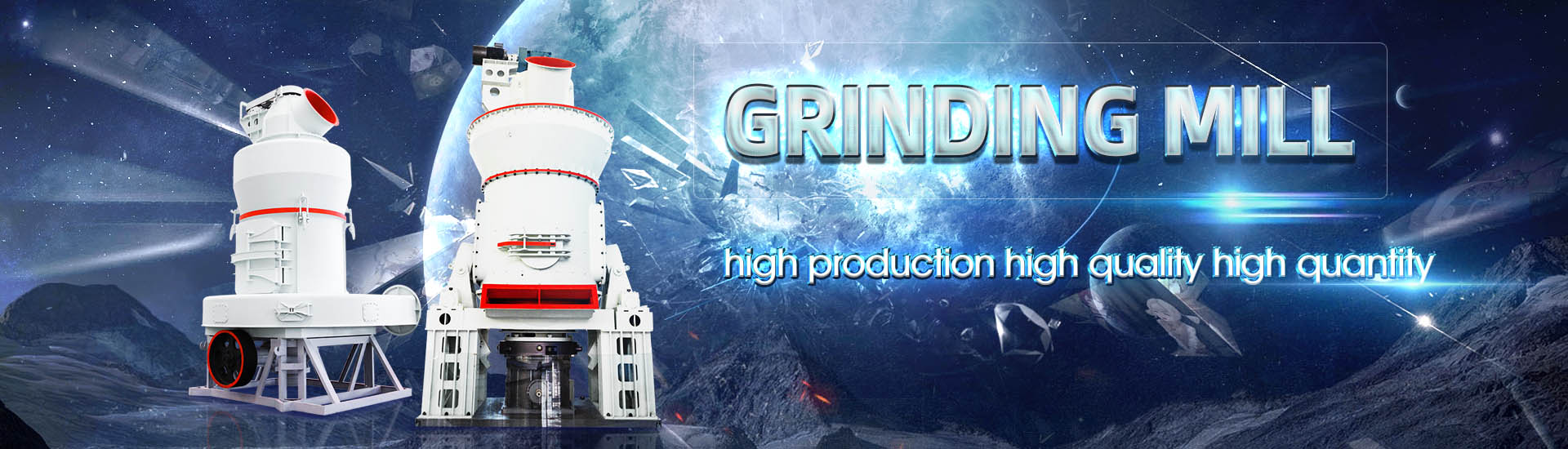
Energy consumption of vertical mills, wear resistance
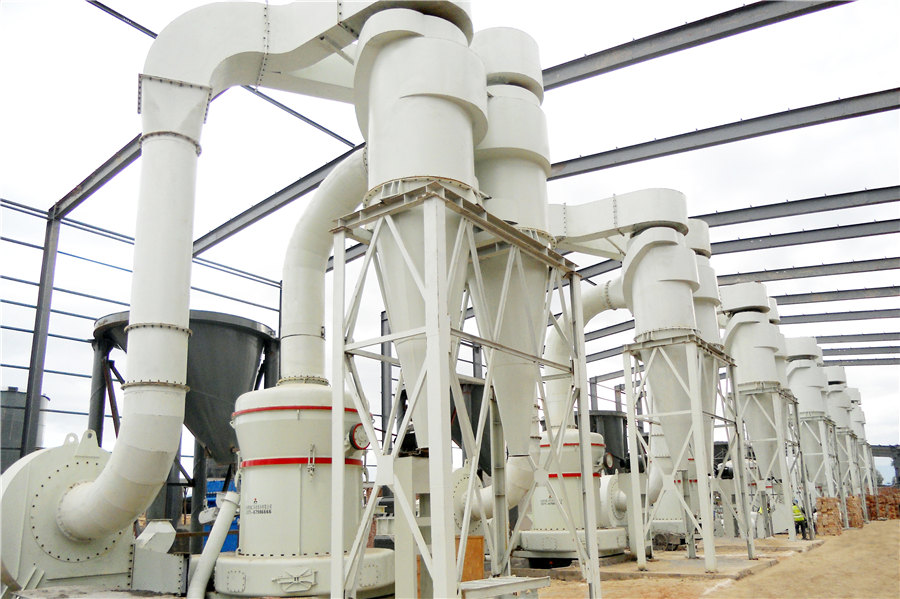
Energy consumption model for milling processes considering
A complete machining process generally consists of three operational states: the startup state, the idle state and the machining state Figure 1shows a general power consumption profile in a cutting process, which is composed of three slot cutting operations with a constant spindle speed A machine tool generally 展开2022年5月9日 By initiating a CL for an industrial cement vertical roller mill (VRM), this study conducted a novel strategy to explore relationships between VRM monitored operational Modeling of energy consumption factors for an industrial cement 2021年9月1日 This study aims to predict the specific grinding energy consumption of vertical roller mills via breakage test Pilot scale tests are used currently for energy consumption Predicting the grinding energy of vrm depending on material 2017年8月15日 The energy consumption by machine tool components can be classified into two types: fixed energy (constant energy) and variable energy The fixed energy is consumed by Energy consumption in machining: Classification, prediction, and
.jpg)
An energy based comparison of vertical roller mills and tumbling
2015年3月10日 In order to address grinding efficiency (defined as the increase in mass specific surface vs net specific energy input) the energy consumption of two pilot scale vertical roller 2020年4月10日 In this study, the energy consumption values of both the spindle and X axis servo motors during chip removal were examined along with the amount of surface roughness Calculation and Estimation of Surface Roughness and Energy 2022年1月23日 This work concentrates on the energy consumption and grinding energy efficiency of a laboratory vertical roller mill (VRM) under various operating parameters For design of experiments (DOE), the response surface method Analysis and Optimization of Grinding Performance of 2022年1月12日 The present study explores the influence of three cutting parameters, namely, cooling/lubrication conditions, cutting speed and feed rate, on the energy consumption at ball Optimization and Prediction of Specific Energy Consumption
.jpg)
MachineSpecific Estimation of Milling Energy Consumption in
2021年3月29日 This paper discusses a methodology for machinespecific energy estimation in milling processes at the detailed design stage based on the unit process life cycle inventory 2017年11月20日 This accurate model can be used to substantially reduce energy consumption in milling processes at machine and factory levels leading to massive cost savings and A mechanistic model of energy consumption in millingconsumption, low wear rates, handling material with high moisture, coarser feed cause gaining an advantage of vertical roller mills over conventional grindingPerformance Evaluation of Vertical Roller Mill in Cement 2017年9月11日 It was concluded that vertical roller mill circuit has an advantage over conventional ball milling circuit in terms of energy consumption Name of the streams Design parameters of vertical roller mill(PDF) Performance Evaluation of Vertical Roller Mill

Polygonal concave wear and irregular packing behavior of
2023年9月1日 The paper investigates the effects of changing the particle–particle restitution and sliding friction coefficients of grinding media within a vertical stirred mill using the discrete element Influence of quartz particles on wear in vertical roller mills Part I: Quartz concentration energyintensive process is consumed about 3% of the energy produced in the industrialized countries in the world (Schonert, 1979; The latter usually has the better wear resistance against quartz(PDF) Influence of quartz particles on wear in vertical roller mills Understanding Our Proprietary Vertical Cement Mill Technology Magotteaux’s proprietary vertical cement mill technology has been developed through decades of innovation and expertise in grinding processesOur vertical cement mill wear parts are designed to provide optimal grinding efficiency, quality, and reliability for cement productionOur systems and parts are like no Vertical Cement Mill Magotteaux2021年4月10日 Vertical stirred mills have been widely applied in the minerals industry, due to its greater efficiency in comparison with conventional tumbling mills In this context, the agitator liner wear plays an important role in maintenance planning and operational costs In this paper, we use the discrete element method (DEM) wear simulation to evaluate the screw liner wear Three Industrial Vertical Stirred Mills Screw Liner Wear Profile MDPI
.jpg)
Regrind of metallic ores with vertical mills: An overview of the
2014年10月20日 Santos Júnior et al (2011) also reported lower consumption of grinding bodies in the Vertical Mill 69 g/kWh versus 80 g/kWh observed in the ball mill The specific energy consumption measured seen, the vertical mill consistently presented lower net specific energy consumption than the ball mills which operate on the same circuit The averages were 113, 117 and 65 kWh/t respectively for ball mill 01, ball mill 02 and vertical mill Figure 5 – Net specific energy consumption of regrinding paring ball and vertical mills performance: An industrial case studyAccording to the running characteristics of vertical coal mill, KINGCERA has designed different wearresistant lining plates for coal mill barrel and coal mill shell The coal mill liner can be installed onsite, or on the curved steel plate in the factory and then welded to the mill barrelMediumspeed coal mill wearresistant ceramic liner Composite Industrial Vertical Stirred Mills Screw Liner Wear Profile electrical energy consumption [2], and more recently, this number was indicated as close to 18% [4]Industrial Vertical Stirred Mills Screw Liner Wear Profile
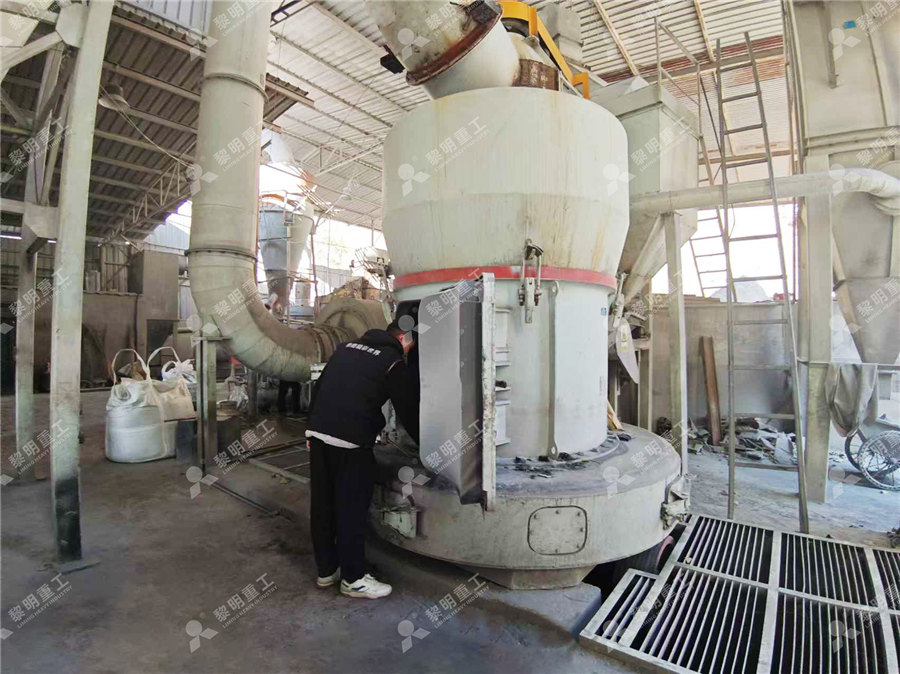
(PDF) Grinding Media in Ball MillsA Review
2023年4月23日 the grinding media reduces energy and material consumption in a ball mill Different performances are achieved when different sizes and shapes of grinding media are used [ 12 ]2017年1月17日 Grinding mills are infamous for their extremely low energy efficiency It is generally accepted that the energy required to produce new mineral surfaces is less than 1% of the electricity consumed Breaking down energy consumption in industrial Vertical stirred mills are a fine grinding equipment that covers advantages of low rotation speed, high reliability and long life cycle The significant advantages that the vertical stirred mills have over the ball mills are smaller size, less auxiliary Vertical Stirred Mill Mineral Processing Equipment80 mm e raw materials were mixed in a certain proportion and fed into a vertical roller mill (LOESCHE mill) e raw vertical roller mill has four rollers, 3000 KW main drive, 48 m table diameter Modeling of energy consumption factors for an industrial cement
.jpg)
An energy based comparison of vertical roller mills and tumbling mills
2015年3月10日 In order to address grinding efficiency (defined as the increase in mass specific surface vs net specific energy input) the energy consumption of two pilot scale vertical roller mills (200 mm and 670 mm table diameter) was compared to that of a sequence of laboratory comminution equipment covering the same size range2015年2月16日 A typical comparison of three competing technologies is given in Table 1, demonstrating that an efficient ball mill/thirdgeneration separator, CKP/ball mill/thirdgeneration separator and vertical mill on a typical 4000Blaine limestone cement show little overall difference in energy consumptionBest energy consumption International Cement Review2019年3月8日 mills or in vertical roller mills resistance, lower material buildup and effects of erosion, energy consumption was reduced by 3956 terajoules The IMPROVING THERMAL AND ELECTRIC ENERGY EFFICIENCY AT 2023年12月4日 A vertical roller mill (VRM) The resulting forces in the vertical and horizontal directions due to changes in rolling resistance and the mill speed are summarized Jensen LRD, Fundal E, Møller P, Jespersen M (2011) Wear mechanism of abrasion resistant wear parts in raw material Vertical Roller Mills Wear 271:2707–2719 Numerical Investigation of Vertical Roller Mill Operation Using
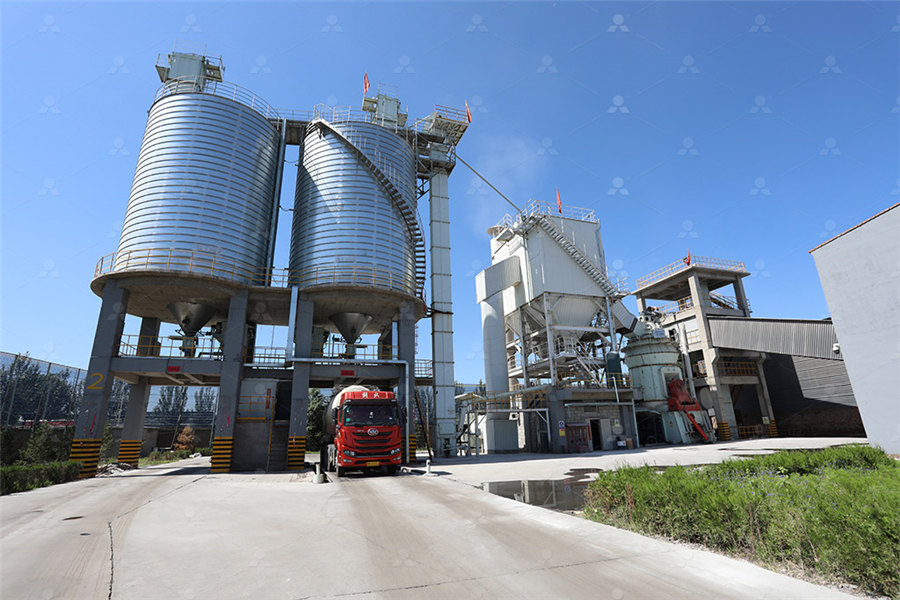
The Smart Welding Concept
aggravated wear Figure 1 shows the evolution over time of equipment performance that is subjected to inservice wear Wear of components results in both lower productivity and higher energy consumption as the amount of wear increases Figure 1 shows that the quicker a mill can pass through Period 1 to reach the optimum grinding phaseIt is characteristic of grinding in vertical roller mills that the energy input to the material per pass between roller and table is small, It appears from the table that the specific energy consumption of the OK mill system is 25% (Blaine) the cost of wear parts (ball, liners and mill internals) is typically 015020 EUR per ton of Cement grinding Vertical roller mills VS ball millsvertical mill raw material final grinding system, and roller press raw material final grinding system This paper compares the characteristics of several grinding systems and summarizes their A Survey and Analysis on Electricity Consumption of Raw Material Mill 2024年1月15日 This paper focuses on the startup and steadystate operation stages of a vertical stirred mill, and the electromechanical coupling characteristics are thoroughly investigated based on the ECSMBDDEM coupling method Firstly, according to the driving and working principles of the vertical stirred mill, the electrical control system (ECS) and multibody Electromechanical coupling characteristics analysis of vertical

VRM In Cement Plant Maximize Energy Saving CNBMSINOMA
Vertical roller mill manufacturers Vertical roller mill or VRM is a largescale grinding equipment designed for pulverizing cement raw meal, cement clinker, slag, coal, fly ash, limestone, and other hard grinding materialIt integrates grinding, drying, separation, and conveying in one machine The equipment is widely used in many industries such as cement, electric power, metallurgy 2021年1月29日 Vertical roller mills, VRMs, are widely used for grinding raw materials in factories engaged in the extraction and processing of minerals Any machine used for grinding or crushing consumes around Increase productivity of vertical roller mill using seven QC tools2019年11月14日 With the modern manufacturing industry evolving and advancing and amid a more energy conscious society, high energy demand in manufacturing—particularly in machining—has drawn more and more attention Accurate energy consumption modelling is critical to the improvement of energy efficiency in machining In the existing energy models of Energy consumption model for milling processes considering 2021年6月7日 Yakushev AA, Dukhanin SA (2020) Improving the wear resistance of the working bodies of a rotaryvortex mill In: Energyresourcesaving technologies and equipment in the road and construction industries: proceedings of the international scientific and practical conference BSTU, Belgorod, pp 444–447 Google ScholarImproving the Wear Resistance of RotaryVortex Mill Hammers
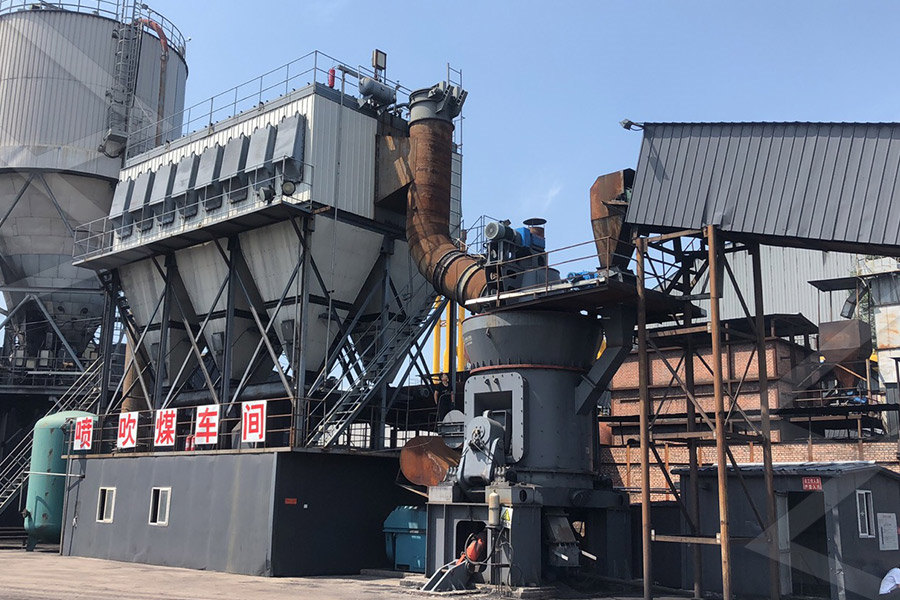
(PDF) Industrial Vertical Stirred Mills Screw Liner Wear Profile
Due to the high energy consumption of milling, such as its effects on load behavior As there is no available information about how to determine and quantify wear for vertical stirred mills, the intensive wear could substantially affect liner material resistance properties, thus reducing wear resistance for very worn conditionsVERTICAL MILL AND SCREW LINER WEAR Vertical stirred mills consist of a large cylindrical shell with a suspended vertical doublehelical screw impeller inside it Minerals Engineering, 2011: 245–251 DOE “Comminution and Energy Consumption” doc NMAB364, US Department of Energy report, 1981, 283 Duffy, Stephen MarkPREDICTIVE MODELLING OF VERTICAL STIRRED MILLS LINER WEAR 2016年1月1日 It consumes most of the energy used in mineral processing plants with grinding using up to 50% of the provided energy Tumbling mills are as energy consumption, mill and wear resistanceA comparison of wear rates of ball mill grinding media2015年5月6日 PIRITA HÄRKISAARI: Wear and Friction Effects on Energy Consumption in the Mining Industry Tampere University of Technology Master of Science Thesis, 77 pages, 14 Appendix pages April 2015 Master’s Degree Program in Material Science Major: Personal Studies in Materials Science Examiners: Professor VeliTapani Kuokkala, Project Manager Kati ValtonenWear and Friction Effects on Energy Consumption in the Mining
.jpg)
Principles of development of grinding media with increased wear
2012年5月5日 The compositions of wearresistant steels used as the material for grinding media are validated in order to obtain the optimal relation between the wear resistance and cost Mathematical experiment planning reveals that lowalloyed hypereutectiod steels with the austenitemartensite structure without secondary carbides and eutectoid steels with the The vertical mill is a very compact machine designed to take up less space and offer the user a high level of production capacity with reduced energy consumption The advantages of using the vertical mill in production, as Vertical hammer mill Lamec2020年11月4日 wind resistance, and energy consumption of the system will increase e pressure nephogram of Z 0 section is shown in Figure 7 e average pressures of each region are preEffects of Blade Parameters on the Flow Field and Classification 2023年6月26日 The issue of reducing tillage resistance and lowering energy consumption has become increasingly relevant Strip tillage has a positive impact on soil protection and energy consumption reduction(PDF) STUDY ON TILLAGE RESISTANCE AND ENERGY CONSUMPTION
.jpg)
Predicting the grinding energy of vrm depending on material
2021年9月1日 It is an important step to present the energy dimension relationship of a fastgrowing application such as HPGR, which is a compression grinding machine, due to low energy consumption The vertical roller mill is also one of the high compression grinding technology and has an important position in the cement and mineral industry due to their 2021年3月24日 In view of the difference between the theoretical and actual wear resistance, a linear correlation between the antiwear property and the ratio of wearrelated hardness H′over compressive elastic modulus E was developed by Ji et al Upon the substitution of original hardness H, the correlation coefficient between the wear resistance and the H′/E ratio was Recent Progress on Wear‐Resistant Materials: Designs, Properties, 2023年7月10日 The present literature review explores the energyefficient ultrafine grinding of particles using stirred mills The review provides an overview of the different techniques for size reduction and the impact of energy requirements on the choice of stirred mills It also discusses the factors, including the design, operating parameters, and feed material properties, EnergyEfficient Advanced Ultrafine Grinding of Particles Using Also, energy consumption for a laboratory mill with fluted rolls was determined, for wheat seeds grinding with different moisture content Results are presented in the paperMATHEMATICAL MODEL TO ESTIMATE THE ENERGY CONSUMPTION
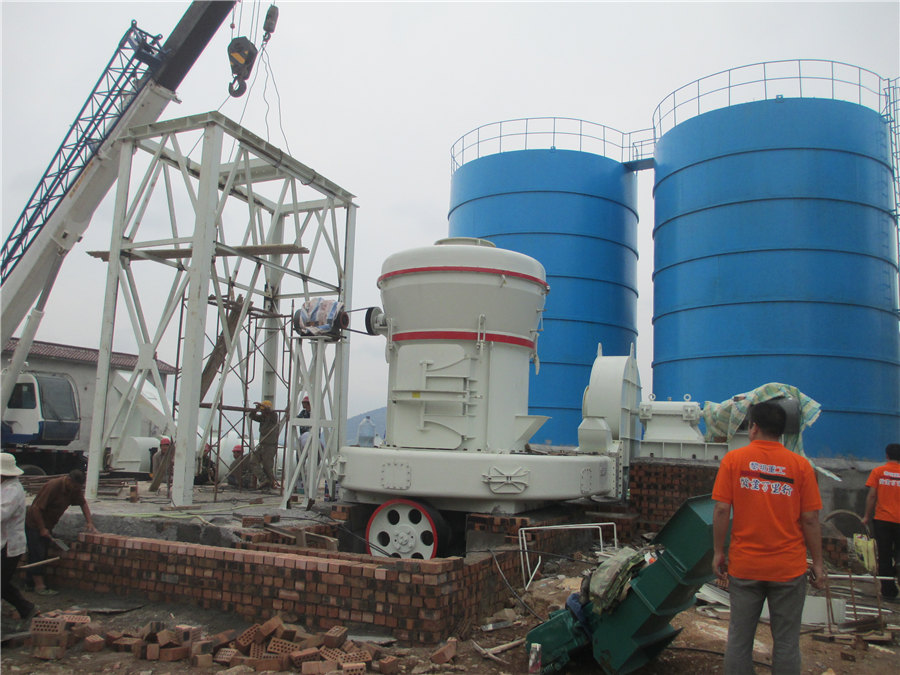
Ball mill upgrade cuts energy consumption by 25% FLSmidth
article Ball mill upgrade cuts energy consumption by 25% Upgrading an existing ball mill circuit with hydraulic roller presses and TRIBOMAX® wear surfaces achieved a 127% increase in production, at the same time as lowering power consumption by 2022年1月23日 This work concentrates on the energy consumption and grinding energy efficiency of a laboratory vertical roller mill (VRM) under various operating parameters For design of experiments (DOE), the response surface method (RSM) was employed with the VRM experiments to systematically investigate the influence of operating parameters on the energy Analysis and Optimization of Grinding Performance of Vertical