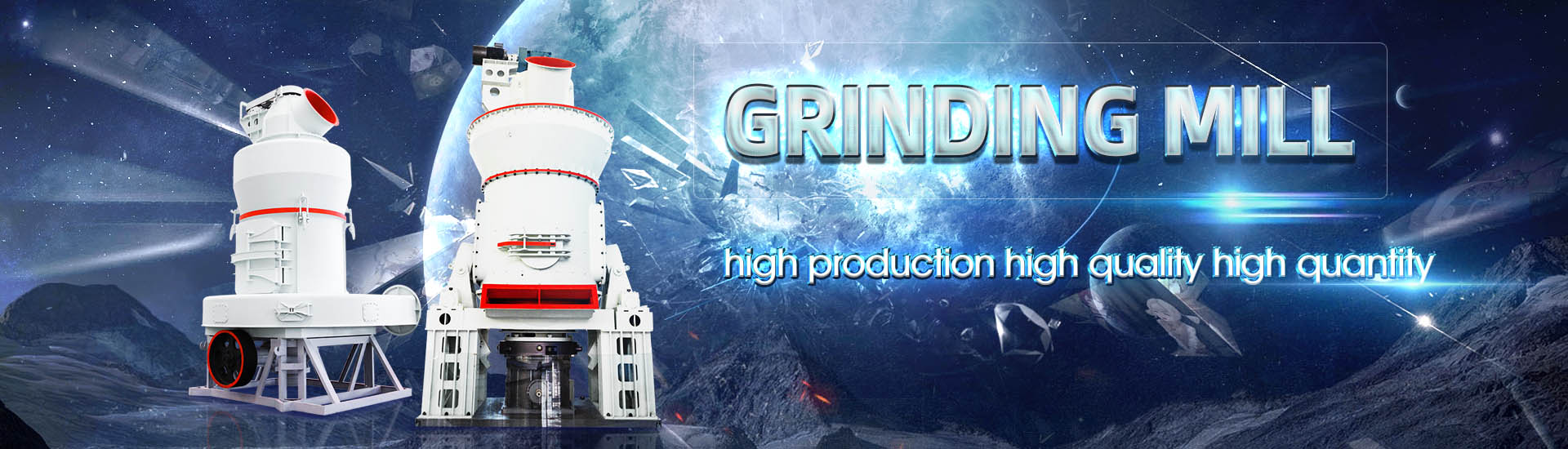
Limestone powder desulfurization system
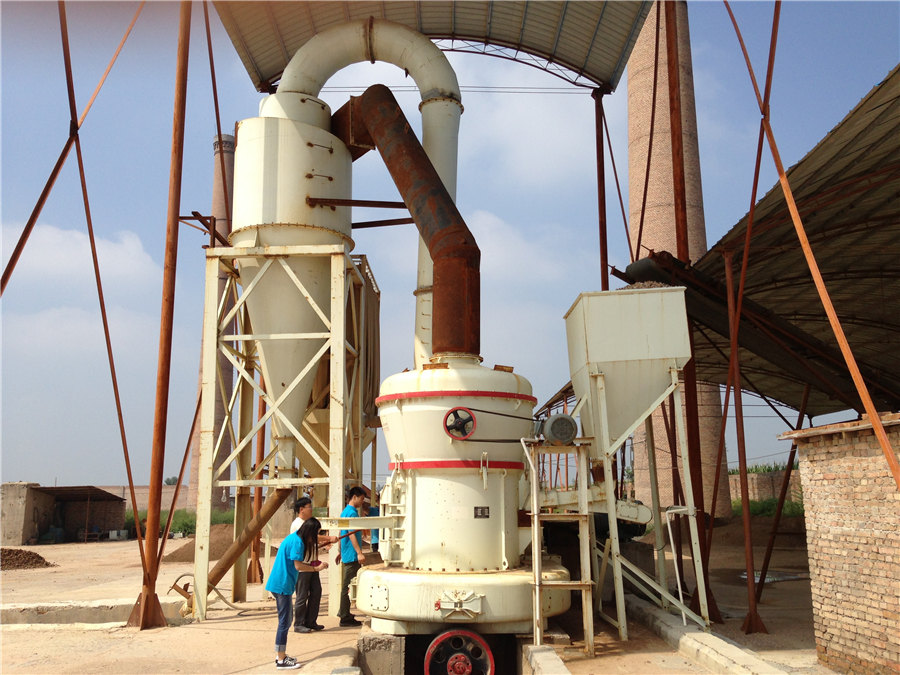
Desulfurization characteristics of limestone slurry with added
2023年3月15日 A desulfurization reaction was performed in bubbling reactor to investigate the effect of six different organic acid additives on improving desulfurization in the limestone slurry 2021年12月1日 In this study, a promising approach of employing lowgrade limestone with different particle sizes as absorbent in wet flue gas desulfurization technique was investigated, Insights into the desulfurization mechanism of lowgrade 2015年10月30日 This study investigated that status of domestic and international furnace desulfurization and desulfurization characteristics of limestone for fluidized bed use depending on the technology(PDF) A Review of Desulfurization Technology using 2006年7月18日 Effect of adjusted mesoscale drag model on flue gas desulfurization in powderparticle spouted beds Frontiers of Chemical Science and Engineering 2022 , 16 (6) , 909920PilotPlant Technical Assessment of Wet Flue Gas Desulfurization
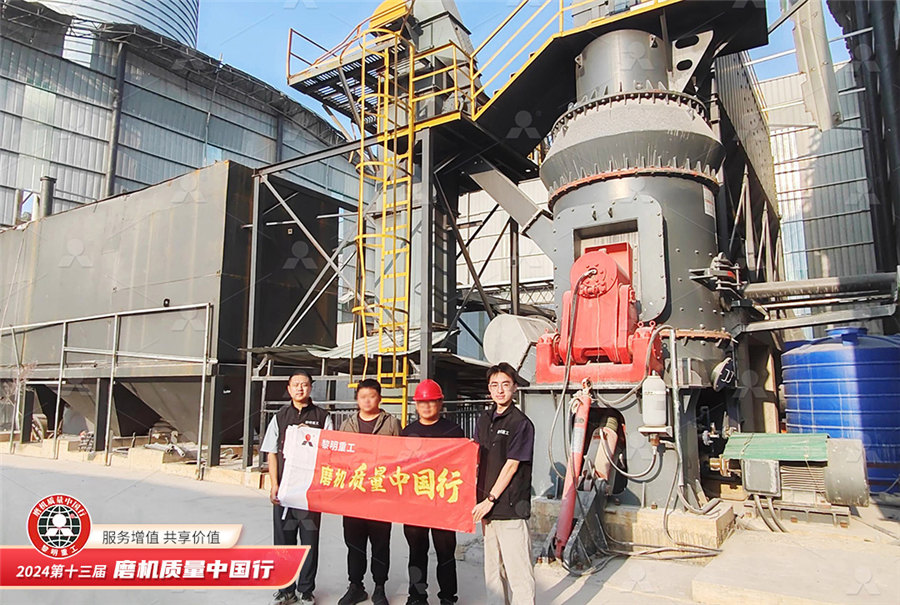
Modeling of the wet flue gas desulfurization system to utilize low
2020年11月11日 Wet flue gas desulfurization was simulated to improve gypsum production using lowgrade limestone Highgrade limestone with 94 wt% CaCO3 content is used for To remove the SO2, the flue exhaust from a coalfired power plant is commonly bubbled through a mixture of lime or limestone and water The resultant reaction typically captures 95 % or Analysis of limestone for flue gas desulfurization in a power plant2001年5月19日 A detailed process model of the wet limestone flue gas desulfurization system has been presented This model can be used to calculate indispensable parameters for Model of the Wet Limestone Flue Gas Desulfurization Process for 2021年1月1日 The results show that the limestone sludge in recycled water is possible to be used as a desulfurizer Due to the large amount of impurities and lower reactivity of limestone Feasibility Analysis and Key Issues of Using Limestone Sludge in
.jpg)
Enhancement of citric acid on lowgrade limestone wet
2022年6月15日 Developing lowgrade limestone as absorbents has been recognized as a prerequisite for industrial application of wet flue gas desulfurization (WFGD) due to the serious Before flue gas desulfurization was installed, the emissions from the Four Corners Generating Station in New Mexico contained a significant amount of sulfur dioxide The G G Allen Steam Station scrubber (North Carolina) Fluegas desulfurization (FGD) is a set of technologies used to remove sulfur dioxide (SO 2) from exhaust flue gases of fossilfuel power plants, and from the Fluegas desulfurization WikipediaAbout 90% thermal power plants in Japan, Germany, and the United States adopted this technology for the flue gas desulfurization Part2 2 Working Principle Limestone is used as the desulfurization absorbent Limestone is crushed and ground into powder Limestone powder is mixed with water to form the absorption slurryLimestoneGypsum FGD Wet Desulphurization2015年7月27日 3 Flue Gas Desulfurization Technologies Flue gas desulfurization is an efficient method for the reduction of the sulfur dioxide emissions Citation 2 Many processes are available in the market, such as (a) wet scrubbers, (b) spray dry scrubbers, (c) sorbent injection, (d) regenerable processes, and (e) combined SO 2 /NO X removal processes The different flue Review of Design, Operating, and Financial Considerations in
.jpg)
Model of the Wet Limestone Flue Gas Desulfurization
2001年5月19日 A detailed process model of the wet limestone flue gas desulfurization system has been presented This model can be used to calculate indispensable parameters for estimating costs and next to 2021年2月1日 Compared with limestonebased wet flue gas desulfurization (WFGD), magnesiabased WFGD has many advantages, but it is not popular in China, due to the lack of good wastewater treatment schemesLimestoneGypsum Wet Flue Gas Desulfurization Wastewater Treatment2022年6月15日 However, the desulfurization efficiency would be definitely less optimistic for WFGD process when using lowgrade limestone as absorbent in view of its relatively large contents of impurities including CaMg(CO 3) 2, SiO 2, Al 2 O 3 and Fe 2 O 3 [13]As such, possibly effective attempts to upgrade the lowgrade limestone have been actively studied in Enhancement of citric acid on lowgrade limestone wet desulfurization 2024年1月10日 It offers a smaller physical size and lower initial cost than wet desulfurization systems, of predicting SO 2 emissions and removal in limestonegypsum WFGD systems Powder Technol 405 Modeling based on machine learning to investigate flue gas
.jpg)
Flue Gas Desulfurization by Limestone and Hydrated Lime
Flue Gas Desulfurization by Limestone and Hydrated Lime Slurries Ayşe Özyuğuran*, Ayşegül ErsoyMeriçboyu Chemical and Metallurgical Engineering Faculty, Istanbul Technical University, 34469 MaslakIstanbulTurkey The sulfation properties of six different natural limestone and hydrated lime slurries were investigatedLimestone powder (kiln dust) The volume of the limestone slurry tank meets the 2h absorbent consumption of the kiln tail flue gas desulfurization system, and the volume is 8m3 The limestone slurry tank includes a tank body and anticorrosion, an Limestonegypsum Desulfurization Process in Cement PlantProcess development of e!ective semidry #ue gas desulfurization by a powderparticle spouted bed Kagaku Kogaku Ronbunshu, 22, 1400}1407 Guo, Q, Kato, K (1998) The e!ect of operating conditions on SO 2 removal in semidry desulfurization by a powderparticle spouted bed Kagaku Kogaku Ronbunshu, 24, 279}284 IEA Coal Research (1997)Use of limestone for SO2 removal from flue gas in the semidry 2017年7月1日 The most common types of FGD system are based on the contact between the flue gases and an alkaline sorbent such as lime or limestone (Wang et al, 2005)Furthermore, the major types of largescale power plant FGD systems include (i) spray towers, (ii) spray dryers and (iii) dry sorbent injection systems (Song et al, 2012)These FGD systems can achieve about Enhancing the recovery of gypsum in limestonebased wet flue
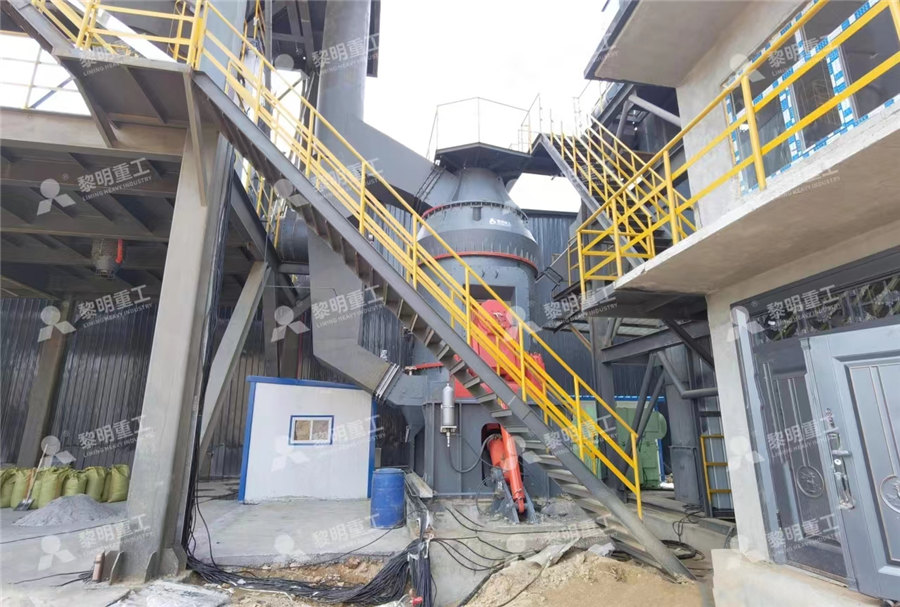
6 important points for Limestone powder uses ZME Zohdy
2024年1月18日 Limestone Powder for Flue Gas Desulfurization Lime stone powder can be effectively used in flue gas desulfurization (FGD) processes to reduce air pollution Lime stone powder is also utilized in water treatment systems to improve water quality It acts as a coagulating agent, 2006年8月1日 A generic wetlimestone flow diagram is outlined in Figure 1 (The diagram also applies for systems using hydrated limeCa(OH 2)as the reagent, where equipment and vessel sizes are smaller)Wet WetLimestone Scrubbing Fundamentals Power 2024年2月1日 In the limestonegypsum WFGD system, the standard operating conditions were as follows: flue gas volume flow of 06 Nm 3 /h (where Nm 3 refers to a cubic meter at normal conditions of 27315 K and 101325 kPa), inlet flue gas temperature of 120 ℃, desulfurization solution temperature of 40 ℃, pH of desulfurization solution of 55, desulfurizing solution Formation and migration of soluble ions in condensable 2022年8月15日 When limestonebased WFGD technology is applied to flue gas desulfurization under oxygenenriched combustion conditions, it is necessary to fully consider the influence of the flue gas characteristics after oxygenenriched combustion on CaCO 3 dissolution, SO 2 absorption, S IV oxidation, and CaSO 4 crystallization, which are processes that occur in the Limestonebased dualloop wet flue gas desulfurization under
.jpg)
Feasibility Analysis and Key Issues of Using Limestone Sludge
2021年1月1日 Feasibility Analysis and Key Issues of Using Limestone Sludge in Power Plant Desulfurization System Jian Hao 1, Shuzhou Wei 1, Xiangdong Cai 1, Gaojun Liu 2, Long Jiang 2 and Qing Li 2 Published under licence by IOP Publishing Ltd2021年2月1日 LimestoneGypsum Wet Flue Gas Desulfurization Wastewater Treatment, Tingting Ni, Yunzhong Wang, Chenghui Huang, Dongsheng Jiang, system is better than the discharge requirements of "Discharge standard of wastewater from limestonegypsum flue gas desulfurization system in fossil fuel power plants" (DL/T9972006)LimestoneGypsum Wet Flue Gas Desulfurization Wastewater 2023年2月6日 Limestonegypsum wet flue gas desulfurization (WFGD) process is widely used in coalfired power plants in China because of its technical characteristics of high desulfurization efficiency, mature process, and strong adjustability (Córdoba, 2017; Wang et al, 2010)With the continuous improvement of atmospheric emission standards, the demands for slurry quality Diagnosis and Traceability Analysis of Slurry Foaming of Limestone 2019年3月13日 In the flue gas treatment systems in coalfired power plants, WFGD systems are commonly installed downstream of the electrostatic precipitators (Sui et al Citation 2016) and the pressure charging fans, operating at positive pressure Exhaust flue gas enters the WFGD system from the entrance, which is located at the lower part of the towerModeling and optimization of wet flue gas desulfurization system
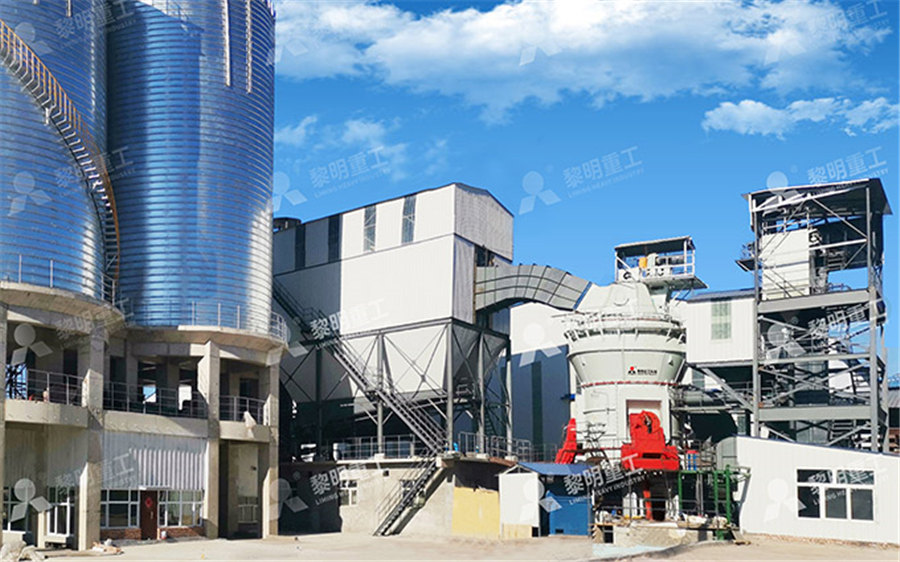
Status of Flue Gas Desulphurisation (FGD) systems from coal
2015年3月15日 Depending on the SO 2 concentrations and the excess air in the flue gas, as well as on the pH of limestone slurry, some systems may be operated in the natural oxidation mode However, for most applications it is beneficial to control oxidation [10]In natural oxidation mode, the main product is a mixture 50–60% of CaSO 3 ⋅½ H 2 O and CaSO 4 ⋅2H 2 O in a oxidation, both in situ systems and units operating with specialized systems that are separate from the absorber reaction tank, most notably on magnesiumenhanced lime systems We are Current BW designs are achieving 99% SO 2 removal with system availability greater than 995% 2 3 a worldwide leader in supplying limestone forced oxidation units,WET FLUE GAS DESULFURIZATION (FGD) SYSTEMS BabcockFluegas desulfurization (FGD) systems have been used to limit the release of sulfur dioxide (SO 2) from coalfired power plants since the late 1960s FGD systems produced more than 45 million tons of solid products in 2015 and represent the secondlargest coal combustion product (CCP) stream by volume after coal ashFlueGas Desulphurization an overview ScienceDirect Topics2023年2月15日 The limestone powder for FGD is a minimum of 90% passing 325 mesh Transportation: deliver the limestone to the power plant in a closed tank car, sent into the limestone powder bin by a hydraulic cyclone Pulping: Suitable FGD limestone mill, low investment in power
.jpg)
Limestone Flue Gas Desulfurization System Supplier
Limestone Flue Gas Desulfurization system The professional manufacture of crushing and grinding desulfurization process,It is imperative to carry on fuel gas desulfurization process high efficiency of desulfurization Using limestone powder as desulfurizer of limestone gypsum wet desulphurization process high yieldSpecial attention is required on the fine particle control after desulfurization because a large quantity of fine particles are emitted into the atmosphere from the coalfired power plants In an attempt to figure out the transformation of fine particles during the limestone gypsum desulfurization, the physical properties of fine particles before and after the desulfurization Fine Particle Transformation during the Limestone Gypsum The limestone powder pneumatic conveying system comprises a sender, a feed valve, security of the desulfurization system is greatly improved, and environmental protection is benefited A blockage removing device is arranged to ensure smoothness of the conveying pipelinePneumatic limestone powder conveying system Google Patents2000年7月31日 Emissions Control Strategies for Power Plants Bruce G Miller, in Coal Energy Systems, 2005 Dry Flue Gas Desulfurization Technology Dry FGD technology includes lime or limestone spray drying; dry sorbent injection, including furnace, economizer, duct, and hybrid methods; and circulating fluidizedbed scrubbersDry Flue Gas Desulfurisation Technology ScienceDirect
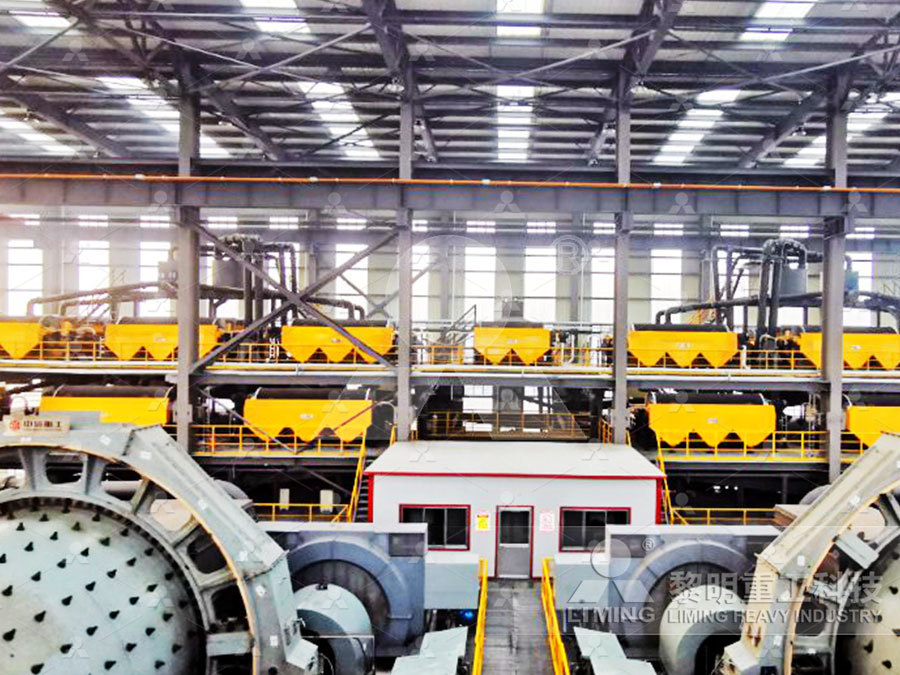
Effectiveness of Limestone Powder in Controlling the Shrinkage Behavior
2021年1月3日 Limestone (LS) powder is commonly used in concrete from the last two decades as it is widely available and having low cost Since, LS powder is mostly used as a replacement of cement for avoiding the CO2 emission; however its incorporation in concrete may influence the shrinkage behavior of the cementitious system mainly by filler and nucleation effect Therefore, DESULFURIZATION SYSTEMS James Parker, Ken Williams, Paul Zhao, containing sorbent is later removed from the flue gas as a dried solid powder For retrofits of burner systems, The overall reaction for a limestonebased desulfurization process is shown in Eq (1)CPFD MODELING OF INDUSTRIALSCALE DRY FLUE GAS DESULFURIZATION SYSTEMS2021年1月14日 Comparative analysis of limestone sludge in recycled water and desulfurization limestone is made in the chemical composition, reaction activity, crystallization properties and pH of SlurryFeasibility Analysis and Key Issues of Using Limestone Sludge in 2021年7月1日 Limestone should exhibit CaCO 3 purity of more than 94 wt% (ie, highgrade limestone) because the other substances such as SiO 2 and Al 2 O 3 decrease the purity of the desulfurization gypsum Optimization of wet flue gas desulfurization system using
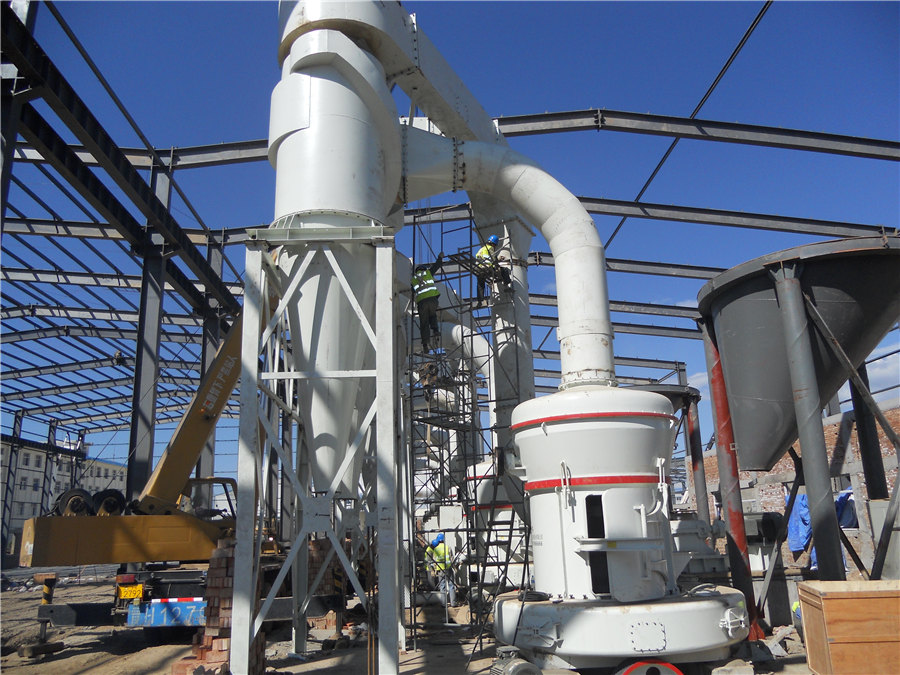
(PDF) Effectiveness of Limestone Powder in
2021年1月2日 Limestone (LS) powder is commonly used in concrete from the last two decades as it is widely available and having low cost Since, LS powder is mostly used as a replacement of cement for avoiding 2019年11月21日 The particulate matter (PM) could be simultaneously removed during the wet flue gas desulfurization (WFGD) process To analyze the underlying mechanism and removal efficiency, the PM removal process in a desulfurization system was numerically simulated based on the population balance model and general dynamics equation in this study The equation Numerical simulation of the simultaneous removal of particulate EMG can support you with limestone powder and on a large scale, limestone powder: Limestone is used in more dairy products than one might think It is used in flue gas desulfurization (FGD) systems, where it reacts with sulfur dioxide (SO2) emissions from power plants to Limestone powder Leading 1 supplier of affordable limestoneTable 2: Excitation conditions used for limestone analysis Condition Voltage (kV) Filter Atmosphere Live Time (s) Elements Low Za 4 None Vacuum 120 Mg, Al, Si Mid Za 18 Thin Pd Vacuum 30 Ca, Fe Figure 2: Calibration curve for magnesium in limestone Figure 3: Calibration curve for calcium in limestone Figure 4: Calibration curve for iron in Analysis of limestone for flue gas desulfurization in a power
.jpg)
Limestone Powder Grinding Process ALPA Powder Equipment
2024年8月26日 Therefore, most limestone powder manufacturers currently choose the closedcircuit process, which can reduce overgrinding, improve mill efficiency, and reduce energy consumption In addition, the limestone powder produced by the closedcircuit process has uniform particle size and is easy to adjust, which can meet different fineness In wet flue gas desulfurization systems, limestone (calcium carbonate) is ground to a powder in a wet ball mill Krebs cyclones are used to classify the ball mill discharge, returning coarse particles to the ball mill for further grinding Finely ground limestone (typically 90% passing 45 micron)Desulfurization system KREBS ENGINEERS DirectIndustry2015年3月1日 Wet fluegas desulfurization (WFGD), which involves the limestoneand ammoniascrubbing methods, has been extensively used in the industry because of its high SO 2 removal efficiency and Status of Flue Gas Desulphurisation (FGD) systems frommaximize the use of lowgrade limestone: gypsum purity=93 wt%, desulfurization efficiency=94%, and total limestone usage=3,710 kg/h MODEL DEVELOPMENT 1 Process Overview Fig 1 shows a workflow chart of the overall WFGD process Initially, the crushed limestone is dissolved in water in the limeModeling of the wet flue gas desulfurization system to utilize low
.jpg)
Limestonegypsum wet flue gas desulfurization based on Cyber
The limestonegypsum wet flue gas desulfurization system has been widely used due to its remarkable desulfurization effect, but there are still problems such as high operation and maintenance costs, difficult control of process indicators, and large energy consumption In view of the above problems, this paper proposes to apply the CyberPhysical System (CPS) to the