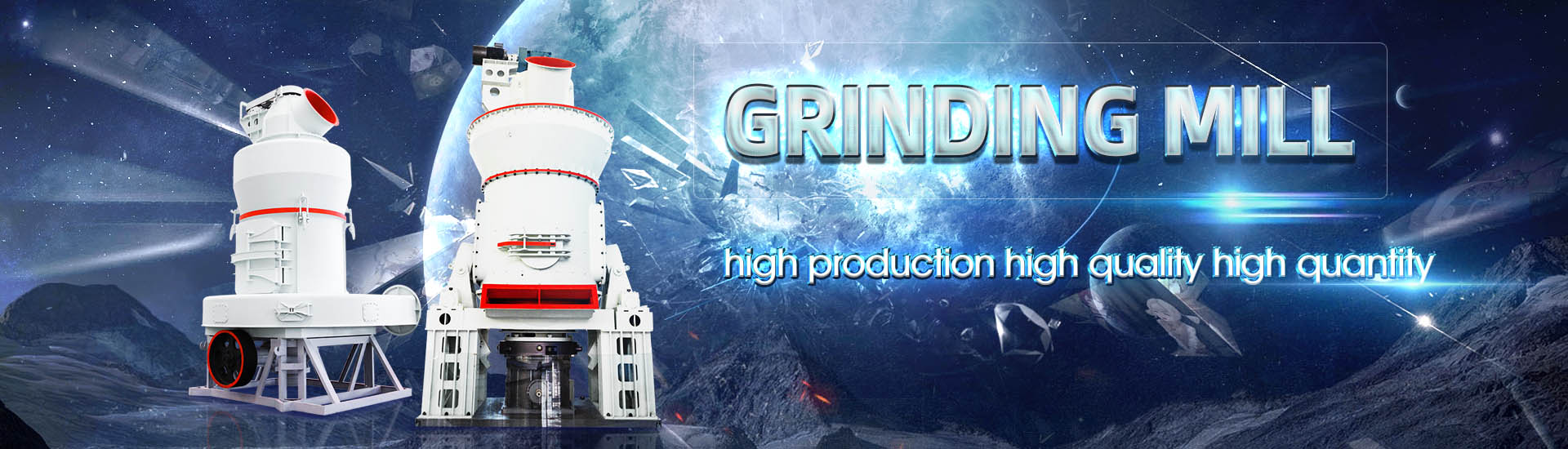
The effect of coal mill separator speed on coal powder fineness
.jpg)
Pulveriser Mill Performance Analysis Optimisation in Super
Abstract Most efficient way of utilizing coal for steam generation is to burn it in pulverised form The coal is pulverised to fineness such that 7080% passes through a 200 Mesh sieve Normally low speed ball mills or medium speed vertical spindle mills are employed in thermal power 2017年6月1日 The coal mill pulverizes raw coal into coal powder to meet certain requirements The coarse coal powder separator separates the large particles of coal powder from the Optimization control of a pulverizing system on the basis of the In May 2022, the # 1C mill will be transformed into a dynamic separator with better adjustment performance, which is used to improve the pulverized pipewind speed, powder uniformity, ZGM113G型磨煤机动态分离器改造性能试验及分析百度文库Based on a positivepressure directfired MPS mediumspeed mill with cool primary air,the effect of following pulverizing parameters on fineness of lean and bituminous coal powder has been Effect of Pulverizing Parameters on Fineness of Coal Powder from
.jpg)
Study on the influence of baffle height and angle on the
2024年10月1日 The optimized and improved powder selector model could reduce the fineness of the coal powder at the outlet by 60 % and increased the fineness of the coal powder at the 2017年11月15日 A method for choosing the optimum fineness of coal in pulverisedfuel boilers is presented This method is based on economic criteria and takes into account variations of Optimisation of coal fineness in pulverisedfuel boilersthis dissertation was to investigate the effect of coal feedstock property variation on the vertical spindle coal pulverising mill’s performance to facilitate optimal plant performance Plant design Performance optimisation of vertical spindle coal pulverisersHence, the objective of the study is to determine the effect of air flow rate and coal particle flow rate on coal fineness output Computational fluid dynamics (CFD) modelling and validation Computational Study of Coal Particle Distribution in Coal
.jpg)
PowerGen 2008, Orlando, USA Online measurement of coal
Not only does the fineness vary with the type of coal (including water content) but also with the mill setup and operating conditions and its wear and tear – the advent of fuel switching Various methods for choosing the fineness of power plant coal dust are reviewed and analytical expressions for determining the fineness are presented It is shown that the use of the yield of Choice of Fineness of Pulverized Coal Springer2015年11月1日 The coal mill grinds the raw coal into fine powder and hot air entering the mill dries and carries the pulverized coal to the burners of the furnace Maffezzoni (1986 ) emphasized that coal mills are the primary cause of slow load following capability and regular plant shutdownsA unified thermomechanical model for coal mill operation2021年8月1日 Yukio et al [7] proposed a model consisting of blending, grinding and classifying processes for pulverizer control Agarawal et al [8] differentiated coal powder into ten size groups, divided the bowl mill into four zones, and developed a unified model Palizban et al [9] derived nonlinear differential mass equations of raw coal, recirculation coal and suspension coal in Coal mill model considering heat transfer effect on mass

Computational Fluid Dynamics (CFD) investigation on
2022年12月1日 Computational Fluid Dynamics (CFD) investigation on associated effect of classifier blades lengths and opening angles on coal classification efficiency in coal pulverizer December 年10月1日 The fineness of coal powder at the fine powder outlet was reduced by 60 % and the fineness of coal powder at the coarse powder return port was improved by 43 % for the optimized model compared with the original coarse powder separatorStudy on the influence of baffle height and angle on the 2017年8月1日 The effect of coal moisture on model accuracy was considered in this study In this study, MPS180HPII medium speed coal mill is used as the research object Its maximum output is 44496 t/h and the fineness of coal powder R90 is 22% [15] Modeling of a medium speed coal mill ScienceDirect2017年6月1日 In the present study, the MPS180HPII mediumspeed coal mill (Yuan, nd) is used as the research object Its maximum output is 44496 t/h, and the fineness of coal powder R90 is 22% (Fig 2) (R90 indicates the probability that coal powders cannot pass through a sieve with a pore size of 90 µm)Optimization control of a pulverizing system on the basis of the
.jpg)
Pulverizer Plant OM Aspects
Effect of fineness Maximum Mill capacity vs PF fineness at 12 % Raw coal moisture and at Coal HGI 100110 3300 3400 3500 3600 3700 3800 3900 4000 4100 65 70 75 80 85 Mill output at raw coal moisture and at Coal HGI 100110 年1月6日 The fineness of the coal powder and the uniformity of the coal flow sent to the burners are crucial parameters to achieve an effective combustion in coalfired power plantsOnline monitoring of coal particle size and flow distribution in coal bowl type medium speed coal pulverizer in detail from the reality, and analyzes the causes, At the same time, part of the performance optimization scheme of this type of coal mill is introduced 1 Introduction In recent years, various types of medium speed coal mills are used more and more in coal pulverizingSHPHGLXPVSHHGFRDOPLOO IOPscience2017年4月11日 The fineness of the coal powder and the uniformity of the coal flow sent to the burners are crucial parameters to achieve an effective combustion in coalfired power plantsPreliminary investigation on the effects of primary airflow to coal
.jpg)
An investigation of performance characteristics and
2020年8月12日 This study shows the performance of a currently running vertical roller coal mill (VRM) in an existing coalfired power plant In a power plant, the coal mill is the critical equipment, whose 2009年1月1日 below shows the particle tracks colored by the particle velocity magnitude for particles with a diameter size of 58 μm Fine particles of such a size are easily entrained in the flow and follow a CFD Modeling of MPS Coal Mill for Improved 2021年6月29日 The research focuses on the mill speed as well as air classifier speed effect on the two compartment Cement ball mill performance in terms of Blaine, Sulphur trioxide contents, mill power, mill Effects of Mill Speed and Air Classifier Speed on 2023年9月1日 The coal powder in the main burner has a coarser grind compared to the average value that was achieved at the exit from the mill A minimum of 33% of gas ventilation and 15% of coal powder from the mill (very fine grinding) is fed into the separate gas nozzleThe Influence of Mill Loading on the Distribution of Pulverized Coal
.jpg)
Fault analysis and optimization technology of HP bowl type medium speed
2021年8月1日 This content was downloaded from IP address 15846163192 on 24/08/2021 at 14:年9月1日 The fineness of the coal powder and the uniformity of the coal flow sent to the burners are crucial parameters to achieve an effective combustion in coalfired power plantsCFD based investigations into optimization of coal pulveriser 2017年8月1日 This kind of coal mill has the characteristics of low energy consumption and smooth output and has a small effect on abrasive wear and an overhaul period [13], [14] In this study, MPS180HPII medium speed coal mill is used as the research object Its maximum output is 44496 t/h and the fineness of coal powder R90 is 22% [15] (Fig 1) (R90Modeling of a medium speed coal mill ScienceDirect2023年8月1日 In pulverized coal separation plants, a coarse powder separator with air flow characteristics is used as a pivotal device to connect the coal mill to the cyclone and preseparate the new coal particle population created by the mill (Cepuritis, Jacobsen, Onnela, 2015) The crucial performance index is R 90 and capacityOptimization of an axial coarse powder separator for lowdensity
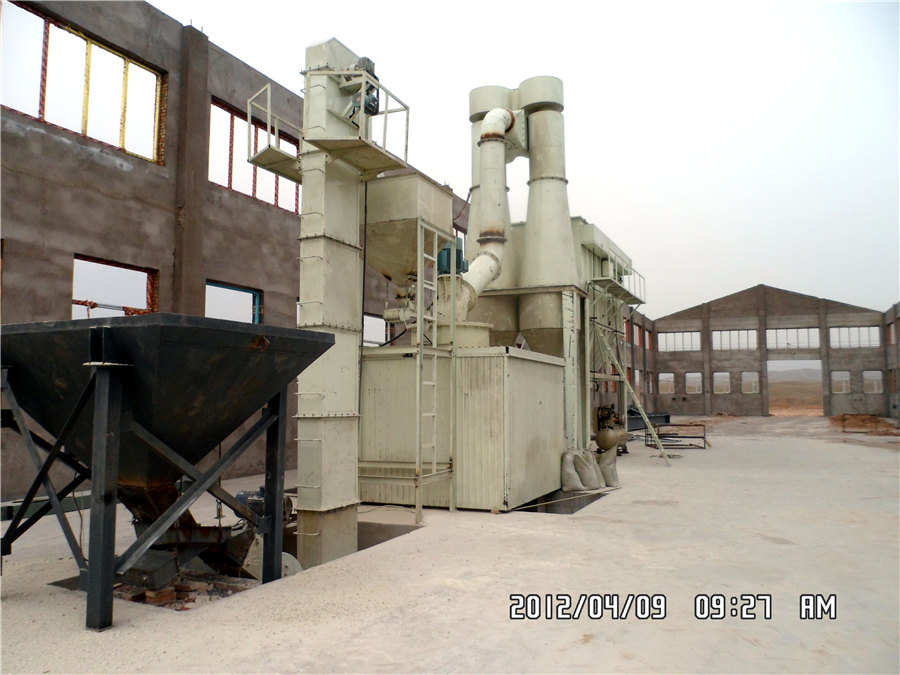
Optimization and transformation of 300MV units steel ball coal mill
IOP Publishing % %% )2 Raw coal properties – Hardgrove index and moisture level 3 Pulverized coal fineness The raw coal is fed into a rotating bowl via a center feed pipe The rate of coal feed is normally determined automatically by a combustion control system, taking into account the MW demand on the unit, coal quality, and the number of coal pulverizers in Bowl Mill Coal Pulverizer COAL HANDLING PLANTS2019年11月7日 Comprehensive treatment,we should have a test on the 300 MV unit steel ball coal mill pulverizing systemAt the same time,analyze the main operating parameters before modificationTransform the Optimization and transformation of 300MV units steel ball coal mill Cement Mill Separator; Cement Mill; Others Menu Toggle Conveying System; Overland Conveyor; Vibrating Grizzly Feeder; The fine material is taken away by the highspeed hot air from the bottom to the top, Coal powder fineness Coal Mill in Cement Plant
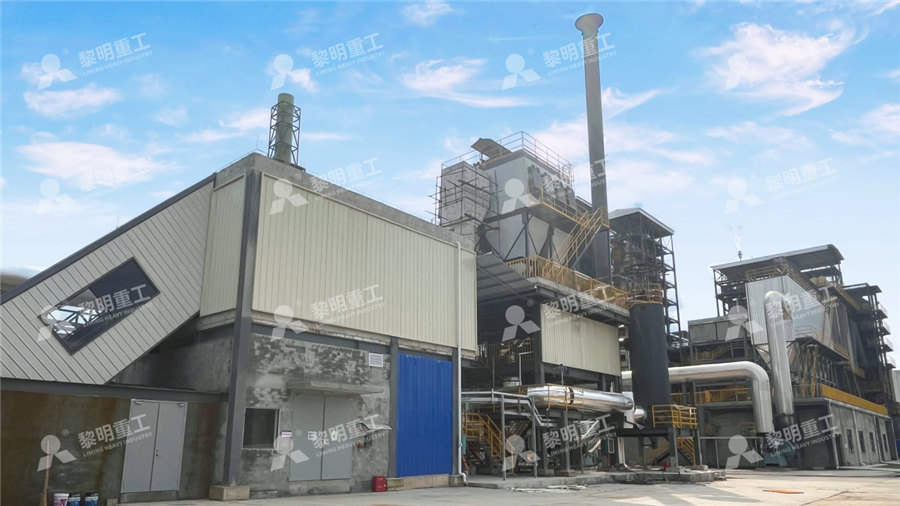
Effect of ball and feed particle size distribution on
2018年2月1日 Hlabangana et al [49] investigated the effect of operating conditions, namely, media/material filling and mill rotational speed on the milling efficiency of a laboratoryscale ball mill using the Download scientific diagram Effect of mill outlet temperature on the coal moisture content from publication: An investigation of performance characteristics and energetic efficiency of vertical Effect of mill outlet temperature on the coal moisture content1311 The ventilation resistance of HP coal mill is smaller than that of other medium speed pulverizers, and the air pressure of primary air fan is smaller, which can reduce the investment cost of fan 14 Working principle The function of HP series coal mill is to mill raw coal to achieve the fineness that can be effectively burned in the HP Bowl type millspower plant equipment2017年5月1日 Download Citation Modeling of a medium speed coal mill This paper presents a coal mill model that considers the effect of coal moisture on its accuracy This mathematical model is derived Modeling of a medium speed coal mill ResearchGate
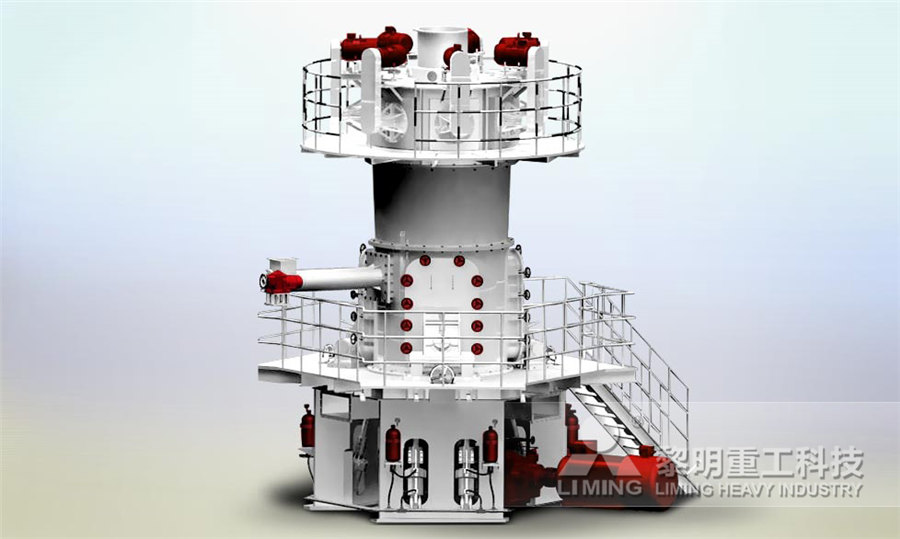
The Effect of Surface Finish and Fillet Design on Tie Rod Shaft
2023年10月11日 The broken incidents of the tie rod shaft at coal mill the coal mill plant of PT X takes effect on to prod uce the power of coal Th e coal powder is parameters such as cutting speed, 2016年9月1日 Furthermore, VRM separator speed (rpm) is one of the key operational parameters that determines product particle size Increasing the classi er rotor speed from 60 to 80 rpm decreases the particle Operational parameters affecting the vertical roller mill the fineness bears composite parameters that allow for the heat value of the volatiles and for the internal surface of the fuel particles Keywords: fineness of coal dust, milling, yield of volatiles, porosity, heat of combustion of volatiles, fuel density, Choice of Fineness of Pulverized Coal Springer2017年6月30日 Gao et al, proposed a fault diagnosis method for coal mill system that can simulate fault samples to effectively solve the problem of fault sample collection [2]; Zhu et al, proposed an HP mill Optimization control of a pulverizing system on the basis of the
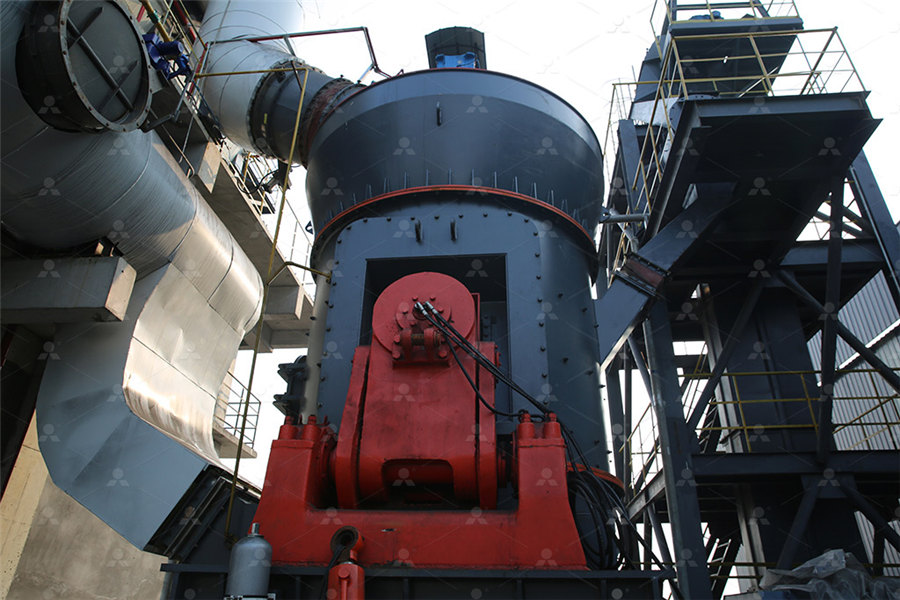
Breakage and separation mechanism of ZGM coal mill based
2014年3月1日 Moreover, coal volatile matter and moisture content are improved by increasing the mill outlet temperature for each coal type Additionally, effect of enhancement of the classifier speed has been Introduction This article concerns itself with vertical grinding mills used for coal pulverization only (coal pulverizers), although vertical grinding mills can and are used for other purposes The 3D model in the saVRee database represents a Vertical Grinding Mill (Coal Pulverizer) Explained2023年1月30日 Based on the problems of high carbon emission and high cost of traditional mining methods and filling materials, the tailings powder modified Coal Ganguebased Cementitious Backfill Material (CGCBM) was used for paste filling mining In this study, the samples were prepared with different tailings powder content and different curing ages The Study on the modification effect and mechanism of tailings powder 2020年4月7日 MPS mediumspeed coal mill is a rolltype mediumspeed coal mill designed and manufactured by Ba bcock, Germany The mill is characterized by low power consumption, smoothModeling of Coal Mill System Used for Fault Simulation
.jpg)
Pulverizer Fineness and Capacity Enhancements at Danskammer
RPM is programmed to follow mill coal flow to obtain a desired fineness vs mill load rela tionship; manual override with manual control of classifier speed from the control room is also provided; instrumentation for monitoring drive assembly oil bath temperature and oil2022年3月1日 Zhang et al investigated the relationship between the diameter of separator and the separation efficiency The results showed that the qualified fine powder will return to the coal mill with the coarse powder if the diameter of the separator is too large, resulting in the decrease of the separation efficiency [24]Operational performance characteristics of an axial double baffles 2014年1月1日 The modification of the blade angle, blade shape, and vertical position of the separator and its effect on the coal powder distribution at the burners were analyzed and are published for the first CFD analysis of the influence of centrifugal separator geometry 2014年3月1日 The crushing efficiency and coal grinding characteristics of the medium speed roller mill and ball mill in power plants were studied by Rubiera and Cho The influence of the coal blending and minerals in coal on the grinding efficiency was studied and the optimization scheme was put forward [8], [9]Breakage and separation mechanism of ZGM coal mill based
.jpg)
Effect of ammonia on the characteristics of coal combustion
2023年8月1日 Under the guidance of “Carbon peak” and “Carbon neutral” goals, traditional coalfired units as a major carbon emitters face enormous pressure to reduce carbon emissions [[1], [2], [3], [4]]For coalfired units, there are two main ways to reduce carbon dioxide emissions: one is to capture carbon dioxide at the end of the power generation system [5], but the capture 2011年10月1日 Coal fineness is a relative measurement of particle size distribution typically applied to the product leaving a pulverizer Standardized wire mesh screens are stacked and used to shake down samplesImproved Coal Fineness Improves Performance, Reduces Emissions