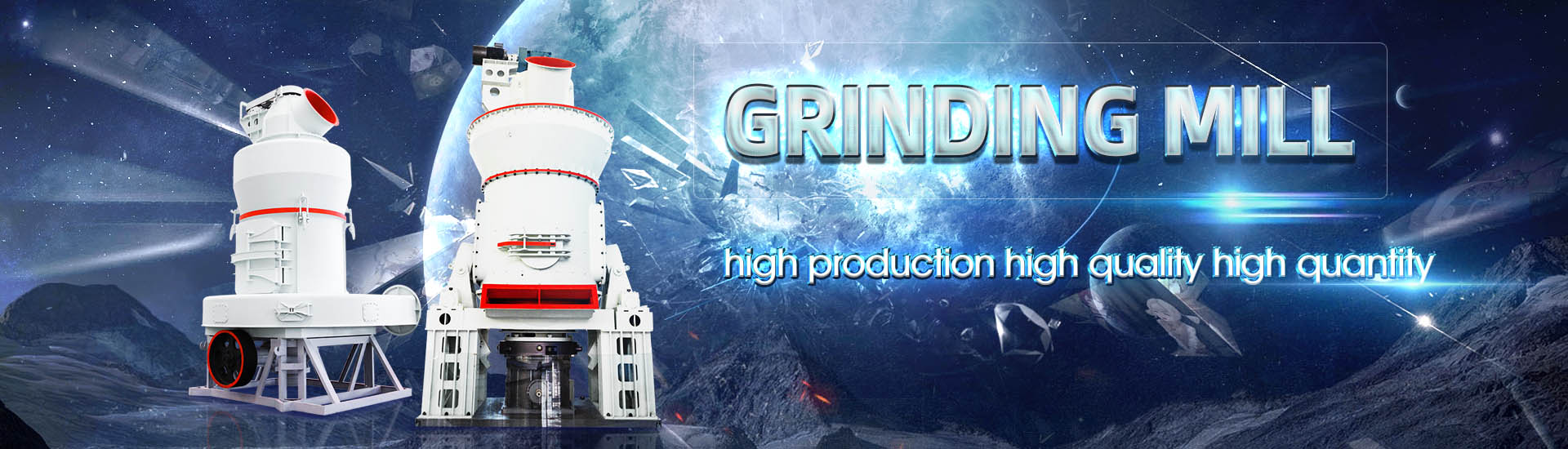
Sinter particle density
.jpg)
Sintering Wikipedia
Most, if not all, metals can be sintered This applies especially to pure metals produced in vacuum which suffer no surface contamination Sintering under atmospheric pressure requires the use of a protective gas, quite often endothermic gas Sintering, with subsequent reworking, can produce a great range 展开2016年1月7日 Sinter density changes with a log–log relationships to sintering time Initially, surface area is eliminated as bonds grow between contacting particles Grain boundaries form Sintering Trajectories: Description on How Density, Surface Area, Mass transport is the underlying mechanism of sintering Mass transport is driven by the desire of the system to reduce the total interface energy and the energy of the particles/grains Sintering theory EPFLSintering is a manufacturing process used for making various parts from metal or ceramic powder mixtures Sintering can be defined as the thermal transformation of bulk materials into Sintering an overview ScienceDirect Topics
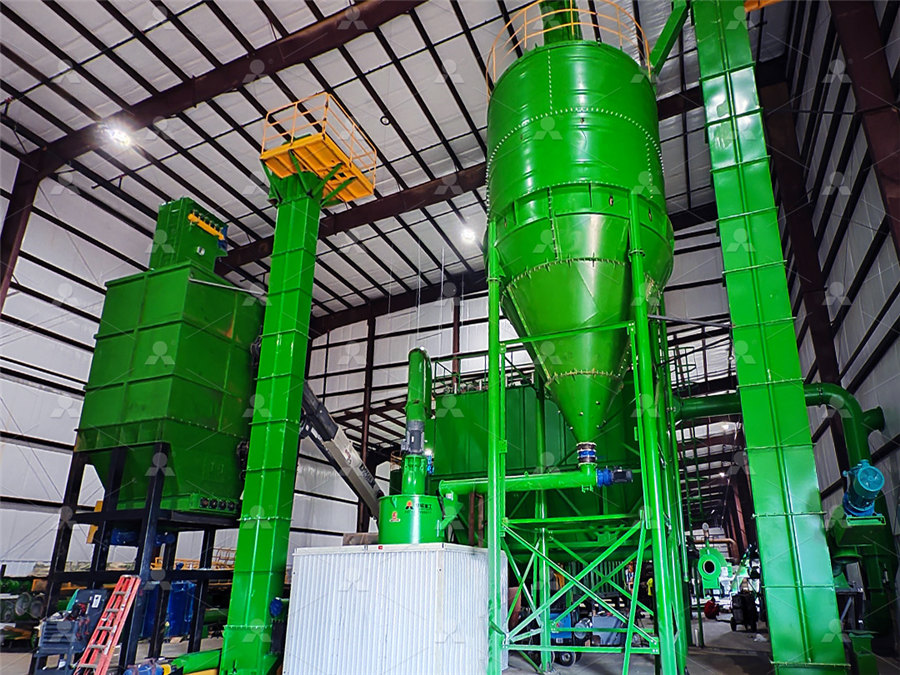
Revealing process and material parameter effects on Nature
2024年3月4日 Sintering is an important processing step in both ceramics and metals processing The microstructure resulting from this process determines many materials properties of 2024年4月19日 Sintering plays a vital role in transforming loose or bonded powder particles into a fully dense, structurally sound metal part This chapter highlights the key aspects of solid Principles of SolidState Sintering Wiley Online Library2010年1月1日 Sintering of crystalline materials can occur by at least six mechanisms or paths: vapor transport (evaporation/condensation), surface diffusion, lattice (volume) diffusion, grain Kinetics and mechanisms of densification ScienceDirect2016年1月7日 Small particles, longer sintering times, and higher sintering temperatures increase sintering densification and improve properties For example, traditional ferrous Sintering Trajectories: Description on How Density, Surface Area,
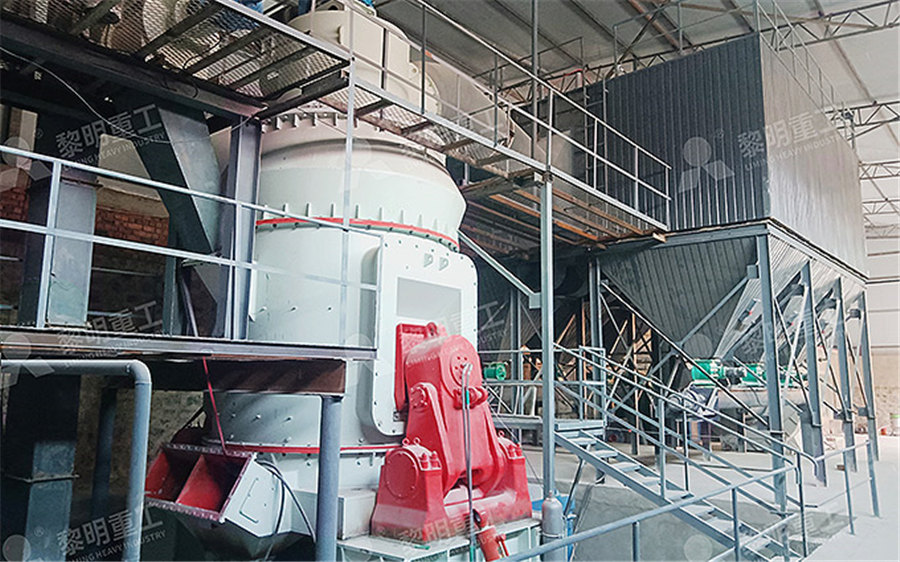
Multicomponent alloys designed to sinter Nature
2024年9月13日 The reactions involve rapid reorganization of matter to full density in cycles up to just 1200 °C, while conventional Ni alloys sintered in the solidstate require about ten times 2021年1月7日 During the sintering densification and grain growth, there are three main stages: particle contact, forming inner pores, and particles combination and inner pores eliminationSintering densification behavior and kinetic mechanism of nano Sintering is a manufacturing process used for making various parts from metal or ceramic powder mixtures Sintering can be defined as the thermal transformation of bulk materials into compact solids at temperatures below their melting point [1–4]The main phenomenon is solid state diffusion, which occurs along the different interfaces of the crystals and through any vacanciesSintering an overview ScienceDirect Topics2024年4月19日 It also explores the role of powder characteristics, such as particle size, shape, and distribution, in influencing sintering behavior Overall, this chapter provides a concise overview of the principles governing solidstate sintering in metal additive manufacturing and its implications for achieving highquality metal partsPrinciples of SolidState Sintering Wiley Online Library
.jpg)
Automated Optical Image Analysis of Iron Ore
2021年5月25日 Density segregation during sample mounting represents a significant problem in the preparation of mounted particle samples for OIA due to the large density differences between different sinter phases, eg, hematite 2024年9月13日 In this work, the authors advance the viewpoint that powder alloys yield better processability and final properties, when they are designed from materials science principles to sinter quickly and Multicomponent alloys designed to sinter Nature2021年3月1日 Similarly, the minimum and maximum possible values of the effective particle density for sinter particles obtained by repeating the experiment three times are found to be 3041 ± 20 kg/m 3 and 3477 ± 10 kg/m 3 The sinter density values used in literature as shown in Table 6 lie within this rangeQuantitative DEM simulation of pellet and sinter particles using Changes in sinter density results were not significant, indicating that the changes in bed bulk density did not have a significant effect on sinter porosity The study was then extended to include a comparable blend and two hematite blends of higher bulk density Decreasing green bed bulk density, bed shrinkage and sinter density did not have a Changing Bed Bulk Density and other Process Conditions during Iron
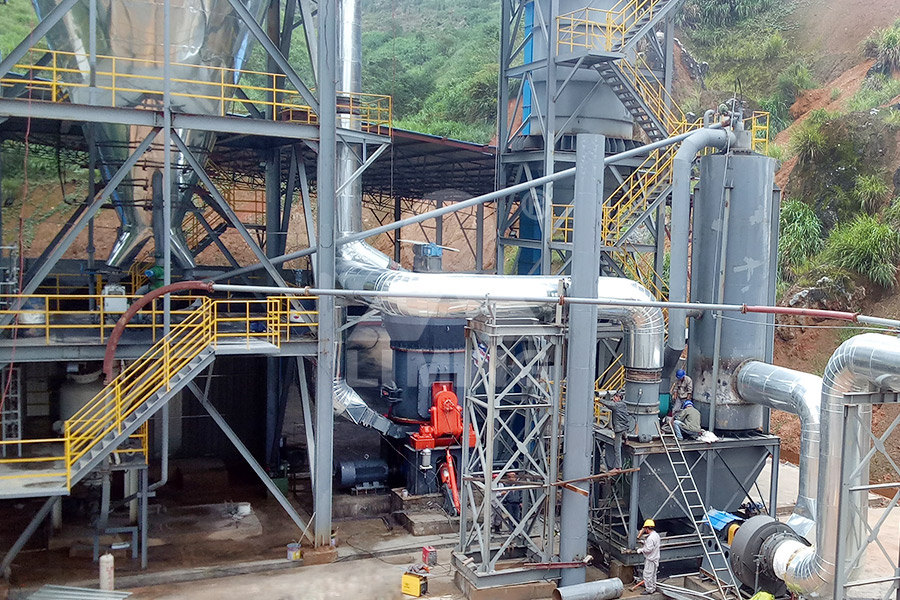
Sintering Temperature an overview ScienceDirect Topics
The scaling law states that the time required to sinter powders with particle radii of R 1 and R 2 is proportional to the ratio of the particle radius On the other hand, the finer the particle sizes, the lower the green density of powder compacts, assuming the compaction pressure is the same It should be noted, 2017年6月1日 This can be attributed to the inherently low green density and the constraint on powder particle size imposed by challenges in recoating fine powders Once depowdered, the green part is thermally treated to burn off the binder and sinter the powder particles together to obtain final density and strength Fig 1 View large Effect of Particle Size Distribution on Powder Packing and 2024年11月1日 Researchers have recently proposed advanced dieattach technologies suitable for hightemperature applications, named transient liquidphase sintering (TLPS) technology [12], [13] and lowtemperature silver (Ag) sinterjoining (LTASJ) technology [14], [15]These technologies exhibit high bonding strength, enhanced electrical and thermal conductivity, and Lowtemperature copper sinterjoining technology for power Particle Density Measures Conventional Press and Sinter •After the metallic powders have been produced, the conventional PM sequence consists of three steps: 1 Blending and mixing of the powders 2 Compaction pressing into desired part shape 3 Sintering heating to a temperature below thePowder Metallurgy PDF
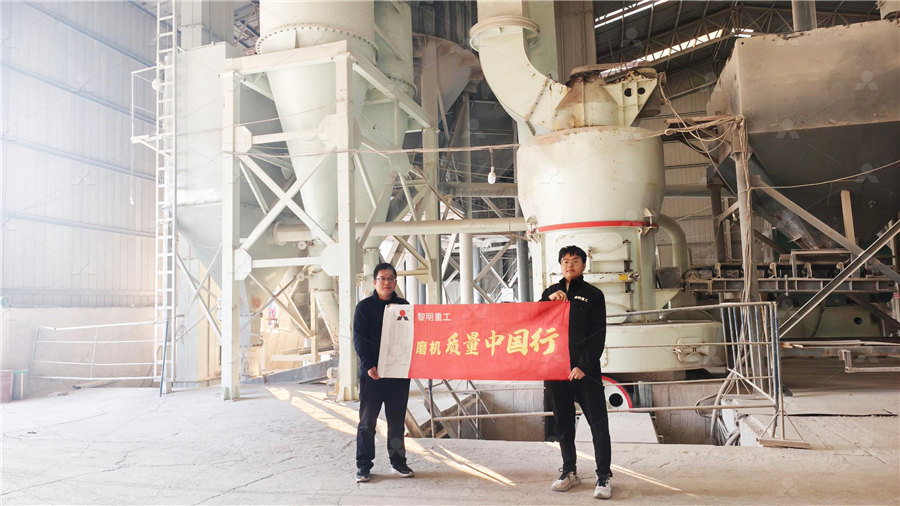
19: Bulk Density, Particle Density, and Porosity
Particle density is approximated as 265 g/cm3 , although this number may vary considerably if the soil sample has a high concentration of organic matter, which would lower particle density, or highdensity minerals such as magnetite, garnet, hornblende, etc Porosity, the percent by volume of a soil sample not occupied by solids, is directly 2020年10月1日 Download Citation Sinter bonding and formation of a nearfulldensity bondline at 250 °C via addition of submicrometer Cu particles to micrometer Agcoated Cu particles Pressureassisted die Sinter bonding and formation of a nearfulldensity 2021年12月7日 We present an approach to efficiently increase the green density of binder jetted alumina parts by optimized slurry infiltration, which also leads to a significant increase in the sintered density In a first step, alumina parts were fabricated via binder jetting, using a 20µmsized alumina powder, yielding relative green densities of about 47–49%Improved green and sintered density of alumina parts fabricated 2022年5月11日 It has been reported that bimodal powder mixtures can improve powder spreading in terms of Hausner ratio, powder bed density, and sintered density compared with the unimodal powders 3, 4 With optimized powder recoating mechanism, fine copper powder with average particle size of ~5 μm results in improved tensile properties compared with coarser Surface chemical and geometrical properties of pure copper
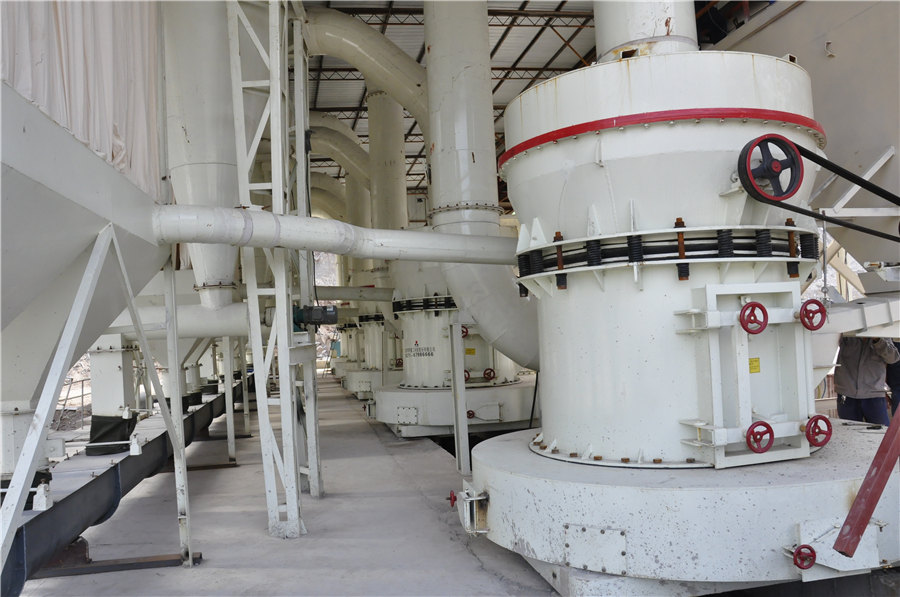
(PDF) Microstructural and sliding wear behavior of SiCparticle
2015年4月25日 Microstructural and sliding wear behavior of SiCparticle reinforced copper matrix composites fabricated by sintering and sinterforging processes April 2015 Journal of Materials Research and 2022年9月29日 Recently, Clares et al (107) proposed a bimodal particle size distribution strategy that can significantly enhance the density and mechanical properties of BJprinted objects, providing an Increasing density and mechanical performance of binder jetting 2020年3月15日 Particle density was measured three times by a pycnometer (Micrometrics AccuPyc1340), which is based on Archimedes principlegas expansion replacement method Sinter Coke; Mean particle size (mm) 14: 11: 10: Number of particles: 5000: 5039: 9911: Time step (s) 1 × 10 −5: 4Measurement and simulation validation of DEM parameters of 2018年10月15日 This work relates sintering theory with process outcomes For this, commercially pure titanium was deployed to study the effect of powder size distributions on green and sintered part qualities (bulk density, relative density, particle size, pore size, sinter neck size)Sinter structure analysis of titanium structures fabricated via
.jpg)
Die Attachment by Extremely Fast PressureAssisted Sintering
2021年3月5日 Abstract To achieve a sinter bonding process of powder devices for the formation of a bondline with hightemperature mechanical sustainability and superior thermal conductance, the bonding between a Cufinished die and substrate was performed at 300 °C in air by using a paste containing 200 nm Cu particles and a reducing solvent For the sinter bonding at 5 MPa, 2023年2月1日 Weight fraction, skeletal density with moisture of each particle type used for building the sinter green bed data Volume fraction is calculated from weight fraction and density Experimental result of iron ore is the summation of G1–G3, and fluxes are the summation of limestone and dolomiteParticle classification of iron ore sinter green bed mixtures by 3D 2020年2月1日 The particle density used in DEM was the apparent density, and apparent densities of pellet and sinter were measured by drainage method as indicated in Fig 5 Measurement and simulation validation of DEM parameters of 2009年6月24日 The pressandsinter method of producing net shapes was applied to titanium alloys The quantitative effects of the particle size of titanium and Ti6Al4V powders on the green and sintered densities were examined Most powders were pressed at 100 to 800 MPa and sintered under vacuum at 1100 °C, 1200 °C, or 1300 °C for 2 hours The green density was Some Effects of Particle Size on the Sintering of Titanium and a
.jpg)
(PDF) Development of an automated single particle impact tester
2022年1月1日 Standardized tests for sinter strength are carried out with bulk samples, but for a detailed determination of breakage behavior and discrete element simulations single particle tests are necessary2020年3月1日 The results are an initial report on the use this technique to sinter graphite under moderate conditions that may support small to moderatescale technical production needs that require lowcost, highpurity, and highdensity graphite Graphical abstract (224080 MPa) The particle size distribution is centered around 62 Densification of graphite under high pressure and moderate Particle Size Sinter Density (g/cm 3) 2100oF 2300oF 2350oF 2400oF 2450oF Fig 6: Density results for as sintered samples The density results for the 90%10µm samples are in the range 956 98% of theoretical and somewhat lower than the levels obtained for the other particle size ranges Densities in excess of 98%Effect of Particle Size Distribution on Processing and Properties of 2020年3月13日 While particle size (or size distribution) is one of the key factors influencing packing density, it cannot fully explain the arrangements illustrated in Fig 1By decreasing the particle size, below approximately 100 \(\upmu \mathrm{m}\), packing density can be changed considerably [1, 9]Due to the decrease in particle size, the specific surface area increases A discrete element study of the effect of particle shape on
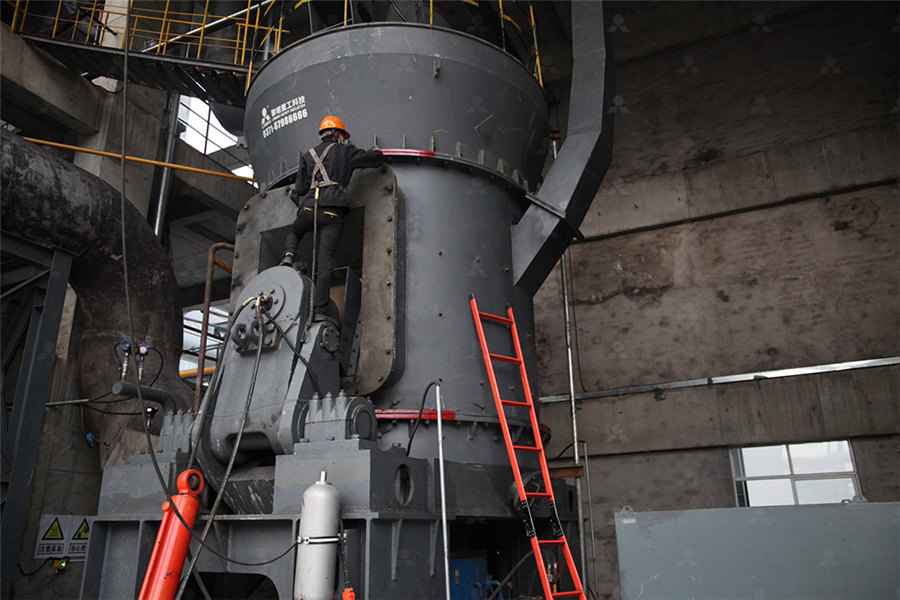
Modeling and Simulation of Sintering Process Across Scales
2023年3月20日 As for the cosintering of multilayer ceramic capacitors (eg, Ni/BaTiO \(3\)), a parametric study based on DEM simulations reveals the influence of green density, heating rate, and thickness, nickel particle rearrangement, and nonsintering inclusions on microstructure features of the final sintered electrode2021年7月1日 The fast sinter bonding and nearfull density formation are mainly attributed to the initial strong contact between the particles and the particle rearrangement behavior by the sliding deformation Die sinter bonding in air using Cu@Ag particulate preform and rapid In addition, the effect of pseudoparticle size and bulk density on flame front speed were evaluated as 55% and 41%, respectively 1Introduction Sinter productivity strongly depends on the sinter permeability In this report, from the viewpoint of the bulk density in sinter packed beds and the pseudoparticle size after mixing and granulaImprovement of Sinter Productivity by Adding Return Fine on Raw 2024年3月4日 Based on prior work 19, the density evolution of 3D phasefield simulations of solid state sintering does not change substantially after more than 262 particles are contained within the green body Revealing process and material parameter effects on Nature
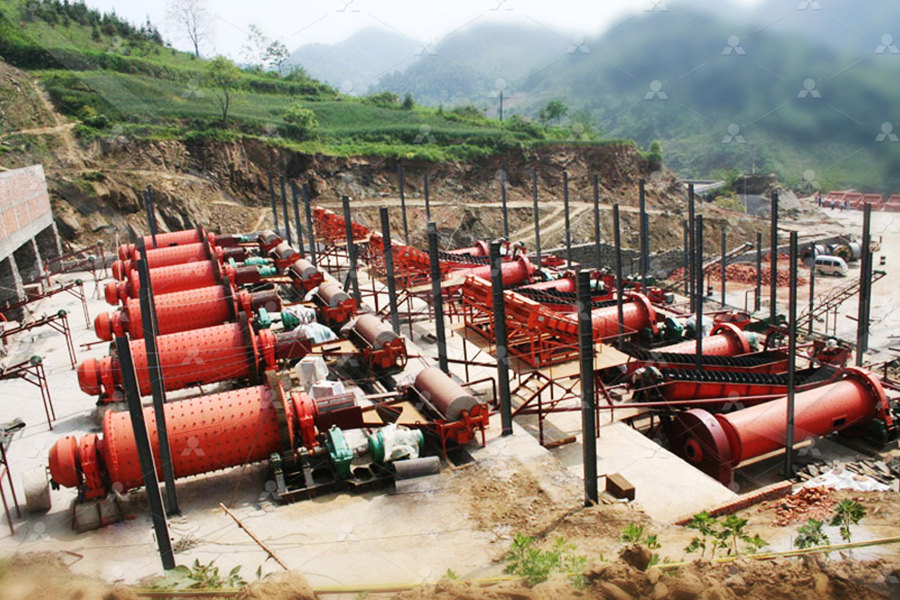
Interval prediction of sinter screening index based on gate
DOI: 101177/ Corpus ID: ; Interval prediction of sinter screening index based on gate recurrent unit and kernel density estimation algorithm @article{Kang2024IntervalPO, title={Interval prediction of sinter screening index based on gate recurrent unit and kernel density estimation algorithm}, author={Zengxin Kang and Zhaoxia 2024年7月1日 Each sinter particle size was randomly determined within the studied particle size range (21) ε = 1 − ρ b ρ p where ρ b is the particle bulk density in the sinter fixed bed and ρ p is the sinter particle density Each measurement work was repeated for three times and then the average packing voidage was obtainedCoupled simulation of fluidparticle interaction for large complex A full description of microstructure development must include the role of green density Green density effects are also important in understanding processingrelated defects Green density inhomogeneities on a microscopic scale have recently figured in models of the development of strengthlimiting flaws in ceramics [1,2]The Influence of Green Density upon Sintering SpringerLinkBulk density, particle density, and porosity are three soil physical properties exemplifying the relationships among the soil phases The volume of voids in soil is related to the percentages of sand, silt and clay (soil texture) and to the arrangement of these soil particles soil structure52: Bulk Density, Porosity, Particle Density of Soil
.jpg)
Effect of particle size distribution on the packing of powder beds:
2020年9月1日 Recent advancements have reduced the dependence of AM part quality on the density of the packed particle bed but the packing is still important for considerations such as thermal conductivity of Powder bed AM methods rely on creating a thin bed of powder on which a laser or electron beam is used to sinter or melt the powder in a 2021年9月1日 The fast sinter bonding and nearfull density formation are mainly attributed to the initial strong contact between the particles and the particle rearrangement behavior by the sliding deformation of sintered Ag after dewetting of the Ag shells on the Cu core particles during the pressureassisted bondingDie sinter bonding in air using Cu@Ag particulate preform and We return to this point later in section 5 Similarly, the minimum and maximum possible values of the effective particle density for sinter particles obtained by repeating the experiment three times are found to be 3041±20 kg/m3 and ~3477±10 kg/m3 The sinter density values used in literature as shown in table 6 lie within this rangeQuantitative DEM simulation of pellet and sinter particles using 2020年6月1日 A high initial surface area enables surface diffusion to form sinter bonds at particle contacts with little densification [95] The integral work of sintering model captures green density, particle size, heating rate, peak temperature, and hold time into a single parameter that enables prediction of densificationTitanium sintering science: A review of atomic events during
.jpg)
Sintering density of the different particle size distributions and
For instance, the effect of mean particle size on the green density at the layer thickness of 30 μm and bed temperature of 40 °C is shown in Fig 2a