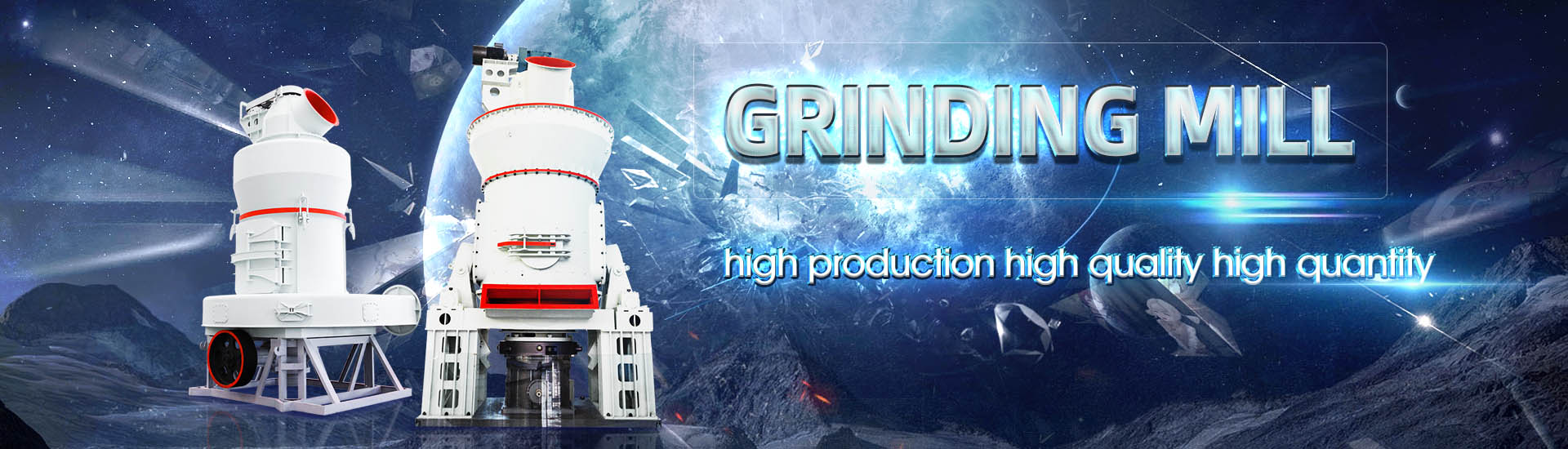
What is the size of the 1060 ore mill body
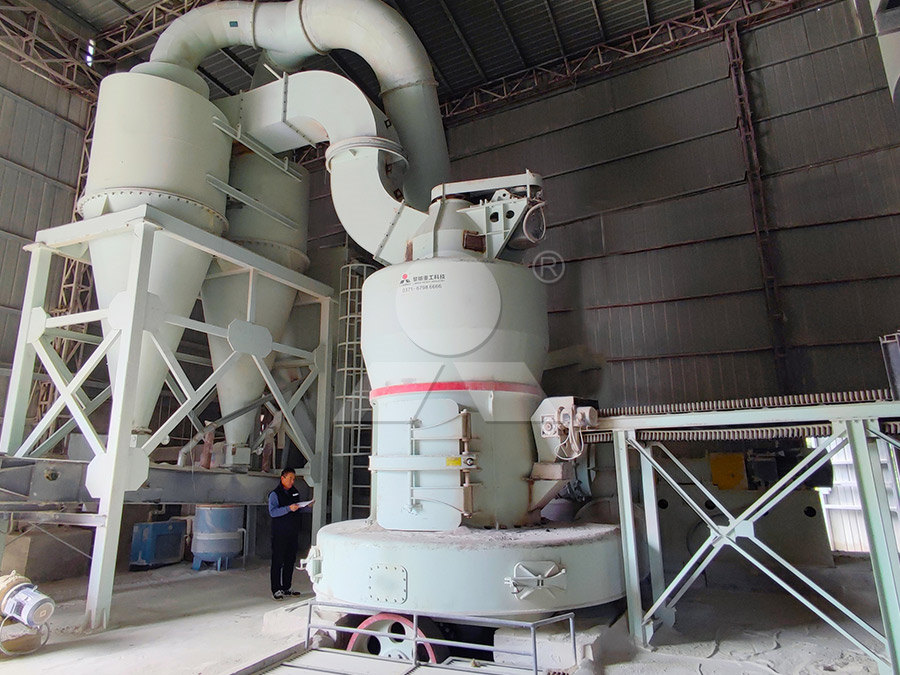
(PDF) Mining Methods: Part ISurface mining ResearchGate
2010年3月1日 size and shape of the orebody) that is used when the ore body is typically pipeshaped, veintype, steeply dipping stratified or irregular Although it is most often associated with metallicramp, measure 45m wide x 4m high Ore drift dimensions vary according to: (i) vein width and attitude on the level, and (ii) geological structures that may influence the size and shape ofNarrow vein mine design at the Hoyle Pond mine ResearchGate2017年9月1日 This paper aims to explore these observations further, focusing on the two fine grinding devices and the breakage mechanisms therein, size by size shape characteristics Fine grinding: How mill type affects particle shape characteristics 2016年1月1日 While criticalsize could be of any dimension, it is most typically synonymous with pebblecrusher feed, with a size range of 13–75 mm Criticalsized particles can result from a Comminution Circuits for Gold Ore Processing ScienceDirect
.jpg)
Three factors that determine the wear life and performance of mill
Mill type Mills come in many shapes and sizes Mills are always individual, with smaller or larger differences in how they are operated, which ore is processed, which type of grinding media is Over a relatively short time period taking a belt cut and sieving the material is the most accurate method of determining the size distribution of the ag/sag mill feed However, fluctuations in I203 I204 INTRODUCTION SMC Testing2023年7月20日 According to the different grinding medium, the grinding mill is divided into three types: (1) ball mill – it is used widely, and almost all materials can be triturated by ball mill; (2) Ore Grinding SpringerLinkWhile tower mills are typically limited to 1012mm fresh media sizing, the IsaMillTM can use media as small as 1mmIsaMill Technology Used in Effecient Grinding Circuits
.jpg)
Comminution SpringerLink
2015年2月2日 As with any material, rock particles only break when the applied tensile stress exceeds the tensile strength of the rock However, in terms of comminution, the main interest is to derive reliable ways of assessing how a particular material breaks in a comminution device such as a crusher or a mill []In general, the breakage of rock particles is dependent on two factors: 2015年6月1日 Within geometallurgy the entire ore body is explored in order to further particle size range of the mill product is suitab le to perform Miner Eng 2009, 22, 1060–1067 (PDF) Testing of Ore Comminution Behavior in the 2015年4月15日 For each ball mill grinding step, a Bond ball mill grindability test for Work Index at one mesh size coarser than the desired 80% passing size and at the mesh size of or just finer than the 80% passing size If 50 mm x 75 mm What Ore Testing is Required For Mill Selection2023年6月27日 The size of the barite ore after crushing is uneven, and the beneficiation equipment generally has its own required input size and size range Therefore, the crushed barite ore after screening can optimize the following separation process, which improves the separation efficiency and separation indicators of the separating equipmentWhat Is The Process Of Barite? Eastman Rock Crusher
.jpg)
CHAPTER 9: ORE DEPOSIT GEOLOGY SGU
Table 1: Table of selected common ore minerals Ridley, J (2013) “What is an ore deposit?,” in Ore Deposit Geology Cambridge: Cambridge University Press The significance of ore deposit size The small and shortlived mining operations, like narrow veins stockwork, would typically be ore bodies of about 1 Mt2018年8月17日 The concept of ore blending is a very relevant notion in modern high tonnage production mines It is not only essential for the prolongation of the mine life of the concerned mine but as well as a The effects of ore blending on comminution behaviour and 2013年3月9日 The sintering process is used to agglomerate a mix of iron ores (blend), return fines, fluxes and coke, with a particle size of less than 10 mm, so that the resulting sinter, with a screened size of 10 mm to 30 mm, can withstand pressure and temperature conditions in the blast furnace Principle of sinteringThe Sintering Process of Iron Ore Fines – IspatGuruwhich reduces the size of the ore to be further refined, and the valuable particles separated Or, in the case of industrial minerals, used as is Grinding is often done in steps: a primary mill grinds the largesized ore and then a secondary mill grinds the ore Three factors that determine the wear life and performance of mill
.jpg)
Ore Body, Shapes and Occurrence of SpringerLink
2022年12月27日 When most of the ore body is exposed to the surface or buried at a shallow depth, the ore body can be mined after stripping, called an openpit ore body The ore body buried underground and not exposed to the surface is called a blind ore body (3) The connection between ore body and rock stratum2016年2月26日 The hammer mill is the best known and by far the most widely used crushing device employing the impact principle of breaking and grinding stone Thus far we have described machines which do a portion of their work by impact, but the only machine described in which this action plays an important role was the sledging roll type and particularly the Edison roll crusher Hammer Mill Crusher Grinder 911Metallurgist2013年7月15日 For any circuit, whether a crushing circuit, a rod mill, or a closed ball mill circuit, the Work Index always means the equivalent amount of energy to reduce one ton of the ore from a very large size to 100 um The sample was Bond Work Index FormulaEquation 911Metallurgist2017年7月26日 Soft ore Work Index 13 = 100,000/90,000 = 11 kwh/t Hard ore Work Index 16 = 100,000/65,000 = 154 kwh/t For the purposes of this example, we will hypothesize that the the crushing index of the hard ore with the increased energy input of 154 kw/t reduces the ball mill feed size to 6,500 micrometersHow Ball Mill Ore Feed Size Affects Tonnage Capacity
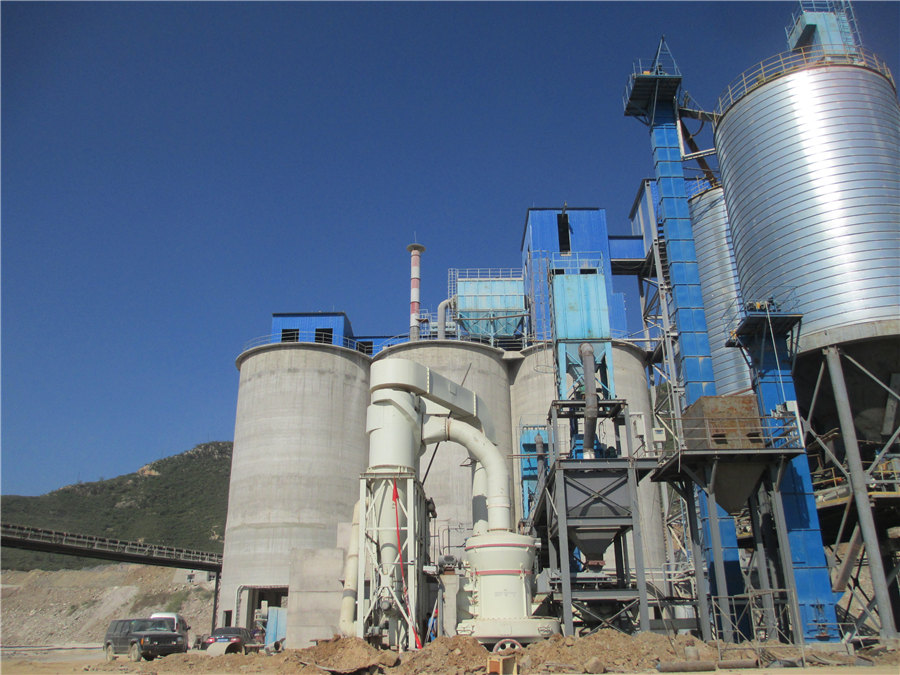
Gold Extraction Recovery Processes
2016年2月29日 A finer size can be considered if the ore needs fine liberation The leach cycle is normally from 20 to 30 days When the leaching cycle is complete, a new crushed ore is piled The second option is the most 2019年9月24日 There are numerous examples in the literature, some of which are quantifying the effect of Mine to Mill Grundstrom et al, 2001;Hart et al, 2001;Scott et al, 2002;Burger et al, 2006;Jankovic et al Simulating the Impact of Ore Competence Variability on Process Understanding Mine to Mill is presented in five parts Part A – Setting the Scene provides some definitions of Mine to Mill (M2M) and the historical background A chronology of Mine to Mill developments is followed by brief descriptions of the very wide range of Mine to Mill applications which have been implemented over the last 15 yearsUNDErsTaNDINg MINE TO MILL 911 MetallurgistThe rod mill is another type of grinding mill used in the copper ore mining process This machine uses steel rods as the grinding media instead of balls, which are commonly used in ball mills The rods grind the ore by tumbling within the mill, similar to the action of a rotating drumUnderstanding the SAG Mill in Copper Ore Mining Process
.jpg)
The six main steps of iron ore processing Multotec
This step involves breaking up the iron ore to obtain an F 80 grind size before it can be ground Once the ore has been crushed, it is diverted to a stockpile The aim of this step is to ensure a smooth crushing process and minimise downtime in the event of a breakdown or to allow planned maintenance in the crushing system, without stopping the grinding and other further steps2018年12月1日 Geometallurgy is an important addition to any evaluation project or mining operation As an integrated approach, it establishes 3D models which enable the optimisation of net present value and effective orebody management, while minimising technical and operational risk to ultimately provide more resilient operations Critically, through spatial identification of Geometallurgy—A Route to More Resilient Mine OperationsThe size, which is around 50–80 mm, of the ore or rock from the secondary crushing process is reduced to between 5 and 12 mm Toggle plate compressed between moveable jaw and main body What is Blade Mill?Blade mill is designed to separate, crush, What Is A Jaw Crusher MEKA2015年6月19日 The basic parameters used in ball mill design (power calculations), rod mill or any tumbling mill sizing are; material to be ground, characteristics, Bond Work Index, bulk density, specific density, desired mill tonnage capacity DTPH, operating % solids or pulp density, feed size as F80 and maximum ‘chunk size’, product size as P80 and maximum and finally the type of Ball Mill Design/Power Calculation 911Metallurgist
.jpg)
SAG Mill Testing Test Procedures to Characterize Ore Grindability
size reduction in a comminution device Because grinding theories are imperfect and ore hardness can vary with size, grindability tests are designed to best represent the size reduction of the industrial equipment analysed For that reason, it is preferable to design a primary ball mill from a rod mill work index rather than a ball mill2020年3月27日 Strength is a critical factor in metal uses, for example, some applications require stronger aluminum parts, while some products need high steel hardness or yield strength of steel, this may determine the selection of Metal Strength Chart – Mechanical Properties Chart 2018年4月8日 Referring to Table VI the L/D can be between 175 and 20 or even greater Referring to Table VII a 305 meter (10 foot) by 305 meter (10 foot) overflow ball mill with a 40 percent by mill volume ball charge, new liners and How to Size Design a Regrind Ball MillWhat is Blade Mill? Blade mill is designed to separate, crush, wash and clean aggregates and crushed stones ranging in size from 0 to 75 mm from sticky clay in order to increase screening efficiency, often used before screening Blade mill is manufactured in different sizes as single or double shaft according to the size of the work to be done, capacity, rock size and contentWhat is Blade Mill? Working Principle and Advantages
.jpg)
Reduction of Fragment Size from Mining to Mineral Processing: A
2022年10月4日 A notable fact is that the energy efficiency of conventional milling is only about 1%, as mentioned in Sect 1 An earlier experimental study indicated that about 80–90% of the energy input of a ball mill was used in heating the material (Schellinger 1951, 1952), and a recent study showed that over 75% of the electrical energy was used to heat the slurry (Bouchard et 2023年7月20日 According to the different grinding medium, the grinding mill is divided into three types: (1) ball mill – it is used widely, and almost all materials can be triturated by ball mill; (2) rod mill – its efficiency is relatively high with the feeding particle size less than 30 mm and the product particle size around 3 mm, and the produced product particle size is uniform with less Ore Grinding SpringerLink2020年1月3日 Iron ores obtained from different sources differ in their chemical and physical properties These variations make the process of grinding a difficult task The work carried out in this context focuses on three different samples of iron ore, viz, high silica high alumina, low silica high alumina, and low silica low alumina The grinding process for all the three iron ores is Estimation of Grinding Time for Desired Particle Size Distribution Aimix’s PE series ore crusher can crush large pieces of limestones The largest broken particle size is 1000 * 1200mm Skip to content Menu Home; Products as selfgrinding machines The grinder mainly includes coarse grinding, micro grinding, highpressure grinding, Raymond Mill, straight grinding, selfgrinding machine, ball mill Ore Crusher PE Series Jaw Type Ore Crusher AIMIX GROUP
.jpg)
Reengineering of the ore preparation production process in the
material Depending on the size of the resistance during crushing, the ores are classified by hardness: soft (less than 10 MPa); medium hard (10 – 50 MPa); solid (more than 50 MPa); very hard (more than 100 MPa) [4, 5] When the ore is crushed, the elastic and plastic deformations of the crushed body appear,2016年3月19日 The EXAMPLE Gold Mill is designed to process 500 tonnes per day of ore The flowsheets are conventional and consist of two stages of crushing, single stage ball mill grinding, cyanidation and a MerrillCrowe precipitation circuit for gold and silver recoveryOperating Costs of Gold Processing Plant 911Metallurgist2021年1月14日 energy required which in this case was to grind the ore represented by the samples, from a feed size F80 of 152 mm to 80% passing 17 mm, and a simple adjustment procedure in case the SAG product size needed to be adjusted Bond rod and ball mill work indices are readily converted to pinion energy for rod and ball mills but not for SAG parison of Ore Hardness Measurements for Grinding Mill Within an ore body, valuable minerals are surrounded by gangue and it is the primary function of mineral processing, to liberate and concentrate those valuable minerals 13 RunOfMine Material and Minerals Generally, mineral Introduction to Mineral Processing or Beneficiation
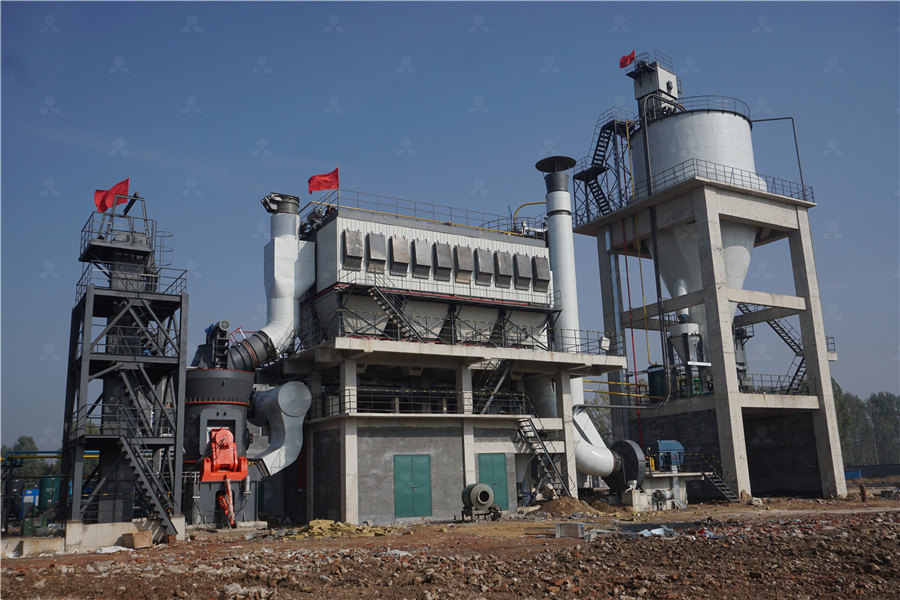
AMIT 135: Lesson 7 Ball Mills Circuits – Mining
Save wear on the steel body; Assist the lift of the media and ore to the desired height in the mill Calculate the mill size required to handle the desired throughput: Solution: W = 10*1125(1/√100 – 1/√100 0) kWt/t = 10125 2016年3月21日 where R represents the ratio: % Pb in crude ore/% Cu in crude ore Formula (32) is very convenient for milling calculations on ores of this type Example: An ore contains 5% lead and 1% copper The ratio of perfect concentration for a concentrate of maximum grade and 100% recoveries of lead and copper would be:Common Basic Formulas for Mineral Processing CalculationsThe dosage of a collector is an important factor that determines the efficiency of a froth flotation process The representative sample of the carbonatitic Palabora copper ore ground 45 % passing Particle size distribution (PSD) of the mill feed2018年10月10日 *Correspondence: MrBiLin@163; Tel: +8673188877665 (ext 8002)Implicit 3D Modeling of Ore Body from Geological Boreholes
.jpg)
Testing of Ore Comminution Behavior in the Geometallurgical
2014年6月3日 Within geometallurgy the entire ore body is explored in order to further identify the variation within the resource and to The particle size range of the mill product is suitable to perform mineral liberation analyses Table 3 Eng 2009, 22, 1060–1067 [Google Scholar] Walters, S; Kojovic, T 2017年10月1日 Feurstenau, JJ, Lutch, A de, (1999) The effect of ball size on the energy efficiency of hybrid pressure roll mill/ ball mill grinding, power technology 204(PDF) Determining optimum wet milling and leaching parameters for 2017年2月13日 In all ore dressing and milling Operations, including flotation, cyanidation, gravity concentration, and amalgamation, the Working Principle is to crush and grind, often with rod mill or ball mill, the ore in order to liberate the minerals In the chemical and process industries, grinding is an important step in preparing raw materials for subsequent treatmentBall Mills 911MetallurgistThe ore is fed into the mill through a large diameter inlet, and the rocks are broken down into smaller pieces by the impact of the ore against the inside of the mill The product from the AG mill is usually fed directly to a ball mill, which operates in a closed circuit with a cyclone Differences Between SAG and AG MillWhat is the Difference Between SAG and AG Mill? ball mills