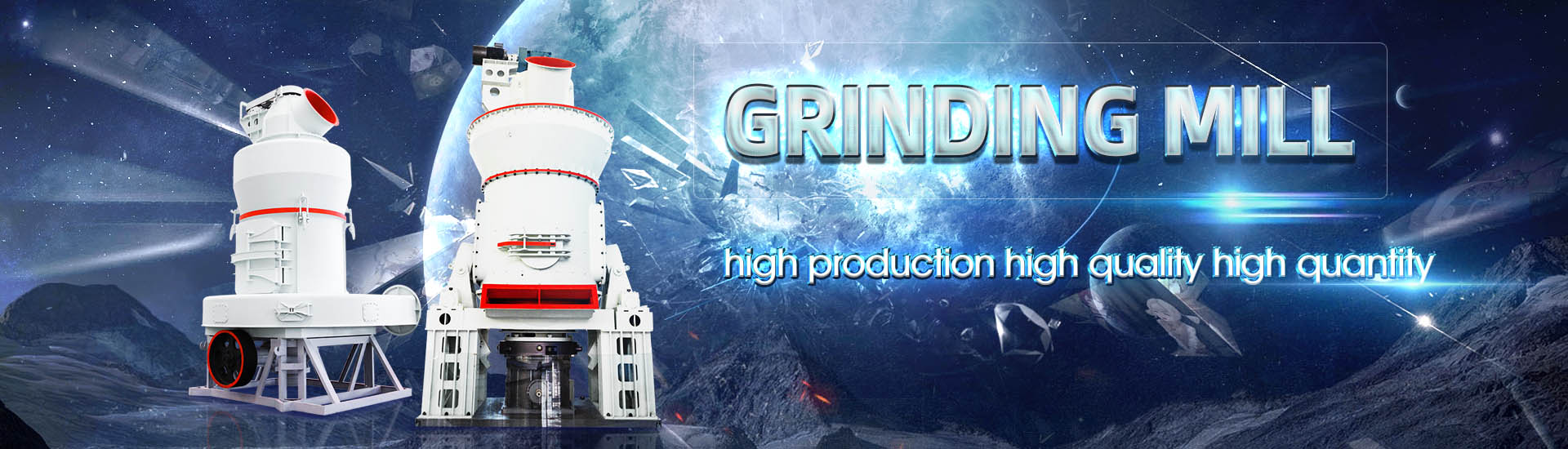
The significance and purpose of process design of cement coal mill workshop
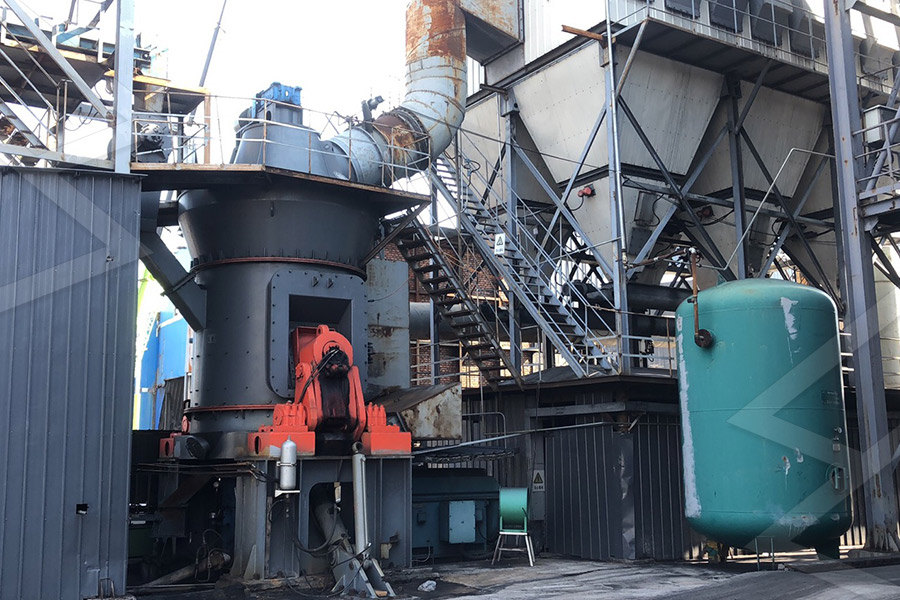
Coal utilisation in the cement and concrete industries
2013年1月1日 Coal combustion products in the form of bottom ash and fly ash derived from the use of coal in power stations is a significant element in coal’s role in the cement and concrete industries The most significant such application is the use of fly ash as a mineral additive in Mills are mechanical devices used to break different types of solid materials in small pieces by grinding, crushing or cutting In pulverised coalfired power plants, a pulveriser coal mill grinds Coal Mill an overview ScienceDirect TopicsThe coal mill system is an important part of the dry process cement manufacturing The usually used coal mills in cement plants include air swept coal mill and vertical coal millCoal Mill – Coal Mill In Cement Plant AGICO Cement Coal mill is an important component of the thermal power plant It is used to grind and dry the moisturized raw coal and transport the pulverized coal – air mixture to the boiler Poor dynamic (PDF) Modeling and Control of Coal Mill Academia
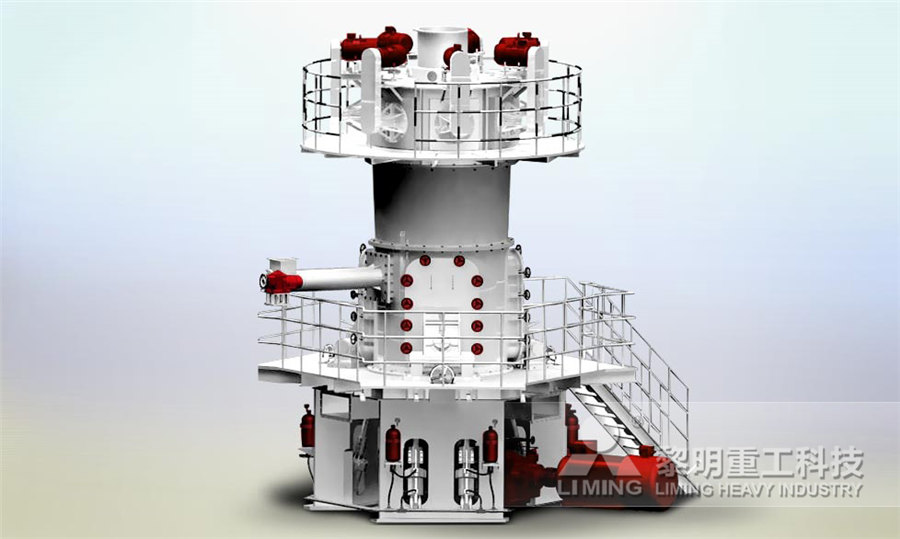
Cement Analysis and Production Information Thermo Fisher
From the coal mill to raw materials storage or the cement mill – learn more how Thermo Scientific bulk material handling equipment and PGNAA/PFTNA analyzers help optimizing the Cement Cement production is a highly energy intensive process and has traditionally depended mainly on coal as fuel Compared to a global coal production of around 37 Gt in 1999, coal use in power Coutilisation of coal and other fuels in cement kilns ICSC2021年5月11日 In this chapter, coal preparation techniques employed in the generation of clean coal for various applications are briefly discussed Presentday coal washeries are equipped Mineral Beneficiation and Processing of Coal SpringerLink2021年8月29日 A kiln for cement production typically uses coal as a fuel to heat a mixture of raw materials at 1450°C, transforming the chemical and physical components to form a new substance called a clinker – a gray pebblelike Coal and its application in the cement production
.jpg)
Coal Preparation SpringerLink
Coal preparation, which may also be called washing, cleaning or processing, is the methodology by which coal feedstocks are upgraded in order to reduce freight costs, improve utilization The wood floating on the water of Three Gorges Dam is even collected to make fuel for cement plants On the other hand, the production process of cement has always been optimizing Some cement plants can even reach 80% efficiency, The Importance of Cement and its Future2020年8月12日 VRM has been widely researched in processing of cement (Ito et al 1997;Jorgensen 2005;Wang et al 2009, Ghalandari et al 2021), coal (Tontu 2020), iron ore (Reichert et al 2015), zinc ore (van An investigation of performance characteristics and The ball mill is a traditional coal pulverizer machine, which has been widely used since it was invented In the cement plant, the new dry process cement manufacturing requires the moisture content of coal powder to be 05% ~ Coal Mill in Cement Plant Vertical Roller Mill Air
.jpg)
Fineness of CementDefinition, Significance, Measurement, Factors
2024年1月15日 The fineness of cement is defined as the particle size distribution of the cement particlesLearn all about Fineness of cement and the significance and measurement English Get Started; Exams accelerating the hydration process The significance of fineness lies in its direct impact on the early The type of mill, grinding When coal is used as fuel, the ash content and its composition should be considered in raw mix design LSF of clinker lies in the range of 9298 Higher LSF at controlled free lime content translates to better quality of clinker (high C3S), difficult clinkerization, high heat consumptionClinkerization Cement Plant OptimizationWet process kilns The original rotary cement kilns were called 'wet process' kilns In their basic form they were relatively simple compared with modern developments The raw meal was supplied at ambient temperature in the form of a slurry A wet process kiln may be up to 200m long and 6m in diameterManufacturing the cement kiln Understanding Cement2012年6月1日 grinding process and analyze several control strategies applied in the design of a control structure and the implementation of an appropriate process control method IIGrinding in Ball Mills: Modeling and Process Control
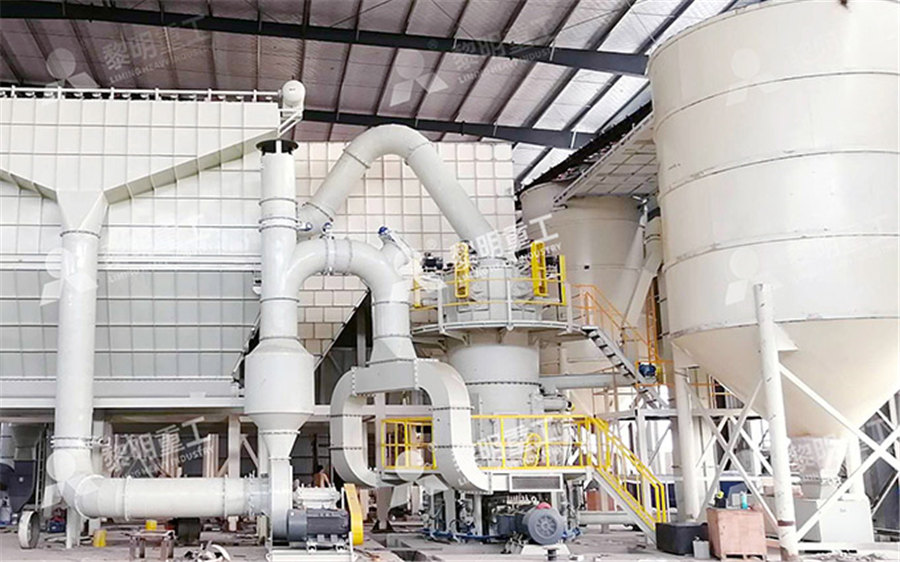
Cement Mill Process Requirement of Mill Motors Kiln Drives
Every stage has its own drive Several drives in Cement Mill Process are raw mill drives, cement mill drives, kiln drives, crusher drives, waste gas fan drives and compressor drives Requirement of Mill Motors: They should have high starting torque The starting current must be limited to a maximum of two times full load value to minimise The coal mill grinding system is an important part of the dry process cement manufacturing In cement plants, we usually adopt the air swept coal mill system or vertical mill system as the pulverized coal preparation system, which is arranged at the cement kiln head or kiln tail to provide fuel for clinker calcination However, due to the flammable and explosive Coal Mill – Coal Mill In Cement Plant AGICO Cement EquipmentVRM has been widely researched in processing of cement (Ito et al 1997;Jorgensen 2005;Wang et al 2009, Ghalandari et al 2021), coal (Tontu 2020), iron ore (Reichert et al 2015), zinc ore (van The layout of the coal mill with a rotary classifierThe gypsum controls the rate of hydration of the cement in the cementsetting process Significant amounts of electrical energy are required for milling The total power demand depends on the fineness of the grind, the distribution of particle size, and the efficiency of separation of the finely ground particlesThe Cement Production Process
.jpg)
Coal and its application in the cement production
2021年8月29日 A year, factories usually have to produce about 800,000 tons of clinker, if in the past they had to use more than 136,000 tons of 4A bran coal, now thanks to the application of the solution of using coal oxide in the production of 2021年11月17日 Portland pozzolana cement (PPC) is made by intergrinding and mixing of OPC with fly ash, Portland slag cement (PSC) is made by mixing OPC with Ground Blast Furnace Slag, and Portland composite cement (PCC) is made by mixing OPC with Fly Ash, GBFS, etc Portland limestone cement (PLC), Sulphateresistant Portland Cement, Masonry Cement, Oil Well Fundamentals of Cement Chemistry, Operations, and Quality capacity of 1 million tonnes per year and a dry process output of 12 million tonnes per year Six operation units are identified for the wet process while five units are identified for the dry process The operation units con sidered for the purpose of this work include crushing, milling, agitation, burning, grinding and bagging (Fig ures 1 Energy and Cost Analysis of Cement Production Using the Wet Stage of Cement Manufacture There are six main stages of the cement manufacturing process Stage 1: Raw Material Extraction/Quarry The raw cement ingredients needed for cement production are limestone (calcium), sand and clay (silicon, aluminum, iron), shale, fly ash, mill scale, and bauxite The ore rocks are quarried and crushed into smaller pieces of about 6 inchesHow Cement is Made Cement Manufacturing Process
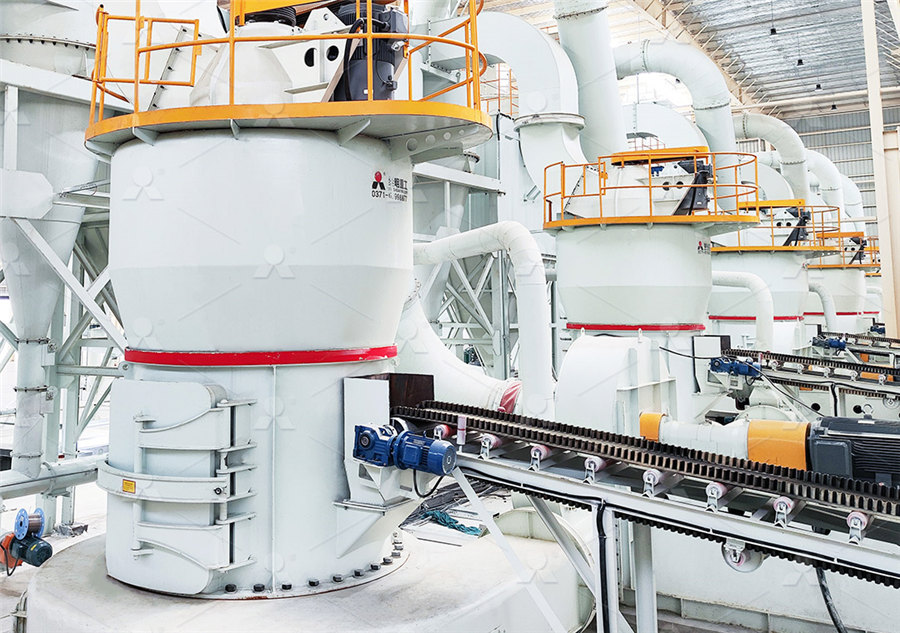
The Cement Plant Operations Handbook International Cement
EN 197 cement specification – 17 Composite cements (intergrinds and blends) – 18 Supersulphated cement – 19 Calcium aluminate cement (CAC) – 20 Shrinkagecompensating cements (SCC) – 21 ISO 9001:2000 Quality 8 Maintenance168 1 Maintenance benefits and costs – 2 Failure modes – (CMMS) – 4Raw mill is generally called cement raw mill, raw mill in cement plant, it refers to a common type of cement equipment in the cement plantIn the cement manufacturing process, raw mill in cement plant grind cement raw materials into the raw mix, and the raw mix is sent to the cement kiln to make cement clinker, next, clinker and other admixtures will be ground into finished cement by Raw mill Cement PlantVertical coal grinding mill integrates crushing, drying, grinding, powder selection and conveying; It has simple system and compact structure Vertical coal mill covers an floor area about 50% of the coal ball mill with the same specification; Coal vertical mills can work in openair environments, greatly reducing the cost of investment The design of the vertical coal mill system is simple Vertical Coal Mill for Coal Grinding in Cement Plant Power PlantA clear purpose guides the design process, ensuring that the experience of the workshop aligns with your objectives Example 1: The purpose of the workshop on deciding an important challenge could be to collectively identify the most pressing issues facing the organization and to prioritize them for future initiativesThe Design of a Workshop: A Guide to Designing Workshops
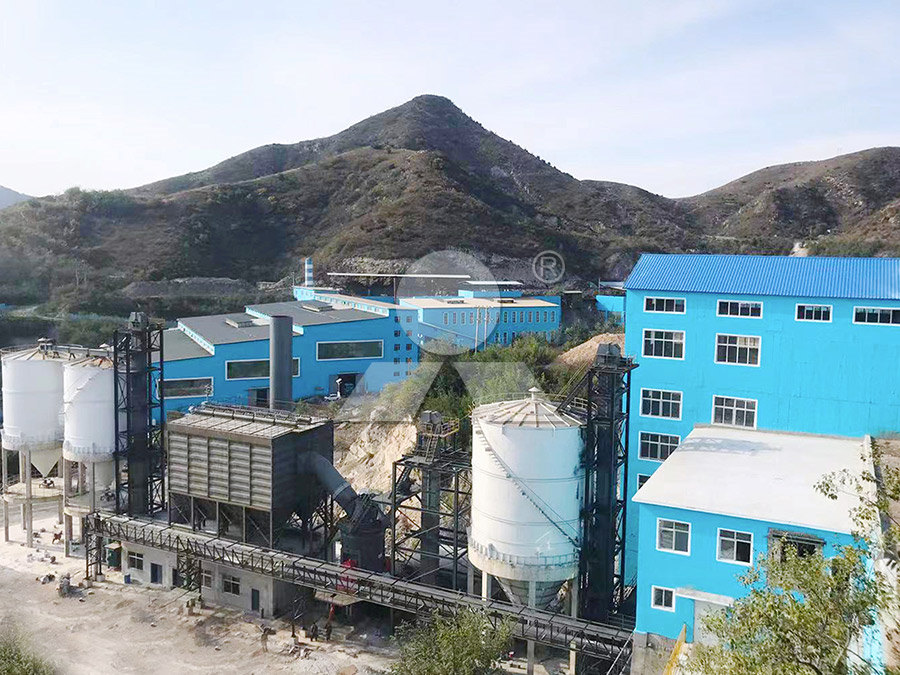
Cement Manufacturing using Alternative Fuels and the
2004年3月15日 In cement production processes, there are several models for the purpose of studying the use of alternative fuels [4, 36, 39]: phase chemistry [40], oxidation process of coal tar pitch [41 The Selection and Design of Mill Liners Malcolm Powell*, Ian Smit#, Peter Radziszewski§, Paul Cleary†, Bruce Rattray+, KlasGoran Eriksson‡ and Leon Schaeffer٭ *Mineral Processing Research Unit, University of Cape Town, Cape Town, South Africa, Anglo Research, Johannesburg, South Africa § Department of Mechanical Engineering, McGill The selection and design of mill liners Academia2013年1月1日 This study assesses the use of hightemperature Xray diffraction (HTXRD) to study the mass transfer of raw meal constituents towards forming clinker phases and the occurrence of free CaO, also Modelling the cement process and cement clinker 2023年12月23日 The coal mill fan is usually installed on the top of the coal mill, and its inlet is connected to the coal mill discharge port, and its outlet is connected to the furnace The coal mill fan is driven by a motor, and the motor drives the fan impeller to rotate, which generates centrifugal force to suck in air from the inlet and blow it out from Centrifugal Fans in Cement Industry: Crucial Roles Techflow
.jpg)
An Experimental Study of the Road Performance of Cement Stabilized Coal
2021年8月20日 Aiming to identify the possible problems of coal gangue as a pavement base, an unconfined compressive strength test, a splitting test, a freeze–thaw test, and a drying shrinkage test of cement 2019年11月17日 As part of this chemical mix design, allowance is made for ash from the fuel, which in coal firing, becomes part of the clinker Coal ash contains the same oxides found in the raw materials After the mixture of raw materials has been properly proportioned and ground to suitable fineness, the resulting raw mix becomes kiln feedClinkering Process in Portland Cement Manufacturing2021年3月9日 The effects of process variables such as aspect ratio, watercement ratio and cement content were investigated using the central composite design of response surface methodologySimulation and Optimization of an Integrated Process Flow Sheet By understanding these aspects, readers can gain a comprehensive understanding of ball mill technology and its significance in various industrial processes Ball Mill Working Principle The working principle of a ball mill is based on the impact and attrition between the balls and the grinding mediaBall Mill Grinding Machines: Working Principle, Types, Parts
.jpg)
Prediction of Loss on Ignition of Ternary Cement Containing Coal Bottom
2019年8月31日 The effect of CBA/CBAL ratio and the cement replacement on the Loss on ignition (LOI) of ternary cement blends was investigated using central composite design approach in the prediction of LOI of 2014年3月1日 All content in this area was uploaded by Dimitris Tsamatsoulis on Apr 02, 2014Optimizing the control system of cement milling: Process at the mill outlet The margin on raw mill fans is typically lower: 10% on volume and 20% on pressure The raw mill fan is of large capacity and its specifications are determined by the mill characteristics The cement mill and coal mill are similar to the raw mill requirements Main filter fan The main filter fan (which evacuates the rawNarayana Jayaraman and Francisco Benavides, PEC Consulting,Safe operation of coal grinding systems: Raw coal silo protection against fire and explosions Safe operation of coal grinding systems: Raw coal yard management The purchasing process for coal grinding systems needs changes Talk at a virtual seminar, November 2023 Accept the probability that the fire and explosion safety of your coal grinding system is nothing more than a mirageOptimisation of coal mill systems, with fire and explosion
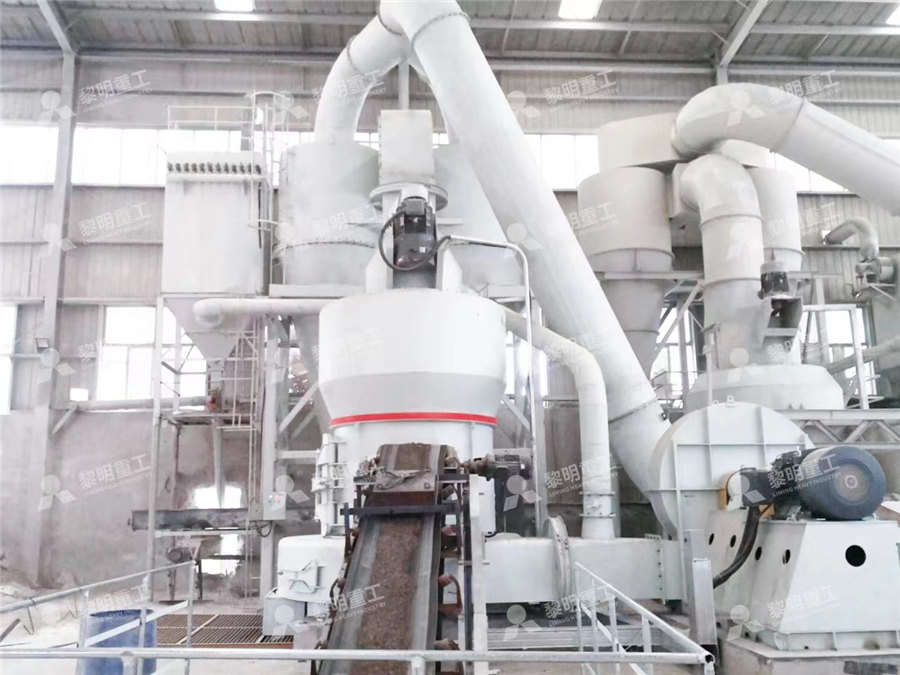
Potential of decarbonized coal gasification residues as the
2021年2月1日 For instance, Zuzhong Li studied the structural characteristics and composition of hydration products of coal gasification slag mixed cement and lime[12] According to the results, coal gasification residues has a certain pozzolanic activity, but the residual carbon can hinder the cementitious reaction between slag and cement2023年1月1日 The utilization of coal in the cement and concrete industries takes three basic this measure is somewhat meaningless if lignite is being considered Most coal mill designs are based upon a 50–55 HGI design point Industrial and process furnaces – Principles, design and operation, ButterworthHeinemann, Oxford (2008), pp Coal utilization in the cement and concrete industriesA 10 MW cement mill, output 270 tonnes per hour A cement mill (or finish mill in North American usage [1]) is the equipment used to grind the hard, nodular clinker from the cement kiln into the fine grey powder that is cementMost cement is currently ground in ball mills and also vertical roller mills which are more effective than ball millsCement mill Wikipedia2019年1月1日 The purpose of this article is to review the aspects related to cement chemistry, more particularly to the process of clinkerization in the cement rotary kilnModeling of cement clinker chemistry and engineering of cement
.jpg)
Impacts of Cement Production on the Environment with Practical
weighting 50 kg each Most cement is used in concrete as an essential material in the construction industry [38, 40] There are two types of processes used in cement production: the dry process and the wet process [38] • Dry process: In this process, the raw materials are dried using different types of dryers or air separators,2021年1月1日 In dry process technology, crushed limestone and raw materials are ground and mixed without addition of water Dry and semiwet processes are more energyefficient The wet process requires 028 tons of coal and 110 kWh to produce one ton of cement, while the dry process requires only 018 tons of coal and 100 kWh of energy [4]Review on vertical roller mill in cement industry its performance Our ATOX® Coal Mill is a compact vertical roller mill that can grind almost any type of raw coal The coal mill utilises compression and shear force generated between the large rollers and the rotating table to crush and grind raw coal, removing the need for a separate piece of equipment for crushing The coal mill can also grind petroleum ATOX® Coal Mill FLSmidth CementManufacture Process of Cement to grinding mills where they are completely mixed and the paste is formed, ie, known as slurry The grinding process can be done in ball or tube mill or even both Then the slurry is led into collecting The kiln is heated with the help of powdered coal or oil or hot gases from the lower end of the kiln Manufacture of Cement Materials and Manufacturing Process of