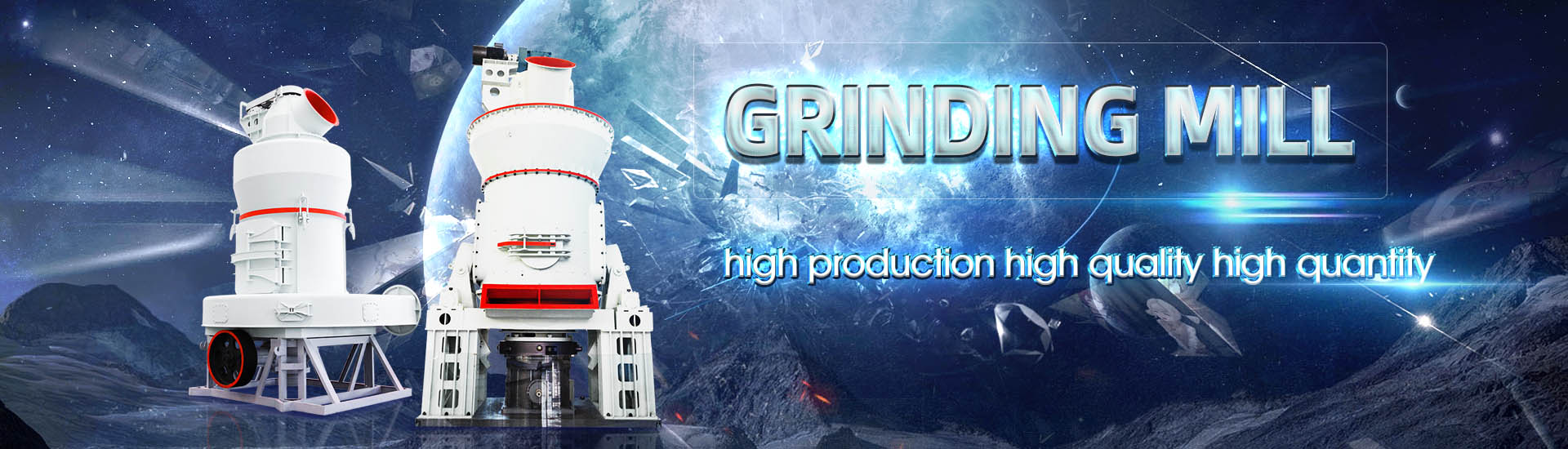
HOME→Is it feasible if the power plant coal mill is not designed with inlet and outlet differential pressure
Is it feasible if the power plant coal mill is not designed with inlet and outlet differential pressure
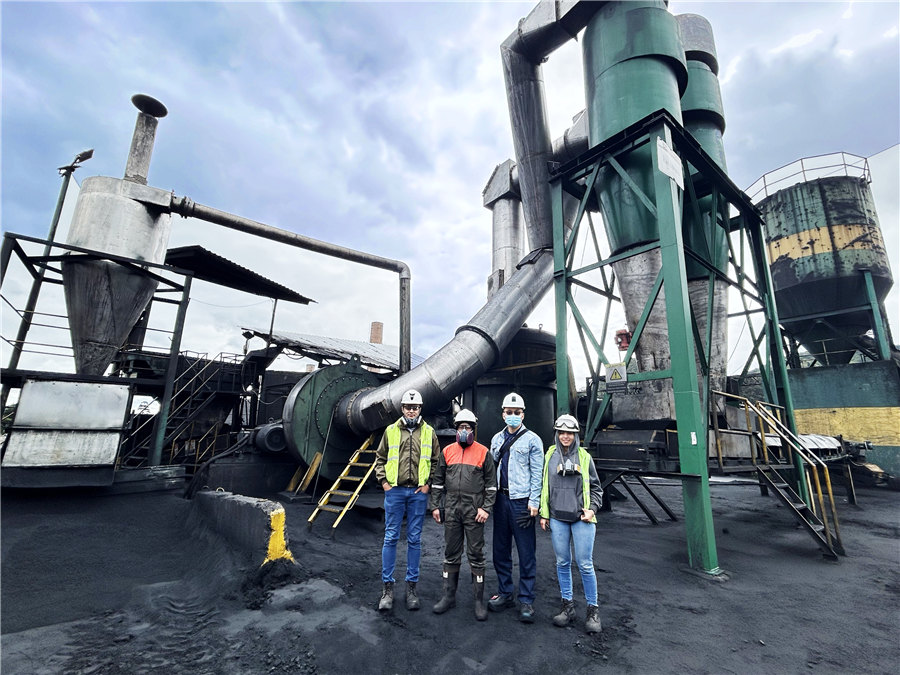
Derivation and validation of a coal mill model for control
2012年5月1日 The paper presents development and validation of a coal mill model to be used for improved mill control, which may lead to a better load following capability of power plants fired by pulverized coal The model is relatively simple, yet it captures all significant mill dynamicsCoal mills or pulverizers play a very essential part in the coalfired power production system Coal mills grind the coal into fine powder, and the primary air entering the mill dries and drives the Coal Mill an overview ScienceDirect Topics2009年9月20日 The coal mill used in the coalfired power plants is modeled in view of the controller design rather than the educational simulator The coal mass flow and the outlet Modeling and Parameter Identification of Coal Mill ResearchGate2010年3月1日 By adopting this multisegment coal mill model in power plants, the power plant engineers will be offered a nonstop model for monitoring the coal mill system The model can (PDF) Condition Monitoring of Power Plant Milling Process Using
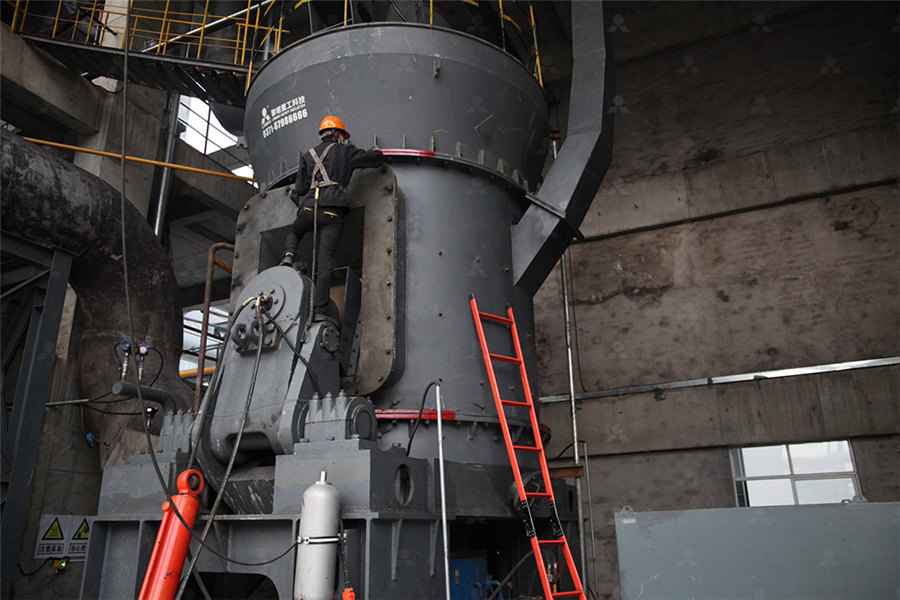
A new modelbased approach for power plant Tubeball mill
2014年4月1日 Adding biomass to coal for cofired power generation has become widely implemented practices in order to meet the emission regulation targets These have impacted 2020年8月12日 In a power plant, the coal mill is the critical equipment, whose effectiveness impacts the overall power plant efficiency Uniform coal feeding mass flow rate and required An investigation of performance characteristics and energetic This report provides a guide to the principles of combustionbased steam cycle plants and combined (gas and steam) cycle plants fuelled by coal The main types of power generation Understanding coalfired power plant cycles ICSC2021年10月28日 CO 2 emissions from coal power generation could be reduced by maximizing the amount of torrefied biomass that can be used in pulverizedcoalfired power plants In this Milling Characteristics of Coal and Torrefied Biomass Blends in a
.jpg)
Review of control and fault diagnosis methods applied to coal
2015年8月1日 Overall plant performance and reliability is highly influenced by the mill downtime If there is less or no pulverized coal for combustion, it leads to plant derating or at the worst, 2013年1月1日 In this paper, we proposed a fault diagnosis method based on fuzzy clustering analysis and DS evidence theory to solve the problem of the faults of complex system with The Research on Fault Diagnosis Method of the Coal Mill Based on 2020年6月29日 Grinding takes place by Impact and attrition The primary air is divided into two parts: A Bypass Air: Mixes with the raw coal and dries it before it enters the Mill It also carries the Pulverized fuel by maintaining sufficient classifications and working of mills in a power plantCoal mill is an important component of the thermal power pla nt It is used to grind and dry the moisturized raw coal and transport the pulverized coal ± air mixture to the boiler Poor dynamic performance of coal mill will lead to decrease in the overall efficiency of the power plant, slow load take up rate and fr equent shut downModeling and Control of Coal Mill
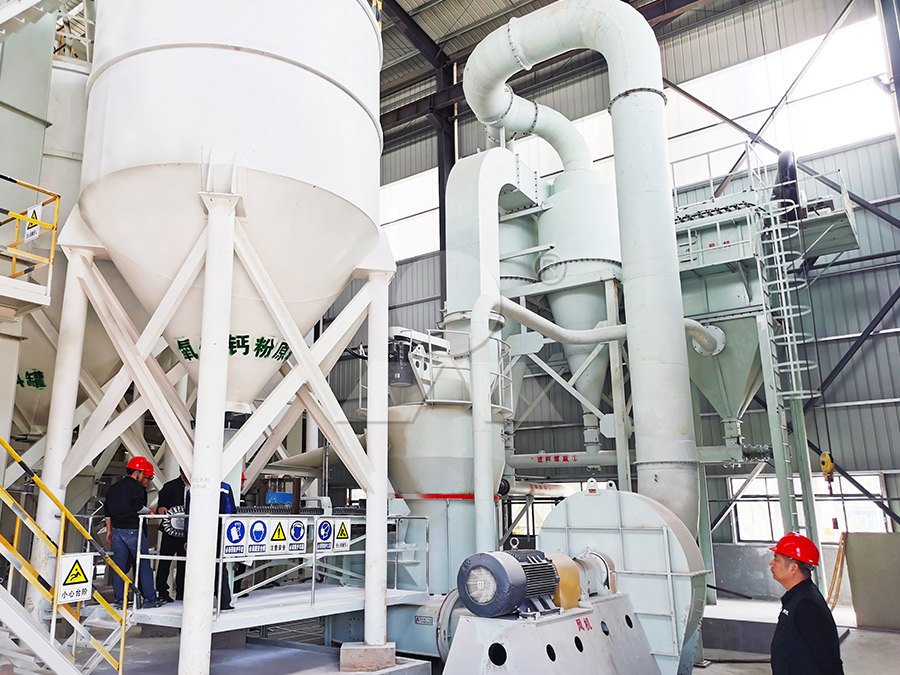
Decision Support System for Coal Mill Fault Diagnosis in Coal
faults are the decrease of differential pressure between the inlet and the coal mill outlet, the reduction of the mill current, and the increased outlet temperature [5] c Fire Coal Mill Mill fire or explosion is a fault that causes the possibility of combustion/ignition of coal 2015年11月1日 From Fig 3, Fig 4, Fig 5, Fig 6 and Table 5, it can be seen that the measured outputs of the proposed model (mill differential pressure, current, outlet temperature) approach the onsite values very well and unmeasured outputs (pulverized fuel flow, mass accumulated inside the mill, outlet moisture content, moisture in accumulated coal inside the mill, mill A unified thermomechanical model for coal mill operationMill drive power or mill differential pressure to control mill feed rate Inlet gas temperature Outlet gas temperature Outlet gas flow Few countable salient Features of Vertical Mills They are air swept mills, therefore has a higher drying capacity to handle an aggregate moisture of up to 20% in raw materialsCoal Grinding Cement Plant Optimization2015年10月1日 The coal mill used in the coalfired power plants is modeled in view of the controller design rather than the educational simulator The coal mass flow and the outlet temperature are modeled by (PDF) Control for pulverized fuel coal mill ResearchGate
.jpg)
Mill Inerting and Pulverizer/Mill Explosion Mitigation
Very hot mill inlet temperatures are required to: Dry coal Achieve mill outlet temperatures Heat required is determined by coal moisture Heat supplied is product of the temperature and quantity of airflow at mill inlet2017年12月18日 In this paper, mass flow rate of flue gas at inlet outlet for pulverized coal power plant are analyzed with consecutive steps For this required coal input for a specific power generation is ANALYSIS ON MASS FLOW RATE OF FLUE GAS FOR A PULVERIZED COAL POWER Coal Mills are used to pulverize and dry to coal before it is blown into the power plant furnace Operation The coal is feed into the coal mill through a central inlet pipe where gravity is used to lead the coal to the bottom of the mill, where the grinding table and some heavy rollers pulverizes the coal to particlesCoal Mills SolidsWikiThis document discusses coal pulverizers/mills which are critical components that convert the stored energy in coal into electricity There are various types of pulverizers that primarily utilize grinding, drying, classification and circulation processes Key aspects covered include the different principles of grinding, types of pulverizers, performance criteria such as fineness and Coal Mill in Thermal Power Plant
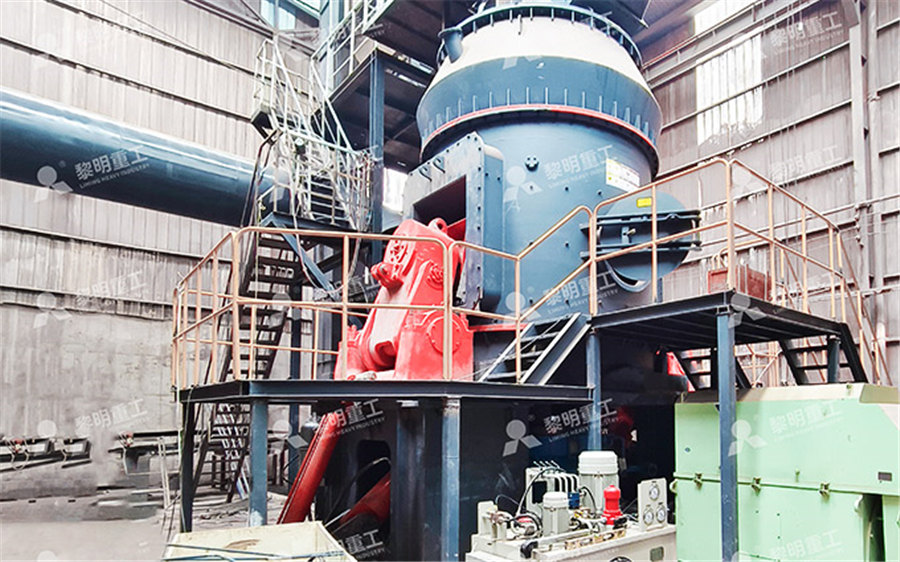
Capturing carbon from coal plants: Is it feasible?
2012年1月5日 The chilled ammonia technology has already been installed at the Pleasant Prairie Power Plant, a standard coalfired power plant in southeastern Wisconsin, where it has been successfully capturing carbon dioxide for more 2020年4月7日 The inlet a ir pressure of coal mill is mainly determined by t he outlet pressure of primary fan and the openings of regulating valves However, when the coal blockage occurs, wit h the increase ofModeling of Coal Mill System Used for Fault 2015年8月1日 Mill problems originate mainly due to poor controls or faults occurring within the milling system As discussed by GQ Fan and NW Rees [3], the control of mills remains very simple in most of the power plants due to the fact that the mill system is highly nonlinear with strong coupling among the variables and it is very difficult to measure some important Review of control and fault diagnosis methods applied to coal standalone centrifugal static classifiers and a ball tube mill Raw coal from the feeders is mixed with hot primary air and then fed to crusher dryers After primary crushing and initial drying with the crushers, the crushed coal is fed into the mill for pulverization The pulverized coal from the mill is air conveyed to the classifiersMill Steam Inerting System Review and Performance Validation
.jpg)
A new modelbased approach for power plant Tubeball mill
2014年4月1日 Input variables Intermediate variables Output variables; A P 1 (%) – A1 feeder actuator position: M c (kg) – mass of coal in mill: T out (°C) – mill outlet: A P 2 (%) – A2 feeder actuator position: M pf (kg) – mass of pulverized coal in mill: Temperature: T in (°C) – primary air temperature inlet the mill: W c (kg/s) – mass flow rate of raw coal into the mill2010年3月1日 differential pressure and the density of air under the mill inlet temperature Equation 2 represents that the flow rate of coal into coal mill is equal to the rate at(PDF) Condition Monitoring of Power Plant Milling Process Using The coal mill used in the coalfired power plants is modeled in view of the controller design rather than the educational simulator The coal mass flow and the outlet temperature are modeled by Sectional view of MBF coal mill Download Scientific Diagram2014年10月1日 Request PDF Numerical and experimental analysis of pulverized coal mill classifier performance in the Soma B Power Plant Coal particle separation in a classifier after the pulverization Numerical and experimental analysis of pulverized coal mill
.jpg)
Observer and DataDrivenModelBased Fault Detection in Power Plant
2008年7月1日 This paper presents and compares modelbased and datadriven fault detection approaches for coal mill systems The first approach detects faults with an optimal unknown input observer developed 2016年8月1日 Because the total pressure of the primary air fan in a coalfired power plant is no less than the total pressure drop of the system including the pipes and devices before and after the primary air fan, the pressure which meets the total pressure drop is regarded as the calculated total pressure p, which can be expressed as follows [27], [28]: (3) p = p in + Δ p in + ∑ Δ p f + A powersaving control strategy for reducing the total pressure 2020年4月2日 Milling system in coal power plant purposely to process the raw coal to become as pulverise fuel before enter to the boiler furnace Pulverise fuel enter to the boiler furnace through pulverise Analysis of the Coal Milling Operations to the Boiler 2013年1月1日 The coal mills are key equipments in the power plant []Faults often happen because they work in the complex operating environment Through analyzing faults, we find that faults of the coal mills present characteristics of fuzzy and uncertain, which a kind of fault may exhibit a variety of different fault symptoms, and for different fault types may also produce the The Research on Fault Diagnosis Method of the Coal Mill Based
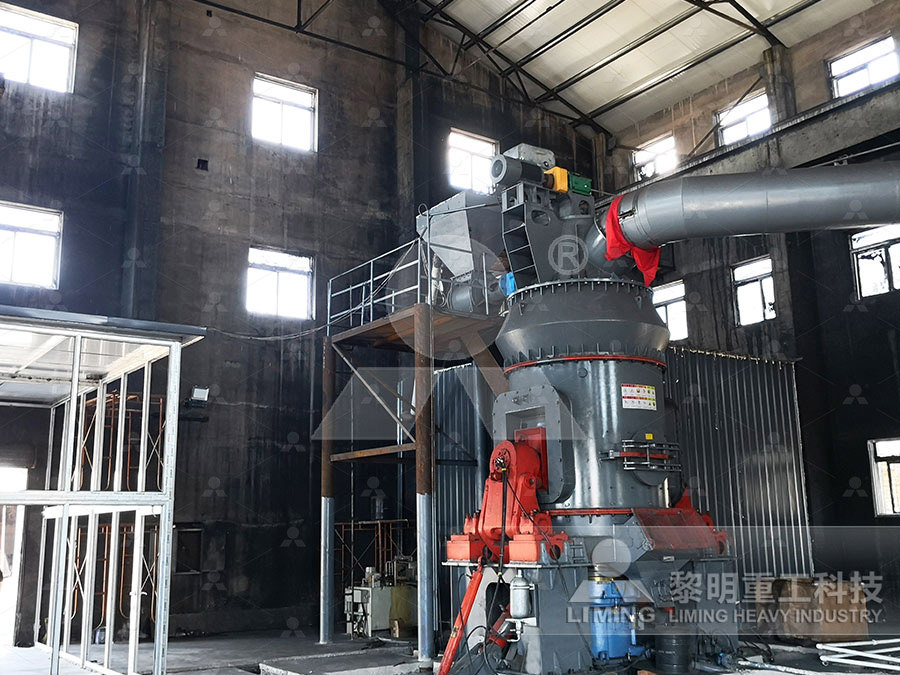
Modeling of complex equipment coal mill in power plant ICJE
steam flow rate, coal feeder nominal speed, inlet coal grindability coefficient, MB coal mill blockage (0100), coal mill outlet pulverized coal temperature, outlet air flow moisture Content, coal storage capacity of the coal mill, average metal temperature of the coal mill machine, and motor power of the coal mill2020年9月1日 For modelbased fault diagnosis method, it first needs to establish a mathematical model of the coal mill Odgaard et al [2] used a simplified energy balance equation to monitor and diagnose abnormal energy flow in the coal mill Andersen et al [3] designed a Kalman filter to estimate the moisture entering and leaving the coal mill, thereby identifying whether the Research on fault diagnosis of coal mill system based on the 2019年8月1日 In thermal power plant each boiler uses pulverized coal as main fuel for combustion High performance bowl mills of bowl size 80" are used for pulverizing the coal to required fineness of about 70 Design and Modify of Mill Discharge Valve Using in Thermal Power Plant In this paper, GA is applied to develop the coal mill model and to estimate the pulverised coal flow using real time onsite plant data 2 COAL MILL MODELLING In thermal power plant, pulverization of coal is carried out by coal mill Raw coal is moved from the storage to the mill by conveyor mechanism The type of coal mill envisaged for ourPulverised Coal Flow measurement in Thermal Power Plant
.jpg)
An Optimization Study on SootBlowing of Air Preheaters in Coal
2019年3月12日 It can be used for the sootblowing optimization in most coalfired power plant boiler with air preheaters Boiler main operation values Parameters of the functions in Figure 6During normal operation, the mill pressure drop is predominately proportional to the primary air differential pressure and a small change in coal mass does not affect the pressure drop significantly Also, when the coal mass becomes zero, the pressure drop also becomes zero These conditions are guaranteed by the term (PDF) Modeling and Control of Coal Mill AcademiaSection of coal bowl mill Table 1 Guaranteed coal conditions for mill performance evaluation Coal Moisture % 20 Coal HGI 55 Mill Outlet Temperarure °C 80 Mill Air Flow T/hr 102 Coal Fineness (% passing trough 200 mesh) 70% passing through 200 mesh and 90% passing through 50 mesh Differental Pressure 300 mmwc Coal Output from Mill 609 t/hrA Study on 500 MW Coal Fired Boiler Unit’s Bowl Mill Besides medium speed coal mill and high speed bleeder wheel mill, double inlet outlet ball mill plays major role of direct fired pulverized coal preparation system in thermal power plant Working principle Double inlet outlet ball mill has two symmetric circuits shown in picture Coal feeder sends coal into drop pipeDouble inlet outlet ball mill Geckointech
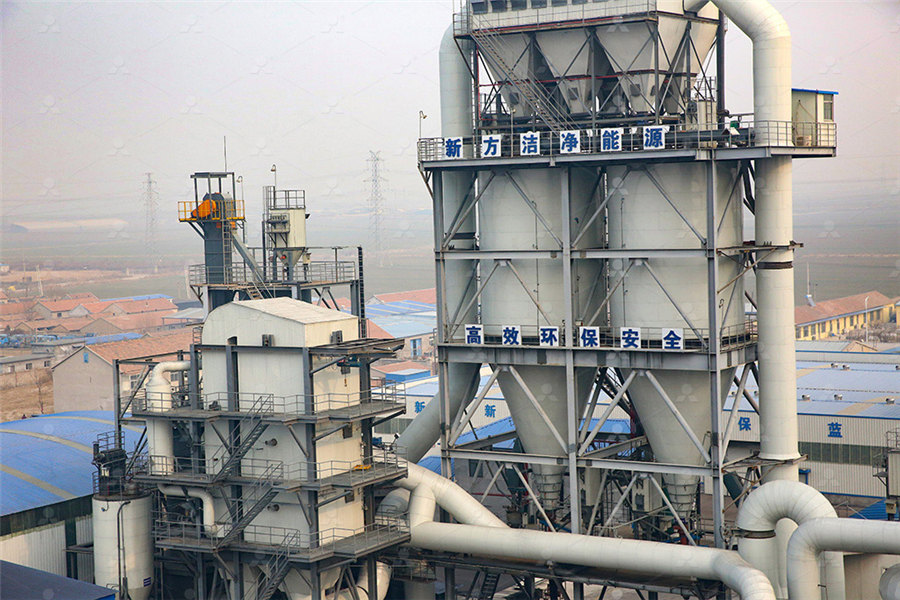
OPTIMISATION OF THE INSTALLED BOILER AND
2022年5月1日 PDF A simple research recommendation for the improvement of the Pagbilao Coal Power Plant Find, read and cite all the research you need on ResearchGateduty watercooled bearings Pressurized air seals between the rotating mill and inlet/outlet boxes prevent leakage of coal dust or air from the mill Each mill is completely enclosed in an insulated soundattenuating housing with panels that provide easy access to the mill The mill is driven by a directcoupled ac motor throughA Comparison of Three Types of Coal Pulverizers Babcock Power2006年6月1日 Three system output parameters of vertical roller coal mill (the pressure drop over the mill, power consumed by the mill and outlet temperature) models have been developed and used in nonlinear Fault Detection in Coal Mills Used in Power PlantsNonlinear coal mill modeling and its application to model predictive control are presented in [7] Three system output parameters of vertical roller coal mill (the pressure drop over the mill, power consumed by the mill and outlet temperature) models have been developed and used in Detection of Malfunctions and Abnormal Working Conditions of a Coal Mill
.jpg)
Monitoring Model of Coal Mill in Power Plant Based on Big Data
In order to monitor the wear condition of grinding roller of coal mill in power plant and improve the reliability of production equipment, it is necessary to establish a state monitoring model with high accuracy and good prediction effect It has been shown that the power of coal mill can reflect the wear degree of grinding roller If the voltage and power factor of coal mill are constant The mill design in the power plant is a vertical bowl The mill rotated on his axis at minimum speed 35rpm by a motorreducer train The grinding rolls are supported by three oscillating journals The rolls rotate freely crushing the coal on the bowl, the pressure for optimal crushing beingAnalysis of the Coal Milling Operations to the Boiler Parameters2015年5月7日 Power plant performance and reliability is highly influenced by coal mills that grind, dry, and transport coal to the furnace This paper presents a review of the current state of technology on Review of Control and Fault Diagnosis Methods Applied to Coal 2021年8月1日 pressure is not less than 28Mpa(5)Low quality coal causes insu fficient output of coal mill Fault treatment and improvement and Optimization: (1) check the operation status of primary fan,(PDF) Fault analysis and optimization technology of HP
.jpg)
Modeling and Parameter Identification of Coal Mill
primary air differential pressure, which are used in practice as control inputs to improve the coal mill performance The grinding motor power consumption can be considered as an additional input variable for a heating source The measured output variables are mill differential pressure and outlet temperature The coal mill model isIn thermal power plant each boiler uses pulverized coal as main fuel for combustion High performance bowl mil ls of bowl size 80” are used for pulverizing the coal to requiredDesign and Modify of Mill Discharge Valve Using in Thermal Power Plant