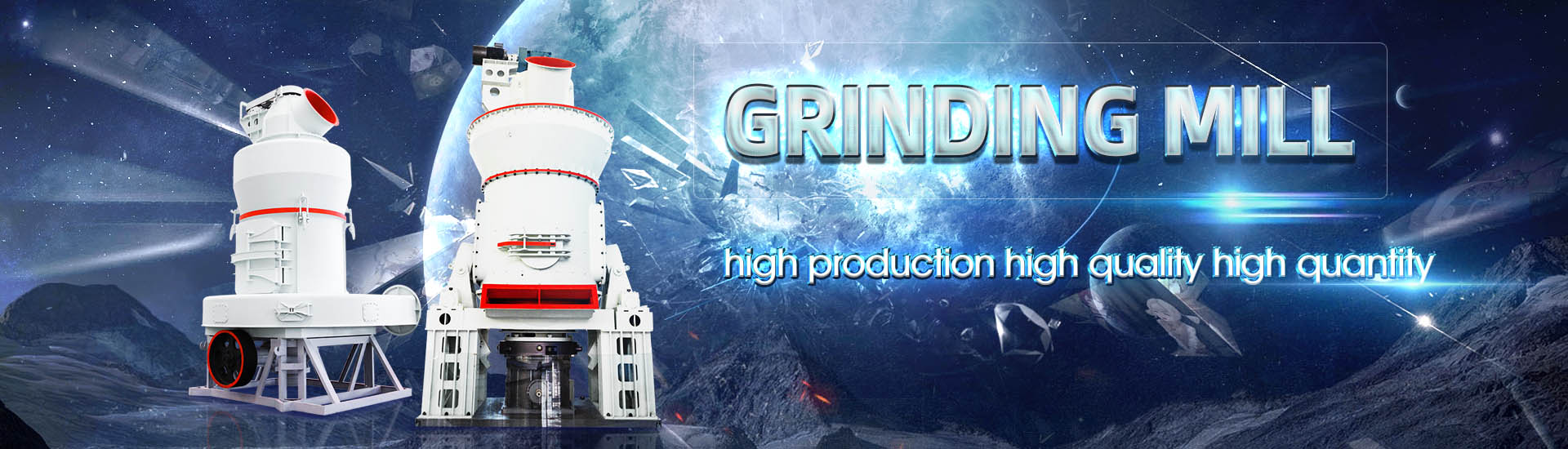
2501000 revolutions of ore grinding mill
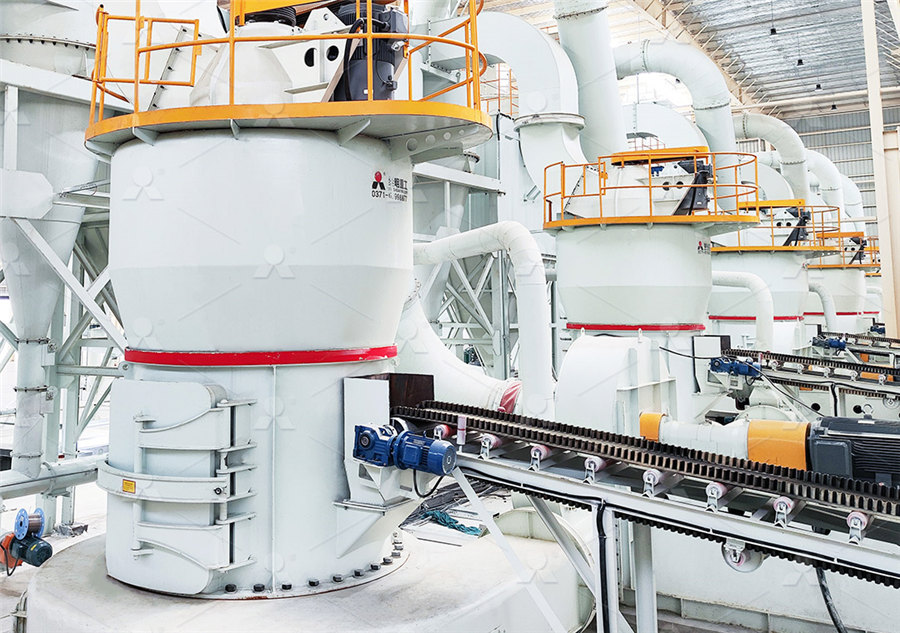
Grinding Mill Operation and Scaleup: Theory and Equations
The ratio: rotational mass flow of media to axial mass flow of ore—a concept recently introduced—has been refined and extended It can account for similar breakage in scaled mills 2023年10月27日 Grinding media play an important role in the comminution of mineral ores in these mills This work reviews the application of balls in mineral processing as a function of the A Review of the Grinding Media in Ball Mills for Mineral Processing 2019年1月30日 In the discrete element simulation of tumbling mills, the energy expended in the collisions between ball to ball and ball to mill shell is summed over one or two full revolutions The Evolution of Grinding Mill Power Models Mining, Metallurgy 2020年6月1日 Stirred media mills are used by the mining industry for ultrafine grinding to enhance liberation, and to decrease particle sizes of industrial minerals to tailor functional Stirred media mills in the mining industry: Material grindability
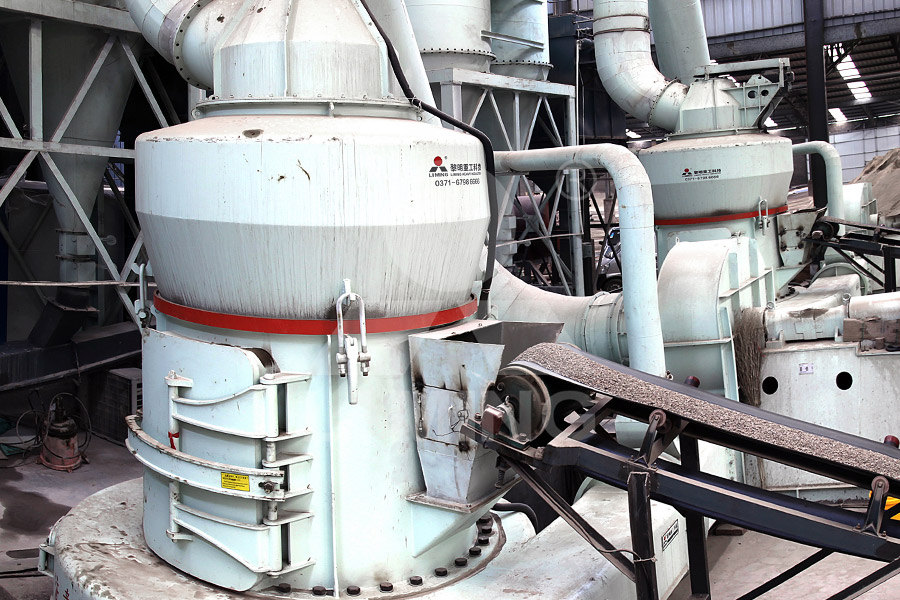
Ore Grinding SpringerLink
2023年7月20日 Moist grinding, a special grinding method, is used to prepare pellets for smelting According to the grinding medium features, ore grinding is mainly classified into ball grinding It is performed in cylindrical steel vessels that contain a charge of loose crushing bodies—the grinding medium—which is free to move inside the mill, thus comminuting the ore particles Grinding Mill an overview ScienceDirect TopicsA major dynamic and kinetic factor now recognized is that the ratio of media rotational flow to ore axial flow, and the number of mill revolutions that ore is subjected to during residence, both ScaleUp And Dynamics Of Large Grinding Mills A Case StudyGrinding mills operate on the principle of breaking down ore particles into smaller sizes through the action of abrasion The primary types of grinding mills include ball mills, rod mills, Understanding the operation of grinding mills in the mining and
.jpg)
Predicting the effect of operating and design variables in grinding
2021年7月1日 Several variables are known to influence the performance of gravityinduced stirred mills, including grinding media characteristics, stirrer geometry and speed, mill 2021年4月29日 Standard Bond tests showed a reduction in the Bond ball mill work index (wi) of the mineral sample used in this study when using Relo grinding media The modified Bond test (PDF) A Comparative Study of Energy Efficiency in Tumbling Mills Speed also plays a role in ore grinding; too high of a speed can cause damage to the mill gears and other components, while too low of a speed can cause excessive wear on these same components It is important to find a balance between these two variables in order to achieve optimal grinding performanceFactors affecting ores grinding performance in ball mills2018年8月17日 The concept of ore blending is a very relevant notion in modern high tonnage production mines It is not only essential for the prolongation of the mine life of the concerned mine but as well as a The effects of ore blending on comminution
.jpg)
Bond´s work index estimation using nonstandard ball mills
2023年9月18日 It is a wellknown fact that the value of the Bond work index (wi) for a given ore varies along with the grinding size In this study, a variability bysis is carried out with the Bond standard 2015年12月14日 The number of revolutions required is calculated from the results of the previous period to produce sieve undersize equal to 1/35 of the total charge in the mill The grinding period cycles are continued until the net grams of sieve undersize produced per mill revolution reaches equilibrium and reverses its direction of increase or decreaseStandard Bond Ball Mill Grindability Test MethodProcedure2015年4月9日 The mill is normally used for grinding of ores Lining of the cylinder plays very important role It protects the mill from abrasions and at the same time it helps in lifting of the material from the bottom of cylinder The types of lining are Grinding Mills and Their Types – IspatGuru2021年7月12日 N 2 —number of revolutions of the mill in the second grinding cycle, (rev) Numerical coefficients and exponents in Equation (6) were determined using the leastA Review of Alternative Procedures to the Bond Ball Mill
.jpg)
Ore mill, Ore grinding mill All industrial manufacturers
This mill accepts grinding set weights of up to 30 kg, the largest grinding jar has a volume of 2,000 ml chemical industry, etc, it has two ore grinding Compare this product Remove from comparison tool ball grinding mill horizontal for ore ball grinding mill Final grain size: 74 µm 2019年8月14日 Ball mill is a common grinding equipment in concentrator Common Types of Ball mill back to top The common industrial ball mills mainly include cement ball mill, tubular ball mill, ultrafine laminating mill, cone ball mill, ceramic ball mill, intermittent ball mill, overflow ball mill, grid ball mill, wind discharge ball mill, double bin ball mill, energy saving ball millThe Ultimate Guide to Ball Mills Miningpedia2023年7月10日 The present literature review explores the energyefficient ultrafine grinding of particles using stirred mills The review provides an overview of the different techniques for size reduction and (PDF) EnergyEfficient Advanced Ultrafine Grinding of Particles 2022年1月1日 The size of grinding media is the primary factor that affects the overall milling efficiency of a ball mill (eg power consumption and particle size breakage)Effect of grinding media on the milling efficiency of a ball mill
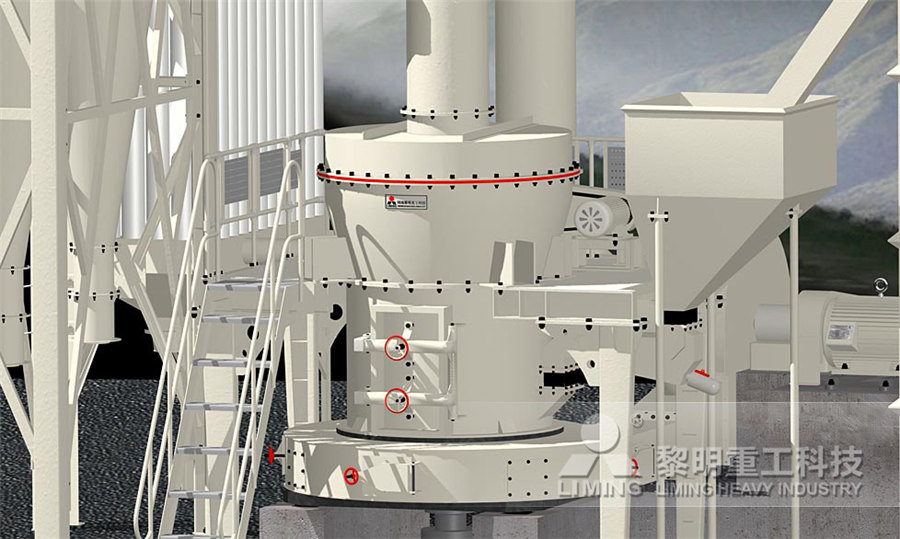
(PDF) A Comparative Study of Energy Efficiency in
2021年4月29日 regression model shows that, at a large number of mill revolutions (longer grinding cycles, Metals 2021, 11, 735 9 of 11 and grinding of ore to liberate valuable mineral particlesThe first example of using an agitated vessel and grinding media for comminution was in 1922 when Szegvari stirred a gallon can full of pebbles to rapidly disperse a sulphur suspension [19]This was developed into the first ‘stirred ball mill’ by Klein and Szegvari in 1928 [20]This prototype was refined into the Attritor mill, a low tip speed (3–5 m/s [21]) vertical pin mill which Semi Autogenous Grinding Mill ScienceDirect Topics2021年7月6日 MLA tests showed that the particlebed breakage did not significantly improve the liberation degree compared to the ball mill grinding; the maximum difference of the proportion of 80100% Comminution a Heart of Mineral Processing2023年3月15日 Types of Grinding Mills Grinding mills can be categorized into several types, each designed for specific purposes and applications Some of the most common types include: Ball Mills: These cylindrical mills use steel balls or rods as grinding media and are often employed in the mining industry for grinding ores into fine powdersThe Evolution and Importance of Grinding Mills in Modern Industry
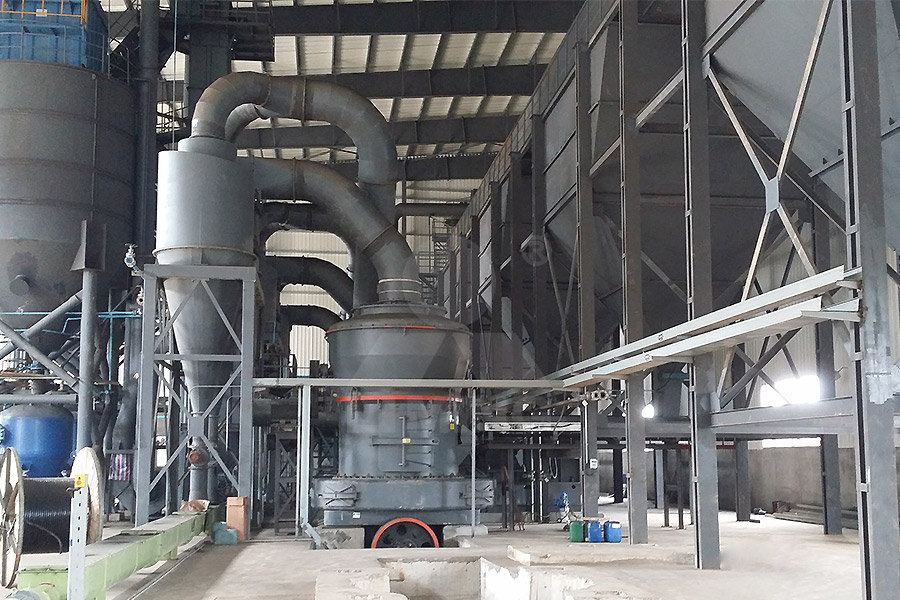
Fine grinding: How mill type affects particle shape characteristics
2017年9月1日 With the continual depletion of high grade simple ore bodies, more complex, finely disseminated ore bodies are being processed, which has led to an increase in the prevalence of fine grinding (Sinnott et al, 2006)This has been evident in the platinum group element (PGE) industry in South Africa, where the Bushveld Complex hosts 70% of global 2005年8月5日 For such materials, a comparative grinding test must be used in which a reference material from an operating plant is ground in a laboratory mill to determine the 'equivalent' energy consumption Determination of work index in a common laboratory mill2019年1月30日 Mill power models have been used in a variety of ways in industrial practice since power directly equates to throughput and fineness of ground product We first start with HoggFuerstenau Power Model and show how this model successfully predicted the power draw of many grinding mills in several mining operations Then, we show how this model was on the The Evolution of Grinding Mill Power Models Mining, revolution of the mill approaches its final equilibrium value after several grinding periods, and this is recorded as the grind ability, or relative ease of grinding, of the sample A cylindrical ball mill, 12 by 12 in inside, with a smooth lining and rounde1 corners, is used with a revolution counter Under standard grinding conditions itStandard Grindability Tests and Calculations 911 Metallurgist
.jpg)
Ball Mill Critical Speed 911Metallurgist
2015年6月20日 Charge movement at Various Mill Critical Speed The Formula derivation ends up as follow: Critical Speed is: N c =766(D 05) where: N c is the critical speed,in revolutions per minute, D is the mill effective inside diameter, in feet Example: a mill measuring 11’0” diameter inside of new shell liners operates at 173 rpm Critical speed is2017年1月1日 In this investigation, we optimize the grinding circuit of a typical chromite beneficiation plant in India The runofmine ore is reduced to a particle size of less than 1 mm in the comminution (PDF) Performance optimization of an industrial ball mill for 2017年7月3日 Variables Affecting Grinding Mill Power Table of Contents Critical Speed Power Speed Obviously, on account of their greater axis of revolution, small particles of ore will centrifugalize at lower speeds than large balls Balls never centrifugalize at speeds indicated by the formula cs 5419/√r where r is the radius of Variables Affecting Grinding Mill Power 911Metallurgist2017年7月20日 Autogenous grinding is favored when the ore is quite competent and a fine grind is required The tester is then run for 500 revolutions after which it is The Union Corporation in a paper on the reduction works at the Autogenous Grinding Semi Autogenous Grinding
.jpg)
(PDF) Assessment of the Performance of Grinding
2021年2月9日 It had been reported by the management that BGM grinding circuit was designed to produce final product size of 125 μm, which had not been achieved for a long period of time under both, low to 2021年11月1日 High chromium balls are recognized as better grinding media in terms of wear rates than forged steel balls, which are conventional grinding media in the milling process of iron ore(PDF) Morphology and wear of high chromium andsample is calculated The present investigation focuses on utilizing the calculated retention time of the iron ore as a standard grinding reference time to the laboratory ball mill for optimizing the grinding time of each ore The desired P 80 (150 μm) with an acceptable range of hematite liberation (>75%) was obtained in the laboratory ball Estimation of Grinding Time for Desired Particle Size DistributionThe Autogenous Mill, also known as AG Mill, is a type of grinding mill used in the mining industry This machine uses ore and rock itself as grinding media to perform its job Unlike other types of mills that use steel balls or rods for grinding materials, the Autogenous Mill relies on the material being ground to break itself into smaller piecesUnderstanding the SAG Mill in Copper Ore Mining Process
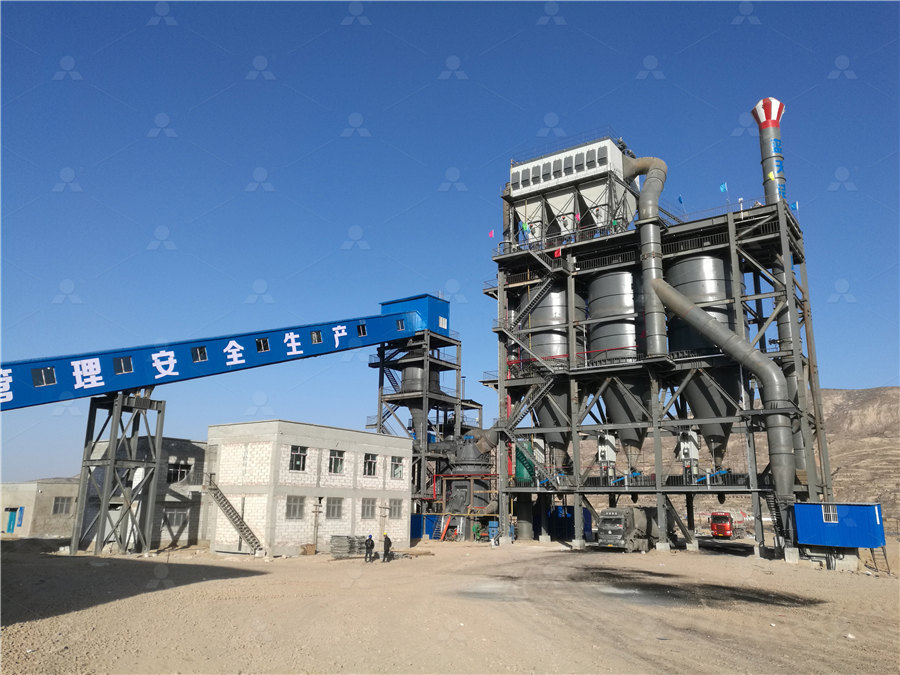
Estimation of Grinding Time for Desired Particle Size Distribution
2020年1月3日 Iron ores obtained from different sources differ in their chemical and physical properties These variations make the process of grinding a difficult task The work carried out in this context focuses on three different samples of iron ore, viz, high silica high alumina, low silica high alumina, and low silica low alumina The grinding process for all the three iron ores is Refractory Gold Ores S Ellis Kalgoorlie Consolidated Gold Mines Kalgoorlie, WA Abstract Since early 2001, Kalgoorlie Consolidated Gold Mines (KCGM) has successfully operated an ultra fine grinding (UFG) circuit to supplement its roaster capacity for the treatment of the refractory gold flotation concentrate A second UFG mill was installed inUltra Fine Grinding A Practical Alternative to Oxidative 2015年6月16日 Weight and transfer ore to the ball mill Grind dry for 100 revolutions Empty the ball charge and ore through a coarse screen to separate the balls from the ore After mill and balls are swept clean, screen and ground ore through the mesh screen to be tested, using coarser protective screens if necessaryBond Grindability Test Procedure 911MetallurgistRequest PDF On Mar 15, 2015, Mathis Reichert and others published Research of iron ore grinding in a verticalrollermill Find, read and cite all the research you need on ResearchGateResearch of iron ore grinding in a verticalrollermill
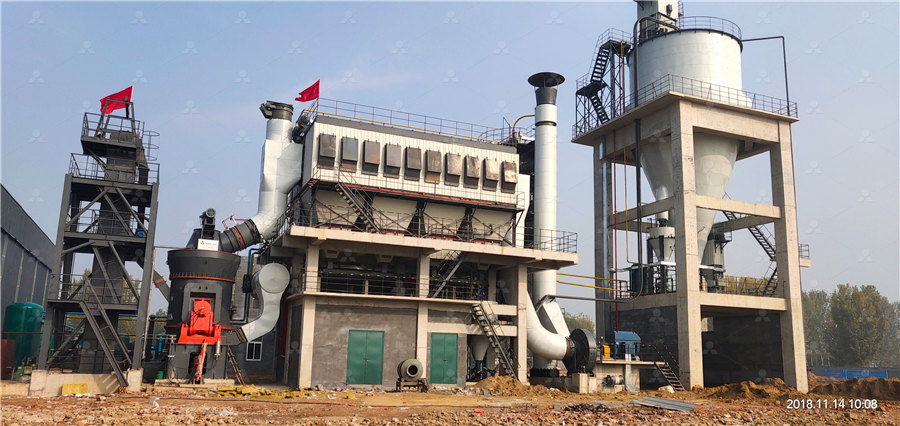
How to choose a suitable ore powder grinding mill?
2023年10月17日 Factors for choosing a suitable ore powder grinding mill 1 Raw material characteristics: Different raw materials have different hardness, humidity and grinding and crushing properties, and the corresponding ore 2016年7月8日 The Work Index values listed in Table I and II apply directly to a wet grinding overflow type rod mill 75 feet in diameter in open circuit; and to a wet grinding overflow type ball mill 75 feet in diameter in closed circuit with a Equipment Sizing: Crusher or Grinding Mill2015年8月6日 It affects retention time and helps distribute the ore throughthe mill so each piece of rock will come in contact with the surface of the rods The % solids by volume of the rod mill discharge Rod mill grinding efficiencies have been shown to increase in the range of 5 to 15% with more dilute discharge slurry (ie, Ball Rod Mill Density – How Water Impacts Grinding2010年12月21日 In the present work, the effects of some key grinding parameters such as ball size (20–40 mm), grinding time (10–30 min), solids content (65–80%), and also ore work index (12–154 kWh/t Optimization of some parameters of stirred mill for ultrafine grinding
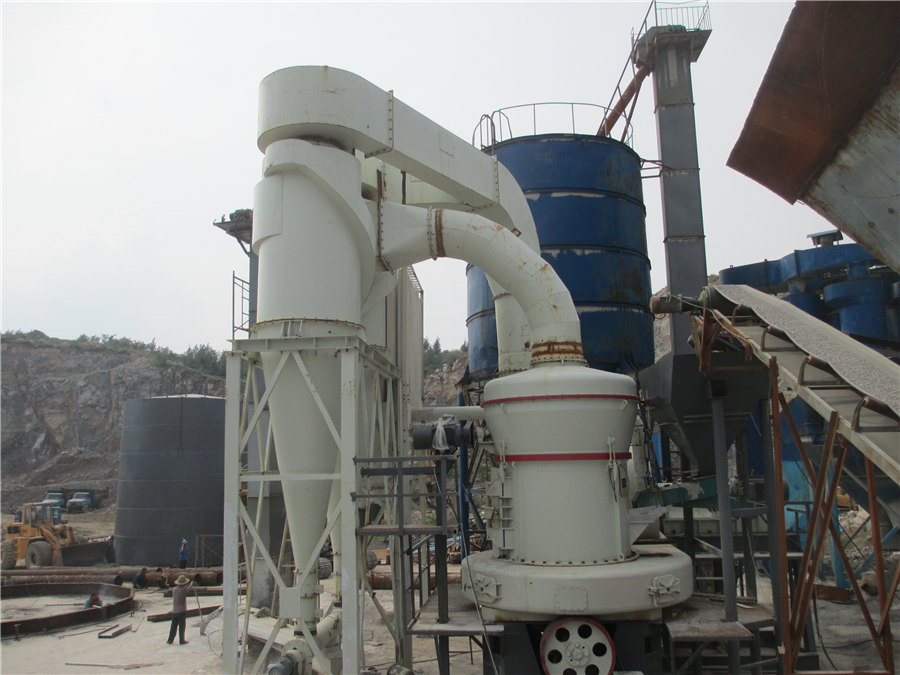
DEM investigation of SAG mill with spherical grinding media
2021年7月1日 After all the particles are randomly generated and settled by gravity, the mill rotates for four revolutions counterclockwise with a speed of 105 rpm to reach the quasisteady state Correspondingly, the percentage of collision energy between ore and grinding media increases from 2125% to 2436%2016年1月1日 In wet grinding practice, highstress abrasion occurs over a small region when ore particles are trapped between the grinding balls and the mill liner, and the load is sufficient to fracture A comparison of wear rates of ball mill grinding media2016年6月6日 Grinding Mill Shell Design Because of the nature of the grinding media (large ore pieces) and lack of steel ball media, various white irons are used because of their high abrasion resistance and, Allow mill to turn five revolutions to pump out slurry, SAG Mill Liner Design 911Metallurgist2009年1月31日 The article discusses the study of the possibility of applying nonstandard mill MSL14K for the Bond ball mill test As a result of ore grinding experiments, the Bond ball mill work index was Procedure for determination of ball Bond work index in the
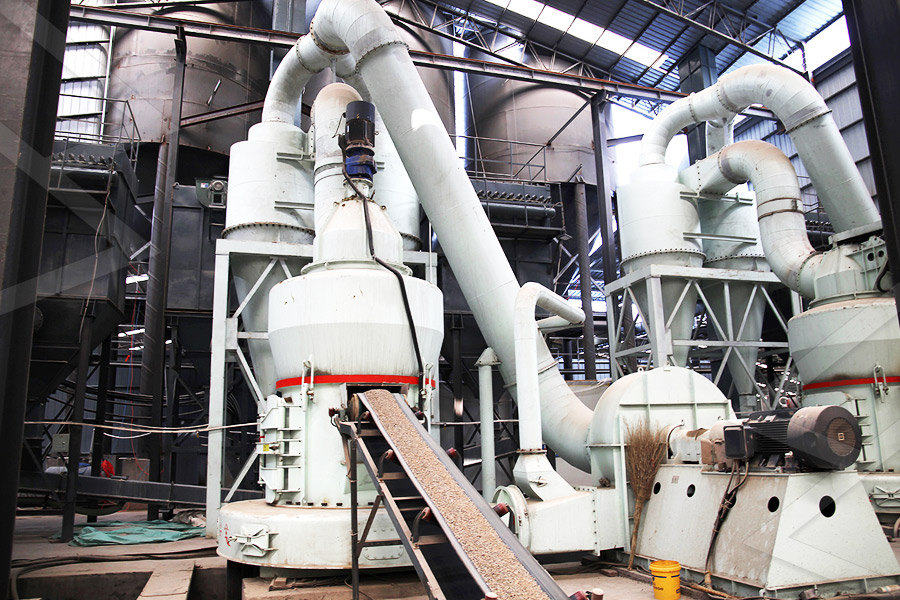
Basic Ball Mill Grinding Circuit 911Metallurgist
2017年1月6日 Tubemills run at a revolution or two faster (see Fig 117) Some ores require much finer grinding than others to liberate the minerals, and this increases the milling cost Ball Mill Product Classifying One passage of ore through a mill is seldom enough grinding to release gold and silver or other minerals from the gangue that grinding the coarse fraction in the rod compartment The Bond formula and power model were used to verify the effects of operational variables, hardness and size distribution of the ore in the mill Mill power calculations were performed based on conditions at the time of sampling, in addition to considering other scenariosMultiCompartment Rod/Ball Mill Evaluation on Bauxite Operation