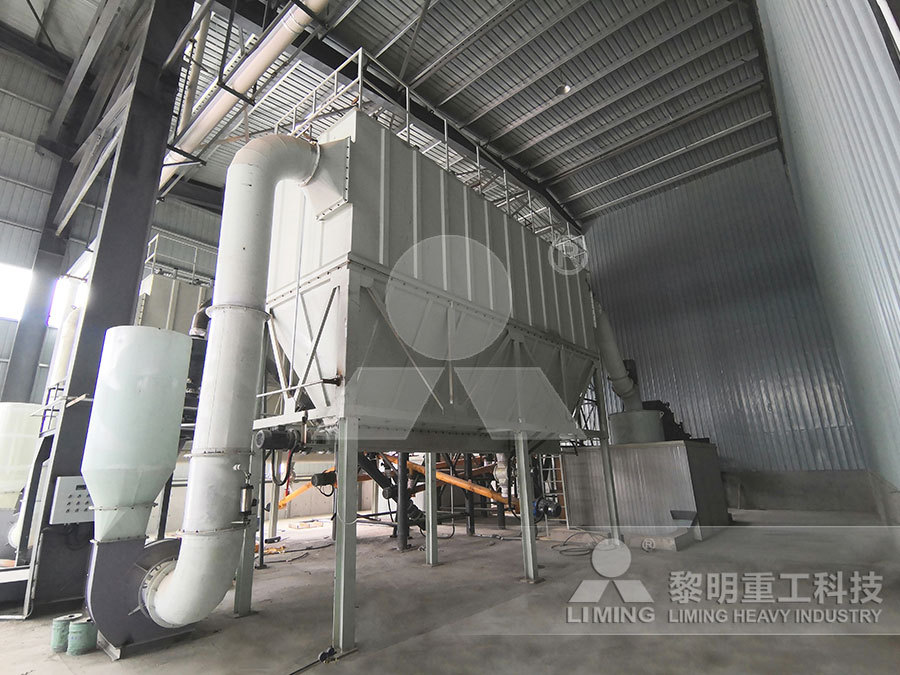
Clean Coal Technology an overview ScienceDirect Topics
2010年3月1日 Clean coal technology, as shown in Fig 24, is a combination of technologies developed in attempts to diminish the negative environmental impact of coal energy generation “Clean coal” connotes supercritical coalfired plants without carbon capture and storage (CCS), since CO 2 emissions are less than for conventional plants (IEA, 2008)2015年7月1日 1 Introduction Coal preparation that aims to physically remove mineral impurities from runofmine coal has long been adopted as an economic and effective way to produce clean coal [1]The increasingly serious environmental problems caused by the pollutant emissions from coal utilization [2] make many countries contribute more effort to improve the ratio of runof Process analysis of fine coal preparation using a vibrated gas mine (open pit) to the coal preparation plant Size degradation occurs during loading coal into rail cars, dump trucks, transportation from the preparation plant stock dump and loading onto silos, at grinding of coarse coal over +200 (100) mm, during supplying coal to the preparation plant by a belt conveyor Coal size degradation depends on Design of coal preparation plants: problems and solutionsresulting from coal preparation activities as well as the issues associated with the sustained operation of coal processing facilitiesThisreview suggests that coal preparation will continue to have a significant impact on the cost, recovery and quality of coal supplies However, future improvements in separation technology and practices areclean coal yield by the theoretical maximum Coal Preparation
.jpg)
Clean Preparation of Formed Coke from Semicoke by the
2023年8月8日 The coldpressed cokeforming process using binders has emerged as the dominant application and subject of research in this field, owing to several advantages such as its simple process, low temperature, lowpressure requirements, and versatility in utilizing various raw materials 15 Binders play a crucial role in the cokeforming process by reducing viscosity, 2022年6月15日 Most raw coal needs to go through the coal preparation process to remove gangue components, thereby improving carbon content, reducing transportation costs, and improving economic The density of the clean coal powder was 125 g/cm 3, and the bulk density was 0655 g/cm 3 The true density of the quartz sand was 255 g Separation performance of 05–1 mm fine coal in a gas–solid 2019年1月15日 Coal is a carbonaceous ore contains maceral and minerals with different properties Due to the presence of high mineral content, the mineral beneficiation process is adopted where the liberation of inorganic minerals plays key role As coal is a soft material, use of impact mills generates coal with homogeneous distribution of minerals In this paper, Generation of low ash fine clean coal powder by autogenous 2019年3月15日 Coal accounts for ~30% of the world's energy resources [1]Only in 2017, China produced 352 billion tons of raw coal, which provided 604% of the total energy consumed [2]Coal preparation is the most economical and effective way to reduce coalburning air pollution and to achieve efficient and clean utilization of coal [3, 4] Simultaneous multiple parameter optimization of variable
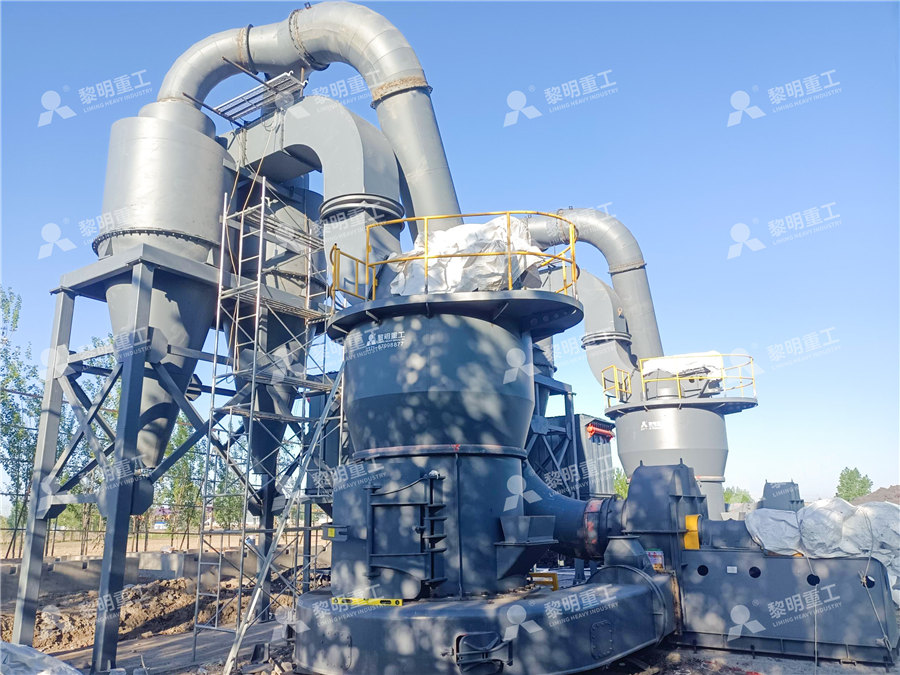
Online prediction of clean coal ash content based on image analysis
2021年3月1日 At present, many coal preparation plants are paying more attention to intelligent process control However, there are three obstacles The first is the monitoring of raw coal material, which could be resolved by two approaches: (a) Evaluation through analysis of a month’s comprehensive floatandsink test material of raw coal [10]; (b) Prediction through real 2020年12月30日 Powdered activated coke (PAC) is a good adsorbent of SO2, but its adsorption capacity is affected by many factors in the preparation process To prepare the PAC with a high SO2 adsorption capacity using JJcoal under flue gas atmosphere, six parameters (oxygencoal equivalent ratio, reaction temperature, reaction time, O2 concentration, CO2 concentration, Optimization of process parameters for preparation of powdered