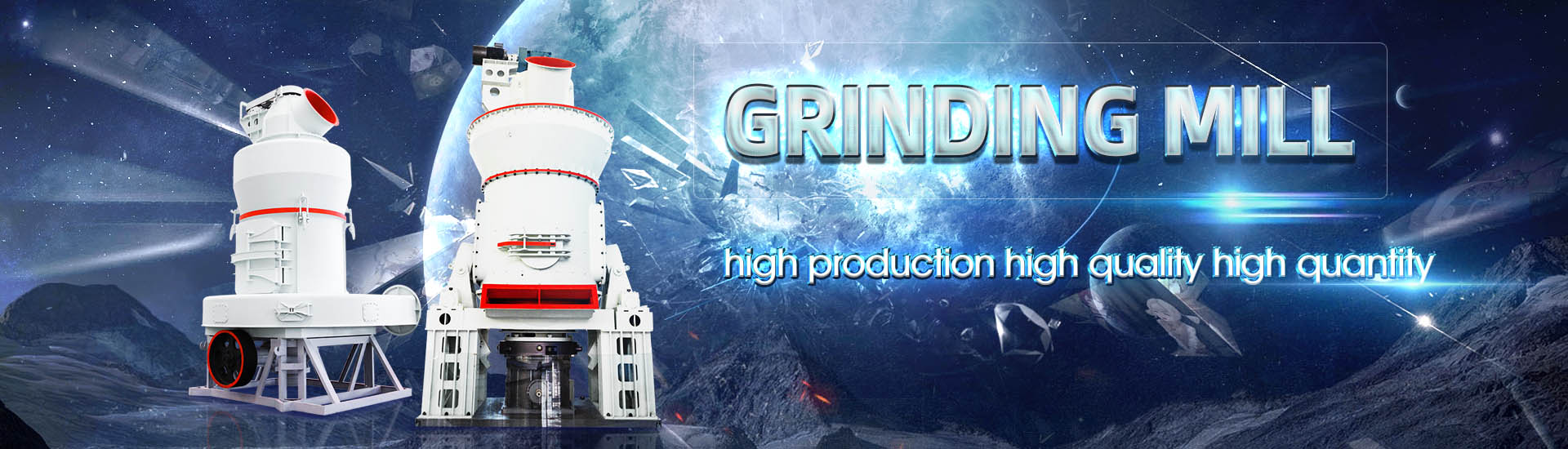
Principle of chemical raw material grinding machine
.jpg)
Lesson 6 GRINDING AND OTHER ABRASIVE PROCESSES KSU
Material removal by action of hard, abrasive particles usually in the form of a bonded wheel • Generally used as finishing operations after part geometry has been established by 2024年6月6日 By combining the concepts of electrochemical machining and conventional grinding, ECG delivers extraordinary accuracy and productivity in material removal Electrochemical machining uses a cutting tool, but ECG Electrochemical Grinding: Parts, Working, Application, 2022年6月24日 Grinding is a manufacturing process which significantly contributes in producing high precision and durable components required in numerous applications such as aerospace, (PDF) A comprehensive review on the grinding process: 2023年7月4日 The highpressure roller mill, also called the roller presser or the extrusion mill, is a grinding equipment based on the principle of material layer crushingRoller Mill SpringerLink
.jpg)
Grinding SpringerLink
2022年2月28日 Comminuting raw materials are extensively utilized in various industries such as food, cosmetics, electronics, pharmaceutical, cement, recycling, and mineral processing Initial considerations include types of inaccuracy, principles of machine design to achieve high machine stiffness and low deflections levels due to grinding forces, temperature rise or Principles of Modern Grinding Technology ScienceDirect2022年6月24日 Grinding is a manufacturing process which significantly contributes in producing high precision and durable components required in numerous applications such as aerospace, A comprehensive review on the grinding process: Advancements 2024年6月6日 Chemical Machining Working Principle The chemical machining working principle is chemical etching The part of the workpiece whose material is to be removed is exposed to a chemical known as enchant The enchantment Chemical Machining: Working Principle, Application
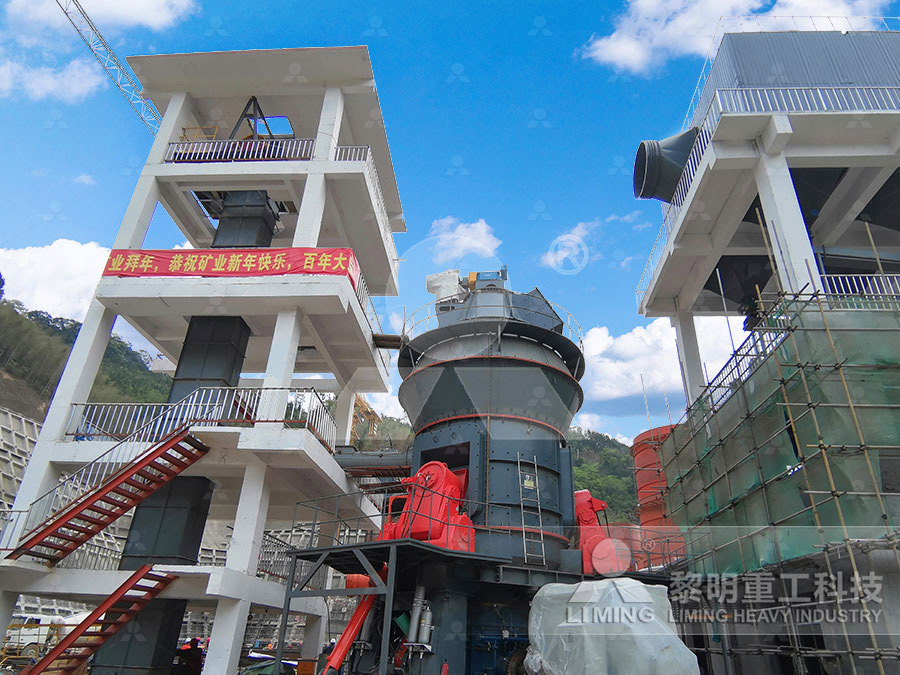
WORKING PRINCIPLE OF THE COTTON ROLLER
The article discusses prediction and assessment of environmental impacts (effects) on the design and interdisciplinary arts cotton textile environment for industry 30 cotton roller ginning process2023年2月22日 All nonconducting materials cannot be machined Tools material and workpiece material should be chemically stable with the electrolyte solution Designing and marking of the tool is difficult, but its life is long, so Electrochemical Machining (ECM): Process, Working 2020年6月15日 Industrial hammer mills are employed in particle reduction applications for processing material Though machine designs vary, the basic hammer mill working principle remains the same—uniform size reduction of aggregate raw material is achieved by repeated blows with hammers mounted to a rotating shaftUnderstanding the Working Principle of Hammer Mills PraterIntroduction to Bearing Grinding Machines Bearing grinding machines are designed to grind the inner and outer rings and the balls of the bearings to achieve the required dimensions and surface finish These machines are highly automated and can perform multiple operations in a single setup, including loading, unloading, and measuring the parts Working principle of bearing grinding machine Phenomenal Blog
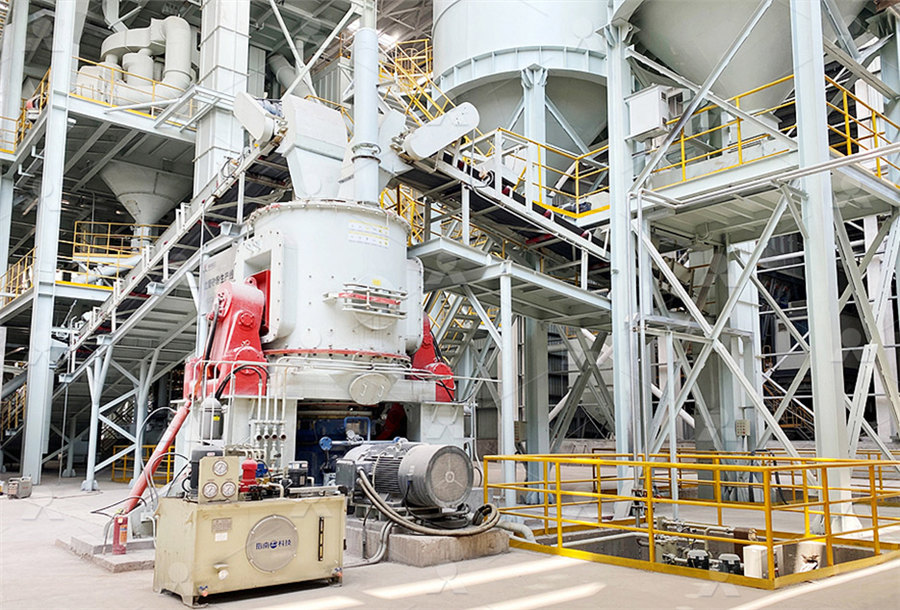
Multimill; Working and principle in Pharmaceutical » Pharmaguddu
2024年2月3日 1 Hopper inlet The hopper is used to feed products to the mill 2 Milling chamber The milling chamber contains a screen to reduce particle size, and twelve milling and cutting edge blades and two scraper blades are responsible for millingA section cutthrough of ball mills A ball mill is a type of grinder filled with grinding balls, used to grind or blend materials for use in mineral dressing processes, paints, pyrotechnics, ceramics, and selective laser sinteringIt works on the principle of impact and attrition: size reduction is done by impact as the balls drop from near the top of the shellBall mill Wikipedia(Horst 1985, p 3A5) Average grinding sizes for the ore can be brought down to 1015 microns at the very most, if using long grinding periods on a product which has already passed a 200 mesh sieve Some specific mills are reported to be available, which are capable of grinding the ore down to sizes of 5 microns or lessCHAPTER 5 GENERAL PRINCIPLES OF MINERAL PROCESSING June 2022; ARCHIVE Proceedings of the Institution of Mechanical Engineers Part C Journal of Mechanical Engineering Science 19891996 (vols 203210) 236(2):1107(PDF) A comprehensive review on the grinding process:
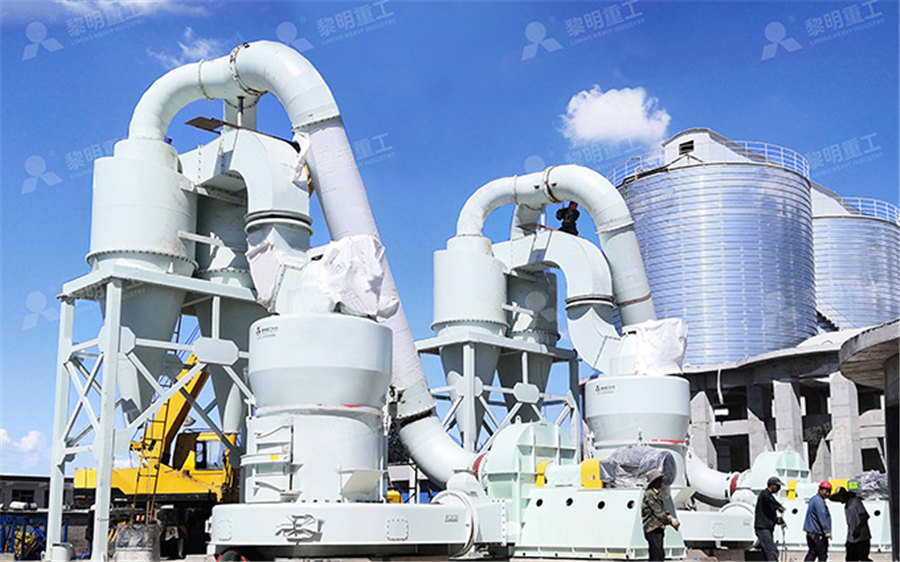
Grinding in Ball Mills: Modeling and Process Control
2012年6月1日 The feed material is typically composed of the BFRs and the catalyst, both in powder form As the cylinder starts to rotate, the grinding balls inside the cylinder crush and grind the feed 2017年6月2日 Autogenous grinding (AG) and semiautogenous grinding (SAG) mills use the material to be ground as the grinding media Autogenous grinding mills use larger rocks to impact and break smaller rocks as the mill rotates How it Works: Crushers, Grinding Mills and Pulverizers2024年8月11日 Material costs are influenced by multiple factors: Raw material costs: Fluctuations in global commodity markets can significantly impact prices Material utilization rate: Efficient nesting and scrap reduction techniques can Metal Material Selection Principles MethodsCylindrical Grinding Machine: Types, Process Working Principle What is Cylindrical Grinder? Cylindrical Grinding Machine: Types, Process Working Principle :Cylindrical grinders are employed to slice or cut very precise and Cylindrical Grinding Machine: Types, Process
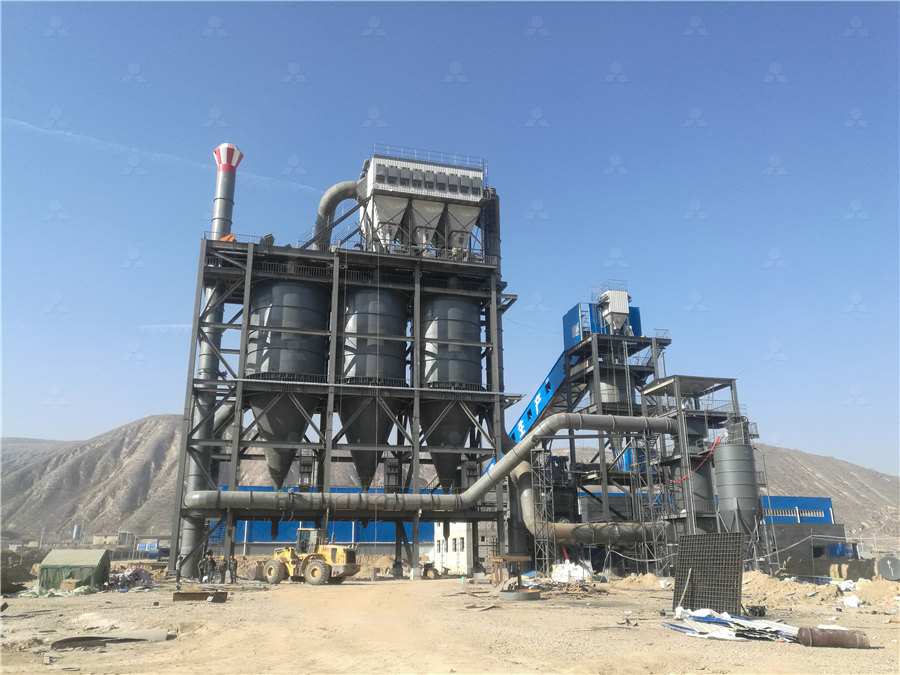
Paper Making Process: From Raw Materials to Finished Products
2023年7月13日 The process of pulping, which turns raw materials like wood chips or recycled paper into pulp slurry, is a basic one in the production of paper Mechanical and chemical pulping are the two main types While mechanical pulping separates fibers from raw materials by grinding them, it may not be appropriate for all types of paper2022年2月28日 Generally, grinding process efficiency can mainly be improved by either improving the grinding behavior of the material being ground or enhancing the grinding machines Recently, the use of additives socalled grinding aids, which is applied in a small amount of 001–025 wt% related to the mass of product, has reduced these problems and been Grinding SpringerLinkFor example, grinding media type, size, and amount; different machine speeds; variable loading or feed rate of raw material In addition to reducing particle size, Attritors also can create the highest intensity intimate blending of dissimilar materials Specific chemicals or additives canWe will discuss the principle of the Attritor and its applications2022年1月12日 This machining process is not magic, but scientifically practical This process uses a strongly acidic or alkaline chemical reagent to remove material from the workpiece This is an ageold process prior to 400 BCE when organic chemicals such as citric acids and lactic acids were used to etch metals to manufacture the desired shape of armorsChemical Machining: Definition, Working Principle, Types,
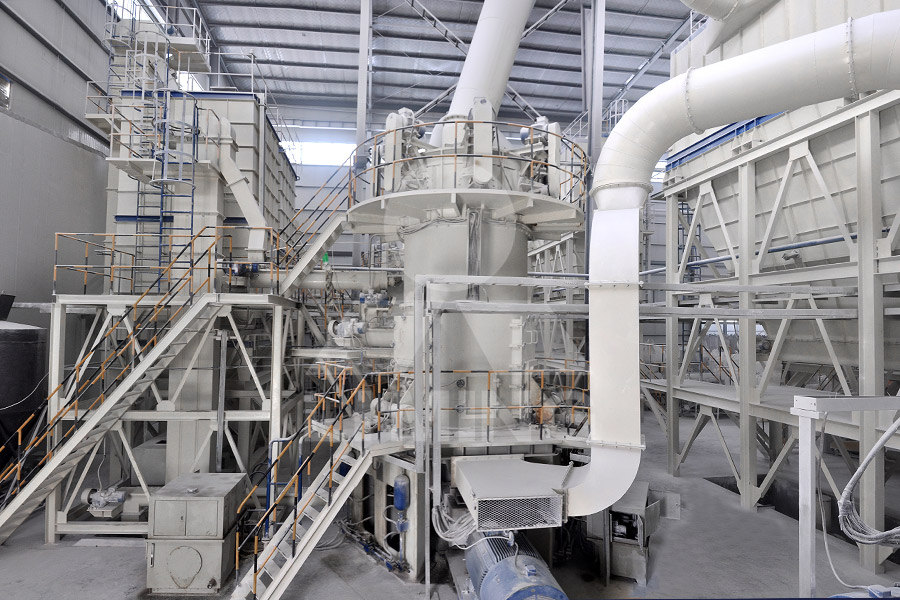
Cement Raw Mill in Cement Plant for Cement Raw Meal Grinding
Raw mill is also called cement raw mill, similar to cement ball mill, it is an important cement milling equipment used in the cement production process Raw mill is mainly used for grinding cement raw meal in the cement factory production process It is also suitable for metallurgical, chemical, electric power and other industrial mining enterprises to grind various ores and other grindable 2018年8月17日 As is quite evident (Marty knows that you know!), the ultimate objective of processing a mineral is to extract the maximum value from a raw material There are two end results that one is trying toGrinding Mills — Types, Working Principle Applications2021年9月28日 What Is the Working Principle of Grinding Machines? During the grinding process, the grinding surface of the grinder tool is evenly coated with abrasive If the material hardness of the grinding tool is lower than that of the workpiece, when the grinding tool and the workpiece move relative to each other under pressure, the abrasive has sharp edges and What Is Grinding and Its Working Principle and Type?2024年4月19日 Discover the inner workings of grinding machines and learn how they transform raw materials into finished products 899 Sheridan Dr, West Chester, Pennsylvania Mon – Sat: 9:00am–18 Surface grinding is the most The Grind: Understanding The Processes Of Grinding
.jpg)
International Journal of ChemTech Research
The principle of attrition and impact is mainly used here appropriate solvent and mechanical process involves subjugation to mechanical forces using grinding machines The former is used mainly for the production of bulk drugs or inorganic raw materials and chemicals like magnesium carbonate or calcium carbonate [4]widely applied in chemical raw materials, nonmetallic processing, refractory materials, and other industries, and is suitable for dry fine grinding of mineral raw materials with Mohs hardness below 6 (such as talc, causticburned magnesia powder, kaolin, wollastonite, gypsum, lime, bentonite, etc), and the particle size can be adjustedRoller Mill Springer2024年8月30日 When discussing the principle of a granulator machine, it is essential to delve into its operational mechanisms and underlying principlesA granulator machine is a commonly used piece of equipment designed to process raw materials into granular products, widely employed in industries such as pharmaceuticals, chemicals, and food processingWhat is the principle of granulator machine?2019年10月31日 Definition of pulverization "Pulverization" (comminution, crushing, grinding) is the process of applying an external force to a (solid) material of a certain Definition of pulverization PRODUCT THINKYMIXER; “Crushing and grinding”, Resources and Materials Vol 113, No 12, 899903 (1985)Pulverization 1: Definition and purpose THINKY MIXER
.jpg)
Grinding Machines: Types and Selection Principles Mining
2020年9月22日 Grinding machine has been widely used in gold mines in South Africa since 1905 At that time, the grinding machine used river pebble as the grinding medium, which was essentially a gravel mill Later, in order to improve the production capacity of the mill, cast iron balls were used as the medium, so normal gravel mills were evolved into ball mills and rod millsRaw material preparation I: Storage and homogenisation Raw material preparation II: Drying and raw grinding Burning The burning of the raw meal at approx 1,450°C is carried out in Lepol or preheater kilns that work by varying methods, the main difference being in the preparation and preheating of the kiln feed By chemical conversion, a From raw materials Extracting raw materials Raw material Publisher Summary Dressing is performed on a grinding wheel in preparation for grinding The aspects of dressing include truing to eliminate deviations from specified form or straightness; dressing to achieve a sharp cutting surface and a uniform random distribution of cutting edges; conditioning to remove the bonds surrounding the abrasive grains and create a more open Principles of Modern Grinding Technology ScienceDirectThey are capable of handling different types of materials and producing highly uniform products The working principle of these machines involves force grinding, which ensures consistent results while minimizing energy consumption The characteristics unique to force grinding also make these mills stand out among other milling equipmentWorking principle and characteristics of vertical mill
.jpg)
Vertical Cement Mill, Vertical Roller Mill Buy Cement Mill From
The vertical cement mill is largescale cement grinding machine With advantages of energyefficient and stable quality, vertical roller mill is widely applied to many industries, such as cement, power, metallurgy, chemical and nonmetallic mining industry and etc As a typical type of Cement Mill, vertical cement mill set crushing, drying, grinding, grading transportation in one, it grind Material is held in the grinding chamber until it is reduced to the size of the openings in the screen The number of hammers on a rotating shaft, their size, arrangement, sharpness, the speed of rotation, wear patterns, and clearance Chapter 18 Feed Milling Processes Food and Grinding is the common collective name for machining processes that utilize hard, abrasive particles as the cutting medium The grinding process of shaping materials is probably the oldest in existence, dating from the time prehistoric humans found that they could sharpen their tools by rubbing them against gritty rocksGrinding Processes SpringerLink2023年7月4日 It is widely applied in chemical raw materials, nonmetallic processing, refractory materials, and other industries, and is suitable for dry fine grinding of mineral raw materials with Mohs hardness below 6 (such as talc, causticburned magnesia powder, kaolin, wollastonite, gypsum, lime, bentonite, etc), and the particle size can be adjusted between 10 and 100 mmRoller Mill SpringerLink
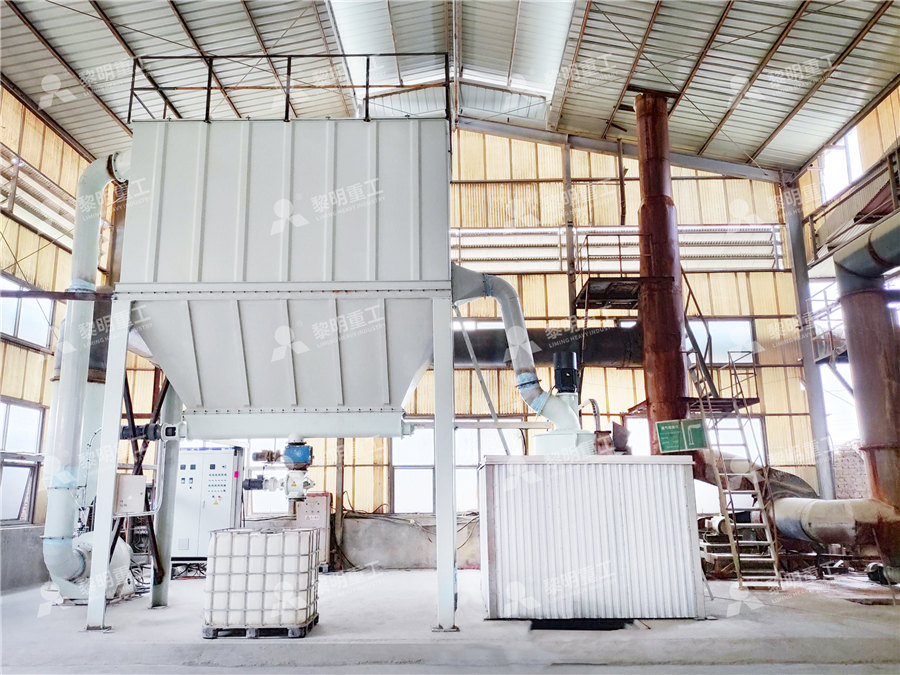
Cement Manufacturing Process INFINITY FOR CEMENT EQUIPMENT
The principal raw materials for cement manufacturing are: Limestone; Silica and alumina from basalt , shale or sand; Iron from iron ore or steel mill scale Sand stone; Pumice (volcanic ash for Portland Pozzolana cement ) Gypsum General Properties of Raw Material Sources Limestone; The basic raw material of the cement production is limestoneElectrochemical Machining Introduction: Electrochemical Machining (ECM): Definition, Parts, Working, Materials, Applications, Principles, Benefits Limitations: – Electrochemical machining utilizes both an electrolyte solution and an electrical flow to alter the workpiece Since electrical conductivity is important for electrochemical machining, the workpiece material should be Electrochemical Machining (ECM): Definition, Parts, Working, Materials ture, and the like This requires the choice of suitable machines for grinding [4] An analysis of the machines used for grinding plant raw material in pharmaceutical chemical fac tories has shown that their selection is not the best in many cases and is made without taking into accountMachines for grinding medicinal plant raw materialWood is the primary raw material used to manufacture pulp, although other raw materials can be used Pulp manufacturing starts with raw material preparation, which includes debarking (when wood is used as raw material), chipping, chip screening, chip handling and storage and other processes such as depithing (for example, when bagasse is used as the raw material) Basic Overview of Pulp and Paper Manufacturing Process
.jpg)
Size Reduction Equipment: Principle, Types, Uses Benefits IQS
A grinder, commonly referred to as a grinding machine, is a power tool designed for grinding materials This machine utilizes an abrasive wheel to cut and shape materials As the wheel rotates, each abrasive grain on its surface removes small amounts of material through a process of shear deformation2020年12月15日 Machining is one of the eight basic manufacturing processes This textbook covers the fundamentals and engineering analysis of both conventional and advanced/nontraditional material removal (PDF) Machining Processes and Machines: Fundamentals2015年1月1日 Separator speed The speed of the separator directly affects the raw material fineness index Either separator speed is too large or too small, it will directly affect the quality of the final collection of the raw material grinding particles (5) Circulating air valve opening Size of the wind also directly affects the raw material fineness indexModeling Based on the Extreme Learning Machine for Raw