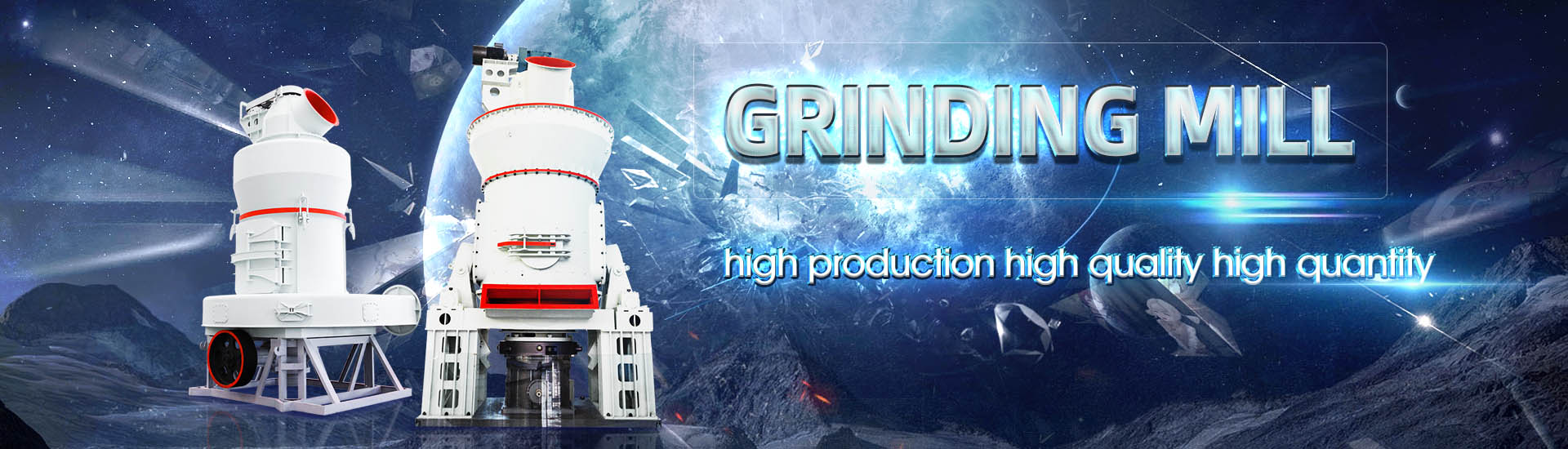
Maintenance of ore silica grinding mill with an output of 30 to 50 tons per hour
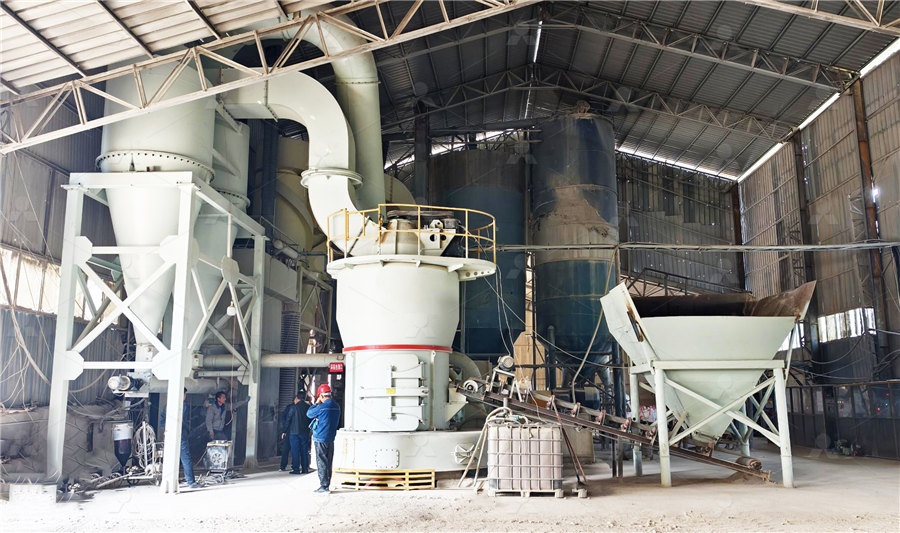
Innovative predictive maintenance for mining grinding mills: from
2024年10月8日 This article presents an innovative predictive maintenance for grinding mills, aiming to enhance operational efficiency and minimize downtime Leveraging advancements 2013年4月1日 A simple, novel and nonlinear model of runofmine ore grinding mill circuit is validated The model is developed for process control and estimation purposes The model Analysis and validation of a runofmine ore grinding mill circuit 2023年10月27日 Grinding media play an important role in the comminution of mineral ores in these mills This work reviews the application of balls in mineral processing as a function of the A Review of the Grinding Media in Ball Mills for Mineral Processing 2013年11月1日 Knowing the remaining useful life of grinding mill liners would greatly facilitate maintenance decisions Now, a mill must be stopped periodically so that the maintenance Remaining useful life prediction of grinding mill liners using an
.jpg)
Mill maintenance – 3 simple ways to keep your mill at its best
2017年12月19日 With the grinding mill critical to a plant’s throughput, it pays to ensure mills receive the necessary care and maintenance Too often mill maintenance is reactive, 2012年6月1日 The paper presents an overview of the current methodology and practice in modeling and control of the grinding process in industrial ball mills Basic kinetic and energy Grinding in Ball Mills: Modeling and Process Control ResearchGategrinding process Clinker grain sizes depend on precrusher settings but are in some cases still up to 50mm when fed to the ball mill and therefore, it is necessary to adjust the grinding tools BALL MILLS Ball mill optimisation Holzinger ConsultingRunning lean requires operational efficiency reliant on a defined service schedule for vehicles that eliminates downtime and maintains vehicle productivity To better contextualize how granular MAINTENANCE EFFICIENCY IS KEY TO MINING OPERATION
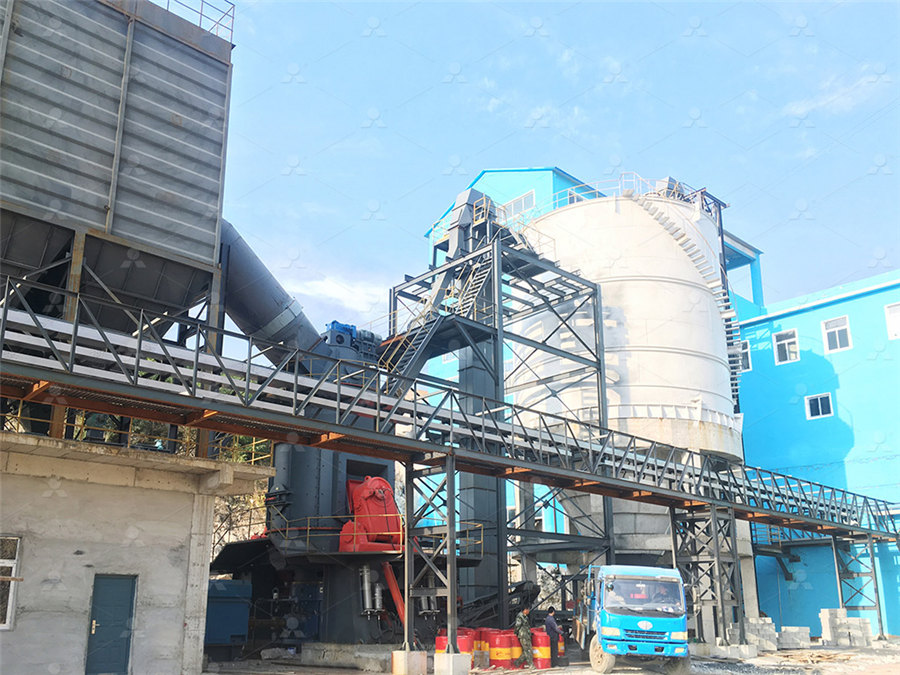
Energy Use of Fine Grinding in Mineral Processing
2013年12月18日 Fine grinding, to P80 sizes as low as 7 μ m, is becoming increasingly important as mines treat ores with smaller liberation sizes This grinding is typically done using stirred 2022年10月4日 The worldwide mining industry consumes a vast amount of energy in reduction of fragment size from mining to mineral processing with an extremely lowenergy efficiency, Reduction of Fragment Size from Mining to Mineral Processing: A Usually small and mediumsized enterprises choose the mill for silica production according to the specification of 1020 tons of output per hour Then, how much is the s ilica grinding mill for 1020 tons of silica production? When users invest in the purchase of 1020 tons of silica production mills, the problem of price is a headacheNews How much is the silica grinding mill for 1020 tons of silica 2014年10月20日 Conversely, finegrained magnetite ores require fine grinding, often to below 30 μm, to liberate the magnetite from the silica matrix, incurring greater costs and energy consumptionRegrind of metallic ores with vertical mills: An
.jpg)
Beneficiation of Gold and Silver Ores SpringerLink
2019年12月15日 429 VertiMills Vertical mills were first designed in the 1950s for applications in fine and ultrafine grinding in Japan Lately, the vertical mill is making progress toward primary grind application and shown promise in energy reduction relative to ball mills, typical to what is normally seen in regrinding applications (Mazzinghy et al 2014)2021年11月23日 The particle size of the finished product can be freely adjusted between 80425 mesh, and the fineness can reach 1000 mesh, producing more than 150 tons per hour 5 The ultrafine mill It is mainly used for ultrafine powder processing The fineness is between 4253250 and the hourly output is more than 110 tons Performance AdvantageWhat Kind of Mill is Used to Grind Dolomite?2022年1月1日 Conversely, finegrained magnetite ores require fine grinding, often to below 30 μm, to liberate the magnetite from the silica matrix, incurring greater costs and energy consumption The comminution energy consumption could be over 30 kWh/t, an order of magnitude higher than for hematite minution and classification technologies of iron oreIn Fig 41, the numbers 150200250 on the graphs of equilibrium relate to caustic soda concentrations in Na 2 CO 3A/C denotes aluminate ion concentration as Al 2 O 3 (A)/caustic soda concentration as Na 2 CO 3 (C) A typical Bayer process cycle with low temperature digestion is also shown Virtually each bauxite contains more or less amount of clay minerals, Chemical Processing of Bauxite: Alumina and Silica
.jpg)
SBM Ore Ultrafine Grinding Mill
HGM ultrafine grinding mill can process nonmetallic ores with Mohs hardness less than 7 The equipment has stable operation, simple operation, long service life, low carbon and environmental protection There are 5 models of HGM ultrafine grinding mill, 2023年7月10日 The present literature review explores the energyefficient ultrafine grinding of particles using stirred mills The review provides an overview of the different techniques for size reduction and (PDF) EnergyEfficient Advanced Ultrafine Grinding of Particles 2020年1月13日 The Vertical vibrating mill is a new design of vibrating mills which are used to produce micropowders, and nanopowders This paper studies the effect of four different parameters (rotational Abstract and Figures ResearchGate2023年4月23日 grinding media in a grinding mill with about 2630 wt% chrome by Chen et al [37] using a phosphate ore in a modified ball laboratory ball mill whose electrochemical potential could be controlled(PDF) Grinding Media in Ball MillsA Review ResearchGate
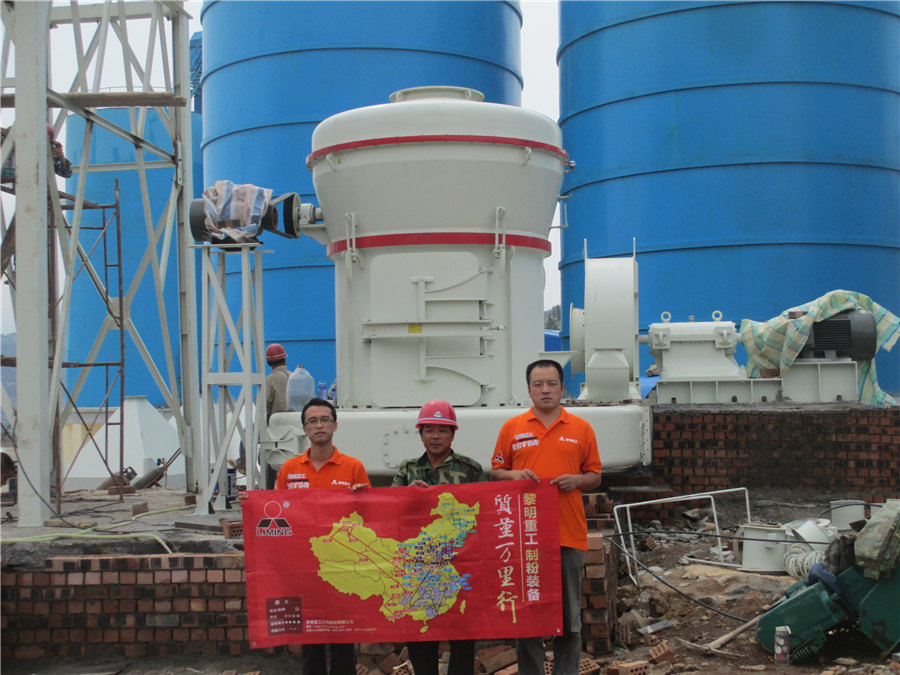
Maintenance of superfine grinding mill
2021年12月29日 ② Regular maintenance: repair and replace the wearing parts of the grinding roller and grinding ring in a certain period of time Regularly check whether the screws on the main parts of the machine are loose, as well as the 3 A cement grinding mill "A" with a capacity of 50 tons per hour utilizes forged steel grinding balls costing P12,000 per ton, which have a wear rate of 100 grams per ton cement milled Another cement mill "B": of the same capacity uses high chrome steel grinding balls costing P50,000 per ton with a wear rate of 20 grams per ton cement milledSolved 3 A cement grinding mill "A" with a capacity of 50 CheggGrinding tests were conducted on an oxidized coppercobalt ore using a pearshaped ball mill Twelve monosized ore fractions were prepared and wet ground batchwise The mill was run for 05 to 30 min intervals The shortest interval Mineral Processing Technology An Introduction to 2013年5月30日 This research has developed a population balance equation (PBE) model simulation to predict the output of biomass pellet grinding for Lopulco E16 mill and a Retsch PM100 planetary ball mill; this Application of multi regressive linear model and neural network
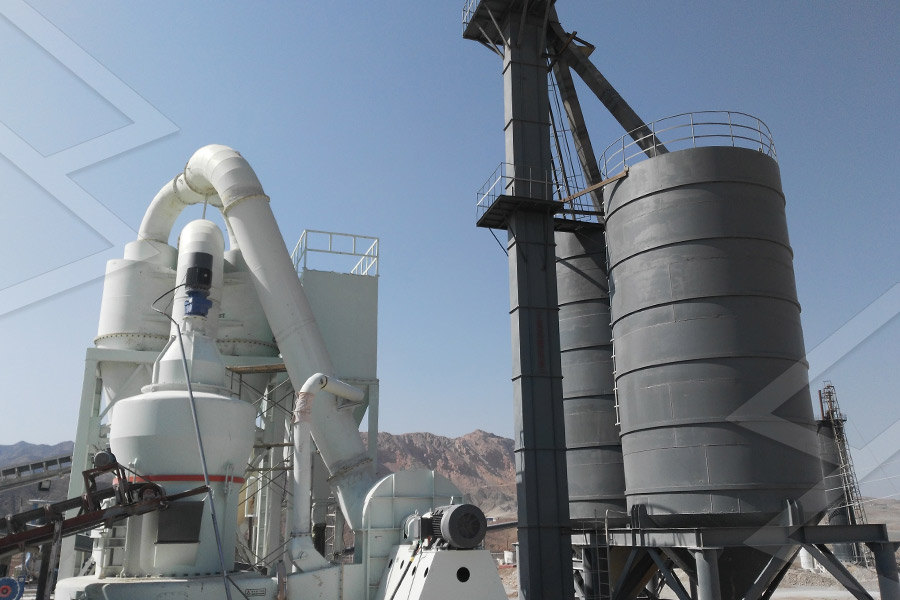
(PDF) A Method of Ore Blending Based on the Quality of
2021年5月31日 The nature of the ore blending problem is due to uncertainty and the uneven distribution of minerals in geology The benefits of ore blending are extending the ore reserve base by utilization of 2016年1月11日 Spending a little extra on drilling and blasting to increase fragmentation will same you multiples ore loading and hauling, then finally crushing The Experts: SandVik Mining + Metso and Quarry Academy = all agree The approximate running costs for crushing plants of different capacities up to 4,000 tons per day on the basis of an eighthour crushing day are Crusher Operating Costs: How to Optimize and Reduce2013年4月1日 This paper presents the design and application of a multipleinput–multipleoutput fractional order proportionalintegral (MIMO FOPI) controller to a grinding mill circuitAnalysis and validation of a runofmine ore grinding mill circuit 2023年10月27日 The ball mill is a rotating cylindrical vessel with grinding media inside, which is responsible for breaking the ore particles Grinding media play an important role in the comminution of mineral A Review of the Grinding Media in Ball Mills for Mineral Processing
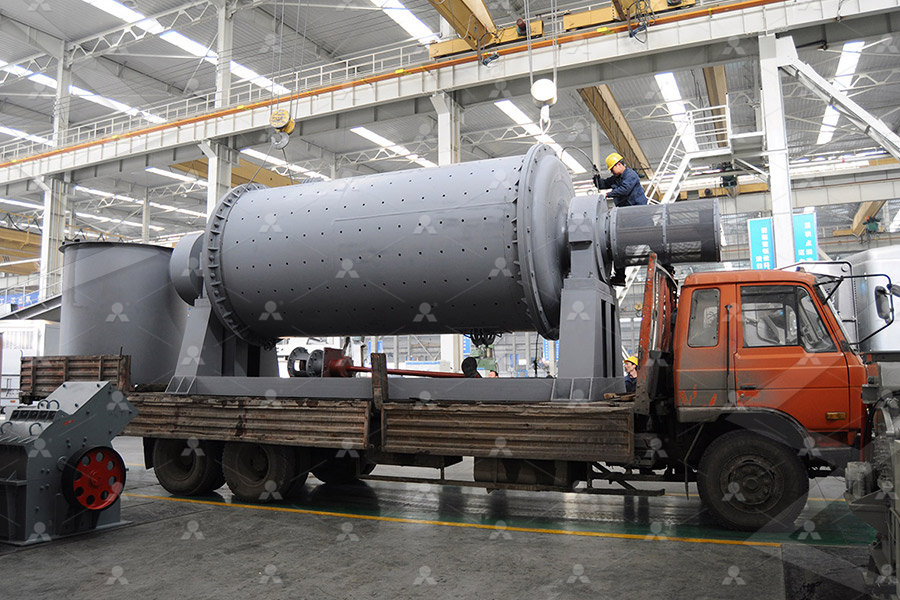
Attrition Grinding Mill Design 911Metallurgist
2017年6月9日 Using quartz sand as the grinding medium, each unit is capable of treating about 2 tons of coarse kaolin per hour; about 20 percent of the feed (800 pounds per hour) is recovered as finished product Figures 33 and 34 show two of the claygrinding units in operationA cement grinding mill “A” with a capacity of 50 tons per hour utilizes forged steel grinding balls costing P12,000 per ton, which have a wear rate of 100 grams per ton cement milled Another cement mill “B” of the same capacity uses high chrome steel grinding balls costing P50,000 per ton with wear rate of 20 grams per ton cement milledSolved A cement grinding mill “A” with a capacity of 50 tons 2012年6月1日 As the cylinder starts to rotate, the grinding balls inside the cylinder crush and grind the feed material, generating mechanical energy that aids in breaking bonds, activating the catalyst, and Grinding in Ball Mills: Modeling and Process ControlAn hydrocyclone is to be installed in a closed circuit grinding circuit with a mill discharge containing 30% solids by volume The solid density is 2800 kg/m 3 and the density of water is 1000 kg/m 3 Given that the maximum pressure deferential between the inlet and overflow was 50 kPa and the throughput from the mill was 800 t/h, estimate:1Grinding Mill an overview ScienceDirect Topics
.jpg)
Ore mill, Ore grinding mill All industrial manufacturers
Find your ore mill easily amongst the 42 products from the leading brands (Fritsch GmbH, Retsch, Eriez, This mill accepts grinding set weights of up to 30 kg, Circulation can be as fast as 50 passes per hour! Rapid mixing and milling There are many models of Raymond mills, among which the Raymond mill with an output of 50 tons per hour is a new type of mill provided by Guangxi Guilin Hongcheng Mining Equipment Manufacturing Co, Ltd As a wellknown manufacturer of ore pulverizer production lines, Guilin Hongcheng is marketoriented and creates greater market value for customers with excellent Raymond Mill With An Output of 50 Tons Per Hour2017年1月1日 An increase of over 10% in mill throughput was achieved by removing the ball scats from a single stage SAG mill These scats are non spherical ball fragments resulting from uneven wear of balls (PDF) Performance optimization of an industrial ball mill for Recently, the deep processing project of kaolin with an annual output of 100,000 tons of Inner Mongolia Shengyue New Material Technology Co, Ltd was successfully put into operation in Zhungeer Industrial Park, Zhungeer Economic Development Zone, Ordos, Inner Mongolia The project mainly uses solid waste coal gangue as raw material, and finally produces products News How To Configure The Calcined Kaolin Grinding Mill
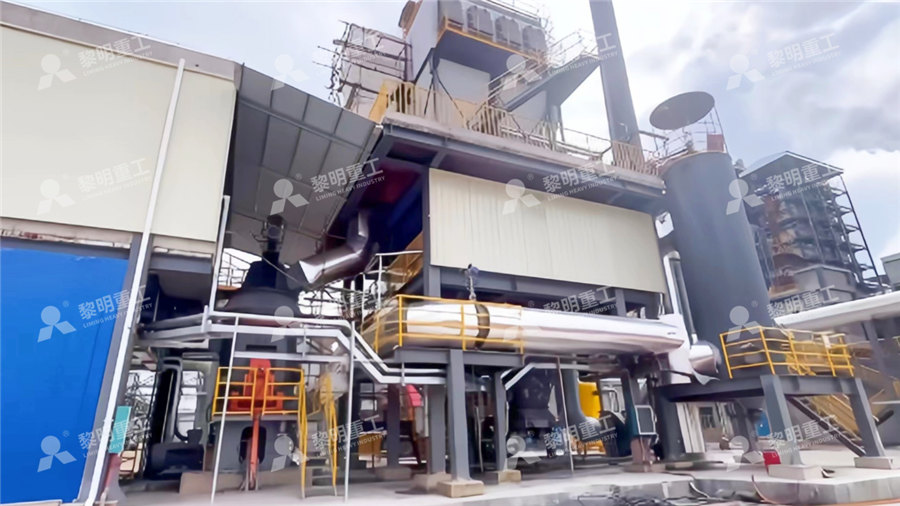
Reduction of Fragment Size from Mining to Mineral Processing: A
2022年10月4日 A notable fact is that the energy efficiency of conventional milling is only about 1%, as mentioned in Sect 1 An earlier experimental study indicated that about 80–90% of the energy input of a ball mill was used in heating the material (Schellinger 1951, 1952), and a recent study showed that over 75% of the electrical energy was used to heat the slurry (Bouchard et The Autogenous Mill, also known as AG Mill, is a type of grinding mill used in the mining industry This machine uses ore and rock itself as grinding media to perform its job Unlike other types of mills that use steel balls or rods for grinding materials, the Autogenous Mill relies on the material being ground to break itself into smaller piecesUnderstanding the SAG Mill in Copper Ore Mining Process2023年12月12日 Mining, metallurgical, enrichment and processing enterprises require a large amount of electricity consumption Among them, hydrometallurgical and enrichment enterprises currently consume 5060% (PDF) Control of ball mill operation depending on ball load and ore 2011年7月1日 Request PDF Grinding in an air classifier mill Part I: Characterisation of the onephase flow In this and the related second paper [1], we present an indepth study of the twophase flow and Grinding in an air classifier mill Part I: Characterisation of the
.jpg)
Calculate Ball Mill Grinding Capacity 911Metallurgist
2015年10月15日 A) Total Apparent Volumetric Charge Filling – including balls and excess slurry on top of the ball charge, plus the interstitial voids in between the balls – expressed as a percentage of the net internal mill volume (inside 2020年7月2日 A properly seasoned charge of grinding media should be able to break large particles and not produce unnecessary ultrafine particles In recent research done by AmanNejad and Barani [93] using DEM (PDF) Effects of Ball Size Distribution and Mill Speed and Their 2015年12月17日 With a typical 6:1 reduction ratio, the power consumption of a large jaw crusher (48 by 60) is approximately 18 tons per horsepowerhour (22 t/kWh) Source: Arthur Taggart; The power consumption of a 42inch gyratory crusher is approximately 24 tons per horsepowerhour (29 t/kWh) Source: Arthur TaggartRock Crushing Rule of Thumb 911Metallurgist2017年3月20日 An effect of a grinding method, that is ball mill and high pressure grinding rolls (HPGR), on the particle size, specific surface area and particle shape of an iron ore concentrate was studiedPhysicochemical Problems of Mineral Processing Investigation
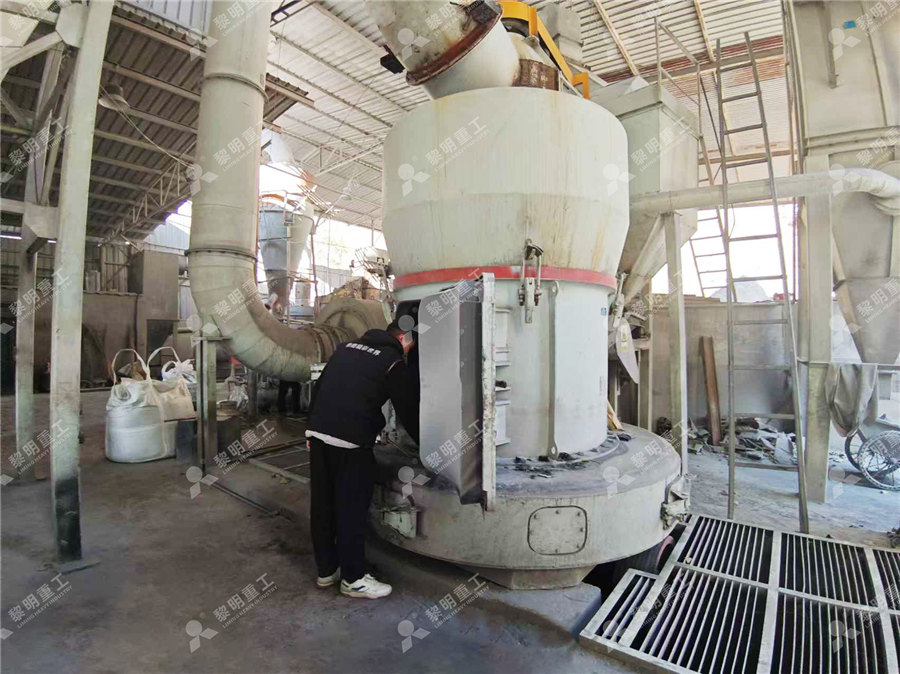
a company of cement grinding mill m with a capacity of 50 tons per hour
A company of cement grinding mill "M" with a capacity of 50 tons per hour utilizes forged steel grinding balls costing P12,000 per ton, which have a wear rate of 100 grams per tone cement milled Another cement mill "M" of the same capacity uses high chrome steel grinding balls costing P50,000 per ton with wear rate of 20 grams per ton cement milledfrom the ores The grinding of ore is a highly energyintensive process [1–4] In this process, the size of the particle obtained depends on the energy consumption of the ball mill The major challenge encountered in the process of iron ore grinding is to maintain the desired product particle size distribution (PSD) with sufficientEstimation of Grinding Time for Desired Particle Size DistributionThe results of the analyses clearly shows that using a sieve of +180µm and its bottom 180µm, the best time for grinding 05kg of Itakpe iron ore with 3kg of grinding media and a mill speed of 92 rpm is 8 minutes, yielding 1710% fines and 8290% coarse, 08 mill critical speed measured 1520% fines and 8480% coarseRegrind of metallic ores with Vertical Mills Academia2017年1月17日 Grinding mills are infamous for their extremely low energy efficiency It is generally accepted that the energy required to produce new mineral surfaces is less than 1% of the electricity consumed Breaking down energy consumption in industrial grinding mills
}@~3SRDG`IA1KP_ICWAA.jpg)
An investigation of performance characteristics and energetic
2020年8月12日 This study shows the performance of a currently running vertical roller coal mill (VRM) in an existing coalfired power plant In a power plant, the coal mill is the critical equipment, whose 2023年1月12日 The grinding balls are made of silica with a diameter of 3–5 cm and an approximate weight of 50–70 g, and the inner walls of the mill are made of silica stones with special dimensions Before the preparation of SiO 2 NPs using ball milling, the preparation stage was performed to remove impurities because the silica stone was directly obtained from the mineFacile, fast, and green preparation of highpurity and quality silica