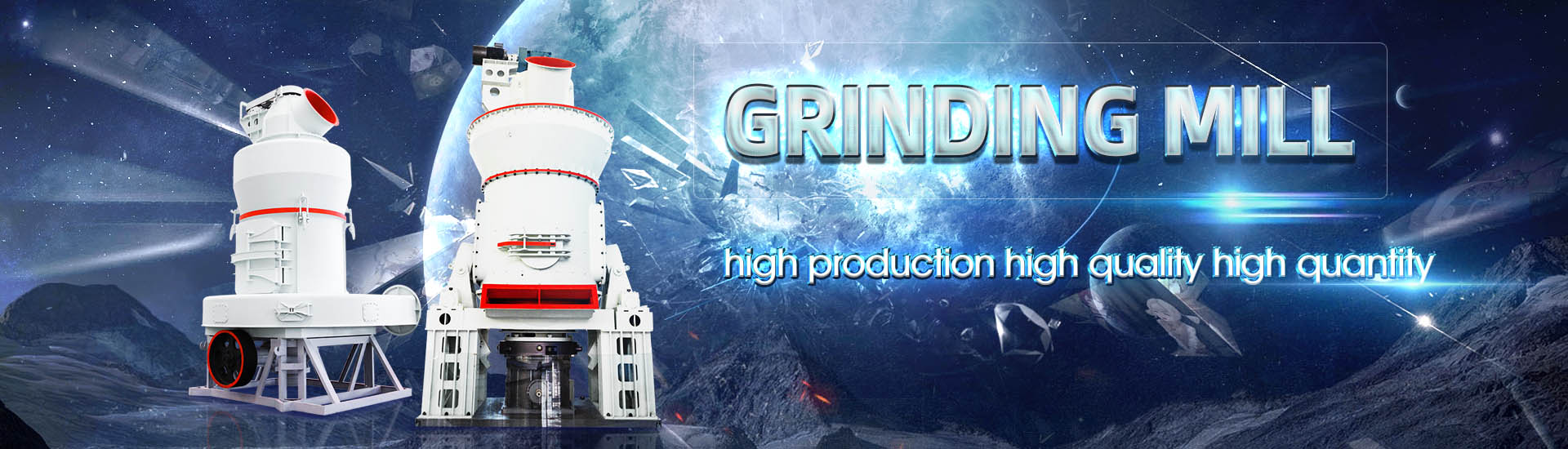
How to do coal grinding in cement plant
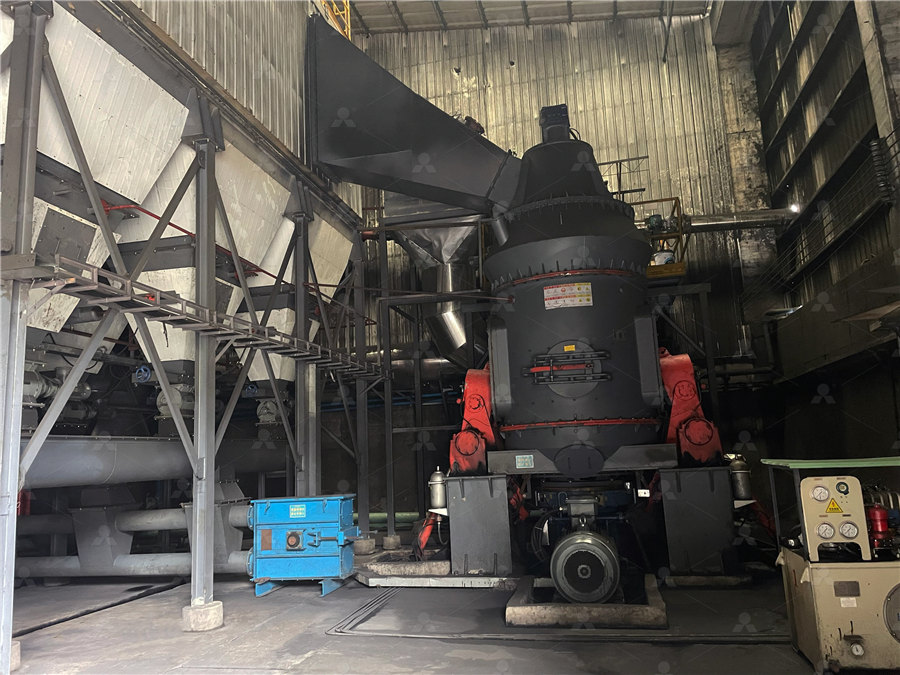
Coal Grinding Cement Plant Optimization
Highly energy intensive unit operation of coal grinding is intended to provide a fine coal as a fuel for calcination and clinkerization Coal grinding operation is monitored for following parameters to ensure objectivity and economy of operation2022年5月14日 We have to improve the Kiln operation until it reaches optimal operation This video is for learning about the cement production process, especially about the clinker production process in theKiln and Coal Mill Operation In Cement Plant English The coal mill grinding system is an important part of the dry process cement manufacturing In cement plants, we usually adopt the air swept coal mill system or vertical mill system as the pulverized coal preparation system, which is Coal Mill – Coal Mill In Cement Plant AGICO Cement Inertization of coal mill circuit and fine coal bins with CO2, N2 or CO2+N2 to replace O2 which promotes spontaneous ignition of fine coal Vertical roller mills can typically handle an Raw Material DryingGrinding Cement Plant Optimization
.jpg)
Air Pollution Control in Cement: Solutions Impact
2023年9月22日 In addition, Lean Phase Pneumatic Conveying systems are environmentally friendly because they do not produce any emissions Applications Across the Cement Production Spectrum Our range of air pollution control A cement ball mill is ready for transportation There are many kinds of industrial equipment used in a cement plant, including thermal equipment, grinding equipment, dust removal system, transportation system, storage system, and How to Start a Cement Factory2024年11月23日 Cement Extraction, Processing, Manufacturing: Raw materials employed in the manufacture of cement are extracted by quarrying in the case of hard rocks such as limestones, slates, and some shales, with the Cement Extraction, Processing, Manufacturing2023年1月1日 Given the complex role of coal as a fuel in cement clinker production, cement plant operations do not benefit from frequent changes of fuel source and fuel quality To achieve stable kiln operation, uniform clinker quality, and safe operations, a Coal utilization in the cement and concrete industries
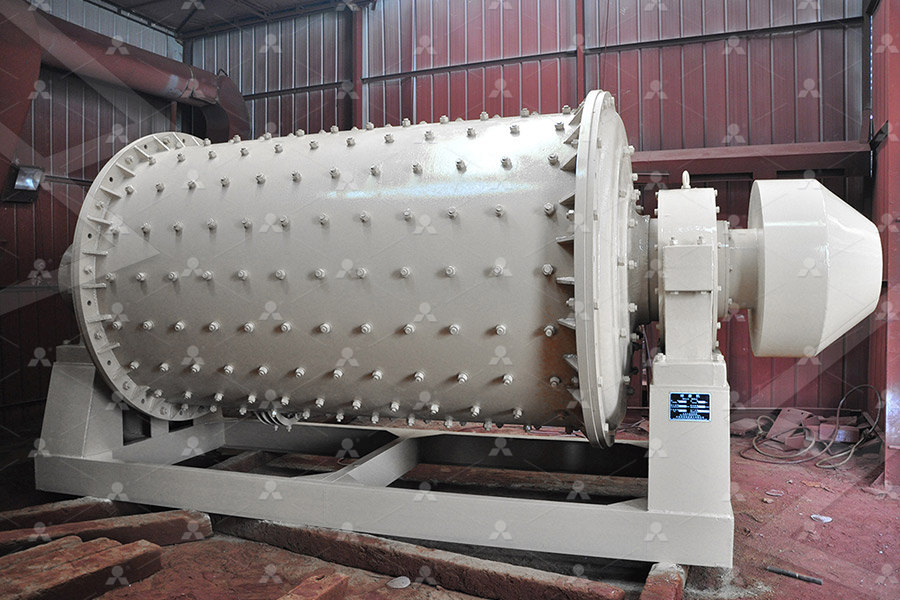
EnergyEfficient Technologies in Cement Grinding IntechOpen
2015年10月23日 In this chapter an introduction of widely applied energyefficient grinding technologies in cement grinding and description of the operating principles of the related equipments and comparisons over each other in terms of grinding efficiency, specific energy consumption, production capacity and cement quality are given A case study performed on a Everything you need to know about clinker/cement Grinding if You read and understand this article , you will be ready to be a cement grinding area manager FEED AND FEED SYSTEM Feed Temperature Plants with satellite coolers have high clinker temperatures: eg Cumarebo, Oujda Exit satellite cooler 200250°C Exit grate cooler 100150°CEverything you need to know about clinker/cement GrindingAs a leading cement plant builder, AGICO offers an expert cement grinding plant EPC service Cement Grinding Unit EPC Solution With a strong RD team, experienced engineers, and firstclass technical services, we aim to provide users with the most advanced and optimized cement production solutionsCement Grinding Plant Expert Cement Grinding Solutions from Dust is the main pollutant from the cement industry Many links in the cement production process, such as raw material crushing, raw meal grinding, clinker calcination, cement grinding, etc, have different degrees of dust spilloverAmong them, the clinker calcination stage has the most serious dust emission degree, accounting for more than 70% of the total dust emission of the cement Cement Dust Collectors Selection Dust Control System in Cement Plant
.jpg)
How much dose it cost to start a cement grinding plant?
2024年5月31日 What does cement grinding plant do? In brief, cement grinding plant helps to grind clinker into finished cement Electrostatic precipitator: remove particulate smoke from the flue gas emitted by coal or oilfired boilers The total investment in this section is about 6 million yuan Packaging and delivery system costStage 2: Grinding, Proportioning, and Blending The crushed raw ingredients are made ready for the cementmaking process in the kiln by combining them with additives and grinding them to ensure a fine homogenous mixture The composition of cement is proportioned here depending on the desired properties of the cement Generally, limestone is 80%, and the remaining 20% How Cement is Made Cement Manufacturing Processenvironmental constraints The coal grinding plant was ordered from GPSE in April 2010 The target was to install a new grinding plant in accordance with technical and legal standards for coal grinding Important conditions were attached to the order The new coal mill had to be integrated into the present plant layoutCOAL GRINDING IMPS: more than meets the eye Gebr Pfeiffer2022年5月14日 Kiln and Coal Mill Operation In Cement Plant English VersionIn the previous video session, we explained how to start the Kiln operation, but the quality andKiln and Coal Mill Operation In Cement Plant English
.jpg)
Cement Grinding Unit Cement Grinding Plant
Equipment in cement grinding plant The cement grinding machine includes cement vertical mill, cement ball mill, cement roller press, cement seperator, conveyor and other cement equipmentWe can provide scheme design for Compared to the traditional grinding station available on the market, the MMG cement grinding plant is more suitable for the small and mediumsized cement market It can be applied to produce all kinds of cement and is also available for other materials such as limestone, gypsum, coal, etcModular Mobile Cement Grinding Plant For Sale AGICO Cement2024年3月16日 Ultimately, the finely pulverized coal is transported via a burner pipe to the furnace of a power plant or cement kiln, where it undergoes combustion to generate heat for electricity production or industrial processes, completing the operational cycle of the coal mill The coal grinding mill serves as a versatile grinding machine, adept at How Does a Vertical Coal Mill Work Coal Grinding Mill In Cement PlantThe vertical roller mill (VRM) is a type of grinding machine for raw material processing and cement grinding in the cement manufacturing processIn recent years, the VRM cement mill has been equipped in more and more cement plants around the world because of its features like high energy efficiency, low pollutant generation, small floor area, etc The VRM cement mill has a Vertical Roller Mill Operation in Cement Plant
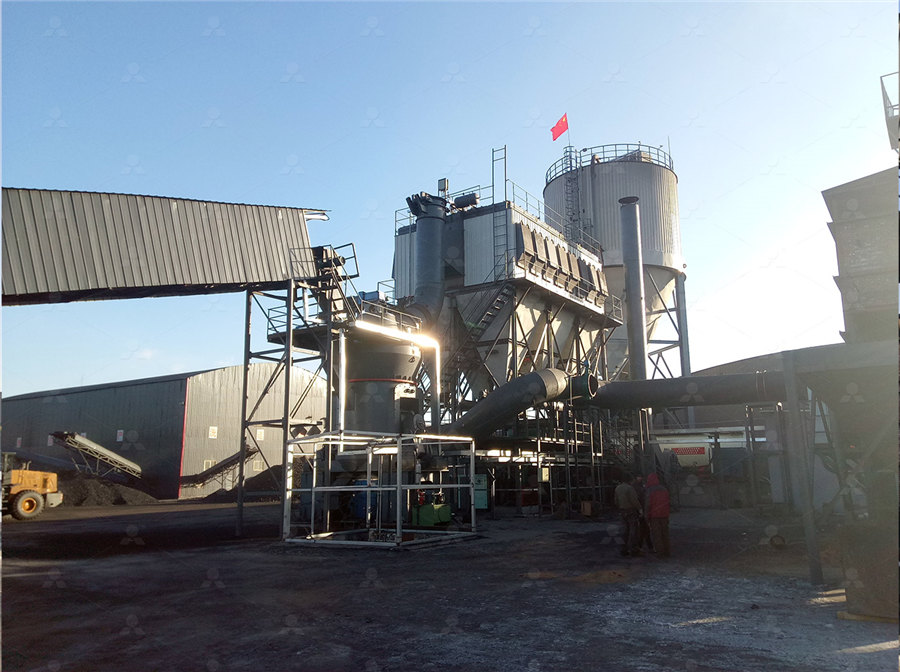
Efficient grinding unit selection impacts profitability Indian Cement
2022年8月10日 Coal grinding: better combustion of fuels, improves the flame property, and avoids CO2 generation, including improved burning process; Cement grinding: cement hydration, strength development, and water demand; How do grinding units contribute to the profitability of the cementmaking process? The grinding unit contributes to profitability in The cyclone preheating system Phase IV: Calcination The calcination is the core phase of the cement making dry process The calcination of the preheated raw meal takes place in the rotary kiln of the cement plant The rotary kiln is a huge rotating furnace in which the raw meal is heated up to 1450 ⁰C and turned to clinkerHow Is Cement Produced in Cement Plants Cement Making In the cement plant, the new dry process cement manufacturing requires the moisture content of coal powder to be 05% ~ 15%, while that of raw coal is 15% ~ 40% Therefore, the ball mill should have a drying function besides grindingCoal Mill in Cement Plant Vertical Roller Mill AirSwept Ball Mill2022年8月10日 Grinding might be an individual step in the cement production line but it is a crucial one, given the energy consumption and impact on the quality of output that it gives ICR explores how grinding methods have evolved with the help of technology and with the use of modernage grinding aids Grinding in the cement []Grinding: Smarter Solutions Indian Cement Review
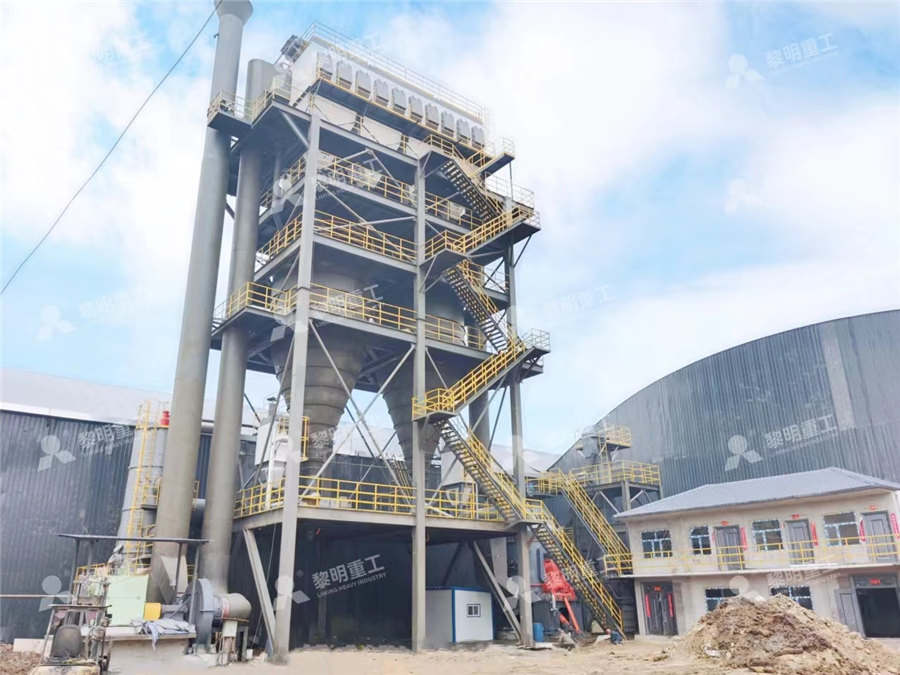
How Cement is Made Portland Cement Association
Cement producers are constantly pursuing innovative, efficient, and environmentally responsible ways of producing highquality cement to realize carbon neutrality across the concrete value chain by 2050 Take a look at how 2024年1月11日 With a vertical roller mill (VRM) VRMs consist of a rotating table or bowl and rollers 1 To grind the coal, feed raw or initially crushed coal into the mill which is then ground between the rotating components; 2 Finally, hot air How to Process Coal into Pulverized Coal in 5 Steps?2019年1月3日 Clinker grinding technology is the most energyintensive process in cement manufacturing Traditionally, it was treated as "low on technology" and "high on energy" as grinding circuits use more than 60 per cent of total energy Clinker grinding technology in cement manufacturingPower Consumption in Cement Manufacturing Plant: The cement industry, as a traditional high power consumption industry, power consumption in the cement grinding process takes a large ratio in the whole production, electric power consumption is Power Consumption of Cement Manufacturing Plant
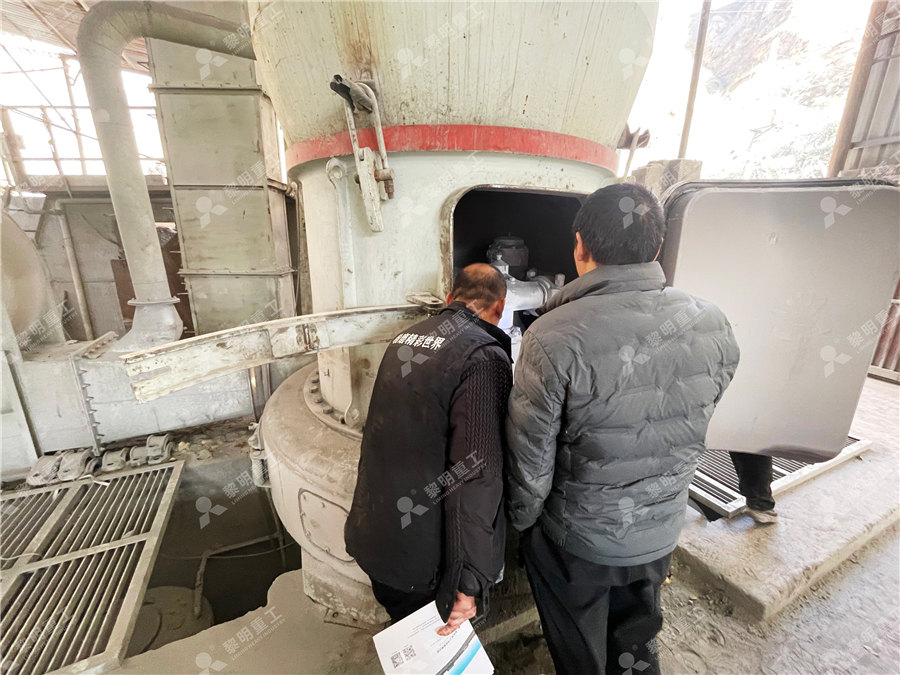
Air Swept Coal Mill Coal Mill In Cement Plant AGICO GROUP
What Is Air Swept Coal Mill The airswept coal mill is also called a coal grinder It is the main equipment of the cement plant, used for drying and pulverizing coal powderIt mainly consists of the feeding device, main bearing, rotary part, transmission device, discharging device, highpressure starting device, and lubrication system2019年9月27日 A cement mill is also applied for grinding clinker into finished cement The cement clinker grinding is the last step of the cement manufacturing process, in this step, cement mill grinds cement clinker, gelatinizing agent and other materials into the required size, which can meet the requirement of cementCement Euipment Overview Cement Making Machines Cement Plant2021年8月28日 This paper is a case study of a Portland cement plant in Romania, the experimental determinations presented mainly focusing on dust emissions in an important sector of the plant (cement mill and related facilities), with dust extraction from two chimneys in working areas (cement mill filtration system and grinder component separator filtration system), as well Dust Emission Monitoring in Cement Plant Mills: A Case Study in 2021年1月1日 Coal Grinding: Grinding Mill Vertical Roller Mill or Ball Mill: Coal is ground in Coal mill, which is a fuel for use in Rashmi cement limited environmental pre feasibility report for Expansion of existing cement grinding plant from 096 MTPA to 111 MTPA by enhancing capacity of 2000 TPD VRM base grinding units to 2500 TPD Review on vertical roller mill in cement industry its performance
.jpg)
PROCESS OPTIMISATION FOR LOESCHE GRINDING PLANTS
vertical roller grinding mills for grinding: • Coal • Cement raw material • Clinker / granulated slag • Industrial minerals, and • Ores The core elements of these plants are the Loesche vertical mills for drygrinding the abovementioned grinding stock Loesche has You will be surprised about what has gone wrong with fire and explosion protection of your system(s) Be sure about that! Evaluation of a coal grinding system’s fire and explosion protection, including the raw coal storage and the fine coal silo storage normally can be done in one day, mostly without having to stop coal grindingCoal Mill Safety In Cement Production IndustriesAGICO CEMENT is a trusted cement plant manufacturer supplies precalciner, cement calciner as you need, high quality and EPC project, get your quote now! Skip to content +86 Precalciner, Calciner In Cement Plant, Cement 2024年8月31日 1 The Role of Coal in Traditional Cement Kilns Historically, coal has been a primary energy source for cement production Cement kilns, which are used to heat raw materials to high temperatures, require substantial Is Coal Needed for Cement Production? A
.jpg)
Grinding trends in the cement industry Cement
Summary: The main trends concerning grinding processes in the cement industry are still higher efficiency, reduction of the power consumption and system simplicity In the case of new orders, vertical mills have increased their share After this, and brief flirtations with natural gas, coal became emphatically the cheapest kiln fuel from the mid1970s, and newer kilns had to be retrofitted with coal grinding equipment Since then, coal has remained the main fuel, although partially and at some plants totally Cement Plants: CoalGrinding is a highly energy intensive process in the cement industry Approximately 60 – 70 % of the total electrical energy used in a cement plant is utilised for the grinding of raw materials, coal and clinker Various technological improvements from the conventional ball mills in this area include: High efficiency separators (HES)Modern Processing Techniques to minimize cost in Cement 2011年8月9日 2 Alternative fuel options for the cement industry Coal is the primary fuel burned in cement kilns, however, the use alternative fuels in cement kilns is now common and increasing The range of alternative fuels is extremely wide They are usually available as gas, liquid and solid as shown in Table 1Alternative Fuels in Cement Manufacturing IntechOpen
.jpg)
(PDF) Grinding Media in Ball MillsA Review ResearchGate
2023年4月23日 A comparison of the grinding media is given together with the knowledge gaps that still need to be bridged to improve the quality and performance of grinding media used in ball millsIn discussion: Coal Mill Safety At best, coal mill safety is not well understood and, at worst, it is ignored When it comes to coal mill systems, most cement plant operators just presume that the supplier of the equipment knows all of the standards and rules and is 100% capable of making a system that conforms to these and is therefore safeIn discussion: Coal Mill Safety Coal Mill Safety, Explosion and Fire 2020年9月14日 Power supply distribution in cement plants Many young engineers consider cement plants pretty complicated because of their weird technology The reason probably lies in the fact that you cannot understand all those technologies unless you worked in such a plant and saw all processes from scratchThe essentials of electrical systems in cement plants EEPRaw meal homogenization is the most important process link of the four, accounting for 40% of the homogenization task It is an important factor to support the balanced and stable working performance of preheaters and kilns, and plays an important role in improving the output and quality of cement clinkerCement Raw Meal Homogenization Process in The Cement