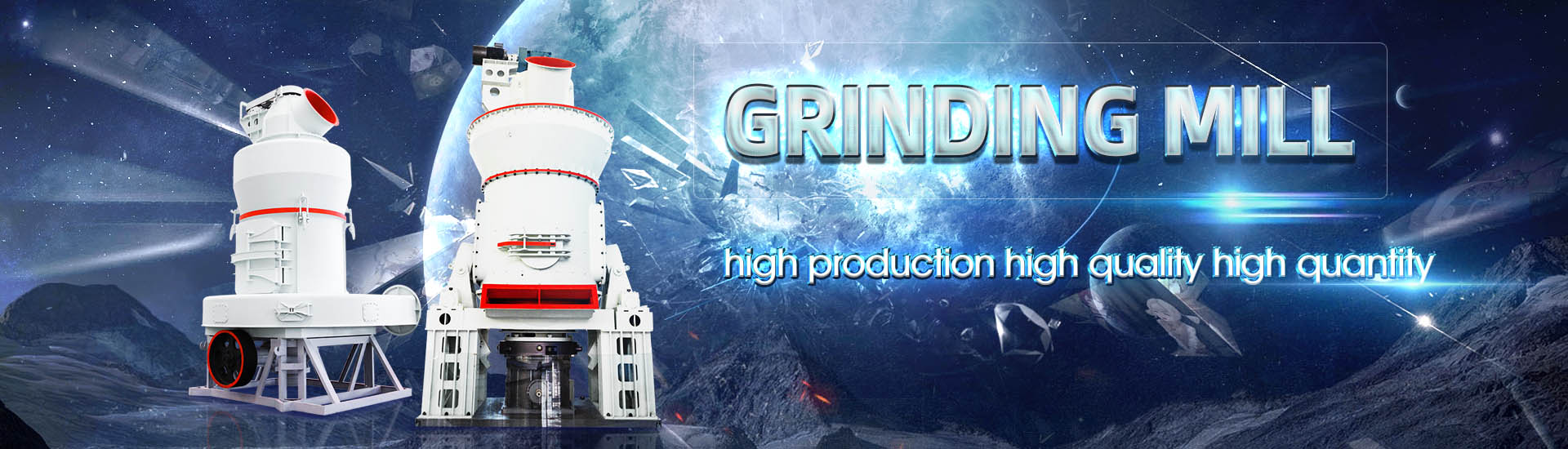
calcite mill crushing particle size
.jpg)
Research on Grinding Characteristics and Comparison of Particle
2022年10月26日 The results show that the impactcrushing capacity of Tongkeng ore and Gaofeng ore are “medium” grade and “soft” grade, respectively The crushing resistance of Tongkeng ore increases with the decrease in particle size, and the crushing effect is more AMA Style Ma S, Li H, Shuai Z, Yang J, Xu W, Deng X Research on Grinding Versions Notes2022年3月1日 To evaluate the influence of grinding aid type and dosage on the ground calcite particles, wet laser sizer measurements were conducted Fig 3 illustrates the particle size Analysis of grinding aid performance effects on dry fine milling of Calcite is a calcium carbonate mineral, which is the most common of natural calcium carbonate Therefore, calcite is a widely distributed mineral The crystal shapes of calcite are various, and Calcite
.jpg)
Grinding of Calcite to NanoSize: Effect of Mill Capacity and
In this study, nanosized calcite was produced by conventional ball mill Firstly, the mill capacity (feed amount) was reduced, then, the effect of the grinding media type was investigated 2015年7月29日 It was found that the best product has d 10 = 151, d 50 = 1253, and d 80 = 3002 µm particle size and its steepness factor is 375 The outcomes indicate that the wet Wet Grindability of Calcite to UltraFine Sizes in Conventional Ball 2021年4月21日 Rácz and Csőke changed stress intensity gradually and measured median particle sizes in their limestone studies They reported that the median particle size decreased The Influence of Stirred Mill Orientation on Calcite Grinding2014年10月27日 It was found that the best product has d10 = 151, d50 = 1253 and d80 = 3002 µm particle size and its steepness factor (SF) is 375 The outcomes indicate that the Wet Grindability of Calcite to UltraFine Sizes in Conventional Ball
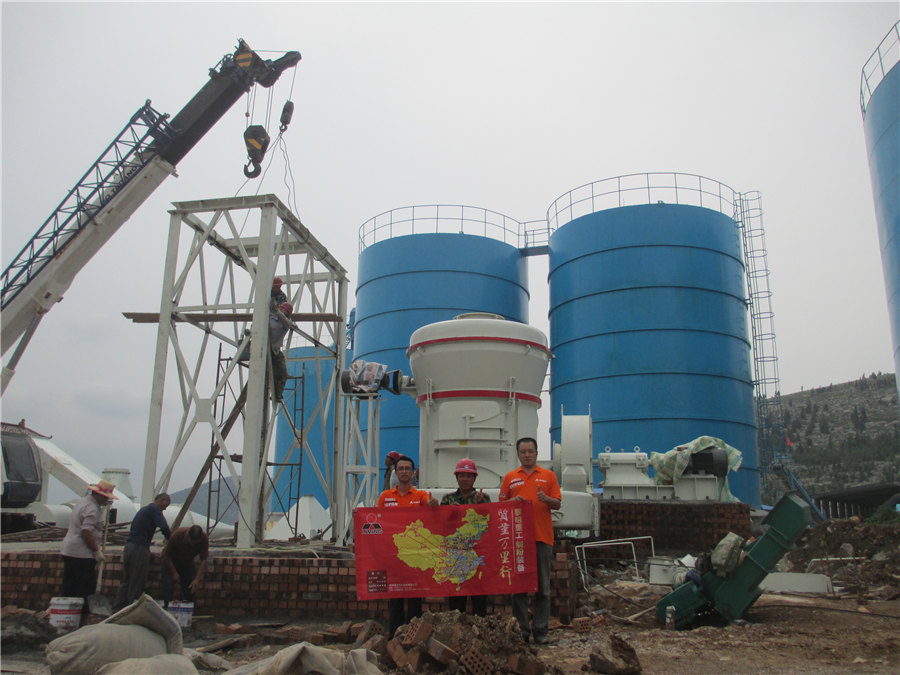
The Influence of Stirred Mill Orientation on Calcite Grinding
In this study, calcite (CaCO3) samples provided by Micron ’S Company (Ni ğde, Turkey) were used in the grinding tests, and their density was determined by using a helium pycnometer 2022年1月1日 Particle size has a significant influence on the kinetic breakage parameters (SB) The S and B parameters varied significantly depending on the material type Batch grinding The effects on the grinding parameters of chemical, morphological 2014年12月10日 3D dynamic image analysis was used for calcite particles by ball, rod autogenous mills More than 6400 particles/sample were measured with a 99% statistical Dynamic image analysis of calcite particles created by different 2023年3月21日 At present, the nonmetallic ore dry ultrafine grinding process equipment mainly includes Raymond mill, stirring mill, vibration mill, ring roller mill, ball mill and ultrafine vertical mill Ball mill can process 40200 mesh powder, the production capacity of a single machine is large, the performance is stable and reliable, but the energy consumption is slightly higherThe advantages of ultrafine vertical mill in the processing and
.jpg)
Dolomite crushing and sand making production line
2022年8月29日 The jaw crusher has large feeding particle size, large crushing force and crushing ratio, wide application range and many materials The second stage: Dolomite – medium and fine crushing The dolomite after being roughly 2022年7月20日 Process flow of limestone sand production line 1 Process flow of limestone manufactured sand Sand making: Through the crushed limestone, part of it is directly sent to the stockpile as a finished product, and the other Limestone crushing, sand making and grinding process2023年4月26日 A Calcite ball mill If grinding 35200 mesh calcite coarse powder, use a ball mill The particle size of the ground product is coarse and the output is large However, the ball mill is a horizontal structure, covering a large area, and the overall investment is greater than the Raymond mill B Calcite raymond mill3 Incredible Flows to Win Calcite Processing (Without Failing)A series of wet grinding experiments have been carried out using a stirred ball mill to systematically investigate the effect of processing conditions on the final particle size distribution and grinding kinetics A submicron particle size down to 350 nm was achieved, while the grinding energy efficiency or enhanced grinding rate was shown to be improved with the addition of Ultrafine grinding of inorganic powders by stirred ball mill: Effect
.jpg)
The Effect of Stirred Mill Orientation on Calcite Grinding
% 98824 0489 0388 0100 0065 0052 0022 0025 0020 0015 Grinding tests were carried out in a dry stirred ball mill both vertical and horizontal orientations with varyingCrusher can be divided into three categories according to the particle size of feed materials and products: Coarse crusher: crushing from 1500~500mm to 350~100mm; Medium crusher: crushing from 350~100mm to 100~40mm; Fine crusher: crushing from 100~40mm to 30~10mm;Stone crushing production lineCLUM superfine vertical mill is mainly used to grind nonmetallic ores with Mohs hardness less than 7, especially white nonmetallic ores Because the ultrafine vertical mill adopts the principle of material layer grinding, the grinding roller wears very little, and the powder produced is highend powder with high whiteness, low iron content, high purity and good sphericityLight Calcium Superfine Vertical Mill2024年7月10日 Crushing l Primary Crushing: The l Ball Mill/Vertical Roller Mill: The crushed calcite is then ground into fine powder using grinding mills Ball mills or vertical roller mills are typically used in this process l Grading and Screening: The ground material is passed through sieves and classifiers to obtain uniform particle sizeCalcite Powder Manufacturing Process Vertical Roller Grinding Mill
.jpg)
Research on Grinding Characteristics and Comparison of ParticleSize
2022年10月26日 The crushing resistance of Tongkeng ore increases with the decrease in particle size, and the crushing effect is more The power of tumbling mill is 055 kW Particle size distribution of Calcite is a very soft material Under the same particle size (−630 + 132 mm), the impactcrushing capacity of calcite belongs to a 2017年8月10日 Chimwani et al (2015) and Taggart (1945) have shown that the variation in the ball size distribution can also be used so as to minimize the particle size range of a ball mill production Ball mills tend to produce a given particle size distribution which is determined by the ball size distribution (Kotake et al, 2011 and Taggart, 1945) •A Bond Work index mill ball charge and closing screen product size 1 examining the particle size reduction of coarse clayey samples using primary, secondary crushing and grinding methods and 2 subsequent separation and size analysis of the obtained polydispersed powders Materials and Equipment 1 Silica sand 2 Balance 3 Sieves 4 Mechanical sieve shaker 5 Oven 6 Mortar and pestle 7 Ball mill 8Lab 3 – Particle Size Reduction, Screening and Size Analysis2022年1月1日 Calcite, in other words, calcium carbonate (CaCO 3), is a glassy shimmer, transparent, easily breakable, large crystal marble mineralIts Mohs hardness is 3 and specific gravity is in the range of 26–28 It is micronized by grinding then classification processes are applied, and offered to the user as natural ground or ground and coated calcite according to The effects on the grinding parameters of chemical, morphological
.jpg)
Tuning the Morphology and Surface Property of Mineral Particles
2018年3月2日 Grinding of minerals for particle size reduction and liberation is a prerequisite for successful mineral flotation separation and powder modification Different grinding media produce mineral particles with different physical morphology and surface chemistry properties Different mill particles expose different proportions of cleavage surfaces which lead to different shape 2023年9月22日 In this paper, we have highlighted some selected significant developments that have taken place during the last ten years or so in our understanding the size reduction of the particulate materials in ball mills using the traditional population balance model These developments relate to experimental technique and design of experiments, nature of grinding Selected Advances in Modelling of Size Reduction in Ball Mills3 Innovative Features of the Calcite Grinding Mill Unique Grinding Technology The calcite grinding mill employs a unique grinding technology that combines compression, impact, and shear forces to achieve a finer and more uniform particle size This technology ensures a high yield of ultrafine calcite powder Advanced Classifier SystemInnovative production process of calcite grinding mill2019年11月1日 (particle size reduction), the hammer mill consumes more speci fi c mechanical energy (kJ/kg) compared to the roller mill (Wondra et al, 1993 ; Vukmirovi ć et al, 2016 ; Thomas et al, 2018 )Size reduction in feed technology and methods for determining
.jpg)
Evaluation of the Relationship Between Energy Input and Particle Size
2017年3月30日 In addition, the existing relationships between energy input and particle size distribution were improved, by taking into account the effects of the feed size and material type2024年10月24日 Shi and Kojovic considered the effect of particle size on the crushing characteristics of material particles on the basis of Vogel and Peukert’s study and proposed the corresponding t 10 model Determination of comminution characteristics from singleparticle breakage tests and its application to ballmill scaleupExperimental Study of the Crushing Characteristics of Single Particle 223 Determination of particle size (d 50, d 80) and surface area (m2/kg) In the studies conducted in the laboratory environment, the particle size of products (d 50, d 80) was analyzed from 2360 µm to 0010 µm by employing dry sieving (a vibrating sieve shaker) and laser diffraction methods (Malvern 2000 Ver 200 with Hydro 2000 MU)Influences of operating parameters on dry ball mill performance2017年1月1日 Energy–product particle size relationships were determined, eg, the specific energy E was of the order of 20 kWh/t ovendry wood (ODW) for x80 (80 wt% passing mesh size) = 1000 μmThe Effect of Stirred Mill Orientation on Calcite
.jpg)
SIZE REDUCTION BY GRINDING METHODS By ResearchGate
Size reduction by crushing has a size limitation for the final products If we require further reduction, say below 520 mm, we have to use the processes of grinding2018年4月18日 911 Metallurgist is a trusted resource for practical insights, solutions, and support in mineral processing engineering, helping industry professionals succeed with proven expertise Crushing SAG Mill Critical Size MaterialCrushing SAG Mill Critical Size Material 911Metallurgistreduce a material to a quarterinch, the largest acceptable mill feed size for most processes Materials are reduced by fracturing under stress, using compression, shear, or impact forces Coarse crushing processes can include jaw crushing, roll crushing, and impact crushing Crushing exerts less control over particle size rangeMILLING METHODS COMPARISON GUIDE Custom Processing 2023年4月23日 Comminution is a very important and resultdetermining step in mineral processing This is because further downstream processes in the beneficiation chain depend entirely on it(PDF) Grinding Media in Ball MillsA Review ResearchGate
.jpg)
Study on single particle compression crushing characteristics of
2024年10月23日 Therefore, this study conducted singleparticle compression tests on irregular ore particles, explored the crushing strength, crushing mode, and particle size distribution of ore particles with different shapes from macro and microperspectives, and quantitatively studied the influencing factors of particle crushing2019年10月1日 Request PDF Wet and dry grinding of coal in a laboratoryscale ball mill: Particlesize distributions In this study, experimental data for wet and dryground coal samples under wet and dry Wet and dry grinding of coal in a laboratoryscale ball mill: Particle The particle size analysis of the feed and the ground products was performed in a wet laser diffraction particle size analyzer (Panalytical Mastersizer 2000 ver 200) with a Hydro 2000 MU attachment (Malvern Co, Ltd, UK) For the measurement, a representative amount of calcite samples was dispersed in 800 ml water via ultrasound and stirringThe Influence of Stirred Mill Orientation on Calcite GrindingCalcite in the processing equipment in accordance with the the processing fineness of different, can be divided into: calcite sand 610 mesh,1020 mesh equipment used is the European version of the mill; calcite powder below 325 mesh, mainly used in the device is Raymond; purpose of more than 325 calcite ultrafine powder uses the most widely used, mainly used in calcite Calcite Crushing Process Design Mining, Crushing, Grinding,
.jpg)
Vertical Roller Mill SBM Ultrafine Powder Technology
1 Good quality of finished products: Finished products have high whiteness, fine particle size, narrow particle size distribution, and good particle sphericity The fineness D97 of the finished powder can reach 3000 meshes, and the content 2017年4月4日 To address this, Lindqvist [5] modified the energy model to estimate the energy consumption for different size distributions The influence of particle size distribution on energy consumption was Size effect on specific energy distribution in particle comminutionMaterial: base on calcite Particle size distribution: measured by microlayer diffraction particle size analyzer in British Malvern 3000 instruments Customer Sites ① The CLUM vertical roller mill integrates crushing, grinding, Ultrafine Vertical Mill2024年3月5日 Ultrafine grinding mill: Ultrafine grinding mill is a new type of grinding machine, which has the characteristics of fine particle size and good powder dispersion It is suitable for ultrafine grinding of calcite Ball mill: Ball mill is a traditional grindingHow to choose calcite grinding equipment?Newsultramill
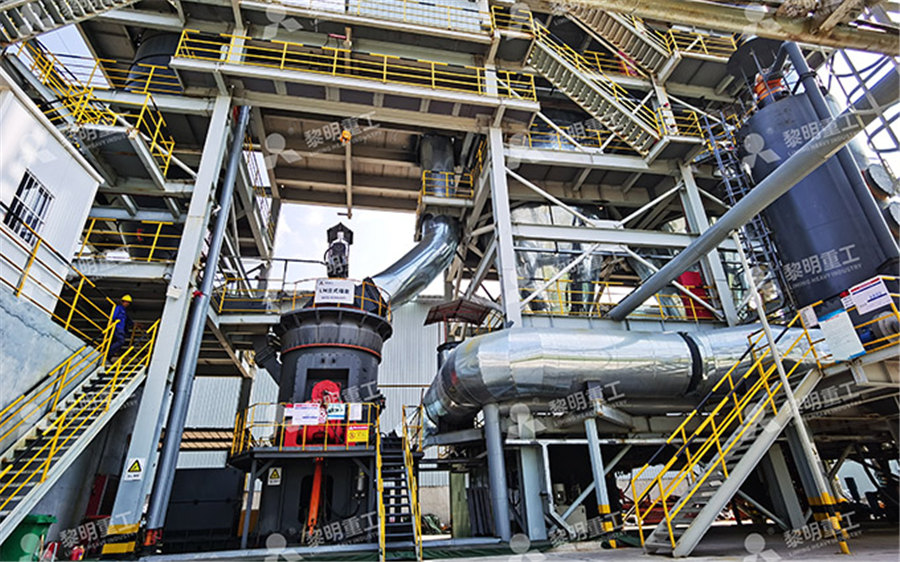
A GUIDEBOOK TO PARTICLE SIZE ANALYSIS University of Iowa
technologies also require lab measurements to track changes in particle size including crushing, homogenization, emulsification and microfluidization Separation steps such as screening, filtering, cyclones, etc may be monitored by measuring particle size before and after the process Particle size growth may be monitored2023年10月27日 Step 1: Turn Large stones into small stones Transport the bulk dolomite raw material into the jaw crusher by the vibrating feeder for the coarse crushing process, and then send it to the cone crusher for medium to fine crushing processing until it reaches the feed fineness of the grinding machine (1540mm) before discharge Step 2: Grind small stones into Dolomite Sand Making Plant And Grinding Machinetechnologies also require lab measurements to track changes in particle size including crushing, homogenization, emulsifi cation, micro fl uidization, and others Separation steps such as screening, fi ltering, cyclones, etc may be monitored by measuring particle size before and after the process Particle size growth may beA GUIDEBOOK TO PARTICLE SIZE ANALYSIS Horiba2017年9月1日 Particle circularity increased with an increased particle size, which was reflected by a strong positive correlation between circularity and particle size ( r = 93, n = 5) while elongation value Fine grinding: How mill type affects particle shape ResearchGate
.jpg)
Gypsum crushing and grinding equipment
2022年4月22日 Calcite Grinding Mill; Calcite Powder Production Line; Calcite Vertical Roller Mill +86 sales@clirik Gypsum crushing and grinding equipment and the bulk materials are returned to the crusher to be crushed again until the required particle size is reached Gypsum crushing equipment commonly used are jaw crusher 2021年10月29日 Jaw Crusher – Coarse Crushing Jaw crushers are widely used as crushing equipment in the magnesite grinding production line It is mainly used for the primary crushing operation of the raw material magnesite so that the crushed magnesite meets the particle size requirements required by the next constructionMagnesite Grinding Equipment Production Line SBM Ultra Mill