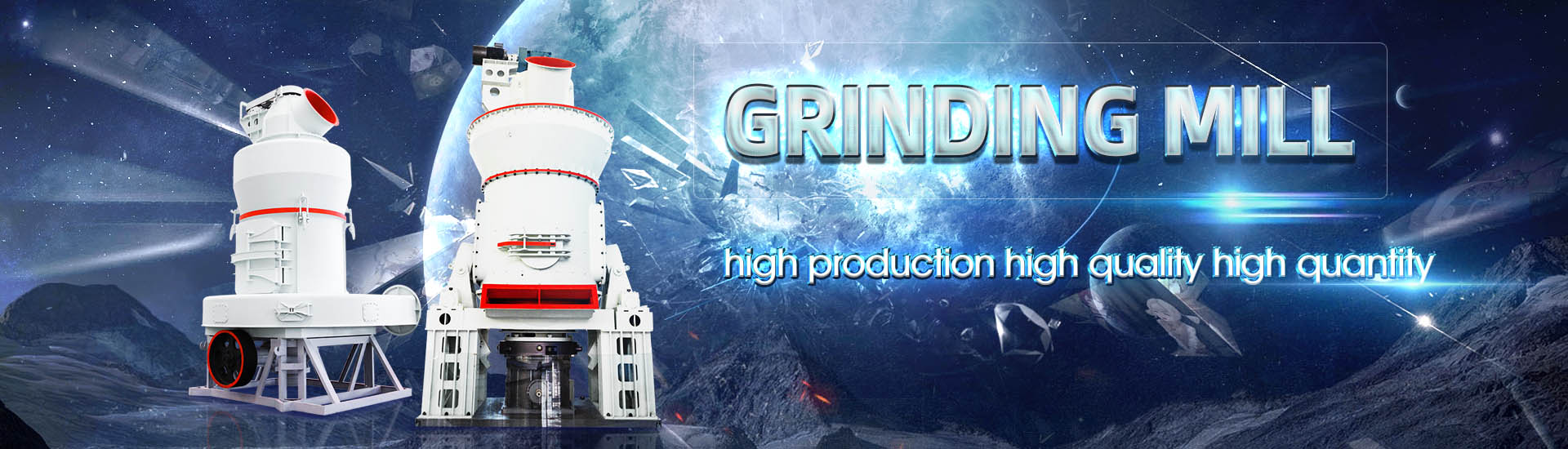
Noise reduction measures and working principles of vertical ore mill
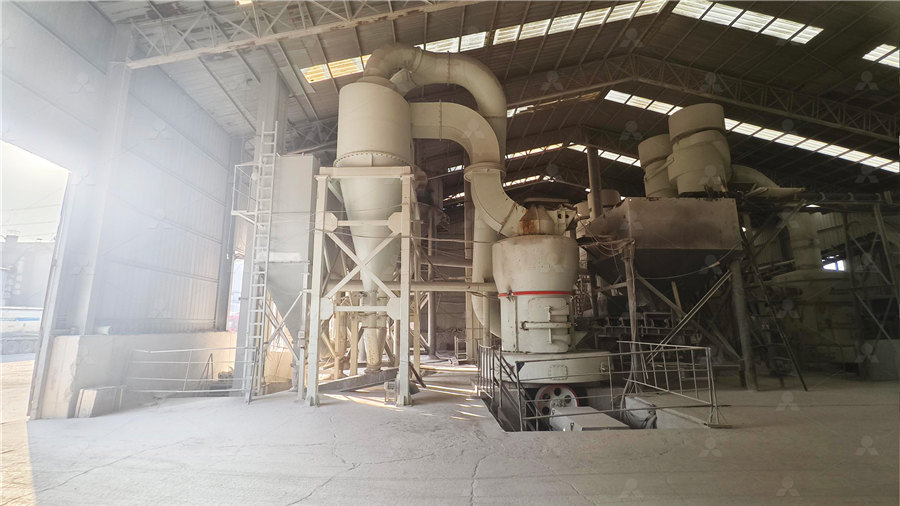
Vertical Roller Mills used for the comminution of mineral ores
Vertical roller mill (VRM) is an established technology in cement and slag grinding applications and Boliden and Gebr Pfeiffer have been collaborating on the application of this technology in the minerals processing industry In such an application a VRM would function as the milling stage 2017年4月1日 In this study, pilot scale tests were performed with a mobile verticalrollermill grinding plant to investigate the relationships between operational parameters The Operational parameters affecting the vertical roller mill Vertical roller mills are adopted in 20 cement plants (44 mills) in Japan In the vertical roller mill which is widely used in the raw material grinding process, raw materials input grinding table Vertical roller mill for raw Application p rocess materials2019年4月16日 The paper demonstrates why the Loesche VerticalRollerMill (VRM) is a serious alternative to conventional grinding technologies and where the limitations of the system are (PDF) LEARNING FROM OTHER INDUSTRIES; WHY THE VRM
.jpg)
Operational parameters affecting the vertical roller mill
2017年4月1日 Pilot plant test results with various ores showed that low energy consumption feature of vertical roller mills is applicable to the ore industry Grinding test results for zinc ore Vertical stirred milling is a wellrecognized technology for the secondary, regrind and fine grinding applications and are increasingly replacing coarser ball mill applications in secondary and RECENT DEVELOPMENTS IN COARSE GRINDING USING VERTICAL 2015年3月15日 Verticalrollermills (VRM) are an energyefficient alternative to conventional grinding technology One reason is the dry inbed grinding principle Results of extensive test Research of iron ore grinding in a verticalrollermill2022年1月23日 This work concentrates on the energy consumption and grinding energy efficiency of a laboratory vertical roller mill (VRM) under various operating parameters For Analysis and Optimization of Grinding Performance of Vertical
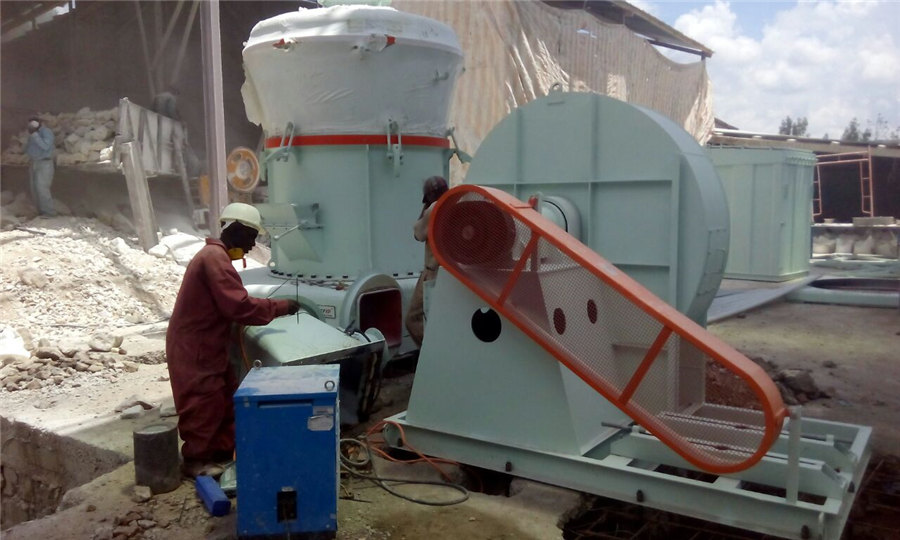
Research of iron ore grinding in a verticalrollermill
2015年3月15日 We investigated whether the vertical roller mill can be efficiently used in the beneficiation of lowgrade magnesite and whether it can improve upon the separation indices 2012年9月1日 The paper is giving an overview about successful operating Loesche Vertical ? Roller ? Mills (VRM) installations and summarises the main benefits of the dry compressive Latest Installations And Developments Of Loesche Vertical Roller leads to lower noise level (4) This type of mill can crush materials which are too large to be fed into the tube (ball) (Reduction) Mill and Separator 89 77 Mill Fan 105 57 50% (Reduction) Kiln IDF Fig1 Flow of Conventional Vertical Mill Grinding System Mill Kiln IDF (Kiln gas exhaust fan)Vertical roller mill for raw Application p rocess materials2022年8月29日 Hammer mill is a size reduction equipment where stresses of varied nature are applied to achieve size reduction Working of Hammer Mill: A pH meter is an instrument used to measure the activity Abhishek Kumar Hammer Mill – Principle, Construction, Working, and
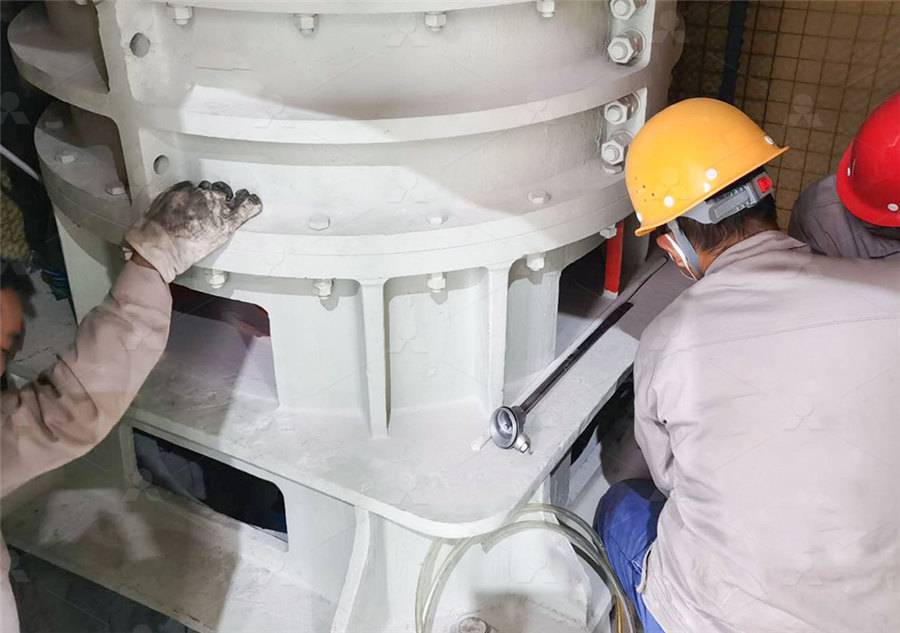
Operational parameters affecting the vertical roller mill
Request PDF On Sep 1, 2016, Deniz Altun and others published Operational parameters affecting the vertical roller mill performance Find, read and cite all the research you need on ResearchGate2022年5月4日 Noise control refers to a set of methods, techniques, and technologies that allows obtaining acceptable noise levels in a given place, according to economic and operational considerationsOverview of Noise Control Techniques and Methods ResearchGate2023年12月12日 In addition, the ore properties are one of the important parameters for the optimal utilizing of the ball mill Ore can have various properties, such as hardness, density, moisture content, etc (PDF) Control of ball mill operation depending on ball load and ore 2024年1月28日 2 Liners: An abrasionresistant material such as manganese steel or rubber typically lines the inner surface of the cylindrical shell to protect it from wear due to the grinding action 3 Balls: They place steel or ceramic balls, typically used as grinding media in a ball mill, inside the shell and rotate them with it 4 Feed and Discharge: Entering the hollow shell at the Ball mill: Principles, construction, working, uses, merits, and
.jpg)
Noise in the Mining Work Environment Causes, Effects and Threats
2020年12月16日 According to the reports, the European Agency for Safety and Health at Work, millions of employees in Europe are exposed daily to industrial noise and all risks associated with itREVERSING ROUGHING MILL WIDTH REDUCTION: Slab width is reduced up to two inches with the vertical edging rolls (squeeze) THICKNESS REDUCTION: Roughing mill reduces slab thickness in five (5) to seven (7) reversing passes down to 1125” (transfer bar) DESCALING: High pressure descale water on entry side of mill removesPrinciples of Hot Rolling AIST2024年1月28日 2 Base Stone: A stationary flat surface against which the material is crushed It provides support for the runner stone and helps create the grinding action 3 Vertical Shaft: A drive mechanism imparts rotational motion to the vertical shaft, which is connected to the mounted runner stone 4 Feed Mechanism: Feeding the material to be ground between the rotating Edge Runner Mill: Principles, construction, working, uses, merits, 2024年4月16日 The figure shows an end runner mill in construction An end runner mill can be thought of as an intermediate mill The mortar consists of a steel plate flanged to a steel mortar The horizontal shaft bearing the pulley is attached to a beveled cog fitting below the flanged plate A high rotational speed is thus possible with the plate with mortarEdge Runner Mill Pharmaguideline
.jpg)
(PDF) LEARNING FROM OTHER INDUSTRIES; WHY THE
2019年4月16日 Vertical roller mills (VRM) have been used extensively for comminuting both cement raw materials and minerals like limestone, clinker, phosphate, manganese, magnesite, feldspar and titanium2015年3月10日 The vertical roller mill equipped with an internal classifier is often said to be more energy efficient than tumbling mills working on the same material and the same size step (eg Gerold et al, 2012) It is long established in the cement industry and gains more and more importance in the industrial mineral and iron ore sectorsAn energy based comparison of vertical roller mills and 2014年10月1日 In a test performed in the Loesche test center in Germany, copper slag grinding saved 229% energy in an airswept model and 344% energy in an overflow model [13,14]Copper Ore Grinding in a Mobile Vertical Roller Mill Pilot Plant2022年10月1日 This study investigated a mathematical model for an industrialscale vertical roller mill(VRM) at the Ilam Cement Plant in Iran The model was calibrated using the initial survey's data, and the (PDF) A cement Vertical Roller Mill modeling based on
.jpg)
Reduction of Fragment Size from Mining to Mineral Processing: A
2022年10月4日 A notable fact is that the energy efficiency of conventional milling is only about 1%, as mentioned in Sect 1 An earlier experimental study indicated that about 80–90% of the energy input of a ball mill was used in heating the material (Schellinger 1951, 1952), and a recent study showed that over 75% of the electrical energy was used to heat the slurry (Bouchard et 2021年11月26日 Solutions of Ball Mill Noise Reduction Ball mill operators are exposed to a noisy working environment for a long time, which seriously endangers their health Therefore, it is very important to use various control techniques to reduce the noise of the ball mill, and the following are several common solutions to deal with noise 1Causes and Solutions of Ball Mill Noise MiningpediaFind your ore mill easily amongst the 42 products from the leading brands (Fritsch GmbH, Retsch, Eriez, Ideal for large quantities The Planetary Mill PULVERISETTE 5 classic line with 4 working stations delivers fast and reliable, The POITTEMILL pendulum roller mill is a vertical mill that works by compressing the material bedOre mill, Ore grinding mill All industrial manufacturers2022年1月23日 This work concentrates on the energy consumption and grinding energy efficiency of a laboratory vertical roller mill (VRM) under various operating parameters For design of experiments (DOE), the response surface method (RSM) was employed with the VRM experiments to systematically investigate the influence of operating parameters on the energy Analysis and Optimization of Grinding Performance of Vertical
.jpg)
Beneficiation of Gold and Silver Ores SpringerLink
2019年12月15日 429 VertiMills Vertical mills were first designed in the 1950s for applications in fine and ultrafine grinding in Japan Lately, the vertical mill is making progress toward primary grind application and shown promise in energy reduction relative to ball mills, typical to what is normally seen in regrinding applications (Mazzinghy et al 2014)2024年4月16日 Ball Mill Principles Ball mills, sometimes referred to as pebble mills or tumbling mills, are milling machines that take the form of cylindrical vessels containing balls mounted on a metallic frame that can revolve around its longitudinal axis Depending on the feed and mill size, balls with varying diameters occupy 30 50 % of the mill volumeFluid energy mill PharmaguidelineThe rod mill is another type of grinding mill used in the copper ore mining process This machine uses steel rods as the grinding media instead of balls, which are commonly used in ball mills The rods grind the ore by tumbling Understanding the SAG Mill in Copper Ore Mining 2023年2月23日 Francis, B Scaleup and Operations of a Vertical Stirred Mill, Master’s Thesis, The University of British Columbia, Vancouver, BC, Canada, 2014 Minerals 2023 , 13 , 315 16 of 16(PDF) Performance Comparison of the Vertical and
.jpg)
RECENT DEVELOPMENTS IN COARSE GRINDING USING VERTICAL
Pilot test work was carried out by Mazzinghy et al (2015) on a batch ball mill and pilot scale vertical mill to assess the energy efficiency factor The results shows that the scaling factor of 135 was required to adjust the ball mill energyspecific breakage rates to match the breakage rates in a vertical mill The vertical mill2021年1月29日 Objective of this research paper is process optimization of Vertical roller mill, improvement in productivity and reduction in vibration breakdowns using seven QC toolsIncrease productivity of vertical roller mill using seven QC tools2023年12月22日 The vibration problem is the key factor that restricts the stabilization and working performance of the precision cold rolling mill As the sheet thickness becomes thinner and the rolling speed increases, the abnormal vibration that occurs in the cold rolling mill becomes more serious and frequent [1, 2]Variations in system parameters can induce changes in the Vertical nonlinear vibration analysis of cold rolling mill 2019年12月4日 Nowadays, each individual is exposed to noise on a daily basis, and noise is often referred as in literature as a plague of modern society Noise pollution is often overlooked when compared to other environmental pollutions (eg air, water, soil pollution) However, same as the all aforementioned pollutions, noise exposure has an accumulating character, meaning Innovative Approaches to Noise Reduction IntechOpen
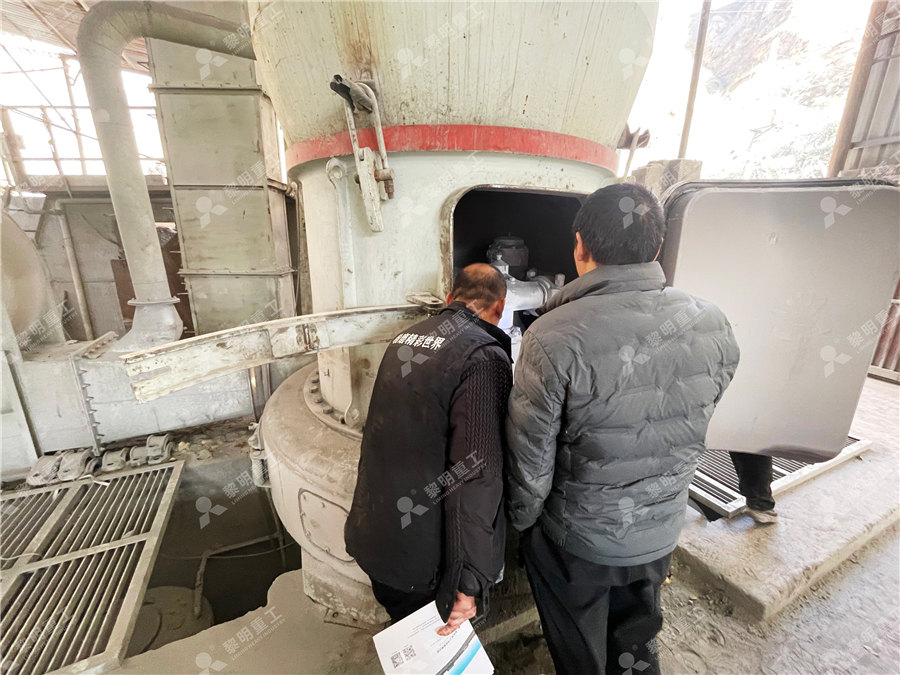
Analysis of vertical roller mill performance with changes in
2022年5月31日 Mineral crushing is the main source of energy consumption in mineral processing According to statistics, this consumption accounts for about 35–50% of the total cost of the mine (Curry et al, 2014), or even higherIt may also account for 18% of the global electrical energy consumption (NapierMunn, 2015)More efficient crushing equipment needs to be 2016年9月1日 Noise reduction today is still fairly experience based, which requires generating a good understanding of noise generation, noise transmission and noise radiation and is discussed in this paperReduction of noise during milling operations ResearchGateThe basic structure of the roller mill includes the grinding roller, the grinding body, the force generation and transmission mechanism, airflow, and the device for easy replacement It can be divided into vertical roller mill, horizontal cylinderrollermill,highpressurerollermill,Raymond mill, and column mill Vertical Roller MillRoller Mill Springer2016年3月30日 In book: Encyclopedia of Iron, Steel, and Their Alloys (pppp 10821108) Chapter: i) Direct Reduced Iron: Production; Publisher: CRC Press, Taylor and Francis Group, New York(PDF) i) Direct Reduced Iron: Production ResearchGate
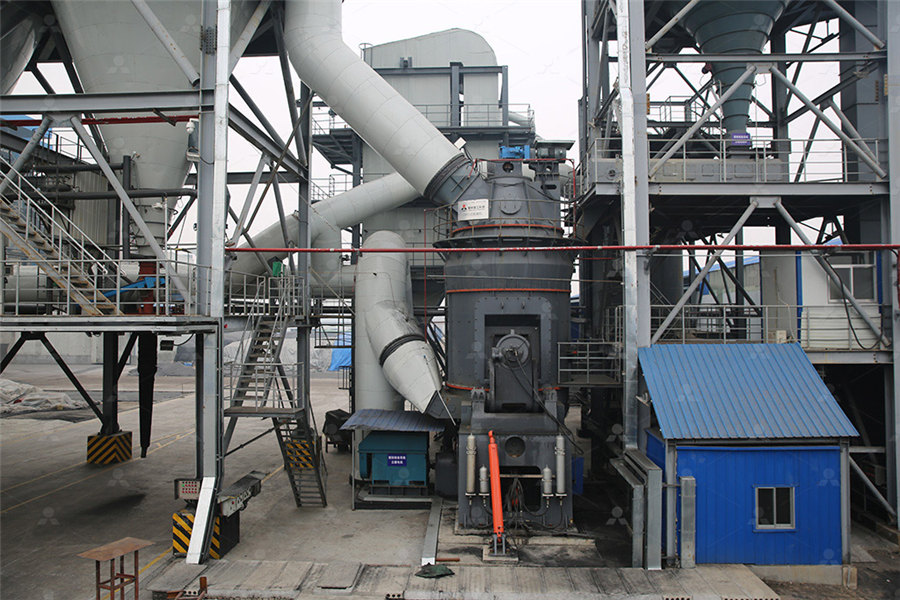
DeepL翻译:全世界最准确的翻译 DeepL Translate
即时翻译文本完整的文档文件。为个人和团队提供准确的翻译。每天有数百万人使用DeepL进行翻译。2014年11月1日 In this study, a coarse sample of iron ore was tested in a pilot scale grinding circuit with a vertical mill Other three samples of pellet feed had already been tested with the methodology used Vertical mill simulation applied to iron oresAmong our working principles – the sort of thing that has helped to drive new thinking in vertical mill technologies for the mining sector – are being responsible and customerfocused For us, this means having integrity with strong values while understanding that it is our customers who drive everything we doVertical Mill Mining MagotteauxOverview of Noise Control Techniques and Methods Alice Elizabeth González Abstract Noise control refers to a set of methods, techniques, and technologies that allows obtaining acceptable noise levels in a given place, according to economic and operational considerations The question of “acceptance” is for what or for whom GenerChapter Overview of Noise Control Techniques and Methods
.jpg)
Design and Evaluation of Crushing Hammer mill ResearchGate
2019年1月1日 A grain size reduction hammer mill for crushing corn (Zea mays L) was designed depending on variety characteristics and by using computer aided design “ANSYS” software2022年6月24日 Comprehensive comparison, the advanced grinding technology of vertical mill can overcome many defects of ball mill The vertical grinding mill has the advantages of high grinding efficiency, low power consumption, simple grinding process, small footprint, low civil construction cost, low noise, low wear, long life and easy operationHow to choose between ball mill and vertical roller mill?2019年10月17日 In this post, we're going to learn more about rod mill We'll cover it from two aspects: 1 Working principle 2 Structure Let's dive right in! 1 Working Principle of Rod Mill Rod mill is a common equipment for grinding operation in mineral concentrator, which is mainly suitable for rough grinding operationThe Working Principle and Structure of Rod Mill2022年11月30日 Disadvantages of Endrunner mill and Edgerunner mill 1 It is not suitable for milling sticky materials 2 Machine noise leading to noise pollution References Sud Sushant and Kamath Archana (2013) Methods of Size Reduction and Factors Affecting Size Reduction in Pharmaceutics International Research Journal of Pharmacy 4(8): 5764Endrunner mill and Edgerunner mill: Operating principles, Uses
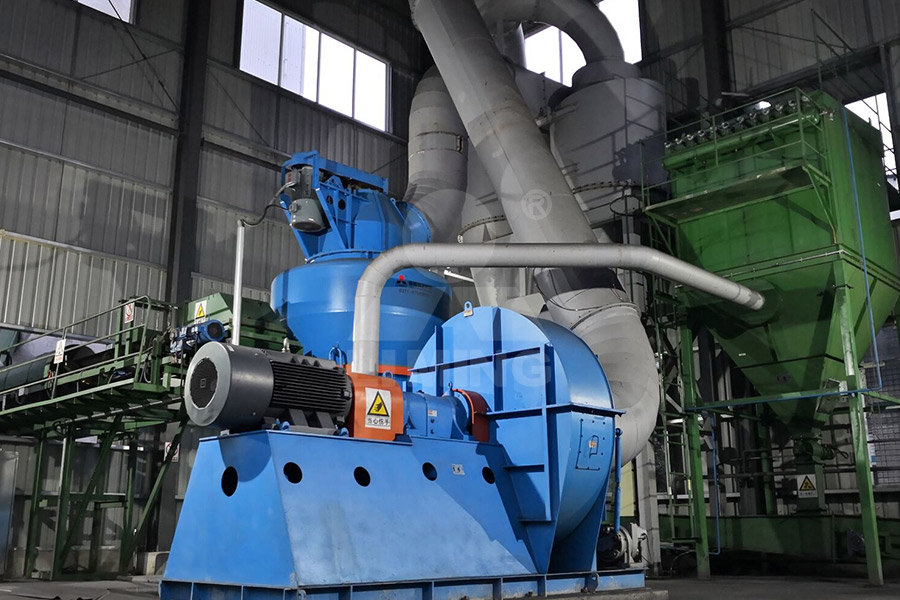
Detection of Malfunctions and Abnormal Working Conditions of a Coal Mill
2018年5月2日 Coal mill malfunctions are some of the most common causes of failing to keep the power plant crucial operating parameters or even unplanned power plant shutdowns Therefore, an algorithm has been developed that enable online detection of abnormal conditions and malfunctions of an operating mill Based on calculated diagnostic signals and defined 2014年10月20日 Rio Paracatu regrind circuit Santos Júnior et al (2011) presented some data on the Paracatu Vertical Mill circuit process, as well as its comparison to the plant's conventional ball millRegrind of metallic ores with vertical mills: An overview of the