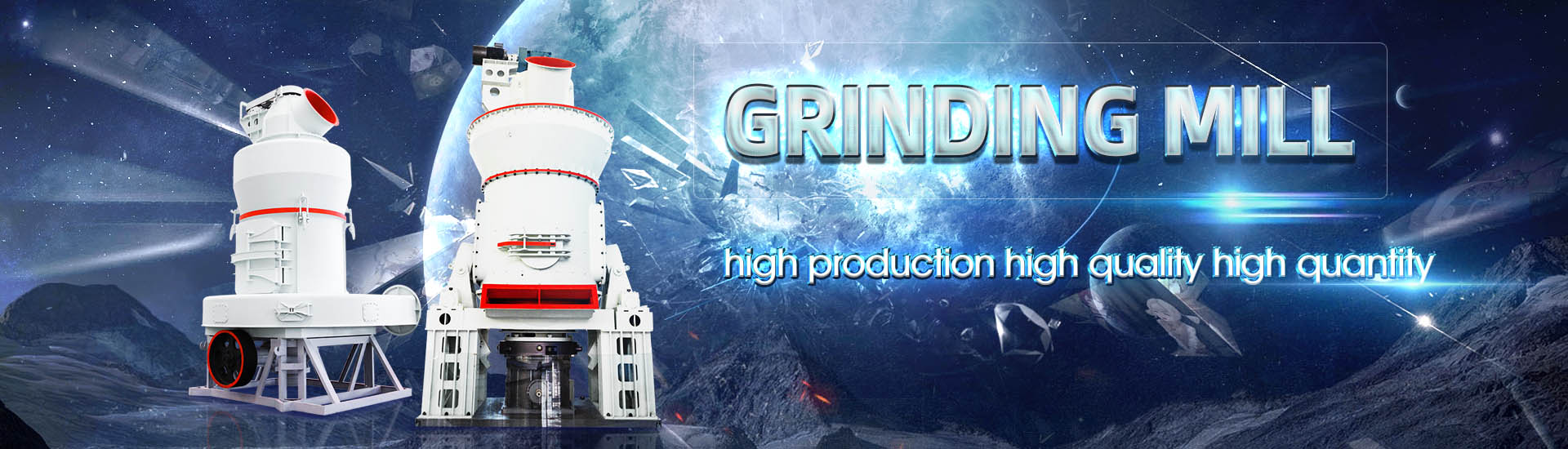
Cement gypsum production line cement grinding accounts for about
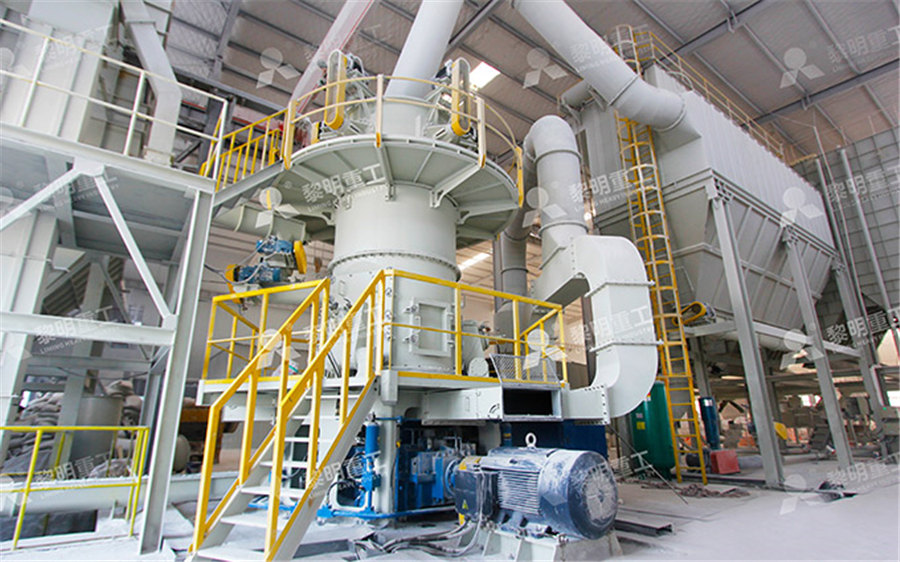
instruction manual of cement production line process
2012年12月31日 Cement production line process, producing 1 ton silicate cement need to grind 3 ton materials (including raw materials, fuel, clinker, mixed materials, gypsum) According to statistics, dry method cement production lines grinding operations need to consume above Finish milling is the grinding together of clinker with some 35 per cent gypsum, natural or synthetic, for set control, and quite often other components: blastfurnace slag, pozzolan, silica The Cement Plant Operations Handbook International Cement AGICO dry process cement production line comprehensively adopts the IT technology, multifunction grinding system, newtype wearresisting and heatresisting materials, mechanical powder conveying device, and some other Cement Production Line Cement Manufacturing 2024年1月17日 According to statistics, the dry cement production line grinding operation consumes Power accounts for more than 60% of the power of the whole plant, of which raw material grinding accounts for more than 30%, coal What Do You Know About Wet Process Of Cement
.jpg)
Everything you need to know about clinker/cement
Everything you need to know about clinker/cement Grinding if You read and understand this article , you will be ready to be a cement grinding area manager FEED AND FEED SYSTEM Feed Temperature Plants with satellite coolers 2020年8月25日 Before you send inquiry Please provide us with project information as much as possible: For a complete project: the material availability, the required output capacity, the process technology, your budgetary and financing status, the estimated starting time, etc For singular machinery: the model, the capacity, your budgetary information, other requirements, etcCement Production Process Cement Manufacturing Process AGICO CEMENT2023年12月26日 As we all know, the dryprocess cement production line is commonly used in the cement industry The new type of dryprocess cement production process includes four main sections: Prehomogenization of raw materials, homogenization of raw materials, clinker firing, cement grinding, etc Raw material conveying system The raw material, including limestone, 6 Cement Equipment For Dryprocess Cement Production LineAccording to the statistics, the grinding operation of dry process cement production line consumes power accounted for above 60% of the entire factory power, of which raw material grinding is more than 30%, coal grinding accounts for about 3% and cement grinding accounts for about 40% of Cement production line in south africa Therefore, it is Cement Production Line In South Africa FTM Machinery
.jpg)
The Cement Plant Operations Handbook International Cement
ASTM cement types and specifications – 16 European EN 197 cement specification – 17 Composite cements (intergrinds and blends) – 18 Supersulphated cement – 19 Calcium aluminate cement (CAC) – 20 Shrinkagecompensating cements (SCC) – 21 ISO 9001:2000 Quality 8 Maintenance168 1 Maintenance benefits and costs – 2 Failure Cement Production Line chinayongh T11:50:36+00:00 Cement According to statistics, the power consumed in the grinding operation of dry cement production line accounts for more than 60% of the power of the whole plant, in which raw material grinding accounts for more than 30%, coal grinding accounts for about 3%, and cement Cement Production Line – My BlogAGICO offers cement production line, stone crushing plant, cement grinding unit, and fly ash processing plant We customize the cement EPC projects for customers according to their requirementsCEMENT MANUFACTURING PLANT cementplantequipmentCement Grinding Plant; Cement Production Line; Stone Crushing Plant; Contact us Tel:+79 mixed materials, and gypsum) Grinding operation consumes about 60% of total power in cement plants, raw material grinding more than 30%, while coal mill used in cement plants consumes 3%, cement grinding about 40%Cement Production Line CHAENG
.jpg)
The role of gypsum in cement Indian Cement Review
2019年1月11日 India’s cement production capacity stood at around 502 million tonnes per year (mtpa) in 2018 and is expected to reach 550 mtpa by 2025 Typically, manufacturing cement uses 2 to 4 per cent gypsum per tonne of Exfactory price cement grinding units for sale! *CEM I: 95%Clinker+5% Gypsum EN1971; *CEM II/BL: 65~79%(Clinker + Gypsum) The water system is for the new production line, which includes only the circulating Modular Mobile Cement Grinding Plant For SaleThese materials include various raw materials, fuels, clinkers, mixtures and gypsum According to statistics, over 60% cement plant power will be consumed to grind materials in dry process cement production line Among which, over Cement production line2023年11月21日 800tph Cement Production line project in Shanxi; 5000tpd Cement Production Line Project In Fujian; 6000tpd Cement Production Line Project In Shandong; 8000tpd Cement Production Line Project In Liaoning; 5000tpd Dry Process Cement Plant Project In Liaoning; 600TPH Limestone Crushing Plant Project In Sichuan; 500tph Limestone Crushing Plant Development Trend Analysis of Cement Production Line
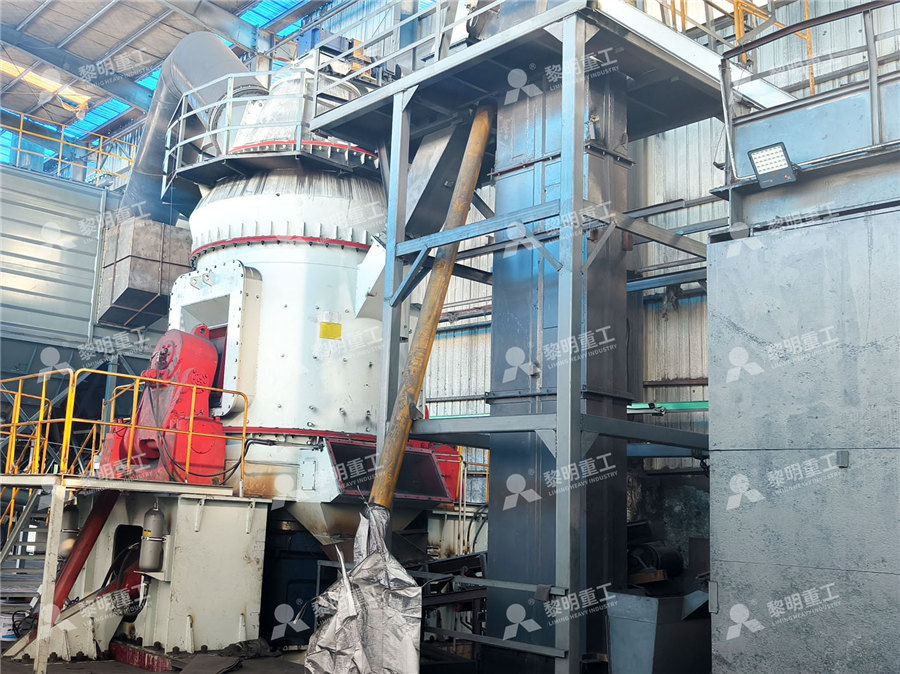
Chapter 1 Introduction To Cement Production PDF Scribd
Cement production involves quarrying limestone and clay, grinding and blending the materials, burning them at high temperatures to form clinker, and finely grinding the clinker to produce cement powder The key steps are: 1) Quarrying limestone and clay and grinding them to powder; 2) Blending the powders in precise proportions; 3) Burning the blend at high heat to form 2022年12月4日 Application of Gypsum in Cement Production:The addition of gypsum to cement changes the properties of cement mortar in a way that Skip to content In addition, Calcium sulfate is added to cement clinker in sizes of 5 to 50 mm during grinding and powdering In most countries such as Japan, Gypsum in Cement Production Jonoub gypsum2019年8月26日 According to statistics, the dry cement production line needs to be consumed The power accounts for more than 60% of the power of the whole plant, of which raw material grinding accounts for more than 30%, coal grinding accounts for about 3%, and cement grinding accounts for about 40%New dry process cement production line process LCDRI CNIn the production of white cement, ceramic balls have been successfully used for years Tests have shown that the use of Cerablu leads to savings in specific power consumption of up to 25 % The grinding media lifetime can be increased by up to +50 %, while the steel contamination sees a decrease of up to 50 gr/tEfficient processes for grinding and separation Cement Lime Gypsum
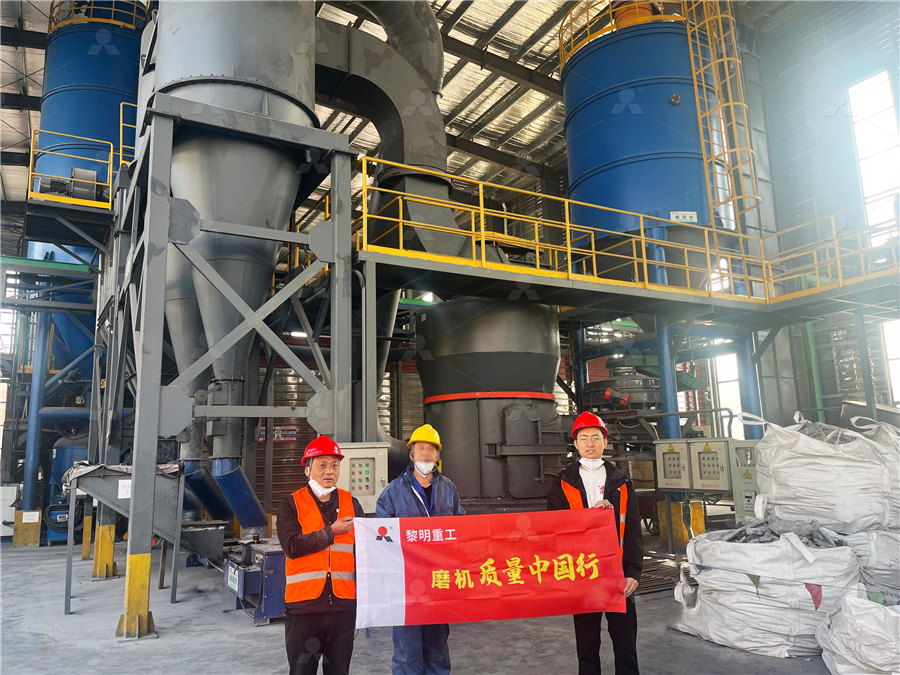
Global database of cement production assets and upstream
2023年10月13日 The top five cement producing countries (China, India, Vietnam, United States and Indonesia) account for approximately 682% of global cement production in 2020, with China alone accounting for 2022年8月10日 Grinding might be an individual step in the cement production line but it is a crucial one, given the energy consumption and impact on the quality of output that it gives ICR explores how grinding methods have evolved with the help of technology and with the use of modernage grinding aids Grinding in the cement []Grinding: Smarter Solutions Indian Cement ReviewThe cement production line is a production line construction project composed of a series of supporting equipment for the production of cement It is mainly composed of crushing, homogenizing, raw material preparing, drying, Cement Production Line Henan Turui Machinery 2024年8月20日 Uses of Gypsum in Cement Gypsum acts as a binding agent in the cement and controls various factors in it It is also used in the walls where fire protection is required since it has a natural fireresistance property Let’s look Uses of Gypsum in Cement BricknBolt
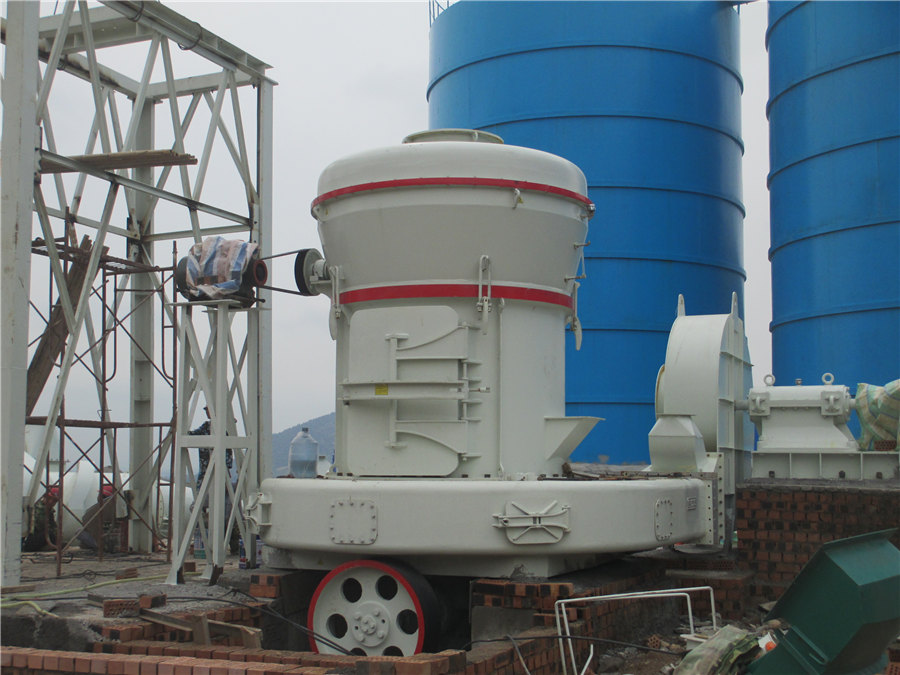
8 Tips For Cement Plant Design
2023年11月1日 The selection of cement production line site must be reliable, that is, the supply of raw materials should be reliable, the market sales should be reliable, and the past will be a complete cement production line in the same The final manufacturing stage at a cement plant is the grinding of cement clinker from the kiln, mixed with 45% gypsum and possible additives, into the final product, cement In a modern cement plant the total consumption of electrical energy is about 100 kWh/t The cement grinding process accounts for approx 40% if this energy consumptionCEMENT GRINDING SYSTEMS INFINITY FOR CEMENT EQUIPMENT2017年5月19日 Grinding is an essential operation in cement production given that it permits to obtain fine powder which reacts quickly with water, sets in few hours and hardens over a period of weeks i Overview of cement grinding: fundamentals, additives, technologies2020年6月3日 Raw material preparation: raw material grinding accounts for more than 30%, coal grinding station 3%, cement grinding station 40%, ensuring product quality Preheating and decomposition: the raw material is fully mixed with the hot gas discharged from the rotary kiln to reduce the heat consumption of the clinker800tph Cement Production line project in Shanxi
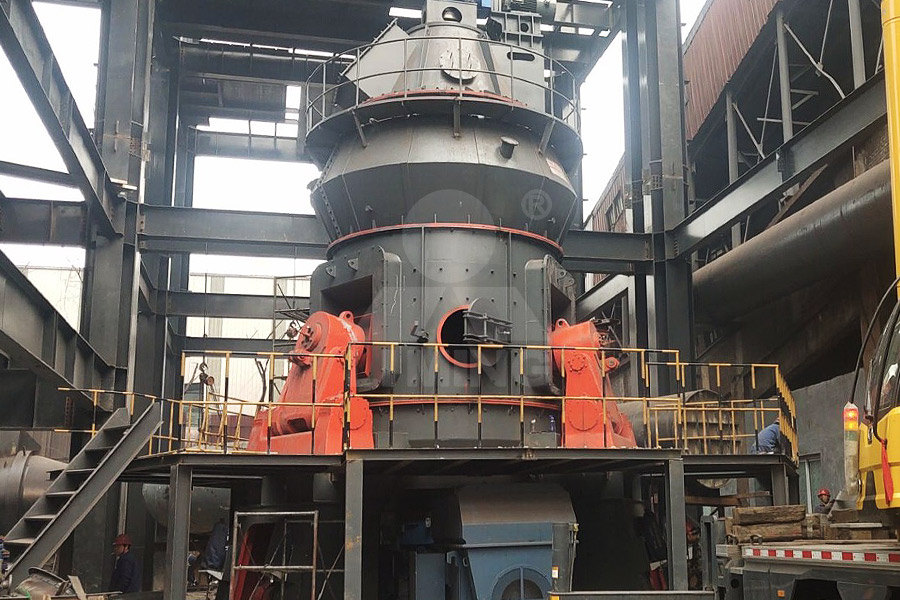
Ball Mill Roller Press for Cement Grinding Process
The grinding process consumes the most energy in cement production, its energy consumption accounts for more than 70% of the total power consumption in the whole process of cement production There are three main grinding processes in cement production: raw meal grinding, cement grinding, and raw coal grinding6000tpd Cement Production Line Project In Shandong; and appropriate gypsum AGICO CEMENT helps you get full knowledge of blast furnace slag cement and provides a one stop solution for your cement plant The core equipment of slag grinding plant is vertical cement millSlag Cement Production Line Blast Furnace Slag Cement Making300 t/d Cement Production Line 300t/d cement production line designed by Great Wall machinery, fully learns from the lessons and experiences of more than 20 years of NSP production line design, advanced vertical roller mill grinding system and DCS automatic control system; 3000 t/d Cement Production Line Xinxiang Great Wall Machinery provides turnkey basis service Cement Production Line2024年3月1日 We’ve found that our cement production articles are some of the highest viewed content on our blog site So, we’ve put together a list of our blog articles related to the cement production process and analysis Here are the top 15 of our most read cement articles, in no particular order:Everything about Cement Production Thermo Fisher Scientific
.jpg)
Gypsum : The Mineral of utmost necessity in Cement
India's cement production capacity stood at around 502 million tonnes per year (mtpa) in 2018 and is expected to reach 550 million tonnes by 2025 Typically manufacture of Cement uses 2 to 4 % gypsum is used per ton of Cement Thus the country requires to import substantial gypsum to cater to the requirements of Cement Industry The time allowed for mixing, transporting and placing plays a important role in strength, composition and workabilty of concrete As gypsum retards the process of hydration, it is termed as retarding agent of cement Effects of Gypsum on Role of Gypsum in Cement and its Effects – As a grinding medium, grinding balls are widely used in the grinding industry, such as concentrators, cement plants, thermal power plants, refractory material factories, etc In the Chinese market, about 4 million tons of steel balls are Grinding Ball Ball Mill Balls For Sale Ball Mill MediaThe dry process cement production line is widely used in cement industry it is generally divided into the following processes: prehomogenization of raw materials, homogenization of raw materials, clinker firing, cement grinding, and so on Get A free quote!Dry Process Of Cement Production 3005000TPD AGICO CEMENT
.jpg)
Cement Grinding Unit Clinker Grinder AGICO Cement
Cement grinding unit classifying, dust collecting and cement packing into a single It can not only grind cement clinker but also process cement admixture, such as gypsum, fly ash, furnace slag, coal gangue, etc, realizing a stable, highquality and automated cement production Unlike the cement production line, the cement grinding 2020年5月1日 This study was conducted to assess the effect of gypsum amount in cement in the production of selfcompacting concrete (SCC) It was found that, up to 15% replacement, the fresh properties of SCC (PDF) Effect of Gypsum Amount in Cement on Fresh and HardIt can be seen from above that in cement grinding process if the cement grinding temperature is not appropriately controlled the added gypsum would convert to hemihydrate It has been observed that when gypsum dehydrates completely to hemihydrate the cement shows false set due to rapid reaction of the high Hemi hydrate with hydration waterFEATURE Gypsum The role of gypsum in cementThe Portland cement manufacturing process can be divided into 6 steps: raw material crushing, prehomogenization, fine grinding, clinker production, cement grinding, cement packing, etc In these processes, we need the assistance of different kinds of cement equipment, such as cement kilns, cement mills, and cement crushersPortland Cement Manufacturing – Ordinary Portland Cement Production
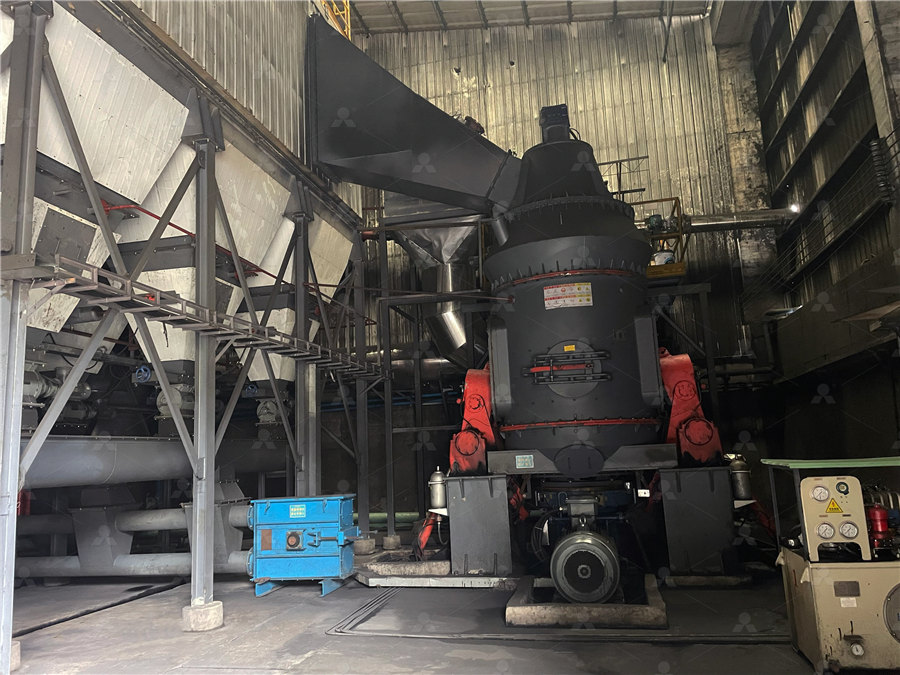
Separate grinding for higherperformance cements Cement Lime Gypsum
From now on, the Opterra cement plant in Karsdorf will be applying this new method to the production both of Portland limestone cements and an additional Portland composite cement For that purpose, the existing production line in the mixing tower will be joined by a second one costing roughly € 3 millionto produce PPC type of cement, (Clinker+Gypsum) to Produce OPC type of Cement, (Clinker+Gypsum+Limestone) to produce PLC type of cement, (Special clinker + Gypsum) to produce LHHS type of cement After grinding, the finished product (cement) is stored in cement silos ready for dispatch 8 Cement packing and DispatchCEMENT PRODUCTION AND QUALITY CONTROL