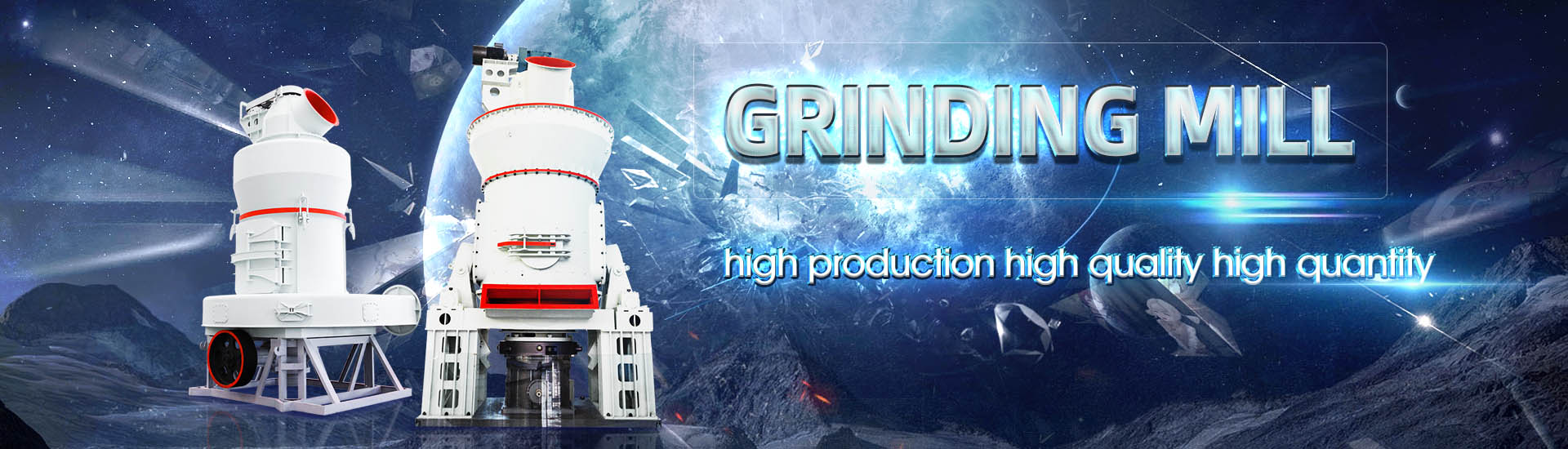
3 chemical pulp ball mill
.jpg)
Ball milling: a green technology for the preparation and
This linear homopolysaccharide is composed of glucose units linked together through β(14)glycosidic bonds6 The cellulose chains are interconnected through hydrogen bonding and Van der Waals interactions to form elementary fibrils, which further assemble into larger micro and nanofibrils about 2–10 nm thick (Fig 展开2020年4月15日 Herein, a facile/ green approach to prepare CNC with high yield and colloidal stability from bamboo fibers is presented Ball mill pretreatment can break down and open up Preparation and characterization of high yield cellulose 2023年10月27日 Grinding media play an important role in the comminution of mineral ores in these mills This work reviews the application of balls in mineral processing as a function of the A Review of the Grinding Media in Ball Mills for Mineral Processing 2021年1月1日 In this paper, the design method of three chamber ball mill is introduced Comchambered with the design of Φ 35 × 13m threechamber ball mill, the design process of ball mill is(PDF) Design of Threechamber Ball Mill ResearchGate
.jpg)
Preparation of cellulose nanofiber from softwood pulp
2015年2月27日 This paper reports the possibility of producing cellulose nanofiber from softwood pulp using a simple ball milling technique under ambient pressure and at room temperature The effects of milling conditions including 2019年1月9日 Ball milling is a simple, fast, costeffective green technology with enormous potential One of the most interesting applications of this technology in the field of cellulose is the preparationBall milling : A green technology for the preparation 2023年10月27日 Grinding media play an important role in the comminution of mineral ores in these mills This work reviews the application of balls in mineral processing as a function of the materials used toA Review of the Grinding Media in Ball Mills for Mineral 2021年1月1日 In this paper, the design method of three chamber ball mill is introduced Comchambered with the design of Φ 35 × 13m threechamber ball mill, the design process of Design of Threechamber Ball Mill IOPscience
.jpg)
Modification of biochar with highenergy ball milling:
2021年9月1日 In this work, six different biochar materials (made from pine, hemp, switchgrass, pulp sludge, wheat straw, and sugarcane bagasse) were ball milled and characterized The Ball milling is a simple, fast, costeffective green technology with enormous potential One of the most interesting applications of this technology in the field of cellulose is the preparation and Ball milling: a green technology for the preparation and 2020年9月1日 Despite these recognized advantages, biochar synthesis and applications have encountered some bottlenecks such as moderate catalytic performance, insufficient porosity and surface area, lack of facile and solvent/chemicalfree modification methods (Li et al, 2019, Tan et al, 2016)It is noted that the production of carbon nanomaterials using conventional topdown Ball milling as a mechanochemical technology for fabrication of 2020年4月15日 The moisture content of this pulp was 856 % The chemical composition of bamboo pulp in this experiment was shown in Table 1 and determined according to the standards (wt %) and the total suspension weight is 300 g The prepared pulp suspensions were pretreated in the ball mill (CSN03 from Chile (Shanghai) Mechanical Preparation and characterization of high yield cellulose
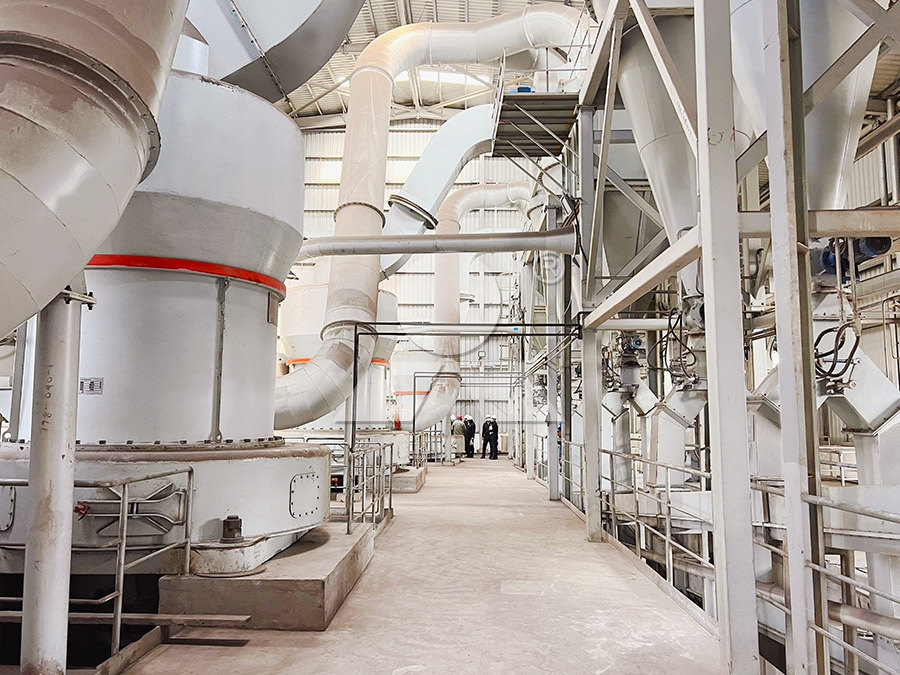
Ball milling : A green technology for the preparation
2019年1月9日 pulp by mechanochemical activation in the presence of phosphotungstic acid 39 Milling was performed for 15 and included a ball mill treatment for two hours at 300 rpm inThe formation of cellulose crystals by ball mill assisted hydrolysis was also reported by Tian and coworkers, who described the preparation of microcrystalline cellulose (MCC) from eucalyptus pulp by mercerization and subsequent ball mill treatment 44 The pulp was first treated with sodium hydroxide, then milled in the presence of the same at 450 rpm for 5 hoursBall milling: a green technology for the preparation and 2018年10月2日 Chemical pulp mills operated as biobased industries producing cellulosic fibers, As described in Sect 13, some pulp mills are nowadays dedicated to biobased products other than pulp and energy However, dedicated plants producing cellulosic ethanol from lignocellulosic materials, particularly nonwood materials, Chemical Pulp Mills as Biorefineries SpringerLink2023年10月27日 PDF The ball mill is a rotating cylindrical vessel with grinding media inside, caused by the lower pH and Fe 3+ concentration in the pulp A Review of the Grinding Media in Ball Mills for Mineral Processing
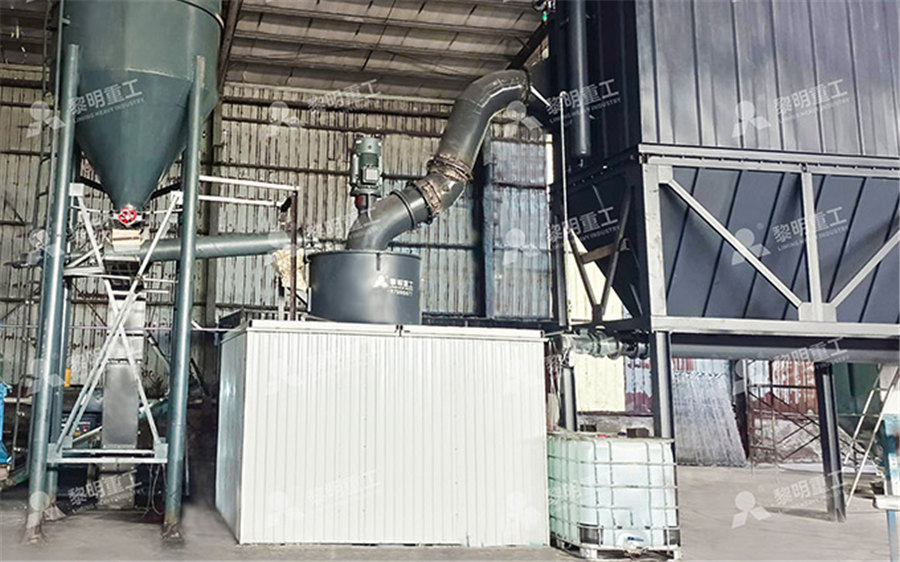
Grinding Media in Ball Mills for Mineral Processing
2023年11月24日 The ball mill is a rotating cylindrical vessel with grinding media This was among other factors caused by the lower pH and Fe 3+ concentration in the pulp obtained by the ceramic media compared to castironbased Quartz is one of the most pervasive abrasive materials in mineral processing The chemical composition, Chemical Pulp Processing: Digester Liquor Recovery Designed with pulp and paper in mind Xomox Tufline Sleeved Plug Valves are designed for handling causticized green liquor and heavy black liquor in the kraft process Knowledgeable plant personnel at sulfite and kraft mills depend on their reliable, proven performance For the most Solutions for Pulp and Paper Industries CRANE ChemPharmaTable 1 Chemical composition of typical grinding media (% wt) Adapted from [24] 211 Cast Iron Cast iron can be grey cast iron or white cast iron, but white cast irons are commonly used in Grinding Media in Ball MillsA Review ResearchGate2021年1月1日 Comchambered with the design of Φ 35 × 13m threechamber ball mill, Beijing: Chemical Industry Press, 20151:109130 Effect of impeller size on SiO 2 2 Effect of grain refinement(PDF) Design of Threechamber Ball Mill ResearchGate
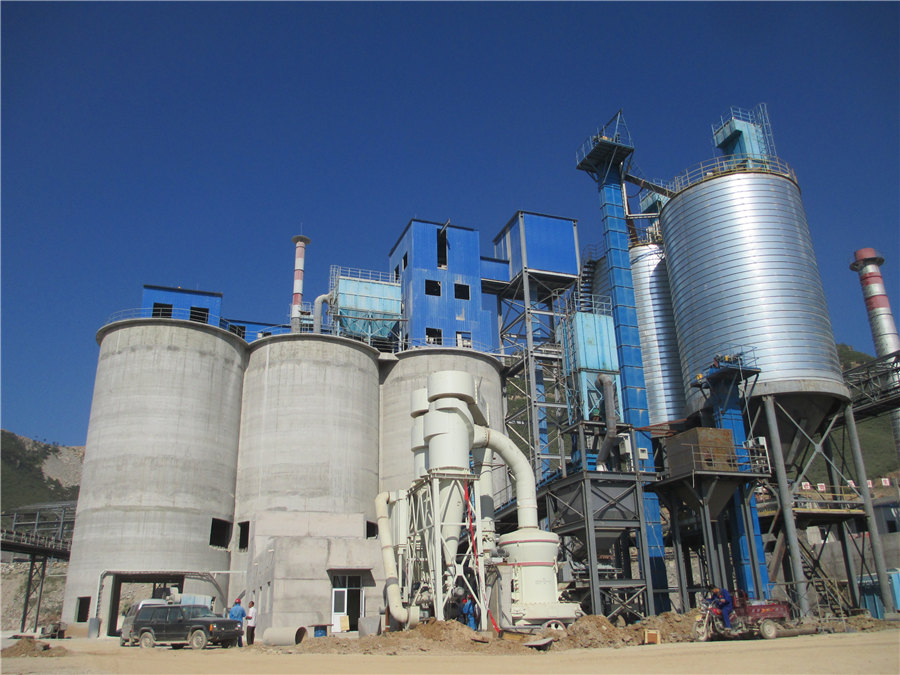
Grinding Media in Ball MillsA Review [v1] Preprints
2023年4月24日 Ball mills operate by movement and interaction between the grinding media and predicting grinding mill load behaviour,” Chemical Technology, vol 1, pp 3–6, Nov 1999 Aldrich, C Consumption of steel “Optimization of mill performance by using online ball and pulp measurements,” J South Afr Inst Min Metall 2022年2月28日 In ball mills, the abrasive and 3 Physical and chemical characteristics of the input feed, namely suspension viscosity 4 Mill geometry Optimization of mill performance by using online ball and pulp measurements J S Afr Grinding SpringerLink2020年10月29日 1 Introduction Chemical processes are the most common for obtaining pulp of cellulose fibers, among which stands out the ‘sulfate process’, commonly known as ‘kraft process’ due to the high physicalmechanical Kraft Pulp Mill Process Encyclopedia MDPI5′ x 10′ ball mill = 15 m X 3 m Ball Mill A PULP level sufficiently high to interpose a bed of pulp, chemical, ceramic, or paint industries The material is ground and mixed in one operation by rotating it together with balls, or pebbles in a hermetically sealed cylinder05 TO 15 TPH SMALL SCALE MINER’S BALL MILL
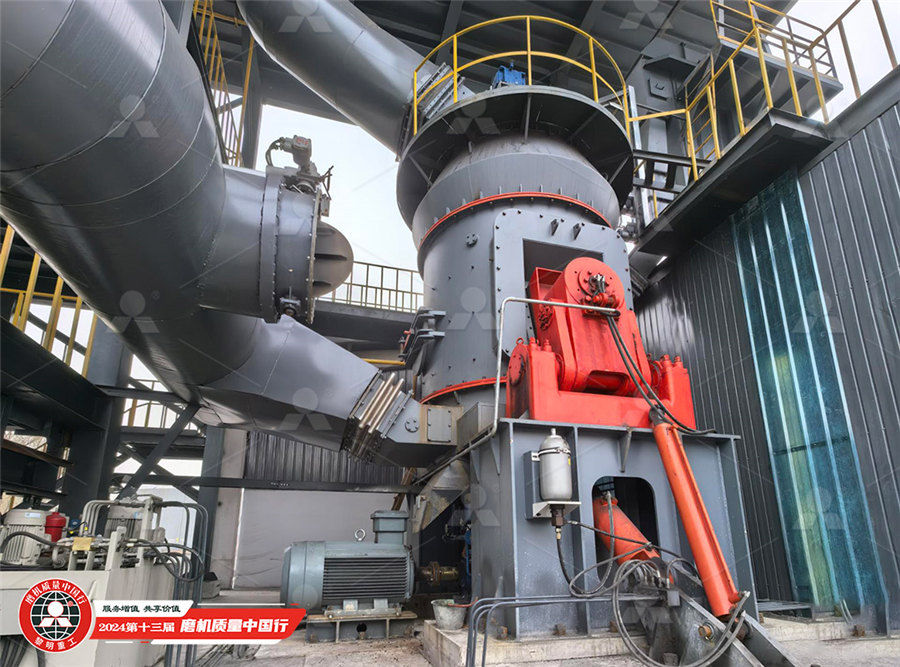
Acoustic Monitoring of Mill Pulp Densities ResearchGate
2020年8月5日 The mill acoustic sensing method has been reported to serve as an alternative means of giving some level of insight into the inmill events and dynamics using an acoustic sensor (Owusu et al 2015年4月28日 Presently, 5060 m 3 of water needed to produce a ton of paper and around 240250 chemicals have been identified in effluents, which are produced at different stages of paper making in pulp and paper industry The pulp and paper industry is typically associated with pollution problems related to high BOD, COD, toxicity, AOX, color, suspended solids, lignin Bioremediation and Detoxification of Pulp and Paper Mill 2010年3月10日 PDF Ball mills are usually the largest consumers of energy within a mineral concentrator A wide range of ball and pulp loads were tested and the findings are reported in this paper(PDF) Optimization of mill performance by using online ball and pulp 2016年1月1日 The wear of balls used during a grinding process is considered one of the losses that cause an increase in the operating cost allocated to the ball mill [21]A comparison of wear rates of ball mill grinding media
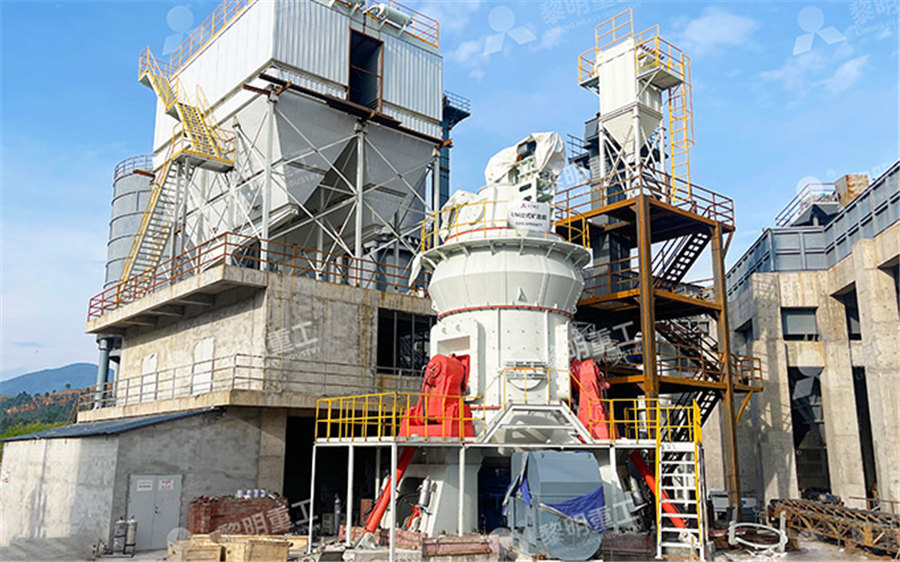
Pulp mill Wikipedia
A pulp mill in Rauma, Finland Woodchips for paper production A pulp mill is a manufacturing facility that converts wood chips or other plant fiber sources into a thick fiber board which can be shipped to a paper mill for further processing Pulp can be manufactured using mechanical, semichemical, or fully chemical methods (kraft and sulfite processes) [1]2021年4月9日 The authors found that chemical composition and lignocellulosic morphologies strongly influence methane yield Gu et al (2021) investigated the effects of wear ball mill pretreatment on food Impact of Attrition BallMill on Characteristics and Biochemical Comparison of Mechanical and Chemical Pulps Debarking Stone Groundwood Refiner Mechanical Pulp Thermo mechanical pulping (TMP) Chemi thermo mechanical pulping (CTMP) About 1/3 of pulp mass is in form of fines 3 In contrast, chemical pul ping produces intact fibres Chemical MechanicalTopic 3 Mechanical Pulpingppt University of British Columbia2020年11月22日 Pulp and paper mills generate huge amount of wastewater depending on the type of processes used in the plant whose unsafe disposal can be very hazardous to environment and human health(PDF) Characteristics and Treatment of Pulp and Paper Mill
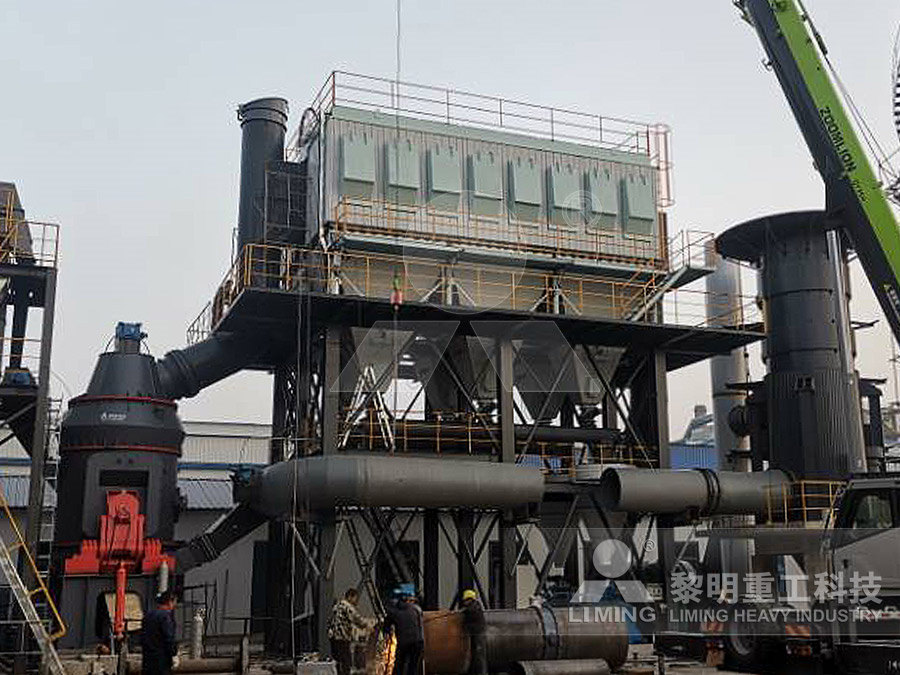
Pulp Paper PT Yokogawa Indonesia
PT Tanjung Enim Lestari Pulp and Paper (PT TEL) operates a pulp mill in Muara Enim, which is 130 km west of Palembang, the capital of Indonesia's South Sumatra province This is the only pulp mill in the world to produce highquality, bleachedhardwood kraft pulp solely from plantation grown Acacia mangium treesIf a ball mill uses little or no water during grinding, it is a ‘dry’ mill If a ball mill uses water during grinding, it is a ‘wet’ mill A typical ball mill will have a drum length that is 1 or 15 times the drum diameter Ball mills with a drum length to diameter ratio greater than Ball Mill (Ball Mills Explained) saVRee saVRee2017年3月29日 The production of chemical pulp in recent times is 180 million tons per year; while the production of eucalyptus pulp has increased intensively, especially in the southern hemisphere The pulp and paper industry has long been considered a large consumer of natural resources (wood and water) and one of the largest sources of pollution to the environment (air, Pulp Mill Wastewater: Characteristics and TreatmentAlfa Laval can help chemical pulp mill operators optimize their processes and extend equipment performance Improving energy efficiency Energy accounts for up to 30 percent of the mill production costs So it comes as no surprise that energyintensive mills Chemical pulp mill Alfa Laval
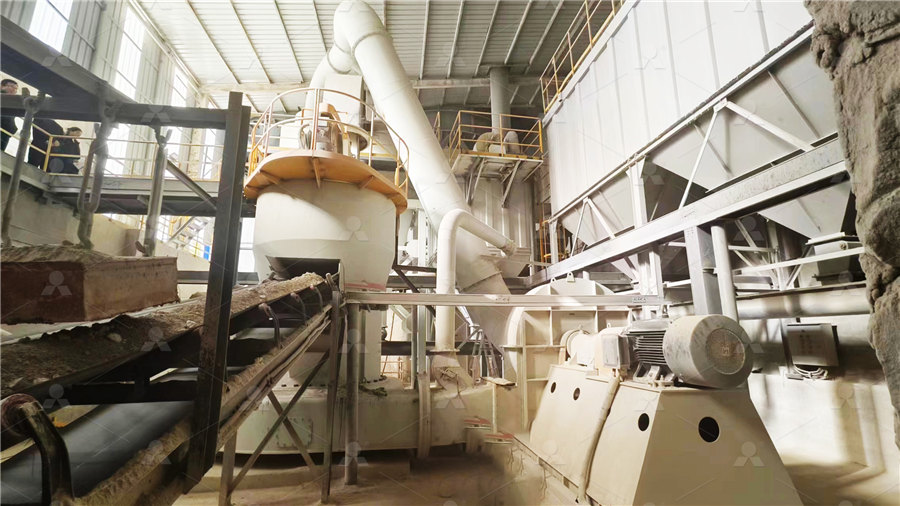
Pulp and paper mill wastes: utilizations and prospects for high
2021年4月29日 3 Process water Pulp washing/screening Dissolved material, residual chemicals, and wastewater 4 Chemicals/energy Pulp bleaching Air emissions, dissolved material, residual chemicals, and 2015年6月1日 Earlier studies using ball milling for cellulose brillation were conducted at low solids loadings of less than 5% For example, a systematic study of various parameters in ball milling on Preparation of cellulose nanofiber from softwood pulp by ball 2019年3月12日 The formation of cellulose crystals by ball mill assisted hydrolysis was also reported by Tian and coworkers, who described the preparation of microcrystalline cellulose (MCC) from eucalyptus pulp by mercerization and subsequent ball mill treatment 44 The pulp was first treated with sodium hydroxide, then milled in the presence of the same at 450 rpm for Ball milling: a green technology for the preparation and 2024年10月22日 Valmet is a fullscope supplier to pulp mills, offering advanced technology for recovering and preparing cooking chemicals, and producing energy Based on our wide experience and indepth knowledge of pulping processes, we have developed and commissioned chemical recovery plants with outstanding performance on all continentsChemical recovery for pulp mills Valmet
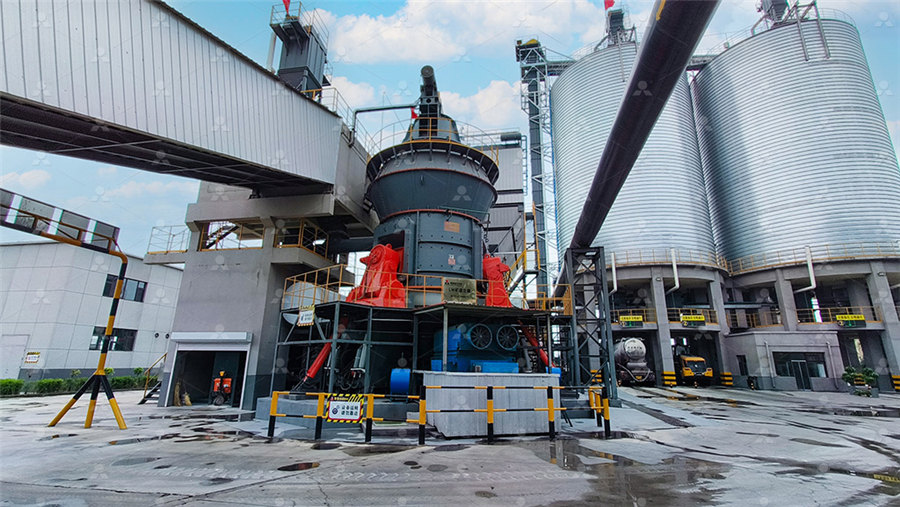
Semiautogenous grinding (SAG) mill liner design and development
2007年8月1日 The mill performance efficiency is significantly affected by multiple processing parameters such a mill speed, feed variability, ball loading, pulp density, water flow rate, mill lifter heights 2016年5月26日 The larger mills are custom built according to your requirements Whatever these are there is a C I W Ball Mill built to meet your particular problem at the right price Ball Mill Capacity Table Small Muleback Small Ball Mills 911Metallurgist1985年11月1日 Pulps containing minus 10mesh solids at high pulp densities {usually more than 55% solids by volume) have such high pulp viscosities 253 Grinding materials at such high pulp densities, in the presence of 003% of the additive, resulted in a higher than average mill torque, a more finely ground product, and a pulp of lower viscosity than those obtained while grinding in Effect of chemical additives on the dynamics of grinding media in 2016年3月21日 Pulp Densities Pulp densities indicate by means of a tabulation the percentages of solids (or liquidtosolid ratio) in a sample of pulp This figure is valuable in two ways—directly, because for each unit process and operation in milling the optimum pulp density must be established and maintained, and indirectly, because certain important tonnage calculations are Common Basic Formulas for Mineral Processing Calculations
.jpg)
The chemical pulp mill as a flexible prosumer of electricity
2023年10月1日 In this work, a reference chemical pulp mill, which is a standalone mill with a daily capacity of 2,000 ADt (airdry tonnes) of bleached market pulp, is modelled It can be operated either exclusively with softwood (spruce or pine) or in campaign mode, whereby the mill switches between periods (campaigns) of softwood pulp production and periods of hardwood • In Ohio, two pulp and paper mills place a total of almost 13 million people at risk In Tennessee, three pulp and paper mills endanger a total of 730,000 people Pulp and paper mills that continue to rely on chlorine and chlorine dioxide endanger at least 400,000 people in Florida, Louisiana, South Carolina, and WashingtonChemical Hazard Reduction at Pulp and Paper Mills93 Generally, a worn liner leads to a more compact ball load which improves the quality of ball/pulp mixing contact This leads to a better grind at a cost of a slightly higher power draw On the other hand, a new liner appeared to have a more expanded ball load, leading to poorer ball/pulp contacts and reduced power draw 33Optimisation of the secondary ball mill using an online ball and pulp 2021年11月1日 Due to the interaction between pulp, ball and mineral particles, the motion of charge is difficult to investigate under wet Although the grinding efficiency indices of the experiment 9, 12, and 15 are larger than 14, the ball mill is underloaded with a feed of 3 kg The resulting load classification is summaried in Table 2Assessing load in ball mill using instrumented grinding media
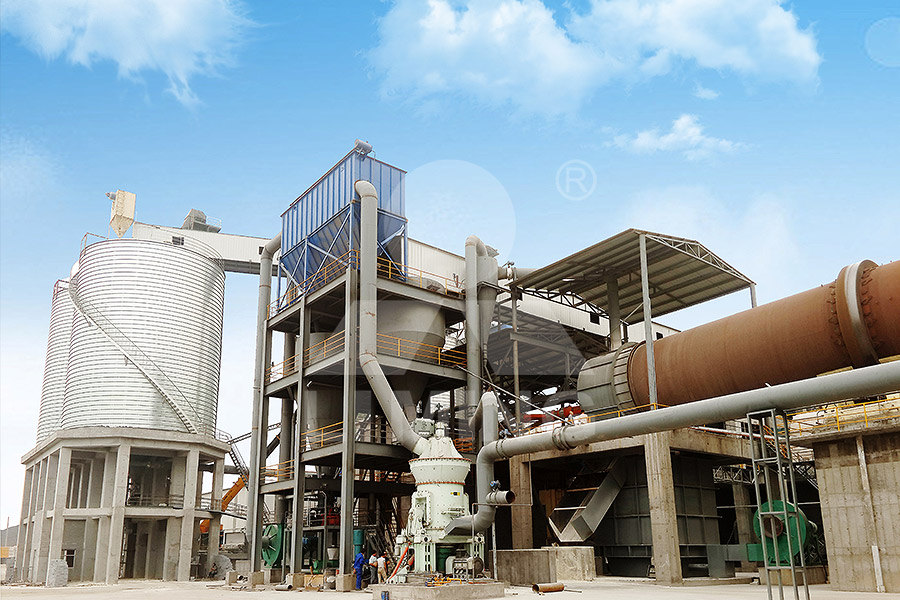
Effect of grinding media on the milling efficiency of a ball mill
2022年1月1日 The effect of ball load composition, by varying the grinding media size distribution (eg alternatively by mixing four groups of 195, 38 mm; 195, 50 mm; 38, 50 mm and 195, 38, 50 mm), on the 2023年7月13日 The Pulp Drum thickeners, also called slushers or deckers, are open rolls with filter wires that spin in a vat filled with suspension They are used for different types of feed Slushers type are used for 34% feed and deckers type are used for 56% pulp consistency feed Pulp Dewatering by Belt Pressing:Paper Making Process: From Raw Materials to Finished Products