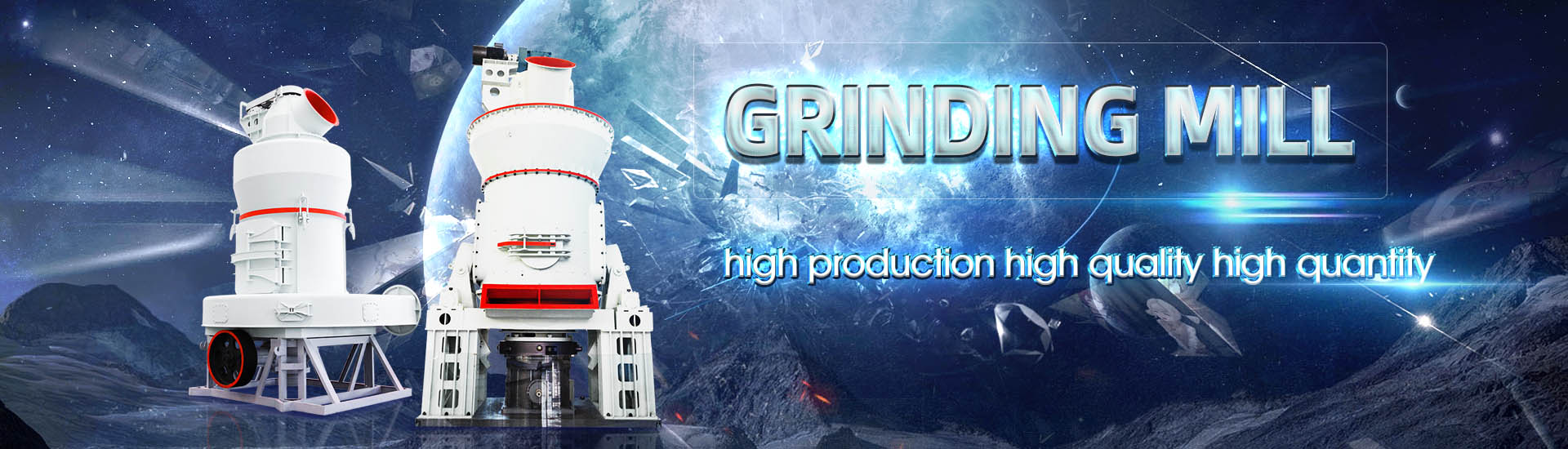
The output of the ore grinding mill is less than 20mm
.jpg)
Ore Grinding SpringerLink
2023年7月20日 According to the different grinding medium, the grinding mill is divided into three types: (1) ball mill – it is used widely, and almost all materials can be triturated by ball mill; (2) rod mill – its efficiency is relatively high with the feeding particle size less than 30 mm and the 2017年3月4日 process when size reduction of below 520 mm is needed Grinding is a powdering or pulverizingSIZE REDUCTION BY GRINDING METHODS2024年9月1日 Fine grinding is a milling method of crushing materials to less than −01 + 001 mm by using grinding, impacting, shearing and other forces within the mill (Kumar et al, Effect of different mills on the fine grinding characteristics and 2023年4月13日 Pebble mill is a type of grinding equipment that uses gravel as a grinding medium In the metal ore beneficiation industry, gravel used as a grinding medium generally Pebble Mill SpringerLink
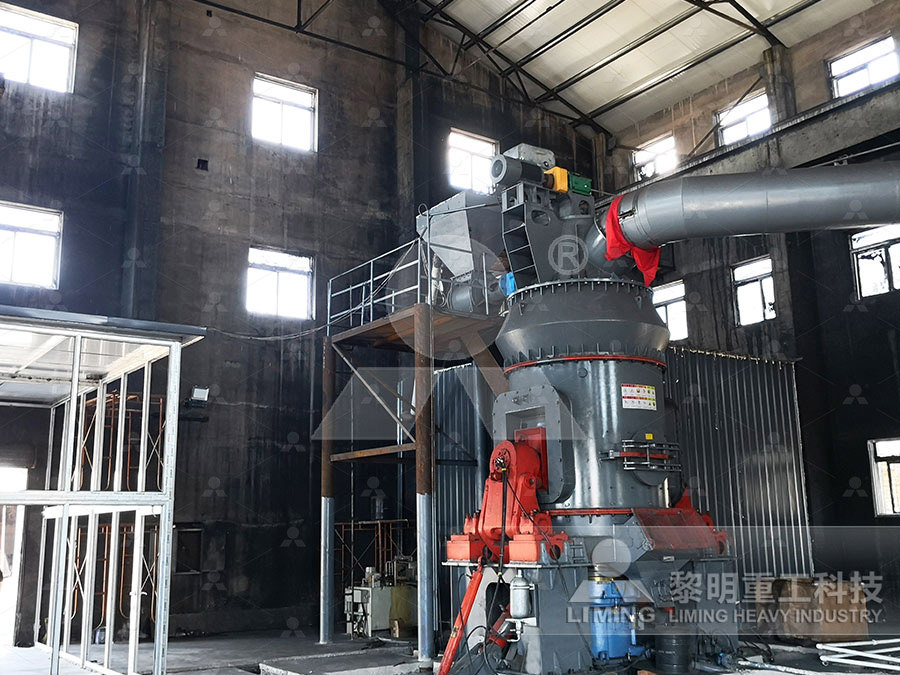
Grinding Mill an overview ScienceDirect Topics
Media ball sizes, for example, range from about 20 mm for fine grinding to 150 mm for coarse grinding Tumbling mills are typically employed in the mineral industry for primary grinding (ie, 2017年9月1日 The findings of this work suggest that at the plant scale, UG2 ore particle shape characteristics within any particular size class are not significantly affected by grinding in an Fine grinding: How mill type affects particle shape characteristics more than 5 mm is obtained, and when grinding it is less than 5 mm Crushing and grinding are preparatory operations of enrichment and are intended for ore grains separation (opening) of Reengineering of the ore preparation production process in the Ore grinding is a process to further reduce and disperse the ore particle size In the mineral processing industry, ore grinding is the particle size preparation before the separation of the Ore Grinding Methods and Process of Ore Grinding
.jpg)
AMIT 135: Lesson 7 Ball Mills Circuits – Mining Mill
Three types of mill design are common The Overflow Discharge mill is best suited for fine grinding to 75 – 106 microns The Diaphram or Grate Discharge mill keeps coarse particles within the mill for additional grinding and typically Effect of ball and feed particle size distribution on the milling efficiency of a ball mill: An attainable region approach N Hlabangana a, G Danha b, *, E Muzenda b a Department of Chemical Engineering, National University of Science and Technology, P O Box AC 939, Ascot Bulawayo, Zimbabwe b Department of Chemical, Materials and Metallurgical Engineering, College of Effect of ball and feed particle size distribution on the milling 2023年6月7日 It is also known as aerofall mill, its cylinder has large diameter and small length, and its lengthdiameter ratio (L/D) is usually 03–035, which depends on the fragmentation characteristics of ore in autogenous grinding The density of ore is far less than that of grinding medium, so the diameter of the cylinder of autogenous mill must be Autogenous Mill SpringerLinkore and corresponds to the scheme, including medium and small stage ball grinding provides a comparative analysis of a wide range of ore processing steps and requires 515% energy in a selfgrinding mill [3] 1 Figure 2 Ball mill process control system using ACS (Adaptable Control System) Figure 2 shows that the input and output signalsControl of ball mill operation depending on ball load and ore
.jpg)
EnergyEfficient Advanced Ultrafine Grinding of Particles Using
2023年7月10日 The present literature review explores the energyefficient ultrafine grinding of particles using stirred mills The review provides an overview of the different techniques for size reduction and the impact of energy requirements on the choice of stirred mills It also discusses the factors, including the design, operating parameters, and feed material properties, 2003年1月1日 The impact of dynamic forces in rockblast fragmentation process has been the subject of investigation for years Nevertheless, while the influence of the macrofragmentation in downstream (PDF) The Effects of Blasting on Crushing and GrindingOutput: 16 t/h 50 t/h Ball mill is suitable to grind various mineral and other materials, which is widely used in various industries such as benefication, chemical industry, etc, it has two ore grinding Compare this product Remove from comparison tool ball grinding mill horizontal for ore ball grinding mill Final grain size: 74 Ore mill, Ore grinding mill All industrial manufacturers2018年2月1日 In another study to investigate ball size distribution on ball mill efficiency by Hlabangana et al [50] using the attainable region technique on a silica ore by dry milling, a threeball mix of Effect of ball and feed particle size distribution on the milling
.jpg)
(PDF) Control of ball mill operation depending on ball load and ore
2023年12月12日 In addition, the ore properties are one of the important parameters for the optimal utilizing of the ball mill Ore can have various properties, such as hardness, density, moisture content, etc CLUM series of ultrafine gypsum powder vertical grinding mills are a new type of ultrafine industrial ore grinding equipment that integrates grinding Superfine vertical grinding mill main machine and multirotor powder separator: Finished product Less than 2μm=30% output (t/h) 912: 1216: 1418: Less than 2μm=45% output (t/h) 5575:CLUM Ultrafine Vertical Grinding Mill2015年7月29日 The result is the ore will not be able to move into the rod load Because there isn’t enough water to carry the ground material deeper into the mill the ore begins to pile up at the entrance This will mean that there is more ore than surface area of the Rods This excess amount of unground ore will cause the rods to lift and separate Effect of Water Density on Grinding Mill 911Metallurgist2017年1月1日 In this investigation, we optimize the grinding circuit of a typical chromite beneficiation plant in India The runofmine ore is reduced to a particle size of less than 1 mm in the comminution (PDF) Performance optimization of an industrial ball
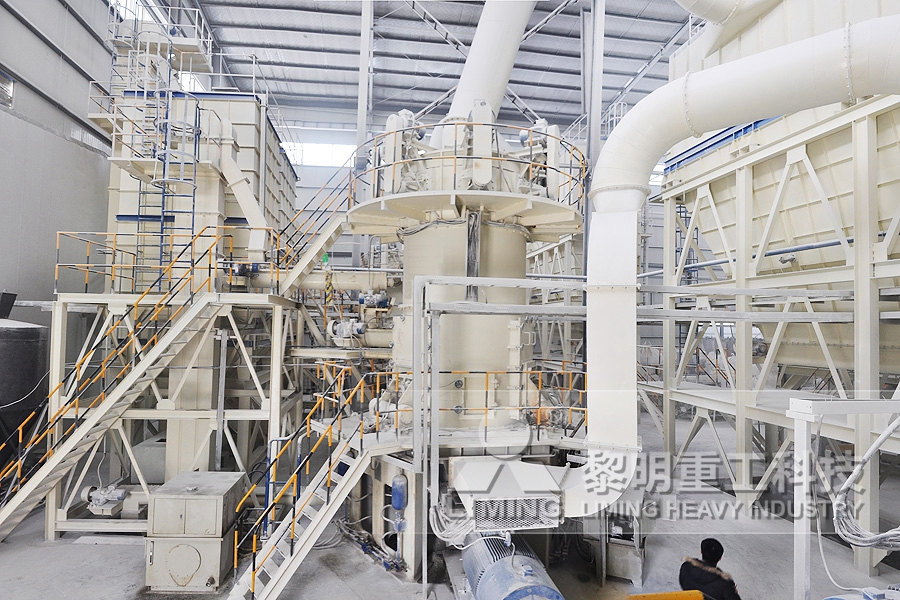
Gold CIP Processing Plant, Gold CarboninPulp
Finally, less than 20mm material into the hopper with an electromagnetic vibrating feeder and evenly fed into the ball mill 2 Grinding system: Ball mills grind fine ore rocks into a fine powder to release the gold in the rocks Then, the output 2018年8月17日 The concept of ore blending is a very relevant notion in modern high tonnage production mines It is not only essential for the prolongation of the mine life of the concerned mine but as well as a The effects of ore blending on comminution 2019年8月14日 Ball mill is a common grinding equipment in concentrator Common Types of Ball mill back to top The common industrial ball mills mainly include cement ball mill, tubular ball mill, ultrafine laminating mill, cone ball mill, ceramic ball mill, intermittent ball mill, overflow ball mill, grid ball mill, wind discharge ball mill, double bin ball mill, energy saving ball millThe Ultimate Guide to Ball Mills MiningpediaCLRM series Raymond mill Discharge fineness: 80500 mesh Feed size: 35 mm Output: 135 t/h Materials: Quartz, feldspar, barite, carbonate calcite, limestone, talc, ceramics, iron ore, emery, bauxite, phosphate rock, coal and other materials, a total of about 400 kinds of materialsCLRM series Raymond mill SBM Ultrafine Powder Technology

Investigation of some parameters affecting the Ultrafine grinding
2013年4月16日 ABSTRACT In this study, ultrafine grinding of a refractory silver ore tailings was studied A laboratory scale pintype vertical stirred mill and ceramic beads were employed for the grinding tests2024年1月1日 Therefore, the rod mill is mostly used for coarse grinding of the previous period of ball mill, or grinding of brittle materials and materials against overcrushing, such as tungsten and tin ore before gravity separation; and (3) autogenous mill – it refers to the materials which themselves are collided and ground mutually to be crushed when the grinding mill rotates, and Ore Grinding SpringerLinkmore than 5 mm is obtained, and when grinding it is less than 5 mm Crushing and grinding are preparatory operations of enrichment and are intended for ore grains separation (opening) of various minerals, contained in the mineral in the form of closely intertwined intergrowths The more fully the minerals are revealed during crushing and Reengineering of the ore preparation production process in the 2019年6月9日 finishing the grinding the quality of the output ore feed and product of the grinding mill process The output product fragmentation recovery mass of pr oduc t less than 0,250 mm Grinding mill process optimization algorithm ResearchGate
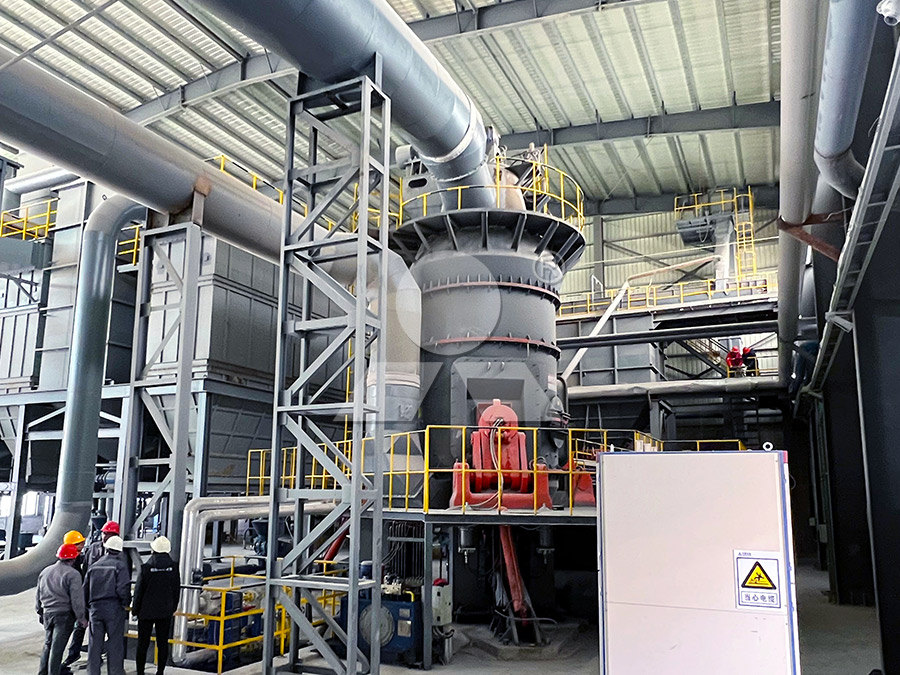
Study on the Selection of Comminution Circuits for a Magnetite Ore
2016年4月26日 Standard drop weight, SMC, and Bond ball work index tests have been conducted to investigate the comminution circuit of a magnetite ore located in Eastern Hebei, China In addition, simulations based on JKSimMet and Morrell models have been performed to compare the specific energy consumption of various comminution circuits According to the 2020年6月3日 Effect of OEM mergers on grinding mill design A wave of grinding mill OEM mergers took place in the 70’s and 80’s During those years, only a handful of OEM’s were competing with one another, and no more than How grinding mill design changed over the last 30 yearsmill by the centrifugal product separator, which produces a sharper cut than fine cyclones It also eliminates the extra capital and operating cost of closed circuit cycloningDensity and Viscosity impacts : stirred mills operate at lower pulp densities than conventional mills The efficiency of the IsaMill is much less affected by density thanFine Grinding as Enabling Technology – The IsaMillJudging from the quality of iron ore in China, it is mainly characterized by "more lean ore, less rich ore, fine embedded particle size, high proportion of polymetallic (associated) ore, and complex ore composition" Under the current technical conditions, magnetite, hematite, limonite, siderite, ilmenite and pyrite are theintroduction of new type iron ore grinding and dry separation
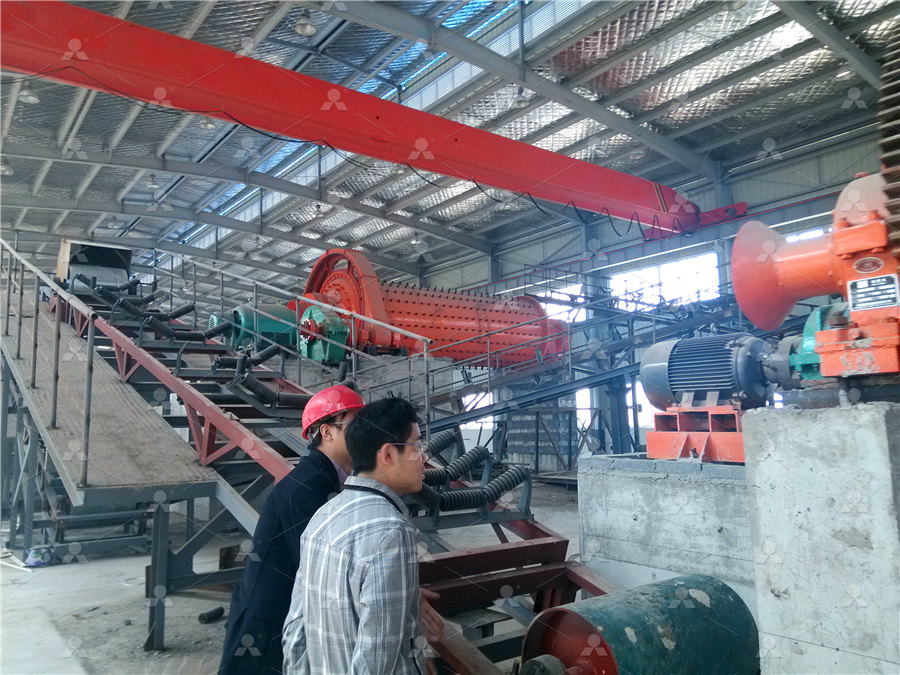
(PDF) EnergyEfficient Advanced Ultrafine Grinding of Particles
2023年7月10日 Metalliferous ore grinding is frequently the most energyintensive collection of activities and accounts for around a quarter of the 2% of the world’s energy that is used for mineral comminution [2002年11月1日 (Zhang 2016) (Lim et al 1994) (Hoagland et al 1973) Dry grinding is less efficient than wet grinding (Fuerstenau and Abouzeid 2002) as it may require more time and therefore more energyThe energy efficiency of ball milling in comminution2022年1月23日 Preparing the RunofMine (ROM) bauxite for the grinding mill circuit must be completed in order to efficiently size the grinding mill circuit The focus of the Sect 412 discussion is about choosing the correct crusher for the bauxite application Including the considerations for using a drum scrubber or not Bauxite mines are in many placesPhysical Bauxite Processing: Crushing and Grinding of BauxiteSpeed also plays a role in ore grinding; too high of a speed can cause damage to the mill gears and other components, while too low of a speed can cause excessive wear on these same components It is important to find a balance between these two variables in order to achieve optimal grinding performanceFactors affecting ores grinding performance in ball mills

Optimization of the makeup ball charge in a grinding mill
1992年3月1日 Batch grinding parameters a T 063 min −1 γ 080 α 137 Λ 47 β 62 Φ 0 060 δ 01 a T 112 mm Table 2 Average input values for the fullscale mill and their corresponding interval ranges 2017年3月20日 An effect of a grinding method, that is ball mill and high pressure grinding rolls (HPGR), on the particle size, specific surface area and particle shape of an iron ore concentrate was studiedPhysicochemical Problems of Mineral Processing Investigation 2020年5月28日 The feed samples of X, Y, and Z iron ores were ground in the BBM (ball mill refers to a BBM of size 300 mm × 300 mm with smooth liners) to identify the PSD, BWI, and RT of each ore Grinding experiments were conducted according to Bond’s standard test procedure []For each iron ore sample, the RT taken to produce 250% circulating load in the BBM was Investigation on Iron Ore Grinding based on Particle Size Distribution Little or no grinding is done when a mill is centrifuging, and operating speeds must be less than the critical The critical speed can be calculated from the expression: Where, is the critical speed in rev/sec, is acceleration due to Size Reduction1: Grinding – Unit Operations in Food
.jpg)
Ultrafine vertical roller mill SBM Ultrafine Powder
Less than 2μm=34% output(t/h SBM’s ore grinding equipment sells well all over the world with high quality and highcost performance Especially the ultrafine vertical roller mill, our ultrafine vertical powder grinding mill has 2023年10月27日 The ball mill is a rotating cylindrical vessel with grinding media inside, which is responsible for breaking the ore particles Grinding media play an important role in the comminution of mineral A Review of the Grinding Media in Ball Mills for 2019年4月16日 Conference: Applying a Successful Technology from the Cement Industry: Advantages of Grinding Ore in a VerticalRollerMill; At: Antalya, Türkey(PDF) LEARNING FROM OTHER INDUSTRIES; WHY THE VRMAccording to one study, the grinding process alone accounts for approximately 40% of total power consumption in a mine complex (Ballantyne et al, 2012) A ball mill employs steel balls to generate a grinding action, ie ore particle comminution via impact and abrasion with steel balls, and is a key component of beneficiation plant productionEfect of grinding media on the milling eficiency of a ball mill
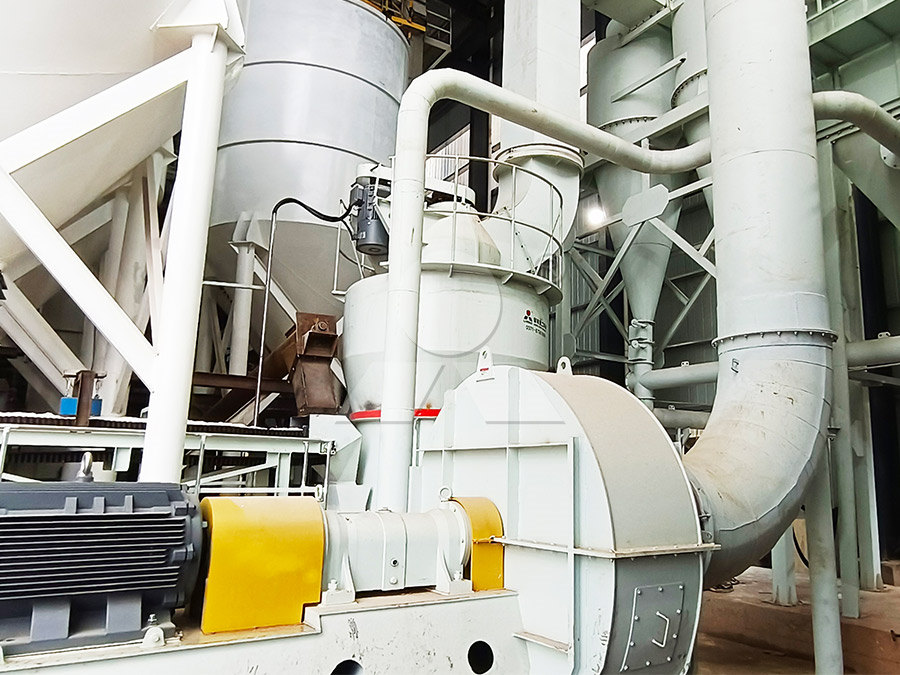
What Is The Crushing Process MEKA
Bake argued in 1964 that the energy spent on size reduction was only 06% of the total energy, and Austin’s estimate was less than 3% Although these ratios are not exact, it is a known fact that the energy spent in the size reduction process is a very small proportion of the total energy spent for this purposeAlthough it is well known and easily experienced that the feed size distribution influences the throughput and stability of operation of a semiautogenous grinding (SAG) mill, the details are poorly understood since it is often only the input and output measurements that are used to identify unfavourable inmill conditions Load cells and power monitoring are sometimes used Understanding Size Effects of Semiautogenous Grinding (SAG) Mill 2017年3月4日 Ball mills are used for wet grinding iron ore, g old/copper ore, nickel ore and other ores, as wel l as lime/limestone for flue gas desulphurisat ion systems, coal and other raw materials Rod mill :SIZE REDUCTION BY GRINDING METHODS ResearchGate2 More crushing and less grinding to reduce the feed size into mill The larger feed size, the more work that the ball mill needs to do on the ore To achieve the specified grinding fineness, the workload of ball mill will be increased inevitably, and then, the energy consumption and power consumption will be increased accordingly10 Ways to Improve the Grinding Efficiency of Your Ball Mill
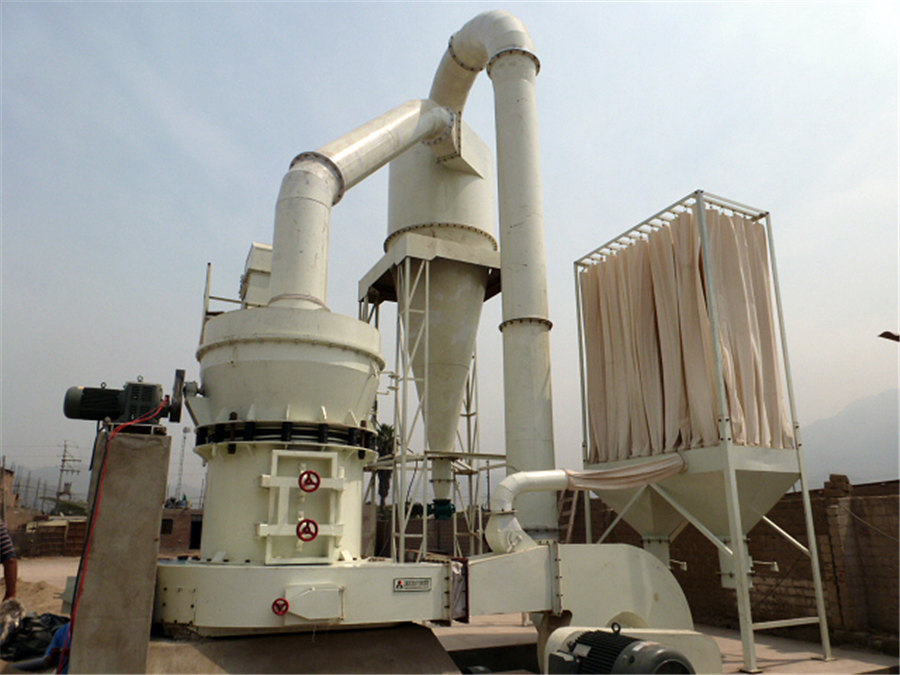
Energy conservation and consumption reduction in grinding
2023年11月1日 Grinding operation is the last preparation stage before beneficiation In this stage, the material undergoes the combined action of impact and grinding, so that the ore particle size is diminished and the qualified materials is provided for succeeding beneficiation operations [1, 2]Generally, the quality of the grinding product is also an important factor to determine the