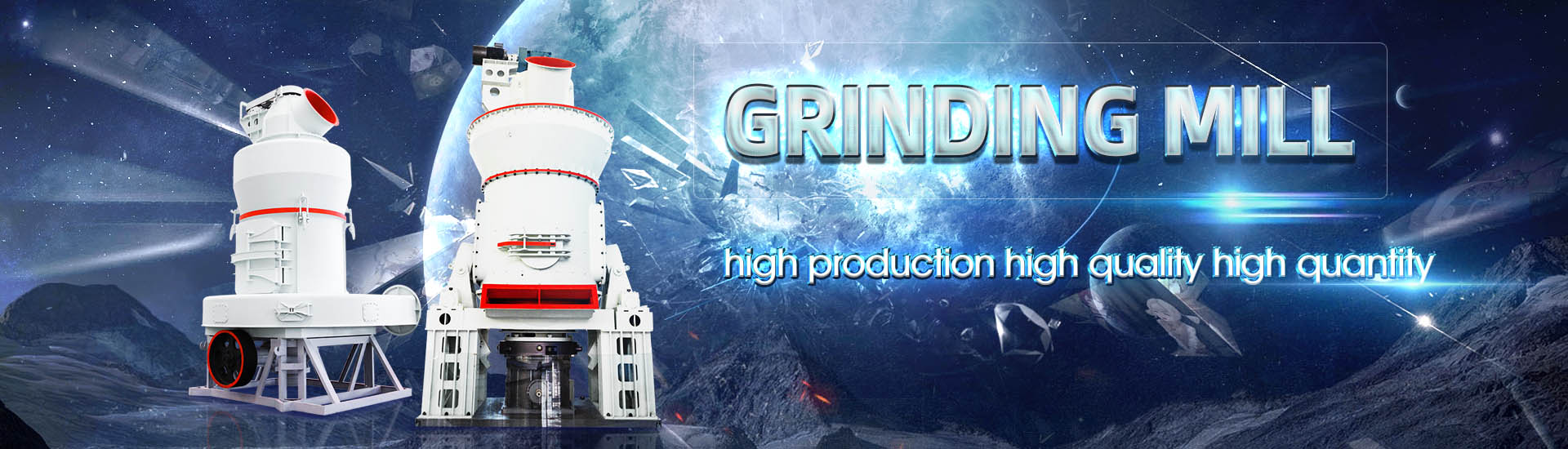
Vertical ore mill model and size
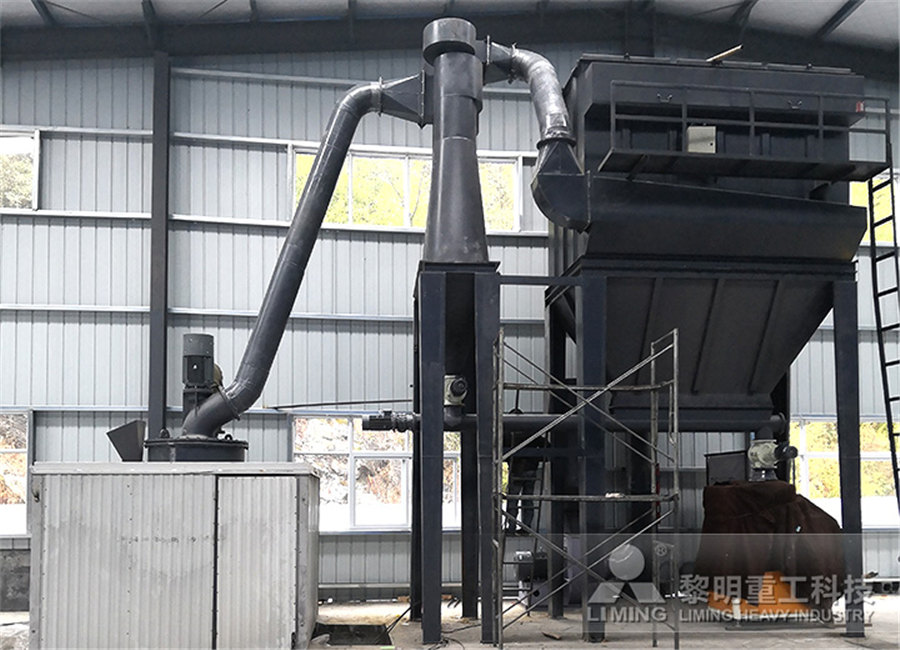
Mechanistic modeling and simulation of a batch vertical stirred mill
2020年9月1日 The present work takes advantage of a mechanistic mill model originally developed for ball mills and the discrete element method (DEM) to simulate breakage in a balance model was developed to analyze the response in product size resulting from changing operating conditions The model prediction was compared with the results obtained in thePREDICTING THE PRODUCT PARTICLE SIZE DISTRIBUTION FROM of 80mm The raw materials are mixed in a certain proportion and fed into a vertical roller mill (LOESCHE mill) The vertical roller mill grinds the marital to D 85 of 90µm The ground product is calcined in a preheater to 850900℃ After calcination, the materials enter to a rotary kiln and heated to 1450℃ to become clinkerModeling and simulation of vertical roller mill using population 2021年7月1日 Vertical stirred mills may be classified according to the speed of the stirrer in two groups: gravityinduced or fluidized mills [[1], [2], [3]]In the gravityinduced mills, the stirrer, generally of the screw type, turns so that the grinding charge exhibits an ascending convective motion at the center, descending from the edges of the screw and close to the mill shell, owing Predicting the effect of operating and design variables in
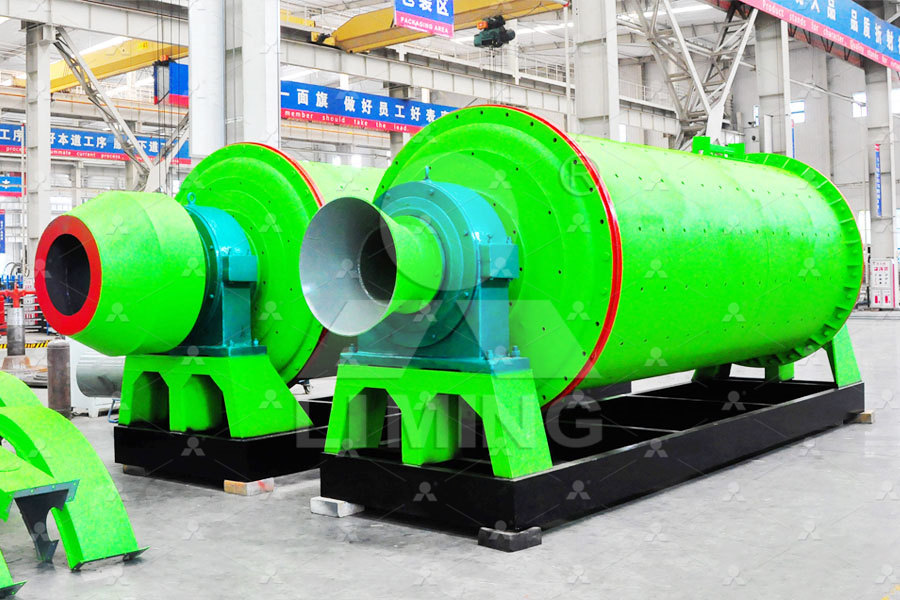
Vertical mill simulation applied to iron ores
2014年11月1日 The model previously implemented in Modsim™ has been successfully applied to represent the vertical mill operated with different ores The simulations produced particle size distributions that 2016年12月1日 It was found that the ball mill consumed 5467 kWh/t energy to reduce the F 80 feed size of 7222 lm to P 80 product size of 2754 lm while stirred mill consumed 3245 kWh/t of energy to produce Vertical stirred mill scaleup and simulation: Model validation by A vertical roller mill, also known as a vertical grinding mill or vertical mill, is a comprehensive grinding equipment integrating crushing, drying, grinding, grading, and conveying Vertical grinding mills can be widely used in electric power, metallurgy, construction, chemical industry, and other industries to make powder, especially for materials such as cement clinker, coal Energysaving and Efficient Vertical Roller Mill Fote Machinery2020年9月1日 Regarding the copper ore of interest in the present work, several of the breakage parameters used in the simulation using the mechanistic model were obtained from a set of experiments combining the use of rotary breakage testing devices as reported in Tavares et al (2020) with particles in the size range from 375 mm to 025 mm Due to the lack of available Mechanistic modeling and simulation of a batch vertical stirred mill
.jpg)
Particle size distributions of the pilot vertical mill circuit feeds
In the present study, size reduction experiments were performed on HighPressure Grinding Rolls (HPGR), ball mill and stirred mill of PGE bearing chromite ore2015年3月1日 It is emphasised that for a ball mill to treat the same ore with different mill feed size distributions and in different mill operational conditions (reflected in the (Shi, 2002; Shi et al, 2003) and the vertical spindle models (Shi et al, 2015; Kojovic et al, 2015) The sizespecific energy term Ei in Eq (2) explicitly Modelling of vertical spindle mills Part 1: Submodels for A vertical stirred mill model, based on the Population Balance Model (PBM) technique, the feed particle size distribution, the ore specific gravity, circuit feed rate and the industrial mill net power draw The simulation was performed using the vertical stirred mill model (Mazzinghy et al, Vertical stirred mill scaleup and simulation: Model validation by 2015年3月1日 Features of the specific energybased ball mill model include the use of an orespecific and sizedependent breakage function, whose parameters are independently measured with a fine particle Modelling of vertical spindle mills Part 1: Submodels
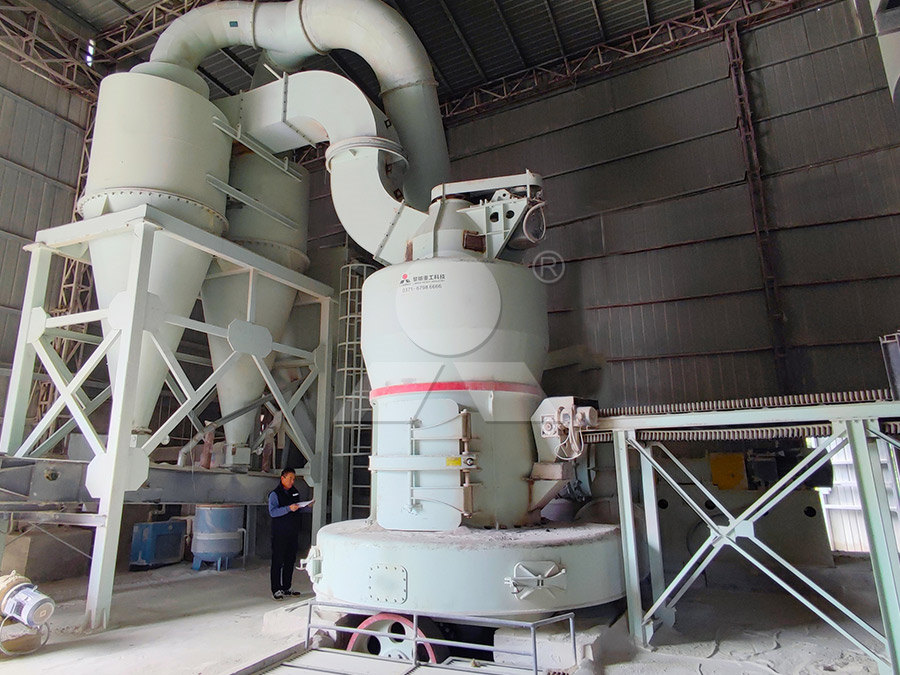
Modelling of vertical spindle mills Part 2: Integrated models
Request PDF On Mar 1, 2015, Toni Kojovic and others published Modelling of vertical spindle mills Part 2: Integrated models for Emill, MPS and CKP mills Find, read and cite all the research 2017年4月1日 The scaleup and simulation model used here is based on the population balance modeling technique using the Herbst Fuerstenau scaleup procedure for ball mills, adapted for vertical stirred mills The model was originally validated with extensive data from pilot scale vertical stirred mill tests (Mazzinghy et al, 2012, Mazzinghy et al, 2013 Vertical stirred mill scaleup and simulation: Model validation of 80mm The raw materials are mixed in a certain proportion and fed into a vertical roller mill (LOESCHE mill) The vertical roller mill grinds the marital to D 85 of 90µm The ground product is calcined in a preheater to 850900℃ After calcination, the materials enter to a rotary kiln and heated to 1450℃ to become clinkerModeling and simulation of vertical roller mill using population The previous study concluded the liberation size of around 1–50 µm for chromite ore bearing PGE minerals A vertical stirred mill model, based on the Population Balance Model Particle size distribution of the batch ball mill test and the model
.jpg)
Modeling and simulation of vertical roller mill using population
The cement raw materials (lime, silica and iron ore) enter the circuit through two apron feeders The raw materials are crushed in a hammer crusher to D95 of 80mm The raw materials are mixed in a certain proportion and fed into a vertical roller mill (LOESCHE mill) The vertical roller mill grinds the marital to D85 of 90µm2018年12月1日 A small size vertical stirred mill was manufactured for this study The curves obtained in Fig 5 indicate that the population balance model used to describe grinding in a vertical stirred mill is in good agreement with the D, Schneider, C, Alves, V, Galéry, R, 2013 Simulation of a Vertical Mill used for an Iron Ore Predicting the product particle size distribution from a laboratory 2024年5月1日 An industrialscale vertical wet stirred media mill (HIGMill) was simulated via a population balance model (PBM) Feed and product particle size distributions (PSDs) of copper ore were measured at various steadystate conditions The PBM incorporated 1large–2smalltanks model and powerlaw specific breakage rate function S iPBM of an industrialscale vertical wet stirred media mill (HIGMill PREDICTING THE PRODUCT PARTICLE SIZE DISTRIBUTION FROM A VERTICAL STIRRED MILL by VTM mill processing copper ore Figure 73 Vertical stirred mill DEM model calibration in terms of power for different stirrer speeds using: (a) 635, and (b) PREDICTING THE PRODUCT PARTICLE SIZE DISTRIBUTION FROM A VERTICAL
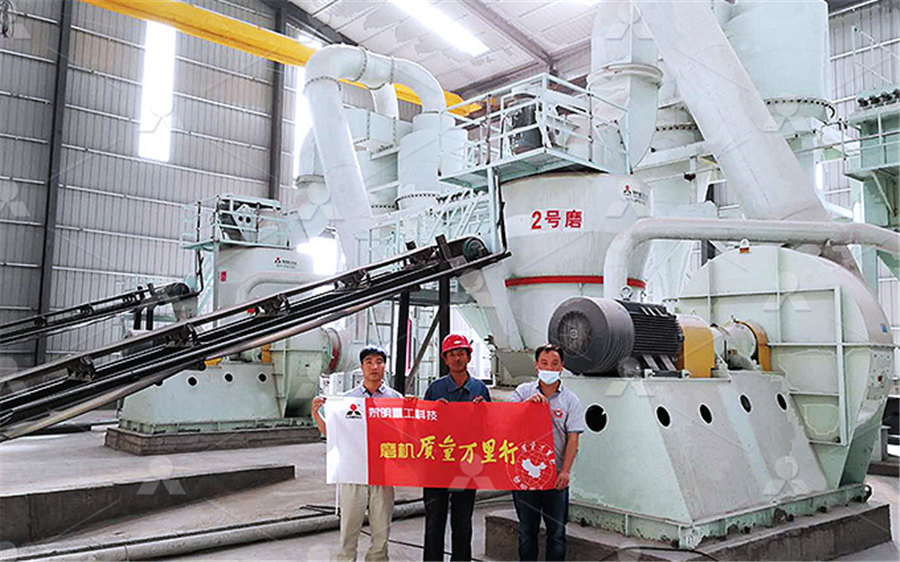
(PDF) Operational parameters affecting the vertical roller mill
The samples collected after the test works and size distributions were determined As and determination of breakage characteristics are part of the verticalrollermill performance model mill Cem Int 3 (2), 54–63 Reichert, M, 2015 Research of iron ore grinding in a verticalrollermill Miner Eng 73, 109–115 Find your ore mill easily amongst the 42 products from the leading brands (Fritsch GmbH, Retsch, Eriez, Final grain size: 74 µm 400 µm Rotational speed: 21 rpm The POITTEMILL pendulum roller mill is a vertical mill that works by compressing the material bedOre mill, Ore grinding mill All industrial manufacturers2021年4月24日 The work uses the UFRJ mechanistic mill model and DEM to analyze the effect of several design and operating variables on the apparent breakage rates and breakage distribution function of a batch Predicting the effect of operating and design variables in grinding Vertical roller mills are mainly engaged in three major fields of slag, coal powder, and nonmetallic ore Divided into: vertical roller mill, vertical slag mill, vertical coal mill, and ultrafine vertical millvertical roller mill, vertical coal mill, vertical slag mill, superfine
R)8OC`6F[ZIB.jpg)
Modeling and simulation of vertical roller mill using population
of 80mm The raw materials are mixed in a certain proportion and fed into a vertical roller mill (LOESCHE mill) The vertical roller mill grinds the marital to D 85 of 90µm The ground product is calcined in a preheater to 850900℃ After calcination, the materials enter to a rotary kiln and heated to 1450℃ to become clinker2023年2月23日 Performance Comparison of the Vertical and Horizontal Oriented Stirred Mill: Pilot Scale IsaMill vs FullScale HIGMill(PDF) Performance Comparison of the Vertical and ResearchGate2015年3月15日 Fig 9 shows the measured vertical mill product size distributions (symbols) and the corresponding simulated size distributions (solid lines) obtained using the parameters shown in Table 5, Table 6, Table 8, and the Austin perfectly mixed mill model with the specific breakage rate corrected by a factor of 135Vertical Agitated Media Mill scaleup and simulation2021年1月22日 Impact of ball filling rate and stirrer tip speed on milling iron ore by wet stirred mill: behavior of the PSD of the fine and ultrafine grinding progress, thus, some researchers turned to study the energysize model It has been recently demonstrated by Guo et al [47], using a vertical stirred media mill, Impact of ball filling rate and stirrer tip speed on milling iron ore
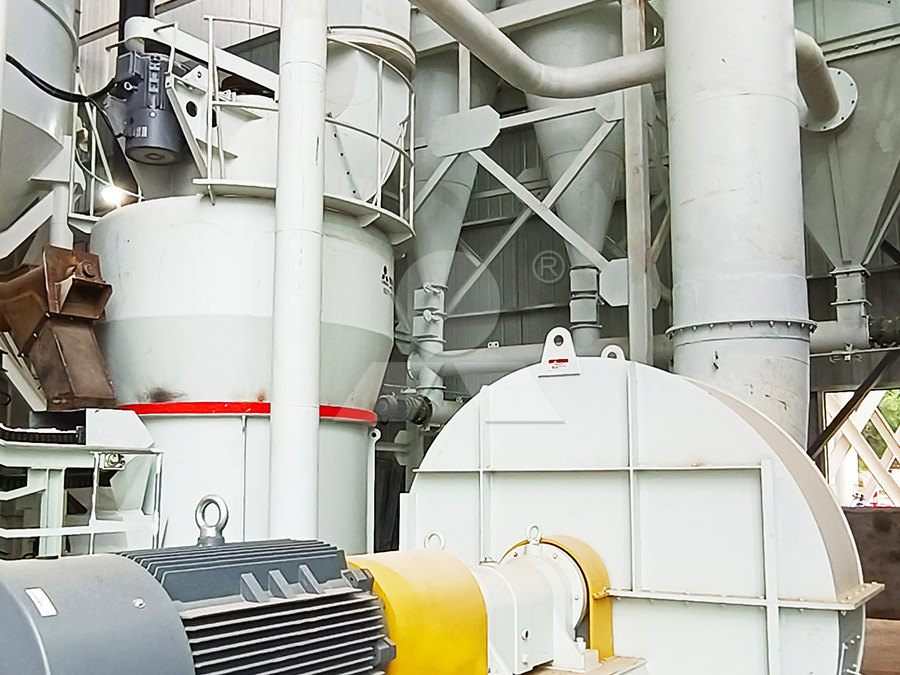
TowerMill Ò (Eirich courtesy) and Vertimill™ (Metso courtesy)
(2) are related to grinding operation as follows: A = f (mill conditions, eg, media size, solids concentration, mill speed, mill filling) α = f (ore hardness, mineralogy, specific gravity, etc 2022年10月1日 This study investigated a mathematical model for an industrialscale vertical roller mill(VRM) at the Ilam Cement Plant in Iran The model was calibrated using the initial survey's data, and the (PDF) A cement Vertical Roller Mill modeling based on2020年9月1日 Application of mechanistic modelling approach to batch wet vertical mills Stirrer rotation frequency and solids concentration effects captured by the modeling approach • Contribution of shear energy losses as function of solids concentration Good agreement between experimental and simulated particle size distribution for grinding of a copper ore and Mechanistic modeling and simulation of a batch vertical stirred mill Here are some common models of gold ore ball mills: 1 The stirrer creates a dynamic mixing and grinding action, resulting in high energy efficiency and reduced particle size distribution 6 Vertical Roller Mill: Vertical roller mills combine crushing, drying, What are the models of gold ore ball mills?
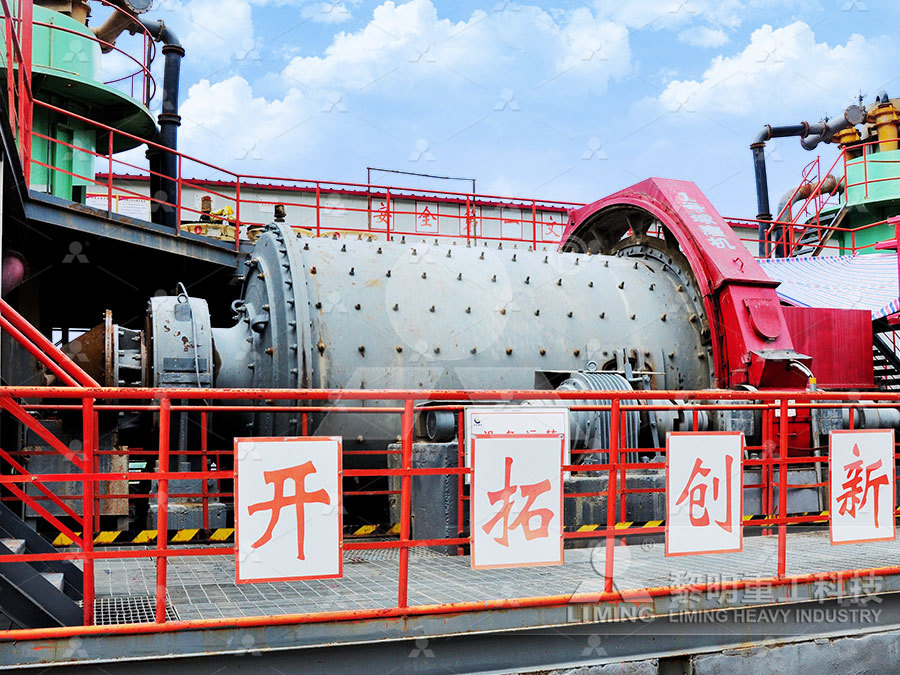
Modelling of vertical spindle mills Part 1: Submodels for
2015年3月1日 Semantic Scholar extracted view of "Modelling of vertical spindle mills Part 1: Submodels for comminution and A review of the applications of the JK sizedependent breakage model Part 1: Ore and coal breakage Performance of the static air classifier in a Vertical Spindle Mill Hong Li Yaqun He +5 authors W Xie2001年10月1日 This model has already been applied to predict the performance of a batch vertical stirred mill in size reduction of limestone and copper ore while operating at different stirrer frequencies and Media stress intensity analysis for vertical stirred mills(2) are related to grinding operation as follows: A = f (mill conditions, eg, media size, solids concentration, mill speed, mill filling) α = f (ore hardness, mineralogy, specific gravity, etc Vertical mill pilot circuit flowsheet as depicted in Modsim™2009年1月31日 In another study, a simple matrix model was used for modelling the grinding process in a cement vertical roller mill (CKP), and multiple grinding cycles were taken into account to obtain the final Grinding process within vertical roller mills ResearchGate
.jpg)
Predicting the product particle size distribution from a laboratory
DOI: 101016/JMINENG201809016 Corpus ID: ; Predicting the product particle size distribution from a laboratory vertical stirred mill @article{Rocha2018PredictingTP, title={Predicting the product particle size distribution from a laboratory vertical stirred mill}, author={Danielle Campos Rocha and Erik Spiller and Patrick R Taylor and Hugh B Miller}, LM Series Vertical Roller Mill is used to pulverize materials, material can be pulverized into 80400Mesh with this mill Feed particle size: 070mm Production capacity: 4300 tons / hour Applicable materials: limestone, coal, feldspar, calcite, fluorite, talc, iron ore, copper ore, phosphate rock, graphite, quartz, slag, etc Online Chat InquiryLM Vertical Roller Mill, Vertical Mill Manufacturer2015年3月1日 Features of the specific energybased ball mill model include the use of an orespecific and sizedependent breakage function, whose parameters are independently measured with a fine particle breakage characterisation device, the JKFBCModelling of vertical spindle mills Part 2: Integrated models 2018年9月28日 Simulation of a Vertical Mill used for an Iron Ore Application translated from: and by combining the RosinRammler particle size distribution model, Predicting the product particle size distribution from a
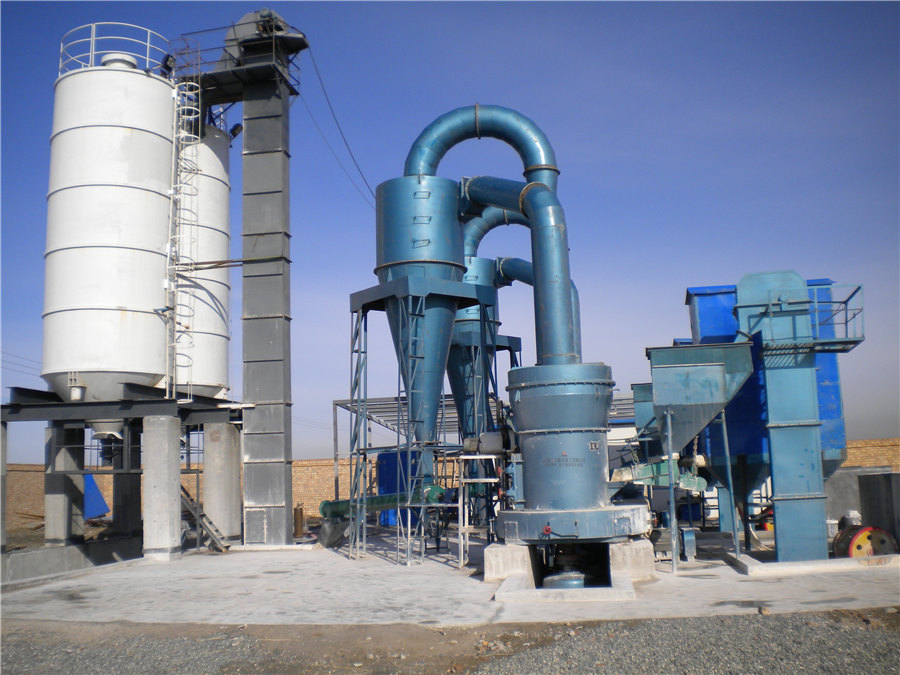
Research of iron ore grinding in a verticalrollermill
Request PDF On Mar 15, 2015, Mathis Reichert and others published Research of iron ore grinding in a verticalrollermill Find, read and cite all the research you need on ResearchGate