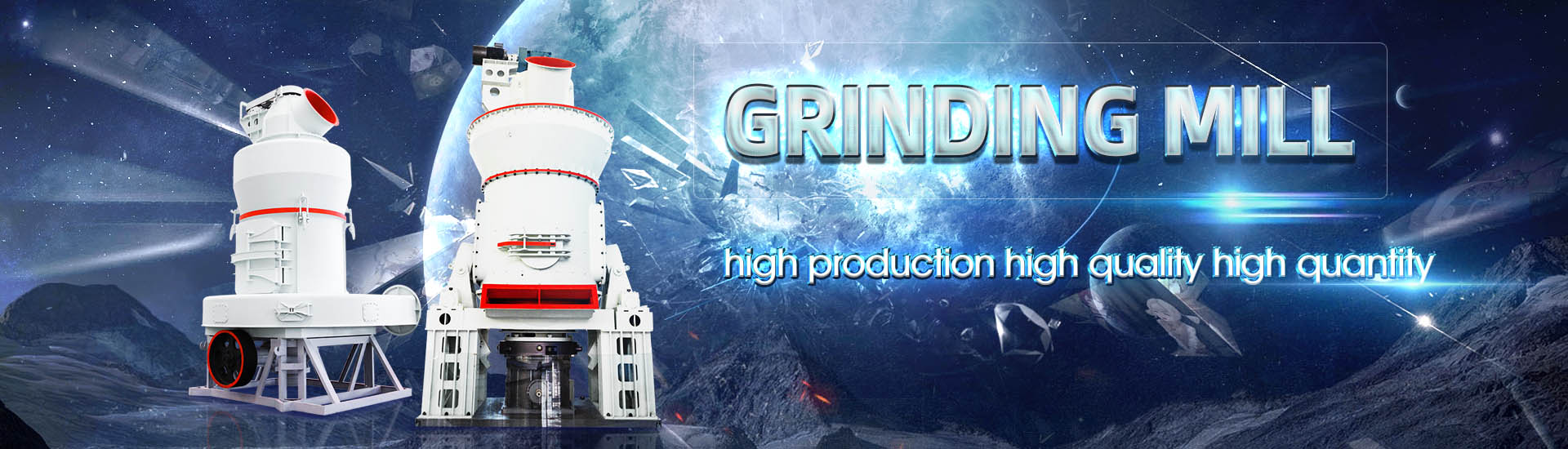
How to increase the processing capacity of bluestone grinding mill
46.jpg)
Implementing strategies to improve mill capacity and efficiency,
Recent advances in fine screening technology allow for the efficient classification of mill products by means of particle size separation only The advantages are numerous, including improved The results showed that the grinding capacity can be increased up to 180% by optimizing the circulating load and it will positively affect the flotation performance It was observed that a Effective circulating load ratio in mill circuit for milling capacity 2020年5月1日 Improving the processing capacity of a mill is primarily dependent on increasing the effective inner diameter and effective length of the mill, and increasing the power of the Enhancing the capacity of largescale ball mill through process Model predictive control provides an additional tool to improve the control of SemiAutogenous Grinding mills and is often able to reduce process variability beyond the best performance that SAG Mill Optimization using Model Predictive Control Andritz
.jpg)
PreProcessing to Increase the Capacity of SAG Mill Circuits MDPI
2022年6月6日 This paper describes the adopted approach for increasing the capacity of an existing industrial grinding circuit by adapting the respective configuration to process the ore 2022年6月6日 This paper describes the adopted approach for increasing the capacity of an existing industrial grinding circuit by adapting the respective configuration to process the ore (PDF) PreProcessing to Increase the Capacity of SAG Mill Circuits The GrindingExpert solution will automatically adjust feed rate, mill speed and water addition to reduce upsets, eliminate grindouts and increase tonnage in SAG / ball mills Secondary Grinding circuit optimisation to increase throughput andGrinding in ball mills is an important technological process applied to reduce the size of particles which may have different nature and a wide diversity of physical, mechanical and chemical Grinding in Ball Mills: Modeling and Process Control Sciendo
.jpg)
Closed circuit ball mill – Basics revisited ScienceDirect
2013年4月1日 Based on the analysis presented here it is estimated that the practical potential for increasing grinding circuit capacity in mineral processing plants by using more efficient June 2022; ARCHIVE Proceedings of the Institution of Mechanical Engineers Part C Journal of Mechanical Engineering Science 19891996 (vols 203210) 236(2):1107(PDF) A comprehensive review on the grinding process: 2019年4月25日 Much work has been devoted to the technical aspects of grinding, the “how” of grinding But, in the writers’ opinion, the economically important subject of optimizing grinding capacity in mill design has not received the attention it deserves, at least not in published literature Optimizing Primary Grinding CapacityOptimizing Grinding and Regrinding Capacity in Mill Design2022年6月6日 This paper describes the adopted approach for increasing the capacity of an existing industrial grinding circuit by adapting the respective configuration to process the ore from a new mine(PDF) PreProcessing to Increase the Capacity of SAG Mill
.jpg)
Solids Choose the Right Grinding Mill Chemical Processing
Thus, increasing the media size increases the grinding time and vice versa Specialized Mill Figure 3 Material of construction is another crucial area to consider during mill and media selection When processing chemicals it's often necessary for mill contact parts to be as inert and contaminationfree as possible2019年4月22日 2 More crushing and less grinding to reduce the feed size into mill The larger feed size, the more work that the ball mill needs to do on the oreTen Ways to Improve the Grinding Efficiency of Your Ball Mill2016年11月22日 The grinding temperature will remain low until the wheel reaches its life as shown in cut 6, where the proportion of high temperature increases Such a grinding performance in a wheel dressing cycle is the same as what has been discussed on the effects of dressing on grinding powerEffect of different parameters on grinding efficiency and its 2015年10月9日 Calculating a grinding circuit’s circulating loads based on Screen Analysis of its slurries Compared to %Solids or Density based Circulating load equations, a more precise method of determining grinding circuit tonnages uses the screen size distributions of the pulps instead of the dilution ratiosPulp samples collected around the ball mill or rod mill and Ball Mill Circulating Load Formula 911Metallurgist
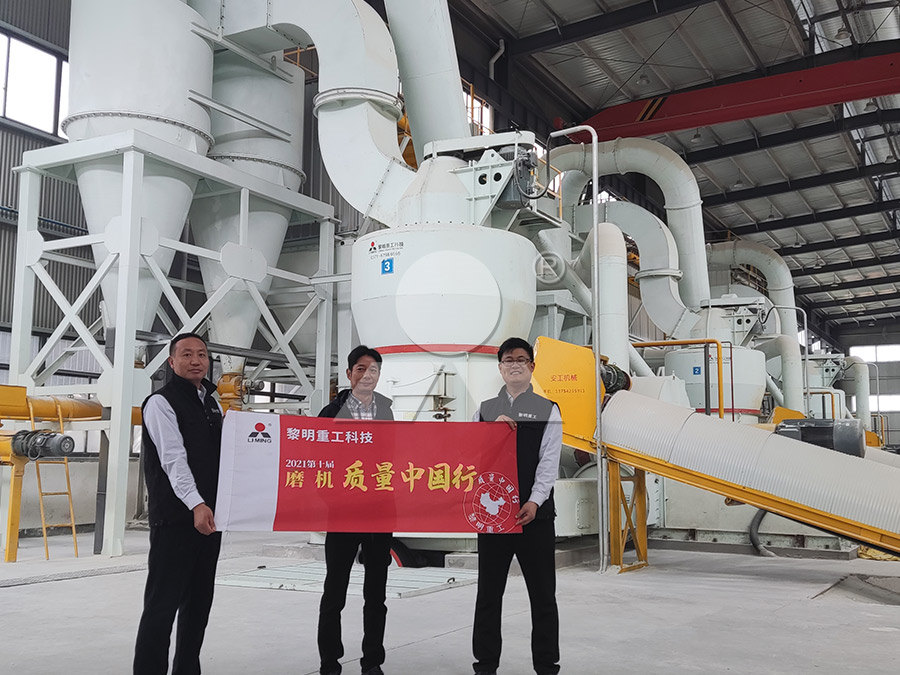
Increase productivity of vertical roller mill using seven QC tools
2021年1月29日 Vertical roller mills, VRMs, are widely used for grinding raw materials in factories engaged in the extraction and processing of minerals Any machine used for grinding or crushing consumes around efficiency, low circulating load and increase in mill capacity as well as decreased numbers of mills (Barrios, 2007; Barkhuysen, 2009; Albuquerque et al, 2013; Frausto et al, 2017; Dündar, 2020) In addition to the idea of using high capacity screens in Effective circulating load ratio in mill circuit for milling capacity 2019年1月1日 This paper analyzes the effects of coal grindability and its characteristics on the grinding capacity and power consumption for beater wheel mill during exploitation in thermal power plant TENT B Practical assessment of grinding capacity and power 2017年7月26日 As a consequence of this, the actual, gain is likely to be closer to 25% and the mill production increased to 65,000 x 125 = 81,250 tons per day Obviously, this will increase the capacity of the crushing plant and coarsen its reduction, again influencing mill outputHow Ball Mill Ore Feed Size Affects Tonnage Capacity

A Review of the Grinding Media in Ball Mills for Mineral Processing
2023年10月27日 The ball mill is a rotating cylindrical vessel with grinding media inside, which is responsible for breaking the ore particles Grinding media play an important role in the comminution of mineral ores in these mills This work reviews the application of balls in mineral processing as a function of the materials used to manufacture them and the mass loss, as minerals Article PreProcessing to Increase the Capacity of SAG Mill Circuits—Case Study Homero Delboni, Jr 1 , Evandro Costa e Silva 2, * , Vladmir Kronemberger Alves 3 and Ana Carolina Chieregati 1 1 2 3 * Citation: Delboni, (PDF) PreProcessing to Increase the Capacity of SAG 2014年4月9日 Despite the increased capacity Skip to Main Content Browse; Close search Miscanthus particlesize distributions after hammer mill grinding operations with no screen in hammer mill and with screens of 6, Testing with the tub grinder focused on processing biomass through a series of screens with different sized Full article: Optimizing hammer mill performance through 2017年8月30日 This article presents observations on grindingstone implements and their uses in ElgeyoMarakwet County, northwest Kenya Tool use in Marakwet is contextualized with a select overview of literature on grindingstones in Africa Grindingstones in Marakwet are incorporated not only into quotidian but also into more performative and ritual aspects of life Back to the Grindstone? The Archaeological Potential of Grinding
.jpg)
How to Improve Your Grinding Efficiency and Profitability
The cooling system in your grinding machine is also important because it controls the temperature, provides lubrication and removes small chips while the machine is grinding The pressure range, filtration system, flow rate, flow location, coolant type and pump capacity of your cooling system are all essential components of an optimized process2016年7月8日 The Work Index values listed in Table I and II apply directly to a wet grinding overflow type rod mill 75 feet in diameter in open circuit; and to a wet grinding overflow type ball mill 75 feet in diameter in closed circuit with a rake classifier at 250% circulating load, and with 80% or more of the feed passing 4 meshEquipment Sizing: Crusher or Grinding Mill 911Metallurgist2023年4月23日 In order to increase the efficiency of the grinding mill, Stoimenov et al [38] suggested the increment of grinding media density Kelsall et al [17] investigated the influ ence of grinding media (PDF) Grinding Media in Ball MillsA Review ResearchGate2016年1月1日 The wear of balls used during a grinding process is considered one of the losses that cause an increase in the operating cost allocated to the ball mill [21] Ball wear occurs due to abrasion A comparison of wear rates of ball mill grinding media
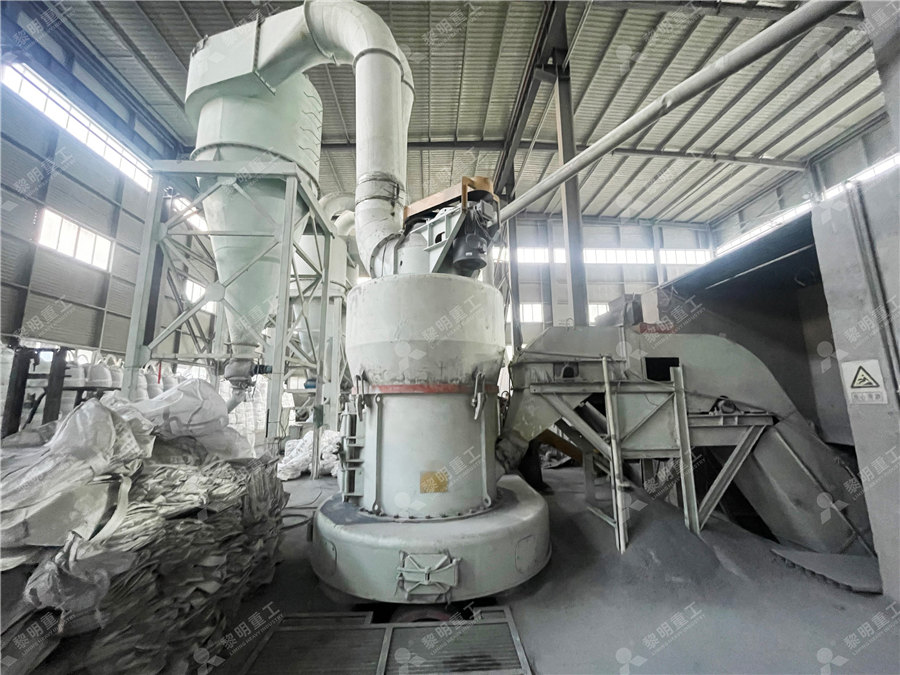
Ways to increase efficiency in feed mills
2022年7月3日 The pellet mill capacity will drop to a level that can overcome the variations without blocking That could be as much as a 50% reduction compared to the design capacity – for example, 67tph of broiler feed on a Ø700mm pellet mill, which should easily do 20tph Another system to investigate would be steam2013年1月1日 Principles of Modern Grinding Technology explains the principles that led to rapid improvements in modern grinding technology over recent decadesPrinciples of Modern Grinding Technology2023年2月22日 ball mill There are several ways to increase the capacity of a ball mill: 1Add more grinding media: Increasing the amount of grinding media, such as steel balls or ceramic beads, can increase the How to increase the capacity of ball mill LinkedIn2017年1月1日 An increase of over 10% in mill throughput was achieved by removing the ball scats from a single stage SAG mill These scats are non spherical ball fragments resulting from uneven wear of balls Performance optimization of an industrial ball mill

5 Ways to Improve the Ball Mill Efficiency FTM
2020年1月11日 Working site of ball mill grinding media refilling In addition to the grinding media proportion and frequency, other factors such as the grinding media material, the shape and so on can improve the ball mill efficiency Consult a professional engineer for details The optimized grinding media can improve the ball mill efficiency by about 30%2014年10月20日 The ball mill is the most common ore grinding technology today, and probably more than 50% of the total world energy consumption for ore grinding is consumed in ball millsEffect of circulating load and classification efficiency on HPGR 2012年6月1日 As the cylinder starts to rotate, the grinding balls inside the cylinder crush and grind the feed material, generating mechanical energy that aids in breaking bonds, activating the catalyst, and Grinding in Ball Mills: Modeling and Process Controlcreates the potential for increased capacity in closed circuit grinding In 1925 EW Davis conducted tests which made comparison between rake classifiers, spiral classifiers and vibratory screens in the closing of grinding circuits He concluded that vibratory screens provided both higher capacity and better control over grind sizeINCREASING THE CAPACITY OF THE GRINDING CIRCUITS
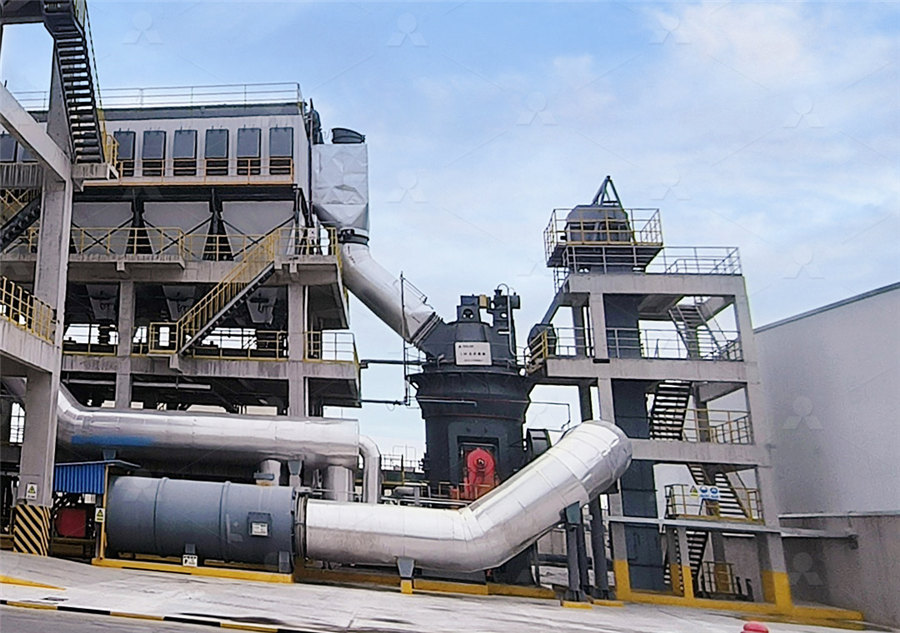
Ball Rod Mill Density – How Water Impacts Grinding
2015年8月6日 Rod mill grinding efficiencies have been shown to increase in the range of 5 to 15% with more dilute discharge slurry (ie, increased feed water) at least down to the range of 45 to 50% solids by volume2015年6月19日 The basic parameters used in ball mill design (power calculations), rod mill or any tumbling mill sizing are; material to be ground, characteristics, Bond Work Index, bulk density, specific density, desired mill tonnage capacity DTPH, operating % solids or pulp density, feed size as F80 and maximum ‘chunk size’, product size as P80 and maximum and finally the type of Ball Mill Design/Power Calculation 911MetallurgistThe Millstone is a more basic equivalent of the Crushing Wheels, and is most likely the first of the two that the Player will construct It is capable of applying milling recipes to any valid items inserted from above There are 2 variables that effect the processing speed of the Millstone: RPM and recipe duration The recipe duration is a number assigned to each recipe to determine is Millstone Create Wiki Fandomclosing of grinding circuits As mill sizes increased, rake and spiral classifiers became less economically viable due to their large footprint requirements and capital costs The hydrocyclone on the other hand required very little space, provided high capacity with relatively low capital costs For these reasons and the increased demand for Implementing strategies to improve mill capacity and efficiency,
.jpg)
SAG Mill Liner Design 911Metallurgist
2016年6月6日 Based on experience, millliner designs have moved toward more openshell lifter spacing, increased pulp lifter volumetric capacity, and a grate design to facilitate maximizing both pebblecrushing circuit utilization and SAG 2020年5月1日 The main aim of this study is to improve the processing capacity of the largescale ball mill Taking a Φ549 × 883 m ball mill as the research object, the reason for the low processing capacity of the ball mill was explored via process mineralogy, physicochemical analysis, workshop process investigation, and the power consumption methodEnhancing the capacity of largescale ball mill through process 2024年8月8日 This change resulted in a noticeable increase in recovery rates, demonstrating how the right grinding media can directly impact operational success and profitability in mineral processing operations Conclusion The strategic selection of grinding media is crucial for maximizing the efficiency and effectiveness of ball milling operationsBall Mill Success: A StepbyStep Guide to Choosing the Right Grinding Increasing Output Of Cement Grinding In Ball MillCase Study 5 INCREASING OUTPUT OF CEMENT GRINDING IN BALL MILLCASE STUDY 1MOHAN SINGH PANWAR, 2AJAY KUMAR BANSAL, 3HEMANI PALIWAL 1Student, 2Guide, 3External Guide Email: l, 2ajaykumarbansal@poornima, 3hemani8588@gmailINCREASING OUTPUT OF CEMENT GRINDING IN BALL MILL
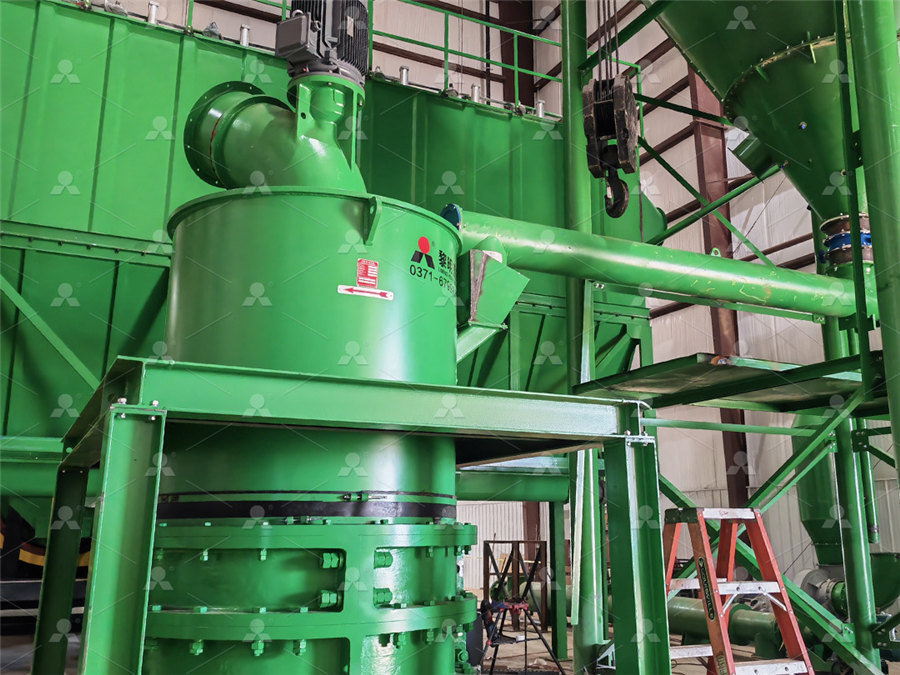
Top 10 tips to improve the grinding efficiency of ball mill
2020年3月21日 Ball mill's low grinding efficiency, low processing capacity, high production energy consumption, unstable product fineness, etc are problems that many customers will encounter How to effectively improve the grinding efficiency of the ball mill is an important issue Now, let's share 10 ways to improve the grinding efficiency of the ball mill!The critical speed of the mill plays a crucial role in determining the optimum operating conditions for efficient grinding Factors such as ball size, rotation speed, and loading capacity also influence the overall grinding performance Types of Ball Mill There are several types of ball mill grinding machines, each designed for specific Ball Mill Grinding Machines: Working Principle, Types, Parts 2017年10月25日 The energy specific grinding rate of the coarse material in the ball mill can then be defined as follows: The mill specific grinding rate reflects both the efficiency of the mill environment in breaking the coarse particles, as well as the grindability characteristic of the ore over the particular size reduction rangeHow to Improve Ball Mill Performance 911Metallurgist2022年1月1日 The size of grinding media is the primary factor that affects the overall milling efficiency of a ball mill (eg power consumption and particle size breakage)Effect of grinding media on the milling efficiency of a ball mill
.jpg)
Grinding Mill an overview ScienceDirect Topics
Grinding Mills Barry A Wills, James A Finch FRSC, FCIM, PEng, in Wills' Mineral Processing Technology (Eighth Edition), 2016 71 Introduction Grinding is the last stage in the comminution process where particles are reduced in size by a combination of impact and abrasion, either dry, or more commonly, in suspension in water