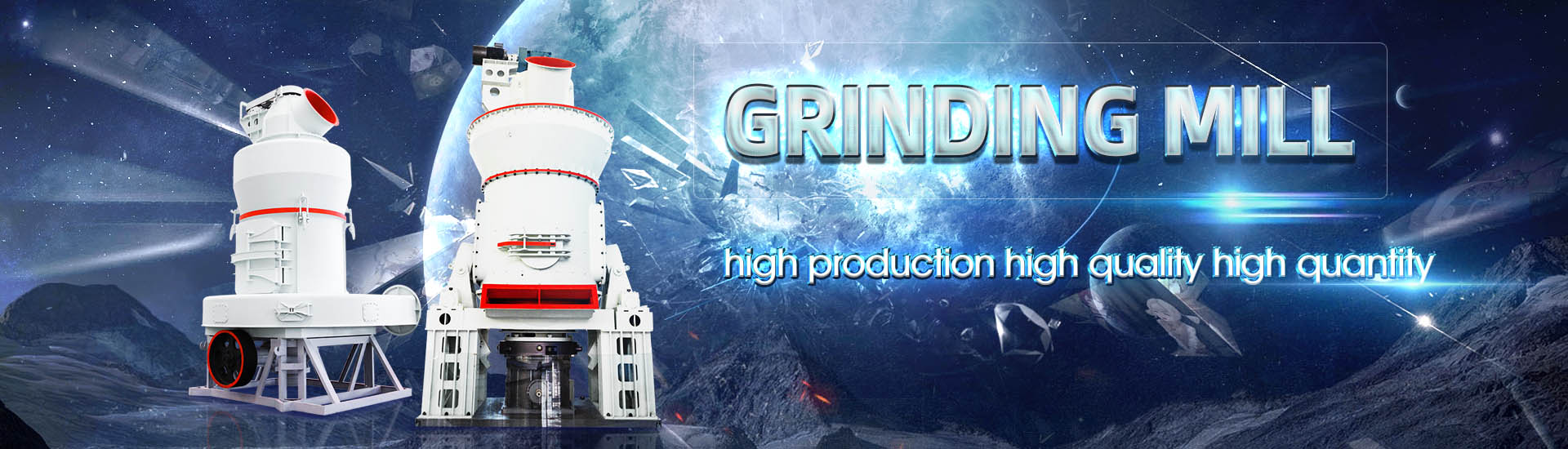
Sintered ore Kendeke sintered ore Kendeke sintered ore Kendeke
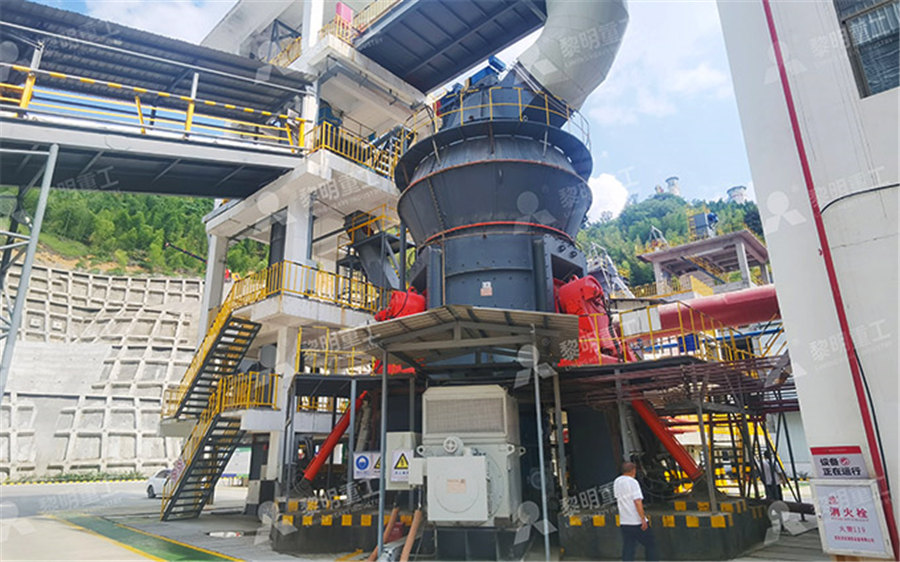
Iron Ore Sintering: Process Taylor Francis Online
2017年3月24日 Sintering is a thermal agglomeration process that is applied to a mixture of iron ore fines, recycled ironmaking products, fluxes, slagforming agents, and solid fuel (coke) The 2023年6月1日 Based on the relationship between the high temperature characteristics of ore and sinter quality/sintering performance, a good melt formation ability of adhering fines fluxed Effect of ore types on high temperature sintering characteristics of 2015年5月1日 In this review, the sintering process is first described and analyzed to identify the key factors affecting the structure and quality of iron ore sinter Under fixed sintering Important iron ore characteristics and their impacts on sinter 2017年2月16日 Sintering is a thermal agglomeration process that is applied to a mixture of iron ore fines, recycled ironmaking products, fluxes, slagforming agents, and solid fuel (coke) The (PDF) Iron Ore Sintering: Process ResearchGate
.jpg)
Iron Ore Sintering SpringerLink
2024年1月1日 Iron ore sintering is the iron ore powder agglomeration process that changes fine iron ore powder into the lumpy ironbearing raw material used for blast furnace ironmaking 2016年8月24日 Sintering is the most economic and widely used agglomeration process to prepare iron ore fines for blast furnace use Owing to the depleting reserves of traditional high Recent advances in iron ore sintering Taylor Francis Online2016年9月1日 Sintering is the most economic and widely used agglomeration process to prepare iron ore fines for blast furnace use Owing to the depleting reserves of traditional high Recent advances in iron ore sintering L Lu, O Ishiyama, 年10月1日 Cheng et al [51] developed a computational model of iron ore sintering with gaseous fuel injection and theoretically explained the impact of gaseous fuel injection on the Recent progress in sustainable and energyefficient technologies
.jpg)
Prediction of sinter yield and strength in iron ore sintering process
2018年2月25日 The iron ore sintering is modeled and simulated based on heat and mass transfer The cool rate and melt fraction could be used as an indicator to predict sinter strength Sinter plants process a mixture of iron ore fines, recycled ironmaking products, slagforming agents and solid fuel (coke) with the finality of obtaining a product with the suitable Iron Ore Sintering: Quality Indices Taylor Francis Onlinean ore bed rises to 20 kPa) and the composition of the sintered ores and pellets Since the softening and melting behavior of ore is significantly affected also by its rate of reduction, which is determined by its physical structure, the influences of the ore composition over the Ts were smaller than those over the Td Nevertheless, the TsQuality Improvement of Sintered Ore in Relation to Blast Furnace 2017年2月16日 PDF Sintering is a thermal agglomeration process that is applied to a mixture of iron ore fines, recycled ironmaking products, fluxes, slagforming Find, read and cite all the research you (PDF) Iron Ore Sintering: Process ResearchGate
.jpg)
A Short Review of the Effect of Iron Ore Selection on
2021年11月3日 A crystallographic understanding of iron ores and sintered ore is necessary to produce qualified iron ore sinter In most Asian countries, iron ore sinters used in ironmaking are produced by mixing iron ores originating from 2024年6月20日 The experimentation allowing comparison of manganese ore fines pellet sintering and traditional sintering of manganese ore fines in terms of sintering performance are studied The results show that, compared with traditional sintering, the pelletsintering process can significantly reduce the coke level while ensuring the quality of sinter Pellet sintering required Study on Sintering Technology of Manganese Ore Fines 2018年11月25日 Based on further studies as well as initial studies, the equation which has been proposed for calculating the optimum moisture (W) as a function of the nature, composition and granulometry of the iron ore is W = 228 + 0427 L + 0810 A – 0339S + 0104D + 0036 E where L is the ore weight loss during heating in grams, A is % Al2O3 in ore, S is % SiO2 in ore, D is Theory and Practice of Sintering of Iron ore – IspatGuru2024年4月24日 To improve the crushing effect and reduce the range of particle size distribution after crushing, the crushing mechanism and the particle size distribution pattern after crushing of sintered ore under different roller rotation speeds are analysed in this paper Based on the discrete element method, the microscopic parameters of sintered ore are calibrated and Crushing mechanism analysis of sintered ore and study of particle
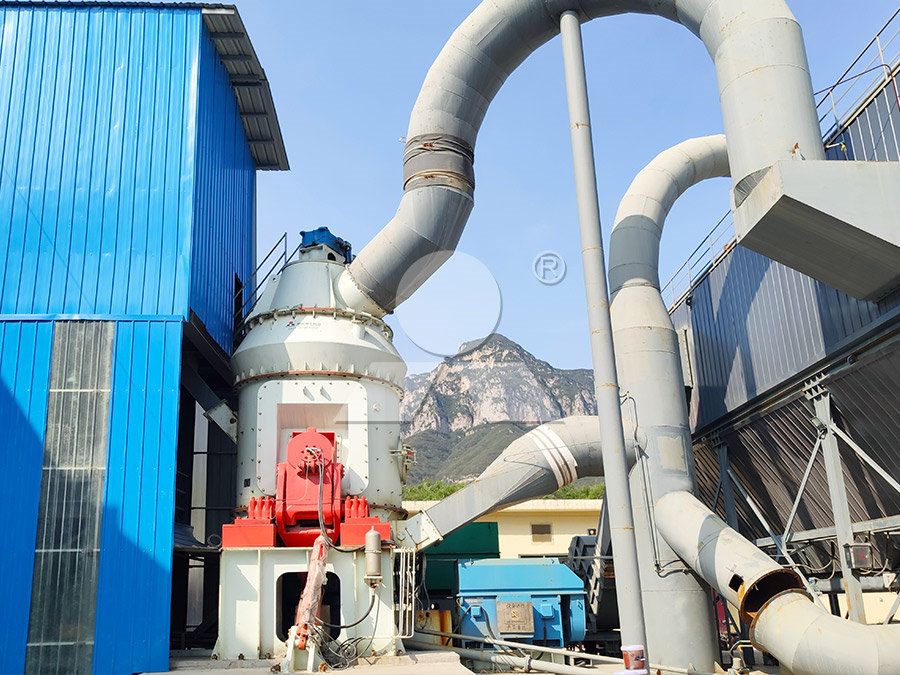
Effect of ore types on high temperature sintering characteristics of
DOI: 101016/jmineng2023 Corpus ID: ; Effect of ore types on high temperature sintering characteristics of iron ore fines and concentrate @article{Han2023EffectOO, title={Effect of ore types on high temperature sintering characteristics of iron ore fines and concentrate}, author={Hongliang Han and Liming Lu and Sarath Many translated example sentences containing "sintered ore" – JapaneseEnglish dictionary and search engine for Japanese translationssintered ore Japanese translation – LingueeManufacturing sintered ores with less Al 2O 3, SiO 2, or FeO content with superior hightemperature properties including reducibility has been explored in many plants5) However, considering the future trend of natural resources, Influence of Ore Assimilation and Pore Formation during Sintering on Reduction Behavior of Sintered OresInfluence of Ore Assimilation and Pore Formation during Sintering 2020年3月1日 This study shows LIBS combining PCAVIRF is an effective method for accurate quantification of the alkalinity of sintered ore and has great significance for the potential application of realtime online analysis of the acidity of sINTered ore The alkalinity of sintered ore has an important impact on the quality, output, and energy consumption of blast furnace Accurate quantification of alkalinity of sintered ore by random
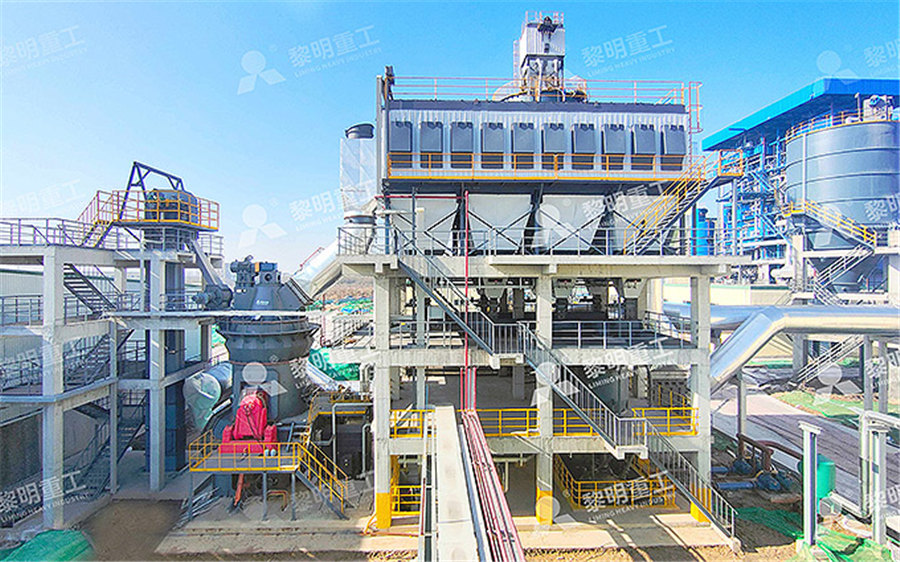
(PDF) Iron ore sintering Part 1 Theory and practice of
2013年8月1日 PDF Sintering is a process by which a mixture of iron ores, fl uxes and coke is agglomerated in a sinter plant to manufacture a sinter product of a Find, read and cite all the research you 2017年7月31日 Sinter quasiparticles consist of nuclei particles and adhering fines Therefore, reaction properties of the nuclei ore will ultimately affect the bonding strength of the sintered body In this study, microsintering tests were conducted to explore the melt absorbability of nuclei ore and its effect on the suitable liquid content of the sintered body The results showed that the Melt Absorbability of Iron Ore Nuclei and Its Influence on Suitable 2023年2月15日 The mineral phase composition and structure of sintered ore are closely related to its quality Analyzing the characteristics of the phase structure of sintered ores and studying the influence of Mineralization Characteristics of Iron Ore Sinter and 2015年1月1日 In modern optical mineral analysis, the information required extends well beyond basic mineral identification and qualitative description The main goal in optical microscopic characterization of iron and other ores is to obtain information, which will assist in the determination of the downstream processing route of such ores (Donskoi et al, 2007, Donskoi Automated optical image analysis of natural and sintered iron ore
.jpg)
Automated optical image analysis of natural and sintered iron ore
2015年12月31日 Automated mineralogy systems based on SEM are dominant for ore characterization, but there are relevant cases where such systems cannot perform the required characterization, as iron ores and 2019年6月11日 World resources are estimated to be greater than 800 billion tons of crude ore containing more than 230 billion tons of iron The only source of primary iron is iron ore, but before all that iron ore can be turned into steel, it must go through the sintering process Sinter is the primary feed material for making iron and steel in a blast furnaceSintering: A Step Between Mining Iron Ore and Steelmaking2024年3月16日 The sintering process is an intricate system with a protracted process flow The steps in the manufacturing line are primarily composed of the ingredients and mixing process, the sintering operation process, and the treatment of the sintered ore [39, 40]22 Important parameters and characteristics of sintering process As shown in Fig 2, all variables affecting Application of deep learning in iron ore sintering process: a review2024年3月20日 Ore fines in the zone of maximal temperatures (14001450°C) are melted and sintered, and then, during subsequent crystallization, a porous structure – an agglomeration cake is formed The burden mix, prepared for sintering, is laid in a layer on the grates of the continuously traveling grate cars of the sintering machineIron Ore Sintering Process: Transforming Raw Ore into High
.png)
Effects of Iron Ore Type and Gangue Mineral Components on
Green pellets were prepared using hematite and magnetite ores, burnt lime and alumina and mullite reagents, and then sintered at 1300°C The strength of sintered pellet increases with increasing basicity (CaO/SiO 2, C/ S) at lower basicity region The pellet using hematite ore with C/S above 15 showed higher strength than 980 N2023年1月18日 Recovery of metallurgical dust by sintering inevitably incorporates Zn into the sintered ore, which can have a significant impact on the ore formation process and the quality of the resulting ore Through miniaturesintering experiments and theoretical firstprinciples calculations, this paper analyzes in detail the influencing mechanism of Zn on the sintering Influence Mechanism of Zn on the Iron OreSintering 2022年4月4日 In this study, compacted hematite (Fe2O3) preforms were made and sintered at various temperatures, such as 1250 °C and 1300 °C, using both conventional and microwave sintering methods The density, porosity, Characteristics of Conventional and Microwave 2021年5月31日 Effects of Iron Ore Type and Gangue MineralComponents on Strength of Sintered FinePowder Granule微粉造粒物の焼結後強度に及ぼす鉱石種および脈石 Effects of Iron Ore Type and Gangue MineralComponents on
.jpg)
Preparation, characteristics and mechanisms of the composite sintered
2019年12月31日 Preparation, characteristics and mechanisms of the composite sintered bricks produced from shale, sewage sludge, coal gangue powder and iron ore tailings"sintered ore"の用例多数 and applications for creation of prospecting rights for the minerals that occur in the same type of ore deposit where the minerals as the subject of the prospecting rights occur are filed within 60 days from the day of extinction of prospecting rights or decrease of smelting ores used as raw materialssintered ore 和訳 – Linguee辞書2017年7月31日 Request PDF Melt Absorbability of Iron Ore Nuclei and Its Influence on Suitable Liquid Content of Sintered Body Sinter quasiparticles consist of nuclei particles and adhering fines Therefore Melt Absorbability of Iron Ore Nuclei and Its Influence on Suitable The mineral composition and structure of the sinter in this process are affected by the cooling stage of iron ore sintering 23) The cooling rate of sintered ore during the cooling process determines the length of time for crystal precipitation during the production of sintered ore, which is a very important factor affecting the crystallization of mineralsMineralization Characteristics of Iron Ore Sinter and the Effects of
.jpg)
Sintered IronOre Manufacturing Capabilities when Using Combined
2020年3月18日 Abstract In order to create thermal conditions that form the same timetemperature conditions throughout the height of the sinterfeed mixture after (1) blending, (2) source material pelletizing, (3) laying on the fire grate, (4) initial layer heating under the ignition hood, and (5) ignition of the solid charge fuel, a natural gasair mixture with an air flow Steel mills blend various iron ores to obtain sintered ore of uniform quality Minerals 2022, 12, 35 3 of 15 Table 2 Chemical composition of iron ores in different nations Mine NationA Short Review of the Effect of Iron Ore Selection on2015年1月1日 Like other sintering processes, iron ore sintering converts iron ore fines of often − 8 mm sizing into larger agglomerates, namely, sinter, between 5 and 50 mm particle size, which possess the physical and metallurgical characteristics and gas permeability required for efficient blast furnace operationAs shown in Figure 141, iron ore sintering is carried out in three Iron ore sintering ScienceDirect2019年4月3日 Sintering basic characteristics of fourteen iron ores were comprehensively evaluated using microsinter and grey relational analysis methods The results show that magnetite has a low assimilability, high bonding phase strength, and high crystal strength Hematite presents a good assimilability, while limonite exhibits a strong assimilability, but the Comprehensive evaluation of sintering basic characteristics of iron ore
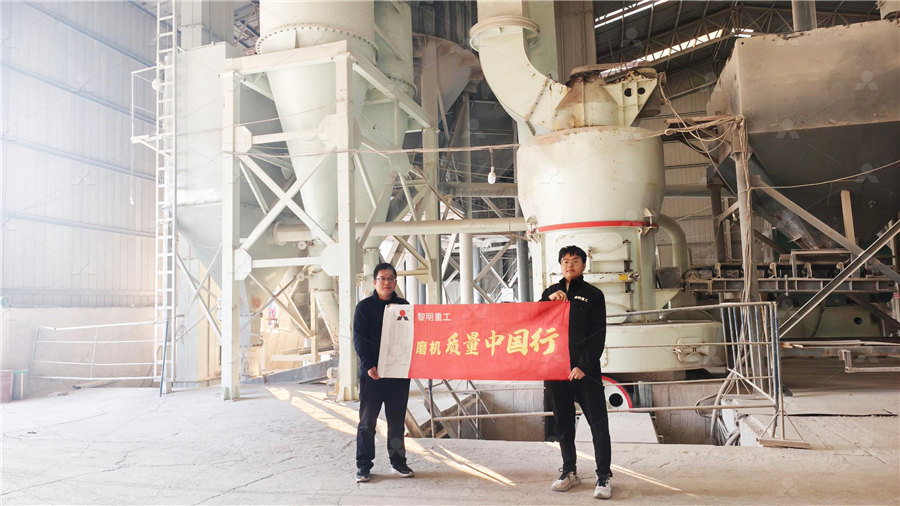
Dynamic Model of HighTemperature Sintered Iron Ore Plastic
ing the behavior of softened sintered ore has been the elastic bodybased model By adopting the DEM, which expresses each sintered ore particle as a single spherical particle, and by associating the interparticle contact force according to Heltz’s elastic contact theory with Young’s modulus, it is possible to express hightemper[6][7][8][9][10] [11] [12][13] Choudhar et al 7,8) studied the effect of the Al 2 O 3 content in iron ore powder on the sintered ore phase, and the results showed that the structure of the silico Chemical compositions of iron ores Download Scientific Diagram2013年12月18日 “Sintered Ore – A coarse granular process ore for charging into blast furnace, obtained through sintering process from grained raw materials”; loading temperature – in the range of 2836 deg centigrade; hazard: the cargo is reported to have low fire risk; hazard : dust of this cargo may be irritating to eye and respiratory tractLoading of sintered iron ore in Philippines SAFETY4SEAisij , , , , , , , , , , , , , , , , ,Mineralization Characteristics of Iron Ore Sinter and the Effects of
.jpg)
Characteristics of Conventional and Microwave Sintered Iron Ore
2022年4月4日 In this study, compacted hematite (Fe 2 O 3) preforms were made and sintered at various temperatures, such as 1250 °C and 1300 °C, using both conventional and microwave sintering methodsThe density, porosity, microhardness, cold crushing strength, microphotographs, and Xray diffraction (XRD) analysis of the sintered preforms were used to 2019年5月20日 In this study, different ore types were used to prepare ironrich, highalumina, and highsilica blends, which were sintered in a laboratory sinter pot to investigate the behavior of fine as well as coarse particles As a result, very different sinter matrices formed depending on the useful basicity in each sinterMinerals Special Issue : Mineralogy of Iron Ore Sinters MDPIIt is suggested that the establishment of integrated comprehensive system of sintering ore, which is based on the iron ore sintered performance, is one of the development direction of sintered ore optimization ore matching The sintering basic performance of iron ore fines and its research status were overviewed,the existing research methodologies and techniques of sintered ore Present Situation and Prospect of Ore Blending for Sinter Process2019年2月22日 During the iron ore sintering process, two types of particles are present in the sinter bed: (1) fines, which are actively taking part in melting and the formation of secondary phases, and (2) coarse ores, which are partially interacting with the surrounding melt The quality of the final sinter is particularly determined by the secondary phases and their bonding ability Ore Assimilation and Secondary Phases by Sintering of Rich and
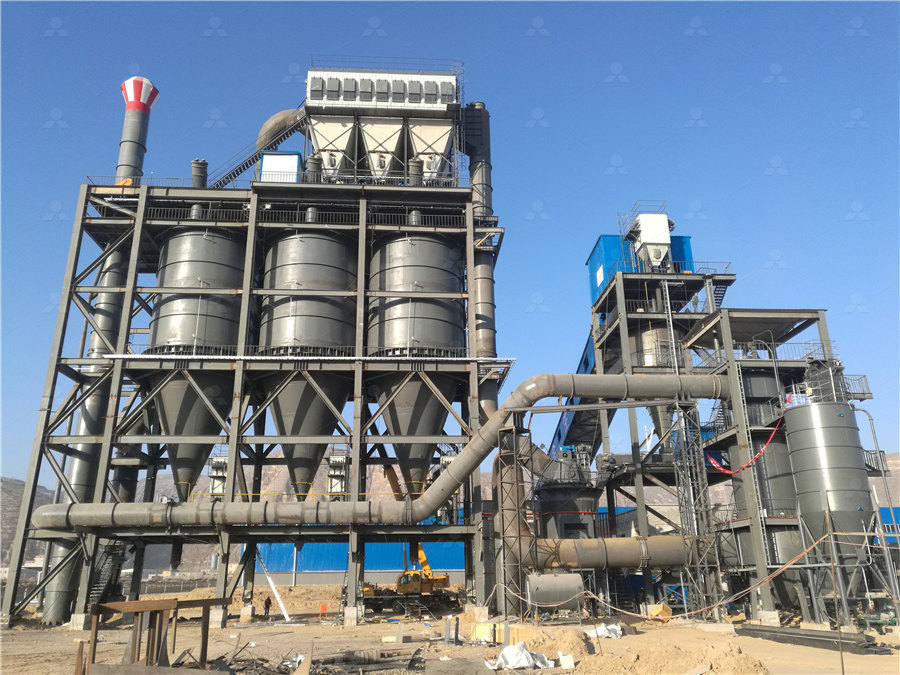
Crushing mechanism analysis of sintered ore and study of particle
2024年4月24日 Increasing the rotation speed properly can improve the crushing effect of sintered ore but also excessive rotation speed Liang Z, Chen J, Huang Z, et al Characteristics and sintering mechanisms of iron ores with a high proportion of highAl 2 O 3 limonite ACS Omega 2023; 8: 15951–159592020年3月1日 The alkalinity of sintered ore has an important impact on the quality, output, and energy consumption of blast furnace smelting, and there is an urgent need for a method for accurate quantifying of the alkalinity of sintered ore The present work explores the combination of the laserinduced breakdo Accurate quantification of alkalinity of sintered ore by random