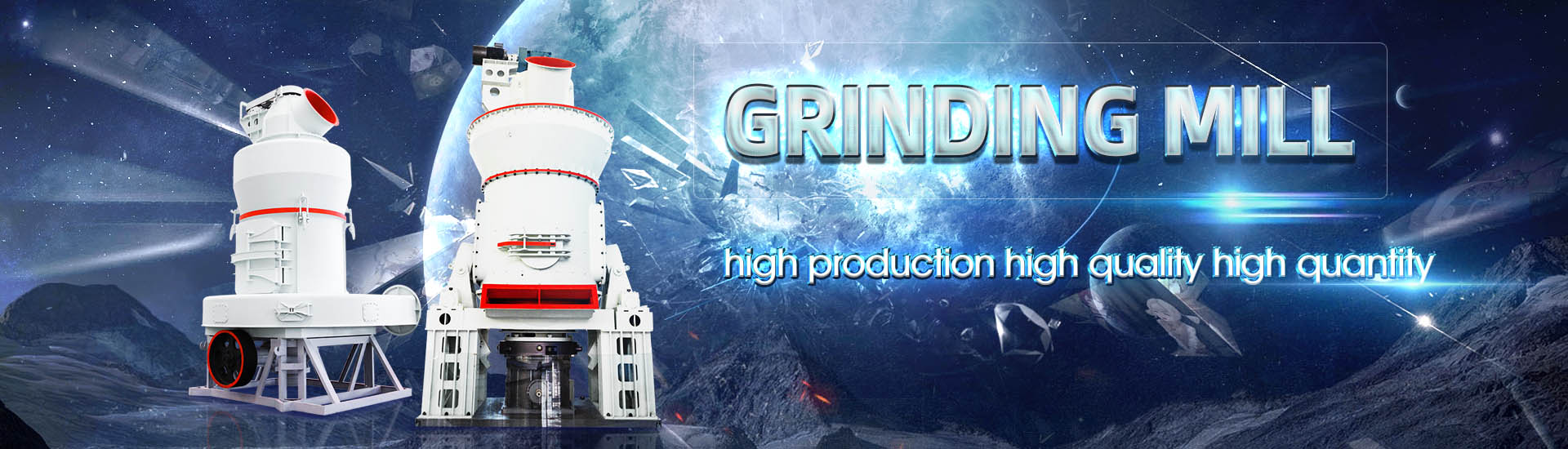
Ore mill quicklime sleeve processing
.jpg)
Oily cold rolling mill sludge conditioned by quicklime to improve
2023年7月20日 Quicklime, a necessary fusing agent in the iron ore sintering process, is used to control the composition and improve the performance of sintered ore The main component of Full Size TableQuicklime was selected as the best conditioning agent through conditioning–dewatering experiments because it could effectively reduce the viscosity of oily CRM sludge and improve the dewaterability of the oil sludge Enhancing the Dewaterability of Oily Cold Rolling Mill 2022年11月25日 Quicklime was selected as the best conditioning agent through conditioningdewatering experiments because it could effectively reduce the viscosity of oily CRM sludge and improve theEnhancing the Dewaterability of Oily Cold Rolling Mill
.jpg)
Enhancing the Dewaterability of Oily Cold Rolling Mill Sludge
2022年12月12日 Quicklime was selected as the best conditioning agent through conditioning–dewatering experiments because it could effectively reduce the viscosity of oily 2023年7月20日 The optimal parameters for conditioning oily CRM sludge were quicklime dosage of 187%, temperature of 54 °C, and time of 433 min, which resulted in filter cake SRF of 050 Oily cold rolling mill sludge conditioned by quicklime to improve The optimal parameters for conditioning oily CRM sludge were quicklime dosage of 187%, temperature of 54 °C, and time of 433 min, which resulted in lter cake SRF of 050 × 1010 Oily cold rolling mill sludge conditioned by quicklime to improve Dewatering is critical to oily cold rolling mill (CRM) sludge treatment Therefore, finding an efficient, energysaving, and applicable dewatering technology for oily CRM sludge is still Oily cold rolling mill sludge conditioned by quicklime to improve
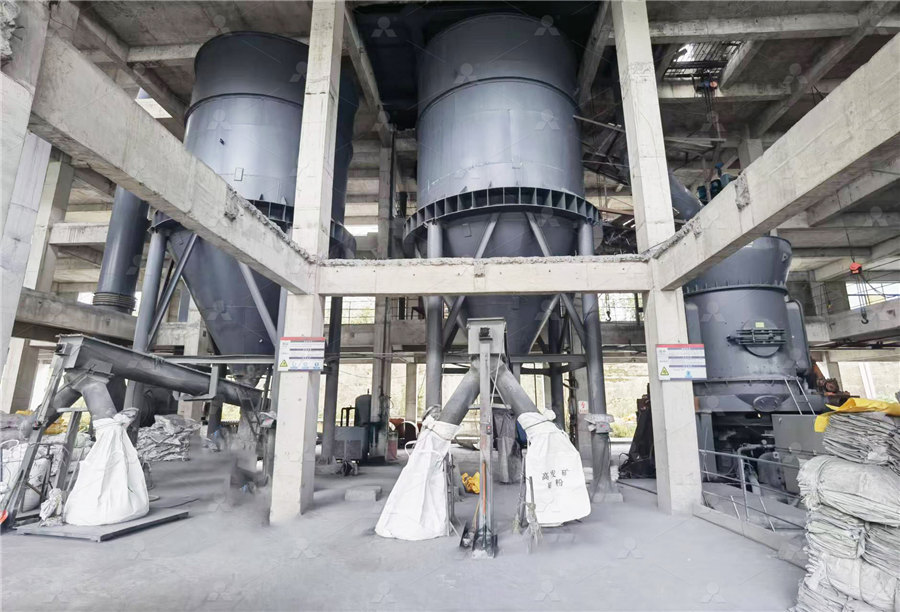
Enhancing the Dewaterability of Oily Cold Rolling Mill Sludge
infooutlined Nodes are locations in the document that facilitate reading from beginning to end You can navigate node by node or select one to jump to2013年10月17日 The compound methods of “vacuum distillation + oxidizing roasting” and “vacuum distillation + hydrogen reduction” were employed for the recycle of oily cold rolling Recycle of valuable products from oily cold rolling mill sludge2019年11月1日 Lime (calcium oxide or calcium hydroxide) is arguably the most common reagent used in the extractive minerals processing industry As an effective and economic pH modifier, Lime use and functionality in sulphide mineral flotation: A review2022年11月25日 The high moisture and viscosity characteristics of oily cold rolling mill (CRM) sludge led to limitations in its recycling In this paper, the results of using quicklime as a conditioning agent to Enhancing the Dewaterability of Oily Cold Rolling Mill
.jpg)
Gold Ore Roasting Plant 911Metallurgist
2016年6月1日 Ground ore is discharged from the grinding mill product recovery baghouse and collected in the roaster feed silos The ore processing activities (such as mining Lime comes out of ground as limestone, add heat you get 2023年12月8日 Limestone Properties The main component of limestone is calcium carbonate (CaCO3), with a Mohs hardness of 3 After limestone is mined from limestone, it is crushed to form limestone particles, that is, stone and Limestone crushing technology and equipment SBM 2019年8月3日 In the treatment of goldbearing polymetallic sulfide mineral ores with high content of valuable heavy metals (such as goldcontaining polymetallic sulphide ores containing copper, copper, zinc, lead, zinc, antimony, arsenic, etc), since these ores contain To eliminate harmful factors, in order to eliminate unfavorable factors, in the actual production process, the flotation Lime in Gold Ore Mining Process Flotation, Cyanidation JXSCApplication field: Coal vertical mills are widely used in cement production, calcium carbonate crushing processing, coal powder preparation stations, gypsum powder processing, power plant desulfurization, phosphate rock grinding, metallurgical industry and HighEfficiency Vertical Coal Mill Enhancing Coal Pulverization
.jpg)
Simulating the Impact of Ore Competence Variability on Process
2019年9月24日 There are numerous examples in the literature, some of which are quantifying the effect of Mine to Mill Grundstrom et al, 2001;Hart et al, 2001;Scott et al, 2002;Burger et al, 2006;Jankovic et al 2016年2月1日 spent on processing waste as ore in the mill It is clear that the mill processing costs would increase directly by an Monitoring ore loss and dilution f or minetomill integration in deep gold Monitoring ore loss and dilution for minetomill integration in It is the chore of the mill manager to decide what methods or techniques will be used to obtain the valuable commodity Treating ore by milling is generally a twostep process, first the ore must be crushed, then the crushed ore must be treated to separate Winning the Metal: Ore Mills of the West Western Mining History2017年1月1日 An increase of over 10% in mill throughput was achieved by removing the ball scats from a single stage SAG mill These scats are non spherical ball fragments resulting from uneven wear of balls Performance optimization of an industrial ball mill for chromite processing
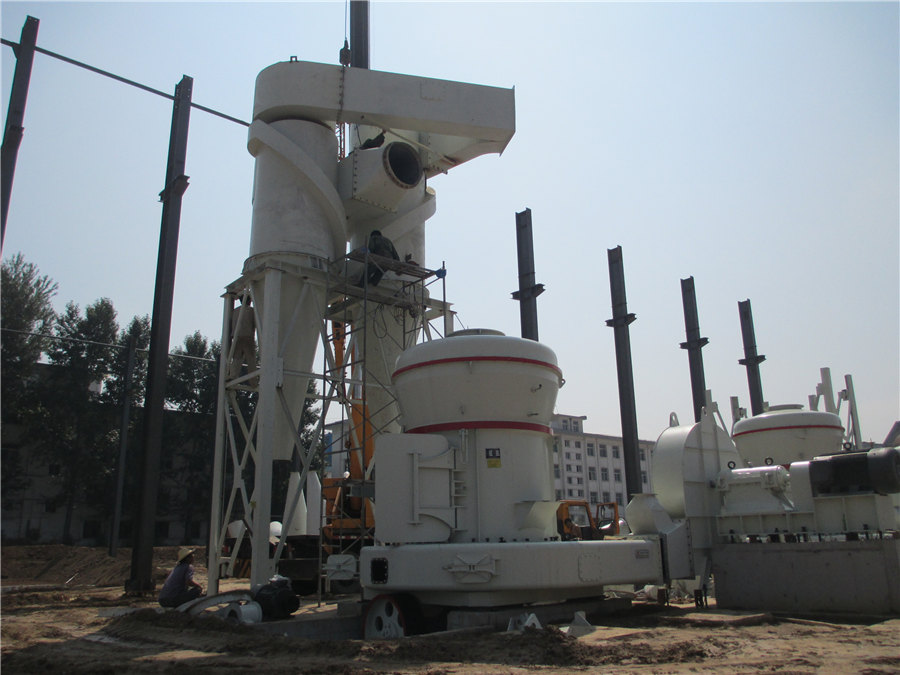
Copper Mining and Processing: Processing Copper Ores
Copper processing is a complicated process that begins with mining of the ore (less than 1% copper) and ends with sheets of 9999% pure copper called cathodes, which will ultimately be made into products for everyday useThe most common types of ore, copper oxide and copper sulfide, undergo two different processes, hydrometallurgy and pyrometallurgy, respectively, 2015年7月28日 If you take a sample of ground ore, heat it until it is completely dry Take 500 grams of that sample, and 911 Metallurgist is a trusted resource for practical insights, solutions, and support in mineral processing engineering, How to do a Sieve Analysis 911Metallurgist1 Raymond mill is used for quicklime powder making It is recommended to use Raymond mill for the processing of quicklime with an output of 1 to 9 tons and a mesh of 80 to 400 meshes CLIRIK Machinery's new Raymond mill is used as How to choose quicklime powder grinding mill?2019年8月16日 Mining, mineral processing and metal extraction are undergoing a profound transformation as a result of two revolutions in the making—one, advances in digital technologies and the other, availability of electricity from renewable energy sources at affordable prices The demand for new metals and materials has also arisen concurrently This necessitates Future of Mining, Mineral Processing and Metal Extraction Industry
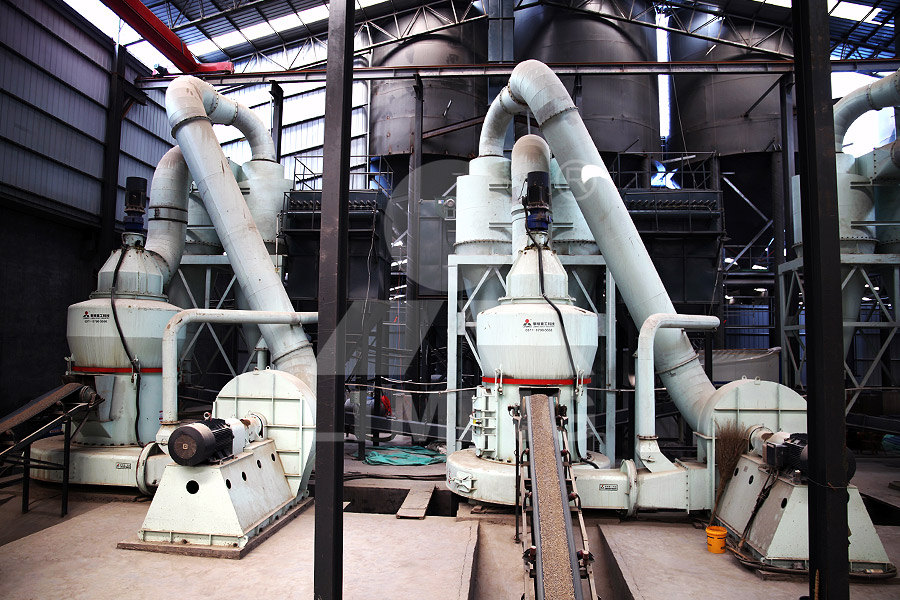
Ore mill, Ore grinding mill All industrial manufacturers
Find your ore mill easily amongst the 42 products from the leading brands (Fritsch GmbH, Retsch, Eriez By the late 1990s the HPGR became standard equipment for processing iron ores Successful hard rock mining installations followed about a decade later and HPGR applications Compare this product Remove from comparison tool See the Media Attributions; Metal deposits are mined in a variety of different ways depending on their depth, shape, size and grade Relatively large deposits that are quite close to surface and somewhat regular in shape are mined using openpit mine methods (Figure 815 in Section 81)Creating a giant hole in the ground is generally cheaper than making an underground 82: Mining and Ore Processing Geosciences LibreTextsWithin an ore body, valuable minerals are surrounded by gangue and it is the primary function of mineral processing, to liberate and concentrate those valuable minerals 13 RunOfMine Material and Minerals Generally, mineral processing begins when an ore is delivered from a mine, to a processing facilityIntroduction to Mineral Processing or BeneficiationA mine can have numerous boring machines working at different locations to provide a continuous supply of ore to feed the processing mill Conveyors carry raw ore to storage areas underground until it is raised up to the surface for milling Buckets called skips take the ore up to the surface in a continuing cycle that takes 90 seconds to completePotash Mining and Processing Infographic
.jpg)
How Ball Mill Ore Feed Size Affects Tonnage Capacity
2017年7月26日 Soft ore Work Index 13 = 100,000/90,000 = 11 kwh/t Hard ore Work Index 16 = 100,000/65,000 = 154 kwh/t For the purposes of this example, we will hypothesize that the the crushing index of the hard ore with the increased energy input of 154 kw/t reduces the ball mill feed size to 6,500 micrometers2016年1月1日 Gold Ore Processing (Second Edition) Project Development and Operations 2016, Pages 447484 Chapter 27 Alternative Lixiviants to Cyanide for Leaching Gold Ores Author links open overlay panel MG Aylmore Show more Outline and the residues from mill liners in gold plantsAlternative Lixiviants to Cyanide for Leaching Gold Ores2022年4月20日 The processing of limestone is mainly to crush, classify and produce quicklime, slaked lime, precipitated calcium carbonate, ultrafine (nano) calcium carbonate, carbon dioxide, etc Limestone generally adopts dry crushing process For limestone used in metallurgy and roads, the ore can be crushed and screenedLimestone crushing and grinding production line SBM Ultrafine 2017年2月16日 Tin Ore Processing The methods employed in dressing the tin ore up to the required percentage of purity depend mainly on the type of ore crushed The ore is conveyed to the mill over a distance of seven miles by a 2foot gauge railwayTin Ore Processing 911Metallurgist
.jpg)
The six main steps of iron ore processing Multotec
When iron ore is extracted from a mine, it must undergo several processing stages Six steps to process iron ore 1 Screening We recommend that you begin by screening the iron ore to separate fine particles below the crusher’s CSS 2016年3月21日 The control of a milling operation is a problem in imponderables: from the moment that the ore drops into the mill scoop the process becomes continuous, and 911 Metallurgist is a trusted resource for practical insights, Common Basic Formulas for Mineral Processing 2022年12月22日 CLRM series Raymond mill Processing fineness: 200400 mesh (080037mm) Standalone production capacity: 3560T/H (depending on the model) Scope of application: It is suitable for quicklime grinding and processing, requiring large output, low energy consumption, and intelligent environmental protection Five core technologies:Type Selection of Quicklime Deep Processing Equipment2016年1月12日 GOLD ORE CRUSHING PLANT In the experimental mill the ore is crushed in rockbreakers and Krupp drycrushing ballmills without drying This plant was formerly used to crush oxidized ore for chlorination and, being on the spot, it was naturally utilized in preference to buying new machineryProcessing Gold Ore by Flotation 911Metallurgist
.jpg)
All About Particles: Modelling Ore Behaviour in Mineral Processing
of an ore to liberate the ore minerals from the gangue minerals Thus, comminution strongly controls the overall efficiency of a mineral processing operation Even though blasting as the first step of extracting an ore from the ground is also a form of comminution, the focus here is on the processes occurring in comminution devices:The rod mill is another type of grinding mill used in the copper ore mining process This machine uses steel rods as the grinding media instead of balls, which are commonly used in ball mills The rods grind the ore by tumbling within the mill, similar to the action of a rotating drumUnderstanding the SAG Mill in Copper Ore Mining Process2021年5月31日 Ore blending can also ensure that the feed is uniform during ore processing, JM Kinetics of DryBatch Grinding in a LaboratoryScale Ball Mill of Sn–Ta–Nb Minerals from the Penouta Mine (PDF) A Method of Ore Blending Based on the Quality of 2016年6月2日 Before the event of ore dressing, crude ores were shipped directly to the smelters, or the refineries, with the shipper paying the freight and treatment 911 Metallurgist is a trusted resource for practical insights, solutions, and support in mineral processing engineering, helping industry professionals succeed with proven expertise Mineral Processing and Ore Mineral Processing and Ore Dressing 911Metallurgist
.jpg)
Oily cold rolling mill sludge conditioned by quicklime to improve
2023年7月20日 The high moisture and viscosity characteristics of oily cold rolling mill (CRM) sludge led to limitations in its recycling In this paper, the results of using quicklime as a conditioning agent to 2019年8月29日 methods of processing the ore are gravity separatio n and flotation In 2016, a plant including XRT ‐ based ore sorting was commissioned for waste rejection f rom a marginal development waste dump,(PDF) Sensor‐Based Ore Sorting Technology in 2005年12月2日 PDF Minerals recovery from the earth's crust and the subsequent processing of economic mineral deposits, ie, ores, mineral processing plant or mill affects the costs of fuel, power, wate r (PDF) Minerals Recovery and ProcessingTechnology and technics of ore preparation processes 13 High pressure grinding rolls were successfully introduced in the cement industry in the late 1980s and enabled appreciable reduction in energy consumption Promptly enough their potential was realized in mineral mining industry Strikingly efficient in diamond ore processing, HPGR immeHIGH PRESSURE GRINDING ROLLS—A PROMISING AND COST
.jpg)
Iron Ore Supply Chain: From Mining to Steel Production
2023年10月25日 Iron ore is a crucial raw material for the global steel industry, and its supply chain is a complex network that involves multiple stakeholders and activities The iron ore supply chain begins with the mining of iron ore, which is then transported to processing plants for beneficiation and further refinement The refined iron ore is then transported to steel mills for The construction of the underground mine and mill complex with an initial milling capacity of 1,360 metric tons/day (1,500 tons/day was com pleted in 1976 increased to 1,590 metric tons/day (1,750 tons/day) and then in early 1981 after a major expansion to 2,086 metric tons/day (2,300 tons/day) Geology, Ore Reserve and Ore ControlUNDERGROUND AND PYROCHLORE ORE PROCESSING Niobium2022年12月12日 1 Introduction The oily cold rolling mill (CRM) sludge is a solid waste generated from the cold rolling steel process comprising a dense slurry of iron fines in lubricating oil and water with other impurities including heavy metal 1 The oil in CRM sludge is derived from lubricants and equipment used in the cold rolling process of steel products 2 According to Enhancing the Dewaterability of Oily Cold Rolling Mill Sludge 2017年3月20日 Physicochemical Problems of Mineral Processing Investigation on the particle size and shape of iron ore pellet feed using ball mill and HPGR grinding methods March 2017 DOI: 105277/ppmpPhysicochemical Problems of Mineral Processing Investigation
.jpg)
What is Quicklime and How is it Made? Science Struck
The production of quicklime is one of the oldest chemical processes developed by mankind But there is often a lot of confusion between terms like lime and quicklime Are you wondering what quicklime is, and what it is made of? Then you've come to the right page! ScienceStruck gives you a lot of information about quicklime, and explains how it is industrially made2016年5月26日 In mineral processing, the Akins AKA spiral or screw Classifier has been successfully used for so many years that most mill operators are familiar with its 911 Metallurgist is a trusted resource for practical insights, solutions, and support in mineral processing engineering, helping industry professionals succeed with proven expertise Types of Types of Classifiers in Mineral Processing 911MetallurgistThe present study investigates the propensity of predicting ore grindability characteristics and varying pulp densities through acoustic measurements on the Magotteaux ball millA typical flowsheet for processing refractory gold ore (Sulphidic