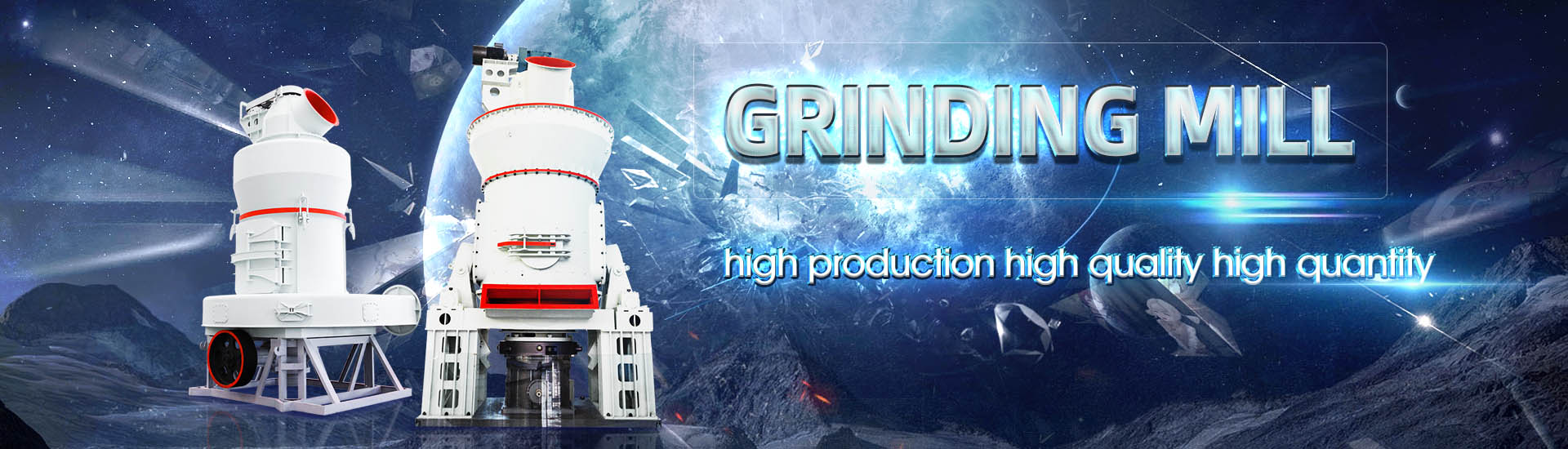
Ore grinding mill cpf12
.jpg)
Ore Grinding SpringerLink
2023年7月20日 Ore grinding is a process to further reduce and disperse the ore particle size In the mineral processing industry, ore grinding is the particle size preparation before the HPGR grinding circuits offer improved capital and operating costs for a large throughput single processing train and will be adopted in favour of semiautogenous grinding mills (SAG) for the PREFEASIBILITY STUDY UPDATE – SINGLE TRAIN OPTION STUDYVertical stirred milling is a wellrecognized technology for the secondary, regrind and fine grinding applications and are increasingly replacing coarser ball mill applications in secondary and RECENT DEVELOPMENTS IN COARSE GRINDING USING VERTICAL 2014年6月1日 The grinding efficiency (and related throughput) of porphyry copper ores in conventional mills is more impacted by certain alteration minerals than by the traditional Ore characterization, process mineralogy and lab automation a
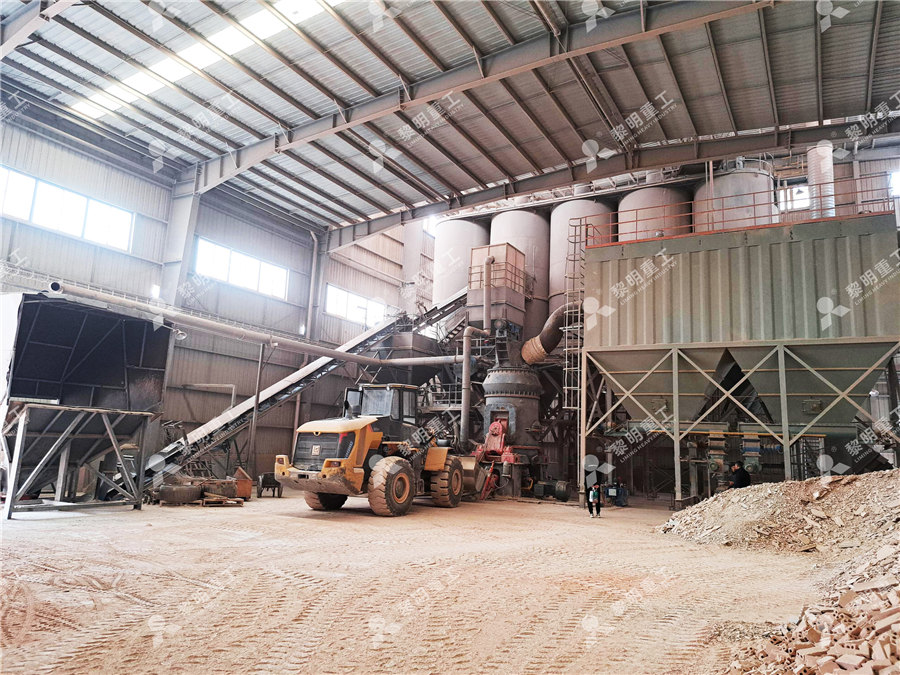
Flotation: The Past, Present and Future of Mineral
If grinding requirements could be reduced by half at some mine sites through the use of CPF, that would have a massive impact on global GHG emissions CPF is not a new concept However, what is new is its application at a commercial Two basic types of UFG mills are available, the vertical stirred mill and the horizontal stirred mill Both use rotating stirrers within a stationary mill shell to impart kinetic energy to a fine media Ultra Fine Grinding A Practical Alternative to Oxidative Treatment 2019年4月12日 高压辊磨机能量利用率高,目前已在水泥行业、金属矿山、冶金球团等领域广泛应用。 结合当前研究成果及工业现场数据,本文对比了高压辊磨机在金属矿山和球团预处理行业中的工艺流程,以及辊面比压力、辊面线速度、 高压辊磨机在金属矿选矿与球团预处理领域的工艺和 It is performed in cylindrical steel vessels that contain a charge of loose crushing bodies—the grinding medium—which is free to move inside the mill, thus comminuting the ore particles Grinding Mill an overview ScienceDirect Topics
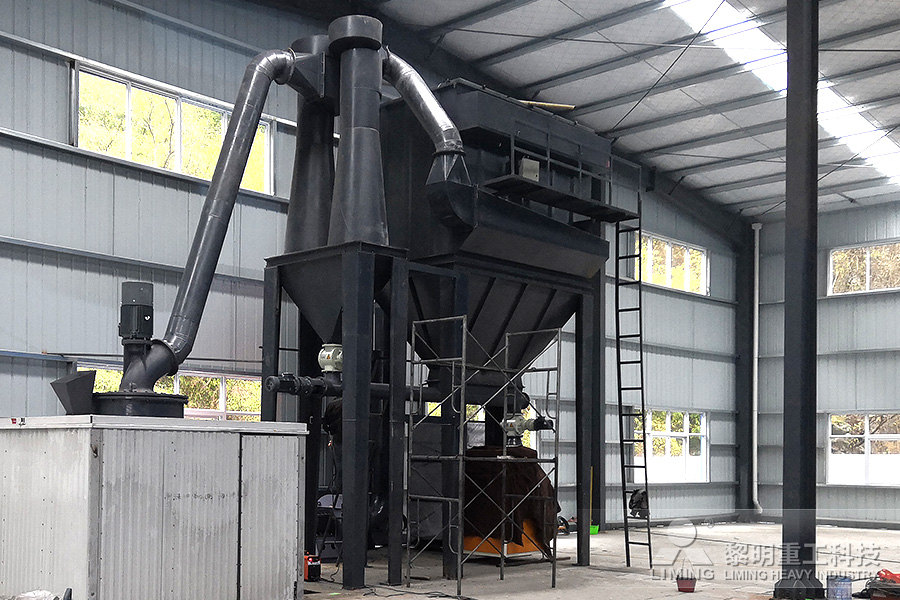
Ore Grinding Methods and Process of Ore Grinding
Ore grinding is a process to further reduce and disperse the ore particle size In the mineral processing industry, ore grinding is the particle size preparation before the separation of the 2015年7月21日 The ultrafine grinding of the ore is done in 48 bead mills, and three other mills are held in reserve in the event of repairs The grinding is done in four stages in 12 separate Ultrafine Grinding in Contemporary Flow Diagrams for Mineral Request PDF On Mar 15, 2015, Mathis Reichert and others published Research of iron ore grinding in a verticalrollermill Find, read and cite all the research you need on ResearchGateResearch of iron ore grinding in a verticalrollermillA crushing plant delivered ore to a wet grinding mill for further size reduction The size of crushed ore (F 80) was 40 mm and the SG 28 t/m 3 The work index of the ore was determined as 122 kWh/t A wet ball mill 1 m × 1 m was chosen to grind the ore down to 200 micronsGrinding Mill an overview ScienceDirect Topics
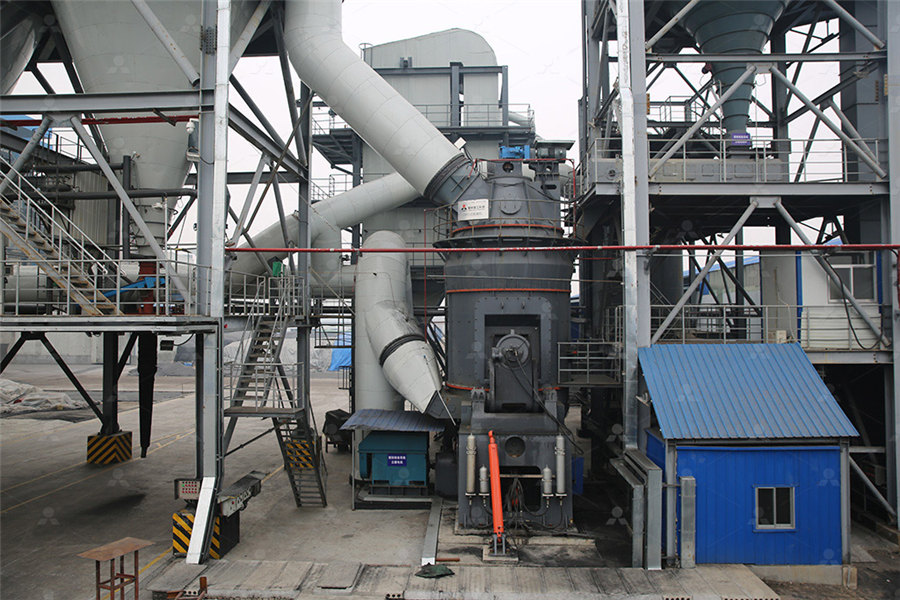
(PDF) Control of ball mill operation depending on ball
2023年12月12日 Ore can have various properties, such as hardness, density, moisture content, etc, which can affect the ore’s productivity and grinding efficiency Discover the world's research 25+ million membersof ore samples to AG/SAG grinding The pilot plant can test coarse feeds (150mm), as well as essentially any Bond Rod Mill 0305 127 Any 118 15 10 Lockedcycle Y Y Bond Ball Mill 0305 335 Any 0149 10 5 Lockedcycle Y Y Mod Bond 0305 335 Any N/A 2 12 Batch N YSAG Mill Testing Test Procedures to Characterize Ore GrindabilityIn the mill, the mixture of medium, ore, and water, known as the mill charge, is intimately mixed, the medium comminuting the particles by any of the above methods Apart from laboratory testing, grinding in mineral processing is a continuous process, material being fed at a controlled rate into one end of the mill and discharging at the other end after a suitable dwell (residence) timeGrinding Mill an overview ScienceDirect Topics2024年4月26日 The choice of grinding mill depends on factors such as the desired product size, capacity requirements, and energy consumption b Autogenous and SemiAutogenous Mills: In some cases, autogenous (AG) and semiautogenous (SAG) mills are used for grinding These mills utilize the ore itself as the grinding media, reducing the need for additional Iron Ore Processing: From Extraction to Manufacturing
.jpg)
Optimizing the performance of highpressure grinding roll based ore
2012年12月28日 All content in this area was uploaded by Daniel Saramak on Jan 12, 2016 Content may be subject to copyright The article concerns issues related to the copper ore ball mill grinding process, 2018年6月18日 Ore pretreatment methods for grinding: journey and prospects, Mineral Processing and Extractive Metallurgy Review, DOI: 101080/2018 To link to this article: https://doior g/10 Ore Pretreatment Methods for Grinding: Journey and Prospectsore and corresponds to the scheme, including medium and small stage ball grinding provides a comparative analysis of a wide range of ore processing steps and requires 515% energy in a selfgrinding mill [3] 1 Figure 2 Ball mill process control system using ACS (Adaptable Control System) Figure 2 shows that the input and output signalsControl of ball mill operation depending on ball load and ore operation (1) Structure parameters of grinding mill, including its specifications, model, aspect ratio, ore discharging method, and liner form (2) Various working parameters of grinding mill, including fraction of critical speed for grinding mill, filling rate for grinding mill, grinding concentration,grindingcycleload,etc(3)AndgrindOre Grinding Methods and Process of Ore Grinding
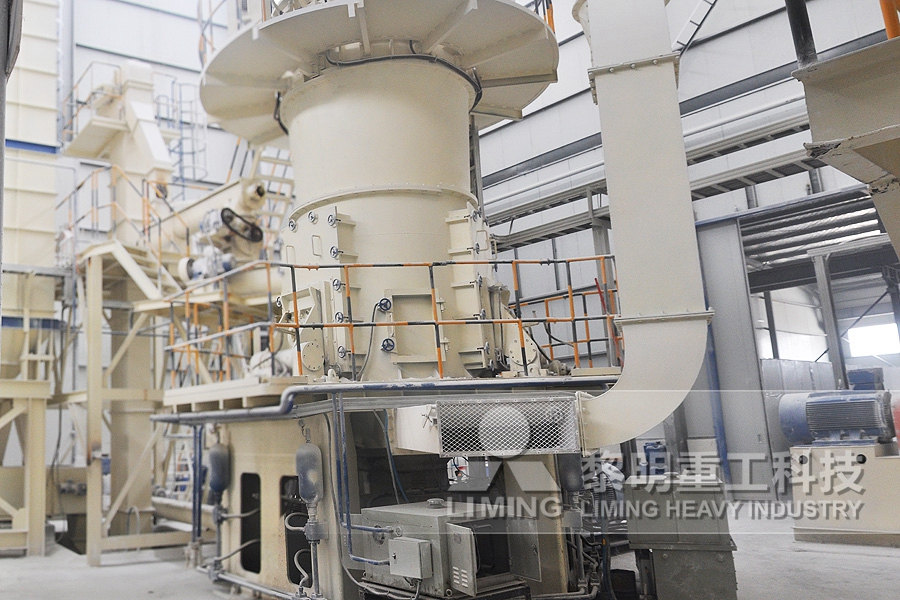
Understanding the SAG Mill in Copper Ore Mining
The Autogenous Mill, also known as AG Mill, is a type of grinding mill used in the mining industry This machine uses ore and rock itself as grinding media to perform its job Unlike other types of mills that use steel balls or rods for 2022年8月31日 The grinding speed of ore and its component minerals decreased exponentially with the grinding time, The effect of mill filling ratio on Gaofeng ore is not obvious Simulations indicated that a capacity increase Grinding Modeling and Energy Efficiency in Ore/Raw 2012年6月1日 As the cylinder starts to rotate, the grinding balls inside the cylinder crush and grind the feed material, generating mechanical energy that aids in breaking bonds, activating the catalyst, and Grinding in Ball Mills: Modeling and Process Control2022年12月31日 OPTIMIZATION OF LATERITE ORE GRINDING PROCESS USING BALL MILL WITH RESPONSE SURFACE METHOD December 2022; Metalurgi 37(3) (127–375 mm) and interstitial filling of 50% OPTIMIZATION OF LATERITE ORE GRINDING PROCESS USING BALL MILL
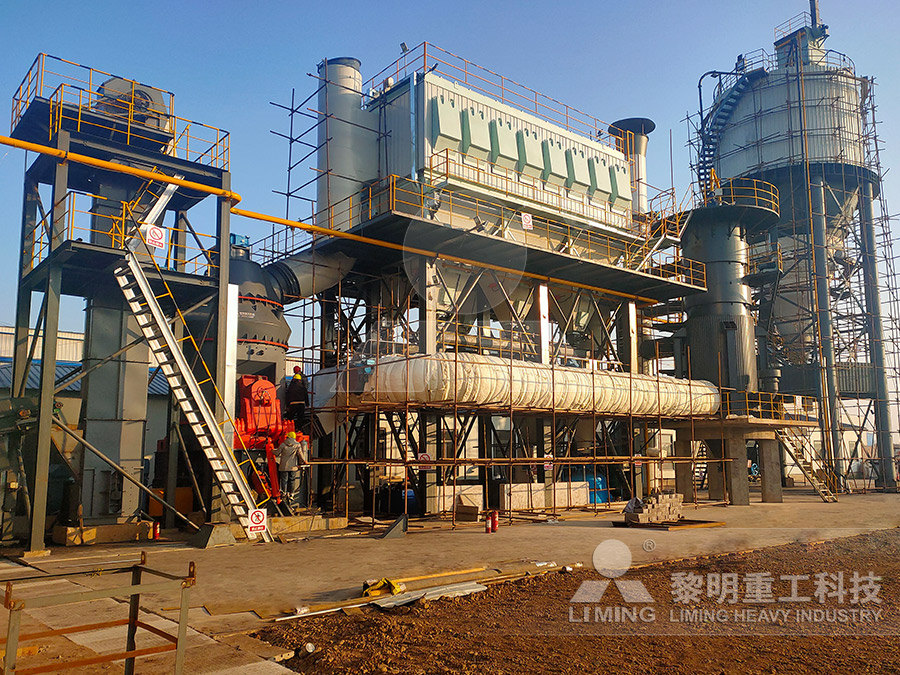
Modeling and application of stirred mill for the coarse grinding
2022年5月23日 Grinding experiments were conducted in a laboratoryscale stirred mill on a lowgrade PGE bearing chromite ore HighPressure Grinding Rolls (HPGR) product of −1 mm was used as feed material to 2019年3月1日 Grinding has become one of the most important unitary operations for producing pellet feed for direct reduction from lowgrade ores and small liberation size, such as compact itabiritesEvaluation of grinding circuits for iron ore ResearchGateGrinding Mills: Ball Mill Rod Mill Design PartsCommon types of grinding mills include Ball Mills and Rod Mills This includes all rotating mills with heavy grinding media loads This article focuses on ball and rod mills excluding SAG and AG mills Although their concepts are very similar, they are not discussed herePhotographs of a glass ended laboratory ball mill show Grinding Mills 911Metallurgistapplied sciences Article Grinding Kinetics Adjustment of Copper Ore Grinding in an Innovative Electromagnetic Mill Marta WołosiewiczGłab˛ 1,*, Paulina Pieta˛ 1, Dariusz Foszcz 1, Szymon Ogonowski 2 ID and Tomasz Niedoba 1 1 Department of Environmental Engineering and Mineral Processing, Faculty of Mining and Geoengineering, AGH University of Science and Grinding Kinetics Adjustment of Copper Ore Grinding in an
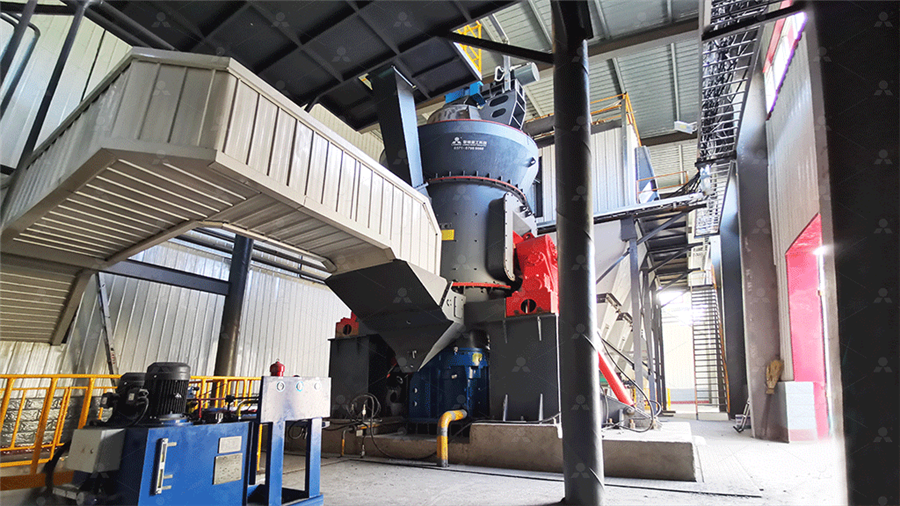
Investigation of some parameters affecting the Ultrafine grinding
2013年4月16日 ABSTRACT In this study, ultrafine grinding of a refractory silver ore tailings was studied A laboratory scale pintype vertical stirred mill and ceramic beads were employed for the grinding testsThe use of small grinding media (5 12 mm), called Millpebs, in regrind mills proved that fi ner grinding can be achieved at lower energy consumption Mill reduction ratio ZnPb ore 1250 HP Vertimill 12 mm media 830 kW F80 = 350 425 μm ZnPb ore 1250 HP Vertimill ENERGY SAVINGS AND TECHNOLOGY COMPARISON USING SMALL GRINDING The mill is filled with a suitable grinding media and the area between each disc is essentially an individual grinding chamber As a result the mill is effectively 8 grinding chambers in series The media is set in motion by the action of the grinding discs which radially accelerate the media towards the shellIsaMill Technology Used in Effecient Grinding Circuitsmilling (12100mm) with a much higher installed power per mill unit volume (Table 1) Table 1 Typical Mill Grinds and Power Intensities Type of Mill Typical Lower Grind Size P80 µm Power Intensity kW/m3 Ball Mill 75 20 Tower Mill 20 40 UFG Mill 5 280 Two basic types of UFG mills are available, the vertical stirred mill and the horizontal Ultra Fine Grinding A Practical Alternative to Oxidative

(PDF) Grinding Media in Ball MillsA Review
2023年4月23日 grinding media in a grinding mill with about 2630 wt% chrome by Chen et al [37] using a phosphate ore in a modified ball laboratory ball mill whose electrochemical potential could be controlledCLUM series of ultrafine gypsum powder vertical grinding mills are a new type of ultrafine industrial ore grinding equipment that integrates grinding, grading, powder Superfine vertical grinding mill main machine and multirotor powder separator: Finished 1216: 1418: Less than 2μm=45% output (t/h) 5575: 79: 1012: Less than 2μm CLUM Ultrafine Vertical Grinding Mill2023年10月17日 3 Ultrafine Powder Grinding Mill Ultrafine powder mill (threering / fourring mediumspeed micropowder mill) feed particle size ≤25 mm, production capacity 0545 t/h, production fineness 1503500 mesh,it is a highefficiency and lowconsumption ultrafine powder processing equipment that successfully replaces the traditional jet mill and complex process How to choose a suitable ore powder grinding mill?2013年4月1日 DOI: 101016/JMINENG201210009 Corpus ID: ; Analysis and validation of a runofmine ore grinding mill circuit model for process control @article{Roux2013AnalysisAV, title={Analysis and validation of a runofmine ore grinding mill circuit model for process control}, author={Johan D le Roux and Ian Keith Craig and D G [PDF] Analysis and validation of a runofmine ore grinding mill
43.jpg)
Factors affecting ores grinding performance in ball mills
Effect of mill type on ore grinding performance Ball mills are widely used in the mining and metallurgical industries for the grinding of ores and other materials There are a wide variety of mill types available, each with its own advantages and disadvantages The 2023年3月15日 The ore sample of underinvestigation was a copper ore The examined parameters include grinding time, mill on the flotation of copper ore 12 40 50 6700 9513 157(PDF) Effect of wet ball milling on copper ore flotation by fractal 2020年3月28日 Based on batch grinding method and normalization idea, a conical ball mill is used and a quantitative separation method of grinding characteristics of multicomponent complex ore is proposedDevelopment of a Novel Grinding Process to Iron Ore Pelletizing These provide the basis for scaleup in industrial grinding plants The OGPmobile provides the user with a means of calculating the effect of Loesche grinding technology on the overall material flow in his processing plant and is a convincing way to demonstrate its benefits Loesche – mobile grinding mill for dry milling of ores Air flow mode Mobile grinding mill for ore Loesche
.jpg)
(PDF) LEARNING FROM OTHER INDUSTRIES; WHY THE
2019年4月16日 Conference: Applying a Successful Technology from the Cement Industry: Advantages of Grinding Ore in a VerticalRollerMill; At: Antalya, Türkey2004年2月1日 Ore G (21 mins 42 sec) has a noticeably longer mill time compared to the more similar milling times of ore H (18 mins 12 sec) and I (17 mins 18 sec)Relationship between microstructure, hardness, 2021年1月1日 Peer review under responsibility of International Federation of Automatic Control 101016/jifacol202112004 101016/jifacol2021 CPD = QcsoÏ O +Qcwo CPF (20c) 34 Grinding Circuit Parameters Table 1 shows the plant data obtained from and validation of a runofmine ore grinding mill circuit model for process Disturbance Propagation Through a GrindingFlotation Circuit2014年1月1日 Ultrafine grinding of the (ground) ore were conducted in a laboratory scale pintype vertical stirred mill (Union Process) at 26%w/w solidliquid ratio and 600 rpm/min stirring rate (Celep et al Improvement of Silver Extraction by Ultra–fine Grinding Prior to
.jpg)
The effects of ore blending on comminution behaviour and
2018年8月17日 The concept of ore blending is a very relevant notion in modern high tonnage production mines It is not only essential for the prolongation of the mine life of the concerned mine but as well as a 2023年10月27日 The ball mill is a rotating cylindrical vessel with grinding media inside, which is responsible for breaking the ore particles Grinding media play an important role in the comminution of mineral A Review of the Grinding Media in Ball Mills for Mineral ProcessingJXSC started manufacture the ball mill grinder since 1985, supply globally service includes flow design, manufacturing, installation, and free operation training in mining, grinding, screening, crushing plant Ball Mills Types According to the discharge type: overflow ball mill, grate discharge ball mill; According to the grinding conditions Ball Mill JXSC MineralThere are suggested various approaches to solving the problem of controlling ore grinding and sorting under conditions of uncertainty and nonstationarity of parameters [22 – 24] It is indicated in [22] that grinding control is an unconventional problem because of complicated measurements of process parameters and synthesis of its accurate modelAdaptive control of ore mill charge
%3C1PGHL[2}HK_]YT.jpg)
(PDF) Optimization and performance of grinding circuits: the
2020年1月16日 This could be achieved through closer monitoring of the primary crusher performance and proper control of the ratios for the SAG mill feeders drawing the ore from the stockpile The ball mill 2019年4月19日 An acceleration time of 8 – 12 seconds is normal, except for clutch drives, where 610 seconds is preferable The performance of a mill is predicted in advance from theory and from pilot plant experience with a particular ore These conclusions are then scaled up and the mill drive sizedElectric Drives for Large Ore Grinding Mills 911Metallurgist