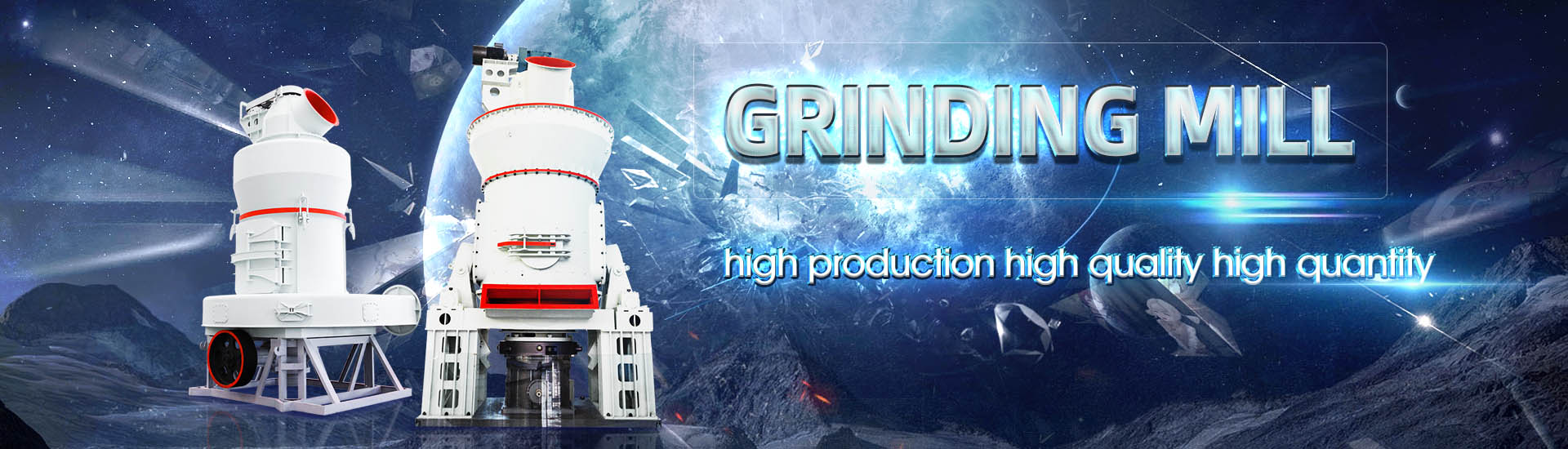
Metso barite mill
.jpg)
Vertimill® Metso
The Vertimill® is globally recognized as an energy efficient grinding mill Through a low total cost of ownership, it brings substantial improvement to the profitability of concentrators During the Vertimill® é um produto oferecido exclusivamente pela Metso A eficiência Vertimil: Referência em eficiêBrowse Metso's wide offering of reliable grinding mills: AG mills, SAG mills, ball and pebble mills, and stirred mills to fit your needs Our pioneering innovations in horizontal grinding mills technology offer exceptional performance and Grinding mills for mining and minerals processing2013年8月29日 Metso has both stirred milling technologies in the Vertimill and the Stirred Media Detritor (SMD), allowing Metso to offer the optimum equipment solution for the circuitVertimill® grinding mills stirred media detritor by
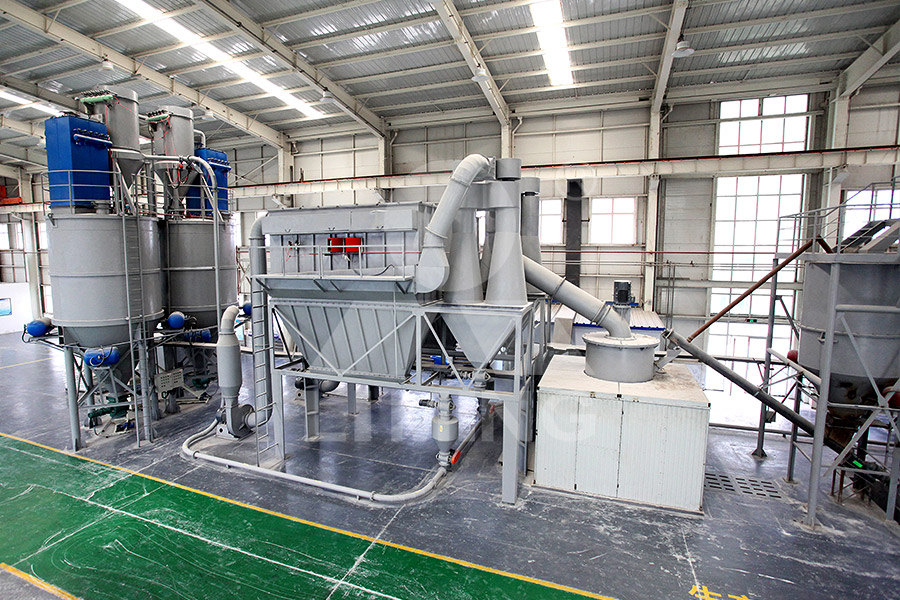
Grinding Metso
With over a century of experience, Metso designs and manufactures the most comprehensive line of grinding mills and entire grinding systems for mining companies around the world The Find out all of the information about the Metso Corporation product: ball mill AG Contact a supplier or the parent company directly to get a quote or to find out a price or your closest point of saleBall mill AG Metso Corporation horizontal / for ore Rotor mills are used for highspeed size reduction of soft to mediumhard as well as temperaturesensitive or fibrous materials The powerful Ultra Centrifugal Mill ZM 300 provides maximum Metso Mills All the products on DirectIndustry2023年12月19日 This highcapacity SAG mill, which will be one of the largest gear driven mills installed in Africa, is based on proven technology It features an efficient LSS drive, and a Metso to deliver a highcapacity grinding mill to Bomboré gold mine

Metso Mills All the products on DirectIndustry
The new compact mills have finally entered in production for all those who need a small production: from 50 to 1000 Kg/h The MINI Cogelme glass crushers get the same concept of Metso HIGmill™ is an advanced and energyefficient fine and ultrafine grinding solution that relies on proven technology The mill takes advantage of gravitational forces and GrindForce™ rotor technology to produce a finer grind HIGmill high intensity grinding mill MetsoFor minerals processing in the mining, aggregates and recycling industries, Metso's offering includes crushers, screens, mining solutions, grinding mills and media, conveyors, solutions Metso WikipediaMetso rubber mill liners are tailormade and developed in close collaboration with our customers Being the pioneer, Metso rubber mill linings are designed and produced based on the world's largest bank of knowhow and experience As Rubber mill liners Pioneering rubber mill linings
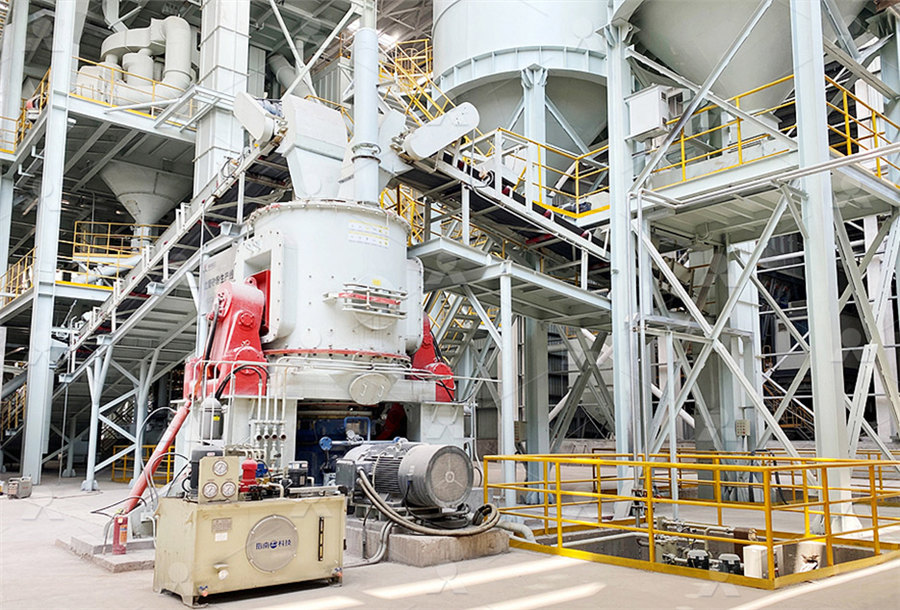
Tube Mill Reline Machine Metso
Mechanical assistance is a critical requirement for safe relining and is often challenging in smaller SAG and ball mills The Metso Tube MRM provides fixed threeaxis hydraulic crane support for relining tasks in mills that are unsuitable Mill liner recycling can help you reach your sustainability targets and and also solve the problem of disposing worn and used mill liners Instead of being sent to a landfill, worn liners are dismantled and the different components can be Mill liner recycling service Metso2020年6月23日 Take mill power draw, product, throughput and conversion costs into consideration when converting a ball mill Menu Close Metso Outotec is able to provide modelling of the mill before and after conversion to quantify Converting a ball mill from overflow to grate discharge MetsoThis includes: Cost savings from investing in a preengineered solutions, time savings from our expedited selection, quotation process, and order execution, and faster delivery and startup of your Select™ horizontal grinding mill The Metso Select™ horizontal grinding mill is a robust mill for exceeding operational goals today and tomorrowSelect™ Horizontal Grinding Mills Metso
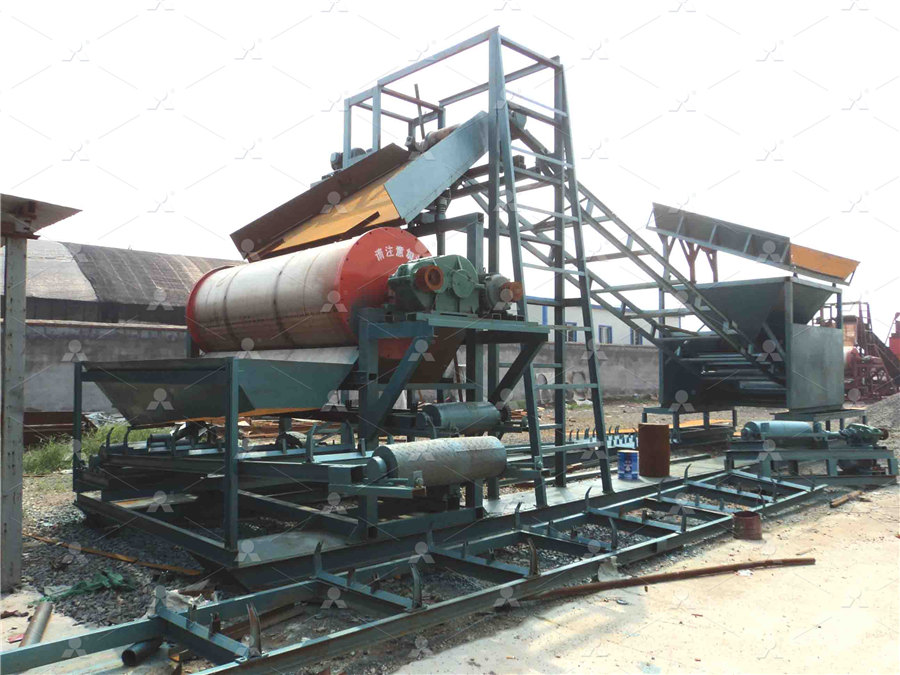
Polymer HSB technology helps avert ball mill bearing failure Metso
2020年4月7日 However, the main mill motor circuit breaker failed to open and cut power to the motor This was due to a preexisting and undetected fault within the circuit breaker assembly The result was the mill continued to rotate for approximately 10 minutes without any oil being supplied to the Polymer HSB bearingsThe Metso Mill Equipment Transporter (MET) is a remotely controlled solution for the safe, reliable, and efficient transportation of mill feed chutes and other large or heavy equipment during maintenance procedures such as mill relining BenefitsMill Equipment Transporter MetsoA Metso Premier™ horizontal grinding mill is able to meet any projects needs, even if it means creating something novel and unseen before This all comes from the premier design approach we take to finding the best solution to fit the project needs, while exceeding operational goalsPremier™ Horizontal Grinding Mills MetsoAs your service partner, we ensure that every solution has the maximum impact on performance and productivity throughout your mill’s entire life cycle Full mill reline equipment packages including mill reline machines, feed chute transporters, bolt hammers, and support tooling; Equipment inspection, maintenance, and training servicesMill reline machines Metso
.jpg)
The magic of bolting for a grinding mill assembly Metso
2020年3月17日 A typical medium size grinding mill undergoes over 5 million revolutions per year A mill, therefore, needs to be designed for infinite life otherwise it could fail within two years The bolts holding the mill segments together play a critical role and must withstand the high levels of alternating loads placed on themThe Metso QdX4TM Mill Drive was developed in close collaboration with both CMD and Ferry Capitain Engineering as a solution for the mining industry for large mill drives The Metso QdX4TM Mill Drive features internal torque splitting capability transmitting motor input power to the pinion shaft and equally dividing into two mill pinionsMetso QdX4 Mill Drive systemEventually, even the toughest mill liner will wear off Understanding how your linings wear has a direct impact on the performance of your grinding mill Metso’s wear management solutions extend liner life cycles, optimize throughput and Mill liner wear and performance monitoring MetsoMetso supplied their first grinding mill back in the late 1950s Since then, we’ve delivered and serviced over 8,000 grinding mills globally, including some of the largest and most powerful mills in the world The mining industry has evolved Grinding mill upgrades Metso
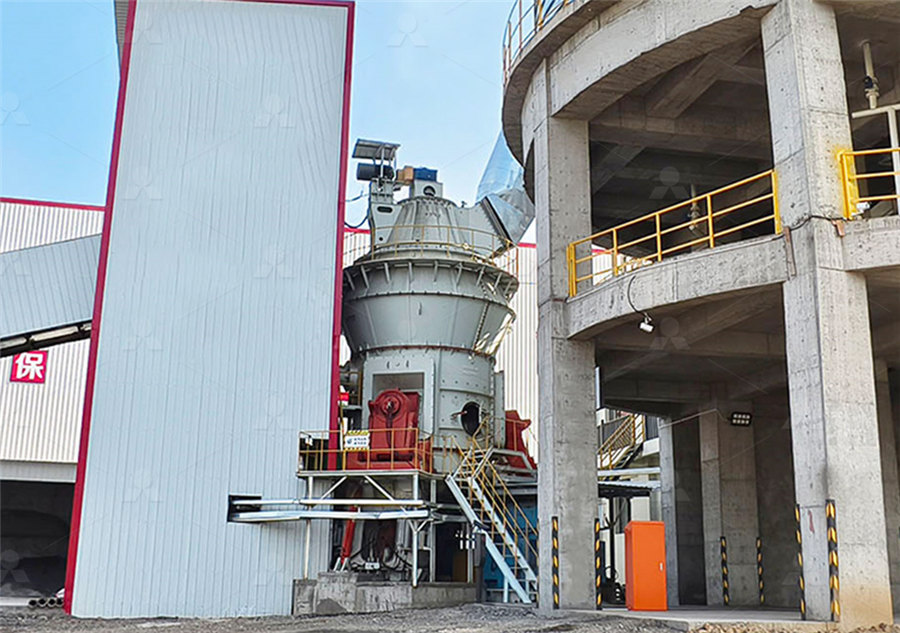
Is your mill a good candidate for Megaliner™ mill liners? Metso
2024年11月25日 Megaliner™ is one of Metso’s most innovative mill lining products and has been available on the market since 2012 The latest addition to the product family was Megaliner for discharge systems, launched in 2020, making the Megaliner mill lining system a complete solution for all sections of a horizontal grinding mill: the feed end, shell and discharge endMetso grinding mill upgrades bring the latest technology to your existing mills, making your operations more productive, sustainable, costefficient, and safer overall Our upgrades are tailored to your production goals and are customengineered to your applicationGrinding mill services MetsoThe system measures the mill’s toe angle with a wireless sensor attached to the liner bolt Together with Metso's advanced process controls, the MillSense sensor system helps to stabilize and optimize grinding processes to ensure reliable operation and increased throughput Increases mill availability while decreasing unexpected shutdownsMillSense Metso2012年4月5日 Outotec has expanded its Grinding mill product family and now offers Outotec® High Intensity Grinding Mill (Outotec® HIGmill) for fine, ultra fine and regrind milling applications Outotec holds an exclusive rights agreement to provide process development, sales, and lifecycle support of the well proven technology from Swiss Tower Mills Minerals Ltd (STM) in the Outotec® High Intensity Grinding Mill Metso
.jpg)
Megaliner™ mill liners Metso
Metso Megaliner™ megaliner mill liner reduces downtime and improves safety by minimizing the number of parts and people inside the mill Fit for large AG, SAG and ball mills Megaliner™ an innovative mill liner made to improve worker safety and uptime Menu Close 2023年11月7日 Are you struggling with high operating costs or unexpected downtime with your mill discharge pump? Through design, selection and application, Metso can determine if your pumps are being a profit killer Read more from our experts on best practices and operational tips to ensure lowest total cost of ownership and higher pump performanceIs your mill discharge pump maximizing profit? MetsoMetso metallic mill linings are produced at our own foundries Our chromium molybdenum steel and highchromium white irons are specially developed for mill lining applications and are carefully selected based on the operating conditions of each mill Our foundries apply strict quality assurance programs at every phase of research, development, design and productionMetallic mill liners MetsoTo keep your grinding mill running for optimal performance, Metso offers an extended warranty program to expand basic coverage from design and manufacturing to also include installation, operation, maintenance and Grinding mill inspections Metso
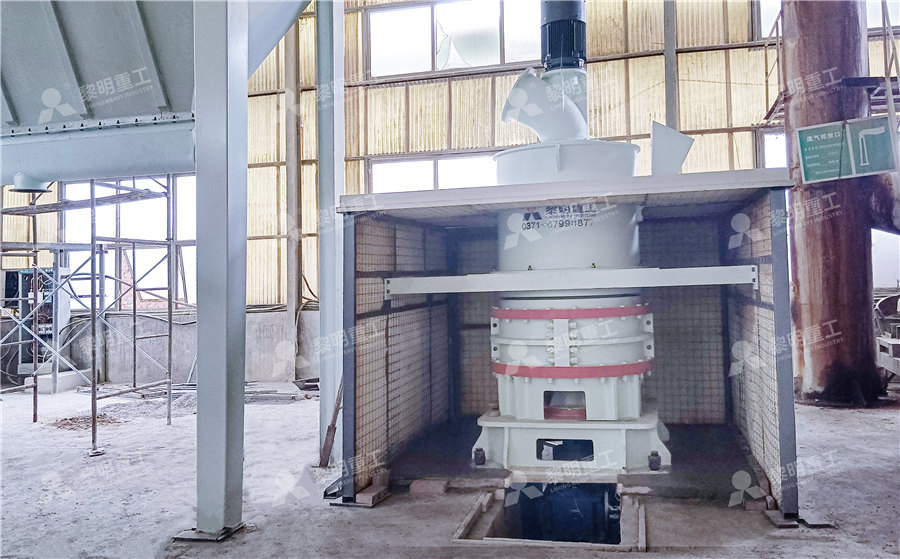
Reline your thinking (2/4): Incremental automation for
2021年6月4日 A new age is dawning in the continuous pursuit of improved mill reline safety and efficiency – the age of automation However, there are multiple approaches to implementing automation and each has its own risk Read on 2023年11月27日 Mill liners play a crucial role in the performance of your grinding operation They protect your equipment and have a major impact on production Metso has recently developed a new rubber, Skega™ Life, with up Stretching the life of your mill liners MetsoThe discharge system of a mill is the most complex and timeconsuming part of the mill to reline The new Megaliner™ for discharge systems integrates dischargers, grates, lifter bars and filling segments in one unit, reducing the number of components used by as much as up to 70% This can cut your installation time in halfMegaliner™ for discharge Metso2012年9月21日 The mill will be driven by a Gearless Motor Drive (GMD) which at 280MW is equal to the largest grinding mill power ever used in the mining industry The SAG mill design is based on Outotec's proprietary grinding mill technology, developed over decades for maximum reliability and performanceOutotec presents the world's largest SAG mill Metso
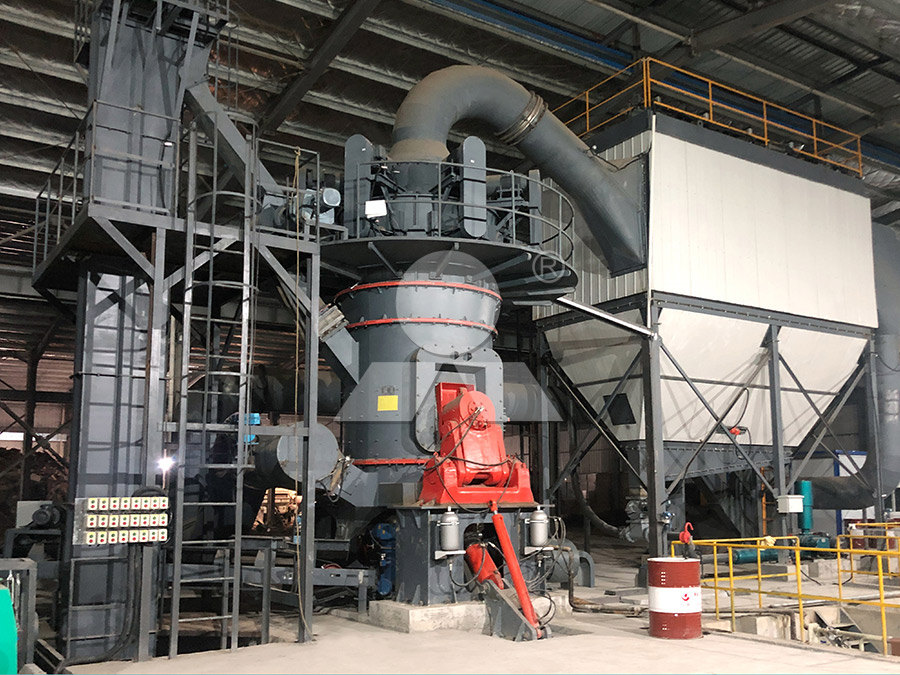
Stirred Mill Plant Units Metso
Metso leads stirred milling innovations and continues to be the industry standard in performance We offer a wide portfolio of stirred milling technologies: Vertimill ®, HIGmill™, and Stirred Media Detritor (SMD) Metso stirred mills are part of the Metso Plus product portfolio, which apply the mill input energy to liberate mineral in a sustainable manner2 Metso d4 TM Mill Drivesystem 7 MW 7 MW 14 MW 28 MW 7 MW 4 MW 7 MW 7 MW 7 MW 4 MW 7 MW 7 MW SAG mill 32 ft single drive The natural progression in gear/pinion mill drives: The Metso QdX4TM Mill Drive provides the next step in the evolution of change in mill drive architecture, while allowing the system to be built with components that are within current Metso QdX4TM Mill Drive systemAn overall inspection while the mill is running, and an internals visual inspection with borescope for the HIGMill™ A quick way to understand your mill’s overall condition for peace of mind Grinding chamber status: Full chamber, main door closed Inspection frequency recommendation: 34 times a year Inspection offering:Stirred mill inspections MetsoMetso Select™ horizontal grinding mills redefine design and selection simplicity, while exceeding operational efficiency with classleading availability, reliability, and productivity Now, you can find all the files you need for flowsheet optimization available for download without having to Metso Select™ mills resource center
.jpg)
Ball feeder Metso
Metso's ball feeding technology utilizes a simple and robust design to continously and efficiently feed the grinding mill With this in place, the grinding mill can operate at maximum productivity levels compared to those mills without a grinding media feeding systemStirred Media Detritor (SMD) is a fluidized media grinding mill It utilizes the rotational energy of the impeller arms to impart a highenergy motion to the media and slurry mixture inside the mill This results in particletoparticle shear and Stirred Media Detritors (SMD) MetsoHome Campañas Mill Lining Campaign Lleva tu molienda al siguiente nivel Revestimientos de molino Lleva tu molienda al siguiente nivel {{activeElement}} Objetivos; Metso ofrece revestimientos para molinos con materiales y Mill Lining Campaign Lleva tu molienda al siguiente Understanding how your linings wear has a direct impact on the performance of your grinding mill Metso’s wear management solutions harmonizes liner life cycles, optimize throughput and uptime and empower better decision making MillMapper Liner Wear Monitoring Metso
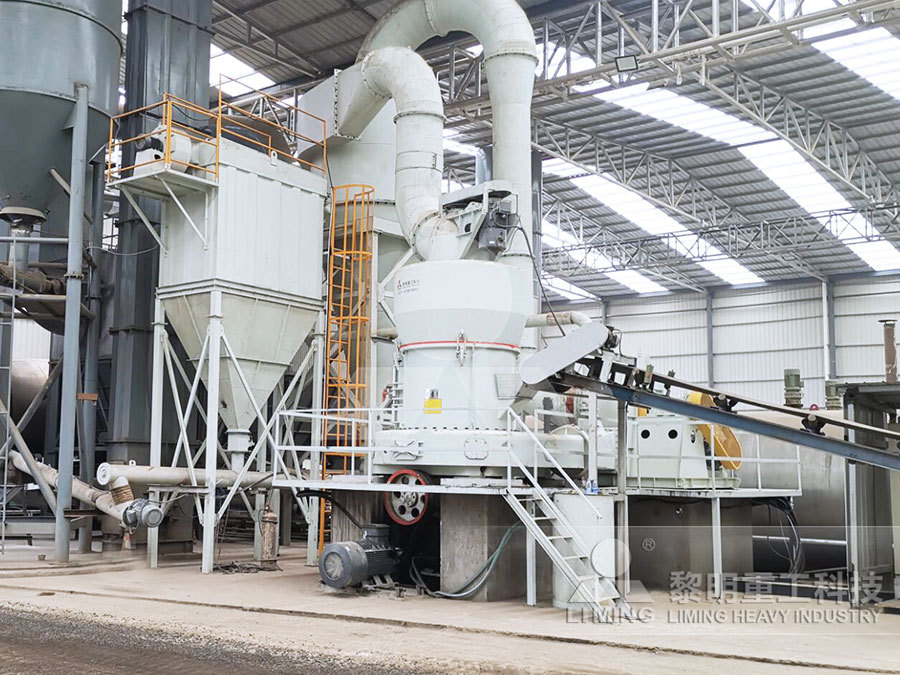
Designed to perform Select™ Horizontal Grinding Mills Metso
Metso Outotec Select™ horizontal grinding mills redefine selection through a simplified process Preengineered mill designs can be specified by a customer, or chosen by the Metso Outotec Process team after a review of the application Next is the quoting phase, where a total proposal package containing the complete offering is provided for 2013年8月29日 Metso Minerals Industries, Inc, 2715 Pleasant Valley Road, York PA, 17402 USA, tel +1 717 849 7213, fax +1 717 849 7252, metso Turn static files into dynamic content formats Create a Vertimill® grinding mills stirred media detritor by Metso 2016年8月29日 Some lining parts in a mill are more exposed to wear than others, and the wear life of the mill lining components can therefore be very different This means that fully utilizing the wear life of all lining parts in a mill may not be the most optimal solution since it can lead to added downtime and production lossBalance the wear life of your mill lining parts Metso2022年3月4日 When it comes to servicing or maintaining a grinding mill, many customers focus on the mill itself rather than all its related components One such component is the feed chute, which is often overlooked However, it is a key part in the grinding process that can cause you downtime if neglectedThree things to consider for your SAG Mill Feed Chute – downtime
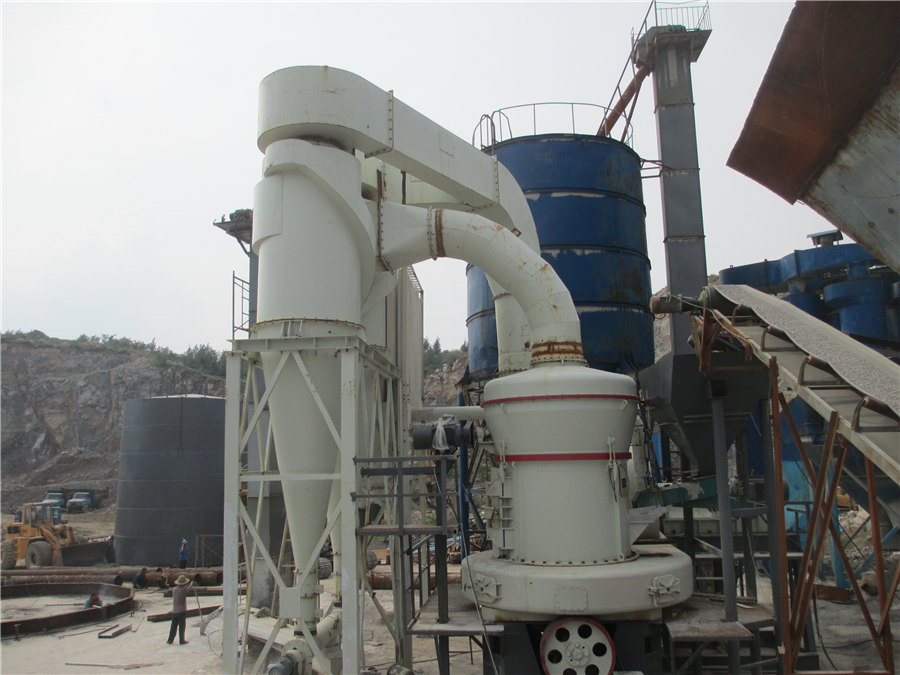
PolyMet mill liners Mill linings from rubber and steel Metso
Metso's Skega PolyMet™ mill linings combine the most desirable properties of rubber and steel to maximum advantage This combination allows the use of more wearresistant alloys of iron and steel than can be used in a conventional metallic lining, as the rubber substantially dampens the impact forces and also results in a lower lining weightOur engineers will help identify your goals for increasing your grinding efficiency We will conduct a mechanical study to evaluate the current condition of your mill which includes a review of the structural capacity of the mill rotating body, bearings, and foundation loads as well as a mechanical review of drive components Once the maximum power draw is confirmed, we will Mill power draw increase MetsoMetso, Brazil ABSTRACT In mineral processing operations, the grinding circuit is a key step in the process to achieve the Mill speed, rpm / % critical speed 13 / 55 Power utilization, % 767 Rod charge, % 272 F 80, µm 56,195 Ball charge, % 278 P 80, µm 280MultiCompartment Rod/Ball Mill Evaluation on Bauxite Operation