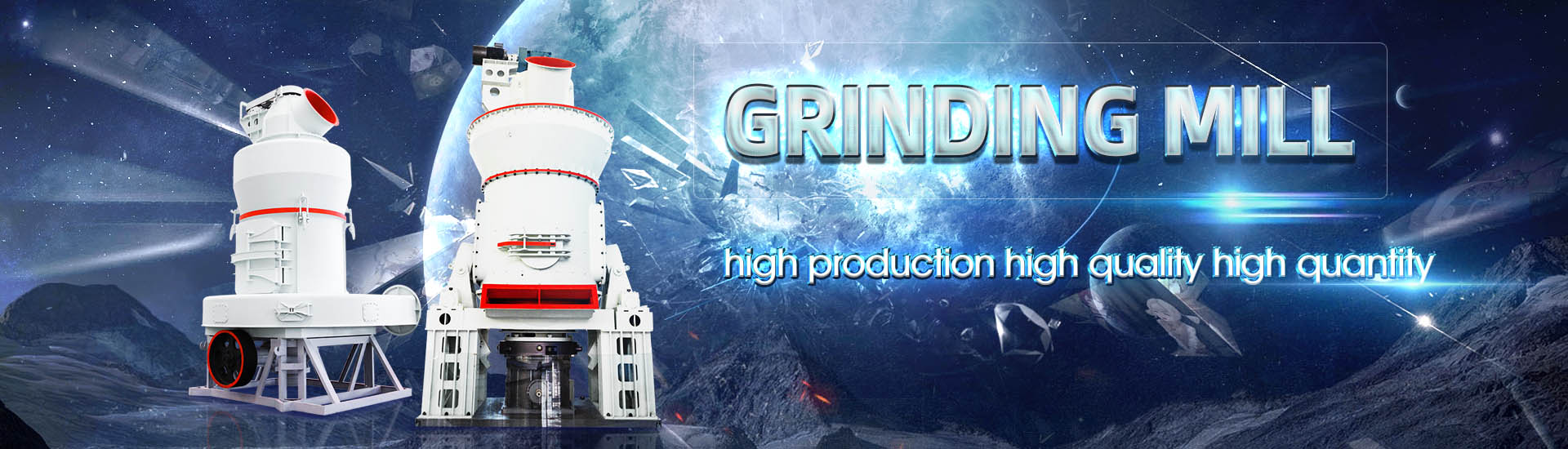
Application of cemented carbide in iron calcite grinding mill
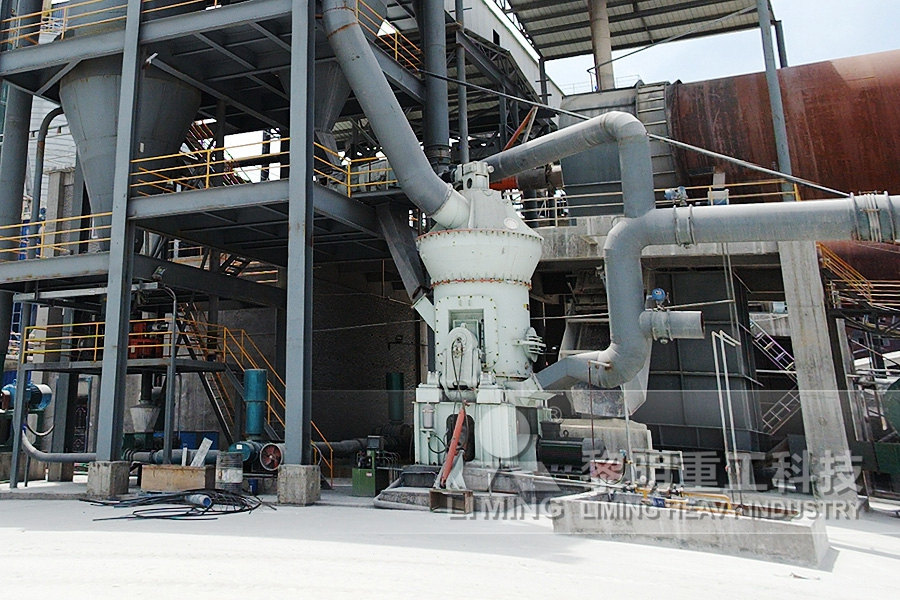
Cemented carbide microstructures: a review ScienceDirect
2019年4月1日 Nowadays, due to the superior performance of CVD and PVD coated cemented carbide grades, the use of cemented carbides containing a significant proportion of this mixed cubic carbide phase is limited Applications are found in milling applications (interrupted cut 2024年2月7日 Experimental results evidence the influence of operational conditions on the chip formation of cemented carbides as well as an important impact of the utilized cutting tool Investigation on micromilling of cemented carbide with ball nose 2023年12月22日 With the increasing application of cemented carbide, it is necessary to optimize process parameters and decrease wear behavior of diamond grains to reduce production A comprehensive review on the cutting and abrasive machining of 2020年5月29日 Milling of ferrous metals is usually performed by applying cemented carbide tools due to their high hardness, temperature and wear A comparative analysis of ceramic and cemented
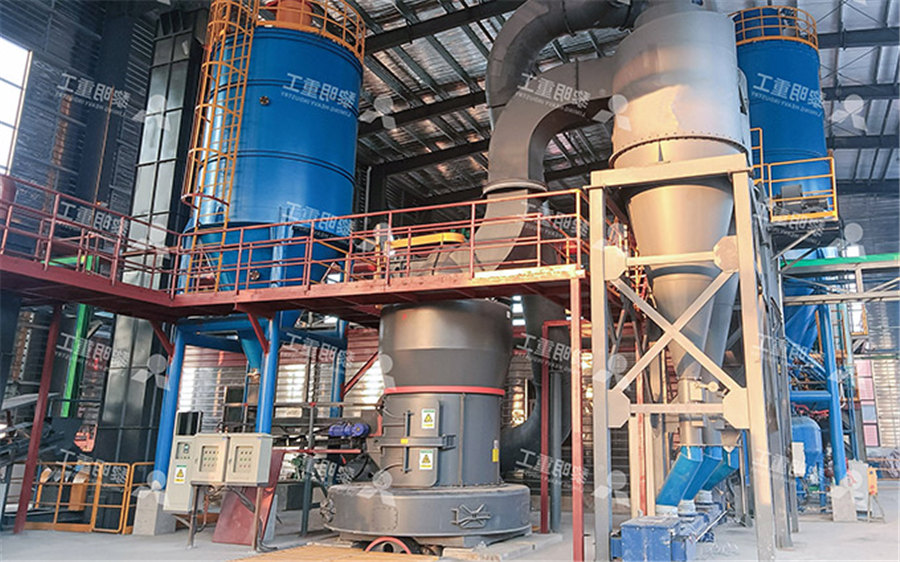
Development of a Rotary Ultrasonic Machining Device and Its Application
2022年4月16日 Considering that different amplitudes require a sufficiently large degree of discrimination, the three amplitudes of high, medium, and low are respectively selected as 2, 5 and 8 μm, using 7000, 8500, and 10000 r/min spindle speed to conduct aspheric surface machining test on YG6X cemented carbide, the feed speed is a constant value of 150 2020年5月29日 The energy consumption of the grinding machine tool during the process was measured with a three phase power meter type PEL 102 from Chauvin Arnoux Overall, the consumed energy sums up to 252 MJ for A comparative analysis of ceramic and cemented Grinding the flutes of cemented carbide end mill cutters results in high and uneven radial wear of the grinding wheel This is a consequence of the varying geometrical contact conditions over the Deep grinding of a cemented carbide end mill cutter2017年5月1日 To improve the mechanical properties of the surface of ironbased alloys, a tungsten carbideiron (WCFe) cemented carbide layer is produced on an alloy by adopting an isothermal annealing process Cutting edge damage in grinding of cemented carbides micro
.jpg)
A comprehensive review on the cutting and abrasive machining of
2023年12月22日 With the increasing application of cemented carbide, it is necessary to optimize process parameters and decrease wear behavior of diamond grains to reduce production costs Furthermore, it is necessary to better understand the main machining mechanisms in grinding of cemented carbide, which is the interaction between diamond grains and workpiece2019年4月1日 The total cemented carbide production in 1993 was around 20,000 tons and increased from 30,000 tons (2000) to almost 60,000 tons in 2008, particularly due to the entry of China on to the market From year 2000 and to date the cemented carbide production in China raised from 7000 tons (2001) to 20,000 tons (2011) and 28,000 (2017)Cemented carbide microstructures: a review ScienceDirect2008年5月1日 Grinding the flutes of cemented carbide end mill cutters results in high and uneven radial wear of the grinding wheel This is a consequence of the varying geometrical contact conditions over the Planning and analysis of grinding processes for end mills of cemented 2008年7月1日 For example, a lower balltopowder ratio results in less efficient grinding and longer grinding times (BeginColin et al, 2000) Planetary, attritor, and vibration mills are different types of (PDF) Parameters optimization in the planetary ball milling of
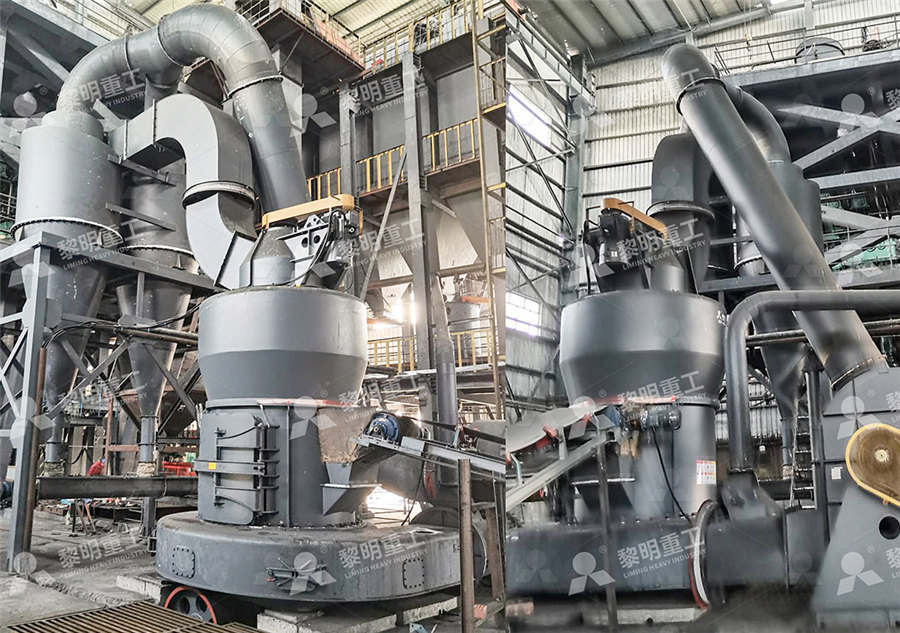
Tungsten Carbide Rings for Rolling Mill and Metalworking Applications
Hyperion Materials Technologies offers a wide range of tungsten carbide rings for use in steel production and rolling mill applications Tungsten carbide provides a unique combination of strength, hardness, and toughness bringing optimal wear resistance to the rings uniquely designed to withstand a very demanding production environmentCemented carbides are metal matrix composites where carbide particles act as the aggregate and a metallic binder serves as the matrix (analogous to concrete, where a gravel aggregate is suspended in a cement matrix) The structure of cemented carbide is conceptually similar to that of a grinding wheel, but the abrasive particles are much smaller; macroscopically, the material Cemented carbide Wikipedia2019年11月27日 Owing to their high hardness and wear resistance, cemented carbide composites (WC–Co) have many roles in the production of wearresistant parts, cutting and milling tools and printed circuit board (PCB) drills [1,2,3]Brazing technique is one the most popular methods for joining of cemented carbides to themselves or to steels in milling tools; Damaging of cemented carbide end mill with different grain 2022年10月29日 1) Cutting tool Carbide is the most common material for cutting tools in CNC machining, including turning tools, milling cutters, planers, drills, etc Tungsten cobalt cemented carbide is suitable for short chip processing of ferrous and nonferrous metals and processing of nonmetallic materials, such as cast iron, cast brass, bakelite, etc Tungsten titanium cobalt What is Cemented Carbide Cemented Carbide Properties,
.jpg)
EXPERIMENTAL INVESTIGATION OF WEARING GRINDING
research papers faculty of materials science and technology in trnava slovak university of technology in bratislava 2020, volume 28, number 47 doi 102478/rput20200014cemented carbide with grinding method, it may cause burns or cracks due to local high temperature Ultrasonicassisted grinding can be used to process hardbrittle materials like cemented carbide, ceramic and glass It could reach the ductilemode machining of hardbrittle materials and improve the material removal rate as well as reduce theDevelopment of a Rotary Ultrasonic Machining Device and Its Application 2017年7月18日 Current demands for flexible, individual microstructures in high quality result in high requirements for micro tools As the tool size defines the minimum structure size, ultrasmall tools are needed To achieve tool diameters of 50 µm and lower, we investigate the complete manufacturing chain of micro machining From the development of the machine tools and Application of UltraSmall Micro Grinding and Micro Milling 2010年1月1日 Cemented carbide shows a wide range for the combination of high hardness and toughness, making them suitable for many wear applications Adapted from [9] Different microstructures of cemented Process development and scale up of cemented carbide production
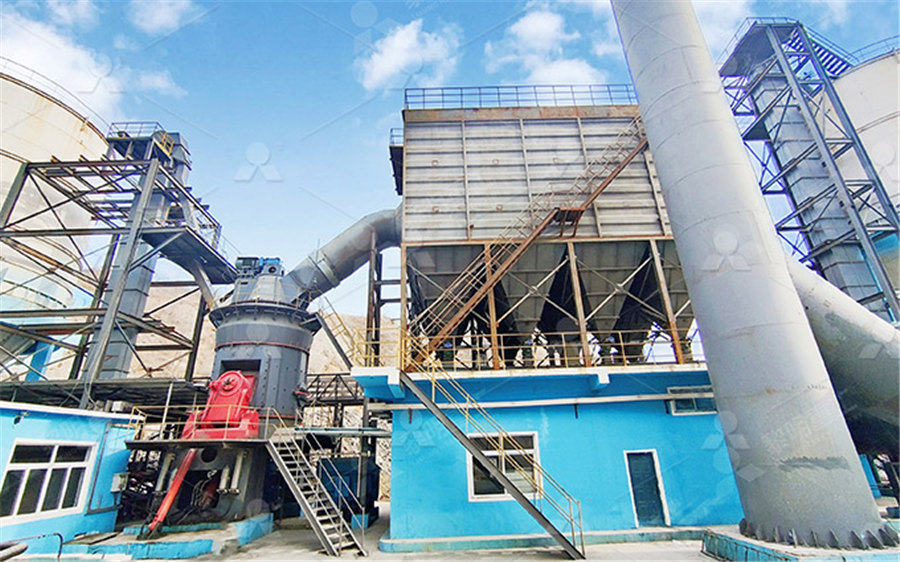
Energy Efficiency Assessment in PlungeFace Grinding of Cemented
2023年5月4日 In order to assess the energy efficiency and cutting insert quality after grinding, four lateral faces of square cemented tungsten carbide (WC–5%Co) blanks (Fig 1a), with original dimensions 125 × 125 × 476 mm, were ground in a fouraxes CNC grinding machine Agathon DOM Plus (maximum power of 16 kW and maximum rotation speed of 2400 rpm, Fig 1b) with It can be likened to concrete Small stones (tungsten carbide) are surrounded by cement (cobalt) Cemented carbide, when sintered, will have nearly twice as high gravity, and about half as much volume as before the sintering process Sintered cemented carbide is ground by a diamond grinding tool and can then be used as a cutting toolCemented carbides MITSUBISHI MATERIALS CORPORATION2023年9月19日 In response to the difficulties in machining cemented carbide, the tool cathode uses the side edge to process it so as mill the plane In the electrochemical machining process, Zhu X Investigation on electrochemical grinding (ECG) of pure iron material Int J Adv Manuf Technol 2022; 119: 885–896 Crossref Google Scholar 5Numerical simulation and experimental study on electrochemical 2018年4月3日 Cemented tungsten carbide (WC) is widely used for wearresistant applications, such as cutting tools and abrasives [141] Cemented carbide (CC) is a useful material for mining tools [142] Discussion on importance of tungsten carbide Cobalt (WcCo) cemented
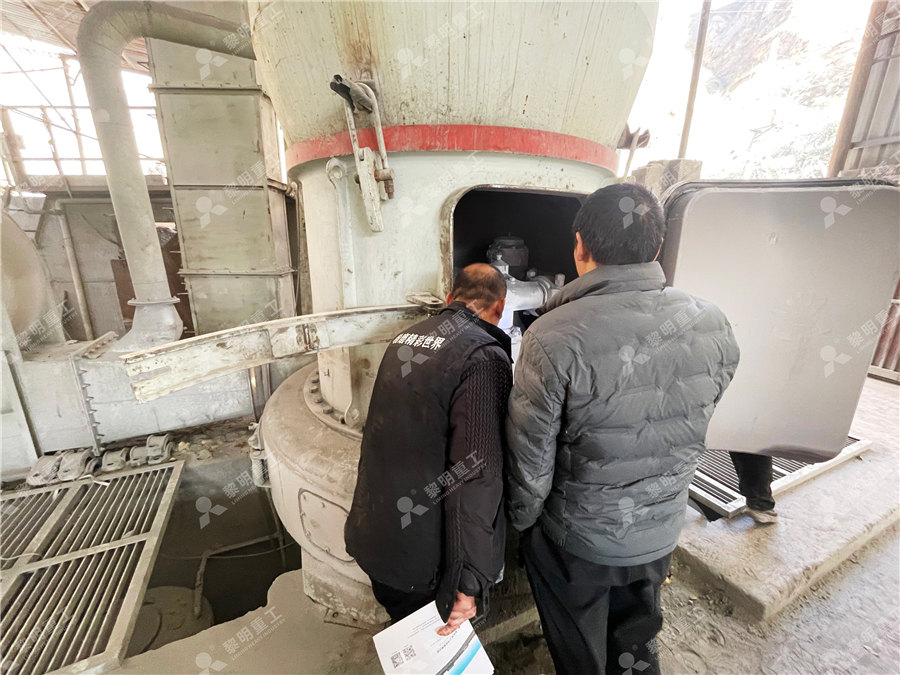
Effect of the grinding process on the surface quality of
2022年12月19日 The surface morphology and roughness of cemented carbide have a decisive impact on its performance and service life Improper grinding parameters will lead to poor surface quality and microcracks, which will affect 2019年6月27日 Cemented carbides are widely used in aerospace and mechanical processing industries due to their excellent physical and chemical properties However, cemented carbide products processed by conventional methods have such deficiencies as poor surface integrity, high surface roughness, and high consumables Given this, a method for machining blind Ultrasonic vibrationassisted grinding of blind holes and internal 2020年4月1日 Cemented tungsten carbide balls (hereafter abbreviated as WC balls) are commonly applied in the grinding of wasted tool steel for purpose of reuse owing to their extraordinary surface hardness (89 The kinetics and efficiency of batch ball grinding with cemented 2017年1月1日 performance of coated cemented carbide drills in drilling of gray cast iron under different lubricooling conditions January 2017 DOI: 1026678/ABCMCOBEM2017COB171133PERFORMANCE OF COATED CEMENTED CARBIDE DRILLS IN DRILLING
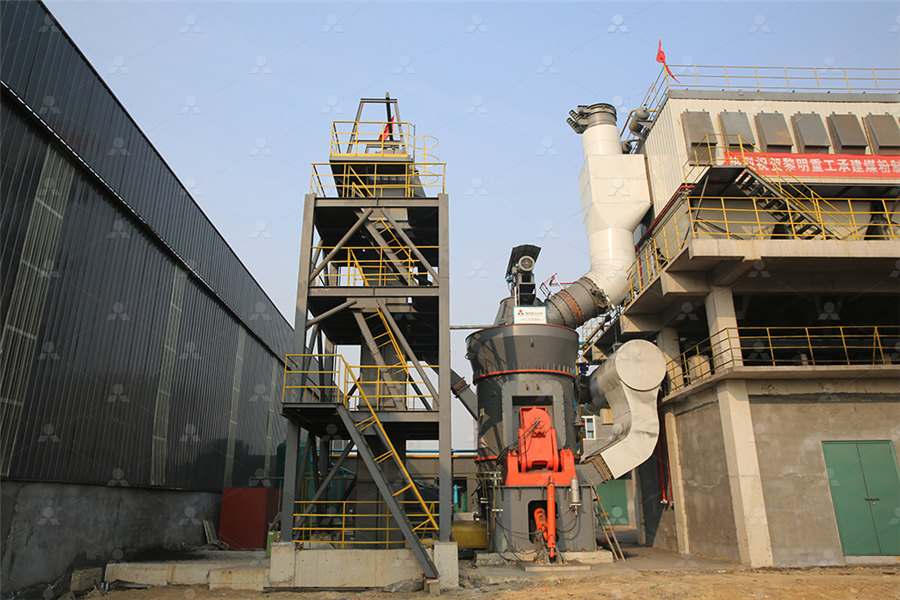
Wear Mechanism of Cemented Carbide Tool in High Speed
2018年12月5日 31 Tool Wear Many studies [21, 22] show that adhesive wear is the dominant factor of tool failure in cutting stainless steels with cemented carbide toolsIn the milling process of 0Cr13Ni4Mo, the cutting temperature can reach 800 °C and the cutting force is also high There is microscopic asperity on the rake face, and the tool’s hardness is decreased due to 2011年12月31日 However, the deep grinding process of the flutes is characterised by high and varying thermomechanical loads The high thermomechanical loads result from the high depth of cut associated with the Tool grinding of end mill cutting tools made from high 2010年1月31日 The chemicals that are added into the grinding process are called grinding additives or grinding aids In addition, the application of grinding aids is mainly adopted in the cement and calcite Effect of grinding aids on the grinding energy consumed during grinding research papers faculty of materials science and technology in trnava slovak university of technology in bratislava 2020, volume 28, number 47 doi 102478/rput20200014EXPERIMENTAL INVESTIGATION OF WEARING GRINDING
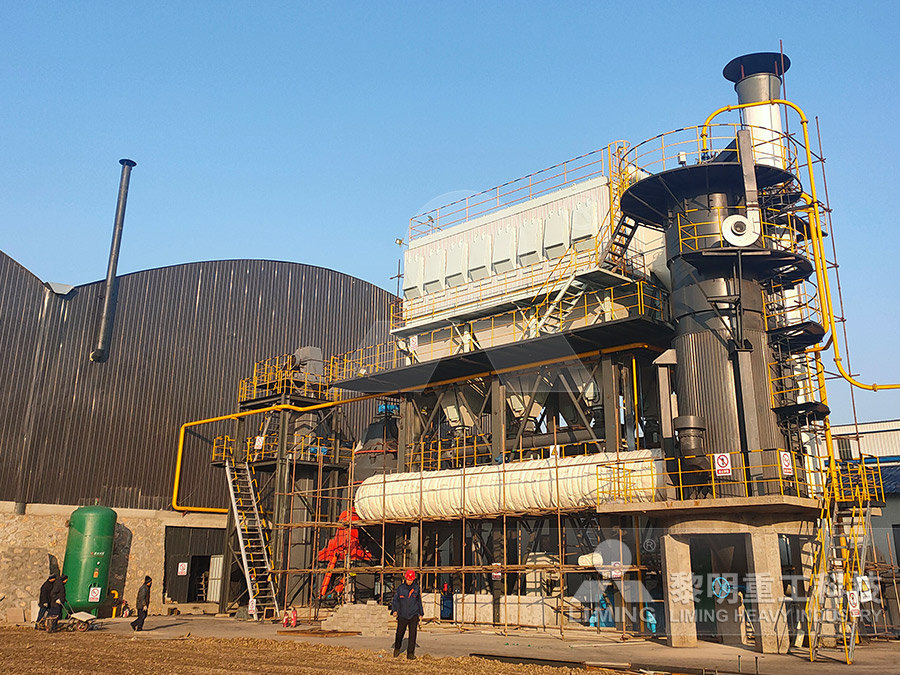
The Influence of Stirred Mill Orientation on Calcite Grinding
2021年4月21日 The purpose of this study was to investigate the dry grindability of calcite powders in a vertically and horizontally orientable laboratory batch type stirred mill The experimental results were evaluated using stress intensity analysis The performance was also compared in terms of mill orientation The results showed that the d50 values decreased with 2023年8月30日 Classification: Industry News Source: Release Time: 10:23 Views: (Summary description) Discover the stepbystep process of manufacturing cemented carbide inserts, a vital component in various industries From raw materials to final products, this article provides an indepth understandThe Manufacturing Process of Cemented Carbide Inserts: A 2023年10月27日 The ball mill is a rotating cylindrical vessel with grinding media inside, which is responsible for breaking the ore particles Grinding media play an important role in the comminution of mineral A Review of the Grinding Media in Ball Mills for 2024年2月7日 Two distinct tool geometries were employed in this study: (i) a microbull nose end mill with a tip radius of 01 mm, herein referred to as “bull nose”, and (ii) a twoflute microball end mill, herein referred to as “ball nose”, with a 05mm tool radius (refer to Fig 2b and d), both with a 1mm diameter Their geometry is described in Table 1Investigation on micromilling of cemented carbide with ball
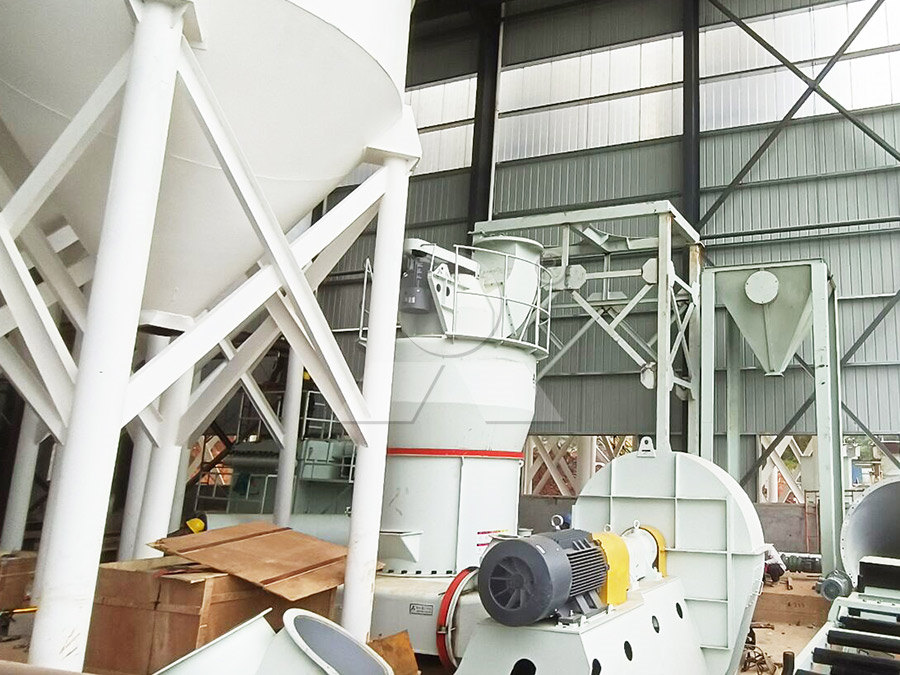
Recycling of tungsten carbide scrap metal: A review of recycling
2018年6月15日 Cemented carbide recycling methods are classified into three categories: (1) Grinding is a finishing process for high precision, With the wide application of cemented carbide, 2021年8月21日 In the forming grinding of a cemented carbide microdrill, edge burrs are generated To explore the formation of the edge burrs, the grinding parameters, such as feed rate, grinding depth, wheel service time, and wheel rotation, are analyzed experimentally Results show that the burrs on the microdrill edge are caused by material plastic flow and cumulative effect The effects of grinding process parameters of a cemented carbide 2023年6月13日 Selection of Grinding Wheel for Grinding Cemented Carbide RodsGrinding is a process of removing material from a workpiece by using an abrasive tool (such as a grinding wheel) that rotates at high speed Grinding can achieve high accuracy, surface finish, and dimensional tolerance for the workpiece However, grinding also generates heat, friction, and Introduction to Grinding of Cemented Carbide Rods2014年4月23日 The tip of the ceramic cemented carbide compound drill was ground to a 118° point angle The reference solid cemented carbide twist drill, especially designed for machining gray cast iron, is made of a fine grained carbide type K20 and characterized by a radius shaped tip, a concave chip flute profile as well as polished chip flutesActive brazed ceramic cemented carbide compound drills for
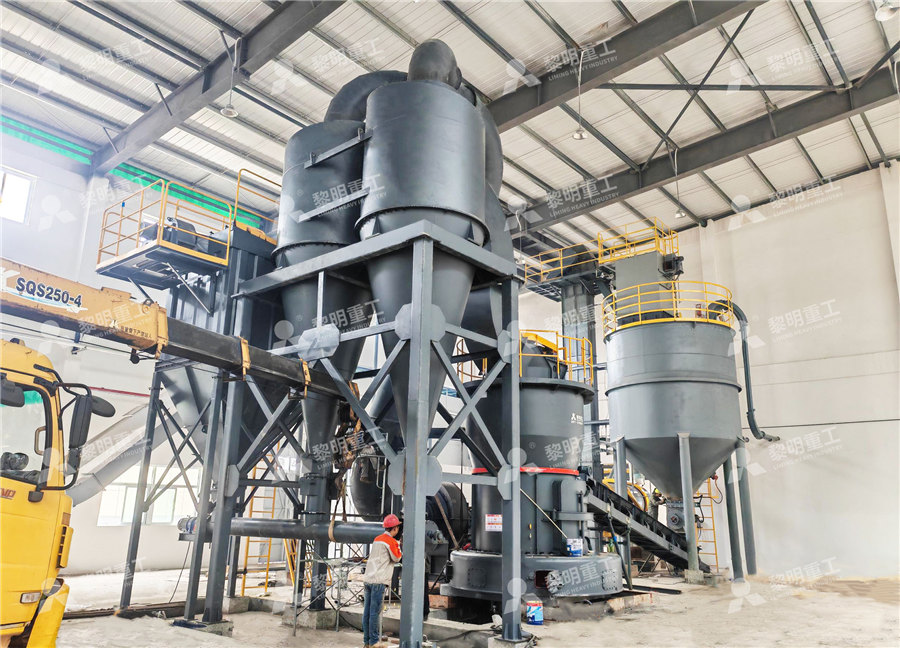
(PDF) An overview on different processes for recovery of
2014年4月24日 The manufacturing of HM tools and components is a complex powder metallurgical process, based on liquid phase sintering at temperatures in the 13501500 • C range [2]2021年9月1日 Titanium alloy Ti6Al4V has the advantages of high specific strength, good heat resistance, and strong corrosion resistance, which is widely used in the manufacturing of aerospace industrial parts However, in the side milling of titanium alloy, the temperature of the cutting area is high, and the cutting edge position is prone to breakage, which affects the Research on breakage characteristics in side milling of titanium What is coated cemented carbide cutting tool material? Coated cemented carbide currently represents 80–90% of all cutting tool inserts Its success as a cutting tool material is due to its unique combination of wear resistance and toughness, and its ability to be formed into complex shapes Coated cemented carbide combines cemented carbide Cutting tool materials Sandvik CoromantWhat applications does Cemented Carbide materials have in the professional field? Today, HRC45/55/60/65 Grinding And Ungrinding Carbide Rod $ 080 ~ $ 17486 Main Cnc Tools:End Mill,Milling Cutter,Carbide Rods, Plates, Strips, Metal Materials; Application of Cemented Carbide