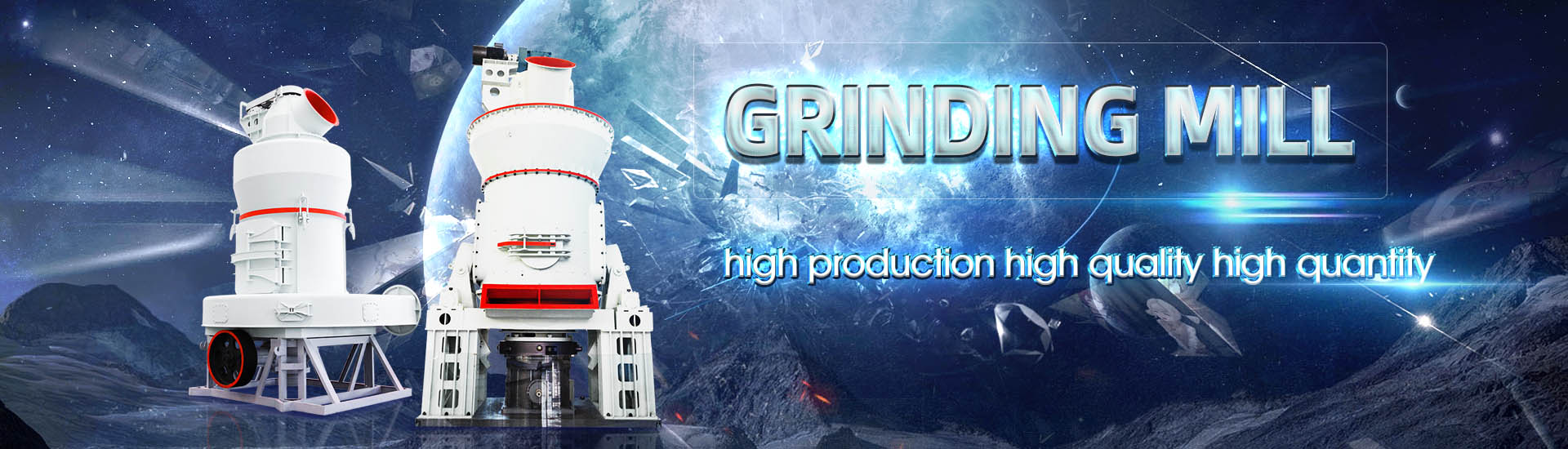
Ball mill consumption
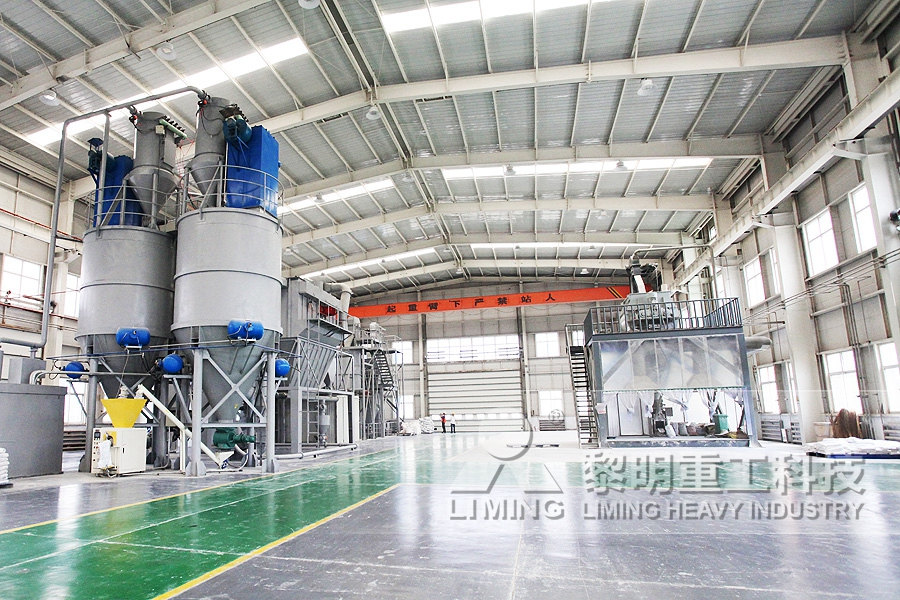
Ball Mill Design/Power Calculation 911Metallurgist
2015年6月19日 Use this online calculators for Motor Sizing and Mill sizing as well as mill capacity determinators In extracting from Nordberg Process Machinery Reference Manual I will also provide 2 Ball Mill Sizing (Design) 2001年8月1日 Typical power consumption for a 5m diameter by 7mlong ball mill is between 25 and 35 MW The actual proportion of this energy usefully used in size reduction is thought Charge behaviour and power consumption in ball mills: sensitivity 2020年2月26日 Measurement results of two ball mills in a real ceramic manufacturing plant showed that the proposed calculation models could achieve an accuracy of more than 96% for Calculation method and its application for energy consumption of 2020年11月16日 The cornerstone of the mathematical treatment presented is the relationship between mill capacity and speed as expressed in Eq 5 The Sullivan rod mill with its fluid drive Ball Mill Capacity and Power Consumption Relationship to Mill
.jpg)
BALL MILLS Ball mill optimisation Holzinger Consulting
the ball mill had an average production rate of 190tph with a specific electrical energy consumption of 355kWh/t Its operational issues included: • oversized limestone • wornout 2020年2月26日 Measurement results of two ball mills in a real ceramic manufacturing plant showed that the proposed calculation models could achieve an accuracy of more than 96% for Calculation method and its application for energy consumption of 2022年3月15日 Various operational parameters, such as mill speed, the ball charge composition, charge filling, lifter type, and lifter number, significantly impact ball milling grinding efficiency [3](PDF) Power consumption management and simulation 2001年8月1日 Typical power consumption for a 5m diameter by 7mlong ball mill is between 25 and 35 MW The actual proportion of this energy usefully used in size reduction is thought Charge behaviour and power consumption in ball mills: sensitivity
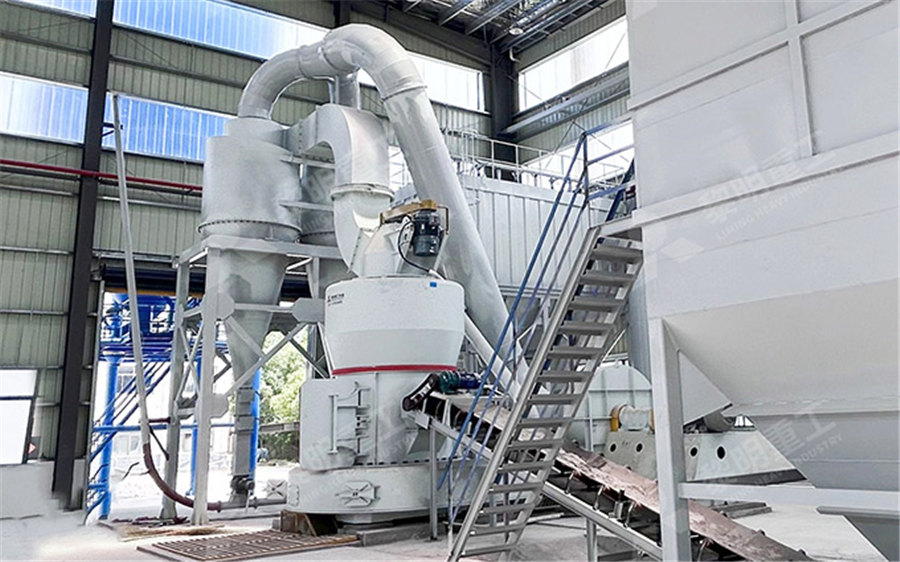
Charge behaviour and power consumption in ball mills: Sensitivity
2001年8月1日 Discrete element method (DEM) modelling has been used to systematically study the effects of changes in mill operating parameters and particle properties on the charge The amount of comminution or fineness of minerals in a mill can be described by various parameters, the most important of which is d 80 (80% passing size) The purpose of this Power consumption management and simulation of optimized 2020年2月26日 Owing to the lack of effective energy consumption models of ball mills in the ceramic industry, a calculation model to forecast energy consumption of ceramic ball mills during the grinding process Calculation method and its application for energy consumption of ball 2015年4月24日 2 Ball mill consist of a hollow cylindrical shell rotating about its axis Axis of the shell horizontal or at small angle to the horizontal It is partially filled with balls made up of Steel,Stainless steel or rubber Inner surface of the Ball mill PPT Free Download SlideShare
.jpg)
Grinding Media in Ball Mills for Mineral Processing
2023年11月24日 The grinding efficiency of a ball mill is determined by the product size distribution, energy consumption, and the grinding costs According to Hassanzadeh [ 6 ] , about 37% of the costs are used for grinding media only,13% for liners, and about 50% is used for energy in an industrial ball mill2001年8月1日 This paper is the second installment of an ongoing numerical study of ball mills The first installment (Cleary, 1998a) described the basic modelling of a 5m ball mill Predictions of charge profile, charge segregation, power draw, torque, liner wear and collisional force distributions were made for a range of mill conditionsCharge behaviour and power consumption in ball mills: 2013年8月3日 In Grinding, selecting (calculate) the correct or optimum ball size that allows for the best and optimum/ideal or target grind size to be achieved by your ball mill is an important thing for a Mineral Processing Engineer AKA Metallurgist to do Often, the ball used in ball mills is oversize “just in case” Well, this safety factor can cost you much in recovery and/or mill liner Calculate and Select Ball Mill Ball Size for Optimum Grinding2017年4月22日 Ball Mill Liner Consumption Average consumption of shell liners, for both chrome and manganese steel, is 1/3lb per ton of ore crushed The consumption of lining seems to be fairly constant regardless of the hardness of the ore, fineness of product, or other conditionsBall Milling 911Metallurgist
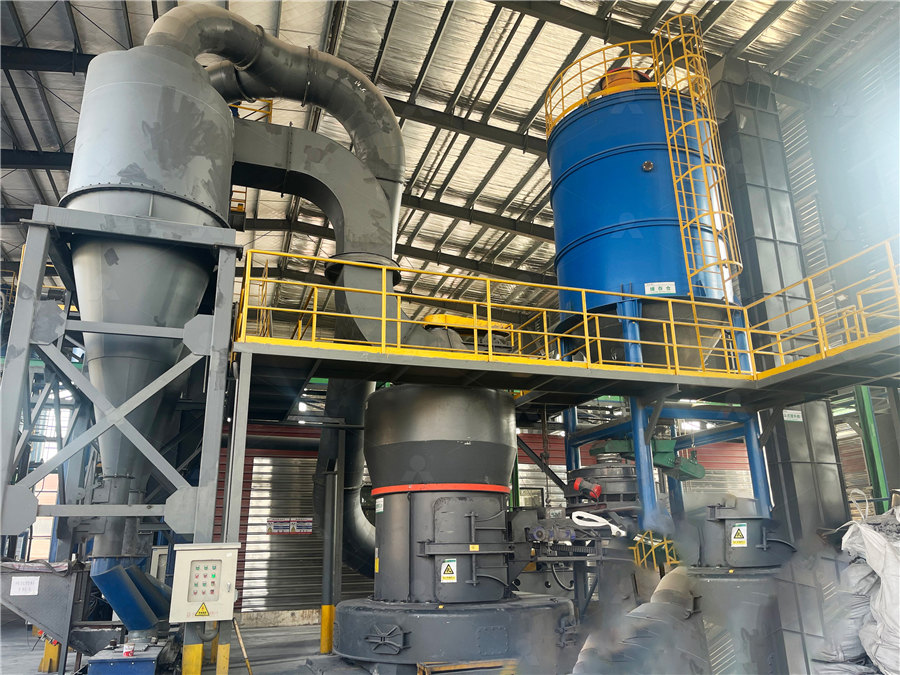
Ball Mill Capacity and Power Consumption Relationship to Mill
2020年11月16日 where v = peripheral speed of the mill in feet per minute If the observed capacity of a mill at speed n1 is = T1 tph, the capacity T2 of the same mill at speed n2 should be The acceleration factor of the ball or rod mass is a function of the peripheral speed of the mill Thus P = f4(F) = f1(D²)f5(υ) Indicating that υ = πDn, andThe characteristic tumbling motion of these mills has given them the name ‘tumbling mills’, which include the ball mill, tube mill and rod mill Ball mills are horizontal rotating cylindrical or conical steel chambers, approximately one third to half full of steel, alloy steel or iron balls, like that shown in Fig 410 A–C , or flint stonesBall Mill an overview ScienceDirect TopicsBall mills are furthermore characterized by significant differences in the sizes of available grinding jars Retsch offers mills with jar capacities from 15 ml up to 150 l and balls are available from 01 mm to 40 mm, see Figure 2 A third and very important characteristic of a ball mill, Ball Mills Suitable for every application RetschBall mills are widely used in the mining and mineral processing industry for the efficient comminution of ores and minerals The ball size distribution in ball mills plays a crucial role in the grinding process, affecting the energy consumption, capacity, and efficiency of the mill 1Ball size distribution in ball mills: Optimization and impact on
.jpg)
ball mill calculations, grinding media filling degree, ball size, mill
online live calculators for grinding calculations, Ball mill, tube mill, critical speed, Degree of filling balls, Arm of gravity, mill net and gross power2020年7月24日 The energy consumption of grinding is the subject of many studies, especially in the case of ball mills for grinding clinkers [8, 9], fuels [10], iron ore [11], hematite ore [12], sulfide ore [13 Determination of granulometrical composition of 2011年1月1日 The digital energy meter was previously tested and evaluated in Bond ball mill Work Index testing where direct measured comminution energy of ores processed in the Bond ball mill were compared Measurement of electrical energy consumption in a Int J Miner Process 63 Ž2001 79–114 elsevierrlocaterijminpro Charge behaviour and power consumption in ball mills: sensitivity to mill operating conditions, liner geometry and charge composition Paul W Cleary ) CSIRO DiÕision of Mathematical and Information Sciences, PriÕate Bag 10, Clayton South MDC, Clayton, Victoria, 3169, Australia Received 21 January 2000; Charge behaviour and power consumption in ball mills:
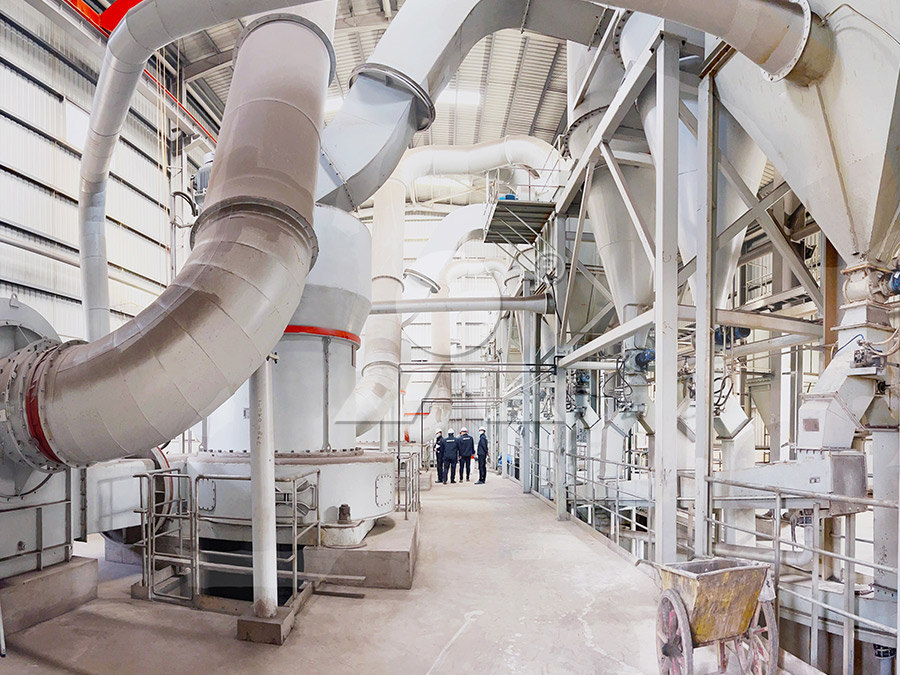
A POWER BASED APPROACH FOR THE SELECTION AND COMPARISON OF BALL MILL
Ball mill energy consumption can be improved by changing its rotational speed when grinding efficiency decreases or by modifying the mill liner shape in a way that ball trajectory can be maintained within an optimum range for the longest period 2017年1月1日 The power consumption of the ball mill was monitored for two months, and the data is shown in the histogram in Figure 2c It can be seen that the power consumption for each(PDF) Performance optimization of an industrial ball mill for consumption W c of the ball mill amounts to 109091 kW h/t Further, applying the Bond correction coefficient, the corresponding grinding power consumption W i for the 244 m overflow ball mill is 159135 kW h/t q 0 ¼ P m W c ð4Þ At any other target granularity, the grinding power consumption W HY can be estimated by employing Eq 5, where tExploring the Link between HY Wet Ball Mill Work Index and Vertical roller mills and ball mills represent two clearly distinct technologies However, with proper adjustments to the operational parameters of the vertical roller mill almost identical cement properties can be achieved by the two mills that satisfy the cement user’s demandsNevertheless, the two types of mills have their distinctive meritsCement grinding Vertical roller mills VS ball mills
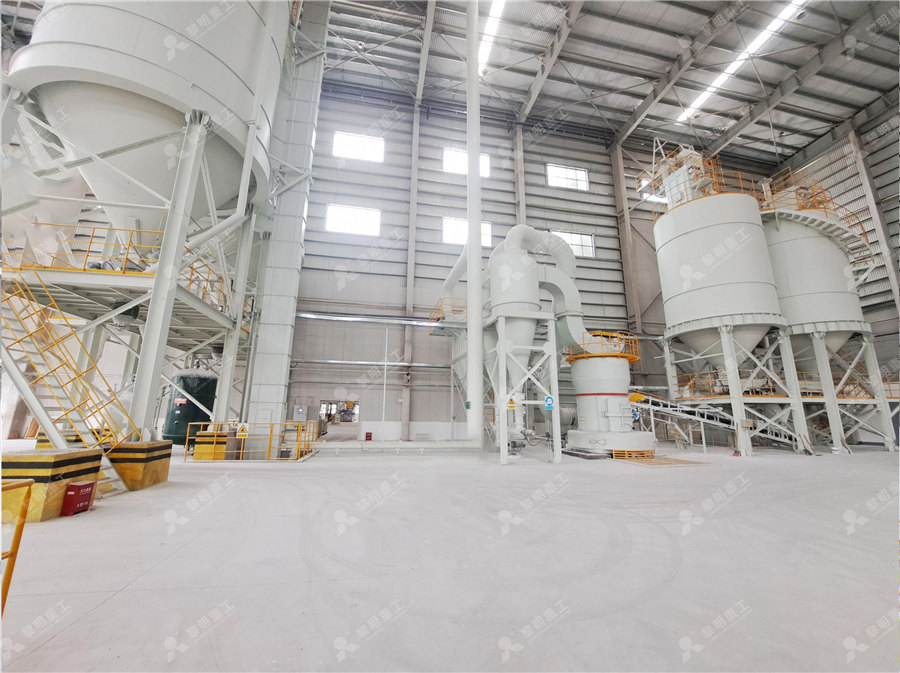
Energy efficiency Glencore Technology
The use of tower mills as an energy efficient alternative to secondary and regrind ball milling became a common inclusion in the latter part of the previous century Traditionally, the higher energy efficiency was attributed to the difference between attrition grinding in tower mills and impact grinding in ball milling2021年2月26日 Milling is among the most energyconsuming technological stages of copper ore processing It is performed in mills, which are machines of high rotational masses The start of a mill filled to capacity requires appropriate solutions that mitigate the overloading One method for increasing the energy efficiency of ball mills is to optimize their drive systems This article Energy Efficiency Analysis of Copper Ore Ball Mill Drive 2017年7月26日 Even though the rod mill could be a relatively inefficient device for both energy and metal consumption, as was evidenced by Bond, it still made the overall circuit energy consumption more efficient Under the right operating conditions, high power rate crushing can bring mill feed size down to near 80% passing 7,000 microns and finer, which can be handled How Ball Mill Ore Feed Size Affects Tonnage CapacityA ball mill is a type of grinder filled with grinding balls, used to grind or blend materials for use in mineral dressing processes, paints, pyrotechnics, ceramics, and selective laser sintering It works on the principle of impact and attrition: Ball mill Wikipedia
.jpg)
Determining cement ball mill dosage by artificial intelligence tools
2013年12月1日 Determining cement ball mill dosage by artificial intelligence tools aimed at reducing energy consumption and environmental impact December 2013 Ingenieria e Investigación 33(3):49年1月11日 In this way, the ball mill efficiency is improved with an appropriate crushing and energy consumption Ball mills of different length and diameter The theoretical ratio of length to diameter is between 109 and 15 While according to different requirements, 5 Ways to Improve the Ball Mill Efficiency FTM2001年8月1日 Request PDF Charge behaviour and power consumption in ball mills: Sensitivity to mill operating conditions, liner geometry and charge composition Discrete element method (DEM) modelling has Charge behaviour and power consumption in ball mills: For overflow ball mills, the charge should not exceed 45% of the mill volume For grate discharge mills, the charge should occupy about 50% of the mill volume Bond developed a relationship that can be used to determine the percent charge by volume as a function of the vertical height above the charge, He, and the radius of the mill, R, ie,AMIT 135: Lesson 7 Ball Mills Circuits – Mining Mill Operator
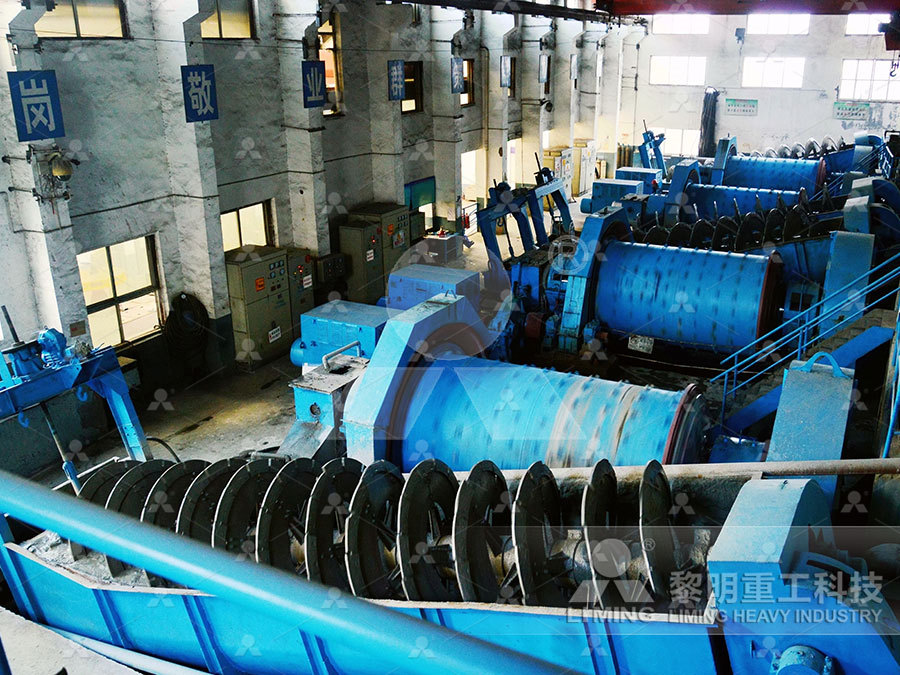
Optimization and Prediction of Specific Energy Consumption in Ball
2022年1月12日 In addition, a regression model was developed to predict specific energy consumption in ballend milling of Ti6Al4V alloy under MQL and cryogenic machining conditions 2 Experimental Setup and Material The cutting tool used in experiments was a ballend mill with diameter of 10 mm and two cutting edges—DORMER S5012013年9月8日 SAG Ball consumption is “average” at 400 g/t while Ball Mill grinding media (3″ balls) usage in 550 g/t Yet, you add steel and nothing seems to happen, tonnage is not noticeably improved You need more tonnage and could actually use a larger/coarser transfer size from the SAG to Ball MillSAG Mill Ball Size Evaluator Evaluation Factors Calculate 2002年11月1日 A ball mill employs steel balls to generate a grinding action, such as lower efficiency, higher steel ball consumption, and severe lining degradation (Cleary, 2001)The energy efficiency of ball milling in comminution2024年8月8日 Unlock the secrets to ball mill efficiency with our comprehensive guide on choosing the right grinding media Learn how material composition, size, shape, Their lightweight nature also contributes to reduced energy consumption during milling Steel Balls: Predominantly made from carbon steel, stainless steel, Ball Mill Success: A StepbyStep Guide to Choosing the Right
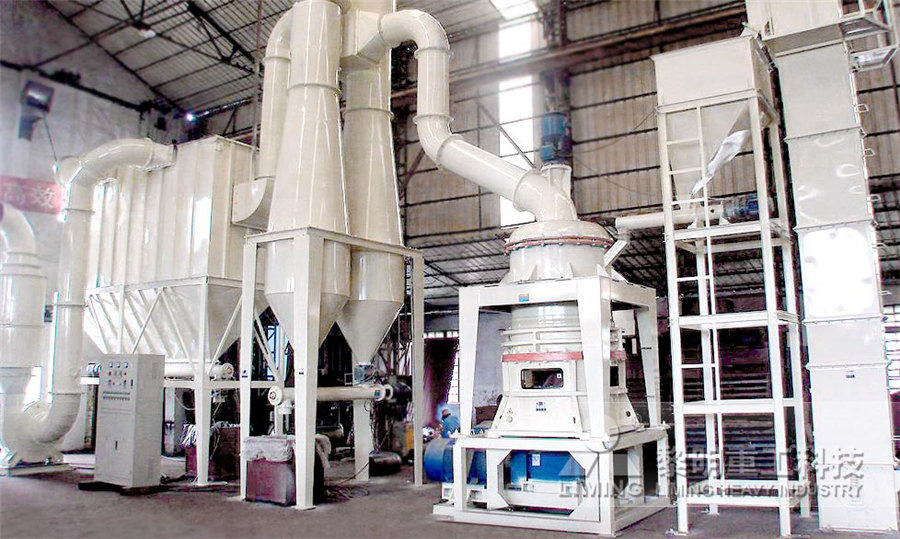
Ball mill: Principles, construction, working, uses, merits,
2024年1月28日 High Energy Consumption: Ball mills often require high energy input for the grinding process, making them less energyefficient compared to some other milling techniques 2 Wear and Tear: The grinding media and The ball mill splits the sample by using repeated hits against the ballsIt moves along an arc of a semicircle due to the dragging of the pitcher in the cylinder motor Isolated jars prevent the contamination of samplesBall mill Nuevo portal web de OrtoAlresa2021年3月23日 One method for increasing the energy efficiency of ball mills is to The energy performance analysis of the three solutions was based on the average energy consumption indicator per mass unit Energy Efficiency Analysis of Copper Ore Ball Mill Drive Systems2006年5月9日 Download Citation Ball charge loading Impact of specific power consumption and capacity In determining the proper mill size required to meet a targeted production rate, many factors are Ball charge loading Impact of specific power consumption and capacity
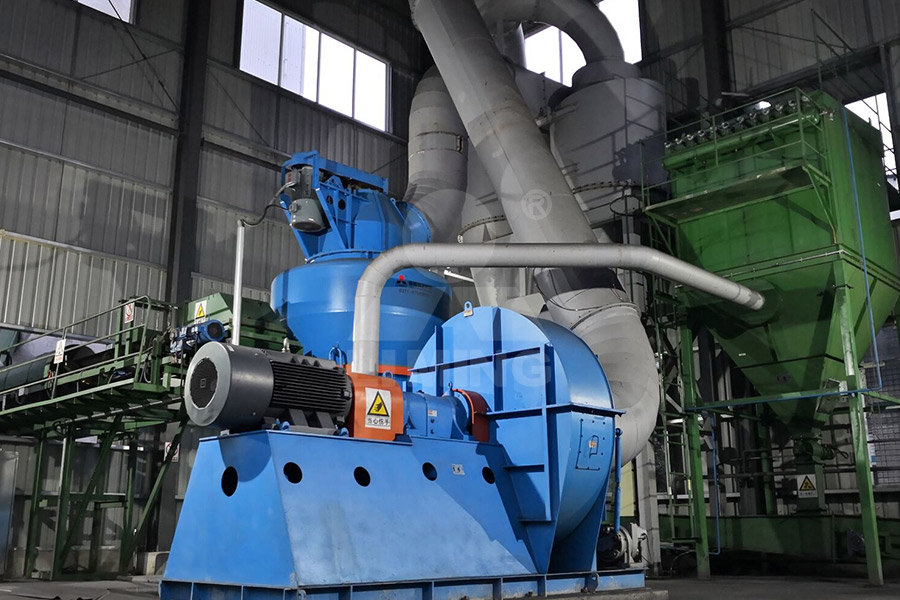
polysius® booster mill
Advantages at a glance: Modular design and small footprint enable integration in existing grinding plants Production increase in range of 1020 %, depending on the fineness, especially for smaller ball mill systems up to 100 tph Quality improvement by use of the additional grinding stage, for example to improve the early strength while maintaining the original production rate2015年10月15日 A) Total Apparent Volumetric Charge Filling – including balls and excess slurry on top of the ball charge, plus the interstitial voids in between the balls – expressed as a percentage of the net internal mill volume (inside liners) B) Overflow Discharge Mills operating at low ball fillings – slurry may accumulate on top of the ball charge; causing, the Total Charge Calculate Ball Mill Grinding Capacity 911Metallurgist2001年8月1日 Ball mills are used in mineral processing for particle size reduction These consist of a rotating cylindrical shell of up to 7 m in diameter with axial lengths greater than this Typical power consumption for a 5m diameter by 7mlong ball mill is between 25 and 35 MWCharge behaviour and power consumption in ball mills: Comparison of typical energy consumption figures for various mills systems are given below Mill System Mill only Kwh / ton Fan Auxiliaries Kwh / ton Total Kwh / ton Air swept ball mill 145 40 185 Double Rotor ball mill 116 48 164 Short single chamber bucket elevator mill 46 45 161Optimizing Electrical Energy Consumption In Cement Process
.jpg)
Mill (grinding) Wikipedia
Compared to ball mills HPGRs achieve a 30 to 50% lower specific energy consumption, although they are not as common as ball mills since they are a newer technology A similar type of intermediate crusher is the edge runner, which consists of a circular pan with two or more heavy wheels known as mullers rotating within it; material to be crushed is shoved underneath the 2024年4月29日 Ball mills are widely used for size reduction in mineral processing, but effective scaling from laboratory to industrial scale remains challenging This study introduces a novel scaling constant approach to replicate energy transfer to ore during milling across different scales by adjusting rotational speed and grinding medium size distribution The scaling constant Scaling Energy Transfer in Ball Mills: A ScaleAgnostic Approach