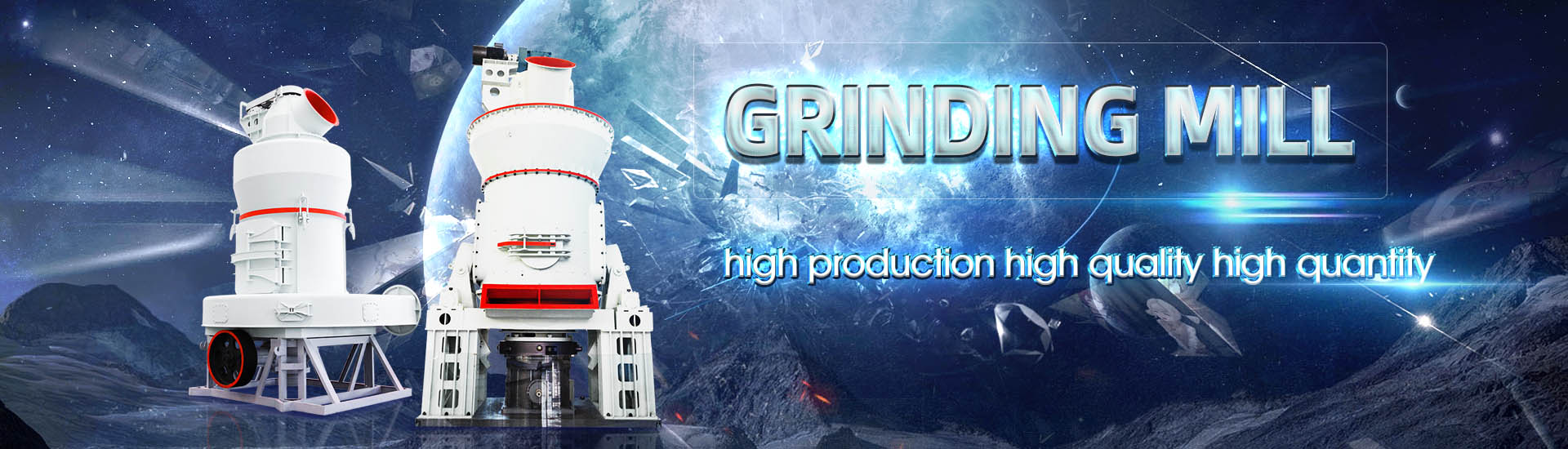
Axial Ore Grinding Mill
.jpg)
SAG mills and AG mills – efficient grinding – FLS
FLS AG and SAG mills deliver high throughput ore grinding with impressive energy efficiency, helping you maximise mineral recovery and reduce TCO Even better, our advanced process 2012年6月1日 The paper presents an overview of the current methodology and practice in modeling and control of the grinding process in industrial ball mills Basic kinetic and energy Grinding in Ball Mills: Modeling and Process Control ResearchGateGrinding in ball mills is an important technological process applied to reduce the size of particles which may have different nature and a wide diversity of physical, mechanical and chemical Grinding in Ball Mills: Modeling and Process Control Sciendo2020年6月15日 Grind curves give the steadystate values of the performance variables throughput, power draw, and grind in terms of the mill filling and critical mill speed The grind Steadystate and dynamic simulation of a grinding mill using grind
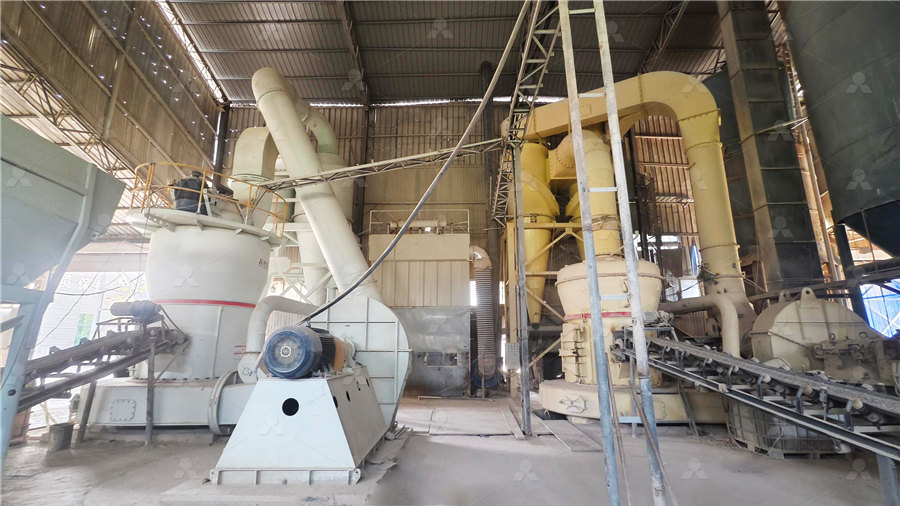
Grinding mills for mining and minerals processing
Customized grinding mill parts including heads, shells, trunnions and liners, main bearings, gears and pinions, and more! Metallic, PolyMet™, Megaliner™, Rubber and Orebed™ mill liners for all mill types Whether old or new, we can The dry milling of ore in LOESCHE vertical roller mills has shown significant process advantages, as well as economic and ecological benefits To demonstrate these a mobile oregrinding plant the OGPmobile has been Mills for minerals and ores Loesche2023年3月15日 In this study, a semiautogenous grinding mill of 88 m x 48 m in SABC process of a mine is taken as the research object The daily ore handling capacity of this series is Journal of Physics: Conference Series PAPER OPEN ACCESS You 2023年7月20日 Moist grinding, a special grinding method, is used to prepare pellets for smelting According to the grinding medium features, ore grinding is mainly classified into ball grinding Ore Grinding SpringerLink

Grinding Mill Operation and Scaleup: Theory and Equations
The ratio: rotational mass flow of media to axial mass flow of ore—a concept recently introduced—has been refined and extended It can account for similar breakage in scaled mills 2017年10月26日 The following are factors that have been investigated and applied in conventional ball milling in order to maximize grinding efficiency: a) Mill Geometry and Speed – Bond (1954) observed grinding efficiency to be a Factors Affecting Ball Mill Grinding Efficiency2019年1月30日 The weight of mill and charge (ore and grinding media) is 3,452 tons The substructure method is used for dynamic analysis of the ball mill foundation, that is, the structure and soil are DYNAMIC ANALYSIS FOR BALL MILL FOUNDATION A Review of the Grinding Media in Ball Mills for Mineral Processing, 2023 The ball mill is a rotating cylindrical vessel with grinding media inside, which is responsible for breaking the ore particles Grinding media play an important Ball motion, axial segregation and power
.jpg)
Endmill Design Basics Mastercut Tool Corp
Axial relief – The relief measured in the axial direction between a plane perpendicular to the axis at the cutting edge and the relieved surface Helps to prevent rubbing as the corner wears Concave relief – The relieved surface behind the cutting edge having a concave form Produced by a grinding wheel set at 90 degrees to the cutter axis1995年1月1日 Grinding tests were carried out using a model agitation bead mill with a single disc Four different types of disc were used to examine the effect of the motion of the grinding media in the axial Motion of Grinding Media in Axial Direction and its Effect on This mill accepts grinding set weights of up to 30 kg, the largest grinding jar has a volume of 2,000 ml chemical industry, etc, it has two ore grinding Compare this product Remove from comparison tool ball grinding mill horizontal for ore ball grinding mill Final grain size: 74 µm Ore mill, Ore grinding mill All industrial manufacturers2023年7月20日 Therefore, the rod mill is mostly used for coarse grinding of the previous period of ball mill, or grinding of brittle materials and materials against overcrushing, such as tungsten and tin ore before gravity separation; and (3) autogenous mill – it refers to the materials which themselves are collided and ground mutually to be crushed when the grinding mill rotates, and Ore Grinding SpringerLink
.jpg)
DYNAMIC DESIGN FOR GRINDING MILL FOUNDATIONS
2019年1月30日 The weight of mill and charge (ore and grinding media) is 3,452 tons Axial, lateral, and rocking oscillations of rigidlycapped pile groups are studied parametricallyCondition in one of the grinding chambers of the mill Results of Optimization The graphical analysis presented in Figure 2 represents progress of grinding along the length of the mill after optimizing the grinding process rogress of grinding is clearly visible in Desired p the graphs Figure 2: Analysis of longitudinal samplesOPTIMIZATION OF CEMENT GRINDING OPERATION IN BALL MILLS2024年4月26日 The choice of grinding mill depends on factors such as the desired product size, capacity requirements, and energy consumption b Autogenous and SemiAutogenous Mills: In some cases, autogenous (AG) and semiautogenous (SAG) mills are used for grinding These mills utilize the ore itself as the grinding media, reducing the need for additional Iron Ore Processing: From Extraction to Manufacturing2023年4月1日 The particle breakage of the ball mill is an extremely complicated breakage process It is difficult to quantify and describe the particle breakage behavior In this study, a dropball experimental setup was developed to demonstrate the impact process of Experimental investigation of the impact breakage characteristics

Effects of axial grinding media distribution on the disc wear
2022年7月1日 This grinding media displacement may lead to hydraulic grinding media packing which has negative consequences for both, the grinding process and the mill wear Moreover, grinding media displacement and which can usually be identified by an extremely high power consumption which goes in line with a worse particle size reduction relation (Kwade and 2009年8月1日 Grinding of clinker for cement production is often performed in a two chamber ball mill In the first shorter chamber, raw feed is ground using media consisting of large ballsBall motion, axial segregation and power consumption in a full herein The diameter of mill is 80 m with length of 131 m, operating at 12 rpm The height of mill shaft is 181 m above ground The weight of mill and charge (ore and grinding media) is 3,452 tonsDYNAMIC DESIGN FOR GRINDING MILL FOUNDATIONS2009年8月1日 The internal shell diameter of the first chamber is 385 m and it is 43 longIt has a wave liner fitted consisting of 36 liner plates around the circumference Fig 1 shows the internal structure of the first chamber of the cement mill Fig 2 shows a close up of the lifter plates whose profile consists of a gradual rise to a high point followed by an abrupt drop back to the shellBall motion, axial segregation and power consumption in a full
.jpg)
A Comprehensive Guide to SAG Mill Operation ball mills supplier
The rock and grinding media are placed in the mill and rotated, causing the grinding media to tumble and crush the rock into smaller pieces The mill operates in a closed circuit with screens that size the ore and send it back to the mill for further grinding The product from the mill is then sent to a cyclone for separation of the desired The Autogenous Mill, also known as AG Mill, is a type of grinding mill used in the mining industry This machine uses ore and rock itself as grinding media to perform its job Unlike other types of mills that use steel balls or rods for grinding materials, the Autogenous Mill relies on the material being ground to break itself into smaller piecesUnderstanding the SAG Mill in Copper Ore Mining Process2024年5月20日 The ball mill lifts the grinding media by rotation of its horizontal cylindrical part which then falls back impacting the ore particles The grinding action is then achieved by attrition, abrasion, and impact between the ore and the grinding media 3 Spherical media has been commonly used in ball mills; however, different shapes of grinding media have different Effect of grinding media shape on the particle size distribution of 2002年7月1日 Axial mixing models have also been used for interpretation of mill performance based on the molecular diffusion (Abouzeid and Fuerstenau, 2012, Kis et al, 2006, van Nierop and Moys, 2002, where Axial mixing of slurry in an autogenous grinding mill
.jpg)
Axial Force Analysis and Roll Contour Configuration of FourHigh CVC Mill
2018年1月4日 In order to analyze the influence of technical parameters on work roll axial force of fourhigh continuous variable crown (CVC) mill, the deformation analyzing model with top roll system and strip Skip to Article Content; Skip to Article Information; which varies with work roll grinding For the thirdorder CVC curve, An autogenous mill of ID 67 m and an effective grinding length of 21 m was fed with ore of SG 38 to 20% of its volume The mill was operated continuously 24 hours per day at 1200 t per day and 75% of the critical speed The solids in the mill charge were at 80% solids Estimate:1Semi Autogenous Grinding Mill ScienceDirect Topics2019年7月19日 A stirred bead grinding mill includes a substantially cylindrical grinding shell and a central stirring shaft within the grinding shell The central stirring shaft is provided with axially spaced stirring elements, preferably grinding discs, along the central stirring shaft A replaceable grinding element is provided that includes an axial support structure arranged to form the outer Stirred bead grinding mills Justia PatentsWe have been designing and manufacturing Semi Autogenous Mill (SAG Mill) and Autogenous Mill (AG Mill) under the FullerTraylor brand since the early 1980s Semiautogenous grinding uses a minimal ball charge in the range of 615% while autogenous grinding uses ore onlySAG mills and AG mills – efficient grinding – FLS
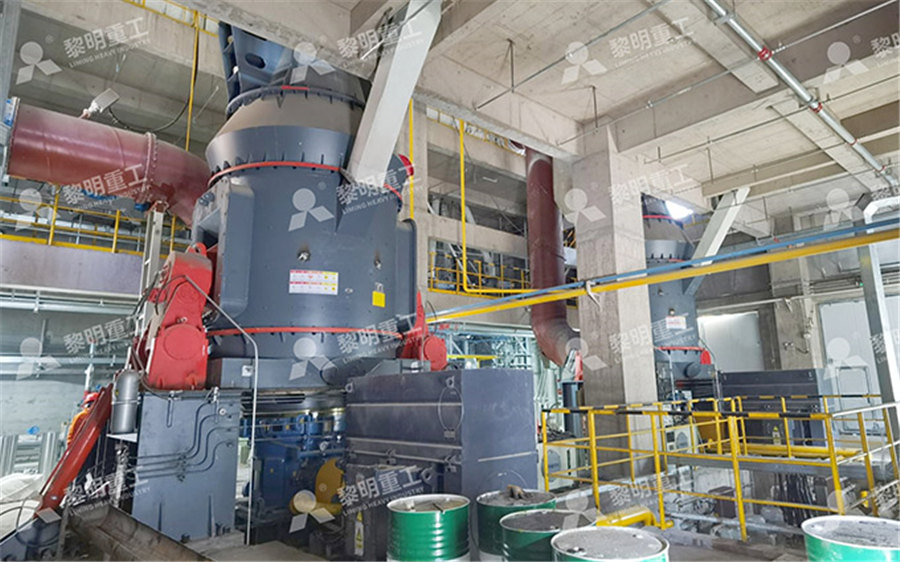
How to choose a suitable ore powder grinding mill?
2023年10月17日 Factors for choosing a suitable ore powder grinding mill 1 Raw material characteristics: Different raw materials have different hardness, humidity and grinding and crushing properties, and the corresponding ore powder grinding mill needs to be selected to meet the processing requirements 2 Production capacity: Determine the required processing Highstress abrasive wear is a major material consumption process in mining and ore beneficiation industries The common laboratory highstress abrasion apparatuses suffer from lack of capability of closely simulating the service conditions of grinding media and mill liners, being the main consumables in these sectors The ball mill abrasion test (BMAT) is a versatile Ball mill abrasion test (BMAT): Method development and statistical With ore grades decreasing, our process team helps to maximize the efficiency of your grinding circuit using Premier™ horizontal grinding mills Combining process expertise, in house capabilities and an unrivaled product portfolio, we aim to Premier™ Horizontal Grinding Mills Metso2022年4月25日 A more positive axial rake lowers cutting forces which helps to increase feed rates The core of the tool is thicker due to the shape of the helix and the tool is stronger High helix Endmills are typically used in tougher harder materials because they wear better, although they can also be used in softer materials like aluminumThe Guide to Grinding a HighPerformance Endmill: Part 1
.jpg)
Ultrasonic vibration millgrinding of singlecrystal silicon carbide
2018年2月15日 For both conventional millgrinding (CMG) and UVMG, the axial grinding force gradually increases with the grinding time and the total machined depth of the blind hole However, the increase tendency of axial grinding force in UVMG is barely visible, and the axial grinding force in UVMG is reduced by 60–70% compared to the CMG process2018年4月18日 These studies have been important in a coordinated optimization program for mill heads, shells and trunnion bearings Mill Shells require a similar but more complicated program for stress and deflection analysis Often, depending on the load concentration and mill length, special shell designs are required An example is shown on Figure 5SAG Mill Components 911MetallurgistResponsive Multipurpose HTML5 Business Template well reputed chinese ball mill companies in ukraine We are a professional mining machinery manufacturer, the main equipment including: jaw crusher, cone crusher and other sandstone equipment;Ball mill, flotation machine, concentrator and other beneficiation equipment; Powder Grinding Plant, rotary dryer, briquette ball mill girth gear radial axial alignment procedure2006年11月1日 Request PDF Axial transport in dry ball mills Ball mills are used for grinding of rocks, cement clinker and limestone from 10100 mm feed sizes down to sub millimetre product They are Axial transport in dry ball mills Request PDF ResearchGate
.jpg)
Roller Mill SpringerLink
2023年7月4日 Roller mill is a type of grinding equipment for crushing materials by pressure between two or more rolling surfaces or between rolling grinding bodies (balls, manganese ore fine grinding, and other fields Horizontal Cylinder Roller Mill As for the horizontal cylinder roller, its roller surface and roller have a horizontal layout2020年10月9日 This method simulates the particles size, mill power, and qualified particles quality of crushed particle, which reveal the grinding strength and energy consumption of the SAG mill In this paper Operation Analysis of a SAG Mill under Different Spindle runout can shorten tool life and increase the likelihood and incidence of producing defective parts Even if your spindle is still in relatively good condition, untreated runout can shorten the spindle’s life and cause further damage to tools and partsSpindle Runout: How to Test, Measure Reduce Northland 2017年2月20日 All Grinding Mill Ball Mill Manufacturers understand the object of the grinding process is a mechanical When choosing primary autogenous grinding, run of mine ore up to 200300 mm in size is fed The spherical roller bearing and the hydrostatic shoe bearing take a very limited axial space compared to a conventional Grinding Mill Design Ball Mill Manufacturer 911Metallurgist
.jpg)
Ball Mill VS AG Mill: What are the Similarities and Differences?
2020年5月20日 Ball mill, rod mill and AG mill are common equipment for grinding operation in mineral processing plants The difference between ball mill and rod mill has been known before, but what are the similarities and differences between ball mill and AG mill? This article will take you to explore so as to help you choose the appropriate grinding equipment more convenientlyAxial mode shapes are movements of stator parts in axial direction of the mill The magnetic forces between rotor and stator in axial direction of the mill are too small to excite axial mode shapes The modal analysis shows the following axial mode shapes: Figure 4: 1st axial mode shape; Bending of upper part of statorDesign and dynamic behavior of large Ring Motors for grindinggrinding balls of up to 150 mm (6 in) in diameter These actions apply crushing, attrition and abrasion comminution processes to reduce primarycrushed ores down to ballmill sized feed Feed ore with a top size of up to 200 mm (8 in) and water enter the feed end of a SAG mill through a feed chute; the ore is milled in the shell andSemiautogenous grinding (SAG) mill liner design and development2019年1月19日 This paper presents the experimental results for grinding of tailings of ore processing to very fine particle sizes with a laboratory stirred ball mill in wet modeSCALE UP FOR ULTRAFINE GRINDING IN STIRRED BALL MILL
.jpg)
SAG Mill Liner Design 911Metallurgist
2016年6月6日 Bolt hole spacing (axial) Some mill vendors provide 305 mm (12 in) spacing, and this provides good flexibility for original and future design work Because of the nature of the grinding media (large ore pieces) and lack of steel ball media, various white irons are used because of their high abrasion resistance and,