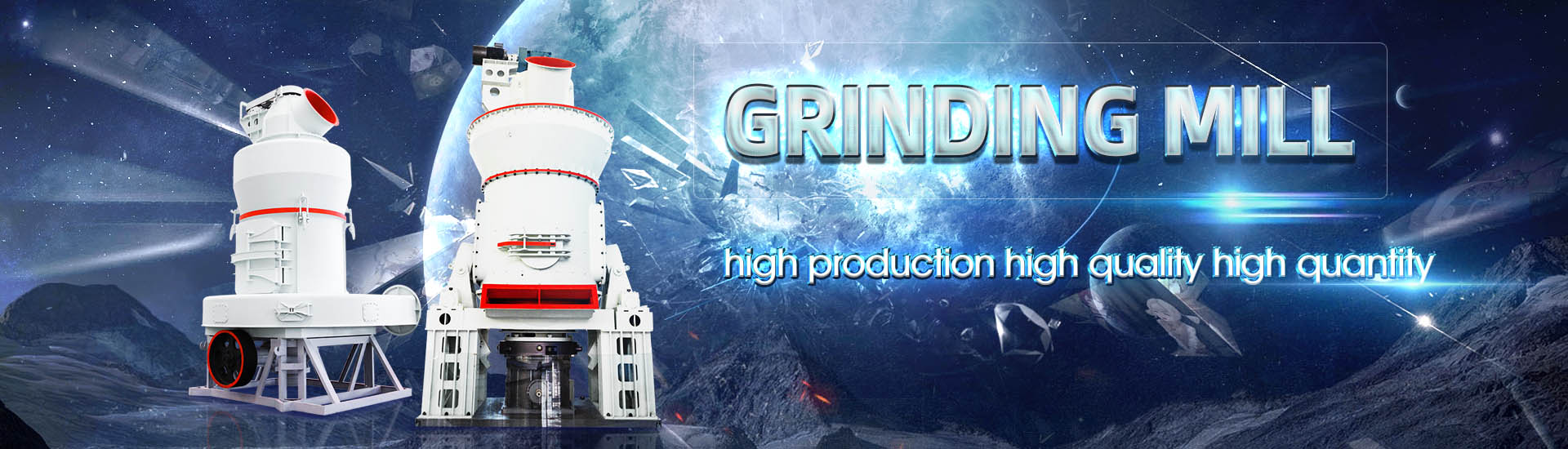
How to wear ore mill
.jpg)
Three factors that determine the wear life and performance of mill
Knowing the current and historical wear rates, wear behavior, and performance of the mill is a prerequisite for liner optimization Areas for improvement can be identified by closely monitoring the wear of the existing lining and by looking back at wear history Usually, certain areas in the mill liner wears and the profile changes It is hoped that this review will better arm mill operators to select suitable mill liners, with a view to decreasing production costs while maintaining mill The Selection and Design of Mill Liners 911 Metallurgist2017年11月1日 To understand the friction and wear of working mediums in iron ore ball mills, experiments were conducted using the ball cratering method under dry and wet milling Friction and wear of liner and grinding ball in iron ore ball mill 2013年8月1日 Relationship between microstructure, hardness, impact toughness and wear performance of selected grinding media for mineral ore milling operationsConsumption of steel grinding media in mills – A review
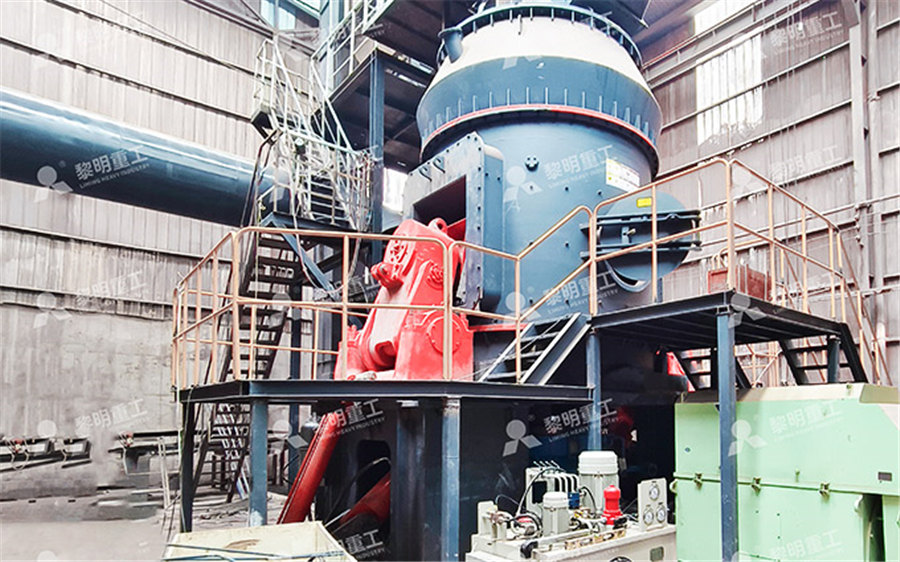
Ball Mill Maintenance Process and Methods Miningpedia
2023年7月18日 The components of the ball mill will wear out after longterm use and need to be replaced regularly Generally, the parts that need to be replaced include bearings, gears, and steel and composite options — ARMOUR mill liners offer industry leading wear protection for your grinding mills By incorporating unique geometric designs, these liners empower you to ARMOURTM Mill liner solutions Augmenting grinding excellence In ball mills, steel balls or hard pebbles to break particle based on impact and attrition A rotating mill charged with media and ore is lifted against the inside perimeter Some of the media falls and impacts the ore particles at the bottom AMIT 135: Lesson 7 Ball Mills Circuitsexponent equal to 2 provides a practical solution to the wear law for conventional ball milling When n is equal to 2, the production wear rate is directly proportional to the surface area ofthe Wear ofgrinding media in the mineral processing industry: An
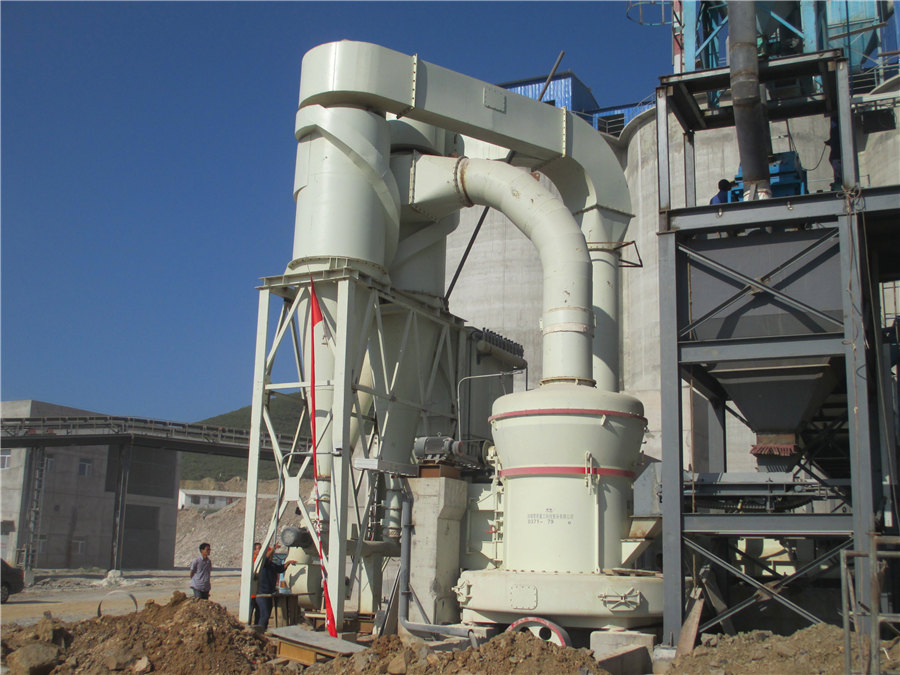
JKTech A Way to More Accurate Grinding Technical Article Media
Consequently, the Bond abrasion test, dating back to 1963, is still used to estimate total mill media wear This is a purely empirical test based only on ore properties A comparison of the 2019年12月15日 The wear of lifter in ball mill directly affects the grinding efficiency and economic cost However, how to evaluate the variation of wear process and predict the wear Effect of the operating parameter and grinding media on the wear 2015年6月19日 The basic parameters used in ball mill design (power calculations), rod mill or any tumbling mill sizing are; material to be ground, characteristics, Bond Work Index, bulk density, specific density, desired mill Ball Mill Design/Power Calculation 911Metallurgist2023年4月23日 The mill critical was 90rpm The wear rate decreased when rates than soft ores Wear resistance depends on the stre ngth of the ore being ground [6 7] 24 Grinding Media filling (PDF) Grinding Media in Ball MillsA Review
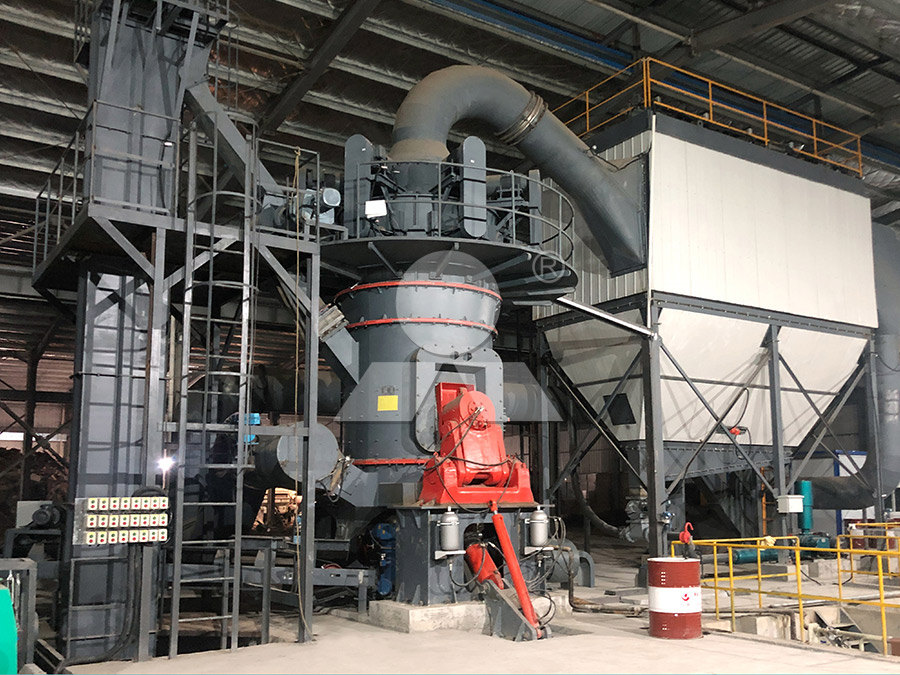
A comparison of wear rates of ball mill grinding media
The Ball Mill Abrasion (BMA) test was developed by the University of Queensland Materials Performance group to simulate the high stress abrasion conditions experienced in production ball mills It gives accurate predictions of the 2017年11月1日 An iron ore mill relies on the grinding and impact of grinding balls to complete iron ore crushing The operating process of an iron ore mill is as follows: first, the ores are poured into the mill, and both the ores and the grinding balls are lifted by the lifting bar arranged on the wall of the cylinder body to a certain height, after which they fall onto the bottom of the mill to Friction and wear of liner and grinding ball in iron ore ball mill 2013年8月1日 It would clearly be futile to attempt prediction of wear losses in the media in a wet mill, based on a model calibrated under dry mill conditions However, even if the same nominal systems are observed, the variation in the ore and internal conditions in the mill may still be affect the reliability of the modelsConsumption of steel grinding media in mills – A review2023年10月17日 Factors for choosing a suitable ore powder grinding mill 1 Raw material characteristics: Different raw materials have different hardness, humidity and grinding and crushing properties, and the corresponding ore powder grinding mill needs to be selected to meet the processing requirements 2 Production capacity: Determine the required processing How to choose a suitable ore powder grinding mill?
.jpg)
Factors affecting ores grinding performance in ball mills
Ore grinding is one of the key stages in the mining process It's where the ore is reduced to a fine powder, which can then be used in other stages of the extraction process Grinding performance is a critical parameter for this stage, as it affects both the speed and quality of the final product The parts of a ball mill2020年1月27日 Figure 2: Cascadingimpact action in a SAG mill Rubber and composite mill lining systems In the past, grinding mills were typically lined with cast metal linings of varying steel or iron alloys, and lining system selection was typically driven by level of Key considerations when selecting a mill lining system2021年9月23日 Using the methods and equipment outlined here, you should be able to process gold ore and extract the gold in an efficient, environmentally friendly manner You can set up a small gold mill to use at home, or trailer mount the various components to take with you These are the basic steps involved, and I will go over each in detailHow To Extract Gold From Rocks Mojave Gold MiningUnderstanding Mine to Mill is presented in five parts Part A – Setting the Scene provides some definitions of Mine to Mill (M2M) and the historical background A chronology of Mine to Mill developments is followed by brief descriptions of the very wide range of Mine to Mill applications which have been implemented over the last 15 yearsUNDErsTaNDINg MINE TO MILL 911 Metallurgist
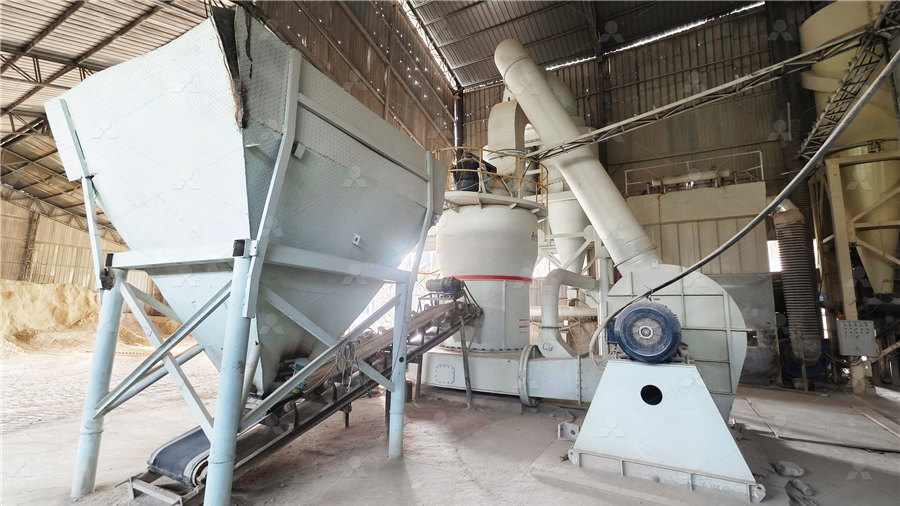
How to use and maintain the gold ore wet pan mill
2022年6月29日 Gold ore wet pan mill have many years of history in beneficiation equipment, and are welcomed by customers because of their convenient operation and fine discharge granularity Especially in Africa, South America and other regions, it is widely used in gold mining This equipment can replace crusher and ball millA mill is a device, often a structure, machine or kitchen appliance, that breaks solid materials into smaller pieces by grinding, crushing, or cutting Such comminution is an important unit operation in many processesThere are Mill (grinding) WikipediaHowever, ore below the pay limit adds variation to the mill grade as increased mill throughput will be required to make up for the loss of gold, and that impacts on the recovery in the plant It is against these perspectives and findings of this Monitoring ore loss and dilution for minetomill 2017年2月16日 The methods employed in dressing the tin ore up to the required percentage of purity depend mainly on the type of ore crushed The ore is conveyed to the mill over a distance of seven miles by a 2foot gauge railway The advantages outweigh the disadvantages of increased cost of belting and increased wear of central brassesTin Ore Processing 911Metallurgist
.jpg)
Factors Affecting Ball Mill Grinding Efficiency 911Metallurgist
2017年10月26日 The following are factors that have been investigated and applied in conventional ball milling in order to maximize grinding efficiency: a) Mill Geometry and Speed – Bond (1954) observed grinding efficiency to be a function of ball mill diameter, and established empirical relationships for recommended media size and mill speed that take this factor into EFFECTS BEAD WEAR AND MILL WEAR •Round: uniform in shape, will roll and move through the mill making consistent contact The smooth rolling action causes less wear on the mill •Oblong: or other nonround shapes such as pyramids or flats will not roll smoothly causing erratic flow, inefficient mill wear and premature mill wearHow to Choose the Correct GRINDING MEDIA PCI Magthroughput capacity of the mill, a number of wear measurements are necessary during the life cycle of mill liners The liner wear reading can be used to calculate available volume inside the mill as the inside mill volume for ore grinding is a function of volume of mill liners The measurement of liners can also be used toEvaluation of Abrasive Wear Measurement Devices of Mill Liners2023年10月27日 The ball mill is a rotating cylindrical vessel with grinding media inside, which is responsible for breaking the ore particles Grinding media play an important role in the comminution of mineral ores in these mills This work reviews the application of balls in mineral processing as a function of the materials used to manufacture them and the mass loss, as A Review of the Grinding Media in Ball Mills for Mineral Processing
.jpg)
5 Ways to Improve the Ball Mill Efficiency FTM
2020年1月11日 Here the structure means the ratio of ball mill length to its diameter According to the industrial tests, the capacity varies with the ball mill types; Even from the same type of ball mill, the energy consumption and milling efficiency are different One of the factors is the function of the diameter and length2023年7月31日 Gold ore ball mills are commonly used for the crushing and grinding of gold ores before the extraction and beneficiation process When selecting a gold ore ball mill, factors such as the properties of the gold ore, the model specifications, the liner material, and the steel ball composition need to be consideredGold ore ball mill common model and price, how to match the 2017年7月26日 We will consider an ore with a ball mill work index varying between 16 and 13, feeding into a single stage ball mill operation with one million kilowatts per day consumed power For the particular mill configuration, a performance graph, Fig (21), has been constructed according to Bond’s methodsHow Ball Mill Ore Feed Size Affects Tonnage Capacity2015年4月15日 Fines from each classification stage, k Power drawn by each mill (motor input) Motor and drive efficiency of each mill, Size of and type of grinding media used in each mill Speed in RPM for each mill Liner design What Ore Testing is Required For Mill Selection
.jpg)
JKTech A Way to More Accurate Grinding Technical Article Media Wear
Consequently, the Bond abrasion test, dating back to 1963, is still used to estimate total mill media wear This is a purely empirical test based only on ore properties A comparison of the wear/energy values resulting from the Bond abrasion test with actual mill data for five ores and 11 mills is shown in Figure 1 0 002 004 006 008 012023年11月24日 The performance of grinding media in a ball mill is measured in terms of wear rate, which is a function of the media composition, hardness, phase structure, and corrosive–abrasive characteristics of the slurry The wear mechanisms involved in a ball mill are impact, abrasion, corrosion, and erosionGrinding Media in Ball Mills for Mineral ProcessingIn general, wear parts are components that require scheduled replacement due to routine wear and tear because they are coming in direct contact with the ore Consumables can also affect the performance of the machine Examples would be crusher and OEM parts expert services FLS2019年7月25日 The wear resistance of an alloy in heavy mill liner sections may be quite different from that of the same alloy in small balls and other light sections This 911 Metallurgist is a trusted resource for practical insights, solutions, and support in mineral processing engineering, helping industry professionals succeed with proven expertise How to Select Grinding Mill Liner How to Select Grinding Mill Liner Alloys for Optimum Wear Resistance
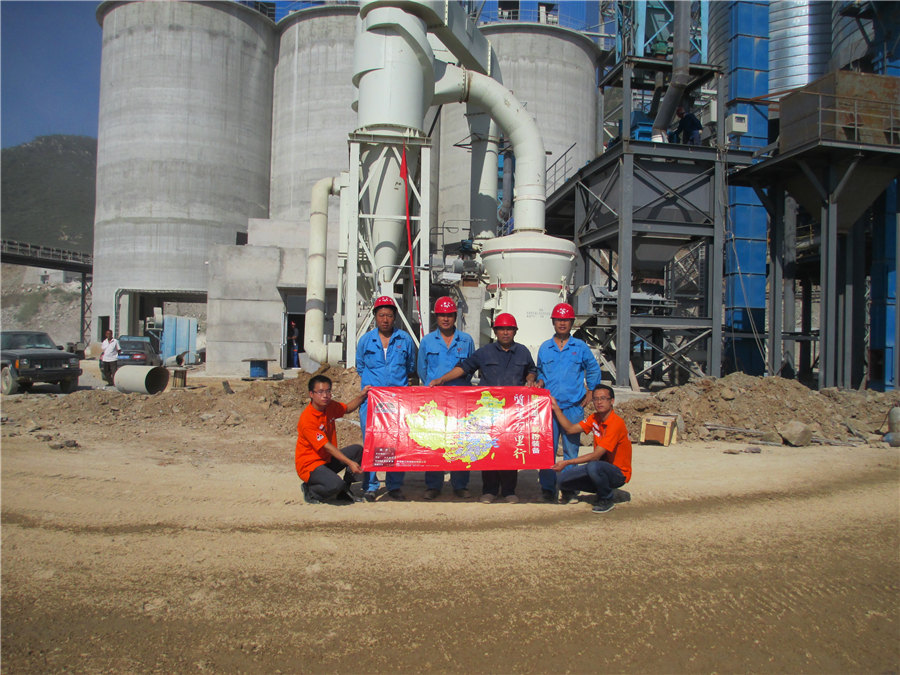
Ore mill, Ore grinding mill All industrial manufacturers
Find your ore mill easily amongst the 42 products from the leading brands (Fritsch GmbH, Retsch, Eriez, ) on DirectIndustry, It is specially designed for adopting new and wearproof materials to enhance crushing capacity as well as the extension of the roller and rings service life This 2017年6月15日 To understand the friction and wear of working mediums in iron ore ball mills, experiments were conducted using the ball cratering method under dry and wet milling conditions, which mimic the Friction and wear of liner and grinding ball in iron ore ball mill 2016年6月1日 The Steel Head Rod Mill (sometimes call a bar mill) gives the ore dressing engineer a very wide choice in grinding design and from 008# to 010# per ton of sand ground as the steel liner wear The overall cost of mill operation, exclusive of amortization, is generally less than 30c per ton (year 1958)Rod Mills: Efficient Grinding Solutions for Mining6 Advanced mill liner wear measurement and prediction services Advanced mill liner wear measurement and prediction services 7 Basic summary: Mill volume calculation Reline date (±7 days accuracy) Minimum remaining liner thickness Liner wear trend Detailed report: Liner longitudinal and crosssectional wear profi lesAdvanced mill liner wear measurement and prediction services
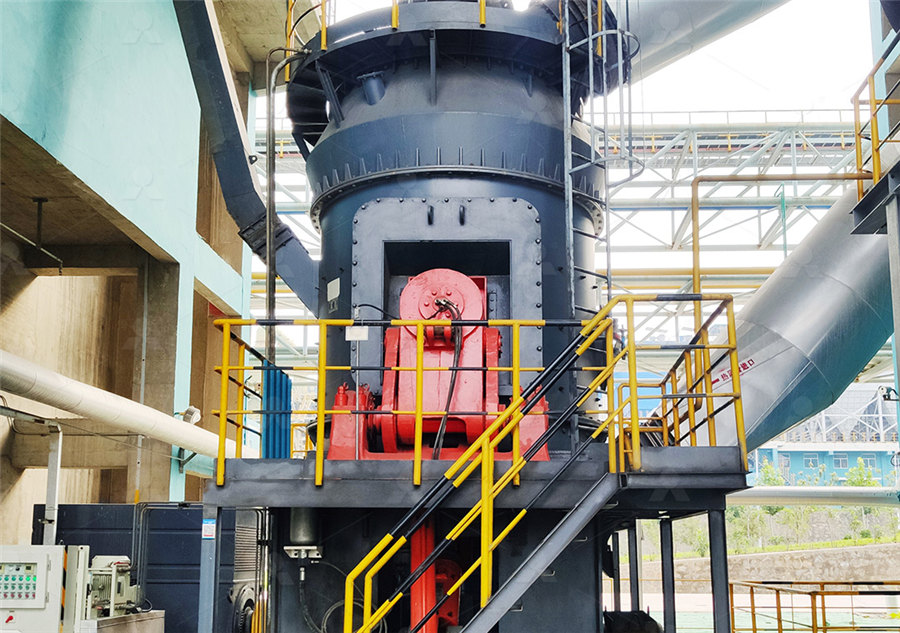
how to design a ball mill grinding circuit for ore grinding
Choose the proper size ball mill and hydrocyclone according to the ore charactor and the processing capacity Adopting the slurry pump with frequency conversion feature to feed the hydrocyclone for easy adjustment Install Particle Sizing DOI: 101016/JTRIBOINT201706017 Corpus ID: ; Friction and wear of liner and grinding ball in iron ore ball mill @article{Peng2017FrictionAW, title={Friction and wear of liner and grinding ball in iron ore ball mill}, author={Yuxing Peng and Xu Ni and Zhencai Zhu and Zhangfa Yu and Zixin Yin and Tongqing Li and Liu Songyong and Lala Zhao and Jie Xu}, Friction and wear of liner and grinding ball in iron ore ball mill2020年1月27日 Figure 2: Cascadingimpact action in a SAG mill Rubber and composite mill lining systems In the past, grinding mills were typically lined with cast metal linings of varying steel or iron alloys, and lining system selection was typically driven by level of Key considerations when selecting a mill lining system2024年5月17日 A SAG (SemiAutogenous Grinding) mill is a giant rotating cylinder filled with grinding media and the ore being reduced As the mill rotates, the grinding media lifts and the impact crushes the feed material SAG mill control refers to the practice of managing the mill load, which is the amount of material inside the mill at any given timeA guide to SAG Mill management
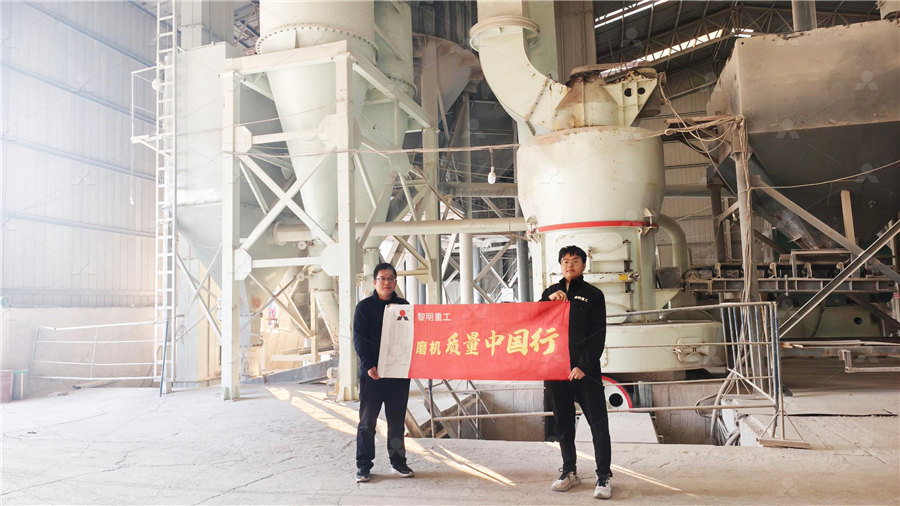
Effect of ore heterogeneity on the ball mill wear rate during a
Effect of ore heterogeneity on the ball mill wear rate during a grinding process at gold mines of Saudi Arabia (KSA) Gamal S Abdelhaffez1,2* , Haitham M Ahmed1 , Hussein A Saleem1,2 1King Abdulaziz University, Jeddah, Saudi Arabia 2Assiut University, Assiut, Egypt *Corresponding author: email gamalhaffez@gmail Abstract Purpose2023年7月18日 The grinding media is an important part of the ball mill for grinding ore and needs to be checked for wear If there is wear, it should be replaced in time 2 Check the sieve The sieve is part of the discharge port of the ball mill and needs to be checked for whether the pore is blocked or the sieve is wornBall Mill Maintenance Process and Methods Miningpedia2016年11月12日 In the work cited the calculation of such wear has, to a first approximation, been carried out and it is suggested that the relationship between rate of wear and relative hardness of ball and particle has the form shown in Fig 82, whilst the relationship between rate of wear and quantity of powder in the mill has the form of Fig 83Grinding Media Lining Media Liner Wear Rate Modelling2017年10月18日 As seen in Fig 9, a decrease in impact wear tended to result in an increase in abrasive wear and vice versa Thus, the choice must be a compromise: balls should be selected with impact and abrasion properties that best match the conditions determined by the mill diam and type of oreGrinding Ball Wear Breakage by Impact Abrasion Tests
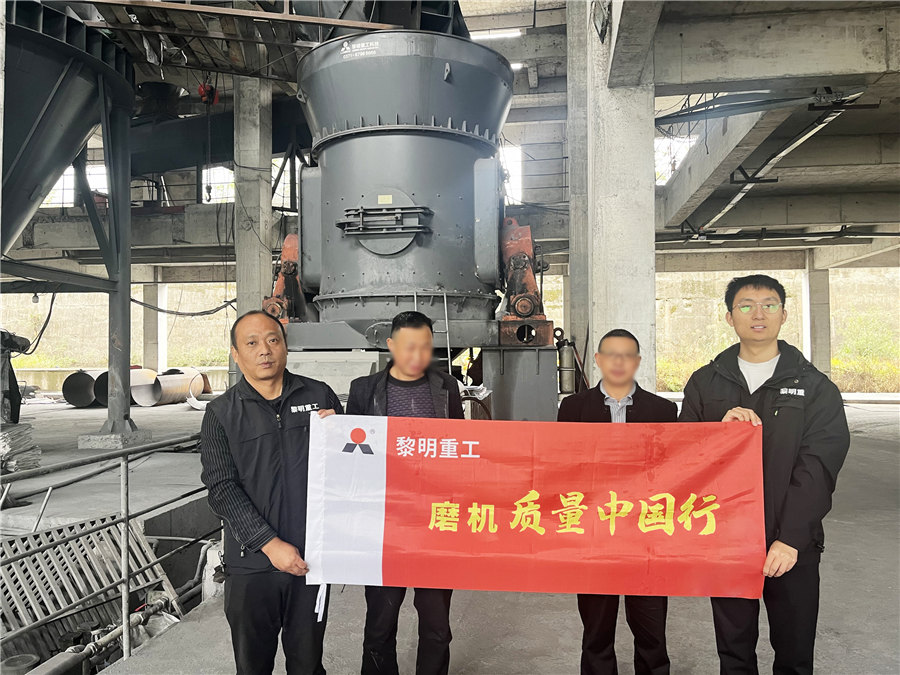
How to Use Hard Ore Components as Grinding Media
2012年10月30日 The ballmill data were analyzed by means of the orespecific breakage distribution function determined from pendulum tests and a multisegment ballmill model, enabling a scaleup relationship to 2020年11月2日 In this process, the material will be impacted by the medium to a certain extent Under the forces of crushing and collision, ball mill completes grinding process Therefore, when ball mill is working, you feed new materials into the mill, and the material grounded and sent out under the help of water power, or wind power, etcHow to Install and Debug Ball Mill Correctly?