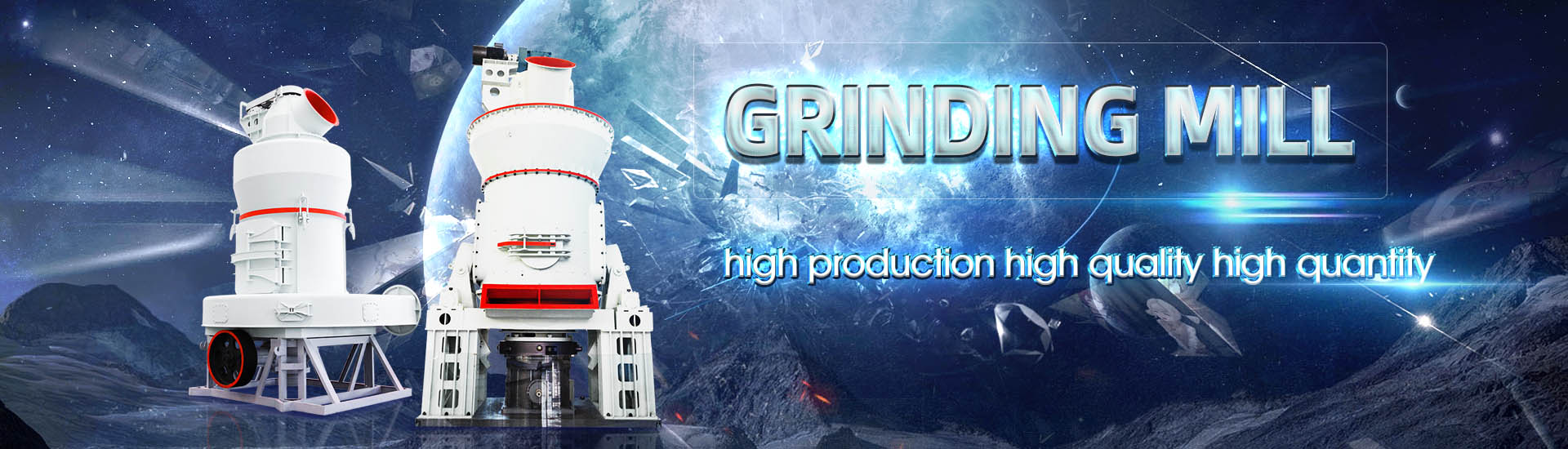
Ball mill waterflying method
.jpg)
SolventFree Ball Milling Synthesis of WaterStable TinBased
4 天之前 A pseudohalide (SCN −) tinbased perovskite material using a solventfree ball milling method is developedThe synthesized perovskite exhibits longterm water stability and demonstrated significant photocatalytic activity in reducing CO 2 to CO under light irradiation 2024年6月3日 In recent years, the use of ball milling to synthesize biochariron based materials has become an emerging and promising method due to its low cost, environmental Research progress on synthesis mechanism and performance2020年9月1日 Mechanochemical synthesis of nanobiochar by ballmilling technology is gaining attention for the sake of its lowcost and ecofriendly nature Ball milling as a non/lesssolvent Ball milling as a mechanochemical technology for fabrication of Amongst all the methods that can be employed for the mechanochemical processing of cellulose, ball milling is an emerging technique, which allows avoiding organic solvents Being easy to use, fast, economical and Ball milling: a green technology for the preparation and
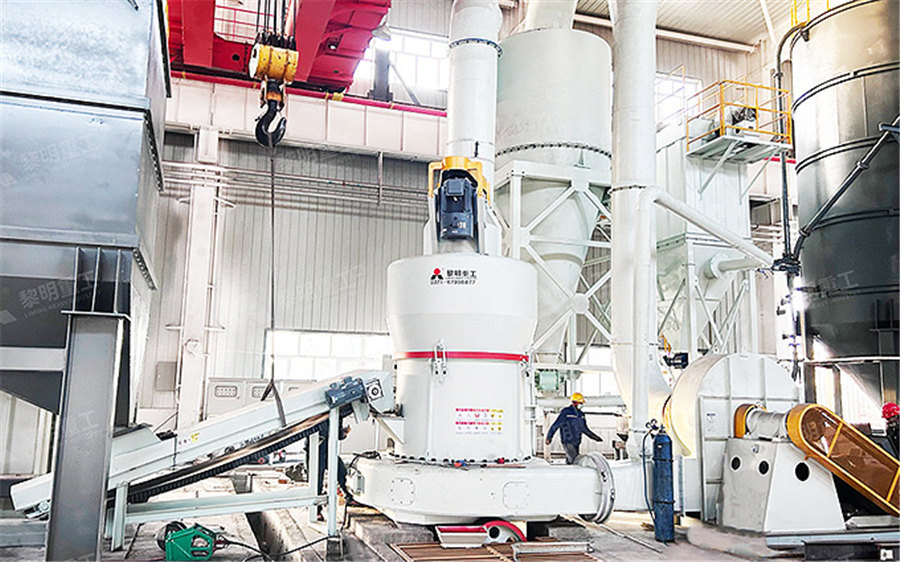
Ball milling: a green technology for the preparation and
Amongst all the methods that can be employed for the mechanochemical processing of cellulose, ball milling is an emerging technique, which allows avoiding organic solvents Being easy to 2024年6月7日 Graphitemodified ZVAls via a ball milling method could not only prevent agglomeration of ZVAls but also promote absorbability, electrical conductivity, and hydrophobicity of materials Recent Advances in BallMilled Materials and Their At present, the synthesis methods of MOFs mainly include the hydrothermal method, microwave assisted method, ultrasonic assisted method, electrochemical method, and ball milling (BM) method [12,13,14,15] Ball milling is a Synthesis of Metal Organic Frameworks by BallMilling2024年2月28日 The results showed that ball milling effectively reduced the particle size of biochar, increased the specific surface area, and more importantly, enhanced the content of Removal of Cr(VI) from aqueous solution using ball mill modified
.jpg)
Suppressing Heavy Metal Leaching through Ball Milling
2016年7月8日 Ball milling is investigated as a method of reducing the leaching concentration (often termed stablilization) of heavy metals in municipal solid waste incineration (MSWI) fly ash Three heavy metals (Cu, Cr, Pb) loose More recently, Song et al described a new method to extract CNCs from raw cellulose by ball mill assisted acid hydrolysis 43 The starting material was first ground in water using a ball mill at 1300 rpm, then treated with oxalic acidBall milling: a green technology for the preparation 2023年1月12日 In this study, silica nanoparticles (SiO2 NPs) were fabricated using a handmade ball mill as a novel, simple, rapid, costeffective, and green approach The sol–gel method was also used to produce these NPs as a comparative method The SiO2 NPs produced by both methods were characterized using highresolution transmission electron microscopy Facile, fast, and green preparation of highpurity and quality silica Y HUANG Peng , et al: New Method to Measure the Fill Level of the Ball Mill: Part II — Analysis of the Vibration Signals 2 et al [11 –12] , is noteworthy In their work, two vibration sensors, 180 degrees apart, were used to collect signalNew Method to Measure the Fill Level of the Ball Mill II Analysis
.jpg)
Ball Mill SBM Ultrafine Powder Technology
Note: In the case of no water addition, the ball mill grinds dry powder, strong sealing, and can be operated under negative pressure to prevent dust from flying 4 Payment methods: Accepted Delivery Terms: FOB, CFR, CIF, EXW, CPT, DDU, Express DeliveryBall milling is a method of small pollution, short timeconsumption, and largescale synthesis of MOFs In recent years, many important advances have been made When water is an auxiliary solvent, a quantitative ZnMOF74 product is obtained after 35 min of grinding under 35 balls, Synthesis of Metal Organic Frameworks by BallMilling MDPI2020年4月21日 While hydrogenation reactions themselves can be conducted via different methods inside the ball mill, 20 the Sawama group found a unique reaction pathway using a stainlesssteel containing chromium and nickel They were able to transfer hydrogen or deuterium from water or deuterium oxide, Direct Mechanocatalysis: Using Milling Balls as CatalystsMechanical alloying uses ball mills to fuse powder particles an alternative to hightemperature alloy production methods small quantities Learn more Retsch ensuring the sample does not overheat, even during extended grinding periods The grinding jars are internally watercooled, allowing for continuous grinding without Mechanical Alloying with Ball Mills Retsch
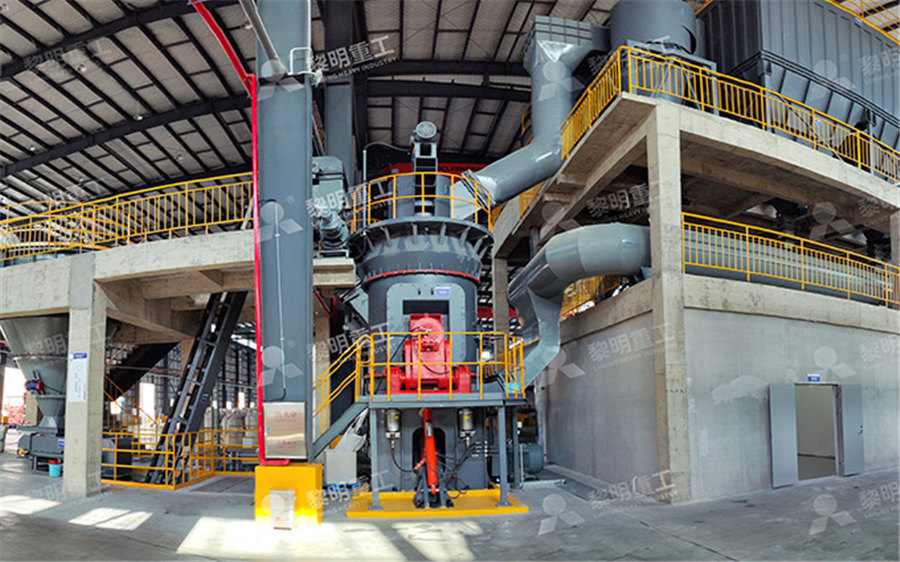
Ball mill: Principles, construction, working, uses, merits, and
2024年1月28日 2 Liners: An abrasionresistant material such as manganese steel or rubber typically lines the inner surface of the cylindrical shell to protect it from wear due to the grinding action 3 Balls: They place steel or ceramic balls, typically used as grinding media in a ball mill, inside the shell and rotate them with it 4 Feed and Discharge: Entering the hollow shell at the In this thesis, a procedure for predicting the charge motion and the power draw of a ball mill based on the discrete element method (DEM) is calibrated and validated by means of photographs of the charge, and power draw measurements of a 1:5scale laboratory mill, which were kindly provided by the company Magotteaux International SA University of Liège uliege2024年7月1日 2Operation of the Motor: When the feed material and grinding balls are put into the mill, the motor (green component on the left) is turned onThis motor is used to offer the required torque to rotate the milling chamber The motor is coupled to the chamber through gears so that the chamber rotates at a desired speedUnlocking the Science of Ball Milling Method JXSCIf a ball mill uses little or no water during grinding, it is a ‘dry’ mill If a ball mill uses water during grinding, it is a ‘wet’ mill A typical ball mill will have a drum length that is 1 or 15 times the drum diameter Ball mills with a drum length to Ball Mill (Ball Mills Explained) saVRee saVRee
.jpg)
(PDF) Effect of Ball Milling on the Properties of
2013年3月1日 The properties of zirconia powder prepared by alcoholaqueous method after ballmilling had been researched by BET,XRD,TEM and laser granularity instrumentThe results show that by using ball 2013年8月3日 In Grinding, selecting (calculate) the correct or optimum ball size that allows for the best and optimum/ideal or target grind size to be achieved by your ball mill is an important thing for a Mineral Processing Engineer AKA Calculate and Select Ball Mill Ball Size for Optimum 2019年1月9日 Ball milling is a simple, fast, costeffective green technology with enormous potential One of the most interesting applications of this technology in the field of cellulose is the preparation Ball milling : A green technology for the preparation and 2024年3月23日 In this work, we report a composite of NiFe2O4 with NiFe2O4/TiO2 prepared by a planetary ball mill for the reactive grinding method, where operating parameters of (sunwheel 200 rpm and jar 350 rpm) for 11 h were optimized XRD, particle size by zeta sizer, VSM, UVNIR spectrometer show that the catalyst has been successfully prepared, having improved Performances of NiFe2O4/TiO2 spinal photocatalyst prepared
.jpg)
Ball Mill Maintenance Installation Procedure 911Metallurgist
2016年10月20日 Am sure your Ball Mill is considered the finest possible There are two methods of identifying the “hand We recommend a mixture of 1:2:3 for ball mill and rod mill foundations The proper water to sand ratio should be carefully regulated since excess water increases the shrinkage in the concrete and lends to weaken it The ball mill abrasion test (BMAT) is an industriallyrelevant multipurpose wear test method that enables tribologists and abrasion scientists to study the abrasive wear behaviour of materials for various service applications, particularly for grinding balls and mill liners, under conditions and contact mechanics very similar to the industrial ball millsBall mill abrasion test (BMAT): Method development and 2019年10月19日 Ball mills are extensively used in the size reduction process of different ores and minerals The fill level inside a ball mill is a crucial parameter which needs to be monitored regularly for optimal operation of the ball mill In this paper, a vibration monitoringbased method is proposed and tested for estimating the fill level inside a laboratoryscale ball mill A vibration Monitoring the fill level of a ball mill using vibration sensing and 2018年6月1日 Our method combined with these chemical methods have the potential to dramatically reduce water and fuel consumption Conclusions The characteristics and enzyme digestibility of corn stover vary depending on water input during ball milling The dry milling mode (0% water input) leads to quick grinding and, subsequently, a high glucose yieldEffects of water content on ball milling pretreatment and the
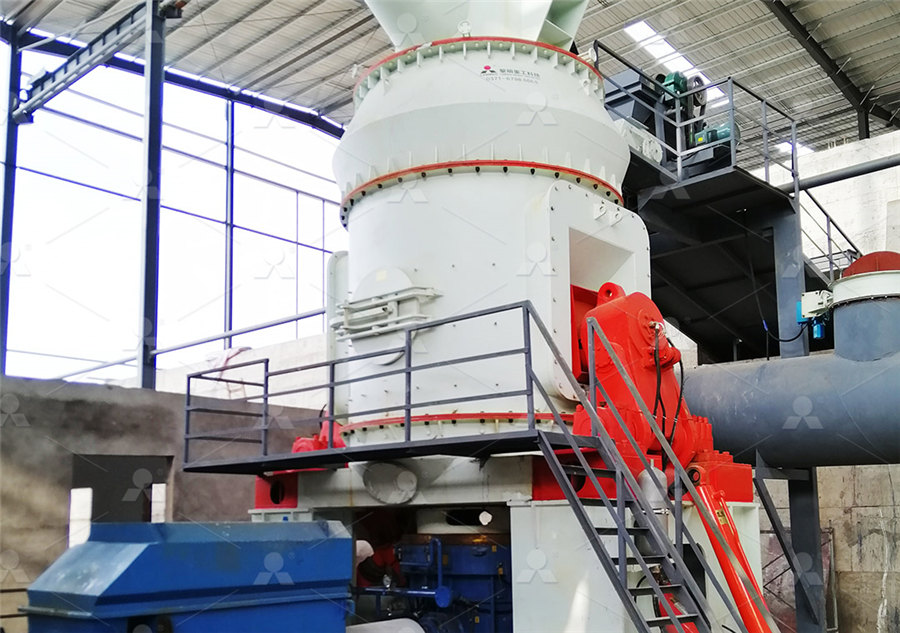
Dry ball milling and wet ball milling for fabricating copper–yttria
2018年7月4日 Yttriareinforced copper matrix composites were prepared by dry ball milling (DBM) and wet ball milling (WBM), respectively, followed by spark plasma sintering (SPS) It is to determine which milling process is better for fabricating Cu–Y2O3 composites It is found that Cu–Y2O3 composites synthesized by DBM exhibit better densification, mechanical and 2020年7月2日 PDF A comprehensive investigation was conducted to delineate the effect of ball size distribution, mill speed, and their interactions on power draw, via a GVL/water antisolvent method(PDF) Effects of Ball Size Distribution and Mill Speed and Their For overflow ball mills, the charge should not exceed 45% of the mill volume For grate discharge mills, the charge should occupy about 50% of the mill volume Bond developed a relationship that can be used to determine the percent AMIT 135: Lesson 7 Ball Mills Circuits – Mining 2015年6月19日 The basic parameters used in ball mill design (power calculations), rod mill or any tumbling mill sizing are; material to be ground, characteristics, Bond Work Index, bulk density, specific density, desired mill Ball Mill Design/Power Calculation 911Metallurgist
[GYQ0R)ZQ]ESS4NJ.jpg)
(PDF) Study on Preparation and Characterization of
2020年12月12日 Study on Preparation and Characterization of Graphene Based on Ball Milling Method December 2020; Journal of Nanomaterials 2020(424):111; DOI:101155/2020/ speed of the ball mill, the 2023年10月27日 The ball mill is a rotating cylindrical vessel with grinding media inside, which is responsible for breaking the ore particles Grinding media play an important role in the comminution of mineral ores in these mills This work reviews the application of balls in mineral processing as a function of the materials used to manufacture them and the mass loss, as A Review of the Grinding Media in Ball Mills for Mineral ball mill, water feed rate to ball mill, water addition rate to sump, sump level and feeding density to hydrocyclone Due to large inertia, strong couplings and uncertainties existing in the grinding process, it is usually difficult to realize optimal control of the whole process by using conventional decentralized PID controllers [2]Intelligent optimal control system for ball mill grinding process2016年4月22日 The apparent difference in capacities between grinding mills (listed as being the same size) is due to the fact that there is no uniform method of designating the size of a mill, for example: a 5′ x 5′ Ball Mill has a working diameter of 5′ inside the liners and has 20 per cent more capacity than all other ball mills designated as 5′ x 5′ where the shell is 5′ inside diameter and Ball Mill Rod Mill Design 911Metallurgist
.jpg)
Effect of ball size and powder loading on the milling SeoulTech
Keywords: Ball size; Particle size; Powder loading; Rotation speed; Wet ball mill 1 Introduction Wet ball mill is one of the most predominantly used method for the purpose of mixing and grinding of raw materials in laboratories and industry [1–3] The ball mill process is very complicated process governed by many parameters, such as ball 2013年11月1日 A highenergy ball milling process along with the hydrothermal method was applied to synthesize Au/GOCeO2 nanocomposites Xray diffraction analysis and FTIR spectroscopy confirmed the (PDF) Optimization of ball milling parameters to produce 2022年1月1日 The ball milling method is classified as vibration mill, planetary mill and magnetoball mill depending on the movement of the balls and vessel and among them, Fe 2+ and Ti 4+ both complex with six water molecules during solvation Ti(H 2 O) 6 4+ is unstableBall milling – A green and sustainable technique for the preparation 2023年10月20日 The basic components and structure of a ball mill play a crucial role in its operation and performance Understanding these elements is essential for effectively operating the equipment 1 Cylindrical Shell The ball mill Comprehensive Guide on Operating a Ball Mill
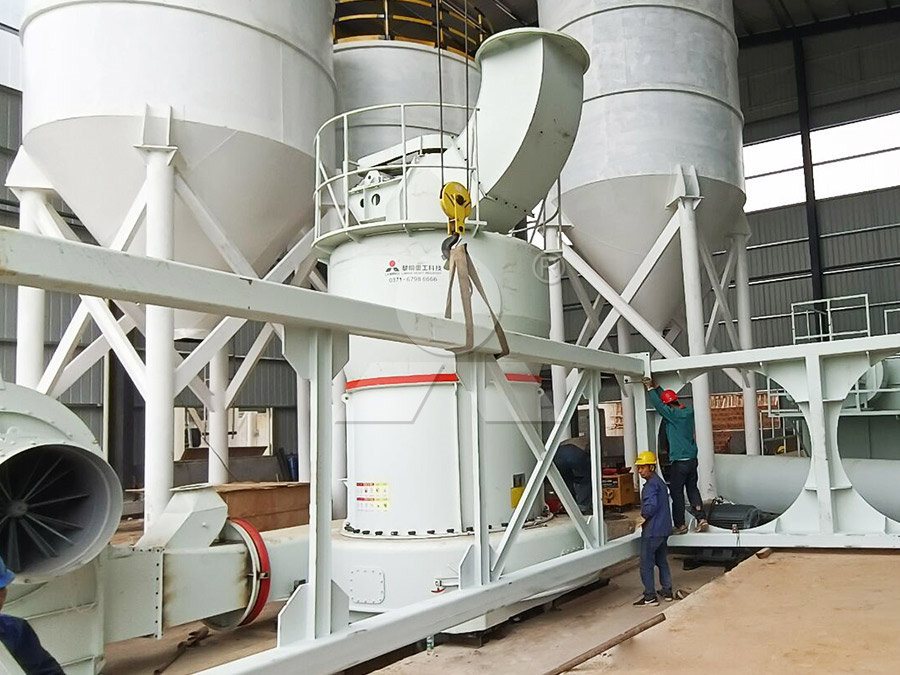
Ball Mill an overview ScienceDirect Topics
The ball mill is a tumbling mill that uses steel balls as the grinding media The length of the cylindrical shell is usually 1–15 times the shell diameter (Figure 811)The feed can be dry, with less than 3% moisture to minimize ball coating, or slurry containing 20–40% water by weightThe Wet Milling Method: A Deep Dive Wet milling, a core aspect of the wet grinding process, involves breaking down materials in a liquid medium The wet ball milling process, a popular choice in many sectors, employs a ball mill to Wet Ball Milling Method and Technology allwin 2022年10月27日 Method name: Ball mill abrasion test — This is an original method developed for industriallyrelevant high stress abr asive wear test Article history: Received 14 July 2022; Accepted 24 October (PDF) Ball mill abrasion test (BMAT): Method development and 2016年2月14日 Do you need a quick estimation of a ball mill's capacity or a simple method to estimate how much can a ball mill of a given size (diameter/lenght) grind for 911 Metallurgist is a trusted resource for practical insights, solutions, and support in mineral processing engineering, helping industry professionals succeed with proven expertise Small Ball Mill Capacity Small Ball Mill Capacity Sizing Table 911Metallurgist
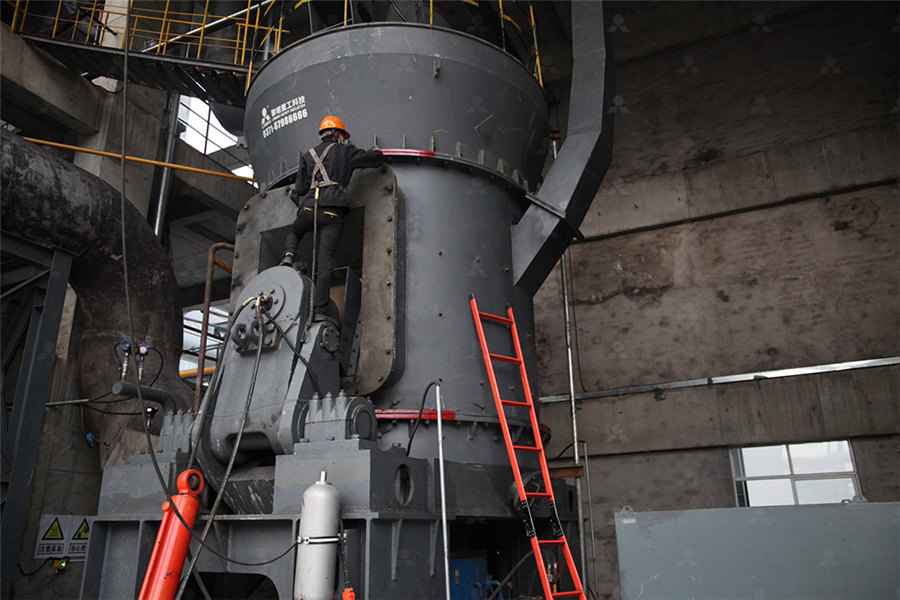
Investigation on the particle size and shape of iron ore pellet feed
Investigation on the particle size and shape of iron ore pellet feed using ball mill and HPGR 909 areas of 500–1600 cm2 g1The concentrate must therefore be reground in order to2023年12月5日 Simple ball millingassisted method enabling Ndoped carbon embedded Si for high Ltd and were of analytical purity Typically, 2 mL deionized water, 02 g Si and 10 g PVP (K29–32) were transformed into a agate ball milling jar (ICPBM04 L vertical planetary ball mill, LICHEN Co, Shanghai, China), and then ball Simple ball millingassisted method enabling Ndoped carbon 4 天之前 The problem of high temperatures in ball mills is a prevalent problem that needs to be addressed to improve their performance and efficiency By implementing the solutions discussed in this article, such as proper lubrication, regular maintenance, and the use of cooling devices, the temperature of a ball mill can be effectively controlledFour Ways To Improve The High Temperature Problem Of Ball Mill2024年7月2日 The application of hydrochar as a costeffective solution has received much attention for the remediation of contaminated water An economical and environmental approach to enhancing the physicochemical and adsorption performance of hydrochar is essential In this study, the green technology of ballmilling was firstly employed to improve the adsorption A green method to improve adsorption capacity of hydrochar by ball
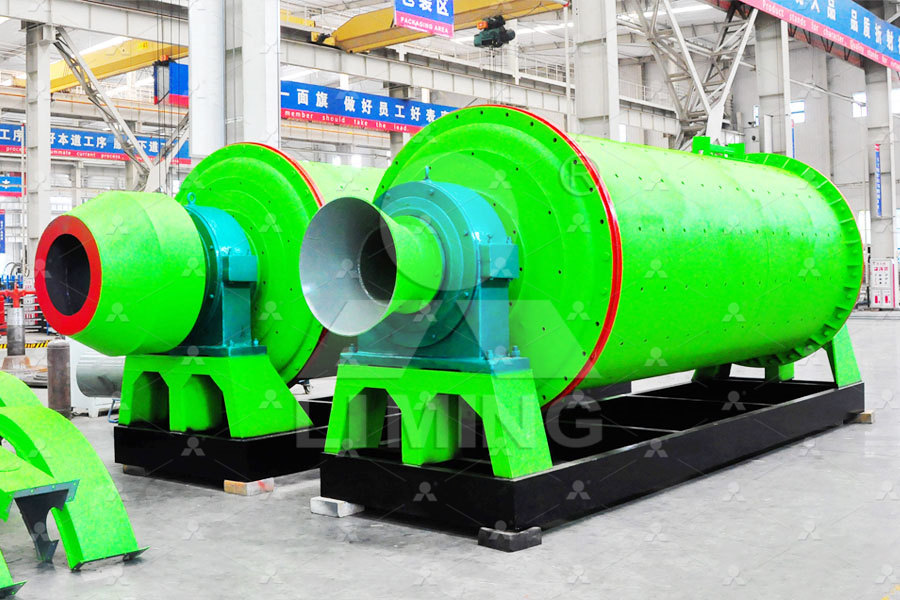
Facile, fast, and green preparation of highpurity and quality silica
silica stones Before installing the inner walls and ball to the mill, the silica stones of the inner walls and the grinding ball were washed by HCL solution and then the deionized water Keywords Silica nanoparticles Ball mill Handmade Green method High purity Sol–gel Introduction