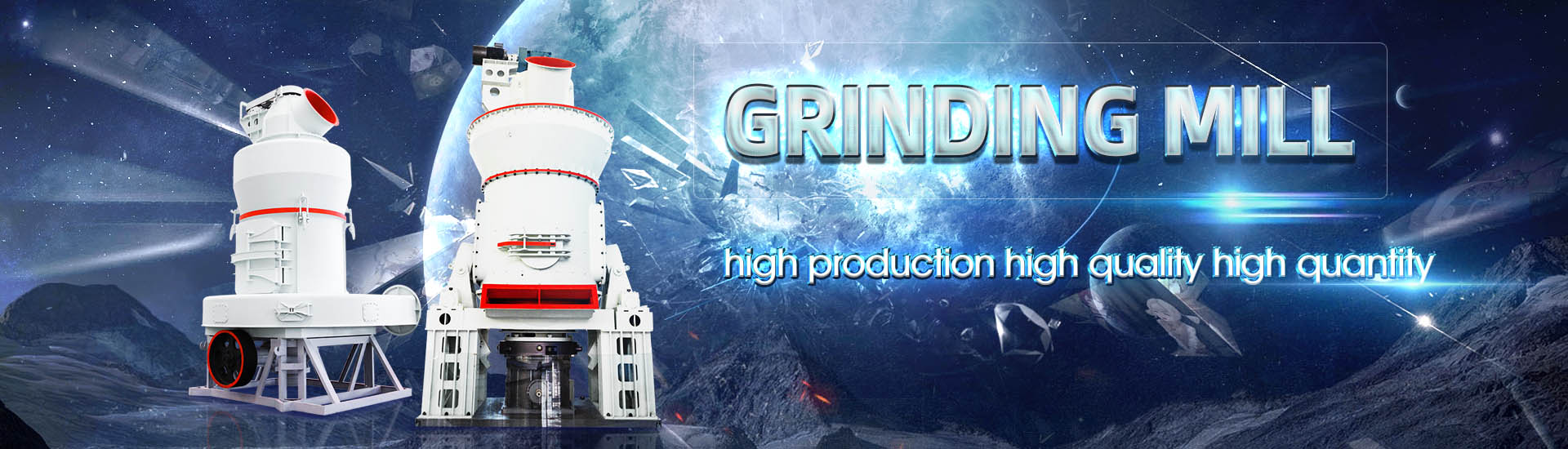
Sulfur production and processing equipment
.jpg)
Sulphur Processing Handling Solutions IPCO
IPCO is a world leader in sulphur processing and sulfur handling, offering a single source supply of complete endtoend systems from the receipt of molten sulphur to the loading of granulated sulphur and solid materialWe engineer total sulphur processing and handling systems to the strictest production and environmental parameters, with a typical turnkey project covering everything from pumping liquid sulphur from the storage tank, to loading Sulphur IPCOChoose IPCO as your partner in sulphur processing and handling and we will deliver the precise support you need, from market leading sulphur solidification solutions to endtoend systems covering everything from receipt of molten Sulphur IPCOIn sulfur recovery, processing and handling, our teams provide leading expertise and proprietary technology to convert molten sulfur into solid granules Downstream, they also bring expertise in sulfur removal from gas streams and Sulfur recovery, processing and handling Matrix PDM
.jpg)
Molten sulfur, sulfuric acid and oleum Sulzer
From the production of molten sulfur in the OG industry to the production of sulfuric acid in fertilizer, metals, and chemical complexes, we are present in all steps of the process with 2020年4月6日 IPCO engineers total sulphur processing and handling systems to the strictest production and environmental parameters, with a typical turnkey project covering everything from pumping liquid sulphur from the storage tank, Sulphur Processing – IPCO Drum Granulation Energy We offer MECS ® sulfuric acid plant processes, products and services for sulfur burning, metallurgical sour offgas removal, spent acid recovery, and wet gas sulfuric acid recovery (SULFOX ™) From design to operation, upgrades to MECS ® Sulfuric Acid Technologies elessentctWe engineer total sulphur melting and filtration systems to the strictest production and environmental parameters, with a typical turnkey project covering everything from feeding the Sulphur Brochure PDF
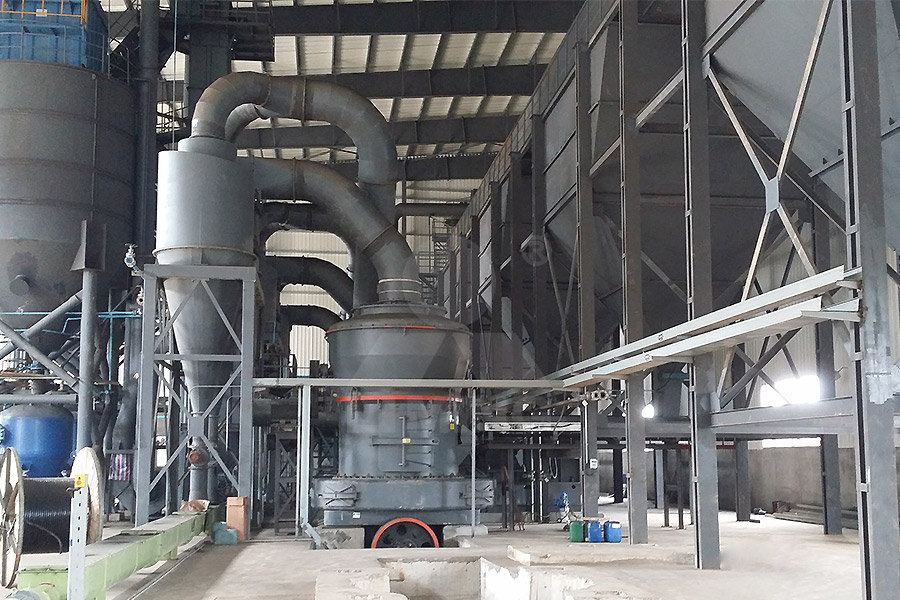
Sulphur Processing – IPCO Drum Granulation
2020年4月6日 About IPCO IPCO activities range from cooperation during FEED (frontend engineering design) to EPC (engineering procurement construction) contracts, and turnkey solutions include liquid sulphur supply, Sulphurnet has focused its activities on the Design and Manufacturing of liquid sulphur processing: melting and purification plants We engineer complete Sulphur melting and filtration systems to the strictest production and Sulphur Melting and Filtration Sulphurnet2019年8月23日 Sulfuric acid has multiple uses in the production of chemicals, petroleum products and a wide range of other industrial applications Sulfur’s main use is in making chemicals for agriculture, mostly for fertilizers Other Sulfur Processing Equipment, Process Flow, CasesDomestic production was about 3,200 metric tons of sulfur valued at $88,100 Native sulfur deposits in Louisiana, Nevada, Texas, and Utah were mined with conventional mining methods Domestic sulfur production, including mined elemental sulfur and pyrites, supplied about onequarter of the US sulfur demand of about 415,000 tonsSulphur Production and Uses Nuroil
.jpg)
Sulfur Mining Processing Equipment Flow Chart Cases JXSC
Sulfur Uses The majority of the sulfur produced in the United States is used to make sulfuric acid Sulfuric acid has multiple uses in the production of chemicals, petroleum products and a wide range of other industrial applications Sulfur’s main use is in making chemicals for agriculture, mostly for fertilizersSRIC Report PEP Review 202103 Sulfur Forming Granulation Process Customer Logins Global sulfur production rose from about 42 million metric tons to 63 million metric tons from 2000 to 2017, material balance, major equipment sizes, and specifications Cost data, including battery limit and offsite costs, SRIC Report PEP Review 202103 Sulfur Forming SP Global2023年2月3日 Sulfur recovery units (SRU) have an important role in the industrial production of elemental sulfur from hydrogen sulfide, whereas the generated acidic gas emissions must be controlled and treated based on local and international environmental regulations Herein, Aspen HYSYS V11 with Sulsim software is used to simulate the industrial and treatment processes Performance assessment and process optimization of a sulfur aspect of sulphur processing and handling We can design, integrate and commission equipment for every stage of the process, from upstream preparation, degassing and filtering of molten sulphur through a range of different solidification options, to downstream conveying, storage, reclamation and bagging or bulk loadingIPCOIPSulphurProcessingandHandling082019dd
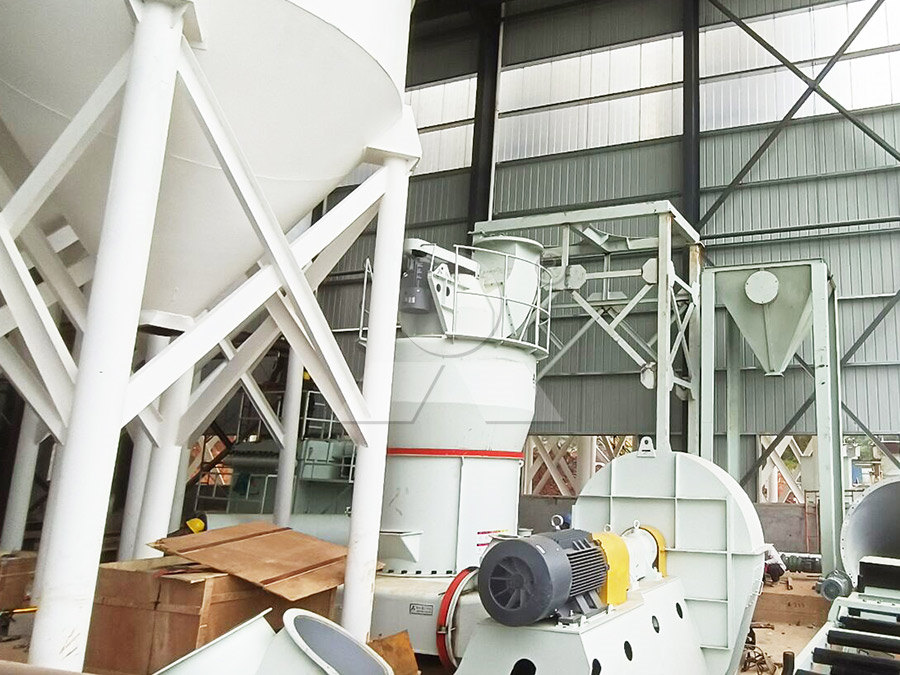
Sulfur Processing Lummus Technology
Lummus Technology provides spare parts, replacements, modifications and upgrades postproject Parts include, but are not limited to, burner tips, burner tiles, sulfur seal legs, tube ferrules and Claus Combustors™ We can expedite quality 2023年2月3日 In economic point of view, a shutdown to modify equipment will stop the production of strategic compounds for local usage and export, but on the other hand, decreasing these process temperatures can affect easily sulfur recovery and may lead to acid gas emissions to environmentalPerformance assessment and process optimization of a sulfur FERTILIZER EQUIPMENT, SYSTEMS, SUPPORT SERVICES Founded in 1951 as the Fertilizer Engineering Equipment Company, the name FEECO has become synonymous with fertilizer granulation expertise in every facet – from Fertilizer Granulation Equipment FEECO International Linde covers the entire hydrogen and synthesis gas (syngas) value chain – extending from standalone hydrogen plants through fully integrated HyCO/syngas installations right up to allinclusive complexes combining ammonia and Hydrogen Synthesis Gas Plants A Linde Company
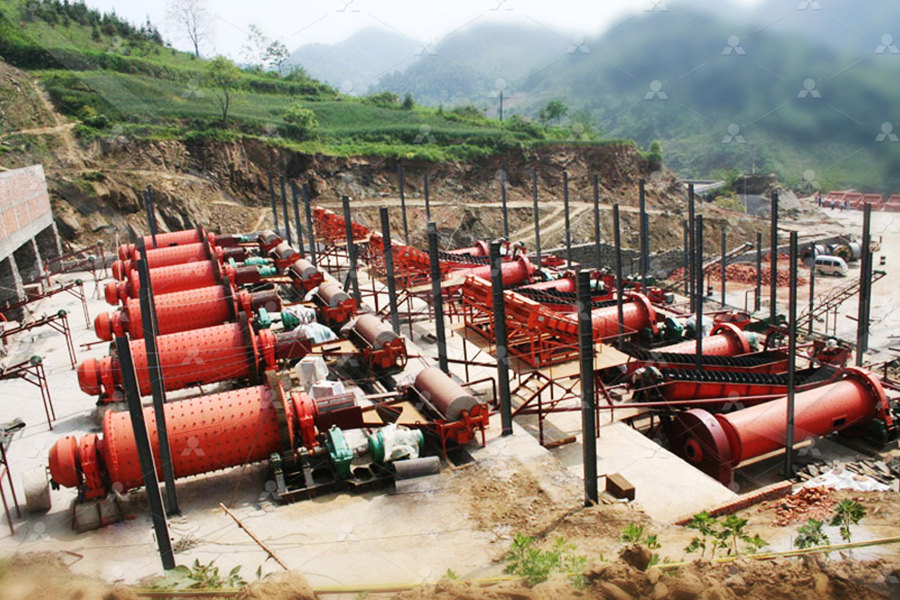
Sulfur furnace and boiler system for sulfuric acid plant
» Sulfur furnace and boiler system Full REVAMP « » Full REVAMP of furnance body and refractory, boiler system and auxiliaries TECHNICAL DATA » Process gas flow max 47,500 m³n/h » Max gas inlet temperature 1,000 °C » Max gas inlet pressure 035 barg » Max heat duty 105 MW » Max steam pressure 62 barg » Max steam production 23 Published February 2018 Sulfuric acid (H 2 SO 4) is the world’s largest consumed chemical, with consumption of around 260 MMT (million metric tons) on a 100% acid basis and a growth rate of around 2%Traditionally, consumption of this chemical is considered as a barometer of a nation’s GDP The majority of sulfuric acid production (59%) is from burning of elemental sulfur, in a Sulfuric Acid from Sulfur Updates on Contact Process2014年7月1日 The sulfur condenser was commonly used to collect the solid or liquid sulfur in Claus Process of the gas processing factory, the refinery and petroleum production sites Show abstract In this paper, a novel desulfurization process was proposed to recover elemental sulfur from smelter offgas with highcontent sulfur dioxide (SO 2 ) using calcium sulfate (CaS) as a Preventing corrosion and tube failure in sulfur condenser during 2021年9月3日 Sulfur in petroleum is corrosive to equipment and detrimental to catalyst The removal of sulphur form crude oil is cumbersome and expensive process, which hikes the oil production cost Review on Sulfur Compounds in Petroleum and Its Products: State
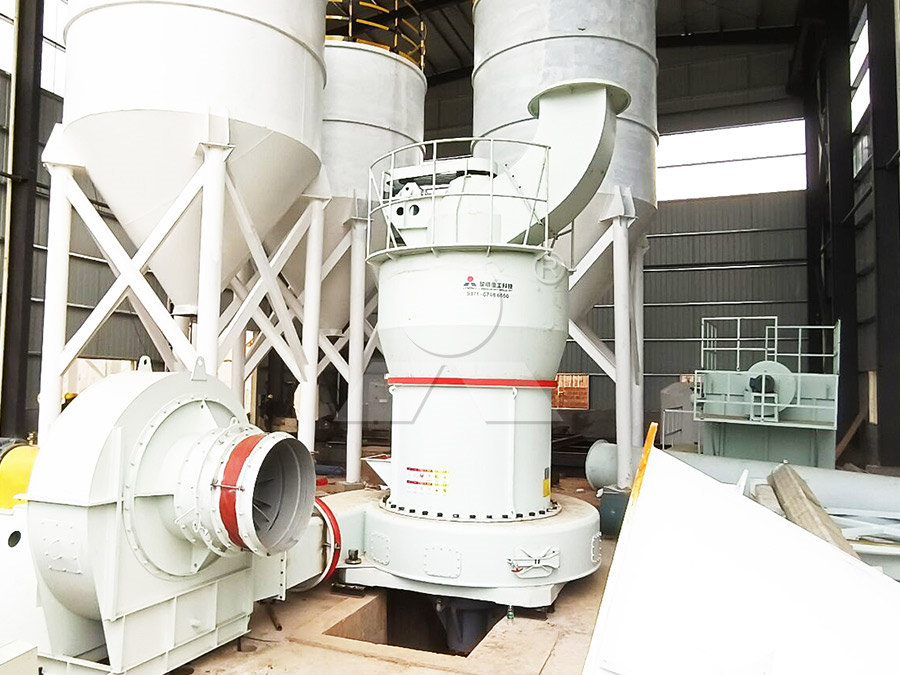
A process simulation study of hydrogen and sulfur production
Aspen Plus model of the IKC Fe–Cl hybrid process for sulfur and hydrogen production This introduces great benefits in the economics of the process Equipment size is reduced and pumping costs are minimized However, the economic benefits Sulfur Recovery Unit Technological Process and Major Equipment The sulfur recovery unit is responsible for converting the sulfide in the toxic sulfurcontaining gas produced in the refinery process into elemental sulfur and removing harmful The project started production in June 2019 and has been running steadily ever since Client NameSulfur Recovery Unit RUICHANGOur Process Analytical Systems and Process Analytical Equipment help you tackle your water Use our gas moisture and sulfur analyzers to successfully monitor sulfur emissions in process heaters and flares by petroleum including water and wastewater treatment, environmental monitoring, electronics production, and more Process Analytical Systems and Equipment Thermo Fisher Separation of impurities along with the production of valuable byproducts such as petroleum coke and sulfur are an integral part of any refinery project Financing construction and modernization of advanced coke and sulfur handling systems at refineries helps companies minimize environmental risks, as well as increase refinery efficiency and reduce operating costsCoke and sulfur handling systems in refineries ESFC Investment
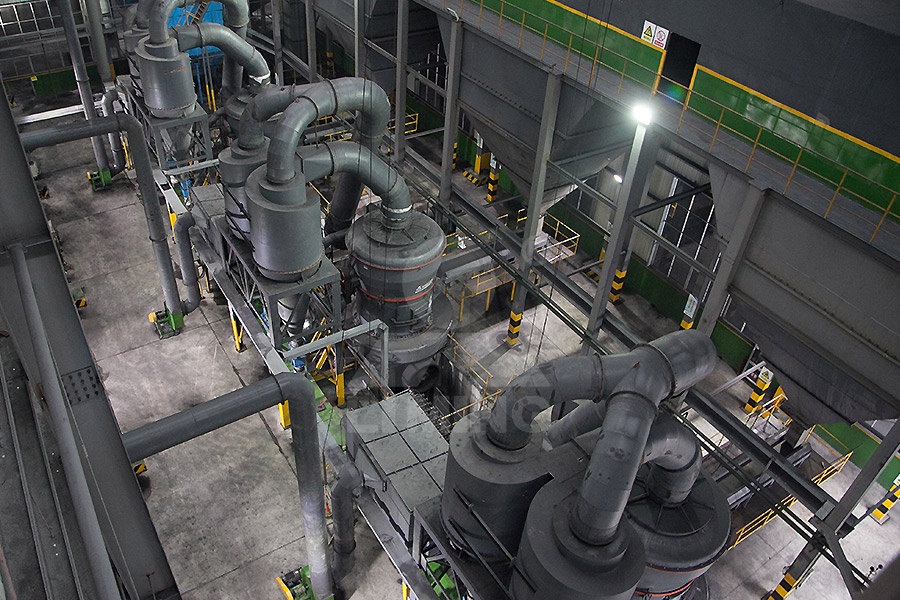
Analysis of Sulfur Granulating Process
In addition to this process, other process suitable for mass production is called Polish Process; please see Figure 4 for principles of Polish process Air cooling granulating process: to store degassed liquid sulfur from sulfur recovery device in liquid sulfur tank; temperature of liquid sulfur should be kept between 130℃ to 140℃ inIn 2000, US sulfur production totaled 103 million tons – 81% from recovery, 9% from one Frasch mine and 10% as In the contact process, sulfur is burned to form sulfur dioxide, which is 2015, 679 facilities emitted more than 34000 t Sulfur Removal and Recovery SpringerLink2017年8月2日 Sulfur is one of the few elements that is found in its elemental form in nature Typical sulfur deposits occur in sedimentary limestone/gypsum formations, in limestone/anhydrite formations associated with salt domes, or in volcanic rock []A yellow solid at room temperature, sulfur becomes progressively lighter in color at lower temperatures and is almost white at the Sulfur and Sulfuric Acid SpringerLink2020年9月18日 First step: Production of Sulpur Dioxide Gas (SO2) The sulphur obtained from any kind of source is burned to form sulphur dioxide gas Care is to be taken in this step so that the air supplied for combustion process is dry Any traces of water present will result in the formation of acid and cause corrosion within the combustion equipmentSulphuric Acid Manufacturing Process Chemical Engineering
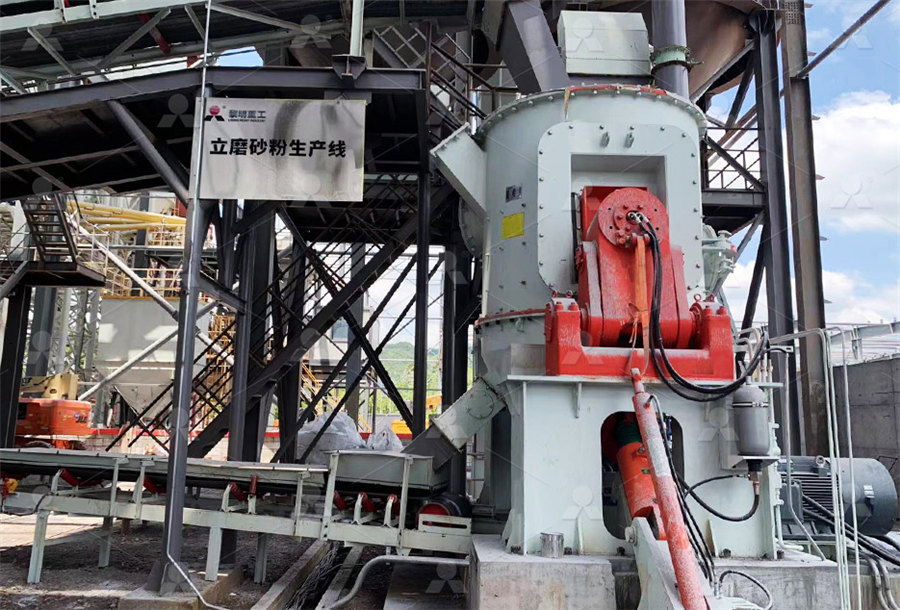
Sulphur Forming and Solidification Technologies Kreber
Nevertheless, the industry developed new ways of production, such as sulfur granulation process, (steel belt) sulphur pastillation and wet prilled sulphur, which took over the role of being the most dominant method of particle engineering in the sulfur industry Two Main Concerns This shift in production method was the result of two main 2021年12月27日 Process Modeling, Optimization and Cost Analysis of a Sulfur Recovery Unit by Applying Pinch Analysis on the Claus Process in a Gas Processing Plant December 2021 Mathematics 10(1):88(PDF) Process Modeling, Optimization and Cost Analysis of a Sulfur Approximately 90 to 95 percent of recovered sulfur is produced by the Claus process The Claus process typically recovers 95 to 98 percent of the hydrogen sulfide feedstream In general, gas processing plants and oil refineries are required to recover between 95 and 9999 percent of The Claus Sulfur Recovery Processfast and reliable production of high quality granules Key features and benefits of the IPCO continuous drum granulation process include: • The highest capacity granulation unit in the industry • Capability to vary production of new granules and control PSD while in operation • Selfcontained with small footprint –SULPHURPROCESSINGADVANCED
.jpg)
Sulfur Recovery from Acid Gas Using the Claus Process and High
2008年5月1日 Sulfurbearing compounds are very detrimental to the environment and to industrial process equipment They are often obtained or formed as a byproduct of separation and thermal processing of The majority of sulfuric acid production (59%) is from burning of elemental sulfur, in a contact process The sulfur is sourced mostly from oil and gas processing facilities, in which the This review specifically updates the contact process for the production of ulfuric acid by Table 37 Major equipment 21 Table 38 Utilities Sulfuric Acid from Sulfur Updates on Contact Process IHS MarkitThe compounds that cause corrosion in the sulfur recovery process equipment are SO2, SO3, H2S, CO2, and elemental sulfur H2S, and CO2 are the main corrosive agents in the petroleum industry Regular checking sulfur (PDF) Preventing corrosion and tube failure in sulfur gas to elemental sulfur and remove it to achieve a higher rate of sulfur recovery Introduction Figure 1 Block flow diagram for sulfur recovery consisting of a SRU and TGTUs Figure 2 Schematic of a modified Claus SRU based on the straightthrough configuration BASF Sulfur Recovery Sulfur Recovery Unit (SRU) Tail Gas Treatment Units (TGTUs Claus Catalysts and Tail Gas Treatment Solutions for Sulfur Recovery
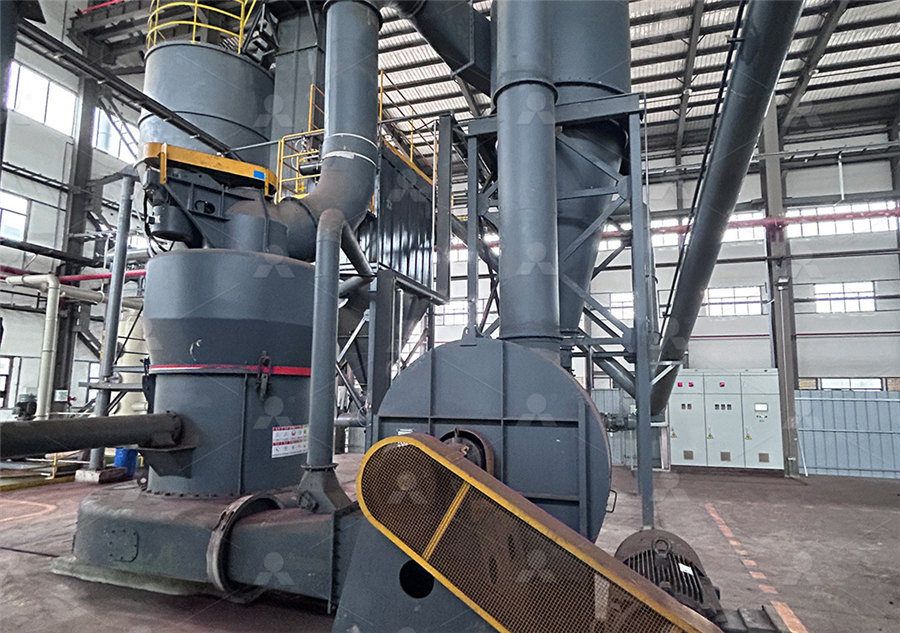
Combustion kinetics of H2S and other sulfurous species with relevance
2020年9月1日 In second process, SO 2 from sulfur combustion is mixed with acid gas in the furnace and in the catalytic units for sulfur production For feeds with 10–65% H 2 S, the optimized sulfur recovery efficiencies varied within 983–985% for the first process, within 968–986% for the second process, and within 96–982% for the Claus process2014年11月27日 The H 2 S is removed to ppmv levels, and the produced sulfur is hydrophilic (ie, it has an affinity for water) and is not sticky, which reduces operational issues, such as plugging of process piping and equipment Developed in the 1990s by Paques for desulfurization of biogas, the Thiopaq OG process was modified by collaboration with Shell Global Solutions Taking on the Technical Challenges of Sour Gas Processing JPTIn the MECS ® sulfurburning process, ambient air is drawn through a highefficiency MECS ® ZeCor ® drying tower by the main compressor to remove moisture A MECS ® Brink ® mist eliminator provides efficient acid mist removal, which is critical for the protection of the main compressor The compressed dry gas enters the sulfur burner, where molten sulfur is burned MECS ® Sulfur Burning Sulfuric Acid Process TechnologyAbstract: Sulfurbearing compounds are very detrimental to the environment and to industrial process equipment They are often obtained or formed as a byproduct of separation and thermal processing of fuels containing sulfur, such as coal, crude oil and natural gas The two sulfur compounds, which need special attention, are: hydrogen sulfide (HSulfur Recovery from Acid Gas Using the Claus Process and High
.jpg)
Hydrogen production using thermochemical watersplitting
2021年6月23日 The threestep thermochemical watersplitting process, ie, the iodine–sulfur (IS) process [3] (or sulfur–iodine process), has been investigated as a way to use the heat generated from hightemperature gascooled reactors (HTGRs) because their temperature range of 300°C900 °C coincides with that of the sulfuric acid decomposition, which is an 2021年9月27日 Also, in the process scheme of the developed unit, the production of 1 ton of liquid sulfur dioxide consumes significantly less energy than in the existing technologies(PDF) Liquid sulfur dioxide production method based on sulfur 2020年10月1日 In addition to H₂S, physical solvents can coabsorb organic sulfur species (COS, CS₂ and RSH) and heavy hydrocarbons, notably aromatics The latter not only may result in a possibly significant loss of production, but also in operational problems Understanding gas sweetening processes Gas Processing LNGSulfur just may be a blessing in disguiseSulfur is a natural component of crude oil and natural gas It is most commonly known for its offensive “rotten egg” odor when in the form of hydrogen sulfide gas On one hand, sulfur creates additional processing requirements for oil and gas producers Sulfur compounds must be removed through sulfur recovery processes to comply Sulfur Processing Solidification : Matrix PDM Engineering