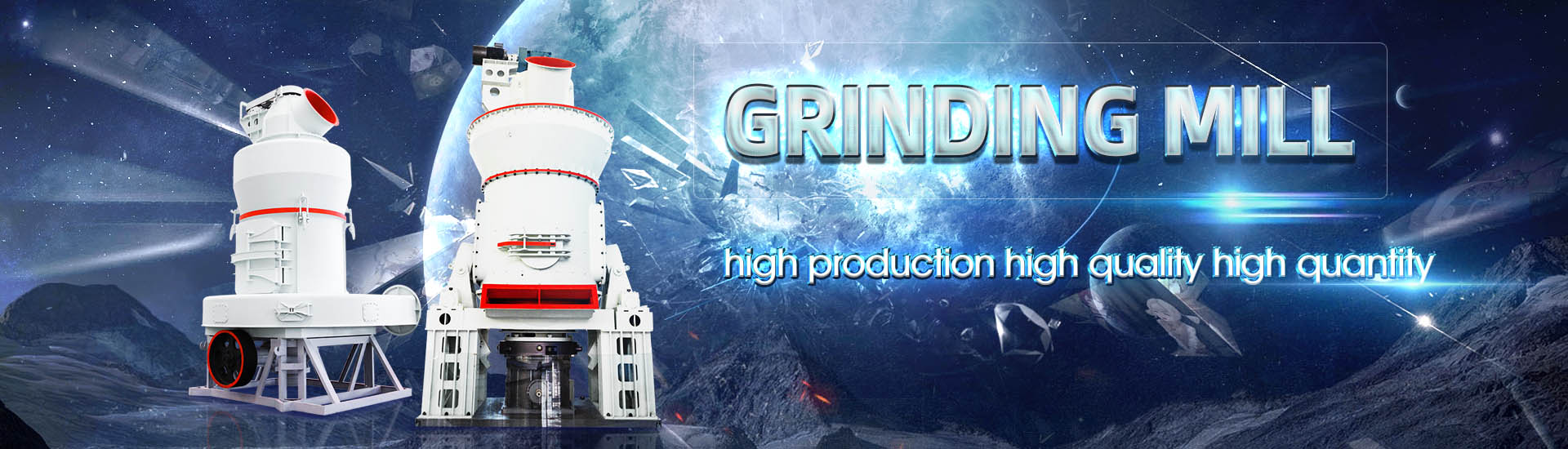
Dimensions of crocodile ore grinding mill
.jpg)
TECHNICAL NOTES 8 GRINDING R P King
the tumbling charge This energy is required to cause grinding of the material in the mill The shape and dimensions of the lifters control the tumbling action of the media The tumbling action is difficult to describe accurately but certain regions in the mill can be characterized in terms of IsaMill™ uses horizontal milling to secure better energy efficiency, product size and availability The IsaMill™ has realworld success in 143 metalliferous installations across 23 countries It’s IsaMill™ Glencore Technology2023年7月20日 According to the different grinding medium, the grinding mill is divided into three types: (1) ball mill – it is used widely, and almost all materials can be triturated by ball mill; (2) Ore Grinding SpringerLink2017年9月1日 The objective of this work is to assess the influence of fine grinding in ball mills and stirred mills on valuable mineral liberation and particle shape characteristics of UG2 ore, a Fine grinding: How mill type affects particle shape characteristics

Grinding Mills — Types, Working Principle Applications
2018年8月17日 SemiAutogenous Mills/ SAG Mills (primary grinding mill) — these mills use grinding balls with forces of attrition, impact, and abrasion between grinding balls and ore particles2016年11月7日 In the first illustration is shown a laboratory batch mill of about 1litre capacity, whilst in Fig 12 is shown a tube mill used in the cement industry the tube having a diameter of about 8 ft and length of about 45 ftGrinding Mills – Common Types 911 Metallurgist2021年1月8日 For peak performance and balancing the power available in the SAG mill and ball mill, the transfer size must be measured and controlled The transfer size will be 500 microns A CRITICAL REVIEW OF GRINDING DESIGN PROCEDURES FOR THE In the calculation of energy consumption in ball mills, classical theories mainly consider factors like the charge fill level, lifter dimensions, the number of lifters, and the rotational speed of the Analyzing the influence of lifter design and ball mill speed on
.jpg)
How grinding mill design changed over the last 30 years
2020年6月3日 Grinding mills are some of the most important equipment in mines, processing over a few thousand tons of ore every hour It is not uncommon to see these days that a single line of a grinding circuit consisting This document provides specifications for various models of ball mills for wet and dry grinding applications Ball mills are used to reduce materials down to finer sizes by means of balls impacting and grinding inside a rotating cylinder The Ball Mill Capacity Dimensions Paul o Abbe PDF Mill 2023年4月23日 grinding media in a grinding mill with about 2630 wt% chrome by Chen et al [37] using a phosphate ore in a modified ball laboratory ball mill whose electrochemical potential could be controlled(PDF) Grinding Media in Ball MillsA ReviewThe first example of using an agitated vessel and grinding media for comminution was in 1922 when Szegvari stirred a gallon can full of pebbles to rapidly disperse a sulphur suspension [19]This was developed into the first ‘stirred ball mill’ by Klein and Szegvari in 1928 [20]This prototype was refined into the Attritor mill, a low tip speed (3–5 m/s [21]) vertical pin mill which Semi Autogenous Grinding Mill ScienceDirect Topics
.jpg)
Design of the 40 foot SAG Mill Installed at the Cadia Gold Copper
mill specific power, pilot plant ball mill specific power, pilot plant product size distributions and Bondtype calculations (as reported by Rowland (Rowland, 1982) and modified by Minproc) SAG Mill Dimensions: The SAG mill was designed for monzonite ore, with allowance in the mine schedule for reduced throughput when treating the harder 2018年12月24日 ABSTRACT In this study, simulation aided design of grinding circuit for a gold mine in Iran is presented The main parameters for the design of the grinding circuit are the ore specifications and EVALUATION OF THE ALTERNATIVES FOR GOLD ORE GRINDING 2023年10月27日 The ball mill is a rotating cylindrical vessel with grinding media inside, which is responsible for breaking the ore particles Grinding media play an important role in the comminution of mineral ores in these mills This work reviews the application of balls in mineral processing as a function of the materials used to manufacture them and the mass loss, as A Review of the Grinding Media in Ball Mills for Mineral 2023年10月30日 Mill's diameter and the dimensions of the lifter used in the DEM simulation (LH: lifter height (mm); LTW: lifter top width (mm)) +10 Lifter geometry and rotational speed effects on mill torqueAnalyzing the influence of lifter design and ball mill speed on
.jpg)
Factors affecting ores grinding performance in ball mills
Speed also plays a role in ore grinding; too high of a speed can cause damage to the mill gears and other components, while too low of a speed can cause excessive wear on these same components It is important to find a balance between these two variables in order to achieve optimal grinding performance2013年8月3日 In Grinding, selecting (calculate) the correct or optimum ball size that allows for the best and optimum/ideal or target grind size to be achieved by your ball mill is an important thing for a Mineral Processing Engineer AKA Metallurgist to do Often, the ball used in ball mills is oversize “just in case” Well, this safety factor can cost you much in recovery and/or mill liner Calculate and Select Ball Mill Ball Size for Optimum Grinding2023年10月27日 The ball mill is a rotating cylindrical vessel with grinding media inside, which is responsible for breaking the ore particles Grinding media play an important role in the comminution of mineral A Review of the Grinding Media in Ball Mills for 2015年8月6日 Rubber liners absorb the impact of the larger grinding media and thus protecting – the mill structure and prolonging it’s life Weight: Rubber weighs about 15% of an equivalent volume of steel This means that a rubber liner Grinding Mill Liners 911Metallurgist
.jpg)
Ore Grinding SpringerLink
2023年7月20日 Therefore, the rod mill is mostly used for coarse grinding of the previous period of ball mill, or grinding of brittle materials and materials against overcrushing, such as tungsten and tin ore before gravity separation; and (3) autogenous mill – it refers to the materials which themselves are collided and ground mutually to be crushed when the grinding mill rotates, and Download Table Dimensions and operating parameters of Aghdarreh SAG mill from publication: Assessment of grinding flowsheet designs of aghdarreh gold ore processing plant based on circuit Dimensions and operating parameters of Aghdarreh SAG mill2021年12月31日 Manual ones might be cheaper, but you need to apply a lot of energy grinding grains with a manual flour mill A fully automatic flour mill can be convenient to use #4 Child Safety Features Child safety options ensure the flour mill’s doors are 10 Best Flour Mills for Home Use in India (Atta Chakki) 年7月29日 As you increase the volume of the through put, the time that the ore has to react to the grinding media is lessened As you add ore to the mill you are also adding WATER and changing density which affects the slurry rheology and workings of the grinding action inside that mill This water is one of the main controls that you have over your grindEffect of Water Density on Grinding Mill 911Metallurgist
.jpg)
DYNAMIC DESIGN FOR GRINDING MILL FOUNDATIONS
2019年1月30日 The weight of mill and charge (ore and grinding media) is 3,452 tons The substructure method is used for dynamic analysis of the ball mill foundation, that is, the structure and soil are 2018年4月8日 Referring to Table VI the L/D can be between 175 and 20 or even greater Referring to Table VII a 305 meter (10 foot) by 305 meter (10 foot) overflow ball mill with a 40 percent by mill volume ball charge, new liners and 50 mm (2″) balls draws 491 HP Using equation 5 there will be a loss of 055 Kw (074 Hp) per metric tonnes of ballsHow to Size Design a Regrind Ball Mill 911MetallurgistThis mill accepts grinding set weights of up to 30 kg, the largest grinding jar has a volume of 2,000 ml chemical industry, etc, it has two ore grinding Compare this product Remove from comparison tool ball grinding mill horizontal for ore ball grinding mill Final grain size: 74 µm Ore mill, Ore grinding mill All industrial manufacturerslifter number, and mill rotational speed on mill performance In their work, the DEM simulations are compared with the experimental results Li et al [15] simulate the particle motion in a ball mill for five distinct lifter shapes at various rotational speeds Rectangular lifters and Analyzing the influence of lifter design and ball mill speed on
.jpg)
Ball Mill Grinding 911Metallurgist
2021年4月16日 Three “ores” were used in the Ball Mill Grinding experiments It is doubtful whether material more resistant to grinding can be found among the world's ores The third conical mill had dimensions of 235 by 116 by 72 The second primary function of a liner is to transfer rotary motion of the mill to the grinding media and charge After all, it is the interface between the mill and the grinding charge Although work on the grinding action in mills was published 100 years ago (White 1905 and Davis 1919), the firstThe Selection and Design of Mill Liners 911 Metallurgist2012年4月17日 Mill load is an important equipment index which is closely related to operating efficiency, product quality and energy consumption of grinding process Due to high dimension and collinearity of (PDF) Effect of Slurry Density on Load Dynamic and2019年8月14日 Ball mill is a common grinding equipment in concentrator Common Types of Ball mill back to top The common industrial ball mills mainly include cement ball mill, tubular ball mill, ultrafine laminating mill, cone ball mill, ceramic ball mill, intermittent ball mill, overflow ball mill, grid ball mill, wind discharge ball mill, double bin ball mill, energy saving ball millThe Ultimate Guide to Ball Mills Miningpedia
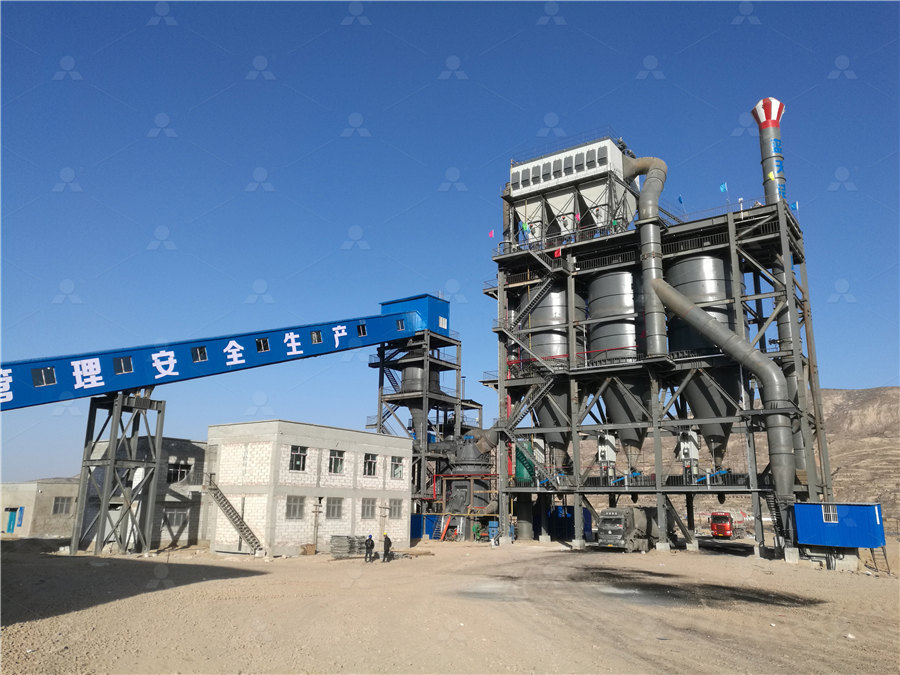
The Effect of Grinding Media on Mineral Breakage Properties of
2021年12月11日 In experiments done by Si et al [98] using magnetite ores to determine the effect of grinding media diameter on the mineral liberation degree, 8 different sizes of steel balls were used ie 2023年12月12日 Ore can have various properties, such as hardness, density, moisture content, etc, which can affect the ore’s productivity and grinding efficiency Discover the world's research 25+ million members(PDF) Control of ball mill operation depending on ball load and ore 2024年5月17日 A SAG (SemiAutogenous Grinding) mill is a giant rotating cylinder filled with grinding media and the ore being reduced As the mill rotates, the grinding media lifts and the impact crushes the feed material SAG mill control refers to the practice of managing the mill load, which is the amount of material inside the mill at any given timeA guide to SAG Mill management2022年5月23日 Grinding experiments were conducted in a laboratoryscale stirred mill on a lowgrade PGE bearing chromite ore HighPressure Grinding Rolls (HPGR) product of −1 mm was used as feed material to Modeling and application of stirred mill for the coarse grinding
.jpg)
Ball Mill Design/Power Calculation 911Metallurgist
2015年6月19日 The basic parameters used in ball mill design (power calculations), rod mill or any tumbling mill sizing are; material to be ground, characteristics, Bond Work Index, bulk density, specific density, desired mill tonnage capacity DTPH, operating % solids or pulp density, feed size as F80 and maximum ‘chunk size’, product size as P80 and maximum and finally the type of 2018年4月17日 Mill Sizing: After laboratory and pilot plant testing confirm the feasibility of autogenous or semiautogenous grinding, it can be used to establish the exact grinding circuit and mill sizeIn the pilot plant tests, the tare power of the pilot plant mills should be determined before and after each test run The tare power should be for the empty millAutogenous and SAG SemiAutogenous Mill Design CalculationsKeywords: iron ore; ball mill; modeling; simulation; population balance model; slurry density 1 Introduction It has been well over half a century since Austin and Gardner [1], followed by Reid [2], applied the concept of firstorder breakage kinetics to steadystate continuous grinding in a mill The grindingOptimization of Solids Concentration in Iron Ore Ball Milling 2023年4月20日 As such, the present work applies a phenomenological ball mill model in integrated process simulations to describe the performance of an industrial ball milling and classification circuit for Simulation of industrial PGM and iron ore ball milling
.jpg)
How Ball Mill Ore Feed Size Affects Tonnage Capacity
2017年7月26日 Soft ore Work Index 13 = 100,000/90,000 = 11 kwh/t Hard ore Work Index 16 = 100,000/65,000 = 154 kwh/t For the purposes of this example, we will hypothesize that the the crushing index of the hard ore with the increased energy input of 154 kw/t reduces the ball mill feed size to 6,500 micrometers2019年1月1日 A grain size reduction hammer mill for crushing corn (Zea mays L) was designed depending on variety characteristics and by using computer aided design “ANSYS” softwareDesign and Evaluation of Crushing Hammer mill ResearchGate2015年3月10日 Within the scope of the study ore grinding performance of the vertical roller mill was investigated with mobile pilot plant In this context, chalcopyrite ore of a plant having rod and ball milling circuit was ground under different operating modes eg, air swept and overflow, and process conditions, then samples were collected around the systemCopper ore grinding in a mobile vertical roller mill pilot plant2023年10月17日 3 Ultrafine Powder Grinding Mill Ultrafine powder mill (threering / fourring mediumspeed micropowder mill) feed particle size ≤25 mm, production capacity 0545 t/h, production fineness 1503500 mesh,it is a highefficiency and lowconsumption ultrafine powder processing equipment that successfully replaces the traditional jet mill and complex process How to choose a suitable ore powder grinding mill?
.jpg)
A comparison of wear rates of ball mill grinding media
2016年1月1日 In wet grinding practice, highstress abrasion occurs over a small region when ore particles are trapped between the grinding balls and the mill liner, and the load is sufficient to fracture 2014年10月1日 In a test performed in the Loesche test center in Germany, copper slag grinding saved 229% energy in an airswept model and 344% energy in an overflow model [13,14]Copper Ore Grinding in a Mobile Vertical Roller Mill Pilot Plant1 Grindability: The grindability of the ore affects the efficiency of the grinding mill Harder ores require more energy and longer grinding times, which can impact the mill's performance and operational costs 2 Media andliner Wear: The condition of the grinding media and liners affects the mill's efficiencyUnderstanding the operation of grinding mills in the mining and 2021年6月17日 Due to its strong lifting capacity and excellent grinding performance, the trapezoidal liner is widely used in the SAG mill The structure of the trapezoidal liner is shown in Fig 1, the main dimensions are: dip angle \(\tau\), length of the top edge \(L\) and height \(h\)Dip angle \(\tau\) determines the trajectory of the mediums in the SAG mill, which directly affects PARAMETER OPTIMIZATION OF LARGE SAG MILL LINER BASED