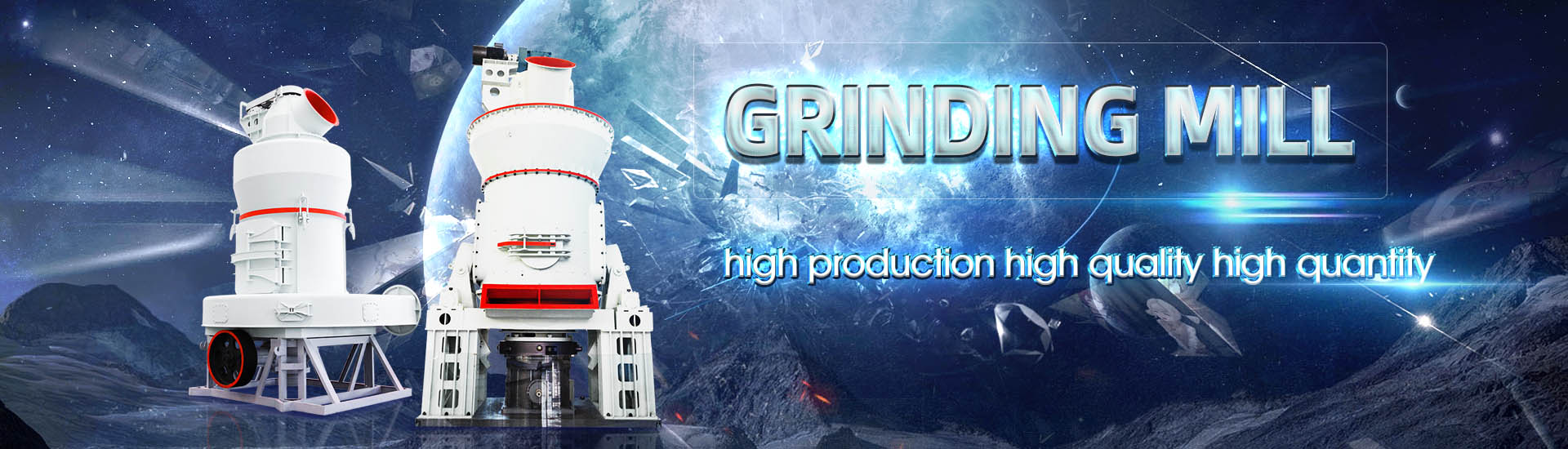
Alumina calcination
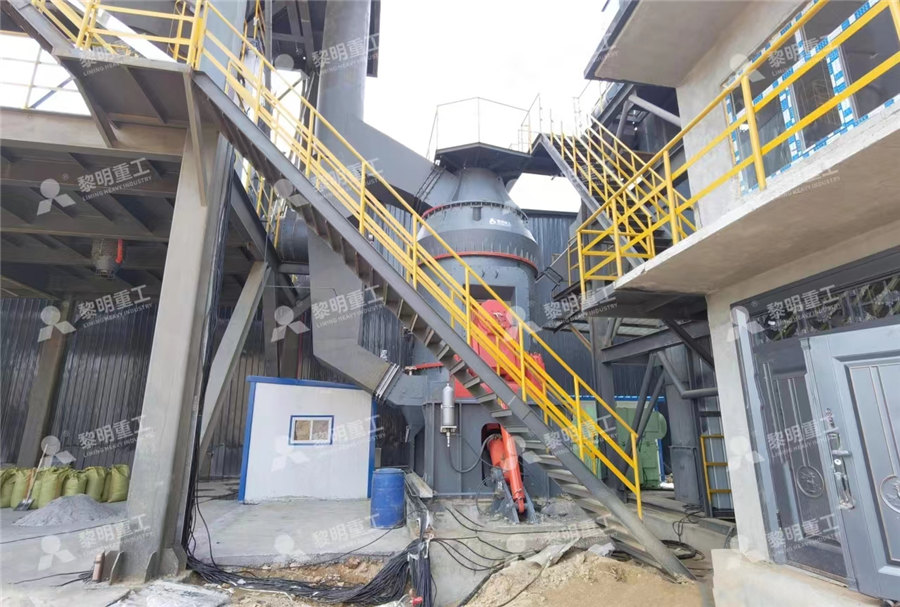
Alumina Calcination: A Mature Technology Under Review from
Calcination is the last step in the production of alumina from Bauxite In modern refineries this step is carried out in stationary calciners, such as Circulating Fluidized Bed (CFB), Gas The refractory lined Calciner Furnace/Reactor design for simultaneous combustion of fuel and final calcination of partly dehydrated hydrate to alumina at high temperature (900–1100 °C) is Production of Smelter Grade Alumina (SGA) by Calcination2016年6月1日 As the AlF 3 acts by a gasphase mechanism, it was demonstrated that even with a simple dryadmixture step and a short calcination time (30 min), it was possible to attain a AlF3 reaction mechanism and its influence on αAl2O3 2024年11月21日 To increase the catalyst efficiency, numerous studies have explored the synthesis of high surface area αalumina Through diaspore calcination at lower temperatures Synthesis of High‐Surface‐Area Alumina using Carbon Templating
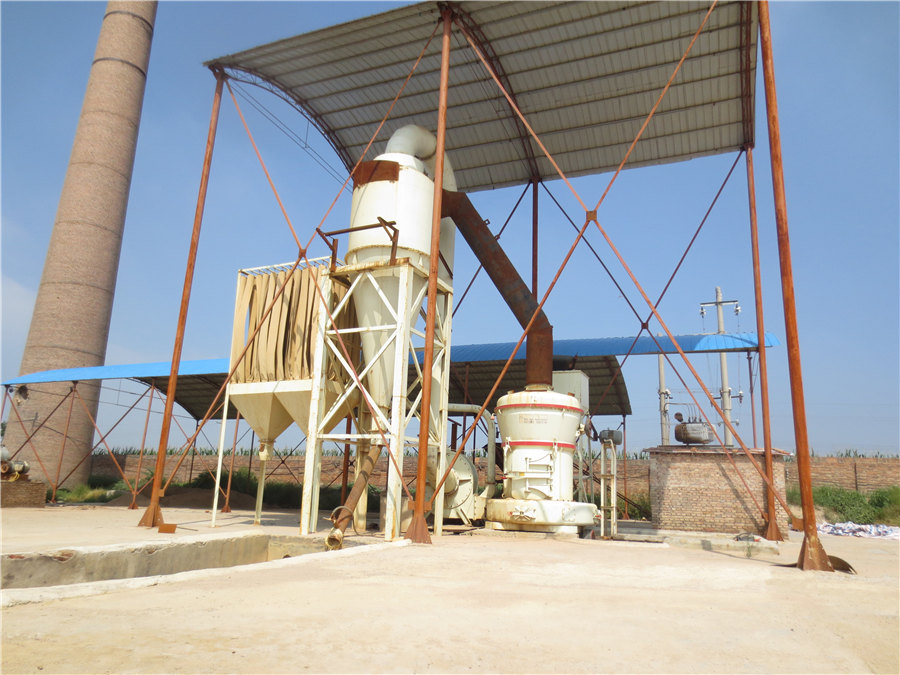
An Innovative Approach to SmelterGrade Alumina Calcination
2024年2月3日 Conduct an energy analysis to refine the alumina calcination process, including power consumption comparisons with the conventional calciners, and explore the potential for 2022年9月1日 Economical alumina precursors, derived from bauxite or nepheline ores, were calcined through a very short time process Results showed that phases of the precursor are a Effect of phase type in the alumina precursor on the flash We report on the firstofakind experimental demonstration of the calcination of alumina with concentrated solar thermal (CST) radiation at radiative fluxes up to 2190 suns using a 5 kW novel solar transport reactorSolardriven alumina calcination for CO RSC PublishingCalcination is the last step in the production of alumina from Bauxite In modern refineries this step is carried out in stationary calciners, such as Circulating Fluidized Bed (CFB), Gas Production of Smelter Grade Alumina (SGA) by Calcination
.jpg)
Worldfirst pilot to electrify calcination in alumina
On behalf of the Australian Government, the Australian Renewable Energy Agency (ARENA) has today announced $86 million in funding to Alcoa of Australia Limited (Alcoa) to investigate and trial electric calcination in the 2021年6月1日 In this study, the effects of calcination time on synthesized the alphaalumina (ie αAl 2 O 3) from aluminum cans wastes was succinctly investigated using the lefthand gel Investigating the effects of calcination time on Αalumina synthesis 2022年3月31日 Alumina is produced from bauxite in a twostep process Firstly, bauxite is digested in the Bayer process to produce alumina hydrate Secondly, alumina hydrate is calcined to produce alumina The calcination process uses high temperatures to remove chemically bound water from the hydrateAlcoa Renewable Powered Electric Calcination Pilot2017年5月10日 We report on the firstofakind experimental demonstration of the calcination of alumina with concentrated solar thermal (CST) radiation at radiative fluxes up to 2190 suns using a 5 kW novel solar transport reactor Solardriven alumina calcination for CO2 mitigation
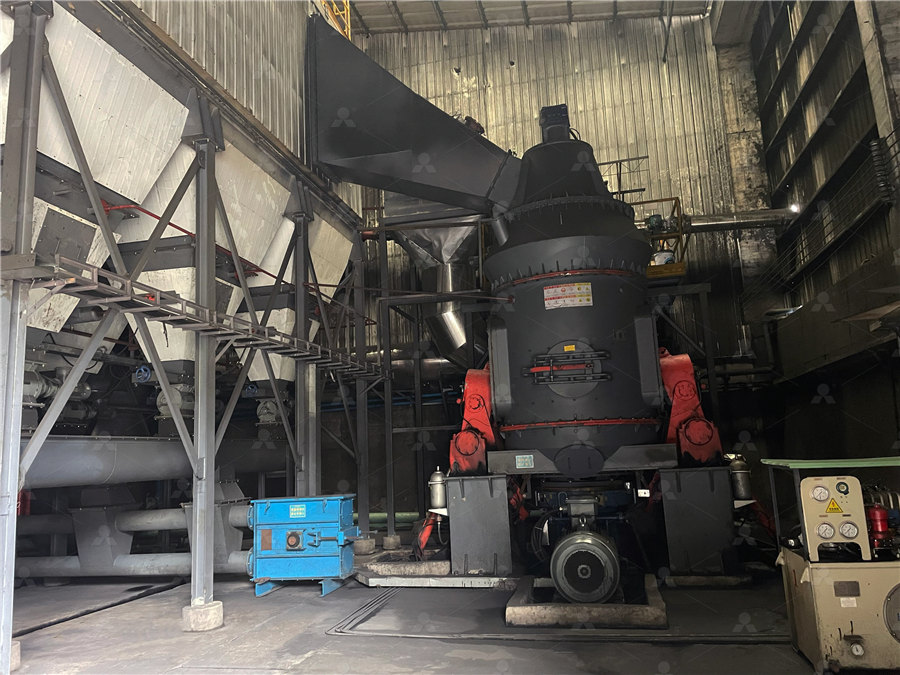
Smelter Grade Alumina CFB Calcination Plant
The purpose of the calcination plant is to produce Smelter (also termed Metallurgical) Grade Alumina (SGA/MGA) from a precipitated aluminium trihydroxide feedstock (referred to as gibbsite or hydrate)In the calciner, the Australia is the second largest producer of alumina in the world, with around 15 per cent of global production from six alumina refineries Step 4: Calcination The precipitated material (called hydrate) is washed and dried at temperatures exceeding 1000 degrees CelsiusAlumina Refining The Australian Aluminium Council2022年5月11日 The full dense alumina fiber with nanograins were prepared using a novel twostep calcination The tensile strength of alumina fibers reaches up to 22 GPa The influencing mechanism of organics removal, phase transformation, grain growth, and densification on the microstructure regulation of alumina fibers was revealedPreparation of a dense alumina fiber with nanograins by a novel 2021年6月1日 Alumina at lower calcination time recorded the lowest surface area among the four synthesized alumina at 63486 m 2 /g and 83407 m 2 /g of Al24403 and Al24303, respectively (Adans et al, 2016) The crystallite size increases linearly with increasing calcination time until a constant size was achieved Investigating the effects of calcination time on Αalumina
FYEFEPS2HDZ49G5Z0[B.jpg)
World first hydrogen pilot for low carbon alumina
ARENA’s Alumina Decarbonisation Roadmap (the Alumina Roadmap), published in 2022, identified hydrogen calcination as one of four technologies that could reduce emissions from Australia’s alumina refineries by up to 98% ARENA has been investing in projects to reduce emissions from the aluminium value chain since 20212015年2月20日 Calcination is the last step in the production of alumina from Bauxite In modern refineries this step is carried out in stationary calciners, such as Circulating Fluidized Bed (CFB), Gas Suspension (GSC) or Fluid Flash (FF) Calciners These technologies have been available for over 40 years, and are thus very far matured The technologies have developed substantially Alumina Calcination: A Mature Technology Under Review from alumina calcination: a mature technology under review from supplier perspective ruqholv ohww /lqxv 3hudqghu 2xwrwhf 3w\ /wg 8qlwv :hvw current trends and drivers for alumina calciner design ,q wkh iroorzlqj vhfwlrq fxuuhqw wuhqgv dqg gulyhuv duhALUMINA CALCINATION: A MATURE TECHNOLOGY UNDER 2013年3月1日 Heat Balance for Pressure Calcination Process Design of Industrial Pressure Calciner Future Developments Conclusions References Alumina and Bauxite, Volume 1 References; Related; Information; Close Figure Viewer Return to Figure Previous Figure Next Figure Caption Additional linksAlcoa Pressure Calcination Process for Alumina
.jpg)
Influence of calcination parameters on the
2016年6月19日 It was found that the calcination of lowtemperature alumina at 800°C allows us to obtain the optimum ratio of the strength and textural properties of a support for use in the synthesis of Metso Outotec’s Generation 5 alumina calcination technology has been successfully applied at 3 alumina refineries for a total of 5 units with a maximum capacity of 3500 tpd of alumina production Keywords: Alumina calcination, Capital cost, Circulating fluidized bed, Specific energy consumption 1 IntroductionMetso Outotec’s 5th Generation of CFB Alumina Calciners ICSOBA2011年1月1日 This is particularly so for metallurgical aluminas where the speed of the modern calcination process, together with the variation of particle size, velocity and residence time, inevitably produces a far from equilibrium phase distribution Production of alumina ScienceDirectAlumina 149 Mt CO₂e 40% 40 30 20 10 00 0 25 50 75 100 CO₂/t of Alumina Global Australia Cumulative Alumina Production % Australian Aluminium Council September 2021 CALCINATION 63% 31% ELECTRICAL PUMPS, FANS, CONVEYORS etc 5% Australian Aluminium CouncilAustralian Aluminium Pathways FACT SHEET #3 Alumina
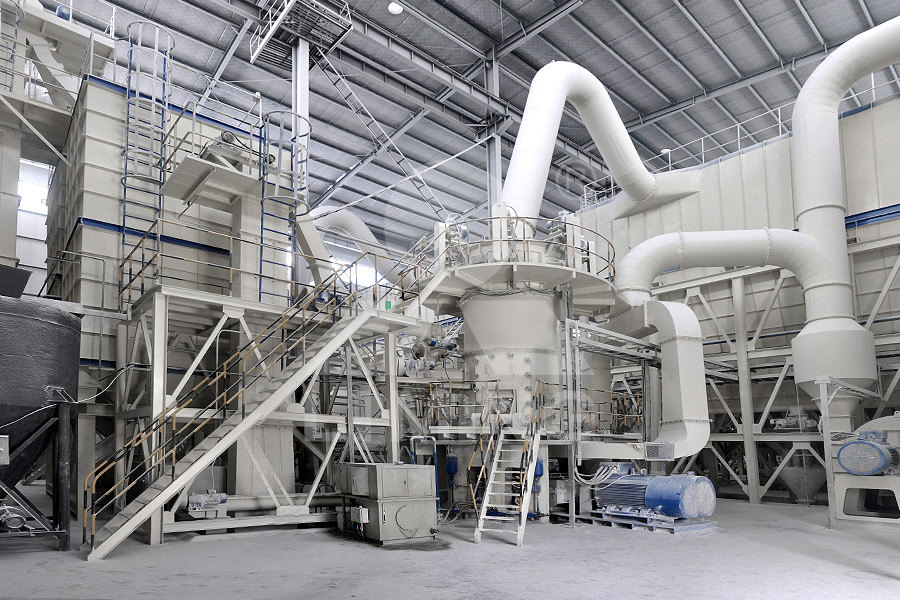
High Temperature Calcination Solar Thermal in the Bayer Alumina
For example, we have recently demonstrated the direct calcination of high quality alumina with concentrated solar radiation in a laboratory scale reactor Industry has been making alumina for about 130 years Its most recent process step change was arguably the introduction of flash calcination in the 1980s2016年6月1日 Alpha alumina phase (αAl 2 O 3) is one of the most used oxides for advanced ceramics due to its excellent properties such as chemical inertness, hardness and wear resistanceIn general, αAl 2 O 3 is produced by the calcination of either aluminum hydroxide or transition alumina phases The thermal transformation route of the precursor involves a AlF3 reaction mechanism and its influence on αAl2O3 31 Energy consumption in current alumina refineries 15 311 Energy consumption by Australian alumina 16 312 Australian refining emissions intensity 17 313 Forecast alumina refining emissions and climate aligned scenarios 18 4 Potential decarbonisation technologies 20 41 Key Decarbonisation Technologies 20A Roadmap for Decarbonising Australian $OXPLQD5H4QLQJ2021年11月9日 Calcination is the final stage in the refining process where alumina hydrate crystals are heated to remove water molecules Currently, fossil fuels are used to power calciners, but with electric calcination renewable energy will Alcoa to design an alumina refinery of the future
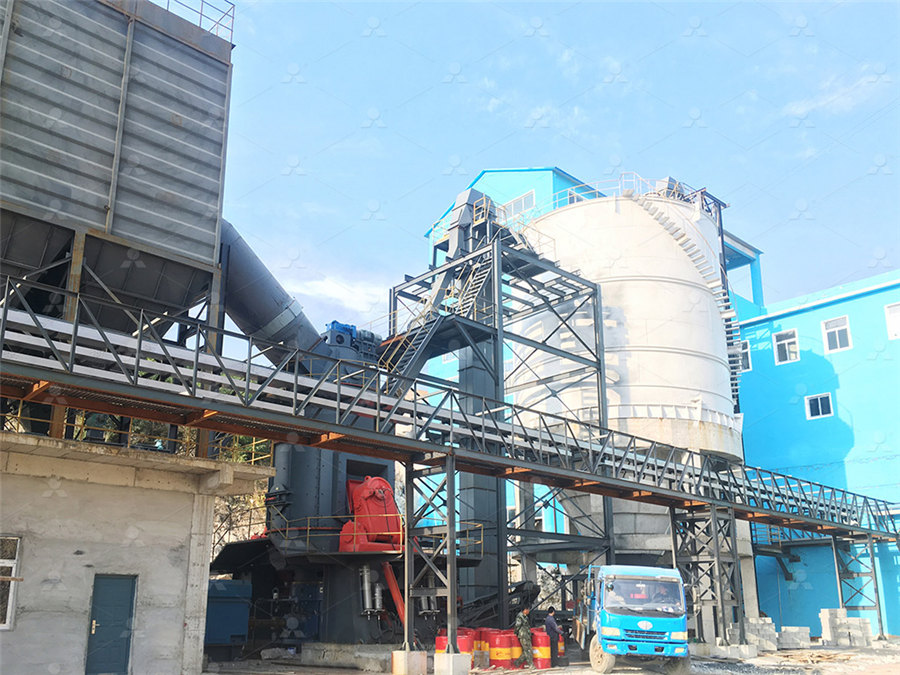
Yarwun Hydrogen Calcination Pilot Demonstration Program
2023年6月14日 By extrapolating based on current alumina production volumes in Australia, a marketwide rollout of hydrogen calcination technology could create demand for approximately 500K tpa of hydrogen and abate approx 37 Mt of CO 2e per annum In addition, there may be opportunities for the technology to be adopted by the global alumina industrySolardriven alumina calcination for CO2 mitigation and improved product quality† Dominic Davis, ‡a Fabian Müller, ‡b Woei L Saw, c Aldo Steinfeld *b and Graham J Nathan *a We report on the firstofakind experimental demonstration of the calcination of alumina with concenSolardriven alumina calcination for CO2 mitigation and contains alumina and other alloying elements, and can be used in dierent industries (ie, cement, ceramic, and building industries) after washing or calcination [19, 20] e methods of extracting aluminum and aluminum compounds from aluminum dross include pyrometallurgy and hydrometallurgy e formerRecycling of aluminum dross for producing calcinated alumina by Alumina 146 Mt CO 2e 43% 40 30 20 10 00 CO 2 /t of Alumina Global Australia Cumulative Alumina Production % Primary aluminium is made from an ore called bauxite, which is refined to make alumina before being smelted to make aluminium It takes 46 tonnes of bauxite (depending on the grade) to make ~2 tonnes of alumina, which FACT SHEET #3 Alumina Australian Aluminium Council

Production of Smelter Grade Alumina (SGA) by Calcination
2022年1月23日 The Alunorte refinery produces 63 million t/a of alumina with seven Circulating Fluid Bed (CFB) Calciners The calcination facility needs about 3 GJ per ton of alumina of the total energy of 8 GJ 2019年5月31日 In the mid 40’s, Alcoa turned to fluidized solids techniques as a means of improving the efficiency of the alumina calcining process This paper traces calciner development from the first pilot operation in 1946 through the first plant fluidbed unit in 1952,Alumina Calcination in the FluidFlash Calciner2024年7月2日 This study explores the transformation of boehmite (AlOOH) into transition aluminas during calcination, emphasizing on the progression from γAl 2 O 3 to α Al 2 O 3Through a combination of insitu techniques, the research elucidates the pseudomorphic retention of structure during initial dehydration and successive structural ordering at higher Evolution of Correlated Morphological and Structural Disorder in 2019年6月30日 CO is highly toxic even at relatively low concentrations and typically regulated (eg in the EU) at max 100 mg/Nm³ for industrial plants Generally, CO emissions are quite low in CFB alumina calcination plants, due to the overstoichiometric combustion conditions and relatively low combustion temperatures Precontrol measures for COEmissions in alumina calcination Metso
.jpg)
Effect of phase type in the alumina precursor on the flash calcination
2022年9月1日 When the flash calcination temperature was increased, the peaks intensity of aluminum hydroxides declined and these phases were converted to the other alumina phases For G precursor ( Fig 2 a), rays of gibbsite still exist up to 500 °C, afterward undergo a partial dehydroxylation that transformed to boehmite phasecalcination of the aluminium trihydroxide into smelter grade alumina, so it is important to control the flow of fuel and air to keep the calcination temperature stable and close to the setpoint However, the bottom temperature and the secondary air temperature may also interfereAdvanced Process Control and Optimization of Alumina CalcinersDEVELOPMENT OF PARTICLE BREAKDOWN AND ALUMINA STRENGTH DURING CALCINATION Susanne Wind, Claus JensenHolm and Benny E Raahauge FLSmidth A/S Minerals Denmark Vigerslev Alle 77, DK2500, Denmark Keywords: Calcination, Particle Breakdown, Alumina Strength Abstract Since the replacement of rotary kilns with stationary DEVELOPMENT OF PARTICLE BREAKDOWN AND ALUMINA STRENGTH DURING CALCINATION2023年2月15日 Industrial alumina was used as raw material in the hightemperature calcination process, and AlF 3 was introduced to promote mass transfer in the gas phase The calcination environment, such as sealing, calcination temperature, and holding time, was analyzed to enhance the effect of AlF 3 to promote the crystal growth of alumina Here, roundlike flake α Enhanced effect of AlF3 and its Coregulatory effect
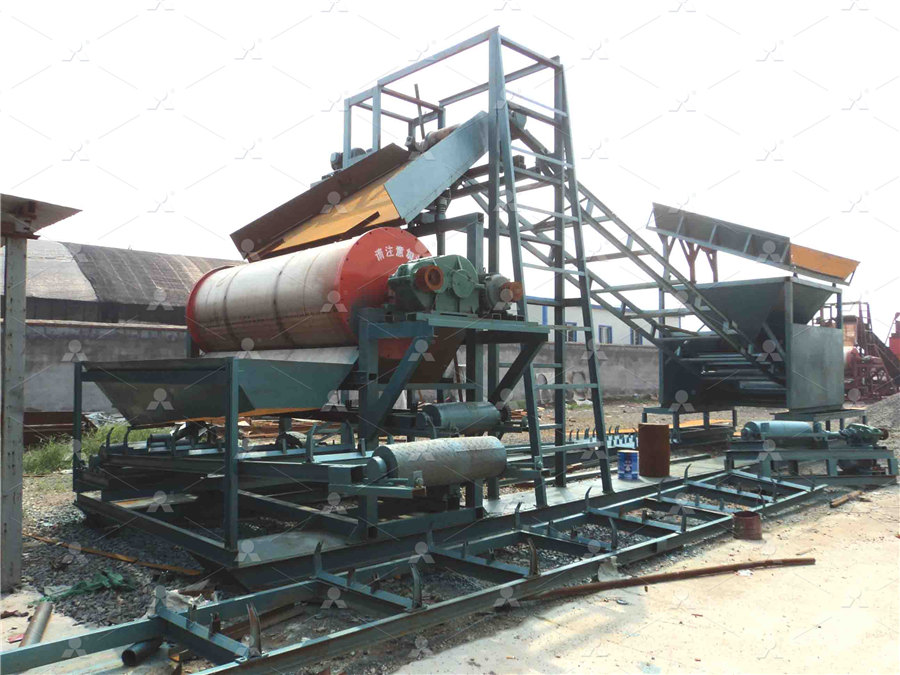
Effect of calcination temperature on the size of
Download Table Effect of calcination temperature on the size of alumina in the presence of additives from publication: The Effect of Novel Synthetic Methods and Parameters Control on Morphology 2023年7月23日 Also, the results demonstrate that calcination of the assynthesized NPs causes a decrease in band gap energies of the NPs, and the indirect band gap energies of boehmite NPs synthesized by different AB concentrations (331 to 458 eV) decrease by calcination and transformation to γalumina NPs (210 to 346 eV)Optical and structural properties of sphericalshaped boehmite 2015年2月20日 Calcination is the last step in the production of alumina from Bauxite In modern refineries this step is carried out in stationary calciners, such as Circulating Fluidized Bed (CFB), Gas Alumina Calcination: A Mature Technology Under Review from 2021年12月15日 The effects of calcination temperature on Pd/γalumina catalysts were studied using a variety of techniques to measure particle sizes, surface species, and activity in methane combustion Pd/Al 2 O 3 catalysts were synthesized using a new impregnationvortexing methodCalcination temperature effects on Pd/alumina catalysts:
.jpg)
Alcoa Pressure Calcination Process for Alumina
2013年3月1日 Heat Balance for Pressure Calcination Process Design of Industrial Pressure Calciner Future Developments Conclusions Essential Readings in Light Metals: Alumina and Bauxite, Volume 1 Related; Information; Close Figure Viewer Return to Figure Previous Figure Next Figure Caption Additional links2023年7月18日 Let’s start with the term “calcination” Alumina refineries take bauxite ore through two main processes: the Bayer process extracts alumina hydrates, or alumina chemically attached to water molecules; calcination drives off the water molecules at temperatures above 1000 degrees C to leave pure aluminaCan hydrogen slash alumina refining emissions?“This study will investigate a potential technology that can contribute to the decarbonisation of the Australian alumina industry If successful, the technical and commercial lessons from Rio Tinto’s study could lead to the implementation of hydrogen calcination technology, not only in Australia, but also internationally”Rio Tinto and ARENA to study using hydrogen to reduce carbon Conventional alumina refining combusts natural gas to achieve the high temperatures necessary in the calcination process Rio Tinto will investigate the technical implications of displacing natural gas with renewable hydrogen at its Yarwun alumina refinery in Gladstone, QueenslandRenewable hydrogen could reduce emissions in alumina refining
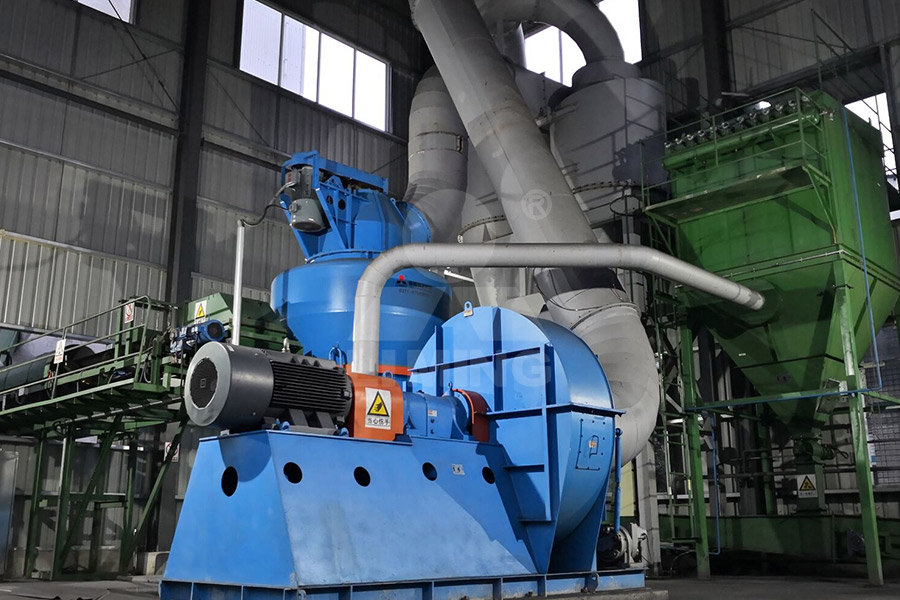
Rio Tinto and Sumitomo to build Gladstone hydrogen pilot plant
The program is aimed at demonstrating the viability of using hydrogen in the calcination process, where hydrated alumina is heated to temperatures of up to 1,000 degrees Celsius It involves construction of a hydrogen plant at the refinery and the retrofit of refinery processing equipment2015年1月1日 Alumina Calcination With The Advanced Circulating Fluid Bed Technology: A Design With Increased Efficiency Combined With Operating Flexibility HW Schmidt W StockhausenAlumina Calcination: A Mature Technology Under Review from