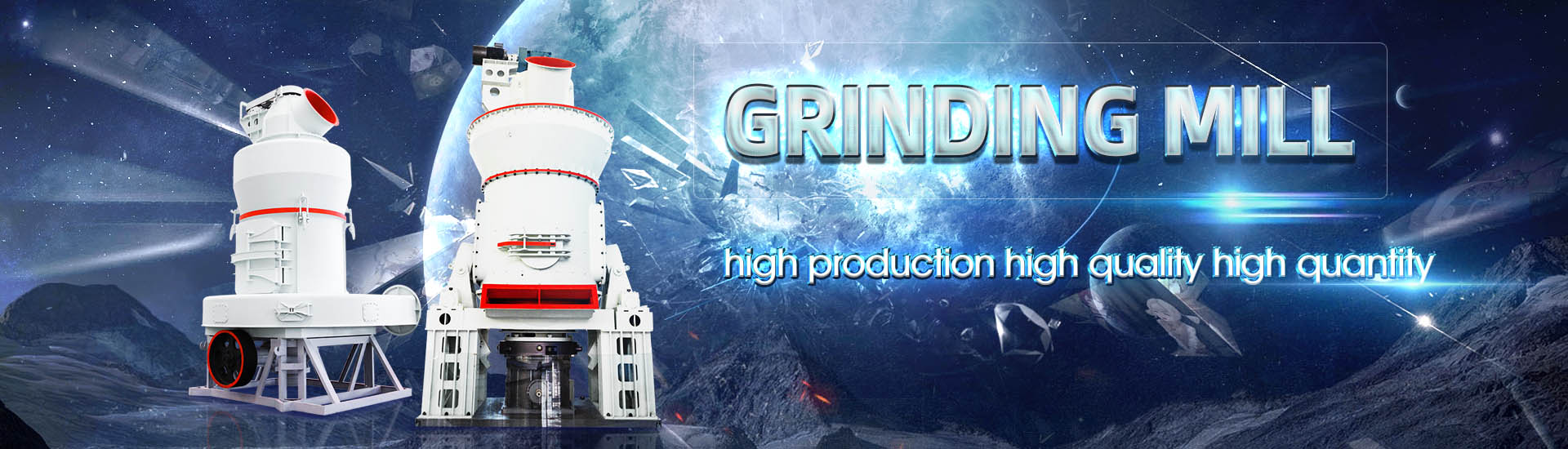
Roller mill process flow chart
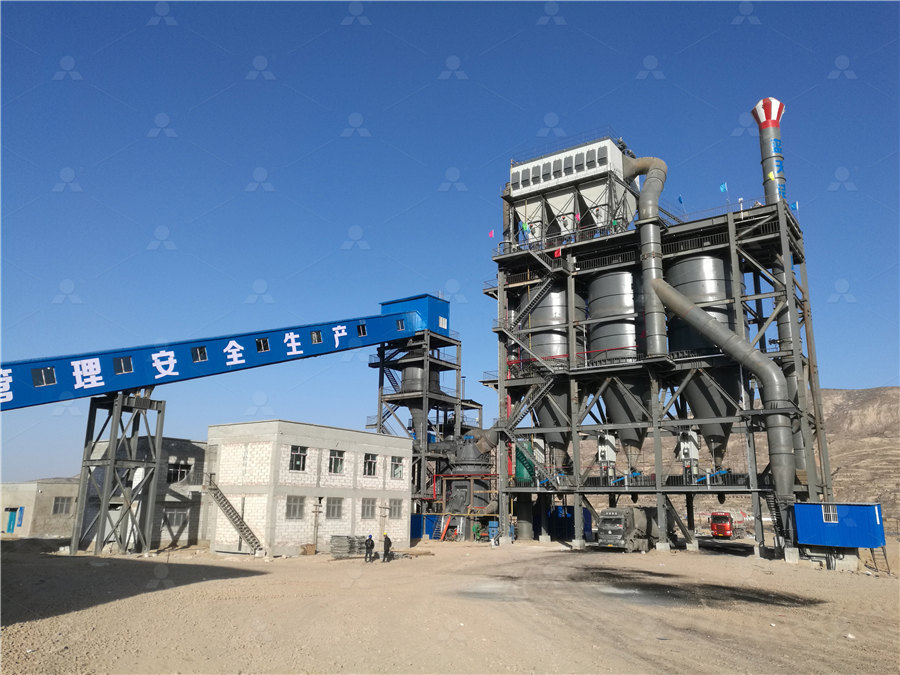
ROLLING AND STEPS IN ROLLING IDCOnline
Rolling Process can be classified either i)based on the temperature of the metal during rolling or ii) based on the arrangement of the rolls and their number orDownload scientific diagram Process flow chart of cold rolling mill2 from publication: Optimization of mechanical properties of high strength dual phase steel through thermomechanicalProcess flow chart of cold rolling mill2 ResearchGateFig Flow chart of roller mill adopting the external circulating system It depends on scale of facilities For example, about 820,000 US$ per unit At the beginning stage when vertical roller Vertical roller mill for raw Application p rocess materialsProduction flow chart of Rolling Mill II:CHINA STEEL The Flow Sheet of Rolling Mill
.jpg)
Process Flow Chart Stelco Limited
The Pickled coils are cold rolled on 4 Hi AGC cold rolling mill to obtain the required thickness and annealed in HSD fired belltype annealing furnace for bright annealing In case of medium and Modern cold mills process takes in hot band coils and roll and continue to make them thinner and have final thickness around 02 07 mm as shown in figure 4 Based on figure 4, firstly, theThe schematic of cold rolling mill process [8] ResearchGateRolling is the most important metal forming process More than 95% of ferrous and nonferrous metals and alloys are processed to their usable shapes by rolling Usable shapes of rolled Introduction to Rolling Process Cambridge University PressCold rolling speeds vary but modern mills operate at exit speeds as high as 3000 m per minute A modern complex including melting furnaces, DC casting facilities, preheat furnaces, hot mill, 1301 The Rolling of Aluminium: the Process and the Product
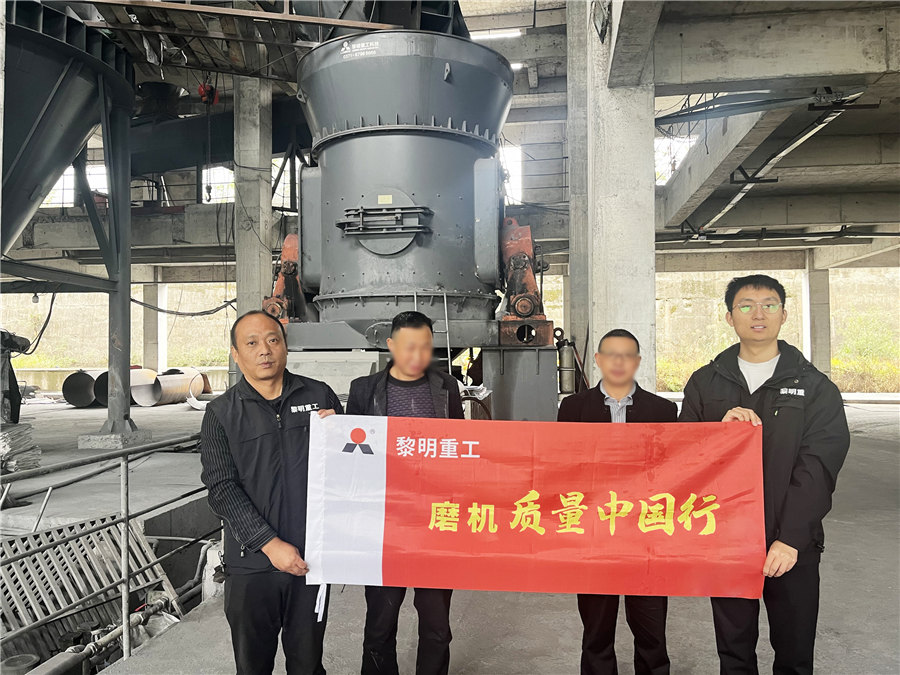
Rolling IIT Bombay
reversing rolling mill (shown below) with 750 mm diameter rolls made of tool steel is available for this task The rolling mill has a power capacity of 5 MW per roll The rolls rotate at a constant Summary: “Discusses the entire gamut of rolling process and the practices followed in rolling industry and operation and use of various rolling mill equipment and systems” Provided by Principles and Applications of Metal Rolling2019年5月20日 Whether called the mill flow diagram or flow chart, this document, is the first stage in the mill’s design stages and is a valuable tool to manage mill successfully The flow chart is a twodimensional road map of the Mill flow diagram, mill adjustment and mill balanceflow sheet? The length of a mill flow is determined by the linear inches or millimeters of roll length in the total process flow Sifter and purifier capacity is sized to support the grinding capacity of the mill The calculations for roll length, sifter surface, and purifier width are listed in Tables 1 and 2 (see Page 52)Flow Sheet Analysis Kansas State University
.jpg)
Roller flour mills at the Mills Archive – The Mills Archive
2017年5月12日 Milling flow charts show how grain moved through the roller mills and other machines in the mill They provide important evidence of the development of milling technology Tucked into the scrapbook was the chart for Sun Flour Mills: We also have the certificate given to Mr Cornwell on retirement:2015年12月3日 When setting the roll gaps for threading, it is critical that this factor be compensated for in each of the mill stands; to do so, sophisticated models are used by mill automation to estimate the rolling force for each transfer bar in each stand based on, among other things, the incoming and outgoing thickness, width, steel grade, and estimated instantaneous Rolling of steel in Hot Strip Mill – IspatGuruFlow chart of the verticalrollermill grinding system 1—Material silo; 2—Vertical roller mill; 3 Feed into flotation Ball mill Fig 4 Flow chart of the ballgrinding test process Magnesite samples × 3 min, collector × 3 min, frother × × × 3 min, regulator 3 Research on new beneficiation process of lowgrade magnesite • Rapid process dynamics are a challenge to operating a vertical roller mill (VRM) • Surpasses the classic methods if the controlled process demonstrates significant disturbances • A high degree of attention to the process states is required in order to make punctual corrections • Process states are displayed and controlled continuPROCESS OPTIMISATION FOR LOESCHE GRINDING PLANTS
.jpg)
Process Flow Chart Stelco Limited
The Pickled coils are cold rolled on 4 Hi AGC cold rolling mill to obtain the required thickness and annealed in HSD fired belltype annealing furnace for bright annealing PHYSICAL PROPERTIES APPLICATIONS PROCESS FLOW CHART About us Stelco was established in the year 1991 for manufacturing of medium carbon, high carbon and Download scientific diagram Process flow chart of cold rolling mill2 from publication: Optimization of mechanical properties of high strength dual phase steel through thermomechanical Process flow chart of cold rolling mill2 ResearchGaterugged ringroll mill manufactured today The roller mill provides the needed flexibility to economically and efficiently process a wide variety of materials ROLLER MILL SYSTEM The typical Raymond roller mill system is designed to dry, pulverize, classify and deliver a number of different products COST EFFICIENCY The Raymond roller mill RAYMOND® ROLLER MILLS Thomasnet2015年9月20日 Roller printing also referred to as intaglio or machine printing The technique dates from the end of the 18 th century (Scotland: James Bell) and has resulted in the disappearance of hand printing, which is a timeconsuming printing technique The technique of roller printing is especially used for very large batches but faces great competition from rotary Flow Chart for Roller Printing Process Textile Flowchart
.jpg)
Fundamentals of Roll Cooling and Control of Flatness at Lechler
In the process of Rolling the most significant aspect is the generation of heat through friction and deformation in the roll bite and in a typical Cold Tandem Mill, work roll temperatures normally fall in the range of 55oC – 70oC with strip recoil temperatures and interstand strip temperature rarely exceeding 160 oC depending on productDownload scientific diagram Flow chart of the complete rice milling process from publication: Development of Existing Engelberg Rice Mill for Improving Milling Yield and Quality The majority Flow chart of the complete rice milling process2007年1月1日 This chapter describes how the flour milling process interacts with the wheat kernel structure to separate it into its functional components It traces briefly the historical development of flour milling technology leading to the introduction of roller mills a century ago, introducing the themes of wheat hardness, bread quality and the international grain trade that Chapter 7 Roller Milling of Wheat ScienceDirectNational Highway NH7 at Bathinda Road, Rampura Phul, Distt Bathinda (Punjab) India Mr GAURAV JINDAL +919876021701 +911651Process Flow Chart Stelco Limited
.jpg)
The schematic of cold rolling mill process [8] ResearchGate
The schematic of cold rolling mill process [8] Modern cold mills process takes in hot band coils and roll and continue to make them thinner and have final thickness around 02 07 mm as Roller milling is one of many methods used to produce flour It's a process used to separate the anatomical parts of grain kernels—like the bran, and RA Flores “Moisture, Ash and Protein Flow Rate Study in a Wheat Flour Pilot Mill Using Simulation Models” Institution of Chemical Engineers (IChemE), Volume 81, Part C, 2003, Roller Milling Baking Processes BAKERpedia2017年5月3日 Flow Chart of Cold Rolling Mill Step 1: Annealing soften mother tube; Step 2: Acid cleaning to get rid of oxide scale on inner surface and outer surface;Cold Rolling Mill Process Flow Chart Suzhou Senbo Machinery The pelleting process starts with a bin (Figure 1, Item 1) in which the mixture of mash is stored From there, the mash will flow by gravity into the pellet mill (Figure 1, Item 2) This machine is usually located on the ground or main work floor level The hot, extruded mash (pellets) flows by gravity into a cooler (FigureThe Pelleting Process CPM
.jpg)
Commercial rice milling systems IRRI Rice Knowledge Bank
The flow diagram below represents the configuration and flow in a typical modern rice mill (using the IRRI rice mill as an example) Description of flow of materials and processes 1 – paddy is dumped in the intake pit feeding the precleaner A – straw, chaff and empty grains are removed 2 – precleaned paddy moves to the rubber roll husker:2 Principles and Applications of Metal Rolling (ii) Shape of the rolled product flat, sections or hollow sections rolling (iii) Direction of rolling lengthwise, transverse, and skew rolling (iv) Mode of rolling mill operation continuous (unidirectional), and reverse rolling, where direction of rotation of rolls are reversed When two rolls of equal diameter and with axis lying in same Introduction to Rolling Process Cambridge University Pressroller mill tests of your material in the manufacturer’s test facility with various roll corrugation styles and under conditions that duplicate your operating environment Figure 1 Particle size distributions: Roller mill versus other grinding methods Other grinding methods Roller mill Overs Target particle size Fines Figure 2Roller mills: Precisely reducing particle size with greater efficiencyTemper Mill (both Stands) 510 mm ~ 560 mm Pinion Stand 15 : 1 (2inputs, 2outputs) Double Red Mill (Stand #1) 360 mm ~ 400 mm Mill Speed 0 / 557 / 1500 mpm (Stand #2) 510 mm ~ 560 mm Exit SBridle Rolls (2 rolls) Backup Roll Diameter: Roll Diameter 510 mm For both Temper DR mill 1,140 mm ~ 1250 mm Drive Motor #1 450 kW @ 936 rpmCold Rolling Mill Tenova
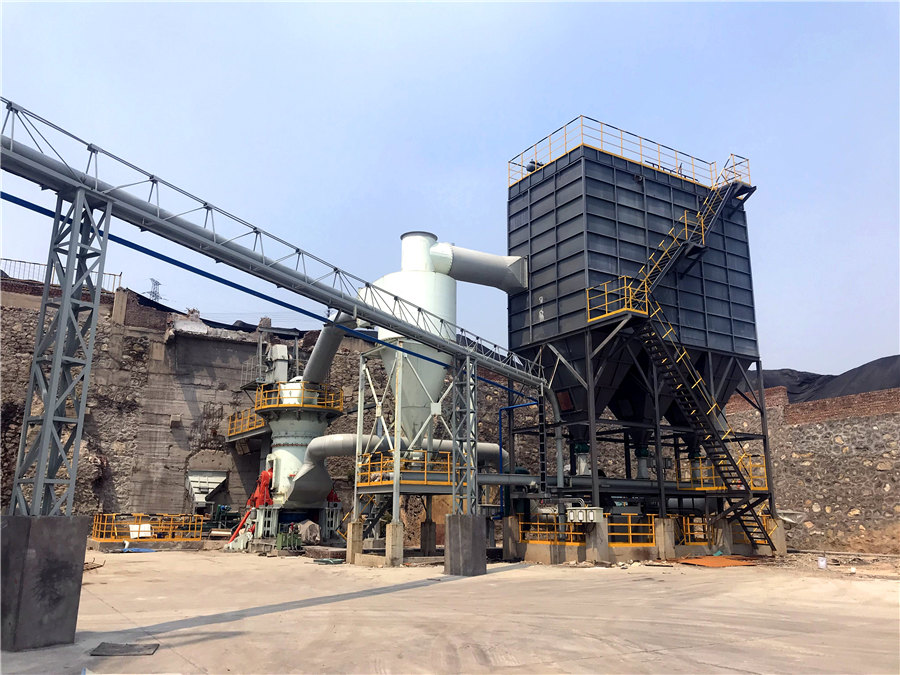
Seamless Pipe Manufacturing Process
The cross roll piercing and pilger rolling process in the size range from approx 250 to 660 mm outside diameter Mandrel Mill Process In the Mandrel Mill Process, a solid round The production flow video shows the transformation The rolling mill is adequate if the required power for the operation is less than or equal to the available power Power required per roll, 60000 FLN P roll p ¢ = kW Roll separating force, ( ) ÷ ÷ ø ö ç ç è æ ÷÷ + ø ö çç è æ = avg avg f h L F Lw Y 2 1 3 2 µ L= RDh= (0375)(0075006)=0075 m 00675 2 0075 006 = + h avg = m Rolling IIT Bombay2019年10月21日 Berst in class flour mill flour mill with best design and functions combined together We mainly engage in 101000ton/d wheat flour mill plant, 10200ton/d maize/corn flour mill plant, and other grain processing machines We also supply all the flour mill machines which can be used in complete flour mill plant GET A FEE PRICING ESTIMATIONflour mill flow chart Flour Mill Machine Flour Mill Price2013年12月22日 Fig 6 Work roll bending and shifting of geometric shaped rolls Roll shifting technology – Different roll shift shape control technologies have been developed These technologies basically consist of (i) a method by which the shape control effect can be improved by shifting rolls, reducing the contact portion between rolls outside the strip width and as a Development of Modern Hot Strip mill and its Main Features
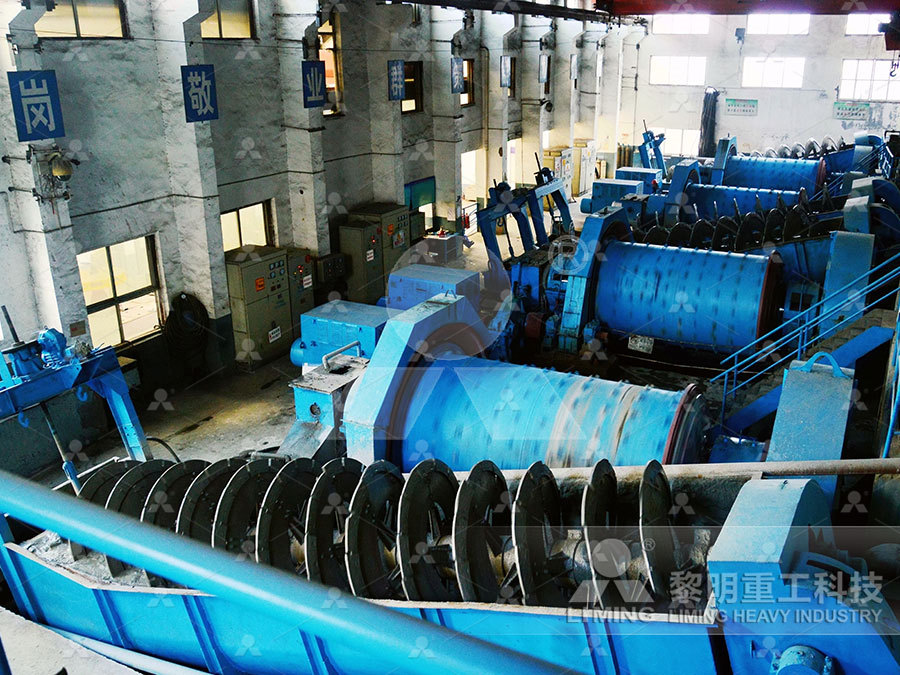
PM FME‐ Detailed Project Report of Wheat Flour Mill Unit
PM FME‐ Detailed Project Report of Wheat Flour Mill Unit 3 TABLE OF CONTENTS S No Topic Page Number 1 Project Summary 3 2 About the Product 46 3 Process Flow Chart 710 4 Economics of the Project 1026 41 Basis Presumptions 1011 42 Capacity , Utilisation, Production Output 1112 43 Premises/Infrastructure 12 444223 Milling / Separation of flour Objective of wheat milling is to separate the branny cover and germ of the wheat kernel from the endosperm Fig 41 Wheat flour milling is a process that consists of controlled breaking, reduction and separation, Food TechnologyII: Lesson 4 MILLING OF WHEAT eKrishi ShikshaThis process stretches a slab into a strip The slab is reheated to approximately 1250°C and rolled in hot conditions The resultant strip steel is wound into a roll like toilet paper (hot coil) Chains for lifting; Toughrollers; Conveyor chains for conveying semifinished productsHot Strip Mill and Cold Rolling Mill Industry Application PROCESS MACHINERY REQUIREMENT Flow Chart: Machine Description Machine Image Emery Roll Dehusker: It’sa machine which utilizes emery rollers to remove outer skin of pulses The pulse or grain is simply pressed inbetween emery rollers to break otter shell to liberate inner Endosperm Classifier SeparatorPROCESSING OF DAL MILL NIFTEM
.jpg)
Using the eightroller mill in the purifierless mill flow
2014年12月20日 Baltensperger W (1993) New development in the mill flow charts grinding process using eightroller mills Assoc Oper MillersBull (December):6327–6332 Baltensperger W (1997) Particle size of semolinas for pasta production Assoc Oper MillersBull (March):6879–6884 Baltensperger W (2001) Stateoftheart grain milling technology2011年8月2日 5 Combing Process: Combing is an optional step in fibre production and is used when a smoother, finer yarn is required Combing allows the production of very fine, highquality spun yarns In this operation, fine Process Flow Chart of Yarn Spinning Technology2014年12月20日 Baltensperger W (1993) New development in the mill flow charts grinding process using eightroller mills Assoc Oper MillersBull (December):6327–6332; Baltensperger W (1997) Particle size of semolinas for pasta production Assoc Oper MillersBull (March):6879–6884; Baltensperger W (2001) Stateoftheart grain milling technologyUsing the eightroller mill in the purifierless mill flowGood milling is all about the process how to reliably separate impurities from grain and then separate the different pieces that make up the grain This helps to improve your yield and quality of your product Automation and digital services can also help to get the most out of your mill and increase food safety and traceabilityWheat Milling Grain Processing Bühler Group
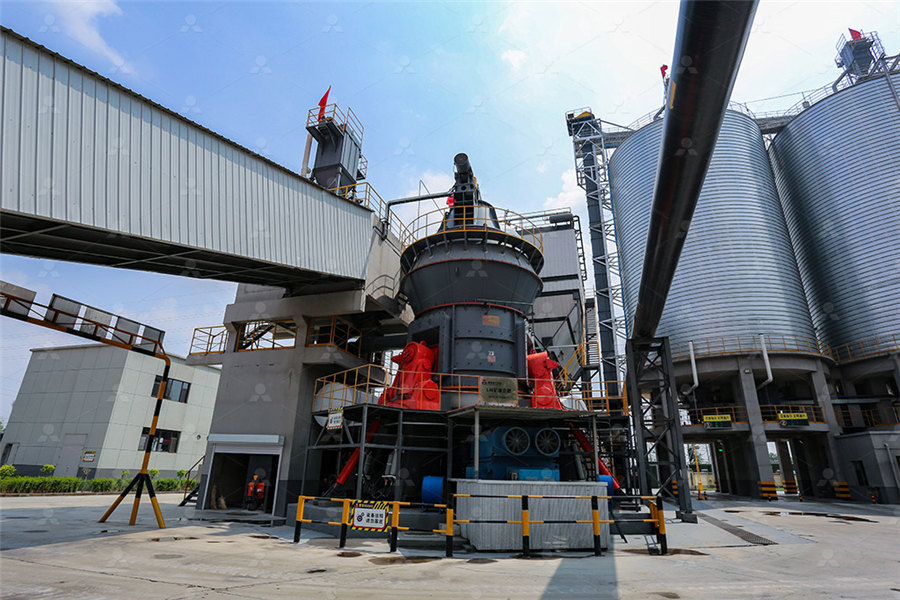
GENERAL ASPECTS OF ROLL COOLING FOR HOT COLD
rolling mill, dedicated roll cooling systems are required to fulfill the flow, cooling, selective roll cooling, profile and flatness, rolls, lubrication, surface temperature, water distribution, plateout Thermal aspects of rolling The plastic deformation of steel during the rolling process generates heat, which is absorbed by the Engleberg mill has led some governments to discourage its use and in many Asian countries, the Engleberg mills can no longer be licensed to operate as service or commercial mills 32 Two Stage Milling Compact Mill Two stage mills are often called compact rice mills and in many countries have superseded the Engleberg mill The twostage millRice Milling Manual International Rice Research Institute2023年7月13日 In the process of making paper, manufacturers treat raw materials like wood fiber and recycled fiber mechanically and chemically to produce paper products The process of making paper has steps like preparing the raw materials, pulping, refining, screening, pressing, drying, and finishing, which improves the paper’s properties and final productPaper Making Process: From Raw Materials to Finished ProductsSpinning is the process, which is used in the production of yarns or filament from fiber or from the chemical compound Spinning is the first step to produce a textile product such as fabric, garments, home textile etc In a spinning industry, several processes are done to produce yarn Process flow chart of carded yarn Spinning flow chart of carded yarnProcess flow chart of Spinning Process flow chart of carded
.jpg)
The Complete Book on Rubber Processing and Compounding
The Complete Book on Rubber Processing and Compounding Technology Author: NIIR Board of Consultants and Engineers Format: Paperback ISBN: Code: NI174 Pages: 712 Price: Rs 1,27500 US$ 12500 Published: 2006 Publisher: Asia Pacific Business Press Inc Usually ships within 5 days Rubber products industry is an important resource based industry Roller mill tangential abrasive dehulling device (TADD) is one of the several dehusking devices available in the market Roller The process flow chart involved in the wet and dry milling process is shown in Figs 112 and 113, respectively Fig 112 Flow chart of wet milling (illustrated as per [25, 26]) Full size image Fig 113Processing of Pulses SpringerLink