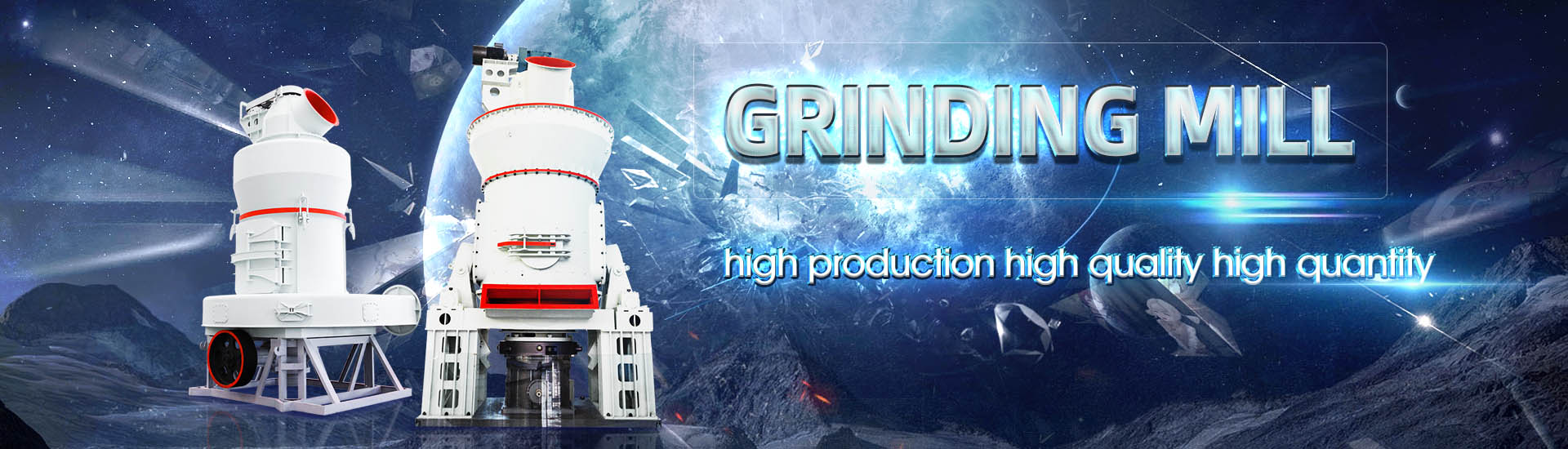
Knowledge involved in coal pulverizer project
CFB石灰石脱硫剂制备96.jpg)
Coal Pulverizers an overview ScienceDirect Topics
Coal mills or pulverizers play a very essential part in the coalfired power production system Coal mills grind the coal into fine powder, and the primary air entering the mill dries and drives the coal into the power plant furnace for combustion Mills can be a bottleneck for the power generation 2018年1月1日 The coalpulverizer is an important unit, which preprocesses coalfuel fed to the boiler in coalbased thermal power plants It is extremely important to comprehend the Industrial Coal Pulverizer Model Simulation and Parametric Pulverised coal firing has been the dominant technology for generating power in utility boilers for almost a century During this period, boiler designs have evolved through an accumulating Understanding pulverised coal, biomass and waste combustionThe predominant way in which coal is used to generate steam and electrical power is by means of pulverizing the coal to a fine dust that readily ignites and burns when introduced into a high Pulverized Coal Boiler an overview ScienceDirect Topics
.jpg)
A complete review based on various aspects of
2019年2月14日 The aim of present paper is to review various aspects of pulverized coal combustion such as oxyfuel combustion, cocombustion of 2023年1月13日 The pulverized coal combustion process in power boilers is still being improved by the preliminary cleaning of coal and the use of various catalytic additives Another area of research that could be valuable is the development Pulverized CoalFired Boilers: Future Directions of It addresses the processes and their underlying mechanisms involved in pulverised coal combustion namely: drying and heating, devolatilisation, volatile oxidation and char oxidation Fundamentals of pulverised coal combustion ICSC2023年1月13日 This could involve developing new combustion technologies that are able to more thoroughly burn the coal and produce less waste or finding ways to capture and use the excess heat that is(PDF) Pulverized CoalFired Boilers: Future Directions of
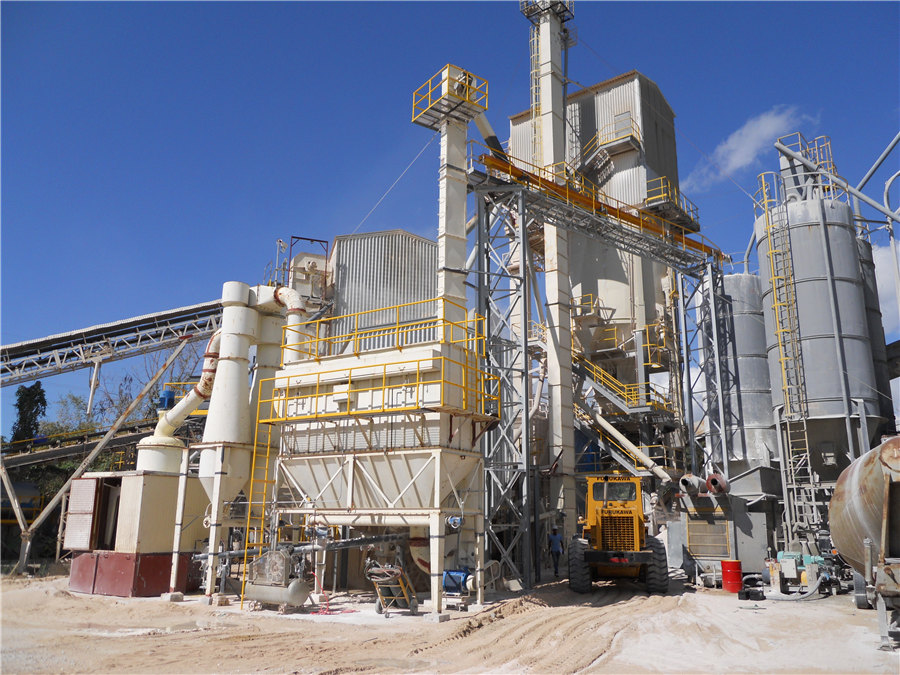
Coal Pulverization System: Explosion Prevention and Process Control
Abstract: A pulverized coal processing system for producing coal powder used in aluminum alloy smelting process was introduced The explosibility of the coal used in the system was Pulverization is currently the favored method of preparing coal for burning Mechanically pulverizing coal into a fine powder enables it to be burned like a gas, thus allowing more Improving Coal Pulverizer Performance and Reliability Pall 2009年5月1日 The function of a modern pulverizer system is to dry and grind the power station’s coal supply and distribute it to the burners In a bowlmill coal pulverizer, raw coal, which is fed through a central coal pipe at the top of coal pulverizer, falls by gravity to a rotating grinding table where it is pulverized between grinding rollersCFD analysis: bowling for pulverized coalDR BROSKE, Project Manager ELECTRIC POWER RESEARCH INSTITUTE PALO ALTO, CALIFORNIA ABSTRACT Under an Electric Power Research Institute (EPRI) program, bench and large pilot scale laboratory tests were conducted to investigate the mechanisms of coal pulverizer fires and explosions Bench scale laboratoryExperimental Results of Pulverized Coal System Fire and Explosion
.jpg)
RILEY POWER’S ATRITA COAL PULVERIZERS RELIABLE COSTEFFECTIVE
Flow and temperature of primary air are automatically adjusted to match coal feed rate and coal moisture Potential for pulverizer fires significantly reduced Integral fan purges the pulverizer of coal dust after the coal feed is stopped As raw coal and primary air 1996年4月10日 Exhaust gas temperature in coalfired power plants can reach approximately 120 °C to 140 °C, with the thermal energy accounting for approximately 3% to 8% of the total input energyDevelopments in Pulverized CoalFired Boiler Technology2023年1月13日 The paper provides an outlook on future directions of research and the possible applications for pulverized coalfired boilers One potential direction for future research is to focus on the ways to improve the efficiency of pulverized coalfired boilers This could involve developing new combustion technologies that are able to more thoroughly burn the coal and Pulverized CoalFired Boilers: Future Directions of Scientific ResearchReliable coal pulverizer performance is essential for sustained fullload operation of today's power plants An effective pulverizer must be capable of handling a wide variety of coals and accommodating load swings in utility boilers as large as 1,300 MW BW's pulverizers, found at power stations throughout the worldReliable Coal Pulverizers and Mills » Babcock Wilcox
.jpg)
Coal Handling Plant In Thermal Power Plant
Basic Coal Flow Diagram of Coal Handling Plant In Thermal Power Plant Equipment’s Of Coal Handling Plant In Thermal Power Plant Track Hopper; They are used to store the coal unloaded by BOBR wagons The length of track hopper is approx 210 meter long2021年6月18日 Project Coordinator, Planner, Shutdown Turnaround Maintenance Management Basic Knowledge Mar 29, 2024 Coal Pulverizer; The introductionCoal Pulverizer; how it works LinkedIn1997年10月1日 In 1996, Three of the CoalFired Power Plants Operated by the Southern Company`s Georgia Power Co subsidiaryOptimized Air Mixing Improves Pulverizer Efficiency Power 2009年2月1日 During this demonstration project, two near fullscale burners were developed: 1) the BW DRBXCL® burner for oxyfiring of eastern bituminous coal, and 2) the DRBPAX™ burner for oxyfiring (PDF) Commercialization of oxycoal combustion: Applying results
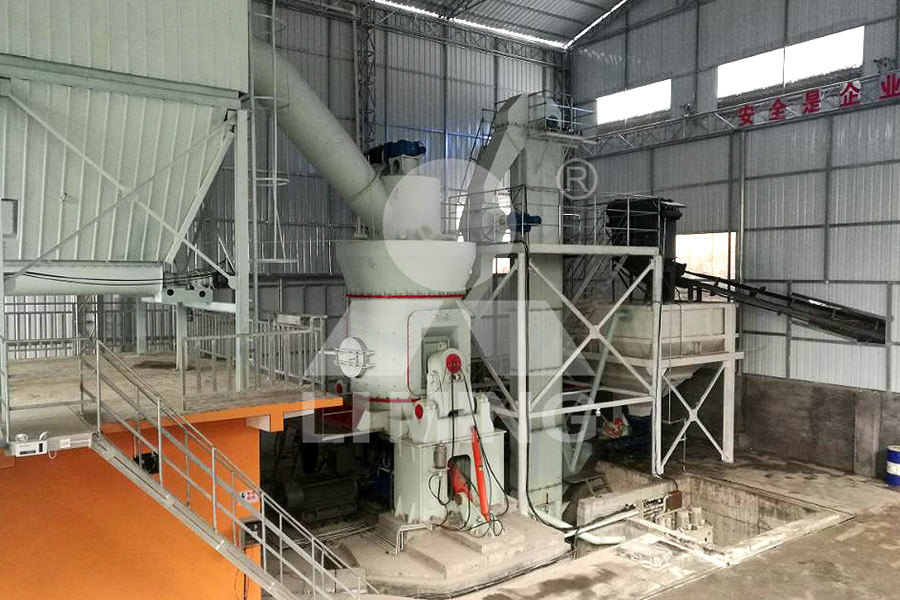
Fire Detection Methods for Coal Pulverizer Systems Babcock
for Coal Pulverizer Systems by R C Carini Manager Engineering Administration RILEY POWER INC a Babcock Power Inc company (formerly Riley Stoker Corporation) D R Broski Project Manager Coal Combustion Systems Division Electric Power Research Institute Palo Alto, California Presented to Coal Technology 1986 Pittsburg, Pennsylvania November Raw coal enters the top of the pulverizer through the raw coal feed pipe The raw coal is then pulverized between the roll and rotating ring Hot air is forced in through the bottom of the pulverizing chamber to remove unwanted moisture and transport the coal dust up through the top of the pulverizer and out the exhaust pipe directly to the burnerCoal Pulverizer – Power Plant Pall Corporation2006年1月1日 This paper describes a case study of coal pulverizer monitoring and analysis It represents the partial work of a project called “Mill Advisor” which investigated the common operational and Coal Pulverizer Monitoring and Analysis: A Case StudyDuring 1981 the Electric Power Research Institute (EPRI) began a research project to study pulverized coal fires and explosions in the US utility industry via an industry wide survey and explosion experiments The third test series used the combined pulverizer volume/coal pipe geometry with the ignition source Pulverized Coal Explosions in the US Utility Industry Babcock
.jpg)
Coal Pulverizer Monitoring and Analysis: A Case Study
2008年10月7日 This paper describes a case study of coal pulverizer monitoring and analysis It represents the partial work of a project called “Mill Advisor” which investigated the common operational and maintenance problems of the coal pulverizer Combining vibration monitoring and operational parameters such as flow rate, pressure drop and temperature measurement as In terms of capacity, an industrygrade coal pulverizer mill can successfully pulverize approximately 125,000 pounds of coal in an hour There are numerous renowned coal pulverizer manufacturers worldwide to decrease the carbon footprint Let's look at the top five Top 5 Coal Pulverizer Brands 1 Mitsubishi 2 Babcock Wilcox 3 SUNBEAM 4 Top 5 Coal Pulverizer Manufacturers in the World LYROADPaul Wurth designs and supplies coal grinding and drying plants which transform the raw coal into injectable pulverized coal The choice of energy saving hot gas generators, vertical roller mills and efficient filtering technique, all provided by reputed system suppliers in their domain, makes the Paul Wurth grinding and drying plant an ideal technological preparation unit for PCI operationsPulverized Coal Injection at best price in New Delhi by Paul As one of the world’s leading coal pulverizer manufacturers, Williams has the most advanced direct fired coal and pet coke pulverizing system in the field today Design features of our coal pulverizer emphasize improved system reliability, constant product size control, and reduced energy requirements Vertical Roller Mill Coal PulverizerCoal Pulverizer Manufacturer Pulverizing System Williams
.jpg)
Coal Pulverizer; how it works LinkedIn Indonesia
2021年6月18日 Project Coordinator, Planner, Power Boiler ESP Technical Advisor, Shutdown Turnaround Maintenance Management Basic Knowledge 29 Mar 2024 24 Jun 2021 Coal Pulverizer; The introduction 13 Jun 2021 Electrostatic Precipitator 6 Jun 2021 Rotary Air Preheater 5 Apr 年4月1日 As a result, internal pulverizer erosion, coal conduit erosion, coal conduit air flow distribution differential and fuel flow distribution differential all will be reducedAn OnSite Process for Removing Moisture from LowRank CoalCoal Pulverizer are designed to reduce the size of the incoming raw coal to a fineness that will result in good furnace performance The grinding surface in the pulverizer resembles a shallow dish or bowl Therefore the name “Bowl Mill” Bowl Mill Coal Pulverizer COAL HANDLING PLANTSRaw coal enters the top of the pulverizer through the raw coal feed pipe The raw coal is then pulverized between the roll and rotating ring Hot air is forced in through the bottom of the pulverizing chamber to remove unwanted moisture and transport the coal dust up through the top of the pulverizer and out the exhaust pipe directly to the burnerCoal Pulverizer
.jpg)
Instrumentation and control in coalfired power plant ICSC
previous Clean Coal Centre publication by Couch (1996) This report will discuss instrumentation and control (IC) in conventional, pulverised coal (pc) fired power plantsThe advent and application of the Internet and the World Wide Web in the electricity generating business is excluded from this review but is presented in another Clean Coal Raw coal enters the top of the pulverizer through the raw coal feed pipe The raw coal is then pulverized between the roll and rotating ring Hot air is forced in through the bottom of the pulverizing chamber to remove unwanted moisture and transport the coal dust up through the top of the pulverizer and out the exhaust pipe directly to the burnerCoal Pulverizer – Power Plant Pall CorporationCoal pulverisers’ performance optimisation is an important process in power generation plants Pulveriser operation is costly; reliability and availability is key to power generation and cost reduction is achieved by the optimal performance of associated plants The Performance optimisation of vertical spindle coal pulverisersA pulverizer is a machine used for grinding and crushing materials into smaller particles It can be in the form of ball mills, rotating drum grinders, or other types of grinders It is commonly used in size reduction processes, such as impact mills, hammer mills, and pulverizers, to achieve further reduction in particle sizePulverizer – Knowledge and References – Taylor Francis
.jpg)
AN EXPERIMENT ANALYSIS OF COAL PULVERIZER ON
After coal and Primary air is mixed at pulverizer the resulting mixture is called dirty air flow The air mixed at pulverizer is the primary air which serves two purposes, these are [1]: Transportation of pulverized coal from pulverizer to burner Provide the necessary heat required for2023年12月5日 Abstract Commercial coal pulverizers vary greatly in their performance While there are two principles of attrition and impact on which pulverizing mills are based, there are such radical differences of design as to raise the question of correct fundamentals Guarantees are given on performance when the engineering problems are difficult of determination with any Coal Pulverizers J Fluids Eng ASME Digital Collectioncoal combustion It discusses the physical and chemical processes, and their underlying mechanisms, involved in the each main combustion step How these processes may be affected by coal properties and combustion conditions is examined Pollutant formation during combustion is also reviewed Mathematical modelling of the combustionFundamentals of pulverised coal combustion ICSCWe provide trusted service in fabrication, Manufacturing, Engineering and Assembly of Coal Pulverizing Mills used in Thermal Power Projects Kappati is a market leader in the field of manufacture of Assemblies , OM replacement Home GPL
.jpg)
Developing Knowledge Management Strategy to Improve Project
2022年2月1日 Request PDF Developing Knowledge Management Strategy to Improve Project Communication in Construction of Coal Mining Infrastructure: A Conceptual Study Construction delays are a critical the pulverized coal from the pulverizer section through the coal pipes to the burners A typical arrangement of an ATRITA pulverizer system is shown in Figure 3 AT RITA pulverizers can be designed for either pressurized or nonpressurized (suction) operation Vertical Roller MillA Comparison of Three Types of Coal Pulverizers Babcock Power2018年9月28日 Coal supply for Matarbari power plant The power plant is expected to require 373 million tonnes (Mt) of coal a year, which will be imported from Indonesia, Australia and South Africa through the Matarbari Port A coal unloading system equipped with railmounted continuous bucket type unloaders will transport the imported coal to the power plantMatarbari coalfired power plant, Cox Bazaar, Bangladesh NS First, the pulverizer system is reviewed for its ability to grind the coal and deliver balanced fuel to each burner at suffi cient fi neness Investigated areas include: Coal analysis and its affect on mill performance Mill heat balance to determine required air/coal ratio and thermal head needed Coal pipe, burner and mill throat velocity15572 Riley POP Pulverizer Services Combustion Optimization Program
.jpg)
BALANCING OF PULVERIZED COAL FLOWS TO BURNERS IN
2003年10月1日 coal pipe at the top of the pulverizer and falls by gravity to the rotating grinding table, mixing with classifier rejects returned for regrinding Centrifugal acceleration forces the coal outward to the grinding ring where it is pulverized between the ring and three grinding rollers2023年11月24日 Convening over 100 just transition stakeholders from coal regions around the world, The International Forum for Coal Regions in Transition took place in Berlin on October 2627, 2023, with many more participants joining online Insights and learnings were shared between policymakers, civil society organisations, academics, trade unions, and coal industry International Forum for Coal Regions in Transition 2023 IISDCoal delivery equipment is one of the major components of plant cost The various steps involved in coal handling are as follows: 1 Coal delivery 2 Unloading 3 Preparation 4 Transfer 5 Outdoor storage 6 Covered storage 7 Inplant handling 8 Weighing and measuring 9 Feeding the coal into furnace Figure: Steps involved in fuel Steps involved in coal handling BrainKart2021年6月13日 Pulverizer secara stuktur merupakan system yang terdiri dari coal feeder, pulverizer dan pyrite hopper 1 Coal feeder Coal feeder merupakan pengatur flow atau banyaknya coal yang masuk ke dalam pulverizer sesuai dengan load demand Coal feeder umumnya berupa gravimetric feeder yaitu belt conveyor dengan sensor massa yang Coal Pulverizer; The introduction LinkedIn Indonesia