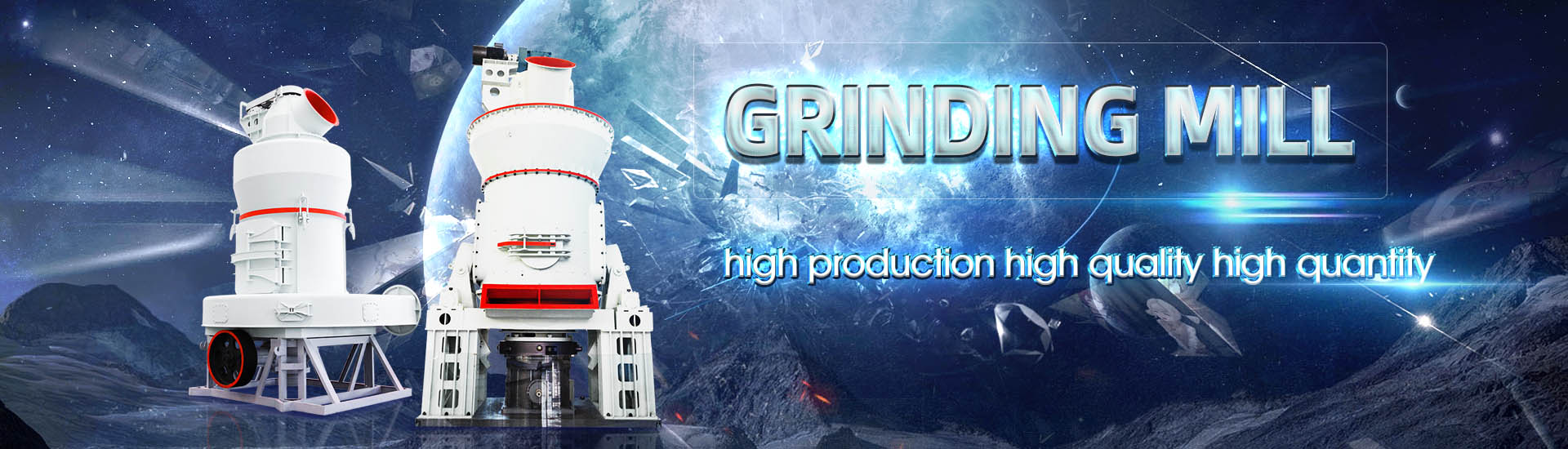
Ore mill flywheel size
.jpg)
Flywheel Design Sizing Calculation Tutorial with Example
The material of flywheel on most applications will be either cast iron or cast steel The Density of the materials (d) is as follows Cast iron – 7250 kg/m3 Cast steel – 7800 kg/m3 展开This thesis guides the path through flywheel design, and analysis the material selection process The FEA model is described to achieve a better understanding of the mesh type, mesh size ANALYSIS AND OPTIMIZATION OF FLYWHEEL IJMERR2014年11月16日 Flywheel design and sizing calculation principles, formulae and practical example with step by step numerical solution is explained here which is useful for sizing IC engine, sheet metal press, compressors and other Flywheel Design and Sizing Calculation Example2015年6月19日 Use this online calculators for Motor Sizing and Mill sizing as well as mill capacity determinators In extracting from Nordberg Process Machinery Reference Manual I will also provide 2 Ball Mill Sizing (Design) Ball Mill Design/Power Calculation 911Metallurgist
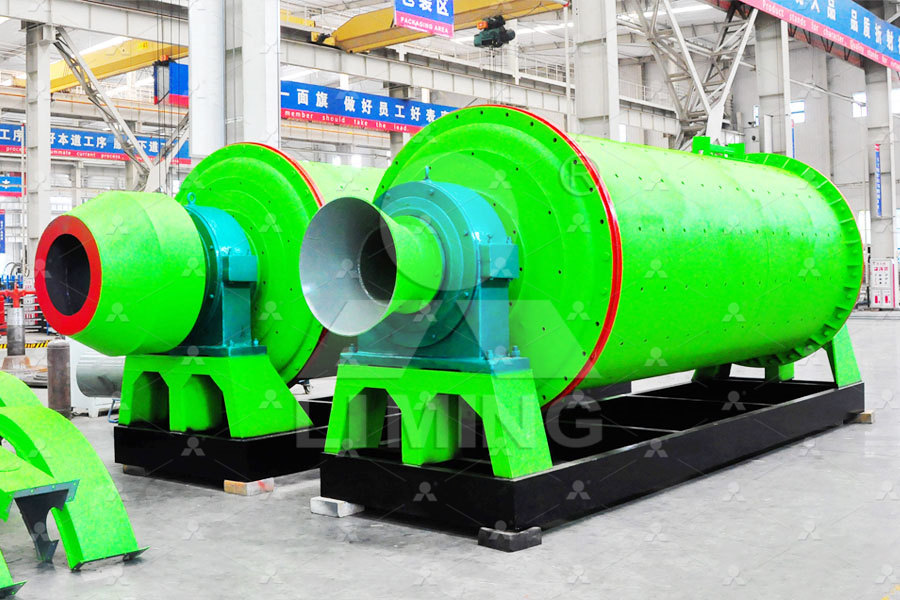
AMIT 135: Lesson 7 Ball Mills Circuits
Three types of mill design are common The Overflow Discharge mill is best suited for fine grinding to 75 – 106 microns The Diaphram or Grate Discharge mill keeps coarse particles within the mill for additional grinding and typically 2016年1月1日 The size of a jaw crusher is usually described by the gape and the width, expressed as gape × width The common crusher types, sizes and their performance are Jaw Crusher ScienceDirect2016年6月20日 Stratification takes place within zone 1, screening of fine undersize particles (75% of the size of the screen apertures) takes place within zone 2 and screening of “critical” undersize particles, ie particles of a size Ore, Rock Aggregate Screening (Complete Guide)January 2007, two complete grinding circuit surveys were performed followed by a SAG mill crash stop and grindout After stopping the mill, a SAG mill feed sample was also collected from Conveyor parison of SAG mill feed size throughputs
.jpg)
Monitoring ore loss and dilution for minetomill
2016年2月1日 The purpose of this study is to understand how ore loss and dilution affect the mine call factor, with the aim of subsequently improving the quality of ore mined and fed to the millIn contrast, gangue (waste material) was mostly bigger than tennis ball size, hence the ore and waste were broken unequally The substantial rock breakage was further exacerbated by the increase in panel length, gully length, scraper routes, a dilution rate of 88% would mean that R176 is spent on processing waste as ore in the millMonitoring ore loss and dilution for minetomill integration in 2016年6月3日 Talc from 9 microns average to 19 microns average particle size Silica from 37 microns average to 17 microns average particle size Barite from 28 microns average to 155 microns average particle size Limestone from minus 74 microns to 31 microns average particle size Limestone from minus 4000 microns to 24 microns average particle sizeTower Mill Operating Work Index 911Metallurgist2018年4月8日 Referring to Table VI the L/D can be between 175 and 20 or even greater Referring to Table VII a 305 meter (10 foot) by 305 meter (10 foot) overflow ball mill with a 40 percent by mill volume ball charge, new liners and 50 mm (2″) balls draws 491 HP Using equation 5 there will be a loss of 055 Kw (074 Hp) per metric tonnes of ballsHow to Size Design a Regrind Ball Mill 911Metallurgist
.jpg)
Estimation of Grinding Time for Desired Particle Size Distribution
2020年1月3日 Iron ores obtained from different sources differ in their chemical and physical properties These variations make the process of grinding a difficult task The work carried out in this context focuses on three different samples of iron ore, viz, high silica high alumina, low silica high alumina, and low silica low alumina The grinding process for all the three iron ores is This helps in smooth working and efficient rolling mill operations Skip to content rmttools@gmail gagan@rmttools +918054971006 001(647)575 2783 Flywheel CI or MS Steel casted Flywheels of varying size and weight ranging upto 30 MT Flywheel is a rotating mechanical device that is used to store rotational energyFlywheel is Buy Rolling Mill Flywheel RMT Tools2016年1月1日 The size of a jaw crusher is usually described by the gape and the width, expressed as gape × width The common crusher types, sizes and their performance are summarised in Table 41Currently, the dimensions of the largest Blaketype jaw crusher in use are 1600 mm × 2514 mm with motor ratings of 250–300 kWJaw Crusher ScienceDirect2017年3月20日 An effect of a grinding method, that is ball mill and high pressure grinding rolls (HPGR), on the particle size, specific surface area and particle shape of an iron ore concentrate was studiedPhysicochemical Problems of Mineral Processing
.jpg)
Flywheel energy storage Wikipedia
NASA G2 flywheel Flywheel energy storage (FES) works by accelerating a rotor to a very high speed and maintaining the energy in the system as rotational energyWhen energy is extracted from the system, the flywheel's rotational Estimation of Grinding Time for Desired Particle Size Distribution and for Hematite Liberation Based on Ore Retention Time in the Mill × Characterization studies 1 Introduction Ball mills are progressively used to grind the ores for particle size reduction and to liberate valuable minerals from the ores(PDF) Estimation of Grinding Time for Desired Particle Size 2015年6月19日 The basic parameters used in ball mill design (power calculations), rod mill or any tumbling mill sizing are; material to be ground, characteristics, Bond Work Index, bulk density, specific density, desired mill tonnage capacity DTPH, operating % solids or pulp density, feed size as F80 and maximum ‘chunk size’, product size as P80 and maximum and finally the type of Ball Mill Design/Power Calculation 911MetallurgistInvestigation on the particle size and shape of iron ore pellet feed using ball mill and HPGR 909 areas of 500–1600 cm2 g1The concentrate must therefore be reground in order toInvestigation on the particle size and shape of iron ore pellet feed
.jpg)
I203 I204 INTRODUCTION SMC Testing
Top size (mm) Mill Weight Power Top Size Figure 4: Feed Top Size vs SAG Mill Performance 5000 5500 6000 6500 7000 7500 8000 8500 9000 9500 10000 13:00 14:00 15:00 16:00 17:00 kW 00 500 1000 1500 2000 2500 3000 3500 4000 Top size (mm) Top Size Power Mill Weight Figure 5: Feed Top Size vs AG Mill Performance2016年6月6日 Such a circuit can counteract the effects of harder ore coarser ore decrease the size of SAG mill required, or rectify poor throughput due to an undersized SAG circuit Notably, harder ore often presents itself to the SAG circuit as coarser than softer ore—less comminution is produced in blasting and primary crushing, SAG Mill Grinding Circuit Design 911Metallurgist2020年10月20日 One of the feed ore properties which can affect the grinding charge of an AG mill is particle size distribution Bergstedt and Fagremo (1977) studied the effect of feed size distribution on the performance of an AG during a series of pilot plant tests They reported that the ideal feed ore to an AG mill should have 10–15 wt% materials coarser than 100 mm Bouajila The performance improvement of a fullscale autogenous mill by setting 2021年5月6日 Thus at each revolution of the flywheel the movable jaw crushes any lump of ore once against the stationary jaw (212) allowing it to fall as it swings back on the return halfstroke until eventually the pieces have been broken small enough to drop out It follows that the size to which the ore is crushedJaw Crusher Working Principle 911Metallurgist
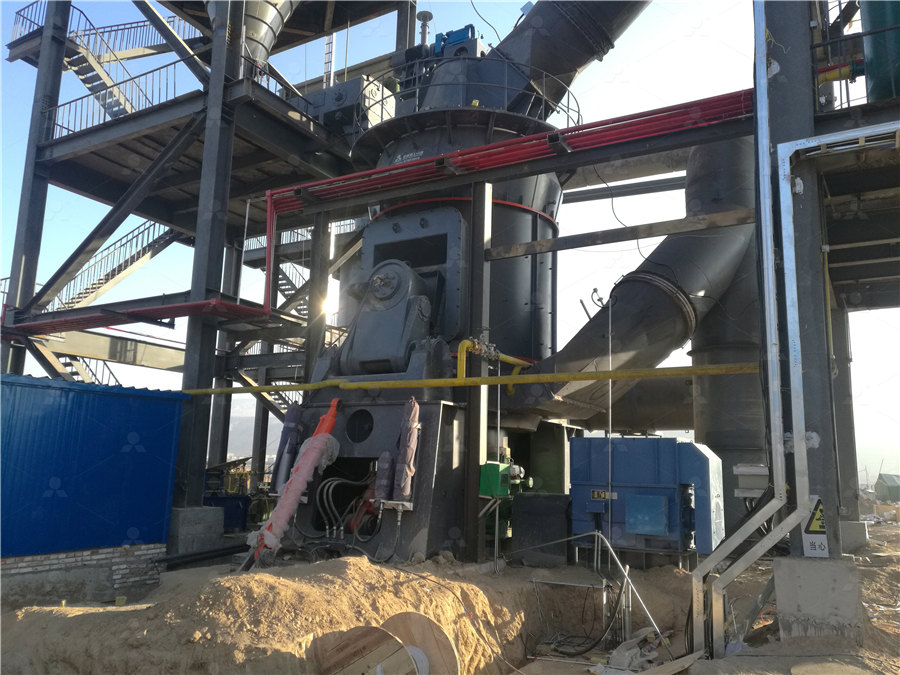
Effect of ball and feed particle size distribution on the milling
Effect of ball and feed particle size distribution on the milling efficiency of a ball mill: An attainable region approach N Hlabangana a, G Danha b, *, E Muzenda b a Department of Chemical Engineering, National University of Science and Technology, P O Box AC 939, Ascot Bulawayo, Zimbabwe b Department of Chemical, Materials and Metallurgical Engineering, College of Estimation of Grinding Time for Desired Particle Size Distribution and for Hematite Liberation Based on Ore Retention Time in the Mill Harish Hanumanthappa1 Harsha Vardhan1 Govinda Raj Mandela1 Marutiram Kaza2 Rameshwar Sah2 Bharath Kumar Shanmugam1 Received: 27 August 2019 /Accepted: 16 December 2019Estimation of Grinding Time for Desired Particle Size Distribution2021年1月22日 To evaluate the net energy consumption of the stirred mill, the specific energy input [26,27] E m (kWh /t) was calculated as follows: E m = ∫ P t − P 0 dt m Where P(t) is the mean power of the stirred mill at each sampling time, kW; P 0 is the mean power of the stirred mill under no load (no water, grinding media and material), kW; t is grinding time,Impact of ball filling rate and stirrer tip speed on milling iron ore 4 10 100 10 100 1000 10000 size (microns) % passing closed circuit SAG cyc o/f closed circuit Ball cyc o/f Figure 2 – Example of a Closed Circuit SAG Mill Cyclone Overflow and a Ball Mill THE APPROPRIATENESS OF THE TRANSFER SIZE IN AG AND SAG MILL
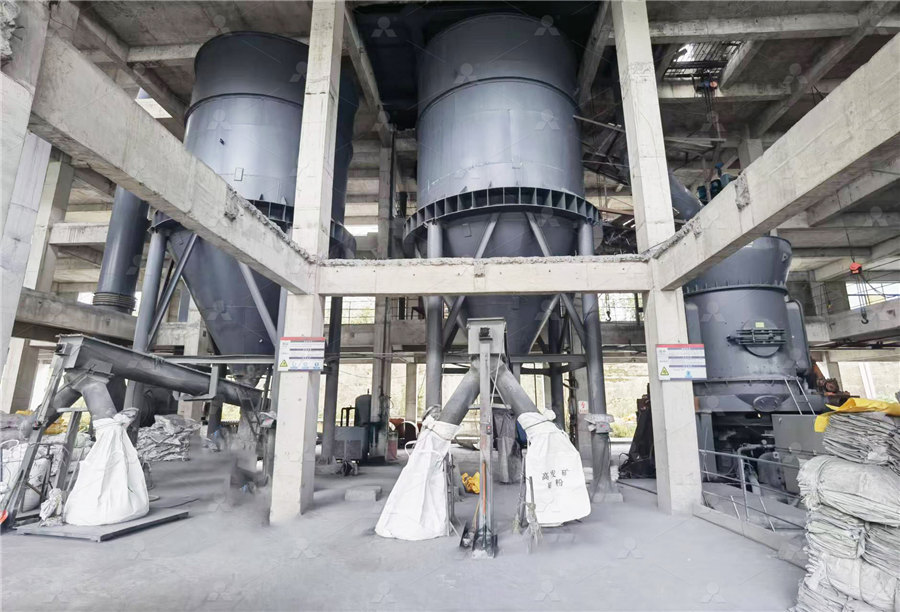
Why use Different Size Balls in a Mill 911Metallurgist
2017年7月3日 If it is desired to find the effect of balls grinding 20mesh ore and the mill is loaded with 20mesh material, the grinding time should be infinitely short, because fine particles are made as soon as the mill starts and if the run continues the test is of the comminuted products of the 20mesh sample rather than that which was supplied for the test2001年1月1日 The efficiency of the mill to break ore is a function of both the feed size distribution and the relative hardness of the ore When the feed size of a SAG mill becomes coarser, ie α r increases Influence of feed size on AG / SAG mill performance2023年10月17日 Type of Ore powder grinding mil 1 Raymond mill Raymond mill feed particle size ≤30mm, production capacity 8176 tons/day, production fineness 80325 mesh, the main transmission device adopts sealed gearbox and pulley, and other Compared with the ore grinding mill, the screening rate is higher, and the screening rate is as high as 99%How to choose a suitable ore powder grinding mill?2020年5月28日 The feed samples of X, Y, and Z iron ores were ground in the BBM (ball mill refers to a BBM of size 300 mm × 300 mm with smooth liners) to identify the PSD, BWI, and RT of each ore Grinding experiments were conducted according to Bond’s standard test procedure []For each iron ore sample, the RT taken to produce 250% circulating load in the BBM was Investigation on Iron Ore Grinding based on Particle Size Distribution
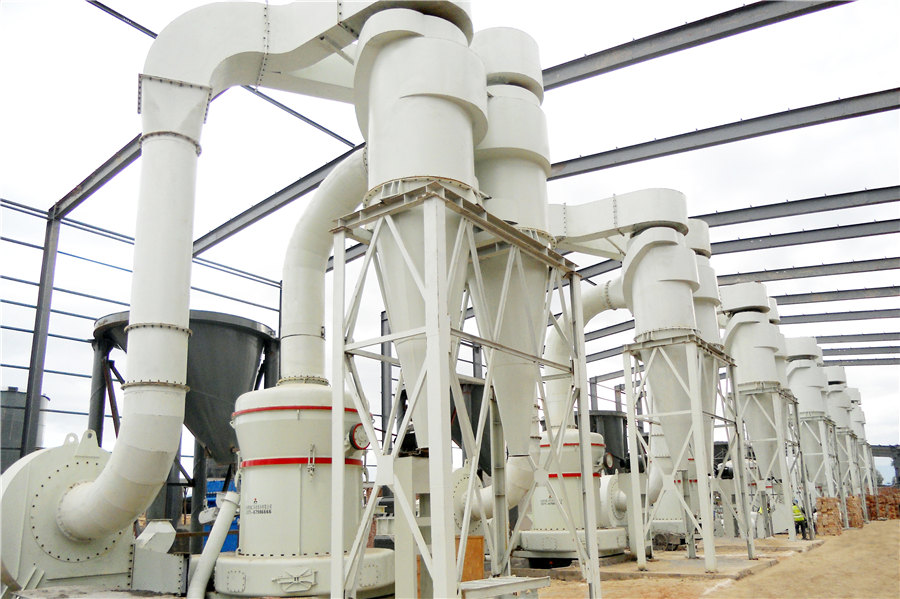
SAG Mill Testing Test Procedures to Characterize Ore Grindability
size reduction in a comminution device Because grinding theories are imperfect and ore hardness can vary with size, grindability tests are designed to best represent the size reduction of the industrial equipment analysed For that reason, it is preferable to design a primary ball mill from a rod mill work index rather than a ball mill2019年8月29日 Mill tailings stream s with a particle size of the solids of around 100 based ore sorting The particle size distribution an d the resulting benefits can generally be controlled(PDF) Sensor‐Based Ore Sorting Technology in Mining—Past, 2023年12月12日 Optimum distribution of ores according to the size of the mill, increasing the efficiency of the grinding process and reducing energy consumption are achieved In addition, (PDF) Control of ball mill operation depending on ball load and ore 2022年5月25日 Flywheel Fund is a oneyear, membermanaged capital fund, run by The Mill, total fund size Flywheel Fund c/o The Mill 642 N Madison St Bloomington, IN 47404 Make An Appt PItch US JOIN our list Home — Flywheel Fund
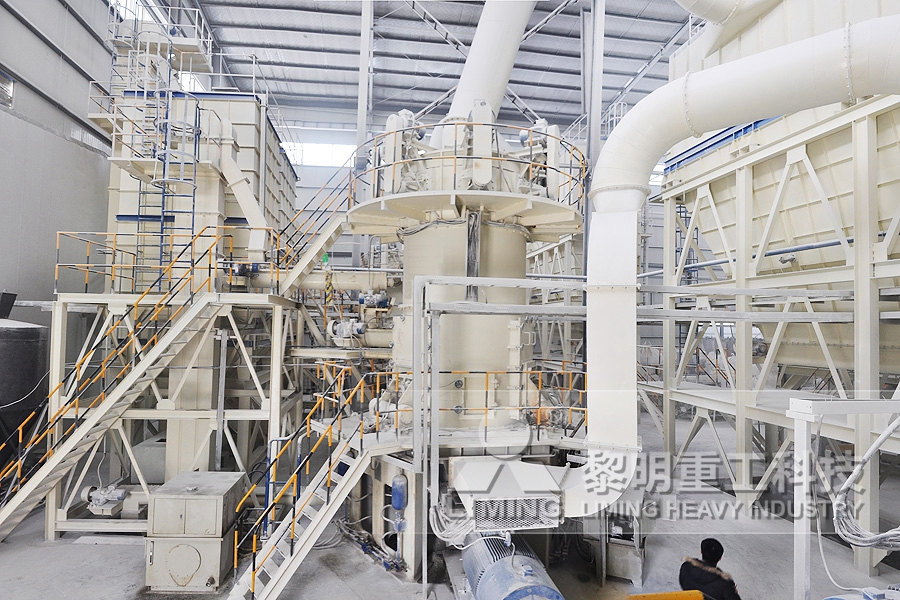
What Are Jaw Crushers and How Do They Work?
The size of a jaw crusher is measured by the top opening of the crushing chamber For example, a 48” x 42” jaw crusher measures 48” from one crushing jaw to another and is 42” across the width of the two crushers The primary The rod mill is another type of grinding mill used in the copper ore mining process This machine uses steel rods as the grinding media instead of balls, which are commonly used in ball mills The rods grind the ore by tumbling Understanding the SAG Mill in Copper Ore Mining 2016年3月11日 It is not just the crushing of the ore but the extraction of the mill feed size that makes the circuit complete A sufficient quantity of vibrating screens and full utilization of the total area they provide is an important factor in economically producing the mill feed size and tonnage established for the plantCrushing Plant Flowsheet DesignLayout 911Metallurgist2015年4月15日 For each ball mill grinding step, a Bond ball mill grindability test for Work Index at one mesh size coarser than the desired 80% passing size and at the mesh size of or just finer than the 80% passing size If 50 mm x 75 mm (2″ x 3″) ore lumps are available an impact crushing Work Index testWhat Ore Testing is Required For Mill Selection
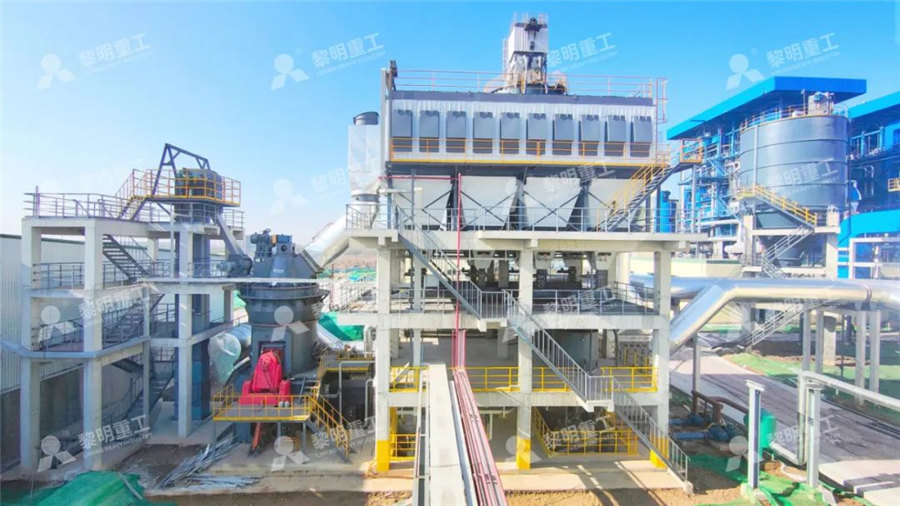
Understanding fine ore breakage in a laboratory scale ball mill using
2011年2月1日 Request PDF Understanding fine ore breakage in a laboratory scale ball mill using DEM DEM models of fine grinding in ball and stirred mills have to date almost entirely focused on the motion 2015年7月29日 The coarser ore being drier and having more space in between each piece than is normal, will not slow the flow of fine material towards the discharge points as much This means that when the crushers stop putting ore into the fine ore storage the size ratio of the mill feed will decrease rapidlyOre Feed Size * Work Index Hardness: Crushing Mill Tonnage2016年3月21日 where R represents the ratio: % Pb in crude ore/% Cu in crude ore Formula (32) is very convenient for milling calculations on ores of this type Example: An ore contains 5% lead and 1% copper The ratio of perfect concentration for a concentrate of maximum grade and 100% recoveries of lead and copper would be:Common Basic Formulas for Mineral Processing CalculationsThe driving flywheel has a diameter of 25 meters and is motor driven through six vbelts In some industries, for example, iron ore or coal, where a specific product size is required (iron ore –30 + 6 mm), a careful choice of jaw settings and screen sizes is required to produce the minimum amount of fines Mill Type Media Size (mm)Primary Crusher an overview ScienceDirect Topics
.jpg)
Flywheel Design and Sizing Calculation Example mechGuru
2014年11月16日 Secondly, calculate the geometry/dimensions of the flywheel based on the calculated mass moment of inertia and material properties This will be covered in another article Design steps and formulas Step1: Coefficient of fluctuation calculation Input required: Maximum minimum speed Flywheel inertia/size depends upon the fluctuations in speed