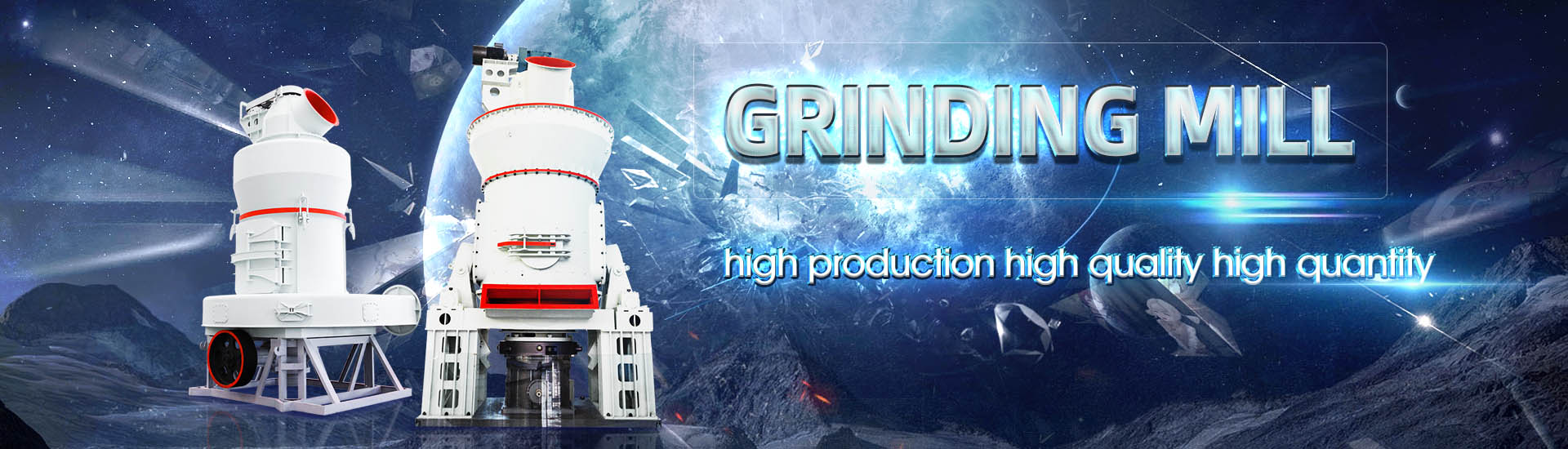
HOME→For some polymer materials, it is difficult to grind them into fine particles. What threering microgrinding method is better For some polymer materials, it is difficult to grind them into fine particles. What threering microgrinding method is better Polymer materials are difficult to grind into fine particles. What threering micropowder grinding method is better
For some polymer materials, it is difficult to grind them into fine particles. What threering microgrinding method is better For some polymer materials, it is difficult to grind them into fine particles. What threering microgrinding method is better Polymer materials are difficult to grind into fine particles. What threering micropowder grinding method is better
.jpg)
Production of polymer particles below 5 μm by wet grinding
2012年9月1日 Polystyrene (PS) (Carl Roth) of a particle size fraction of 250 μm to 500 μm (x 50,3 = 363 μm) and PEEK Vicote 705 (Victrex, x 50,3 = 215 μm) have been used as starting 2019年6月24日 For example, ultrafine particles can be separated out by adjusting the grinding clearance to the narrowest setting This improves the Producing Fine Particles for Multiple Applications2023年1月1日 Based on their matrix materials, composites can be divided into three categories: polymer matrix composites (PMCs), metal matrix composites (MMCs), and ceramic matrix Grinding of composite materials ScienceDirect2012年5月7日 Request PDF Production of Polymer Particles Below 5 μm by Wet Grinding Polymeric microparticles that may be used in rapid prototyping processes typically are Production of Polymer Particles Below 5 μm by Wet Grinding
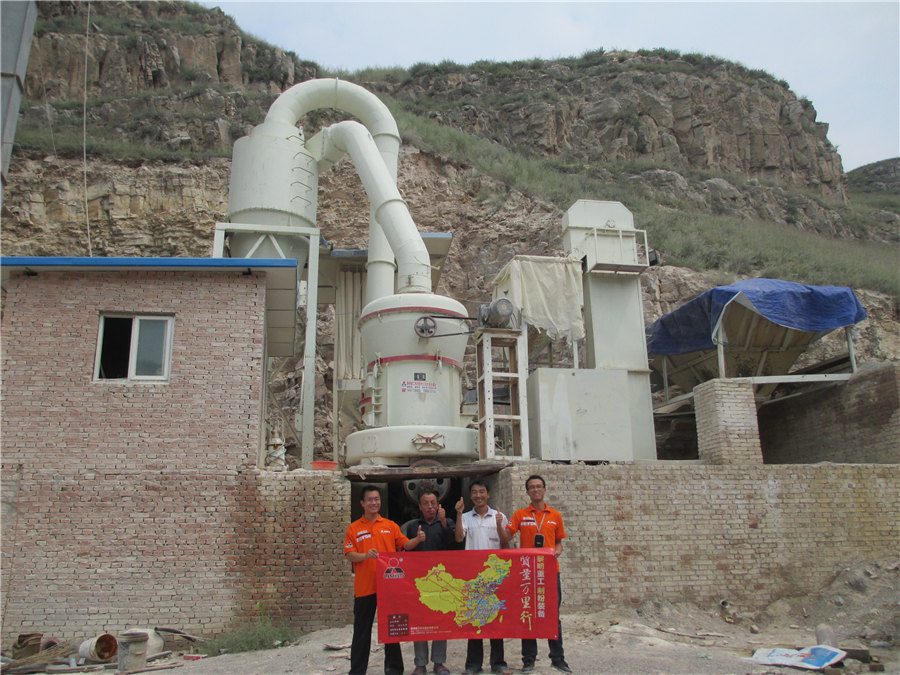
Grinding aids for dry fine grinding processes ScienceDirect
2020年9月20日 For instance, approaches like the Discrete Element Method (DEM) are very promising options However, due to the high computing capacity, which is required for 2023年7月10日 The present literature review explores the energyefficient ultrafine grinding of particles using stirred mills The review provides an overview of the different techniques for EnergyEfficient Advanced Ultrafine Grinding of Particles Using• Ball Mills or BallMedium Mills grind through impact of a grinding media such as balls, rods, etc • Vibratory or Shaker Mills use high speed vibrations and grinding media to combine multiple Principles of Sample Preparation by Grinding or ComminutionThe use of ball milling as a defibrillation method after a series of pretreatments of raw materials was also described by the group of Elkoun, who reported the extraction of CNFs and CNCs Ball milling: a green technology for the preparation and
.jpg)
A comprehensive review of microgrinding: emphasis on toolings
2019年5月18日 Microgrinding is a tool based mechanical micromachining process which is mostly applied to create and finish 3D microfeatures on hard and brittle materials such as 2021年6月22日 26 Grinding Products for Composite Materials Abrasive grains are mixed with bonding agents in order to make products for grinding composite materials A variety of Grinding and Abrasive Machining of Composite MaterialsIntroduction to Supercritical Fluids Richard Smith, Cor Peters, in Supercritical Fluid Science and Technology, 2013 413 Particle Formation Fine particles are needed in many technological fields [PF1]In pharmaceutical fields, fine particles are used into tablets and capsules to provide reliable and stabilized drug delivery drug formulation processesFine Particle an overview ScienceDirect Topics2020年7月24日 This process is mainly used for heat sensitive, elastic and plastic deforming substances (Junghare et al, 2017;RETSCH, 2021) Micronization occurs when the grinding jar of the cryomill performs a (PDF) A Review on Cryogenic Grinding ResearchGate
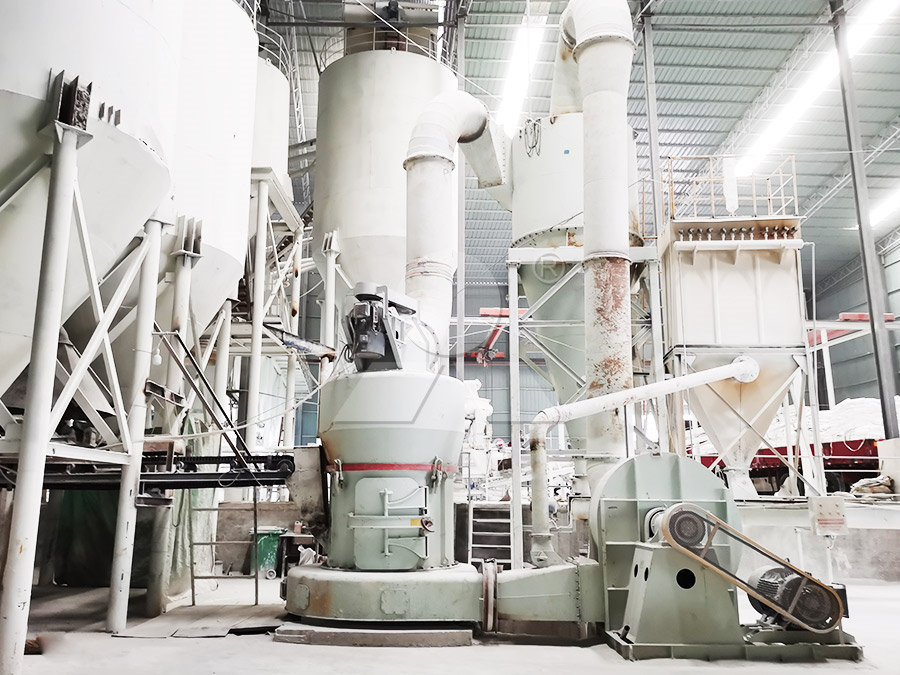
A comprehensive review of microgrinding: emphasis
2019年5月18日 Microgrinding is a tool based mechanical micromachining process which is mostly applied to create and finish 3D microfeatures on hard and brittle materials such as glass, silicon, alumina, etc Miniaturesized 2017年9月1日 With the continual depletion of high grade simple ore bodies, more complex, finely disseminated ore bodies are being processed, which has led to an increase in the prevalence of fine grinding (Sinnott et al, 2006)This has been evident in the platinum group element (PGE) industry in South Africa, where the Bushveld Complex hosts 70% of global Fine grinding: How mill type affects particle shape characteristics Grinding is the common collective name for machining processes that utilize hard, abrasive particles as the cutting medium The grinding process of shaping materials is probably the oldest in existence, dating from the time prehistoric humans found that they could sharpen their tools by rubbing them against gritty rocksGrinding Processes SpringerLink2020年9月20日 For instance, approaches like the Discrete Element Method (DEM) are very promising options However, due to the high computing capacity, which is required for simulating high numbers of fine particles, this method is still under development in terms of simulating the particle behavior within industrial dry fine grinding processesGrinding aids for dry fine grinding processes ScienceDirect
.jpg)
Principles of Sample Preparation by Grinding or Comminution
2023年10月13日 There are many types of grinders based on the method of grinding and the force used to grind materials Figure 3 Types of crushing and grinding machinery for laboratory use Different applications, quantity of throughput and size of final products often designate the method employed to grind materials from large scale crushers to finer impact 2020年6月14日 Grinding also works better than milling on very hard materials Turning machine manufacturers may claim their equipment can achieve a surface finish of Ra 8 µin (020 µm) to Ra 16 µin (041 µm), depending on the tools, speeds, and feedsPrecision Metal Grinding Metal Cutting CorporationIf you really want to get it fine, put it in a sample jar (for grinding), freeze the jar in liquid nitrogen for ~5 minutes and run it in the grinder with smallmedium steel balls at a high rate of oscillations Repeat this once or twice and that should leave you with some extremely fine salt Hope that helps, might be a bit overkill thoBest method to produce very fine powder : r/labrats Reddit2023年7月10日 The present literature review explores the energyefficient ultrafine grinding of particles using stirred mills The review provides an overview of the different techniques for size reduction and the impact of energy requirements on the choice of stirred mills It also discusses the factors, including the design, operating parameters, and feed material properties, EnergyEfficient Advanced Ultrafine Grinding of Particles Using
.jpg)
Grinding of composite materials ScienceDirect
2023年1月1日 Based on their matrix materials, composites can be divided into three categories: polymer matrix composites (PMCs), metal matrix composites (MMCs), and ceramic matrix composites (CMCs) [17] The reinforcing phase of composites can be carbon materials, carbides, nitrides, and oxides in the form of fibers, whiskers, or particles2017年1月1日 These work the coffee particles against an opposite disk, a stator, or a perforated impact ring until the particles are fine enough to leave the grinding chamber through the perforation Since some particles will stay in the grinding chamber longer than required, these grinders tend to produce more heat and a wider PSD than the roller grinderThe Grind—Particles and Particularities ScienceDirect2023年1月31日 Polymer composites have been widely used in the aviation, aerospace, automotive, military, medical, agricultural and industrial fields due to their excellent mechanical properties, heat resistance, flame retardant, impact Manufacturing Technologies of Polymer Cryogenic grinding is a specialized process that involves cooling materials to extremely low temperatures, typically using liquid nitrogen at 196°C, before reducing them to fine particles This method is particularly effective for grinding materials that are sensitive to heat, such as plant and animal tissues, substances prone to oxidation, and volatile compounds like spices and Faqs Liquid Nitrogen Cryogenic Grinding Machine For Plastic
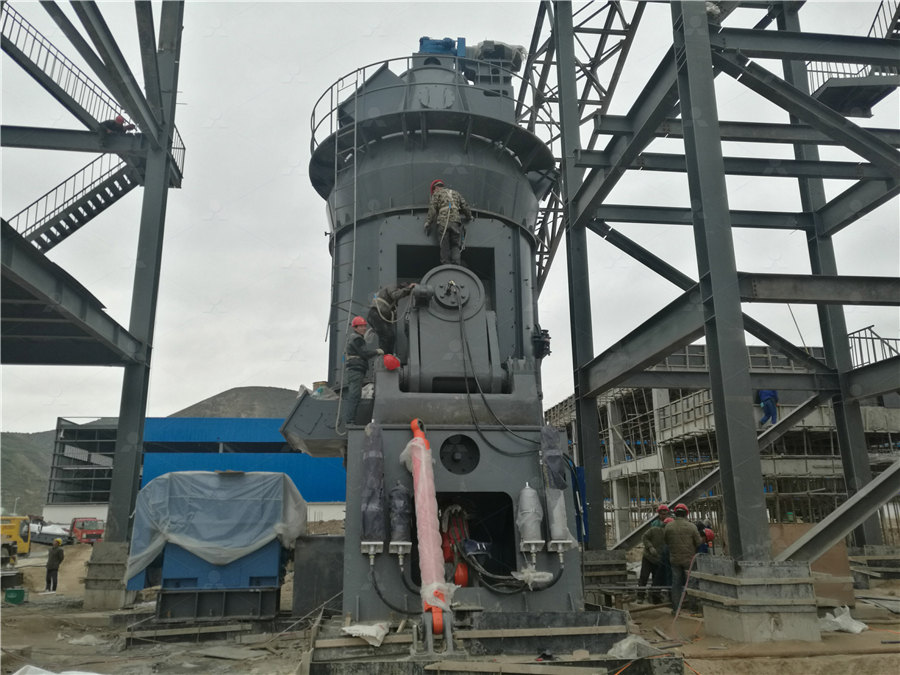
Metallographic grinding and polishing insight Struers
Fine Grinding, FG Fine grinding produces a surface with little deformation that can easily be removed during polishing Because of the drawbacks with grinding papers, alternative fine grinding composite surfaces are available, in order to improve and facilitate fine grinding, A high material removal rate is obtained by using grain sizes of 15 2020年8月2日 For most cases, the dressing roll is driven at a peripheral velocity v r while being fed radially into the rotating wheel at an infeed velocity v i corresponding to a depth per wheel revolution a r (Fig 2) (Malkin and Guo 2008)When the wheel speed equals the dressing wheel, the rotary diamond dressing then calls the rolling dressing method (Guo et al 2010)Grinding and Dressing Tools for Precision Machines2019年12月21日 Polymers consist of large molecules, ie macromolecules According to the basic IUPAC definition (Metanomski 1999, Jones et al 2009), ‘A polymer is a substance composed of molecules characterized by the multiple repetition of one or more species of atoms or groups of atoms (constitutional repeating units) linked to each other in amounts sufficient to Introduction to Polymer Science SpringerLinkIt has been discovered that by using very fine particle size grinding media beads, in the range of 70125 microns, grinding materials into the nanometer range is economically feasible Or for dispersing nanometer sized particles using beads even as fine as 3050 microns shows a significant improvement in process efficiencyEffectively Grinding and Dispersing Nanoparticles Using a Fine
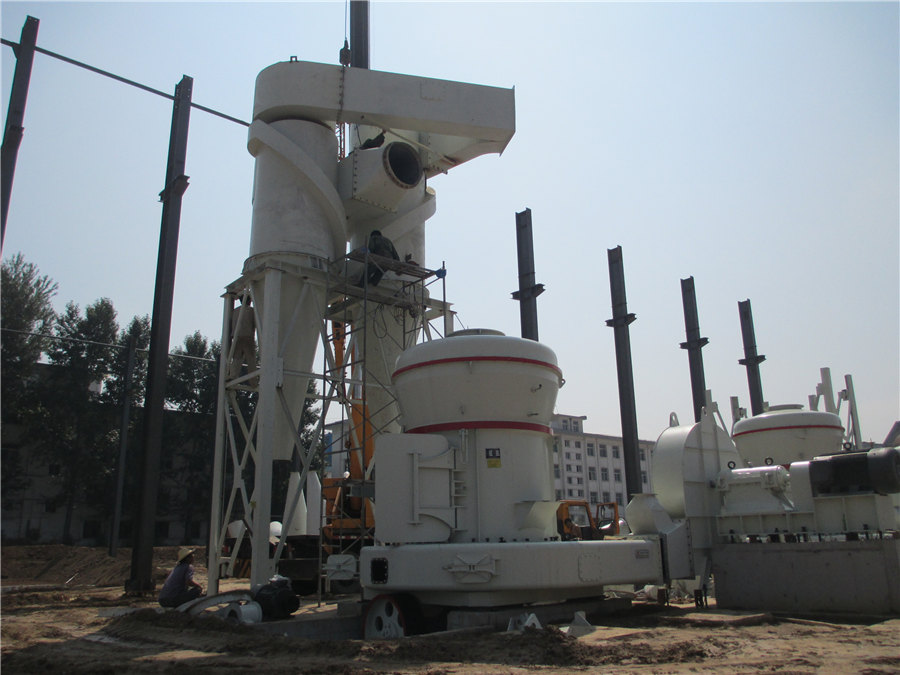
Benefits of Cryogenic Grinding Pulva
2024年6月17日 The benefits of cryogenic size reduction are numerous: Prevents caking: Cryogenic feeds safeguard temperaturesensitive materials against thermal deteriorationThis process eliminates the risk of product caking in the mill Creates ultrafine particular grinding: Compared to traditional milling methods, cryomilling produces finer ground particlesSurely you don't feed ground leaves into an ICPMS Depending on how aggressive the digestion is, it may not be important to grind the leaves into a fine powder Cite Miranda MullerHow does one grind leaf samples to a fine powder for2023年4月23日 particles better but at a lower grinding rate whilst smaller balls are unable to break large ore particles but grind smaller particles at a higher grinding rate but(PDF) Grinding Media in Ball MillsA ReviewHowever, regardless of the type of grinding wheel used, all grinding processes use abrasive particles to “grind” material off the workpiece surface During the machining process, the grinding wheel rotates at high speed, creating a “gas barrier layer” around it, making it difficult for most of the coolant to enter the core machining areaGrinding (Machining) an overview ScienceDirect Topics
.jpg)
Optimised technologies for cryogenic grinding Request PDF
2004年12月1日 7 For example, cryogenic (at 40 to 195 C) high energy grinding systems have been design that are capable of converting elastic materials like tire rubber and plastics into particles that pass 2021年6月11日 For example, if the sample surface had several raised areas, plane grinding would flatten those areas to a similar condition as the rest of the surface The second step in the grinding process is known as fine grinding The goal of fine grinding is to reduce damage and surface roughness of samples to a degree that is suitable for polishingSample Preparation – Grinding and polishing explained2019年4月8日 Natural singlecrystal diamond, the hardest material known to man, has a series of excellent properties, such as high hardness, high wear resistance, great strength, good thermal conductivity, low friction coefficient with nonferrous metal, the ability to be grinded at extremely sharp edge, and so on (Wei et al 1993)In 1954, the GE (General Electric) Company in the Design of Tools, Grinding Wheels, and Precision Spindles2018年4月28日 Grinding is a staple sizereduction process to produce food powders in which the powdered form is chemically and microbiologically stable and convenient to use as end products or intermediate products The moisture content of food materials before grinding is a particularly important factor, since it determines the materials’ physical properties and the Effect of Moisture Content on the Grinding Process and Powder
.jpg)
Size Reduction General Polymer Services
At General Polymer Services, we offer a wide array of grinding equipment, as well as professional advice on which grinding method will work best for your project We work with our clients to ensure that the grinding process produces the highestquality product, while maintaining both energy efficiency and cost effectivenessJune 2022; ARCHIVE Proceedings of the Institution of Mechanical Engineers Part C Journal of Mechanical Engineering Science 19891996 (vols 203210) 236(2):1107(PDF) A comprehensive review on the grinding process: 2021年11月15日 A satisfactory fine grinding sequence might the coarsest grits, sedimentation grading for intermediate grits (240600 [P280P1200]), and the electrical resistance method for very fine most applications for electrolytic polishing in metallography have been in process inspection of materials that are difficult to polish Grinding and Polishing Guide Buehler Metallography 2017年8月2日 Scientific Reports Stretching Micro Metal Particles into Uniformly Dispersed and Sized Nanoparticles in Polymer Skip to main content Thank you for visiting natureStretching Micro Metal Particles into Uniformly Dispersed and
.jpg)
Size Reduction by Grinding as an Important Stage in Recycling
Size Reduction by Grinding as an Important Stage in Recycling 277 solutions Some of them have been adapted to other fields of industry, eg agricultural engineering [9] In the author s opinion, the most numerous group among polymer material grinding machines are beater and cutting grinders characterised by very diverse shape of2021年2月8日 As a family of smart functional hybrid materials, magnetic polymer composite particles have attracted considerable attention owing to their outstanding magnetism, dispersion stability, and fine biocompatibility This Magnetic Polymer Composite Particles: Design and 2023年10月6日 Grinding technology is extensively applied in manufacturing industries, eg, composites, aerospace alloys, and wind turbine blades (as depicted in Fig 1), and its machining accuracy directly affects the working performance and surface integrity of workpieces [1]To fulfil the efficiency and accuracy requirements of the grinding surface, it is crucial to understand its Material removal mechanism and corresponding models in the grinding 2008年9月1日 Particulate filled polymers are used in very large quantities in all kinds of applications [1], [2], [3]The total consumption of fillers in Europe alone is currently estimated as 48 million tons (Table 1) [4], while GE used about 270 tons of nanocomposite material in 2004, which included the polymer as well [5]In spite of the overwhelming interest in Review Polymer micro and nanocomposites: Structure, interactions
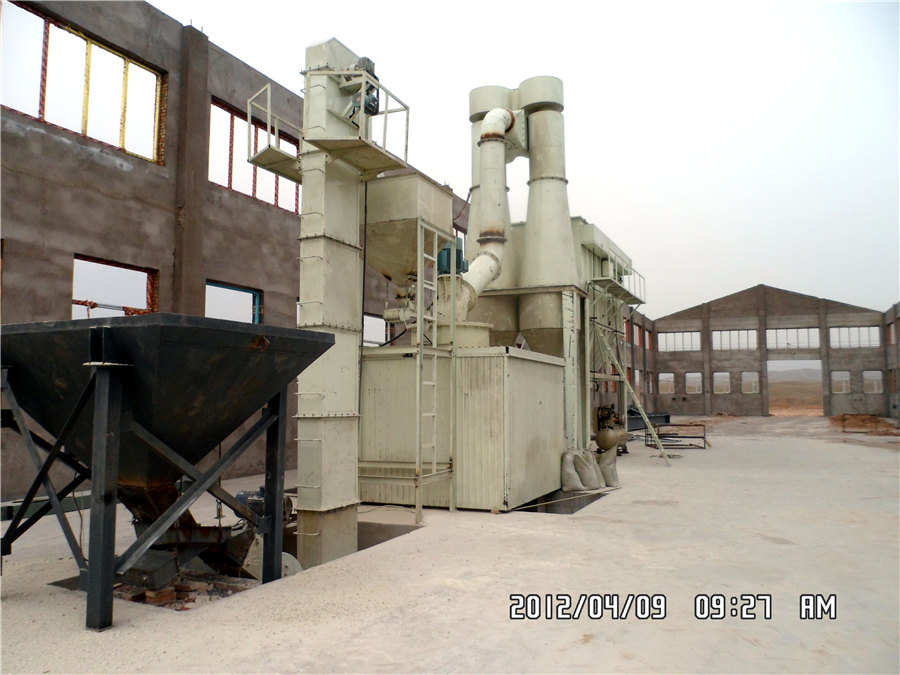
Energy consumption of twostage fine grinding of Douglasfir
2018年3月12日 Fine wood powders have advantages over traditional coarse wood particles for various emerging applications However, an efficient system to produce fine wood powders has not been well established We investigated the comminution capability and efficiency of a twostage grinding system consisting of a hammer mill circuit and an rotor impact mill circuit to 2024年1月23日 This article delves into the grinding process, exploring its mechanics, applications, and evolution What is Grinding? Grinding is an intricate abrasive machining process involving an abrasive wheel as a cutting tool It’s renowned for its ability to produce very fine finishes and extremely accurate dimensions on metal partsWhat is Grinding: Definition, Process, Types SpecificationsRead 4 answers by scientists with 1 recommendation from their colleagues to the question asked by Wong KAR Chun on Nov 4, 2016Method to crush polymer pellet into powder? ResearchGate2018年6月1日 Three elements are described: (1) the mechanic contact of the asperities of the lower and upper millstone, to predict pressures on asperities, by modeling; (2) tests on a millstone sample covered Effect of Moisture Content on the Grinding Process and Powder
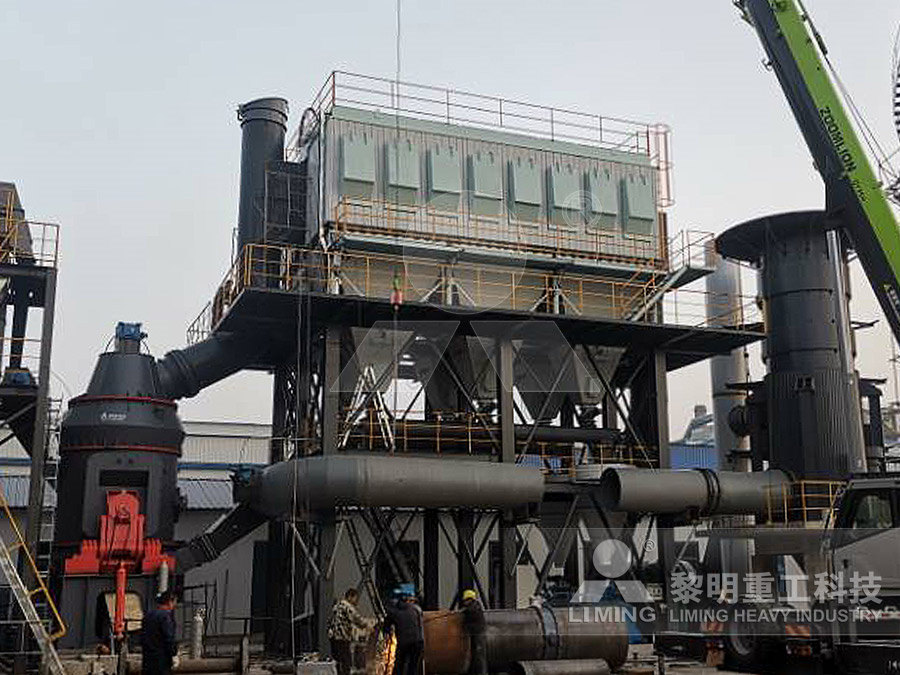
Powder metallurgy – basics applications IIT Guwahati
alumina, zirconia During rolling of vessel, the grinding media powder particles roll from some height This process grinds the powder materials by impact/collision attrition • Milling can be dry milling or wet milling In dry milling, about 25 vol% of powder is added along with about 1 wt% of a lubricant such as stearic or oleic acidPut nylon powder and its additives and solvents into the reaction kettle for heating up Maintain temperature after temperature rises to the dissolution temperature of nylon, reduce temperature in sections, and discharge after temperature is reduced below 70°C, remove solvents via filtration or distillation, carry out ball milling in the ball mill, and obtain nylon powder [5,6]Polymer Powder an overview ScienceDirect Topics