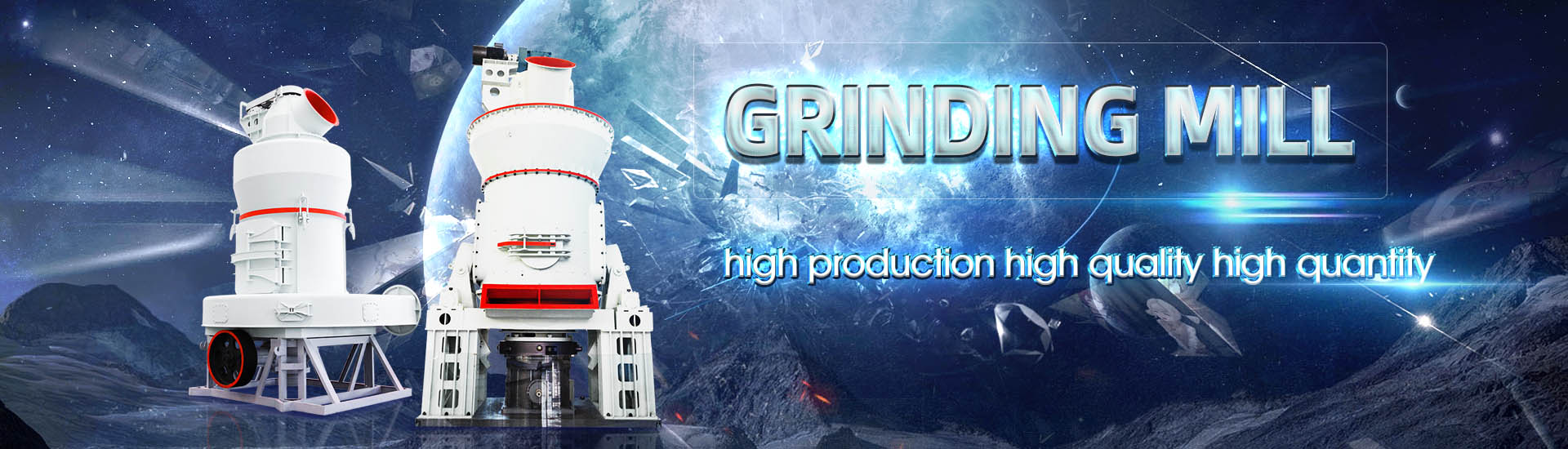
Micro powder unit standard cleaning procedures
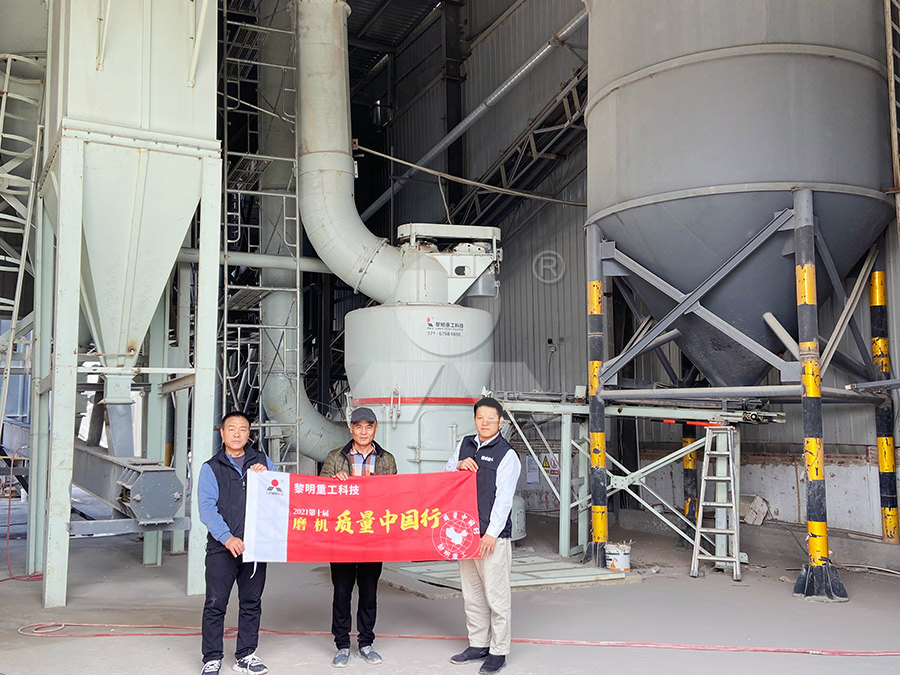
Microbiological Aspects of Cleaning Validation Pharmig
Cleaning validation methodology applied to give the assurance that a cleaning process has removed residues and contaminants from a piece of equipment or machinery Residues: •Microorganisms •Active pharmaceutical ingredients •Other process chemicals, such as 2024年4月17日 Standard operating procedure of LAF chamber unit cleaning, filter cleaning and frequency of cleaning and calibration that is used to maintain the area for microbial analysis in SOP for Laminar Air Flow Unit PharmaguidelineTo define the requirements for cleaning plant and equipment used to manufacture active pharmaceutical ingredients (APIs) or their intermediates To give guidance on how to assure Manual 038 Cleaning and Cleaning Validation of API Plant and 2021年6月29日 It provides guidance on cleaning validation It will help you understand and comply with Part C, Division 2 of the Food and Drug Regulations (the Regulations) This guide Cleaning validation guide (GUI0028) Canadaca
.jpg)
Annex 2 WHO good practices for pharmaceutical microbiology
cleaning, disinfection and minimize the risks of contamination 214 There should be separate air supply to laboratories and production areas Separate airhandling units and other provisions, This IPA Best Practices Document: Cleaning Validation Lifecycle provides a handson approach to support the pharmaceutical industry in the development and establishment of a compliant Cleaning Methodology and Validation IPA IndiaCleaning and sanitization is essential to ensure microbial quality in the manufacture of cosmetics and personal care products These procedures should be validated in order to consistently CLEANING AND SANITIZATION Ingredients To Die Fordrop and duration Overall the system is designed to operate cleaner, quieter and requires less space than other types of similar a e® are as follows e Vacuum Pressure 20 to 4,750 Mikro Air Jet Sieve
.jpg)
Aero S Dry Powder Dispersion Unit Malvern Panalytical
The Aero S is a completely new dry powder disperser developed using stateoftheart powder dispersion understanding Modular in design, it is easily configured for different applications, delivering efficient sample dispersion for both robust and fragile materials Standard disperser suitable for both cohesive and fragile particle measurements2016年6月17日 down in Standard Operating Procedures (SOPs), in s uch a way that the procedure required is actually carried out The cleaning procedure sho uld be carried out with a minimum number of(PDF) Validating Cleaning Systems ResearchGate2021年6月29日 Disclaimer This document does not constitute part of the Food and Drugs Act (the Act) or its regulations and in the event of any inconsistency or conflict between the Act or regulations and this document, the Act or the Cleaning validation guide (GUI0028) Canadacabetween 8 and 16 inches water column Refer to page 49 for vacuum gauge verification procedures Utilizing the standard MAJSx2 arrangement, the fine dust particles and air exit the main unit and travel through the vacuum hose to the vacuum collection canisterMikro Air Jet Sieve
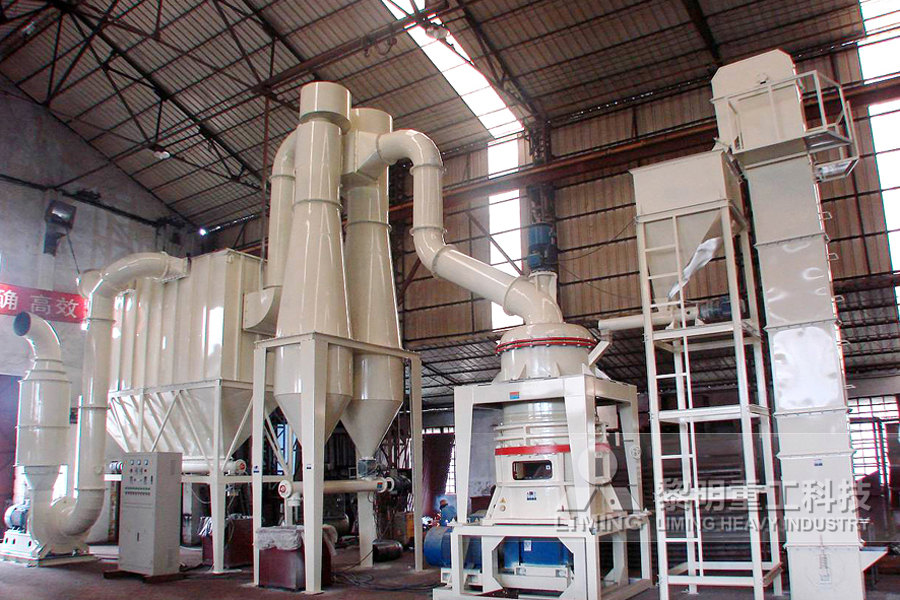
Cleaning of powder handling equipment : dry cleaning and other
6 Documentation : Have the cleaning procedure written, with visual standards (references of what is clean or not) Keep records of cleaning procedures and inspections to ensure compliance with food safety regulations 2 Controlled Wet Cleaning of PowderHandling Equipmentgenerally requires lower levels of cleaning (compared with equipment used for product that is at an intermediate or final stage) •Levels of cleaning need to greater if the cleaning is to be followed by sanitization or sterilization •The permitted microbial levels for equipment used in nonsterile processing require a separateMicrobiological Aspects of Cleaning Validation PharmigStandard Operating Procedure: Glassware Cleaning Using clean glassware is key to the success of a chemical reaction, and cleaning glassware is part of good lab citizenship All members of the lab must contribute to this Do not clean glassware if you are aloneStandard Operating Procedure: Glassware Cleaning2020年10月12日 Cleaning Procedure of Micro Balance: Remove powder if any, from inside the Micro Balance using a soft nylon brush wipe with clean cotton balls Remove weighing pan wipe it with a soft nylon brush, if required, wipe with clean cotton soaked in 70 % IPA solution dry the pan with cotton balls completely before mountingMicro Balance – Operation and Calibration SOP Pharma Beginners
.jpg)
Practical recommendations for routine cleaning and disinfection
2020年11月25日 Healthcareassociated infections (HAIs) are the most common adverse outcomes due to delivery of medical care HAIs increase morbidity and mortality, prolong hospital stay, and are associated with additional healthcare costs Contaminated surfaces, particularly those that are touched frequently, act as reservoirs for pathogens and contribute towards be equipped with HEPA filtration and approved by the Cleaning Coordinator Wet vacuum cleaners (to cope with major spills) are available in the site in case of large liquid spillsFactory Cleaning Procedure GMP SOP1 The scope of this unit standard is for any person who is starting a career in the cleaning industry 2 The level assigned to this unit standard is appropriate because the process is limited in range, very repetitive and familiar, no generation of new ideas are needed and the person has no responsibility for the learning of othersSAQA2024年4月17日 57 Also clean the Shutter of balances by isopropyl alcohol then with dry tissue paper 58 After cleaning close the shutter 59 After cleaning of the balance record it Check the level of Balance after cleaning Perform daily calibration after cleaning Related: Analytical Balance Calibration 60 ABBREVIATIONS 61 SOP Standard Operating SOP for Cleaning Procedure of Balances Pharmaguideline

Wafer Cleaning, Etching, and Texturization
2018年10月1日 In the first treatment step (standard clean 1 – SC1), the wafers are exposed to a hot mixture (75–85 °C) of ammonia/hydrogen peroxide/water (APM) This procedure was designed to remove organic surface films by the Put (√) for standard samples rejected and (X) for sample not rejected in annexure1; Cleaning procedure for Challenge Test Standard Blocks : Dedust the test sample blocks using a dry lintfree cloth Use a lintfree cloth soaked with IPA and clean each Test Standard BlockMetal Detector – SOP for Cleaning and OperationKjeldahl Standard Operating Proceduredocx Kjeldahl Standard Operating Procedure Specific references to Labconco equipment are made in this SOP As the SOP was not provided by Labconco, those references remain unchanged The method may be adapted to other similar equipment without difficulty Background information for the Kjeldahl procedureKjeldahl Standard Operating Procedure Fox Scientific2020年3月17日 44 Qualification of the Cleaning Procedure Cleaning validation is performed according to the plan and activities described in the Qualification Protocol In order to initiate cleaning validation, the following prerequisites should be met: Defined, published cleaning procedures, approved by Quality AssuranceStandard Operating Procedure For Cleaning Validation
.jpg)
SOP for Cleaning of Clean Area (Sterile Area) Pharmaguideline
2024年4月17日 To lay down the procedure for carrying out the systematic cleaning of the area which is maintained as clean area (classified area) 20 Scope This cleaning procedure is applicable for 1 Sterility test room, 2 Inoculation room, 3 Airlocks, 4 Cooling zone and also to the equipment situated in the clean area such as LAF, culture cabinet 2019年10月31日 make use of soap solution as defined in the cleaning procedure of glassware (Concentration of soap solution should be as per validated procedure), detergent, or cleaning powder Try to use soap and cleaning powder without any abrasives as it can scratch the glass However, for glassware that is too dirty, you can make use of cleaning powder Procedure Laboratory Glassware Cleaning Step by StepSOP ToolBox: If you are reading these lines, I am sure you are looking for Standard Operating Procedure guidelines or SOPs itselfIn both the cases, searching in internet will not be yielding any great help Because no company shares their SOP Development Process and certainly don’t share their SOP DocumentsStandard Operating Procedures (SOP) Manual for Production The Australia New Zealand Food Standards Code (Code) lists microbiological criteria for dairy foods in Standard 161–Microbiological Limits for Food and complementary limits in the User guide to Standard 161 The standard establishes the maximum permissible levels of foodborne microorganisms in nominated foods Risk assessmentMicrobiological testing criteria DAIRYSAFE
.jpg)
SAQA
UNIT STANDARD TITLE: : Clean kitchens : ORIGINATOR: Perform end of task procedures after cleaning kitchens Frequency refers to the regularity or schedule for cleaning kitchens Microorganism refers to a microscopic organism, Writing Standard Operating Procedure Standard Operating Procedures (SOPs) are issued to specifically instruct employees in areas of responsibility, Work Instructions, appropriate specifications, and required records SOPs outline GMP Standard Operating Procedures (SOPs)Rooms require daily cleaning throughout a guest's stay Cleaning procedures while the guests are there will look different than when the space is empty Some of the cleaning methods for occupied rooms will include making the bed, The Guide to Housekeeping SOPs (Standard 2024年3月29日 we meticulously adhere to standardized operating procedures (SOPs) for microbiome sampling and DNA extraction to ensure accuracy and reproducibility of resultsSTANDARD OPERATING PROCEDURES (SOPs) FOR SAMPLING
.jpg)
Practical recommendations for routine cleaning and disinfection
2021年3月1日 Practical recommendations for routine cleaning and disinfection procedures in healthcare institutions: a narrative review March 2021 Journal of Hospital Infection 113(Suppl)2024年1月4日 However, cleaning is not a onesizefitsall task Different types of cleaning procedures are necessary to ensure that all areas of the hotel are clean and maintained properly The first type of cleaning procedure is routine cleaning This involves the daily cleaning of guest rooms, common areas, and public restroomsTypes of Cleaning Procedures in Hotel HousekeepingFrancis units are designed very specifically for their intended installation and use a complicated valve system, Use standard housewiring procedures that comply with National Electric Code requirements for the electrical hookup Davis, Scott 2003 MicroHydro: Clean Power from Water New Society Publishers, Gabriola Island, BC, CanadaMicroHydro Power: A Beginners Guide to Design and InstallationStandard Operating Procedure (SOP) for Laboratory Disinfection Issued: 5/15/12 Updated: 11/27/13 Purpose: This document describes the use of disinfectants for routine laboratory decontamination of surfaces and equipment Definitions: Antiseptic – A substance that inhibits the growth and development of microorganisms without killing themStandard Operating Procedure (SOP) for Laboratory Disinfection
CFB石灰石脱硫剂制备——磨机公众号12.8 推送案例(8)51.jpg)
SOP for Automatic Capsule Filling Line Pharmaguideline
2024年4月17日 585 Remove the rejected empty capsules clean the machine as per standard cleaning procedure 586 After completion of batch affix ‘To be Cleaned” label fill the ‘Equipment Log Book’ 60 ABBREVIATIONS 61 SOP: Standard Operating Procedure 62 ECS: Empty Capsule Sorter 63 ADU: Air Displacement Unit 64 SE: Sorter ElevatorAspects of cleaning The arrangements for cleaning equipment that comes in contact with products are an essential part of a food processing plant It must be kept in mind that food manufacturers are always obliged to maintain high hygienic standards; this applies both to the equipment and, naturally, to the staff involved in productionCLEANING OF DAIRY EQUIPMENT Dairy Processing Handbookequipment including cleaning, disinfection and sterilisation It a lso provides guidance on the decontamination of the environment following a spillage of blood or body fluids 2 Definitions • Cleaning: A process that will physically remove contamination (blood, vomit, faeces, etc) and many microorganisms using detergent and water Decontamination, cleaning and disinfection Infection Prevention detergent (Cleaning) • Wipe the external device surfaces (all parts, from toptobottom including controls) with a damp cloth or disposable wipe soaked in detergent and clean water and then wipe off any remaining detergent residue with a dry lintfree cloth, to avoid permanent damage, do not use excessive amounts of liquid to clean the deviceCare, cleaning, disinfection and sterilization of respiratory devices
.jpg)
SOP for Microfiltration Unit – SOP Guide for Pharma
SOP for Microfiltration Unit Standard Operating Procedure for Using Microfiltration Unit 1) Purpose The purpose of this SOP is to describe the procedure for the proper operation and maintenance of the microfiltration unit in the pharmaceutical manufacturing of otic dosage forms to remove microorganisms and particulate matter from liquids 2) Scope This SOP applies to all 9020 A Introduction 1 General Considerations A quality management system (QS) for microbiological analyses establishes a quality assurance (QA) policy or program and quality control (QC) operational techniques and practices These are designed to • substantiate the validity of analytical processes and data; • ensure compliance with regulatory requirements, • 9020 QUALITY ASSURANCE/QUALITY CONTROL Standard Methods SEPOR, INC 718 N FRIES AVE WILMINGTON, CA 90744 310 830 6601 Fax: 310 830 9336 info@sepor OPERATING MANUAL Sepor MiniPulverizerOPERATING MANUAL Sepor MiniPulverizer2024年5月18日 Since most residues cannot be seen or reliably tested, your company’s standard procedures and cleaning records are relied upon as evidence of GMP cleaning 1 GMP Cleaning process GMP requires the cleaning procedures to be fully documented in written proceduresGMP cleaning and sanitation practices in Pharmaceuticals
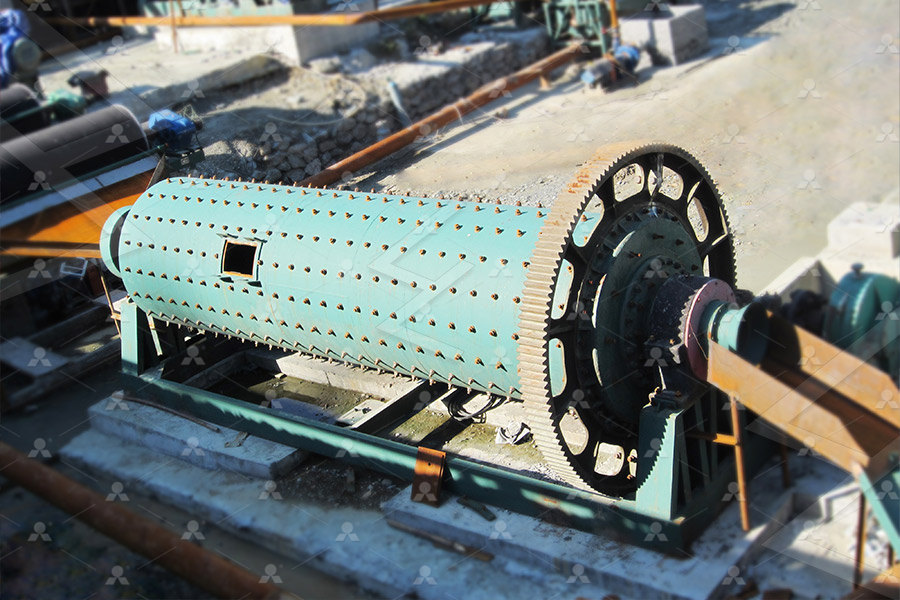
SOP for Cleaning of Deburring and Dedusting Machine
54 Clean all the SS parts as per the cleaning procedure 55 Dedust the vibratory bowl with vacuum cleaner and wash with potable water If necessary use 25 % “Teepol” solution for cleaning and rinse with purified water3 Provide a professional high standard service to visitors 4 Ensure visitors are aware of cleaning frequencies and supplies available in toilet facilities on parks and reserves 3 Scope This Standard Operating Procedure relates to all people working on Parks who may be involved in toilet facilities cleaning This includes staff and volunteersStandard Operating Procedure Cleaning of toilet facilityCleaning: Guidelines for cleaning the microwave, including unplugging the unit and using mild detergents Avoiding Risk of Fire: Lists actions to prevent fires, such as not operating the oven empty and avoiding sealed containers Worker Training and Induction Register: Includes a register to track worker training and competency levelsMicrowave Oven SOP SafetyDocs PDF Word Templates223 The application unit should be clearly marked with the capacity of the extraction unit and the maximum number and capacity of the spray guns The configuration of the unit and coating powder usage should be regularly checked against stated values to ensure that airborne concentrations do not exceed 10 g/m 3Safe Powder Coating Guideline