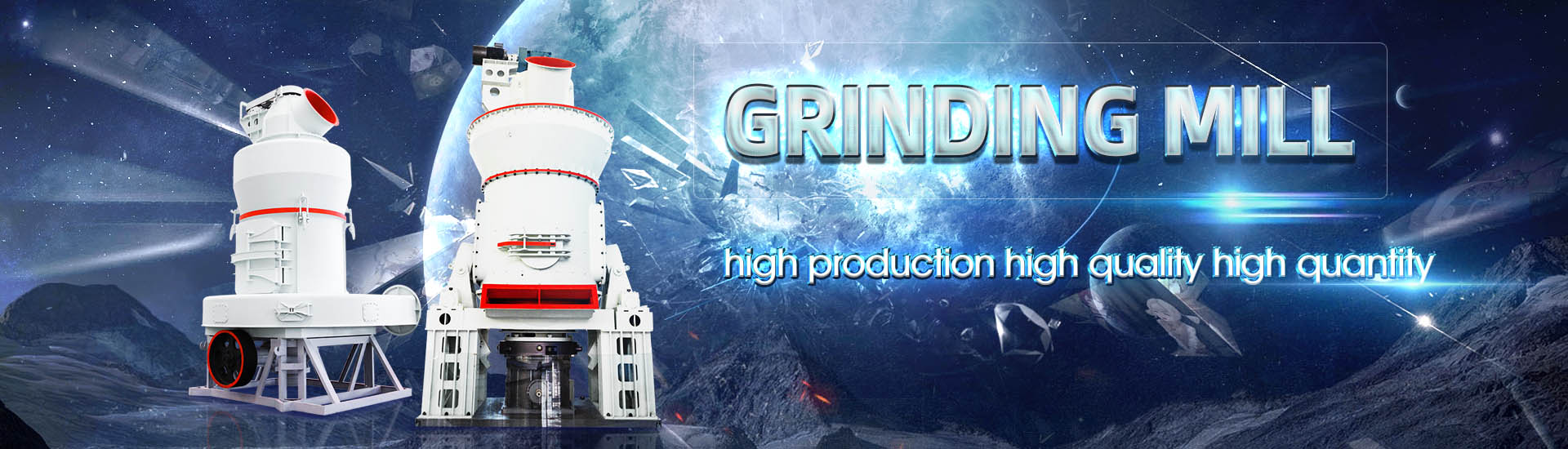
HOME→Ore mill power consumption know power ore mill power consumption know power ore mill power consumption know power
Ore mill power consumption know power ore mill power consumption know power ore mill power consumption know power
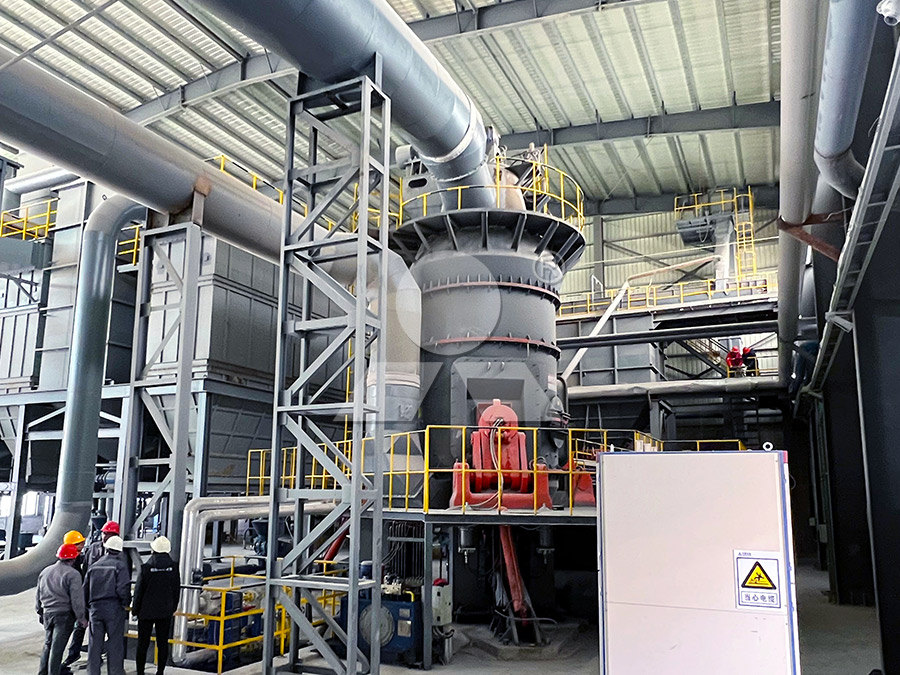
Modelling SAG milling power and specific energy consumption
2015年1月1日 Two new SAG milling models are developed in this work, able to predict power or specific energy consumption, including the usual design variables such as mill size; balls charge level, solids concentration in the SAG mill feed and % of critical speed, but adding a variable energy consumption Comminution is generally the single largest consumer of energy on a mine site, accounting for an average of a 53% (CEEC the future, 2012) The average grade of ores Modelling SAG milling power and specific energy consumption 2020年10月20日 Tracking the mill performance showed that the mill power consumption decreased from 949 to 663 kWh/t (a nearly 30% reduction), P 80 of the mill product The performance improvement of a fullscale autogenous mill by The mill power draw models are used to predict how much power will be consumed by a particular type of mill, mill geometry and set of mill operating conditions This power is transferred to the Mill power draw models
.jpg)
A comparison of SAG mill power models
SAG Mill power draw models are used in mill design and grinding circuit modelling to predict how much power will be consumed by a particular mill geometry and operating configuration This 21 CONCLUSIONS Continued In the present work, equations were also derived, giving: zthe ballmill power drawP as a function of its dimensions: internal mill diameter D and length L, zthe MODELING THE SPECIFIC GRINDING ENERGY AND BALLMILL The amount of comminution or fineness of minerals in a mill can be described by various parameters, the most important of which is (80% passing size) The purpose of this study is to Power consumption management and simulation of optimized Abstract: Milling is among the most energyconsuming technological stages of copper ore processing It is performed in mills, which are machines of high rotational masses The start of Energy Efficiency Analysis of Copper Ore Ball Mill Drive Systems
.jpg)
Grinding power : step by step calculation PowderProcess
31 STEP 3 : Estimate the power consumption of a grinding mill for a particular application The Bond 3rd theory of comminution is estimating the power required to mill a particular ore thanks The analysis of the specific consumption of electric power of mills, obtained during the instrumental examination, showed that the following factors influence the consumption of Specific power consumption of mills when working on various 2020年2月26日 The total energy consumption was divided into three parts: power lost in the electrical motor, power lost in mechanical transmission and power used for grinding materialsCalculation method and its application for energy consumption Energy Efficiency Analysis of Copper Ore Ball Mill Drive Systems Piotr Bortnowski, Lech Gładysiewicz, Robert Król and Maksymilian Ozdoba * industry [7] In Poland, the annual electric energy consumption from copper ore processing plants is approximately 25 TWh [8] components and cause the overloading of the power supply line [30] 3Energy Efficiency Analysis of Copper Ore Ball Mill Drive Systems
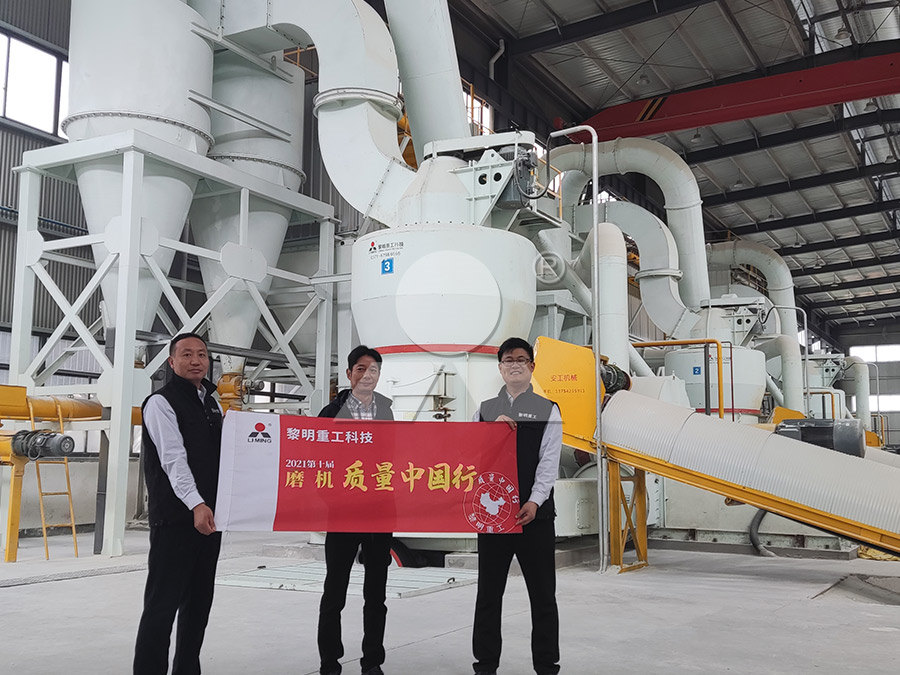
Modelling SAG milling power and specific energy consumption including
2015年1月1日 In general these equations are used to predict power consumption as a function of mill size, level and density of the internal charge and % of critical speed The link between operational practices and specific energy consumption in metal ore milling plants – Ontario experiences Minerals Engineering, Volume 71, 2015, pp 146158Depending on the mill type, the power range of the SAS motors was 400 kW to 1120 kW Low‐power units work with 1875 RPM, while higher‐power units work with 1666Energy Efficiency Analysis of Copper Ore Ball Mill Drive Systemsparticle size of the mill product also has a great influence on the mill power consumption since more mill power consumption is required for more reduction of mill product size [12] The mill weight is dependent on the mill feed rate, mill filling percentage, circulating load, and Model development for prediction of autogenous mill power consumption 2017年5月8日 The power required to drive a tumbling mill is of interest both to the designer and to the mill operator: to the former as a basis of design for the determination of the necessary size of the elements of the machine; and to the latter because all other factors being equal, the most economical machine is that which demands a minimum power for drivingGrinding Mill Power 911Metallurgist
.jpg)
Breaking down energy consumption in industrial grinding mills
2017年1月17日 Excessive mill speeds caused more power consumption but resulted in reduced grinding rate Based on the simulation data, two scaleup models were proposed to predict power draw and grinding rate2015年10月20日 We certainly prefer using JKSimMet when sufficient DWT and SMC data is available It’s much easier to test different conditions, ores and flowsheets than other methods My feeling is that there are two reasons for most of the recent mill design screw ups: i) poor data lack of sample representivity, ore types missed or tests screwed upMethods to Estimate AG/SAG Mill Power Requirements2017年7月26日 Even though the rod mill could be a relatively inefficient device for both energy and metal consumption, as was evidenced by Bond, it still made the overall circuit energy consumption more efficient Under the right operating conditions, high power rate crushing can bring mill feed size down to near 80% passing 7,000 microns and finer, which can be handled How Ball Mill Ore Feed Size Affects Tonnage Capacity2001年8月1日 Decreasing the fill level to 30% again increases the specific power consumption, (but by a smaller percentage than that of the last increase) The peak specific power consumption remains around 105% but continues to broaden For the 25% fill level the power curve is again translated higher by a smaller increment and again the peak broadensCharge behaviour and power consumption in ball mills:
.jpg)
(PDF) Rod Mill Product Control and Its Relation to
2022年1月30日 Energy consumption and pollution are current strategic issues that and related to engine power, material flow model and to evaluate the correct operation of the rod mill with potash oreBall Mill Design Power Free download as PDF File (pdf), Text File (txt) or read online for free This document provides information about grinding mills, including standard sizes and dimensions of mills, descriptions of mill types Ball Mill Design Power PDF Mill (Grinding) Iron 2011年1月1日 b Power profile of the rotating mill, which averages out at 737 W for a mill rotating at 70 rpm Measurement of electrical energy consumption in a ore pretreatment laboratory equipped for fullfledged implementation of the first two methods in the list above All of the said methods aim to find specific energy for the required SAG comminution of test ore material Specific energy consumption (SEC) measured in kWh/t is a ratio of the mill drive power to the milling circuit output,CALCULATION OF THE REQUIRED SEMIAUTOGENOUS MILL POWER
.jpg)
power consumption mill
power consumption of roller mill Home; power consumption of roller mill; show paper grinding mill sri lanka amroninternational on the outside, horizontal grinding mills often face the elements skf solutions help drive grinding mill reliability and safety while reducing maintenance and operating costs skf hydrostatic shoe bearings Assuming the efficiency is 100%, the power required to remove the material is the same as the power used by the machine’s motor Each machine has a maximum power limit that it can handle Therefore, it is helpful to calculate the power required to perform a machining operation such as milling or turning and compare it to our machine’s abilityMachining Power Calculator and Formulasoperating conditions of the mill, particle size distribution of the mill discharge, mill flowrate, material retention time, breakage mechanism and other parameters All parameters affecting the efficiency of mills also affect the mill power draw The diameter and length of the mill, mill charge amount, the amount of grinding mediaPower consumption management and simulation of optimized Process 63 (2001) 79–114 97 Fig 7 Ža Dependence of the specific power consumption vs mill speed curve on the lifter shape for face angles between 858 and 2258 The fill level here is 40% Žb Change in specific power consumption with face lifter angle throughout the lifter life cycle for the rotation rates N s 70%, 80%, 90% and 100%Charge behaviour and power consumption in ball mills:
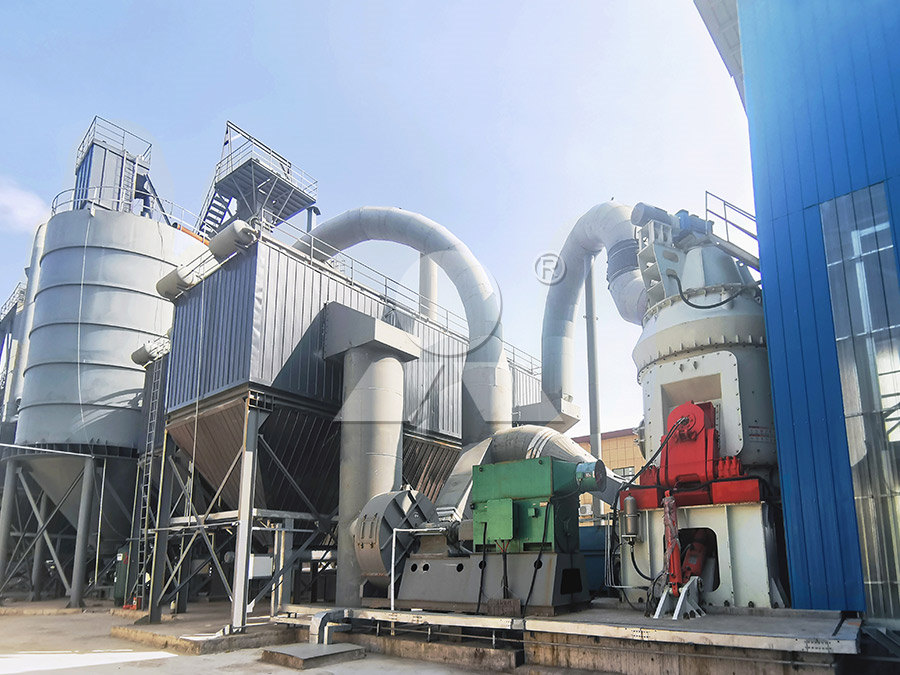
Modelling SAG milling power and specific energy consumption including
2015年1月1日 The feed size distribution is also the implicit result of the ore competence (affecting blasting and crushing performance) This distribution affects the SAG mill load and the load affects directly the mill power and the efficiency of the mill operation (Van Nierop and Moys, 2001)If a SAG mill has been designed with a conventional power or specific energy model 2001年8月1日 Request PDF Charge behaviour and power consumption in ball mills: Sensitivity to mill operating conditions, liner geometry and charge composition Discrete element method (DEM) modelling has Charge behaviour and power consumption in ball mills: 3 Estimation of the power consumption of a grinding mill 31 STEP 3 : Estimate the power consumption of a grinding mill for a particular application The Bond 3rd theory of comminution is estimating the power required to mill a particular ore thanks to the following formula [Chopey] :Grinding power : step by step calculation PowderProcessMill Power Draw Models The mill power draw models are used to predict how much power will be consumed by a particular type of mill, mill geometry and set of mill operating conditions This power is transferred to the ore and used to predict the throughput when combined with the specific energy consumption modelsMill power draw models
.jpg)
Modeling of energy consumption factors for an industrial cement
representative energy consumption factors (output temperature and motor power) Using SHapley Additive exPlanations (SHAP) as one of the most recent EAI models accurately helped ll the lack2020年10月20日 Tracking the mill performance showed that the mill power consumption decreased from 949 to 663 kWh/t (a nearly 30% reduction), P 80 of the mill product decreased from 611 to 355 μm, and the mill fresh feed flow rate increased from 511 to 521 t/h by decreasing the feed ore hardness from 112 min to 58 min based on SAG power index (SPI)The performance improvement of a fullscale autogenous mill by setting 21 CONCLUSIONS Continued In the present work, equations were also derived, giving: zthe ballmill power drawP as a function of its dimensions: internal mill diameter D and length L, zthe ballmill power drawP as a function of the feed D f (mm) and the product size d (mm), the Bond work index w i (kWh/short ton) and the mill throughput T (short ton/h), zthe ballmill dimensions (D MODELING THE SPECIFIC GRINDING ENERGY AND BALLMILL 2001年8月1日 Discrete element method (DEM) modelling has been used to systematically study the effects of changes in mill operating parameters and particle properties on the charge shape and power draw of a 5m ball mill Specifically, changes in charge fill level, lifter shape (either by design or wear) and lifter pattern are analysed The effects of changes to the properties of the Charge behaviour and power consumption in ball mills:
.jpg)
Comminution a Heart of Mineral Processing ResearchGate
2021年7月6日 which mineral aggregates are gotten from the ore accordingly, the power consumption requirements are computed, and pieces of It is interesting to know that a total of 5% of world energy 2017年1月1日 the material inside the mill Feed rate and power consumption are correlated with each other, It is important to avoid agglomeration and reduce the power consumption per ton ore produced(PDF) Performance optimization of an industrial ball mill for 2016年6月6日 The original SAG mill control loop, a mill motor power draw set point of 5200 Amperes controlling the coarse ore feeder speeds, was soon found to give excessive variation in the mill ore charge volume and somewhat less than optimal power drawSAG Mill Grinding Circuit Design 911Metallurgist2018年4月17日 The computer data input sheet Figure 2 shows the set of data given to the computer to finalize the mill sizing Figure 3a and 3b gives the results of the computer calculation The mill power at the pinionshaft for a 30% volume charge is the sum of: Figures 3a 3b give the power for an autogenous millAutogenous and SAG SemiAutogenous Mill Design Calculations
.jpg)
Fine Grinding as Enabling Technology – The IsaMill
simply cannot produce a 10 micron product at any practical power consumption In this case the IsaMill has extended the economic range of grinding from about 2030 microns to 10 microns – enabling technology if a 10 micron grind is needed, as it was for the KCGM cyanide leach Mill Diameter Mill Length Installed Power Mill Volume Power IntensityIt is generally accepted that practical mill power (PM ) is a function of mill capacity and diameter, ie,P M = Mill Constant * (Mill Diameter ) n where n = 03 to 05 It is evident that mill power is a function of the height at which the media is lifted AMIT 135: Lesson 7 Ball Mills Circuits – Mining 2023年4月23日 Fortsch [87] also found that when the mill loading is reduced, there is a reduction in mill power draw However, in a commercial mill study, the findings indicated a negative impact for ball mill (PDF) Grinding Media in Ball MillsA Reviewmachines, power models and, where available, DEM simulation results Additionally, stirred milling power draw is significantly affected by the mass of the media in the mill and the machines are designed with flexibility such that media can be added as required to achieve the desire mill power consumption OVERVIEW OF POWER MODELSTowards a Better Understanding of Stirred Milling Technologies
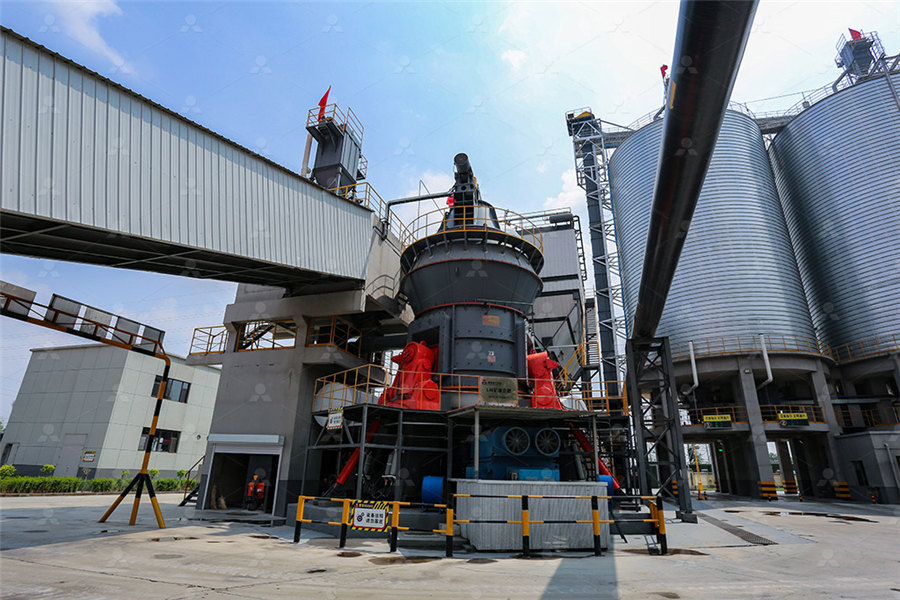
Modelling SAG milling power and specific energy consumption including
2015年1月31日 Tracking the mill performance showed that the mill power consumption decreased from 949 to 663 kWh/t (a nearly 30% reduction), P80 of the mill product decreased from 611 to 355μm, and the mill 2003年10月3日 It was observed that at all mill speeds, the mill power draws for worn liners were higher than that of the new liners For example, for 25% filling and 70% mill speed, the power draw of the worn Grinding mills: how to accurately predict their power draw2023年10月1日 Fig 2 shows a proportional relationship between the simulated work index (W i(sim)) and mill power drawn (kW) This confirms the low energy consumption based on the low works index values The limestone ore shows the highest mill power consumption of 0340 kW and a work index value of 130 kWh/ton However, the lowest belong to the fluorite oreEstimation methodology for Bond ball mill work index experiment Abstract: Optimizing power consumption in grinding, the most consumed stage in the mining industry, plays an influential role in reducing operating costs Obtaining an efficient model to predict tumbling mills' power consumption accurately took the attention of researchers, mineral processing engineers, and tumbling mill manufacturersModelling the power draw of tumbling mills: A comprehensive
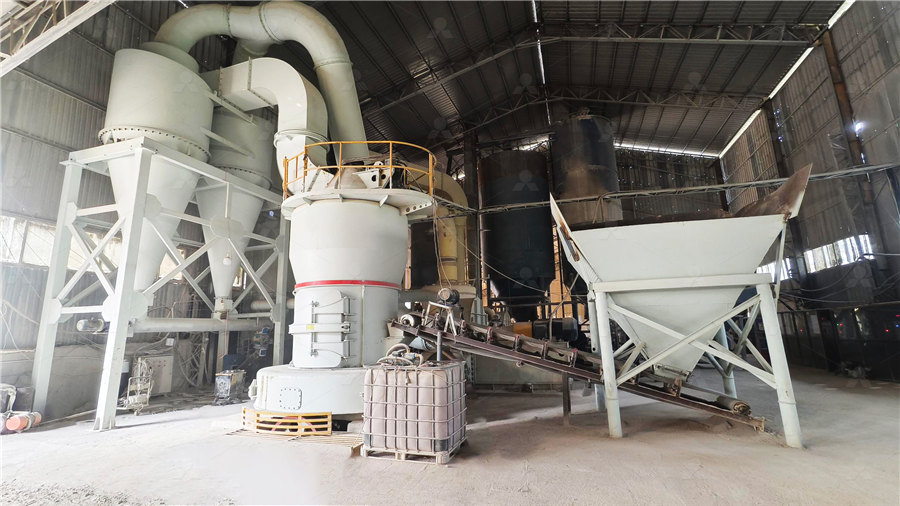
Ball Mill Motor Power Draw Sizing and Design Formula
2015年10月19日 The following equation is used to determine the power that wet grinding overflow ball mills should draw For mills larger than 33 meters (10 feet) diameter inside liners, the top size of the balls used affects the power drawn by the mill This is 2017年5月1日 Crushing and grinding consume most of the energy in mineral processing Ball mill is an important kind of grinding equipment used to decrease the size of ore particles The power consumption of a ball mill is one of the most important parameters to consider in the design of a ball mill because it determines its economic efficiencyEffect of lifters and mill speed on particle behaviour, torque, and