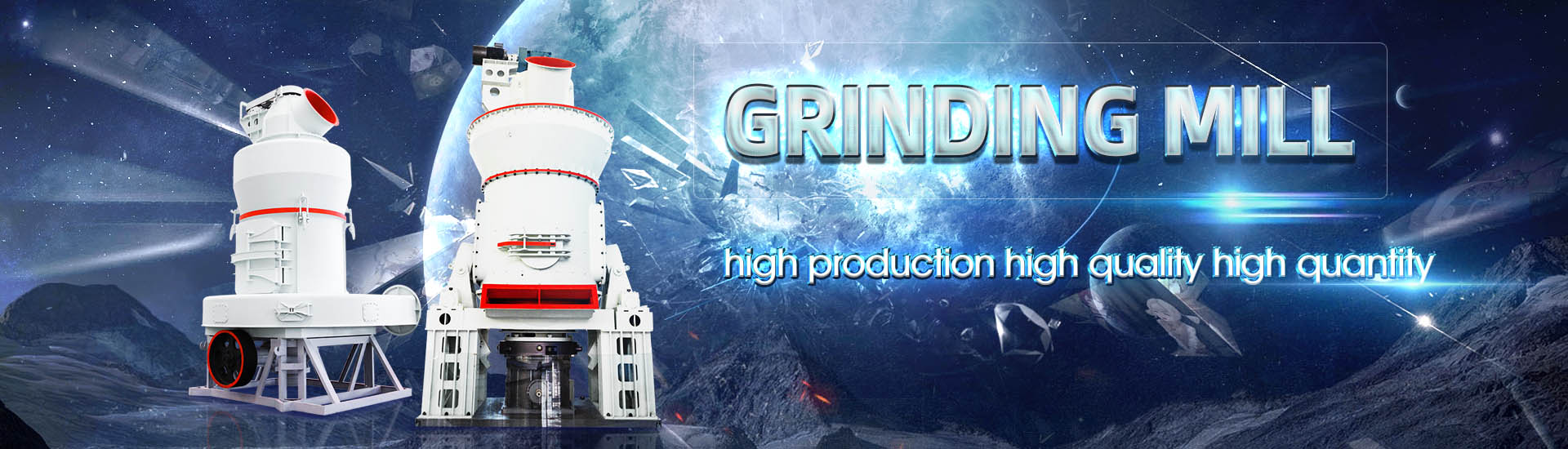
Cement raw material grinding system flow chart China Cement Network
.jpg)
Sankey diagram of cement grinding system
Cement is a fundamental ingredient in the construction industry and infrastructure development; these sectors depend on this raw material and the demand proportionally increases as theFigure 1 shows a schematic of a closedloop cement grinding process control system [6] Inside the rotating ball mill, the feed flow supplies raw material (natural stones of variousA schematic of a closedloop cement grinding control Raw material grinding The current standard solution for raw material grinding is the VRM, offering the advantages of an efficient comminution system combined with a high drying capacity Thomas Holzinger, Holzinger Consulting, grinding system common solution to grind raw materials and cement Roller presses are used mainly in combination with a ball mill for cement grinding applications and as finished product grinding BALL MILLS Ball mill optimisation Holzinger Consulting
.jpg)
Analysis of material flow and consumption in cement production
2016年1月20日 In the surveyed cement plant, three balances are established between input and output material in the raw mill, clinker production, and cement grinding system 248 t, 469 t, 2015年8月1日 The results show that approximately 248t, 469t, and 341t of materials are required to produce a ton of the product in raw material preparation, clinker production, and cement grinding(PDF) Analysis of material flow and consumption in raw materials, burning, grinding and quality control are supported by a range of chapters addressing critial topics such as maintenance and plant reporting, alongside a detailed The Cement Plant Operations Handbook International Cement 2024年9月15日 Operating parameters of a cement plant were optimized by BP neural network and GA Feeding quantity of raw meal, coal at kiln inlet and outlet were the main objects The Operation optimization of cement clinker production line based
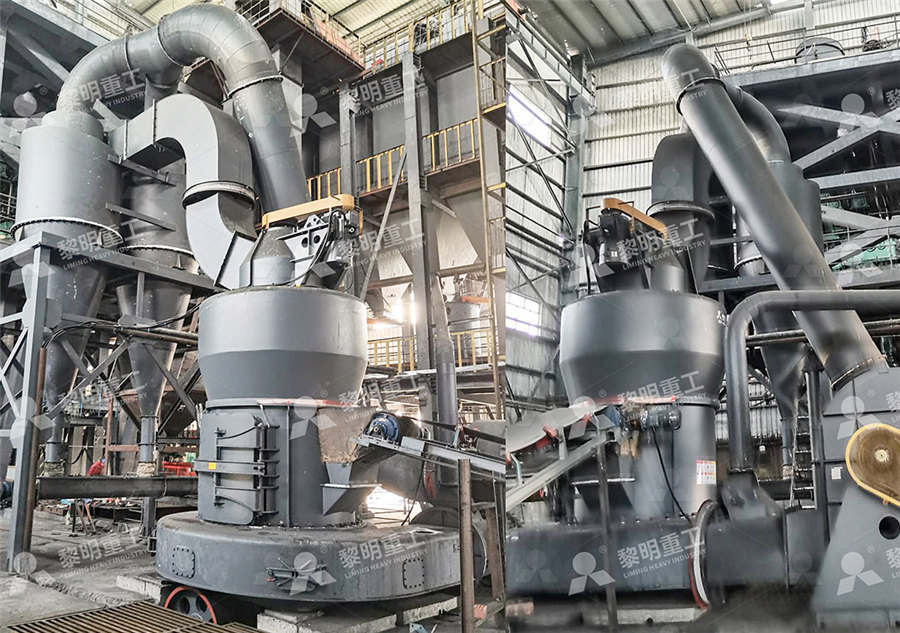
DOUDCGAN: Optimization of cement grinding operational
Targeting the problems of multiple equivalent optimal solutions and easy to fall into local optimal solutions in Paretobased optimization algorithms, this paper proposes a new optimization An evaluation of the grinding system and operation includes meaningful and critical inspection of all equipment, components and the process parameters by experts PEC Consulting can help OPTIMIZATION OF CEMENT GRINDING OPERATION IN BALL MILLSRaw material blending is an important process affecting cement quality The aim of this process is to mix a variety of materials such as limestone, shale (clay), sandstone and iron to produce The cement raw material blending process and its control system Download scientific diagram Stages in cement production flow chart [43] from publication: A review on kiln system modeling The purpose of this study is to evaluate performance cement of Stages in cement production flow chart [43] ResearchGate
.jpg)
Modeling Based on the Extreme Learning Machine for Raw Cement
2015年1月1日 Vertical grinding mill is the main grinding equipment for the newtype dry cement raw meal production, raw material grinding process in cement industries accounts for approximately 50#8211;60#160;% of the total energy consumption The dynamic characteristics of theThomas Holzinger, Holzinger Consulting, discusses cement grinding system optimisation Introduction The cement industry uses a wide range of different systems in raw material, coal, and cement grinding While new plants mainly focus on highly energy‑efficient systems, using roller comminution systems like vertical roller mills (VRMs) and highThomas Holzinger, Holzinger Consulting, grinding system Download scientific diagram Flow chart of the grinding and blending process from publication: Effective Optimization of the Control System for the Cement Raw Meal Mixing Process: I PID Tuning Flow chart of the grinding and blending process2019年11月30日 The raw materials are fed into the kiln via a multiplestage suspension preheating system The dry mixture is preheated by direct contact with the waste gases in a two or fourstage cyclone system The gases and raw feed move countercurrently The raw feed attains a temperature of about 180°C and is then directly fed into the rotary kilnManufacture Of Portland Cement Process Flow chart civil
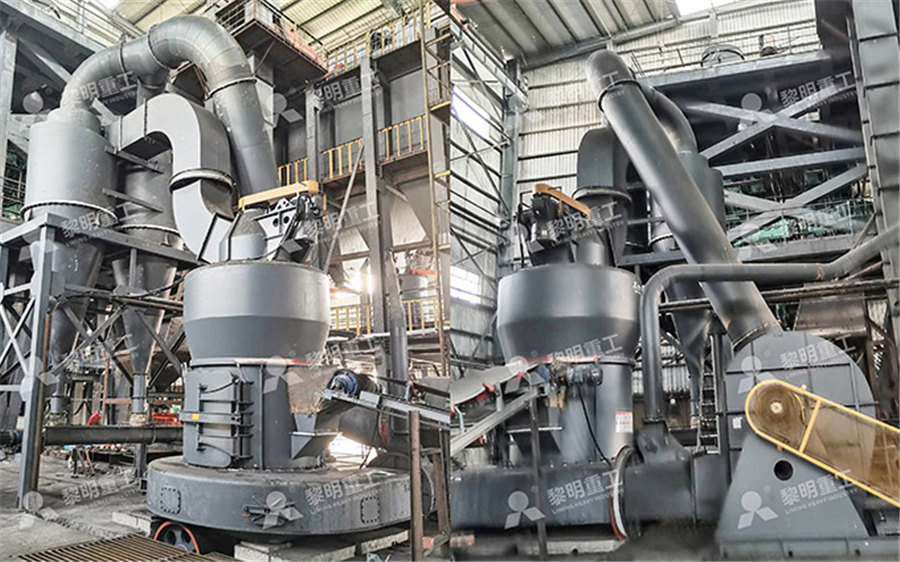
Prediction of raw meal fineness in the grinding process of cement raw
2020年10月24日 Raw meal fineness is the percentage content of 80 µm sieving residue after the cement raw material is ground The accurate prediction of raw meal fineness in the vertical mill system is very 1 OVERVIEW GRINDING SYSTEMS The common cement grinding systems are summarized in Figure 1 and can be divided into three main groups: Tube Mill Only All grinding work is done in the tube mill and the setup is: ¨ Tube mill in open circuit ¨ Tube mill in closed circuit with; Mechanical air separator; Rotor type separatorCEMENT GRINDING SYSTEMS INFINITY FOR CEMENT EQUIPMENT2012年12月10日 This paper focuses on modelling and solving the ingredient ratio optimization problem in cement raw material blending process A general nonlinear timevarying (GNLTV) model is established for Modeling and Optimization of Cement Raw Materials Blending ProcessDownload scientific diagram A schematic of a closedloop cement grinding control system Adapted from [6] from publication: Coarse Return Prediction in a Cement Industry’s Closed Grinding A schematic of a closedloop cement grinding control system
.jpg)
Everything you need to know about cement Materials
Brundick, H, “Drying and grinding of extremely moist cement raw materials in the Loesche mill,” ZKG International, No2, 1998, pages 6471Brundick, Horst, and Schäfer, HeinzUllrich, “Loesche mills for clinker grinding,” Asian Cement and 2017年10月12日 The results show that approximately 248t, 469t, and 341t of materials are required to produce a ton of the product in raw material preparation, clinker production, and cement grinding stages Predictive Control of a Closed Grinding Circuit Download scientific diagram Flow chart of cement clinker burning system from publication: Technical Route to Achieve UltraLow Emission of Nitrogen Oxides with Predictive Model of Nitrogen Flow chart of cement clinker burning systemBall Mill Cement Grinding System In Cement Plant English VersionIn this session I will explain about How To Operate The Ball Mill Cement Grinding SystemBalBall Mill Cement Grinding System In Cement Plant English Version
.jpg)
Simulation and Optimization of an Integrated Process Flow Sheet
2021年3月9日 In this study the process flow diagram for the cement production was simulated using Aspen HYSYS 88 software to achieve high energy optimization and optimum cement flow rate by varying the flow 2022年2月15日 However, different from ordinary multivariate time series prediction problems [12], cement raw materials grinding is a dynamic process with nonlinear, strong coupling among input variablesIn the grinding process, the fluctuation of one variable will lead to the fluctuation of other related variables [13]Therefore, it is difficult to extract the dynamic characteristics SALSTMs: A new advance prediction method of energy2021年3月3日 Cement is produced by a hightemperature (about 1500 °C) reaction in a rotary kiln of carefully proportioned and blended ratios of lime (CaO), silica (SiO 2), alumina (Al 2 O 3), and iron oxide (Fe 2 O 3)The production of cement is a chemical process requiring an accurate blend of the previously cited four key organic oxides and the limitation of several undesirable Cement SpringerLink2021年1月22日 In the whole process of cement production, the electricity consumption of a raw material mill accounts for about 24% of the total Based on the statistics of the electricity consumption of the raw material mill system of 1005 production lines in China between 2014 and 2019, it is found that the average electricity consumption of the raw material preparation A Survey and Analysis on Electricity Consumption of Raw Material
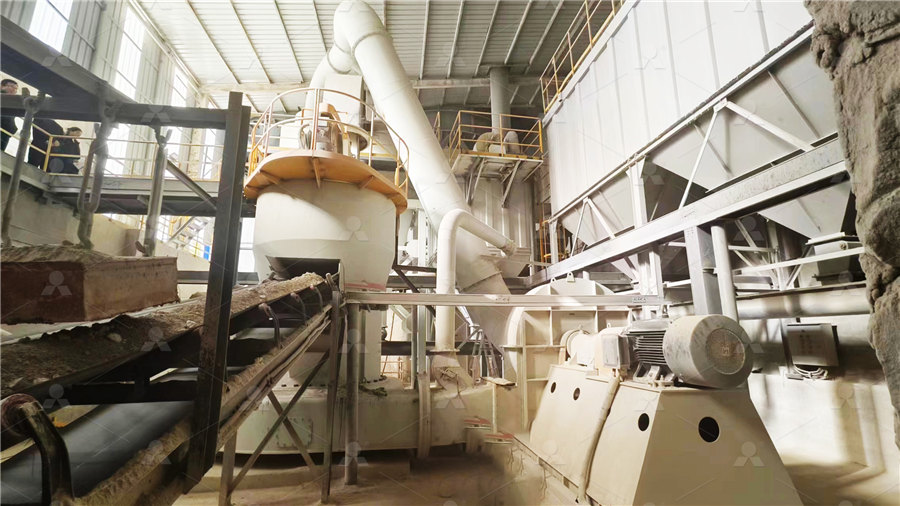
The flowchart of cement grinding, A, Bsampling points
This paper presents aspects of monitoring material dust emissions from stationary emission sources (monthly dust measurements performed on cement mill stacks—mill outlet and separator outlet)2020年10月24日 A twodimensional convolutional neural network method is proposed that is used to predict raw meal fineness during the grinding process of raw material and is proved to be very effective by comparing with the stateoftheart methods Raw meal fineness is the percentage content of 80 µm sieving residue after the cement raw material is ground The Prediction of raw meal fineness in the grinding process of cement raw 2022年3月3日 Cement Raw Materials Grinding Process (Raw Mill System) English VersionRaw Mill System is a system for grinding raw materials in the form of raw materialsCement Raw Materials Grinding Process (Raw Mill Charah Solutions is committed to providing our customers with a complete portfolio of highquality raw materials and byproducts for cement and concrete manufacturing Plus, the strength of our global network provides a consistent and reliable It is widely used after calcining as a primary ingredient in the manufacture of ChinaCEMENT MANUFACTURING RAW MATERIALS Charah
.jpg)
SALSTMs: A new advance prediction method of energy
2022年2月15日 Electricity consumption is a major energy efficiency indicator in cement raw materials grinding system Advance prediction of electricity consumption provides the basis for cement production scheduling and achieves the energy saving However, due to the influence of strong coupling, delay, intrinsic nonlinearity and uncertainty, it is difficult to model the raw When grinding cement, the additive must also have been shown not to be harmful to the finished cement Grinding aids may be added in solution, as solids to the mill feed or directly to the mill itself The addition of a fluid may be more readily con trolled than the addition of a small amount of granu lar material Grinding aids are metered Finish grinding INFINITY FOR CEMENT EQUIPMENTAGICO Cement is a cement grinding plant manufacturer, we'd like to helps you learn more about cement grinding plant and cement grinding machines Skip to content +86 Cement Grinding Plant Overview Cement Grinding Unit AGICO CementFig 49 shows a grinding system with predrying and precrushing of the SKET/ZAB, The wear of grinding media when grinding cement raw materials is approx 2050 grams/t of mill throughput According to the flow chart shown in Fig 421, the raw material is conveyed by an air current from the dryerpulverizer to an air flow Drying of raw materials INFINITY FOR CEMENT EQUIPMENT
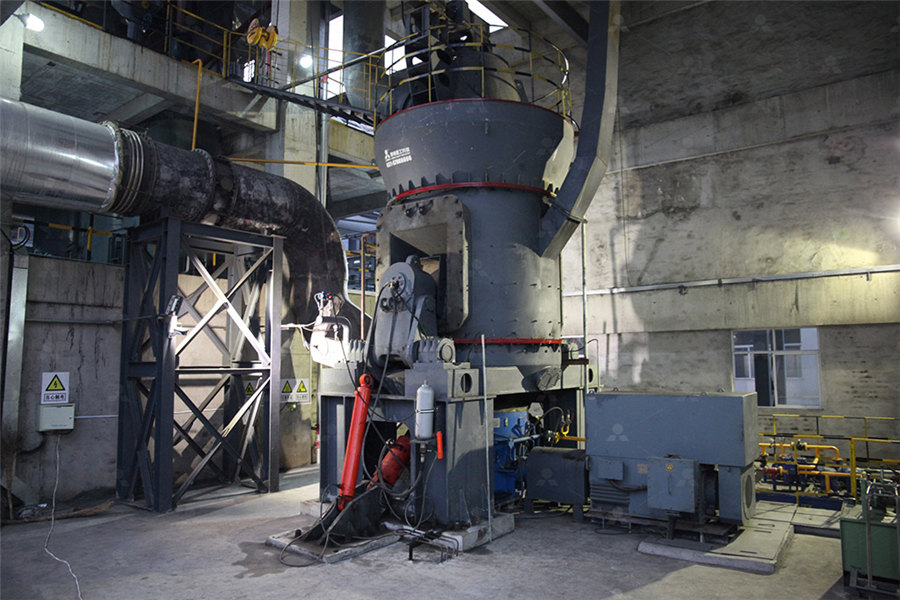
Analysis of material flow and consumption in cement production
2016年1月20日 In the surveyed cement plant, three balances are established between input and output material in the raw mill, clinker production, and cement grinding system 248 t, 469 t, and 341 t of materials are required to produce a ton of the product in raw material preparation, clinker production, and cement grinding stages; waste gases account for the largest proportion of the Material abrasivity The [%] of slag or pouzzolana content on the fresh mill feed for cement grinding The [%] of free silica at mill feed for raw material grinding Moisture content of the mill fresh feed Above or below 2 [%H2O] content The diaphragm type: the name indicated refer to Magotteaux – Slegten denominationEverything you need to know about clinker/cement GrindingDownload scientific diagram Flow chart of raw meal production from publication: Modeling of Raw Materials Blending in Raw Meal Grinding Systems The objective of the present study is to build a Flow chart of raw meal production Download Scientific Diagram2021年10月5日 Fu Lijuan, China National Building Materials Exhibition Trade Centre (CBME), and Tian Guiping Cui Yuansheng, Institute of Technical Information for Building Materials Industry of China (ITIBMIC), discuss the development status and future prospects of China’s cement industryFine China World Cement
.jpg)
Roller mills INFINITY FOR CEMENT EQUIPMENT
Fig 133 shows a flow chart of a Loeschemill for dryinggrinding of cement raw material applying exit gases from a preheater kiln Besides regular operation, at which the kiln exit gases pass the mill, and, if necessary, are boosted by an air It uses a hydraulic system to generate pressure act on the material (044mm) between the roller and the grinding disc to achieve the purpose of grinding AGICO, as a cement equipment manufacturer in China, offers different types Cement Vertical Mill Vertical Grinding Mill Vertical Vertical raw material grinding has been widely used in dry process cement plants The raw material preparation system of the 2 500 t/d cement production line can adopt the vertical mill with the disc diameter of 3 400 mm as the main grinding Raw Material Preparation in Cement Manufacturing Download scientific diagram Flow chart of the grinding and blending process from publication: Modeling of Raw Material Mixing Process in Raw Meal Grinding Installations The objective of the Flow chart of the grinding and blending process
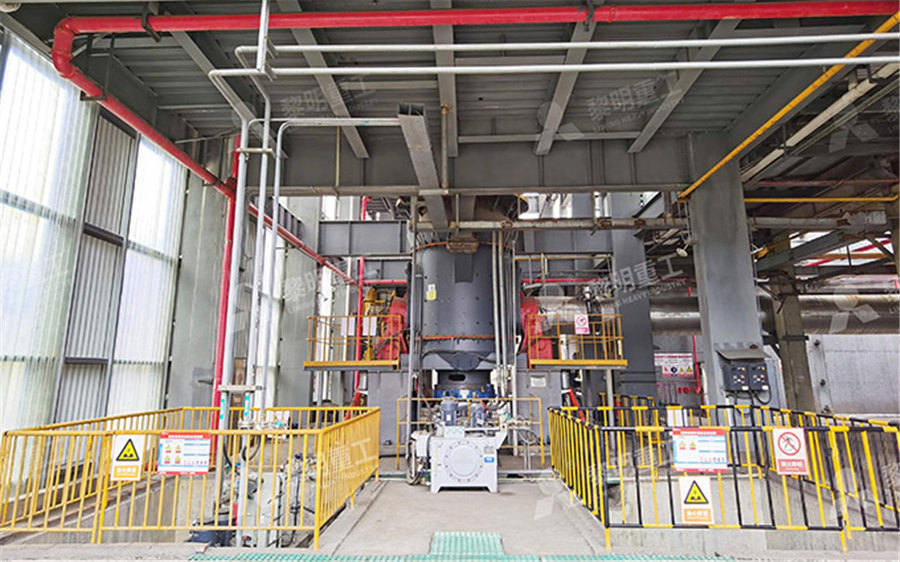
GRINDING TECHNOLOGY COURSE The Cement Institute
2024年11月4日 Gas flow, advantage and disadvantage in the Raw mill and Cement mill installations – Grindability concept and the effects of intergrinding materials of different grindability – Ball mill grinding equations and dimensioning – Describe working principles for a separator – Grinding aids and other tools to boost efficiency – Control concepts – Influence of 2020年8月25日 Cement raw material preparation: Limestone is main raw materials for cement manufacturing, and most cement plants are located next to the quarry to reduce the transportation cost; Using explosion or getter loader to mine raw materials; sending raw materials to the cement crusher to crush or hammer; crushed raw materials are stored to prevent from environment Cement Production Process Cement Manufacturing Process AGICO CEMENTChina, 62% in India, 27% in Japan, 132% in other Asian countries), cement grinding In the first step, the raw materials are fed to the kiln system to produce clinker Clinker consists of silicates, aluminates and ferrites of calciumI03 cement June 2010 GSgct IEAETSAPDownload scientific diagram Flow chart of raw meal production from publication: Modeling of Raw Material Mixing Process in Raw Meal Grinding Installations The objective of the present study is Flow chart of raw meal production Download Scientific Diagram

116 Portland Cement Manufacturing US Environmental
B Raw material unloading 07 C Raw material piles 08 D Primary crushing 09 E Secondary crushing 10 F Screening 11 G Raw material transfer 12 H Raw material grinding/drying 13 I Clinker cooler 14 J Clinker piles 15 K Clinker transfer 16 L Clinker grinding 17 M Cement silos 18 N Cement load out 19cement quality is the variability of the clinker activity [1] which depends on the conditions of the clinker formation, raw meal composition and fineness A stable raw meal grinding process provides a low variance of the fineness Figure 1 Flow chart of raw meal production Figure 1 depicts a typical flow chart of raw meal productionModeling of Raw Materials Blending in Raw Meal Grinding Systems