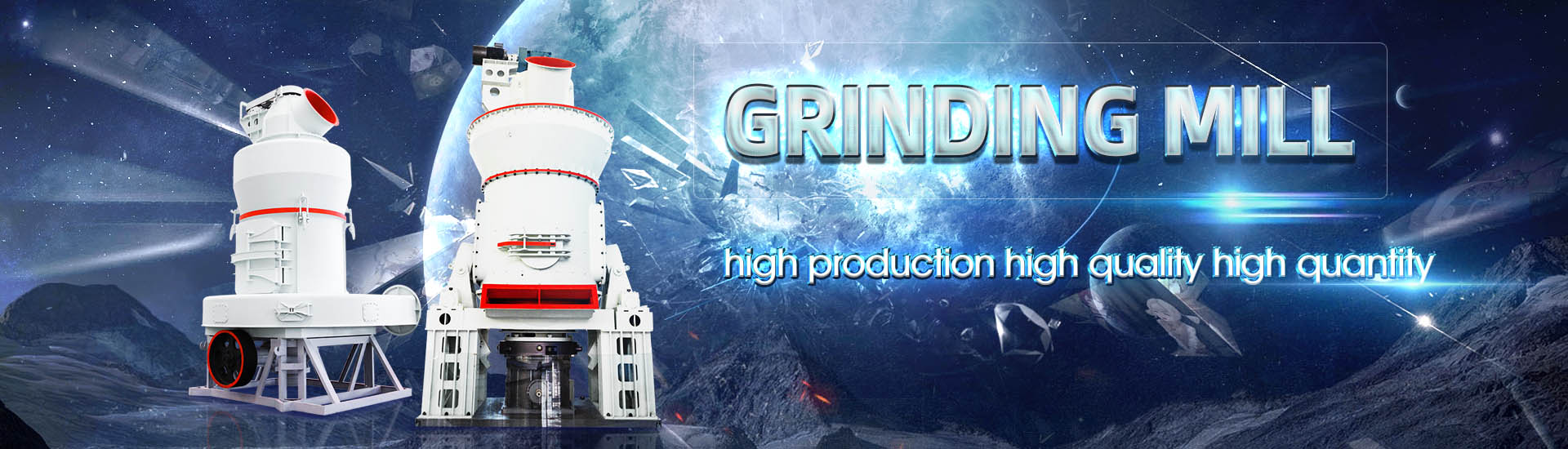
Coal mill bearing temperature
.jpg)
Coal Mill an overview ScienceDirect Topics
The temperature of the primary air is used to control the temperature in the coal mill at the classifier The temperature controller is often required to keep temperature constant at 100 °C in order to evaporate the moisture content in the coalAbstract: The paper presents development and validation of coal mill model (including the action of classifier) to be used for improved coal mill control The model is developed by using the Modeling and Control of Coal Mill通过建立LightGBM轴承温度预测模型获取磨煤机轴承温度阈值,并引入改进GWO算法优化模型超参数,以提高算法效率和性能。 试验结果表明,改进GWOLightGBM算法相比支持向量机 (SVM) 基于改进GWOLightGBM的磨煤机故障预警方法研究【维普 2020年8月12日 Obtained results indicate that grinding pressure, primary air (PA) temperature and mill motor current have a tendency to rise by increasing coal feeding mass flow rates for all used coalAn investigation of performance characteristics and
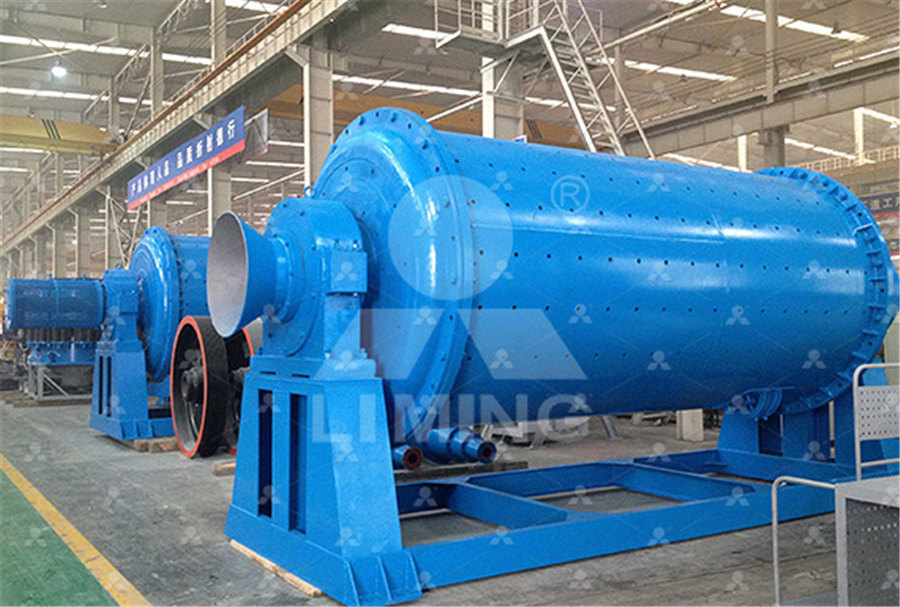
An investigation of performance characteristics and energetic
2020年8月12日 Uniform coal feeding mass flow rate and required particle size and temperature at the outlet channel throughout with better classifier performance are crucial indicators that Coals have different characteristics and heat content The behaviour of a coal in a boiler is strongly influenced by its rank and by the mineral matter and other impurities associated with Expert systems and coal quality in power generation USEA2015年11月1日 Coal mills are bottleneck in coal–fired power generation process due to difficulty in developing efficient controls and faults occurring inside the mills In this paper, a dynamic A unified thermomechanical model for coal mill operation2016年9月1日 Uniform coal feeding mass flow rate and required particle size and temperature at the outlet channel throughout with better classifier performance are crucial indicators that Operational parameters affecting the vertical roller mill

Derivation and validation of a coal mill model for control
2012年5月1日 The paper presents development and validation of a coal mill model to be used for improved mill control, which may lead to a better load following capability of power plants 2015年11月1日 From Fig 3, Fig 4, Fig 5, Fig 6 and Table 5, it can be seen that the measured outputs of the proposed model (mill differential pressure, current, outlet temperature) approach the onsite values very well and unmeasured outputs (pulverized fuel flow, mass accumulated inside the mill, outlet moisture content, moisture in accumulated coal inside the mill, mill A unified thermomechanical model for coal mill operation2020年4月7日 Monitoring and diagnosis of coal mill systems are critical to When the coal interruption fault occurs, coal powder flow needed to be dried reduces to 0, and the outlet temperature of the mill will rise rapidly In order Modeling of Coal Mill System Used for Fault Coal ball mill is mainly used in coal power plant or mineral calcining system Skip to content The main structure of coal ball mill includes the feeding part, discharging part and driving part The main bearing is made of cast steel, Coal Ball Mill Grinding for Different Kinds of
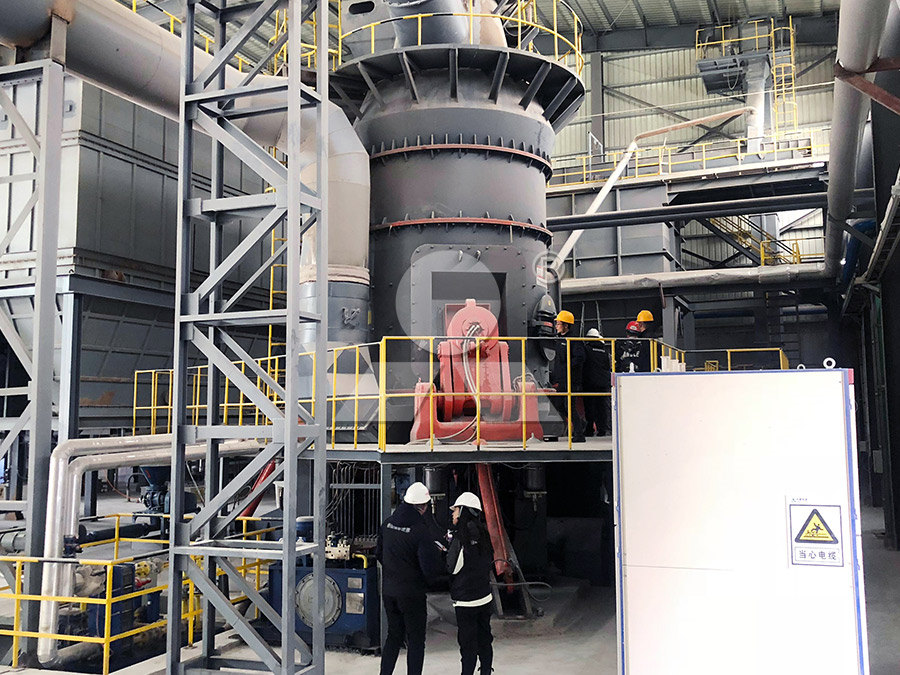
Derivation and validation of a coal mill model for control
2012年5月1日 Sensors for coal flow measurement from the mill to the furnace have become available on the market (Blankinship, 2004, Department of Trade and Industry, 2001, Laux et al, 1999)Unfortunately the equipment tends to be expensive and requires frequent calibration; thus it cannot be used directly for control purposes at this time of writing1927 First Loesche coal mill delivered for the Klingenberg power station in Berlin 1953 500th coal mill plant sold worldwide 1961 Introduction of hydraulic spring assembly system 1965 Construction of first pressure mill (LM 122 D) 1980 Delivery of first modular coal mill (LM 263 D) 1985 Delivery of first selfinerting coal grinding plant (LM 212 D) for the steel industry (PCI LOESCHEMILLSwhich can scan a numbers of RTD / Thermocouple signal As we have eight numbers (08) of coal mill and each coal mill has four outlet coal pipes, so we have to measure 32 numbers of coal pipe temperature We design and procure 32 numbers of special type surface mounted RTD Fixed the RTD on each and every coal pipe beforeMeasurement and Control of Coal Pipe Temperature of Coal Vertical Coal Mill (VCM) is equipment for grinding and pulverizing coal into micron size Rotary kilns then use the powders as fuel burners The VCM has a housing section equipped with a lining The layout of the coal mill with a rotary classifier
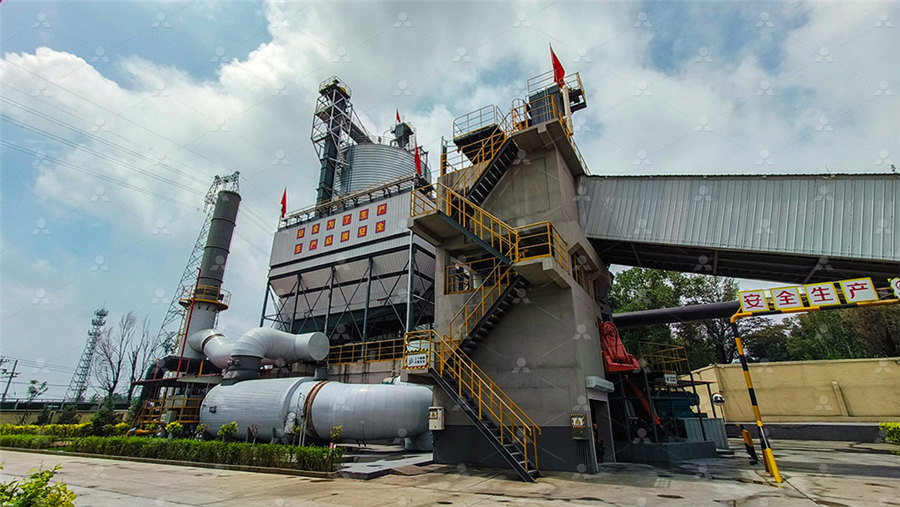
Measurement and Control of Coal Pipe Temperature of Coal
which can scan a numbers of RTD / Thermocouple signal As we have eight numbers (08) of coal mill and each coal mill has four outlet coal pipes, so we have to measure 32 numbers of coal pipe temperature We design and procure 32 numbers of special type surface mounted RTD Fixed the RTD on each and every coal pipe before2012年11月17日 20 131Fineness Fineness is an indicator of the quality of the pulverizer action Specifically, fineness is a measurement of the percentage of a coal sample that passes through a set of test sieves usually designated at 50, 100, and 200 mesh A 70% coal sample passing through a 200 mesh screen indicates optimum mill performance The mill wear and Coal mill pulverizer in thermal power plants PPT SlideSharewheel mill to dry the coal While the coal is being pulverised, the coal dust is mixed with the flue gas, resulting in a high drying efficiency The lignite/flue gas mixture is blown to the pulverised coal burner through pulverised coal pipes The N 53543V beater wheel mill is the biggest one built by ALSTOM Power to dateRolling Bearings in ALSTOM Beater Wheel Mills Schaeffler Group2020年7月1日 During the operation of No2 boiler in a power plant, the fracture of a coal mill shaft occurred The fracture causes of the coal mill shaft were found by macroscopic inspection, metallographic Fracture failure analysis of coal mill shaft ResearchGate
.jpg)
A Study on 500 MW Coal Fired Boiler Unit’s Bowl Mill
Section of coal bowl mill Table 1 Guaranteed coal conditions for mill performance evaluation Coal Moisture % 20 Coal HGI 55 Mill Outlet Temperarure °C 80 Mill Air Flow T/hr 102 Coal Fineness (% passing trough 200 mesh) 70% passing through 200 mesh and 90% passing through 50 mesh Differental Pressure 300 mmwc Coal Output from Mill 609 t/hr2015年8月1日 Mill problems originate mainly due to poor controls or faults occurring within the milling system As discussed by GQ Fan and NW Rees [3], the control of mills remains very simple in most of the power plants due to the fact that the mill system is highly nonlinear with strong coupling among the variables and it is very difficult to measure some important Review of control and fault diagnosis methods applied to coal 2020年6月14日 What are the causes for an increase of Cement Mill trunnion Bearing temperature and what are the possible solutions Cement mill trunion bearing temperature may increase due to following reasons: 1 HP pump pressure is low 2 Cutoff time of HP pump after mill start up; 3 Mixing of contamination with oil; 4 LP pump oil flow is less; 5Improving Mill Shoe Bearing Reliability and Productivity(2) The temperature of the mill is assumed to be same as the temperature of the classifier (3) Heat emitted from the mill to its environment is negligible (4) The mass change of coal causes insignificant change in the total heat capacity of the mill (5) The ambient temperature (temperature of raw coal entering the mill) , coal moisture and Modeling and Control of Coal Mill
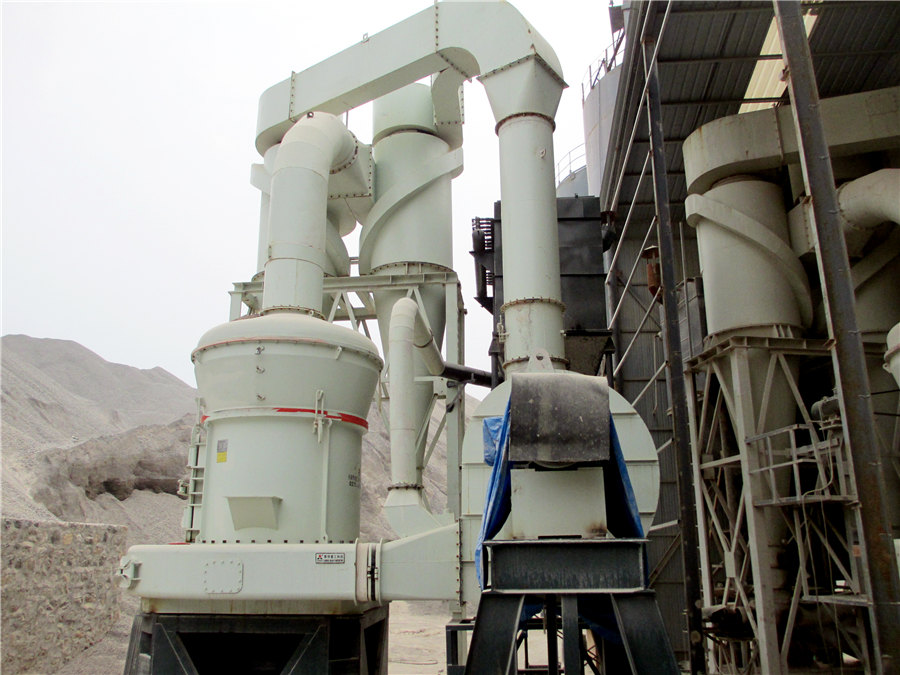
COAL GRINDING SYSTEMS SAFETY CONSIDERATIONS PEC
Coal Mill Temperatures Coal mill hot air inlet temperatures never be more than 600should F and the outlet temperature should not exceed 200°F on Raymond coal mills If the flow of raw coal to the coal mill is interrupted for any reason (for example: plugging, failure of the coal feeder, etc), the outlet temperature of the coal mill can Main bearing: the airswept coal mill is supported by the main bearing The main bearing adopts a large hollow shaft diameter structure, First, the raw coal is fed into the feed chute by the feeding device Then, the hot air with a temperature of about 300 ℃ enters through the air intake pipe and begins to dry the raw coal while they are Air Swept Coal Mill Coal Mill In Cement Plant AGICO GROUP2020年4月7日 a coal mill model used for the precise control of outlet temperature of mixture and pulverized coal flow was developed and validated, in which th e action of classifier was included Reference [14]Modeling of Coal Mill System Used for Fault SimulationAs one of the three major forces of coal mills, the grinding force exerts a significant impact on the working process of coal mills and parameters like mill current and outlet temperatureEffect of mill outlet temperature on the coal moisture content
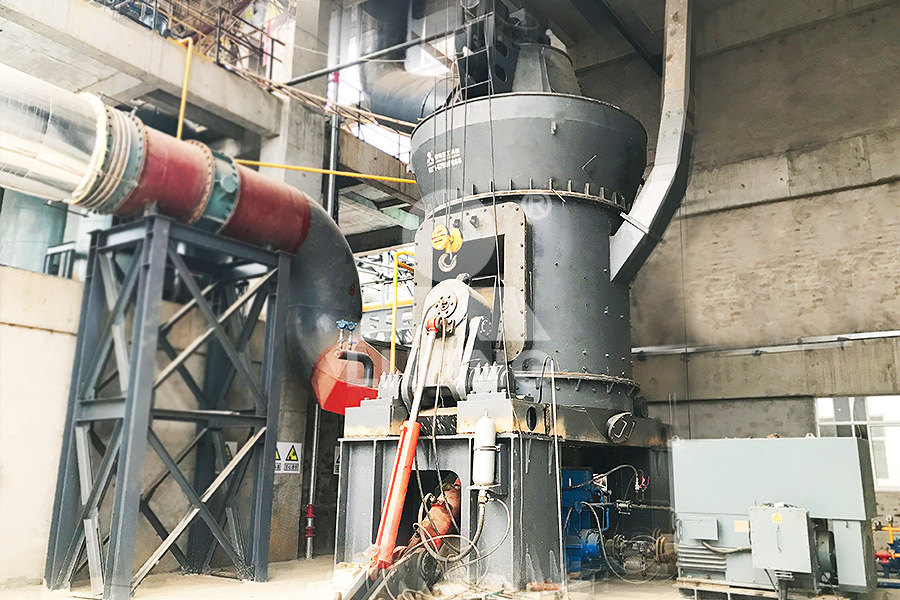
Coal Grinding Cement Plant Optimization
Mill Inlet Temperature (0 C) Mill Outlet, bag filter outlet Temperature (0 C) O2 + CO Percent at bag filter outlet and in fine coal bins Bag filter hopper and fine coal bin temperature (0 C) Elements of Coal Grinding System: Mill Feeding: Consists of following activities Coal Crusher: Generally, require when ball mill is used for grinding As one of the three major forces of coal mills, the grinding force exerts a significant impact on the working process of coal mills and parameters like mill current and outlet temperatureEffect of mill outlet temperature on the coal volatile matterGrease for raise boring roller bearings under high torque and temperature Oil for ball mill trunnion bearings Keep a problemfree operation with RCE SS, a semisynthetic oil for creating highthickness lubricating films Learn more Mining Industry Lubricants InterlubIntroduction This article concerns itself with vertical grinding mills used for coal pulverization only (coal pulverizers), although vertical grinding mills can and are used for other purposes The 3D model in the saVRee database represents a vertical grinding bowl millOther grinding mill types include the ball tube mill, hammer mill, ball and race mill, and , roll and ring millVertical Grinding Mill (Coal Pulverizer) Explained saVRee

Ball Mill Trunnion Bearing – Cast Steel 1150 Tons AGICO
AGICO manufactures ball mill trunnion bearing housings with customizable color +86 Home; Ball Mill Application Menu Toggle Cement Ball Mill; Gold Ball Mill; Coal Ball Mill; Limestone Ball Mill; Ball Mill Grinder Menu Toggle Overflow Ball Mill; Grate Discharge Ball maintains the normal operating temperature, and has a good Fine coal particles and wear metals from grinding surfaces enter the lube oil through worn bearing and shaft seals, as well as being “inhaled” through reservoir vents Historically, the design of coal pulverizers has been based on the expectation of few drive system problems under prescribed operation and maintenanceCoal Pulverizer – Power Plant Pall Corporationmenghasilkan mill outlet temperature (MOT) sebesar 336°K Hasil tersebut sudah mendekati nilai MOT yang diijinkan pada operasi coal pulveriser mill yaitu 338°K Jika temperatur udara primer dinaikkan lagi, maka dikhawatirkan akan membahayakan pengoperasian coal pulveriser mill Hasil lainnya yang diperolehSTUDI NUMERIK PENGARUH TEMPERATUR UDARA PRIMER Coal Mills are used to pulverize and dry to coal before it is blown into the power plant furnace Operation The coal is feed into the coal mill through a central inlet pipe where gravity is used to lead the coal to the bottom of the mill, where the grinding table and some heavy rollers pulverizes the coal to particlesCoal Mills SolidsWiki
.jpg)
A powersaving control strategy for reducing the total pressure
2016年8月1日 After about 30 min, the outlet temperature of mill A exceeds the set value and y off increases to −0775 kPa to control the temperature by increasing the primary air pressure of the primary air fan While y off remains −0775 kPa, the outlet temperature of mill A continues increasing to a maximum value 871 °CThe utility model discloses a heat exchange coil cools off the motor, avoids the high temperature of motor, The utility model discloses a coal mill dynamic separator, (1021) through a bearing CNU Dynamic separator of coal mill Google Patents* Technical contribution to the 11th International Rolling Conference, part of the ABM Week 2019, October 1st3rd, 2019, São Paulo, SP, Brazil BACKUP ROLL BEARING TEMPERATURE MONITORING ON A TANDEM COLD MILL * Rogério Martins Pereira1 Lucas Gabriel Correa2 Charles Pierri de Souza3 Danilo Gonçalves de Oliveira4 AbstractBACKUP ROLL BEARING TEMPERATURE MONITORING ON A TANDEM COLD MILL2019年9月28日 Detecting classifiercoal mill damage using a Bearing 3379%, Pulley 503%, and produce a Data is collected by measuring the results of temperature and enthalpy of a refrigerant (PDF) Detecting classifiercoal mill damage using a
.jpg)
Coal Mills SolidsWiki
Coal Mills are used to pulverize and dry to coal before it is blown into the power plant furnace Operation The coal is feed into the coal mill through a central inlet pipe where gravity is used to lead the coal to the bottom of the mill, where the grinding table and some heavy rollers pulverizes the coal to particlesIn 2009, coal flow and outlet temperature of mill were modelled using mass and heat balance equations for startup, shutdown and normal conditions (HwiBeom et al, 2009)Sectional view of MBF coal mill Download Scientific DiagramMultiobjective Optimization of Coal Mill Outlet Temperature Control Using MPC Zengji Zhang1, Yicheng Zhang2, Wei Shen2, BOE Xukang Lyu3,∗ 1Sinoma International Engineering Co, Ltd, Nanjing, Jiangsu, China 2College of Computer Science and Technology, Zhejiang SciTech University, Hangzhou, Zhejiang, China 3Zhejiang New Rise Digital Technology Co, Ltd, MultiObjective Optimization of Coal Mill Outlet Temperature Coal mills are used to grind and dry the raw coal containing moisture and to transport the pulverized coal air mixture to the boiler Poor dynamic performance of coal mill causes difficulties in maintaining the frequency, boiler pressure and temperature of the plant This paper presents development and validation of coal mill model for improved coal mill control The parameters Modeling and outlet temperature control of coal mill using
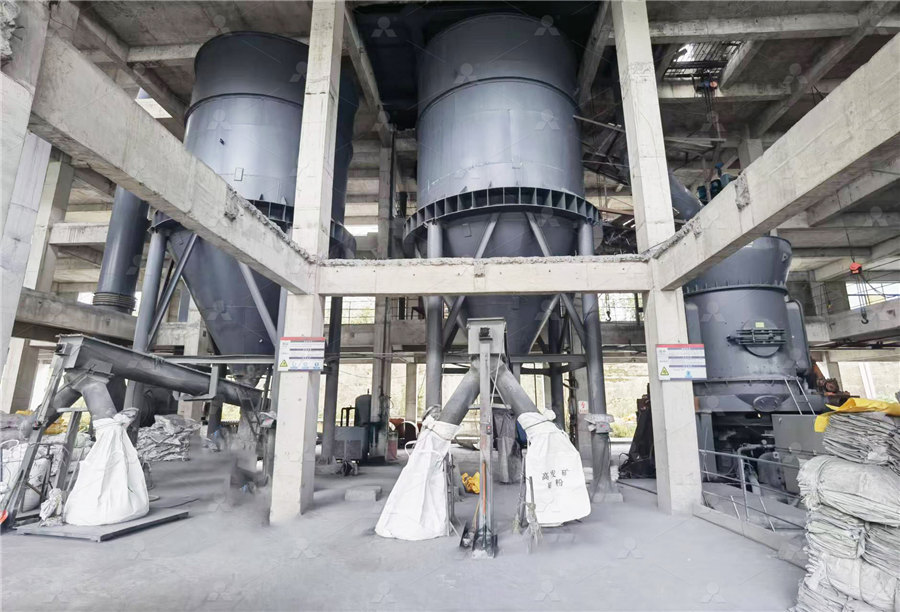
COAL PREPARATION AND FIRING INFINITY FOR CEMENT EQUIPMENT
Fine coal leaves the mill with the gas stream, the coal fineness is adjusted by altering the angle of the separator vanes, or the rotor speed Coal drying is ensured by controlling the coal mill inlet temperature, to give a target mill exit temperature, usually between 70 and 900CThe results showed that the FEGT value during cofiring was 07 % lower than during coal firing The mill outlet temperature ranges from 58 °C to 60 °C in both test conditionsThe effect of cofiring on mill outlet temperature Both of two As one of the three major forces of coal mills, the grinding force exerts a significant impact on the working process of coal mills and parameters like mill current and outlet temperatureTechnical specifications of vertical roller coal mill2009年9月1日 The coal mill used in the coalfired power plants is modeled in view of the controller design rather than the educational simulator The coal mass flow and the outlet temperature are modeled by reinvestigating the mass balance and heat balance models physically The archived data from a plant database are utilized to identify the model Modeling and Parameter Identification of Coal Mill