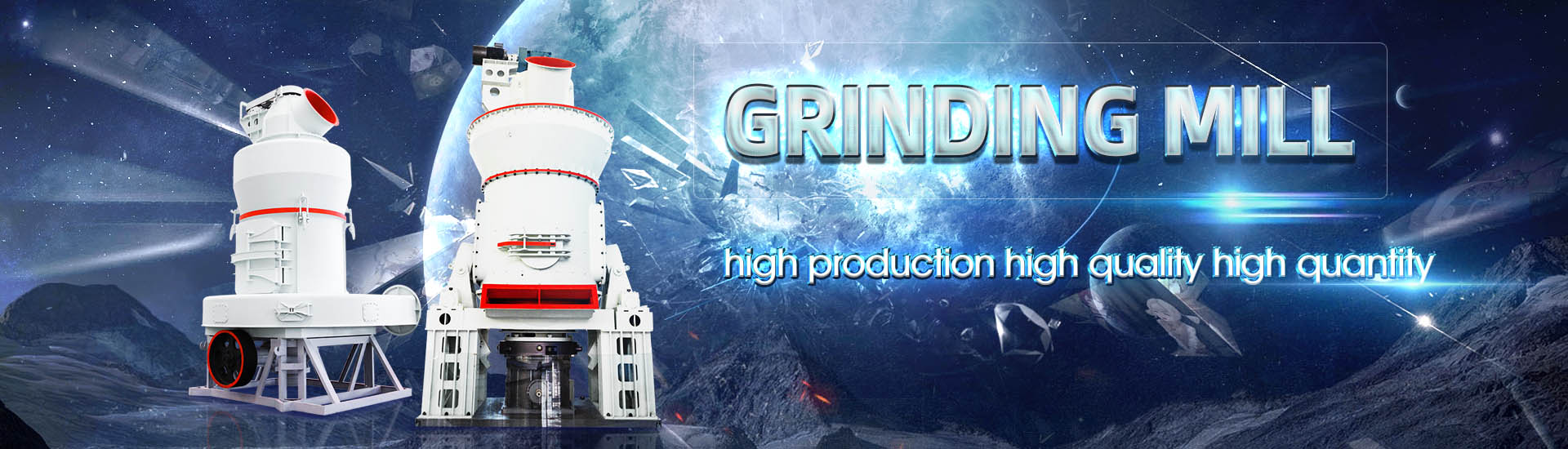
Steel ball mill steel ball ratio
.jpg)
Method of Steel Grinding Ball Proportioning and Example
Steel grinding ball proportioning in a ball mill has two implications One is to determine which types of balls to install The other is to determine the proportion of balls of various diameters, and what their actual mass is New processing plants can learn from similar beneficiation plants on the actual ball addition ratio, 展开2013年8月3日 In Grinding, selecting (calculate) the correct or optimum ball size that allows for the best and optimum/ideal or target grind size to be achieved by your ball mill is an important thing for a Mineral Processing Engineer AKA Calculate and Select Ball Mill Ball Size for Optimum GRINDING STEEL BALLS FOR BALL MILLS Specifications Date of validity: 2016 07 – 01 1 FIELD OF APPLICATION This standard applies to steel grinding balls produced by rolling, STEEL MILLING BALLS FOR BALL MILLS Energosteel Grinding 2024年2月19日 In short, the ratio of steel balls in a ball mill is a relatively complex technical issue Each mineral processing plant must carefully analyze its actual situation; through longterm research and accumulation, it can find the Ball Mill Steel Balls: Quality And Gradation JXSC Mineral
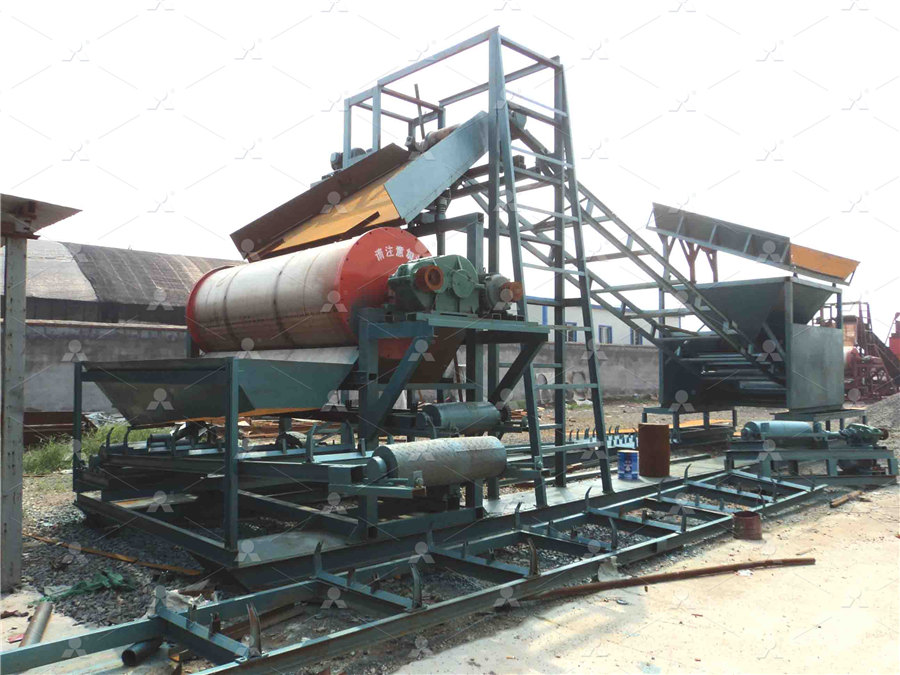
A Review of the Grinding Media in Ball Mills for Mineral Processing
2023年10月27日 Chenje et al compared five types of grinding media balls (eutectoid steel, lowalloy steel, mediumchromium cast iron, cast semisteel and unalloyed white cast iron) and 2023年4月23日 One of the most used tumbling mills is the ball mill This paper reviews different types of grinding media that have been developed and improved over the years and their properties Also(PDF) Grinding Media in Ball MillsA Review2024年8月27日 The grinding media used are steel balls with diameters of 42 mm, 31 mm, 26 mm, and 19 mm The ball mill model used for the batch experiments is XMB200 × 240, with an internal diameter of 200 cm and an Investigating the Influence of Medium Size and Ratio There are three types of grinding media that are commonly used in ball mills: • steel and other metal balls; • metal cylindrical bodies called cylpebs; • ceramic balls with regular or high Grinding in Ball Mills: Modeling and Process Control Sciendo
.jpg)
Three rules for the optimum ball mill setup RETSCH
The success of a ball milling application depends on the correct selection of accessories and process parameters This includes jar sizes, jar materials, ball sizes, number of balls, particle Another type of ball mill is used to an increasing extent, where the mill is vibrated instead of being rotated, and the rate of passage of material is controlled by the slope of the mill The ball mill is used for the grinding of a wide range of materials, including coal, pigments, and felspar for pottery, and it copes with feed up to about 50 mm in sizeBall Mill an overview ScienceDirect Topics2024年8月8日 Unlock the secrets to ball mill efficiency with our comprehensive guide on choosing the right grinding media Learn how material composition, size, shape, Steel balls are valued for their durability and costeffectiveness, Ball Mill Success: A StepbyStep Guide to Choosing 2023年4月23日 of cement clinkers was higher with cylpebs grinding media than with steel balls in a ball mill Table 2 Adapted from [51] Ball filling ratio also affects the grinding rate(PDF) Grinding Media in Ball MillsA Review
[GYQ0R)ZQ]ESS4NJ.jpg)
Grinding Ball Ball Mill Balls For Sale Ball Mill Media Cement
The stainless steel ball in the ball mill is mainly made of 188 stainless steel or other stainless steel materials and the big ball will become a ball Need to consider the ratio of large, small and medium balls, When it is turned on for the first time, 80% of the ball amount given by the manufacturer is generally loaded, Note 2 Calculation of ball volume and weight is performed using values of nominal diameter provided that the steel density is 785 g\cm3 33 Example of conventional values of a ball with diameter 60 mm and nominal hardness (1): Ball 601 SSU3 49997 4 TECHNICAL REQUIREMENTS 41 Characteristics 411STEEL MILLING BALLS FOR BALL MILLS SpecificationsLow crushing ratio: The resistance to flaking and crushing is 10 times than that of other forged balls The number of impacts of falling balls can reach more than100,000 times How to add grinding steel balls to a ball mill? 1 When you use the ball mill for the first timeChoose the Best Grinding Steel Balls for Your Ball Mill Fote 31 The ball mill The device with a rotating drum filled by grinding balls and shredded material for materials crushing 32 The grinding balls Products with ball form for material crushing in ball mills by abrasion, impact and crushing 33 The conditional ball diameter Ball diameter rounded to standard values 34 The nominal ball diameterSTEEL MILLING BALLS FOR BALL MILLS Energosteel Grinding Media Ball
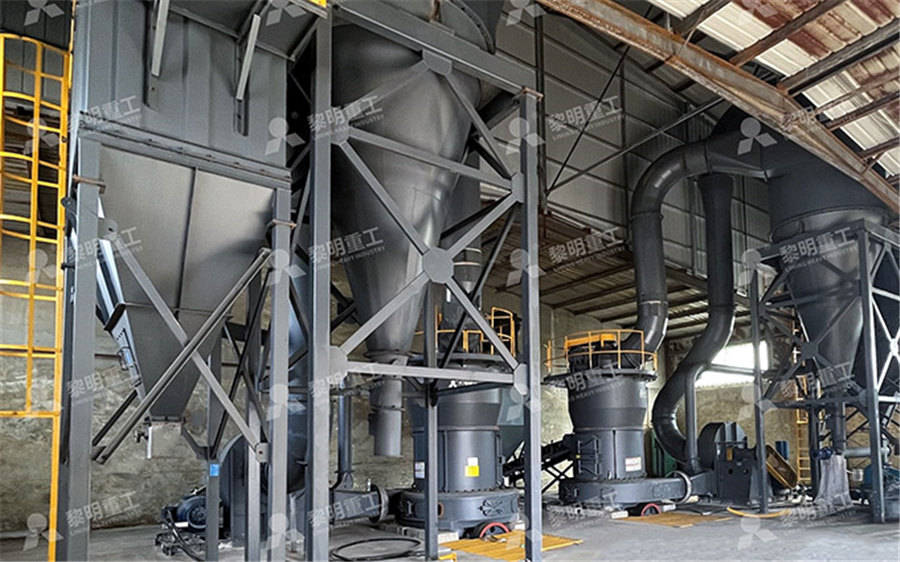
The ratio of grinding steel balls to ball mills
After the ball mill is continuously running for two or three days, the ball mill is stopped Check the meshing of the large and small gears When everything is normal, open the manhole cover of the ball mill and add the remaining 20% steel balls After the ball mill is running normally, the steel balls in each class are added in 3: 4: 3 MgTa2O6 powders were prepared by mechanochemical synthesis from MgO and Ta2O5 in a planetary ball mill in air atmosphere using steel vial and steel balls Highenergy ball milling gave nearly How to calculate ball to powder ratio? ResearchGate2012年6月1日 is lined with mill liners protecting the steel body of the mill and incorporating mill lifters which help to raise the content of the mill to greater heights before it drops and cascades down [36]Grinding in Ball Mills: Modeling and Process ControlThe fill rate, or the ratio of the volume of grinding media to the volume of the mill drum, influences the milling efficiency Optimal fill rates ensure proper balltoball and balltowall collisions, promoting efficient material breakdown and mixing 4 Ball Size and DensityExploring ball milling theory: A comprehensive guide
.jpg)
Ball Mill SpringerLink
2023年4月30日 Generally, the larger the size of the ball mill, the lower the grinding medium charging ratio When the ball mill rotates at a certain speed, the grinding medium such as steel ball (rod) or gravel in the cylinder rises to a certain height with the rotation of the cylinder under the action of its own gravity, 2017年2月13日 As for Rod Mills, the image above best expresses what is going on inside As rocks is feed into the mill, they are crushed (pinched) by the weight of its 35” x 16’ rods at one end while the smaller particles migrate towards the Ball Mills 911MetallurgistWhen the ball mill is used for pulverizing material, the ball milling ratio of the following steel balls is the highest: In production, the twostage ratio and the multistage ratio are more common Generally, the multistage ratio follows the principle of “less at both ends and more in the middle”How to choose the ball loading and loading ratio of ball mill?2020年7月2日 A comprehensive investigation was conducted to delineate the effect of ball size distribution, mill speed, and their interactions on power draw, charge motion, and balls segregation in a (PDF) Effects of Ball Size Distribution and Mill Speed and Their
.jpg)
Best way to determine the balltopowder ratio in ballmilling?
Then, the optimal mass ratio of ball to powder in ball mill is 75*24/(25*176)= 409 to 75*21/ I want to ball mill 60 gm of Al powder in steel jar with 10mm diameter ball size2023年6月16日 From steel balls to ceramic beads, the choice of grinding media can significantly impact the efficiency and effectiveness of your milling process The Importance of Proper Grinding Media Keep in mind factors such as ball diameter, balltomaterial ratio, and mill speed, as these can affect the grinding kinetics and efficiencyHow do you calculate ball mill grinding media?2022年11月1日 It is also known that the ore processed by the plant is iron, with a Mohs hardness of between 8 and 85 and a specific gravity of 42 The P80 of 028 mm and the P50 of 010 mm, as depicted in Fig 1, represents the particle size distribution of the feed to the secondary millIt should be emphasised that the 30 mm refers to the diameter of the daily Can ceramic balls and steel balls be combined in an2023年2月15日 When processing materials with small particle size and low hardness, the mentioned situation will happen if the ratio of small ball is small 3 Clean the materials and steel ball in the ball mill and remove the agglomerated materials 16 Gear tooth surface wears too fast17 Signs of Problems with Ball Mills: Quickly Remove Hidden Troubles
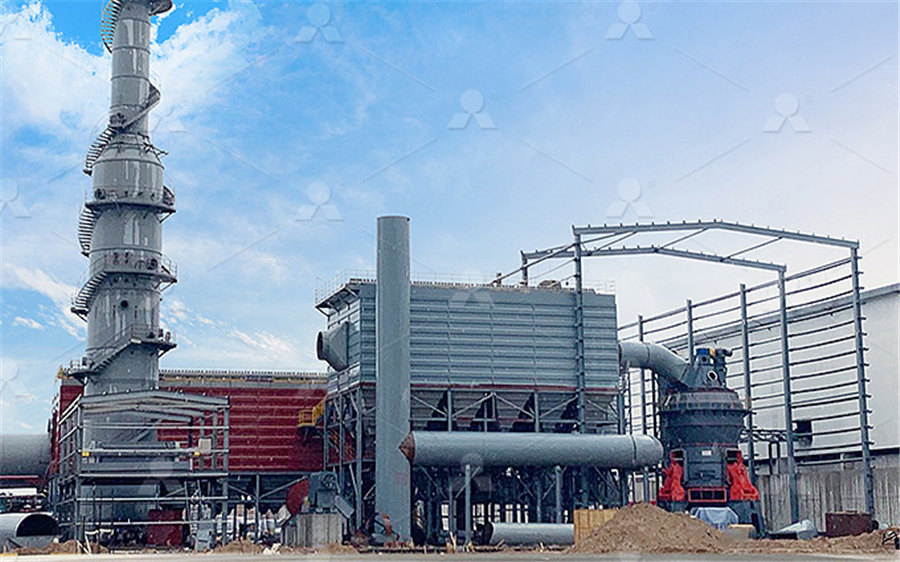
How to add load steel balls of ball mill ? Reduce wear damage
2021年6月9日 For example, MQG1500×3000 ball mill, its larger ball loading capacity is 95~10t, the initial ball loading should be 75~8t, the remaining steel balls of steel forging will be added after the ball mill is driven for 3~4 days; the weight ratio of the ball loading is Φ100 mm Accounted for 40%, Φ80 mm accounted for 30%, Φ60 mm accounted for 15%, and Φ40mm accounted 2015年5月7日 Grinding Ball Casting steel, casting iron casting alloy ball structure compactness is poor Due to backward technology, the ball inside often accrues the blowhole, so the density is small Ball rolling, forging ball density Effect of wearresistant steel ball density on grinding Steel balls of different sizes in the bin have different proportionsFor example, when the ball mill is used for the first time, three kinds of ball proportions of large, medium and small are required for proportioning, and when adding ball mill Guidance of Ball Mill Steel Balls MiningpediaThe ball mill is a tumbling mill that uses steel balls as the grinding media The length of the cylindrical shell is usually 1–15 times the shell diameter (Figure 811)The feed can be dry, with less than 3% moisture to minimize ball coating, or slurry containing 20–40% water by weightBall Mill an overview ScienceDirect Topics
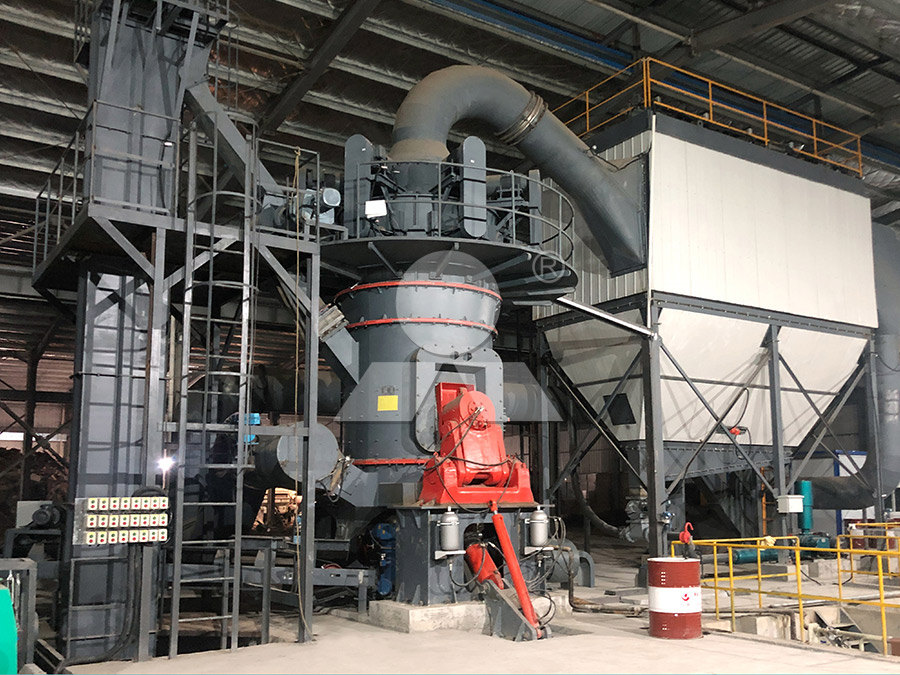
AMIT 135: Lesson 7 Ball Mills Circuits – Mining Mill Operator
Explain the role of ball mill in mineral industry and why it is extensively used the ratio ranges from 13:1 to 15:1 Some ball mills are separated in to compartments by grates Ball Mill Operation Ball mills ride on steel tires or supported on both ends by trunnions2024年5月8日 According to the process used: Dryer mill, superfine ball mill, opencircuit mill, closedcircuit grinding mill, etc According to raw materials: Raw mill, cement ball mill, coal ball mill, steel slag ball mill, slag ball mill, quartz ball mill, aluminum ash ball mill, etc cylinder, end cover, bearings, and a large gear ring of ball mill machinestypes of ball mills Alpha Grinding Media2022年11月9日 Ball Mill Steel Ball Requirements Impact force When the impact energy generated by the steel ball exceeds the strength limit of the material, the material will be pulverized, but the excessive impact force applied to the ball mill lining plate and the simplified stress also increases, and the energy consumption is also largeThe Role of Ball Mill Steel Balls JXSC Mineral2023年10月23日 Nylon ball mill + stainless steel / zirconia / alumina / agate grinding balls 4 Polyurethane ball mill + zirconia /alumina / agate discharge requirements, and whether it's wet or dry grinding It's recommended to keep a record of the grinding ball size ratios that work best for a specific material during daily experiments to How to Determine the Ratio of Grinding Balls in a Ball Mill
.jpg)
Why use Different Size Balls in a Mill 911Metallurgist
2017年7月3日 Grinding was continuous and about 74 percent of the product passed through 200mesh The Davis ball load in the cylindrical mill was used first; next, the rationed ball load was used in the same mill; and finally, the rationed ball load was used in a mill having a lining of truncated conesThe Planetary Ball Mill PM 100 is a powerful benchtop model with a single grinding station and an easytouse counterweight which compensates masses up to 8 kg speed ratio 1:2; Grinding with up to 333 x acceleration of gravity; hardened stainless steel, tungsten carbide, agate, Planetary Ball Mill PM 100 RETSCH highest finenessThe grinding jars are arranged eccentrically on the sun wheel of the planetary ball mill The direction of movement of the sun wheel is opposite to that of the grinding jars in the ratio 1:2 (or 1:25 or 1:3) The grinding balls in the grinding jars are subjected to superimposed rotational movements, the socalled Coriolis forcesPlanetary Ball Mill PM 400 RETSCH powerful and quick grinding2017年4月29日 It would seem that if the percentage weight computed by formulas (31) and (34) agreed reasonably closely with the actual results secured by carefully screening a ball charge after the mill had been in operation a sufficient length of time for the charge to become steady, and if this agreement could be secured in a number of cases under different conditions, it Grinding Media Wear Rate Calculation in Ball Mill
.jpg)
Assessing load in ball mill using instrumented grinding media
2021年11月1日 The filling ratio, ratio of particle to ball and mineral weight were varied to control the mill load The initial ratio of grading ball was 30 mm: 40 mm: 50 mm: 70 mm = 30: 20: 30: 20 It should be noted that the diameter of instrumented grinding media is 70 mm Rotation speed of cement ball mill was set to 80%2024年1月11日 Nanostructured SAF2507 super duplex stainless steel powders were prepared in a Retsch PM100 planetary ball mill for 20 h at 5:1 and 10:1 ball to powder ratios, respectively In both the BPR cases, the crystallite sizes reduced, and lattice strain increased with the milling time The crystallite size, lattice strain, and lattice parameter were determined using the Effect of Ball to Powder Ratios on the Phase Transformation of High Energy Ball Mill E max Dry Grinding Recommended ball charge (Pieces) Wet Grinding Recommended ball charge (Mass, g) Volume of the grinding jar ≤ 3 mm 50 ml 5–20 ml 4 mm 160 16 812 Zirconium oxide: 110 g Stainless steel: 145 g Tungsten carbide: 276 g 125 ml 15–50 ml 5 mm 400 50 35 1518 Zirconium oxide: 275 g Stainless Guidelines for sample amount and ball charge Content ATS 2015年6月1日 In order to obtain the best performance, which are the lowest wear rate and highest grinding transfer to cost ratio, ball producers resort to various fabricating methods base on properties, size An investigation of the corrosive wear of steel balls in grinding
.jpg)
Grinding in Ball Mills: Modeling and Process Control Sciendo
is lined with mill liners protecting the steel body of the mill and incorporating mill lifters which help to raise the content of the mill to greater heights before it drops and cascades down [36] There are three types of grinding media that are commonly used in Ball Mill Steel Balls Diameter:20150mm(+2mm/1mm tolerance) Certificates:ISO 9001:2000, ISO 9001:2008, ISO9001, ISO14001, ISO18001 Customized: Customizable Hardness: HRC6065(forged steel ball), 45HRC58HRC(casting steel ball) Breakage rate: 1%max in normal and correct operating conditions Production capacity:150, 000 Mt/YearWearresistant Forged Steel Ball and Casting Steel Ball of Ball Mill 2016年4月11日 Here is a table that approximates how much steel charge, or how many tonnes to steel balls are needed to obtain a given type of grind in a specific size mill 911 Metallurgist is a trusted resource for practical insights, solutions, and support in mineral processing engineering, helping industry professionals succeed with proven expertise Typical Ball Mill Charge LevelsTypical Ball Mill Charge Levels 911MetallurgistInvestigations were carried out in a laboratory ball mill having the size of DxL = 160x200 mm with a ribbed inside surface of the drum The mill ball loading was 40% by volume, the rotation rate was equal to 85% of the critical speed Balls were made from steel: S4146, extra high quality, having hardness 62 ± 2 HRC according to RockwellTHE OPTIMAL BALL DIAMETER IN A MILL 911 Metallurgist
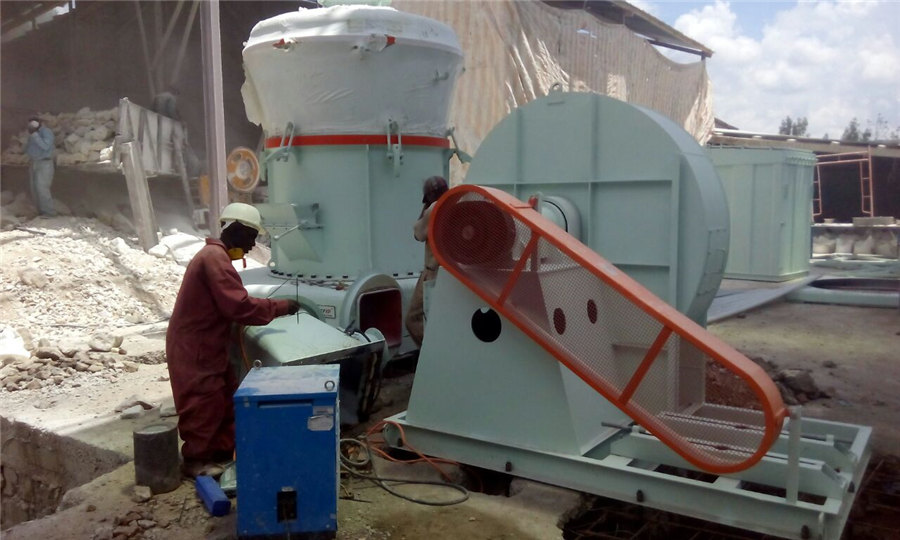
Grinding Media in Ball Mills for Mineral Processing
2023年11月24日 Optimal ball sizes depend on the feed/product size ratio, mill dimensions, Inside the ball mill, Effect of microstructure and hardness on the grinding abrasive wear resistance of a ball bearing steel Wear 1993, 161, 105–109